LMTD Correction Factor Chart Nimish Shah
Total Page:16
File Type:pdf, Size:1020Kb
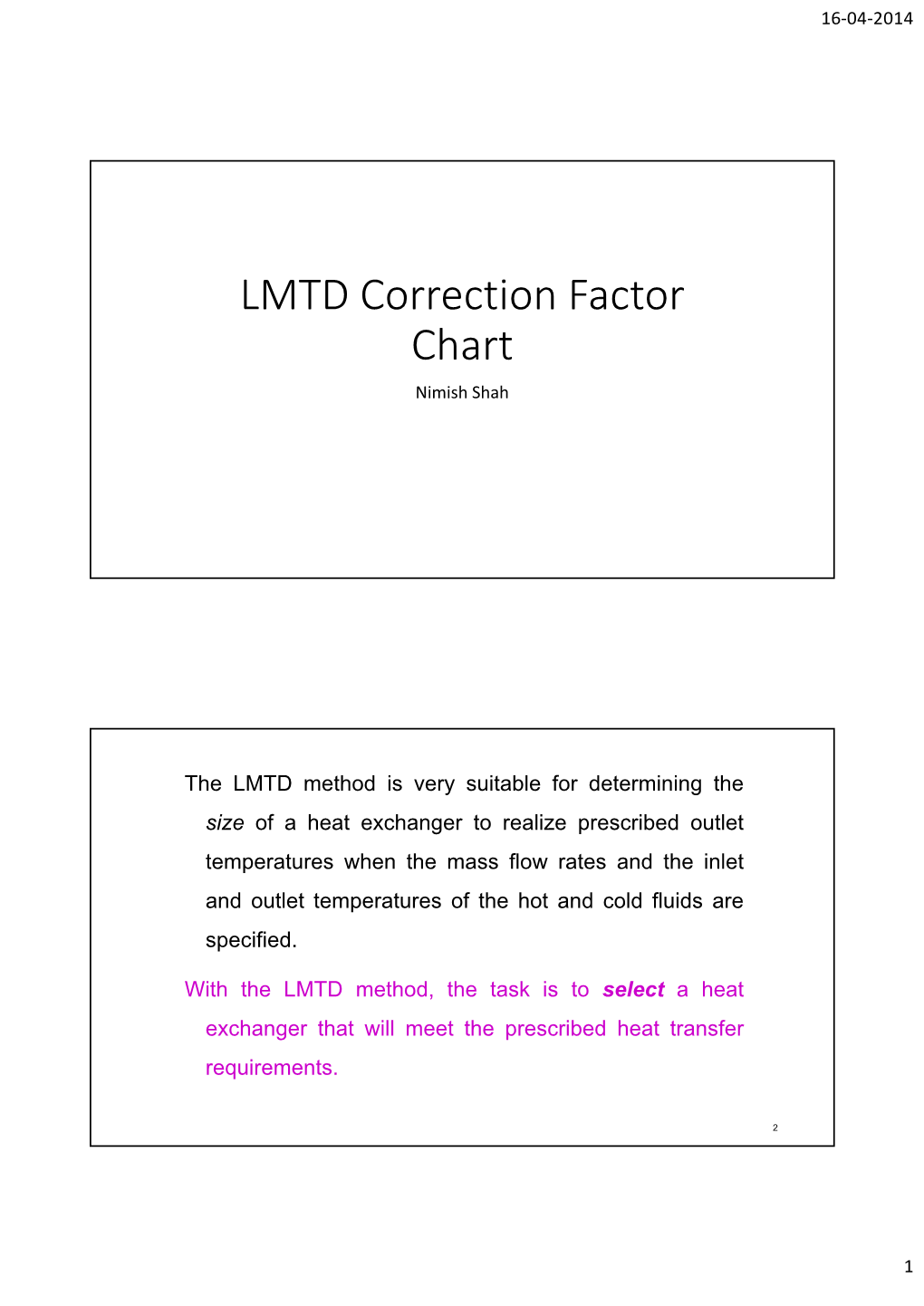
Load more
Recommended publications
-
Analysis of Air-To-Air Rotary Energy Wheels
ANALYSIS OF AIR-TO-AIR ROTARY ENERGY WHEELS A dissertation presented to the faculty of the Russ College of Engineering and Technology of Ohio University In partial fulfillment of the requirements for the degree Doctor of Philosophy Abdulmajeed S. Al-Ghamdi June 2006 © 2006 Abdulmajeed S. Al-Ghamdi All Rights Reserved This dissertation entitled ANALYSIS OF AIR-TO-AIR ROTARY ENERGY WHEELS by ABDULMAJEED S. AL-GHAMDI has been approved for the Department of Mechanical Engineering and the Russ College of Engineering and Technology by Khairul Alam Moss Professor of Mechanical Engineering Dennis Irwin Dean, Russ College of Engineering and Technology ABSTRACT Al-GHAMDI, ABDULMAJEED S., Ph.D., June 2006. Integrated Engineering ANALYSIS OF AIR-TO-AIR ROTARY ENERGY WHEELS (269 pp.) Director of Dissertation: Khairul Alam Integration of the energy recovery ventilator (ERV) with a traditional HVAC system has gained recent attention because of the potential for energy savings. The energy recovery ventilator selected for this research employs a rotary air-to-air energy wheel with a porous matrix as the heat and moisture transfer medium. The wheel is symmetrical and balanced, operating with counter-flow pattern. The primary goal of this research is to develop a mathematical and numerical model to predict the effectiveness of this energy wheel. Three models were developed for the energy recovery ventilator (ERV) containing a porous exchange matrix: a sensible model, a condensation model, and an enthalpy model. The sensible model describes the heat transfer in a rotary wheel with a non-desiccant porous matrix. Two energy conservation equations were used to model this ERV. -
Energy Effectiveness of Simultaneous Heat and Mass Exchange Devices
Energy effectiveness of simultaneous heat and mass exchange devices The MIT Faculty has made this article openly available. Please share how this access benefits you. Your story matters. Citation Narayan, G. P. et al. "Energy effectiveness of simultaneous heat and mass exchange devices." Frontiers in Heat and Mass Transfer (FHMT), 1, 023001 (2010)Copyright © 2010 by Global Digital Central As Published http://dx.doi.org/10.5098/hmt.v1.2.3001 Publisher Global Digital Central Version Final published version Citable link http://hdl.handle.net/1721.1/65079 Terms of Use Article is made available in accordance with the publisher's policy and may be subject to US copyright law. Please refer to the publisher's site for terms of use. Frontiers in Heat and Mass Transfer (FHMT), 1, 023001 (2010) Global Digital Central DOI: 10.5098/hmt.v1.2.3001 ISSN: 2151-8629 ENERGY EFFECTIVENESS OF SIMULTANEOUS HEAT AND MASS EXCHANGE DEVICES a a a b a, G. Prakash Narayan , Karan H. Mistry , Mostafa H. Sharqawy , Syed M. Zubair , John H. Lienhard V y aDepartment of Mechanical Engineering, Massachusetts Institute of Technology, Cambridge, USA. bDepartment of Mechanical Engineering, King Fahd University of Petroleum and Minerals, Dhahran, Saudi Arabia. ABSTRACT Simultaneous heat and mass exchange devices such as cooling towers, humidifiers and dehumidifiers are widely used in the power generation, desalination, air conditioning, and refrigeration industries. For design and rating of these components it is useful to define their performance by an effectiveness. In this paper, several different effectiveness definitions that have been used in literature are critically reviewed and an energy based effectiveness which can be applied to all types of heat and mass exchangers is defined. -
