The Effect of Lignosulfonates on the Floatability of Molybdenite And
Total Page:16
File Type:pdf, Size:1020Kb
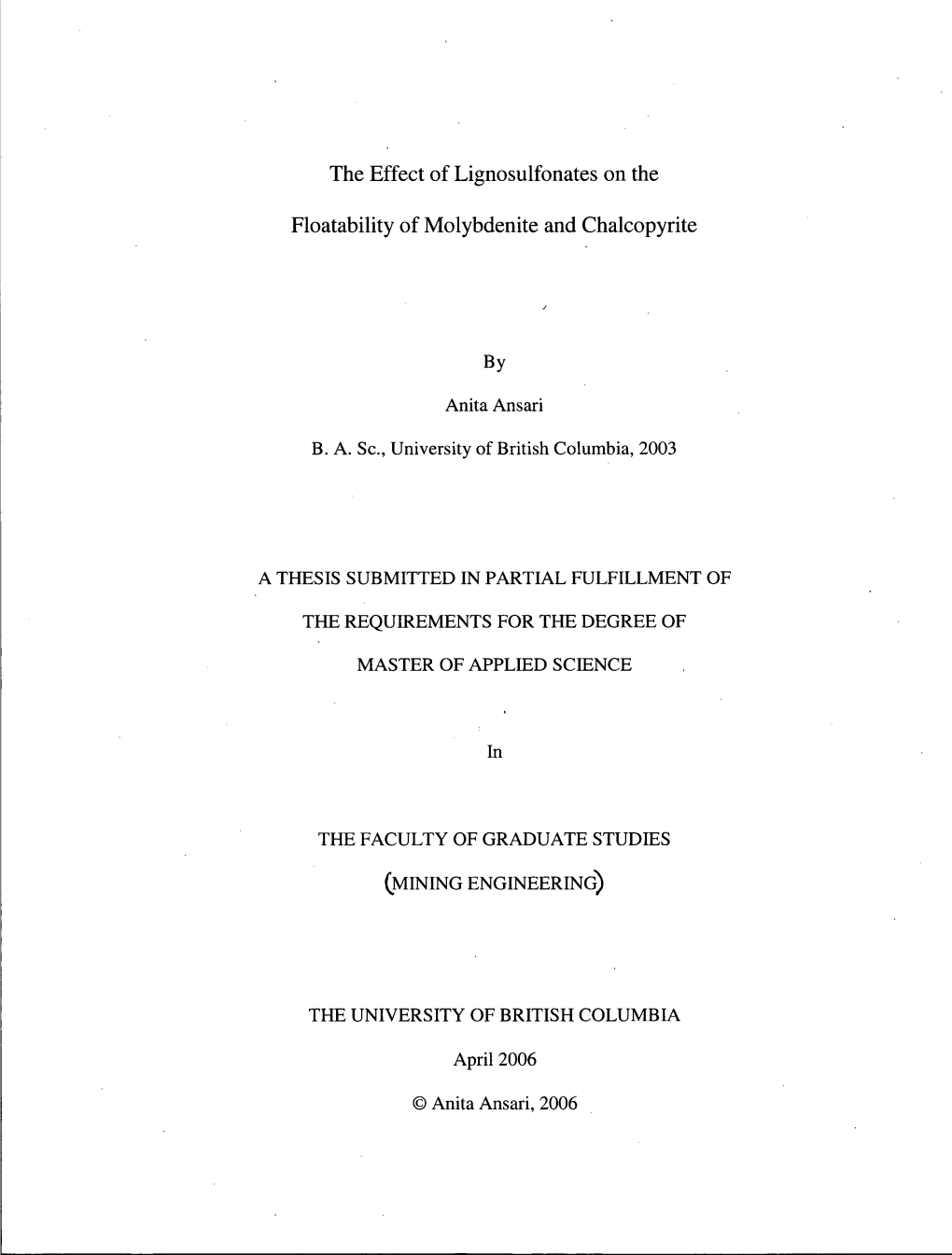
Load more
Recommended publications
-
Optimization of the Continuous Analysis Pearl-Benson Method for Lignosulfonates
AN ABSTRACT OF THE THESIS OF ROGER LEE BLAINE for the DOCTOR OF PHILOSOPHY (Name) (Degree) in CHEMISTRY presented on January 21, 1969 (Major) (Date) Title: OPTIMIZATION OF THE CONTINUOUSANALYSIS PEARL- BENSON METHOD FOR LIGNOSULFONATES Redacted for Privacy Abstract approved Dr. Hty'ry Freund A procedure is described for the optimizationof a previously described continuous analysis adaptation ofthe Pearl-Benson or nitroso method for estimation of spentsulfite liquor (SSL) or ligno- sulfonates.The optimized procedure has a responsetime of 6. 5 minutes.In order to monitor samples whoseSSL concentration is between 0 and 10 ppm, a long path length,dual beam, flow through colorimeter was developed.The colorimeter has a range of 0.94 absorbance units for a 10 cm cuvette length,and has a readout which expresses the sample concentrationdirectly in millivolts. Both the continuous analysis chemicalthanipulation system and the colorimeter are packaged as portable units. An empirical equation is obtained for the response curveof continuous analyzers.This equation permits simulation of the con- tinuous analyzer response in both amathematical form and on an analog computer.Examination of the electrical analog leads to information about the response of continuous analysis apparatus toa' variety of input signals and provides an approach to figures ofmerit for comparison of continuous analysis systems. An electronic method is illustrated for predicting the steady state value of a con- tinuous analysis apparatus long before that steady state condition is -
Systematic Review on Isolation Processes for Technical Lignin
processes Review Systematic Review on Isolation Processes for Technical Lignin Marlene Kienberger *, Silvia Maitz, Thomas Pichler and Paul Demmelmayer Institute of Chemical Engineering and Environmental Technology, Graz University of Technology, Inffeldgasse 25c, A-8010 Graz, Austria; [email protected] (S.M.); [email protected] (T.P.); [email protected] (P.D.) * Correspondence: [email protected]; Tel.: +43-031-6873-7484 Abstract: Technologies for the isolation of lignin from pulping process streams are reviewed in this article. Based on published data, the WestVaco process, the LignoBoost process, the LigoForce SystemTM and the SLRP process are reviewed and discussed for the isolation of lignin from Kraft black liquor. The three new processes that have now joined the WestVaco process are compared from the perspective of product quality. Further, isolation processes of lignosulfonates from spent sulfite liquor are reviewed. The limitation for this review is that data are only available from lab scale and pilot scale experiments and not from industrial processes. Key output of this paper is a technology summary of the state of the art processes for technical lignins, showing the pros and cons of each process. Keywords: Kraft lignin; lignosulfonates; lignin isolation processes; technical lignin 1. Introduction Citation: Kienberger, M.; Maitz, S.; After cellulose, lignin is the second most abundant biopolymer worldwide. Lignins are Pichler, T.; Demmelmayer, P. non-toxic and renewable, and hence may play an essential role during the change-over from Systematic Review on Isolation a fossil-based to a bio-based economy. The value-added application of technical lignin not Processes for Technical Lignin. -
Overview of Lignin Applications