Heat Exchanger Design – Part II
ME340A: Prof. Sameer Khandekar http://home.iitk.ac.in/~samkhan ME340A: Refrigeration and Air Conditioning Department of Mechanical Engineering Instructor: Prof. Sameer Khandekar Indian Institute of Technology Kanpur Tel: 7038; e-mail: [email protected] Kanpur 208016 India Heat Exchanger Design – Part II Sameer Sameer Khandekar 1 ME340A: Refrigeration and Air Conditioning Department of Mechanical Engineering Instructor: Prof. Sameer Khandekar Indian Institute of Technology Kanpur Tel: 7038; e-mail: [email protected] Kanpur 208016 India In this lecture… Part I ◉ Types of Heat Exchangers ◉ The Overall Heat Transfer Coefficient ◉ Fouling factor Part II ◉ The Log Mean Temperature Difference Method ◉ Counter-Flow Heat Exchangers ◉ Multipass and Cross-Flow Heat Exchangers: Use of a Correction Factor ◉ The Effectiveness–NTU Method ◉ Selection of Heat Exchangers Sameer Sameer Khandekar 2 Department of Mechanical Engineering Indian Institute of Technology Kanpur 208016 Kanpur India 1 ME340A: Prof. Sameer Khandekar http://home.iitk.ac.in/~samkhan ME340A: Refrigeration and Air Conditioning Department of Mechanical Engineering Instructor: Prof. Sameer Khandekar Indian Institute of Technology Kanpur Tel: 7038; e-mail: [email protected] Kanpur 208016 India Analysis of heat exchangers An engineer often finds himself or herself in a position: 1. to select a heat exchanger (Sizing) that will achieve a specified temperature change in a fluid stream of known mass flow rate - the log mean temperature difference (or LMTD) method. 2. to predict the outlet temperatures of the hot and cold fluid streams in a specified heat exchanger (Rating)- the effectiveness–NTU method. Sameer Sameer Khandekar 3 ME340A: Refrigeration and Air Conditioning Department of Mechanical Engineering Instructor: Prof. -
Calculating the Loads for Liquid Cooling Systems
Calculating the Loads for Liquid Cooling Systems This article presents basic equations for liquid cooling and provides numerical examples on how to calculate the loads in a typical liquid cooling system. When exploring the use of liquid cooling for thermal management, calculations are needed to predict its performance. While it is often assumed that a liquid coolant itself dissipates heat from a component to the ambient, this is not the case. A closed loop liquid cooling system requires a liquid-to-air heat exchanger. Because of its structure, several equations must be calculated to fully understand the performance and behavior of a liquid cooled system. For this article we consider a liquid cooling system as a closed loop system with three major components: cold plate, Figure 1. Closed Loop Liquid Cooling System [1] . heat exchanger and pump. The cold plate is typically made from aluminum or copper, and is attached to the device being cooled. The plate usually has internal fins which transfer Rcp = thermal resistance of the cold plate and TIM heat to the coolant flowing through them. This fluid moves Tw1 = water temperature entering the cold plate from the cold plate to a heat exchanger where its heat is transferred to the ambient air via forced convection. The final In an open loop cooling system, the value of Tw1 is known part of the cooling loop is the pump, which drives the fluid and controlled by the supply system. Calculating Tw1 in a through the loop. closed loop system is more involved. This is because the water temperature is both rising from the power transferred Equation 1, below, was derived to predict the final temperature from the device and dropping while transferring heat to the of the device being cooled [1]. -
Analysis of a Novel Waste Heat Recovery Mechanism for an I.C. Engine
Michigan Technological University Digital Commons @ Michigan Tech Dissertations, Master's Theses and Master's Dissertations, Master's Theses and Master's Reports - Open Reports 2012 Analysis of a novel waste heat recovery mechanism for an I.C. engine Jasdeep S. Condle Michigan Technological University Follow this and additional works at: https://digitalcommons.mtu.edu/etds Part of the Mechanical Engineering Commons Copyright 2012 Jasdeep S. Condle Recommended Citation Condle, Jasdeep S., "Analysis of a novel waste heat recovery mechanism for an I.C. engine", Master's report, Michigan Technological University, 2012. https://doi.org/10.37099/mtu.dc.etds/551 Follow this and additional works at: https://digitalcommons.mtu.edu/etds Part of the Mechanical Engineering Commons ANALYSIS OF A NOVEL WASTE HEAT RECOVERY MECHANISM FOR AN I.C. ENGINE By Jasdeep S. Condle A REPORT SUBMITTED In Partial Fulfillment Of The Requirements For The Degree Of MASTER OF SCIENCE (Mechanical Engineering) MICHIGAN TECHNOLOGICAL UNIVERSITY 2012 COPYRIGHT © JASDEEP S. CONDLE 2012 This report, “Analysis of a Novel Waste Heat Recovery Mechanism for an I.C. Engine,” is hereby approved in partial fulfillment of the requirements for the Degree of MASTER OF SCIENCE IN MECHANICAL ENGINEERING. Department of Mechanical Engineering-Engineering Mechanics Signatures: Report Advisor __________________________________ Scott A. Miers Department Chair __________________________________ William W. Predebon Date _______________________________________ Table of Contents Chapter 1 Introduction.................................................................................................. -
The Property Diagram in Heat Transfer and Its Applications
Article Engineering Thermophysics December 2012 Vol.57 No.35: 46464652 doi: 10.1007/s11434-012-5476-5 SPECIAL TOPICS: The property diagram in heat transfer and its applications CHEN Qun*, XU YunChao & GUO ZengYuan Key Laboratory for Thermal Science and Power Engineering of Ministry of Education, Department of Engineering Mechanics, Tsinghua University, Beijing 100084, China Received May 12, 2012; accepted August 21, 2012 Inspired by the property diagrams in thermodynamics, which distinctly reflect the performance and characteristics of thermody- namic cycles, we establish a state equation for heat motion and introduce a two-dimension property diagram, T-q diagram, in heat transfer to analyze and optimize the performance of heat exchangers, where heat flow is a state parameter for heat motion. Ac- cording to the property diagram, it is convenient to obtain the influences of heat exchanger area, heat capacity rate and flow ar- rangement on the heat transfer performance during the analysis of heat exchangers and their networks. For instance, when analyz- ing the heat exchanger network in a district heating system, it is obvious to find that: if both the heat demand and the indoor air temperature in each branch of the network are the same, the total area of heat exchangers, the flow rate of water and the return water temperature in each branch are all the same; if the indoor air temperatures in different branches are different, the tempera- tures of the waters after flowing through different branches are different, which means that the mixing process of return waters with the same temperature is not an essential requirement to realize the best performance of district heating systems. -