Lignin Applications Brief Overview Lignin Applications: Concrete Low lllevels of lignin and modfdifie d lignin can yield • High performance concrete strength aid • Concrete grinding aid • Reduce damage of building external wall caused by moisture and acid rain • Set retarder for a cement composition • Sulfonated lignin contributes higher adsorption properties and zeta potential to cement particles, and hence shows better dispersion effect to the cement matrix. • Select lignins can improve the compressive strength of cement pastes Lignin Applications: Antioxidant • Liiignin acts as free radica l scavengers •Lignin provides thermal protection to: • Styrene /butadiene/rubber polymer • RbbRubber • Polypropylene • polycaprolactam • Lignin’s natural antioxidant properties provides use in cosmetic and topical formulations. • Lignin sulfonate‐containing cosmetic compositions have been developed for decorative use on skin Lignin Applications: Asphalt • CkCrack filling composiiition iliinvolving quaternary ammonium salt, aliphatic amine, lignin amine, imidazoline, and amide. • Water stability of an asphalt mixture can be improved by adding 03%0.3% lign in fibers • Asphalt‐emulsifying agent containing SW Na lignin salt with an av. mol. wt. of 200‐100,000 (Na lignosulfonate or Na lignophosphate, and the lignin is that broad‐leaf pine or needle‐leaf pine) has the proper HLB value, slow demulsification speed, proper frothing ability, and strong foam stability. • Lignin amine additive has been shown to provide a warm mix additive that can modify the combination state of asphalt and stone material surface; modifying the fluidity; and decrease production cost of the asphalt mixtures Lignin Applications: Carbon Fiber and Related • Native lignin or industrial lignin can be used for carbon fibers • Carbon nanotubes have been made from lignin/lignosulfonates. -
A Review on the Lignin Biopolymer and Its Integration in the Elaboration of Sustainable Materials
sustainability Review A Review on the Lignin Biopolymer and Its Integration in the Elaboration of Sustainable Materials Francisco Vásquez-Garay 1,*, Isabel Carrillo-Varela 2, Claudia Vidal 2, Pablo Reyes-Contreras 1 , Mirko Faccini 1 and Regis Teixeira Mendonça 2,3 1 Centro de Excelencia en Nanotecnología (CEN), Santiago 7500724, Chile; [email protected] (P.R.-C.); [email protected] (M.F.) 2 Laboratorio de Recursos Renovables, Centro de Biotecnología, Universidad de Concepción, Concepción 4030000, Chile; [email protected] (I.C.-V.); [email protected] (C.V.); [email protected] (R.T.M.) 3 Facultad de Ciencias Forestales, Casilla 160-C, Universidad de Concepción, Concepción 4030000, Chile * Correspondence: [email protected] Abstract: Lignin is one of the wood and plant cell wall components that is available in large quantities in nature. Its polyphenolic chemical structure has been of interest for valorization and industrial application studies. Lignin can be obtained from wood by various delignification chemical processes, which give it a structure and specific properties that will depend on the plant species. Due to the versatility and chemical diversity of lignin, the chemical industry has focused on its use as a viable alternative of renewable raw material for the synthesis of new and sustainable biomaterials. However, its structure is complex and difficult to characterize, presenting some obstacles to be integrated into mixtures for the development of polymers, fibers, and other materials. The objective of this review is to present a background of the structure, biosynthesis, and the main mechanisms of lignin recovery Citation: Vásquez-Garay, F.; from chemical processes (sulfite and kraft) and sulfur-free processes (organosolv) and describe the Carrillo-Varela, I.; Vidal, C.; different forms of integration of this biopolymer in the synthesis of sustainable materials. -