ATS Liquid Cooling Ebook Select Technical Articles on Liquid Cooling and Its Various Roles in the Thermal Management of Electronics
ATS Liquid Cooling eBook Select Technical Articles on Liquid Cooling and its Various Roles in the Thermal Management of Electronics 89-27 Access Road, Norwood, MA 02062 | T: 781.769. 2800 F: 781.769.9979 | www.qats.com © Advanced Thermal Solutions, Inc. 1 Table of Contents Calculating The Loads For A Liquid Cooling System 2 Heat Transfer Analysis of Compact Heat Exchangers Using Standard Curves 4 What Fluids Can Be Used With Liquid Cold Plates in Electronics Cooling Systems 7 Cold Plates and Recirculating Chillers for Liquid Cooling Systems 10 Measuring The Thermal Resistance of Microchannel Cold Plates 13 © Advanced Thermal Solutions, Inc. 2 Calculating The Loads For A Liquid Cooling System This article presents basic equations for liquid cooling and Where: provides numerical examples on how to calculate the loads Tmod = surface temperature of the device being cooled in a typical liquid cooling system. When exploring the use qL= power dissipated by the device of liquid cooling for thermal management, calculations Rcp = thermal resistance of the cold plate and TIM are needed to predict its performance. While it is often Tw1 = water temperature entering the cold plate assumed that a liquid coolant itself dissipates heat from a In an open loop cooling system, the value of Tw1 is known component to the ambient, this is not the case. A closed and controlled by the supply system. Calculating Tw1 in a loop liquid cooling system requires a liquid-to-air heat closed loop system is more involved. This is because the exchanger. Because of its structure, several equations water temperature is both rising from the power transferred must be calculated to fully understand the performance and from the device and dropping while transferring heat to the behavior of a liquid cooled system. -
On the Design of a Reactor for High Temperature Heat Storage by Means of Reversible Chemical Reactions
On the Design of a Reactor for High Temperature Heat Storage by Means of Reversible Chemical Reactions Patrick Schmidt Master of Science Thesis KTH School of Industrial Engineering and Management Energy Technology EGI-2011-117MSC EKV 862 Division of Energy Technology SE-100 44 STOCKHOLM Abstract This work aims on the investigation of factors influencing the discharge characteristics of a heat storage system, which is based on the reversible reaction system of Ca(OH)2 and CaO. As storage, a packed bed reactor with embedded plate heat exchanger for indirect heat transfer is considered. The storage system was studied theoretically by means of finite element analysis of a corresponding mathematical model. Parametric studies were carried out to determine the influence of reactor design and operational mode on storage discharge. Analysis showed that heat and gas transport through the reaction bed as well as the heat capacity rate of the heat transfer fluid affect the discharge characteristics to a great extent. To obtain favourable characteristics in terms of the fraction of energy which can be extracted at rated power, a reaction front perpendicular to the flow direction of the heat transfer fluid has to develop. Such a front arises for small bed dimensions in the main direction of heat transport within the bed and for low heat capacity rates of the heat transfer fluid. Depending on the design parameters, volumetric energy densities of up to 309 kWh/m3 were calculated for a storage system with 10 kW rated power output and a temperature increase of the heat transfer fluid of 100 K. -