Lignin and Lignosulfonate Characterization with SEC-MALS and FFF-MALS Christoph Johann, Ph.D., Wyatt Technology
WHITE PAPER WP2303: Lignin and lignosulfonate characterization with SEC-MALS and FFF-MALS Christoph Johann, Ph.D., Wyatt Technology Introduction • Analytical SEC combined with UV or RI detection has been widely applied. But because lignin standards Lignin is the second most abundant natural polymer and are not available, and lignin can be highly branched, a major constituent of green plants. In contrast to cellu- accurate column calibration is not feasible. lose, it has no industrial/technical use except incinera- tion for energy production. In view of the push for • Universal Calibration (UC) using SEC with a differen- sustainability, efforts to find new ways for utilization of tial viscometer is an improvement over standard lignin have been increasing and more research is de- analytical SEC, but it does not provide reliable molar voted to finding productive applications. mass information. This is because of 1) branching (UC is only defined for linear polymers) and 2) non- The most fundamental property of biopolymers is their ideal interactions of this chemically heterogeneous molar mass distribution. Originally, lignin was assumed molecule with the SEC column matrix (retention is to be a very large macromolecule that provides support not based purely on diffusion). for cellulose in cell walls; then there seemed to be evidence that it is merely an oligomer consisting of a few • SEC-MALS is generally preferable for polymer analy- monomer units. A significant breakthrough in the molar sis since it is an absolute method that does not rely mass characterization of lignin and its derivative lignosul- on calibration standards or assumptions about con- fonate was achieved by coupling the DAWN online formation and ideal column interactions. -
Metal-Free Aqueous Flow Battery with Novel Ultrafiltered Lignin As
Research Article Cite This: ACS Sustainable Chem. Eng. XXXX, XXX, XXX−XXX pubs.acs.org/journal/ascecg Metal-Free Aqueous Flow Battery with Novel Ultrafiltered Lignin as Electrolyte † † ‡ † Alolika Mukhopadhyay, Jonathan Hamel, Rui Katahira, and Hongli Zhu*, † Department of Mechanical and Industrial Engineering, Northeastern University, 360 Huntington Avenue, 334 Snell Engineering, Boston, Massachusetts 02115, United States ‡ National Renewable Energy Laboratory, Denver West Parkway, Golden, Colorado 80401, United States *S Supporting Information ABSTRACT: As the number of generation sources from intermittent renewable technologies on the electric grid increases, the need for large-scale energy storage devices is becoming essential to ensure grid stability. Flow batteries offer numerous advantages over conventional sealed batteries for grid storage. In this work, for the first time, we investigated lignin, the second most abundant wood derived biopolymer, as an anolyte for the aqueous flow battery. Lignosulfonate, a water-soluble derivative of lignin, is environmentally benign, low cost and abundant as it is obtained from the byproduct of paper and biofuel manufacturing. The lignosulfonate utilizes the redox chemistry of quinone to store energy and undergoes a reversible redox reaction. Here, we paired lignosulfonate with − ffi Br2/Br , and the full cell runs e ciently with high power density. Also, the large and complex molecular structure of lignin considerably reduces the electrolytic crossover, which ensures very high capacity retention. The flowcell was able to achieve current densities of up to 20 mA/cm2 and charge polarization resistance of 15 ohm cm2. This technology presents a unique opportunity for a low-cost, metal-free flow battery capable of large-scale sustainable energy storage. -
United States Patent (15) 3,644,167 Mowry (45) Feb
United States Patent (15) 3,644,167 Mowry (45) Feb. 22, 1972 3,180,787 4/1965 Adams................................... 162,163 54). PREPARATION OF CORRUGATING 3,202,570 8/1965 Videon. ... 162/181 X LNERBOARD 3,223,543 12/1965 Savina................................ 162/175 X (72) Inventor: Warren E. Mowry, Bellingham, Wash. 3,231,559 1/1966 Wheeler et al.... ... 162/175 UX . 73) Assignee: Georgia-Pacific Corporation, Portland, 3,300,360 1/1967 Williams et al.................... 117/156 X 3,305,435 2/1967 Williston et al.... ... 162/63 X Oreg. 3,398,047 8/1968 Michalski....... ... 162/163 X (22) Filed: July 14, 1969 Primary Examiner-William D. Martin (21) Appl. No.: 841,578 Assistant Examiner-M. R. Lusignan Attorney-Peter P. Chevis 52 U.S.C......... a w w as a 4 & as w w w 8 161/125, 117/156, 117/157, 156/307, 156/318, 156/328, 161/268 57 m ABSTRACT 511 Int. Cl.........................................D21h1/04, D21h 3/28 58 Field of Search.................. 117/156, 157, 158; 156/307, A corrugating inerboard is prepared from a paperboard made 156/327,328,332,336,318; 161/137,238,246, from waste paper fiber by surface sizing the paperboard with 266, 125, 268; 162/163, i75, 181 A an aqueous solution of 5 to 30 weight percent solids concen tration of an alkali metal borate treated mixture of lignosul 56 References Cited fonate and starch. The starch is present in the mixture in an amount of from 15 to 25 weight percent of the lignosulfonate UNITED STATES PATENTS solids and the mixture is treated with the alkali metal borate in 2,102,937 12/1937 Bauer................................... -
Characterization of Wood-Based Industrial Biorefinery
Waste and Biomass Valorization (2020) 11:5835–5845 https://doi.org/10.1007/s12649-019-00878-5 ORIGINAL PAPER Characterization of Wood‑based Industrial Biorefnery Lignosulfonates and Supercritical Water Hydrolysis Lignin Venla Hemmilä1 · Reza Hosseinpourpia1 · Stergios Adamopoulos1 · Arantxa Eceiza2 Received: 29 March 2019 / Accepted: 11 November 2019 / Published online: 14 November 2019 © The Author(s) 2019 Abstract Understanding the properties of any particular biorefnery or pulping residue lignin is crucial when choosing the right lignin for the right end use. In this paper, three diferent residual lignin types [supercritical water hydrolysis lignin (SCWH), ammonium lignosulfonate (A-LS), and sodium lignosulfonate (S-LS)] were evaluated for their chemical structure, thermal properties and water vapor adsorption behavior. SCWH lignin was found to have a high amount of phenolic hydroxyl groups and the highest amount of β-O-4 linkages. Combined with a low ash content, it shows potential to be used for conversion into aromatic or platform chemicals. A-LS and S-LS had more aliphatic hydroxyl groups, aliphatic double bonds and C=O structures. All lignins had available C 3/C5 positions, which can increase reactivity towards adhesive precursors. The glass transition temperature (Tg) data indicated that the SCWH and S-LS lignin types can be suitable for production of carbon fbers. Lignosulfonates exhibited considerable higher water vapor adsorption as compared to the SCWH lignin. In conclu- sion, this study demonstrated that the SCWH difered greatly from the lignosulfonates in purity, chemical structure, thermal stability and water sorption behavior. SCWH lignin showed great potential as raw material for aromatic compounds, carbon fbers, adhesives or polymers. -
Evaluating Lignosulfonates Potential As Legume Hay and Silage Preservatives