Calculation Method for Fin-And-Tube Heat Exchangers Operating with Nonuniform Airflow
Energy and Sustainability VIII 13 CALCULATION METHOD FOR FIN-AND-TUBE HEAT EXCHANGERS OPERATING WITH NONUNIFORM AIRFLOW PAOLO BLECICH, ANICA TRP & KRISTIAN LENIĆ Faculty of Engineering, University of Rijeka, Croatia ABSTRACT This paper presents a new calculation method for fin-and-tube heat exchangers operating with nonuniform airflow. The calculation method consists of discretizing the heat exchanger tubes into tube elements and applying mass and energy conservation equations. The calculation method is capable of predicting local and overall values of thermal effectiveness, heat transfer rates and fluid outlet temperatures in fin-and-tube heat exchangers subject to airflow nonuniformity. The results of the tube element method are compared against experimental data, and good accordance has been achieved between predicted and measured values. Experimental data is collected for fin-and-tube heat exchangers placed inside an open wind tunnel, where airflow nonuniformity is generated by partially obstructing the entrance cross section. This study revealed that airflow nonuniformity causes effectiveness deterioration in fin-and-tube heat exchangers. The exact value of effectiveness deterioration depends on the heat exchanger dimensionless groups – the number of heat transfer units (NTU) and the heat capacity rate ratio (C*) – as well as on the intensity and orientation of the airflow nonuniformity. The design of the tube-side fluid circuitry, which affects the heat exchanger flow arrangement, also plays a role in the effectiveness deterioration. The tube element method revealed that the effectiveness deterioration increases with the intensity of airflow nonuniformity. For an observed nonuniform airflow profile, the effectiveness deterioration is maximum in heat exchangers with a balanced heat capacity rate ratio (C* = 1) and minimum in evaporators and condensers (C* = 0). -
Heat Transfer Coefficient Estimation and Performance Evaluation Of
processes Article Heat Transfer Coefficient Estimation and Performance Evaluation of Shell and Tube Heat Exchanger Using Flue Gas Xuejun Qian 1,2,* , Seong W. Lee 1,2 and Yulai Yang 1,2 1 Industrial and Systems Engineering Department, Morgan State University, 1700 East Cold Spring Lane, Baltimore, MD 21251, USA; [email protected] (S.W.L.); [email protected] (Y.Y.) 2 Center for Advanced Energy Systems and Environmental Control Technologies, School of Engineering, Morgan State University, 1700 East Cold Spring Lane, Baltimore, MD 21251, USA * Correspondence: [email protected]; Tel.: +1-443-885-2772 Abstract: In the past few decades, water and air were commonly used as working fluid to evaluate shell and tube heat exchanger (STHE) performance. This study was undertaken to estimate heat transfer coefficients and evaluate performance in the pilot-scale twisted tube-based STHE using the flue gas from biomass co-combustion as working fluid. Theoretical calculation along with experimental results were used to calculate the specific heat of flue gas. A simplified model was then developed from the integration of two heat transfer methods to predict the overall heat transfer coefficient without tedious calculation of individual heat transfer coefficients and fouling factors. Performance including water and trailer temperature, heat load, effectiveness, and overall heat transfer coefficient were jointly investigated under variable operating conditions. Results indicated that the specific heat of flue gas from co-combustion ranging between 1.044 and 1.338 kJ/kg·K while specific heat was increased by increasing flue gas temperature and decreasing excess air ratio. The developed mathematical model was validated to have relatively small errors to predict the overall heat transfer coefficient. -