The University of Maine DigitalCommons@UMaine Electronic Theses and Dissertations Fogler Library Fall 12-20-2020 Evaluating Lignosulfonates Potential as Legume Hay and Silage Preservatives Angela Yenny Leon-Tinoco [email protected] Follow this and additional works at: https://digitalcommons.library.umaine.edu/etd Part of the Animal Sciences Commons Recommended Citation Leon-Tinoco, Angela Yenny, "Evaluating Lignosulfonates Potential as Legume Hay and Silage Preservatives" (2020). Electronic Theses and Dissertations. 3367. https://digitalcommons.library.umaine.edu/etd/3367 This Open-Access Thesis is brought to you for free and open access by DigitalCommons@UMaine. It has been accepted for inclusion in Electronic Theses and Dissertations by an authorized administrator of DigitalCommons@UMaine. For more information, please contact [email protected]. EVALUATING LIGNOSULFONATES POTENTIAL AS LEGUME HAY AND SILAGE PRESERVATIVES By Angela Yenny Leon Tinoco M. Sc. Universidad Nacional Agraria La Molina, 2015 A THESIS Submitted in Partial Fulfillment of the Requirements for the Degree of Master of Science (in Animal Science) The Graduate School The University of Maine December 2020 Advisory Committee: Juan Romero, Assistant Professor of Animal Nutrition, Advisor Seanna Annis, Associate Professor of Mycology Anne Lichtenwalner, Associate Professor of Animal and Veterinary Sciences Brian Perkins, Research Assistant Professor of Food Science Denise Skonberg, Professor of Food Science EVALUATING LIGNOSULFONATES POTENTIAL AS LEGUME HAY AND SILAGE PRESERVATIVES By Angela Yenny Leon Tinoco Thesis advisor: Dr. Juan Romero An Abstract of the Thesis Presented In Partial Fulfillment of the Requirements for the Degree of Master of Science (in Animal Science) December 2020 The aim was to screen and optimize low-cost lignosulfonates (LST) as legume silage and hay preservatives to decrease losses of DM and nutritive value due to spoilage. -
Effect of Raw Material and Kraft Pulping Conditions on Characteristics of Dissolved Lignin
KTH 2014 Effect of raw material and Kraft Pulping Conditions on Characteristics of Dissolved Lignin Degree Project in Pulp technology KF274X Antonia Svärd Supervisors: Assistant professor Elisabet Brännvall and PhD Olena Sevastyanova Examiner: Professor Mikael Lindström Abstract Lignin is one of the main components in wood and during the chemical pulping processes it is degraded and dissolved into the cooking liquor. The current challenge is to meet the need for energy and raw materials, and reform to a more environmentally sustainable society, so there is a great interest in using kraft lignin as a raw material for energy, materials and as source of chemicals. ) To meet this goal, it is essential to obtain kraft lignin with desirable properties. The overall goal of this master thesis project was to understand the relationship between kraft process conditions and the structure and properties of the dissolved lignin. Wood chips of pine, spruce and eucalyptus were pulped with the kraft process at constant temperature and similar alkali charge and sulphidity to different cooking times. From the collected black liquor, the dissolved kraft lignin was precipitated by acidification with sulphuric acid. It was observed that longer cooking time yields more precipitated material, where pine gave the highest yield. There was a significant difference in colour of the precipitated between eucalyptus and the softwood samples. Some the characteristic properties of the collected samples were investigated. Results from the Klason lignin and ionic chromatography showed variation in lignin and carbohydrate composition depending on raw material and cooking time. This was also indicated by results lignin carbohydrate ratio from analytical pyrolysis. -
United States Patent Office Patented Apr
3,180,787 United States Patent Office Patented Apr. 27, 1965 2 not suitable. In general, polyethylene polyamines having 3,180,787 PROCESS FOR MAKENGHGH FLEXURAL molecular weights in excess of 150 are satisfactory, and STRENGTH PAPER those ranging in molecular weight from 500 to 1000 are James W. Adams, Schofield, Wis, assignor to American preferred. Can Company, New York, N.Y., a corporation of New 5 Lignosulfonates satisfactory for use in my invention Jersey may be obtained by isolation from spent sulfite liquor by No Drawing. Filed May 20, 1959, Ser. No. 844,409 any of several means. For example, treatment of spent 2 Claims. (C.162-163) sulfite liquor with lime according to the Howard process described in the United States Patents Re. 18,268, Decem This invention relates to a method for increasing the 10 ber 1, 1931; 1,856,558, May 3, 1932 and 1,924,361, Au flexural strength of fibrous cellulosic products by incorpo gust 29, 1933, results in the recovery of lignin material as rating therein a polyethylene polyamine lignosulfonate basic calcium lignosulfonate. This water-insoluble ma and to the improved fibrous products obtained thereby. terial may be converted to the water-soluble lignosulfonic Stiffness, without accompanying brittleness, is a desir acid or soluble salt derivative such as the ammonium or able attribute of paperboard products such as cartons 5 alkali metal salt by known methods. These water solu used in the protective packaging of various commodities. ble compounds are suitable for use in our invention. Such cartons must have adequate stiffness to insure proper I have also found that separation of the lignosulfonate operation on packaging machinery, to retain the packaged fraction from spent sulfite liquor is not a necessary pre product without undue deformation of the package and requisite to its use in my invention, since the whole spent to give the customer a feeling of sturdiness and strength 20 sulfite liquor may be economically utilized in my proc of package rather than flimsiness and shoddiness. -
Investigation of a Two-Stage Steam/Organosolv Pretreatment Approach for the Fractionation of Softwood Biomass
Investigation of a two-stage steam/organosolv pretreatment approach for the fractionation of softwood biomass by Mandy Lin B.Sc., The University of British Columbia, 2013 A THESIS SUBMITTED IN PARTIAL FULFILLMENT OF THE REQUIREMENTS OF THE DEGREE OF MASTER OF SCIENCE in THE FACULTY OF GRADUATE AND POSTDOCTORAL STUDIES (Forestry) THE UNIVERSITY OF BRITISH COLUMBIA (Vancouver) December 2016 © Mandy Lin, 2016 Abstract In order to improve the economic viability of a bioconversion process it would be extremely beneficial to maximize the recovery of all of the lignocellulosic components while enhancing enzyme accessibility to the cellulosic component. Wood residue derived pellets are already a prominent Canadian commodity and the existing supply-chain produces a high density, low moisture feedstock suitable for mass collection and transport. However, pellets are almost exclusively used for combustion and not as a possible biorefinery feedstock. As a result, there is limited information on the influence of the pelletization process (e.g. grinding, drying, compressing) on the susceptibility of pellets, as opposed to chips, to the various pretreatment, fractionation and cellulose hydrolysis steps that are components of a typical bioconversion process. The work described in the thesis assessed the potential of a two-stage steam/organosolv pretreatment process to fractionate and isolate the hemicellulose and lignin components from softwood pellets, yielding a more accessible, cellulose-rich substrate. Various steam pretreatment conditions were compared for their ability to enhance hemicellulose solubilisation while minimizing lignin condensation (first-stage), to improve subsequent organosolv delignification (second-stage). Carbocation scavengers were compared for their ability to minimize lignin condensation during either stage.