NTU Method Wikipedia NTU Method from Wikipedia, the Free Encyclopedia
12/31/2016 NTU method Wikipedia NTU method From Wikipedia, the free encyclopedia The Number of Transfer Units (NTU) Method is used to calculate the rate of heat transfer in heat exchangers (especially counter current exchangers) when there is insufficient information to calculate the LogMean Temperature Difference (LMTD). In heat exchanger analysis, if the fluid inlet and outlet temperatures are specified or can be determined by simple energy balance, the LMTD method can be used; but when these temperatures are not available The NTU or The Effectiveness method is used. To define the effectiveness of a heat exchanger we need to find the maximum possible heat transfer that can be hypothetically achieved in a counterflow heat exchanger of infinite length. Therefore one fluid will experience the maximum possible temperature difference, which is the difference of (The temperature difference between the inlet temperature of the hot stream and the inlet temperature of the cold stream). The method proceeds by calculating the heat capacity rates (i.e. mass flow rate multiplied by specific heat) and for the hot and cold fluids respectively, and denoting the smaller one as . A quantity: is then found,where is the maximum heat that could be transferred between the fluids per unit time. must be used as it is the fluid with the lowest heat capacity rate that would, in this hypothetical infinite length exchanger, actually undergo the maximum possible temperature change. The other fluid would change temperature more slowly along the heat exchanger length. The method, at this point, is concerned only with the fluid undergoing the maximum temperature change. -
Introduction to Pinch Technology
Downloaded from orbit.dtu.dk on: Sep 25, 2021 Introduction to Pinch Technology Rokni, Masoud Publication date: 2016 Document Version Peer reviewed version Link back to DTU Orbit Citation (APA): Rokni, M. (2016). Introduction to Pinch Technology. Technical University of Denmark. General rights Copyright and moral rights for the publications made accessible in the public portal are retained by the authors and/or other copyright owners and it is a condition of accessing publications that users recognise and abide by the legal requirements associated with these rights. Users may download and print one copy of any publication from the public portal for the purpose of private study or research. You may not further distribute the material or use it for any profit-making activity or commercial gain You may freely distribute the URL identifying the publication in the public portal If you believe that this document breaches copyright please contact us providing details, and we will remove access to the work immediately and investigate your claim. Introduction to Pinch Technology Division of Energy Section Masoud Rokni Technical University of Denmark [email protected] DTU Building 402, 1st Floor DK-2800 KGS, Lyngby July 2006 Revised April 2016 1 Introduction to Pinch Technology 1. Introduction The demand for effective usage of energy processes is increasing and nowadays every process engineer is facing the challenge to seek answers to the questions related to their process energy patterns. Below the questions that frequently may be asked are listed: