Silver Nanowire Coated Threads for Electrically Conductive Textiles
Total Page:16
File Type:pdf, Size:1020Kb
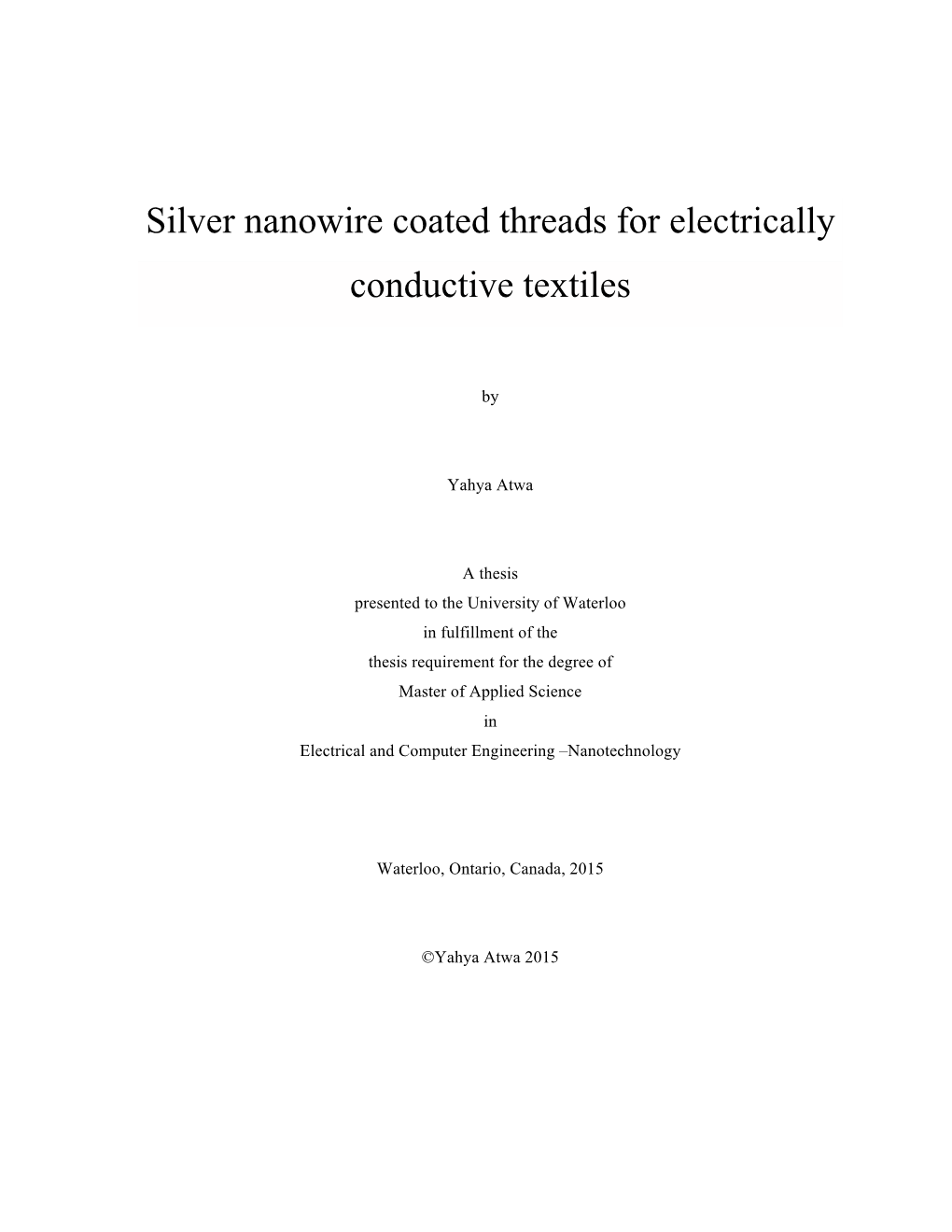
Load more
Recommended publications
-
Integration of Conductive Materials with Textile Structures, an Overview
sensors Review Integration of Conductive Materials with Textile Structures, an Overview Granch Berhe Tseghai 1,2,3,* , Benny Malengier 1 , Kinde Anlay Fante 2 , Abreha Bayrau Nigusse 1,3 and Lieva Van Langenhove 1 1 Department of Materials, Textiles and Chemical Engineering, Ghent University, 9000 Gent, Belgium; [email protected] (B.M.); [email protected] (A.B.N.); [email protected] (L.V.L.) 2 Jimma Institute of Technology, Jimma University, P.O. Box 378 Jimma, Ethiopia; [email protected] 3 Ethiopian Institute of Textile and Fashion Technology, Bahir Dar University, 6000 Bahir Dar, Ethiopia * Correspondence: [email protected]; Tel.: +32-465570635 Received: 5 November 2020; Accepted: 1 December 2020; Published: 3 December 2020 Abstract: In the last three decades, the development of new kinds of textiles, so-called smart and interactive textiles, has continued unabated. Smart textile materials and their applications are set to drastically boom as the demand for these textiles has been increasing by the emergence of new fibers, new fabrics, and innovative processing technologies. Moreover, people are eagerly demanding washable, flexible, lightweight, and robust e-textiles. These features depend on the properties of the starting material, the post-treatment, and the integration techniques. In this work, a comprehensive review has been conducted on the integration techniques of conductive materials in and onto a textile structure. The review showed that an e-textile can be developed by applying a conductive component on the surface of a textile substrate via plating, printing, coating, and other surface techniques, or by producing a textile substrate from metals and inherently conductive polymers via the creation of fibers and construction of yarns and fabrics with these. -
PRINTING CONDUCTIVE INK TRACKS on TEXTILE MATERIALS TAN SIUN CHENG a Project Report Submitted in Partial Fulfillment of the Requ
View metadata, citation and similar papers at core.ac.uk brought to you by CORE provided by UTHM Institutional Repository i PRINTING CONDUCTIVE INK TRACKS ON TEXTILE MATERIALS TAN SIUN CHENG A project report submitted in partial fulfillment of the requirement for the award of the Degree of Master of Mechanical Engineering Faculty of Mechanical and Manufacturing Engineering Universiti Tun Hussein Onn Malaysia July 2015 v ABSTRACT Textile materials with integrated electrical features are capable of creating intelligent articles with wide range of applications such as sports, work wear, health care, safety and others. Traditionally the techniques used to create conductive textiles are conductive fibers, treated conductive fibers, conductive woven fabrics and conductive ink. The technologies to print conductive ink on textile materials are still under progress of development thus this study is to investigate the feasibility of printing conductive ink using manual, silk screen printing and on-shelf modified ink jet printer. In this study, the two points probe resistance test (IV Resistance Test) is employed to measure the resistance for all substrates. The surface finish and the thickness of the conductive inks track were measured using the optical microscope. The functionality of the electronics structure printed was tested by introducing strain via bending test to determine its performance in changing resistance when bent. It was found that the resistance obtained from manual method and single layer conductive ink track by silkscreen process were as expected. But this is a different case for the double layer conductive ink tracks by silkscreen where the resistance acquired shows a satisfactory result as expected. -
Intelligent-Textiles-And-Clothing.Pdf
240x159x24Pantone648C&722C 32mm WOODHEAD PUBLISHING IN TEXTILES WOODHEAD PUBLISHING IN TEXTILES WheOODHEAD use of intelligent textiles PUBLISHING in clothing is an exciting IN new field TEXTILES with wide-ranging Intelligenttextilesandclothing WOODHEAD PUBLISHING IN TEXTILES Tapplications. Intelligent textiles and clothing summarises some of main types of intelligenttextilesandtheiruses. Part I of the book reviews phase change materials (PCMs), their role in thermal regulationandwaystheycanbeintegratedintooutdoorandothertypesofclothing.The secondpartdiscussesshapememorymaterials(SMMs)andtheirapplicationsinmedical textiles, clothing and composite materials. Part III deals with chromic (colour change) andconductivematerialsandtheiruseassensorswithinclothing.Thefinalpartlooksat currentandpotentialapplications,includingworkwearandmedicalapplications. Withitsdistinguishededitorandinternationalteamofcontributors,Intelligenttextiles andclothingwillbeanessentialguidefortextilemanufacturersinsuchareasasspecialist clothing(forexampleprotective,sportsandoutdoorclothing)aswellasmedicaltextiles. DrHeikkiMattilaisProfessorofTextileandClothingTechnologyatTampereUniversity ofTechnology,Finland. Intelligenttextiles andclothing WoodheadPublishingLtd CRCPressLLC Mattila AbingtonHall 6000BrokenSoundParkway,NW Abington Suite300,BocaRaton CambridgeCB16AH FL33487 England USA www.woodheadpublishing.com CRCordernumberWP9099 EditedbyH.Mattila WoodheadPublishing CRCPress ii Related titles: Smart fibres, fabrics and clothing (ISBN-13: 978-1-85573-546-0; ISBN-10: 1-85573-546-6) This important book provides a guide to the fundamentals and latest developments in smart technology for textiles and clothing. -
Polypyrrole Coated Nylon Lycra Fabric As Stretchable Electrode for Supercapacitor Applications Binbin Yue University of Wollongong
University of Wollongong Research Online Australian Institute for Innovative Materials - Papers Australian Institute for Innovative Materials 2012 Polypyrrole coated nylon lycra fabric as stretchable electrode for supercapacitor applications Binbin Yue University of Wollongong Caiyun Wang University of Wollongong, [email protected] Xin Ding Donghua University, China Gordon G. Wallace University of Wollongong, [email protected] Publication Details Yue, B, Wang, C, Ding, X & Wallace, GG (2012), Polypyrrole coated nylon lycra fabric as stretchable electrode for supercapacitor applications, Electrochimica Acta, 68, pp. 18-24. Research Online is the open access institutional repository for the University of Wollongong. For further information contact the UOW Library: [email protected] Polypyrrole coated nylon lycra fabric as stretchable electrode for supercapacitor applications Abstract Wearable electronics offer the combined advantages of both electronics and fabrics. Being an indispensable part of these electronics, lightweight, stretchable and wearable power sources are strongly demanded. Here we describe a daily-used nylon lycra fabric coated with polypyrrole as electrode for stretchable supercapacitors. Polypyrrole was synthesized on the fabric via a simple chemical polymerization process with ammonium persulfate (APS) as an oxidant and naphthalene-2,6-disulfonic acid disodium salt (Na2NDS) as a dopant. This material was characterized with FESEM, FTIR, tensile stress, and studied as a supercapacitor electrode in 1.0 M NaCl. This -
The Application Wearable Thermal Textile Technology in Thermal-Protection Applications
Latest Trends in Textile and L UPINE PUBLISHERS Fashion Designing Open Access DOI: 10.32474/LTTFD.2018.01.000106 ISSN: 2637-4595 Research Article The Application Wearable Thermal Textile Technology in Thermal-Protection Applications Yang Chenxiao and Li Li* The Hong Kong Polytechnic University, Hong Kong Received: January 03, 2018; Published: January 20, 2018 *Corresponding author: Li Li, The Hong Kong Polytechnic University, The institute of Textiles and Clothing, Hong Kong Abstract The needs for better thermal protection exist in various fields of our life, like the better thermal treatment, outside chill sports field and developed.freezing working This article condition reviews etc. However,the relevant the wearable traditional thermal passive textile thermal technology insulated by clothing utilizing is theinsufficient, latest conductive too blocky textile and heavymaterials to constrain in three the movement of wearers and uncomforted to wear. Thus, an innovative light, flexible and active wearable thermal protection needs to be developing levels: the fiber level, the yarn level and the fabric level, to provide more possibilities for new products development in various fields,Keywords: which Wearable will facilitate technology; the transfer Thermal from protection; research achievement Conductive textile;into mass Silver-coated production yarn to realize its commercial benefits. Introduction With the capability of the human to survive in various extreme structure constrains the free movement of human beings, especially environments is growing stronger and stronger, the desire to act protection is insufficient. Further, this bulky and massive multilayer when human doing exercises and conducting works in chill winter and move freely in chill condition is growing as well. -
Supporting Information for Adv
Copyright WILEY-VCH Verlag GmbH & Co. KGaA, 69469 Weinheim, Germany, 2020. Supporting Information for Adv. Mater. Technol., DOI: 10.1002/admt.202000383 Smart Thermally Actuating Textiles Vanessa Sanchez, Christopher J. Payne, Daniel J. Preston, Jonathan T. Alvarez, James C. Weaver, Asli T. Atalay, Mustafa Boyvat, Daniel M. Vogt, Robert J. Wood, George M. Whitesides, and Conor J. Walsh* Copyright WILEY-VCH Verlag GmbH & Co. KGaA, 69469 Weinheim, Germany, 2018. Supporting Information Smart Thermally Actuating Textiles Vanessa Sanchez†, Christopher J. Payne†, Daniel J. Preston, Jonathan T. Alvarez, James C. Weaver, Asli T. Atalay, Mustafa Boyvat, Daniel M. Vogt, Robert J. Wood, George M. Whitesides, and Conor J. Walsh* †Indicates equal contribution. *to whom correspondence should be addressed: [email protected] 1. Detailed Materials and Fabrication of STATs 1.1 Laser Fabrication Methods Material patterning for smart thermally actuating textiles (STATs) was done using vector cutting on a laser cutter. All laser cutting was performed using a 60-Watt CO2 laser (VLS 6.60, Universal Laser Systems) with the 2.0 lens. According to the manufacturer, this lens has a focal length of 50.8 mm, a focal spot size of approximately 0.13 mm, and a 2.54-mm depth of focus which define the width, w, of the zone of ablation. The width was measured to be approximately 200 µm with the system configuration in this work (Figure S1). Figure S1. (A) Schematic and (B) SEM image indicating zone of ablation and width. 1 1.2 Textile Heater Fabrication Joule heaters were incorporated on the interior of STATs. For the active heating material, woven silver-plated nylon (Shieldex Bremen Ripstop, V Technical Textiles Inc.) was adhered to a 5 μm double-sided adhesive (3M #82600 5 μm electronic double-sided tape, Bristol Tape Corporation). -
Electrically Conductive Textile Coatings
Electrically conductive textile coatings with PEDOT:PSS Maria Åkerfeldt Copyright © Maria Åkerfeldt Research School of Textiles and Fashion Faculty of Textiles, Engineering and Business University of Borås ISBN 978-91-87525-39-1 (tryckt) ISBN 978-91-87525-40-7 (pdf) ISSN 0280-381X, Skrifter från Högskolan i Borås, nr. 56 Printed in Sweden by Ale Tryckteam, Bohus 2015 ABSTRACT In smart textiles, electrical conductivity is often required for several functions, especially contacting (electroding) and interconnecting. This thesis explores electrically conductive textile surfaces made by combining conventional textile coating methods with the intrinsically conductive polymer complex poly(3,4-ethylene dioxythiophene)-poly(styrene sulfonate) (PEDOT:PSS). PEDOT:PSS was used in textile coating formulations including polymer binder, ethylene glycol (EG) and rheology modifier. Shear viscometry was used to identify suitable viscosities of the formulations for each coating method. The coating methods were knife coating, pad coating and screen printing. The first part of the work studied the influence of composition of the coating formulation, the amount of coating and the film formation process on the surface resistivity and the surface appearance of knife-coated textiles. The electrical resistivity was largely affected by the amount of PEDOT:PSS in the coating and indicated percolation behaviour within the system. Addition of a high-boiling solvent, i.e. EG, decreased the surface resistivity with more than four orders of magnitude. Studies of tear strength and bending rigidity showed that textiles coated with formulations containing larger amounts of PEDOT:PSS and EG were softer, more ductile and stronger than those coated with formulations containing more binder. -
Conductive Textile 4711 Technical Datasheet
Conductive textile 4711 Technical datasheet Material - Conductive textile 4711 Options • Rigid floor for heavy load Our RFI/EMI shielding tents are made of highly conductive, • Easy mounting frame lightweight and ultra strong textile for radiofrequency and • Shielded power filters microwave shielding. • Shielded ventilation/ AC • Cable sleeve for entry of filtered cables Rugged rip-stop polyester substrate (for superior strength • Many other options on request and handling), conductive Nickel and Copper plated (for excellent shielding and low corrosion), then coated Access to the shielded tent on one side with a non-conductive hot melt adhesive (activates at 130°C = 266°F) so you can iron it on to Typically the access point is made out of magnetic strips cotton, wood, glass or paper, or roll it into a tube and heat covered with electrically conductive layers of textile. seal the seam! Maximum temperature is 200°C (=392°F). The magnetic closure ensures superb electrical contact Can also be cut and sewn like ordinary fabric. after the tent is closed. When necessary, the entrance can also be equipped with conductive Velcro strips. Shielding performance This Conductive textile 4711 offers an amazing shielding performance: >60 dB from 10 MHz to 3+ GHz. Will also block virtually all ELF & VLF electric fields when grounded. Great for shielding extension cords and computer cables. Connect strips of it to make a sheet shield under your bed, or hang it on the wall. Makes a great liner for drapes too! Line a vest or a hat to protect your vital organs from radiowaves and electric fields. It doesn’t breathe well, and Nickel may cause skin irritation, so plan to line it with cotton if you will be using it against the skin. -
Is Challenged Elite 'Stork Club' Has Real 'Blowout'
Distribution M. Partly cloudy tonight, low, M. Partly cloudy tomorrow, Today chance of showeri; high 80. See page 2. 13,950 An Independent Newspaper Under Same Ownership Since 1878 BY CARRIER Issued Dally. Monday through Friday, entered as Second Clus Matter 7c PER COPY VOLUME 82, NO. 200 it the Foit Office at Rrd Bank. N. J., under tht Act of March 3. 1879. RED BANK, N. J., FRIDAY, MAY 20, 1960 35o PER WEEK PAGE ONE Plan to Build 'City' of 30,000 ToRezone In Madison Told; Is Challenged Area 'For SPOTSWOOD — "Electric City, TV Firm U.S.A.," a 190-million-dolIar com- plex of homes and apartments HOLMDEL — Local officials, for 30,000 persons, was planned jeeting with representatives of here today. llonder-Tongue, Inc., last night Soviet Stand Construction will begin next nnounced that the township will month on a 2,500-acre tract near iroceed with plans to rezone the Spotswood, about seven miles imbrosino tract on Rt. 35 for in- rewarning south of South Amboy in Middle- iustry. sex County, a developer and two The Newark firm hopes to electric firms announced yester- mild a $1,000,000 pilot electronics Is Disclosed day. ilant on the 141-acre tract and The plans drew an immediate iventually hopes to move its en- LISBON, Portugal (AP) response from John L. Cham- ire operation to the site. — President Eisenhower berlain, former mayor of Madi- Last night's session was de- left for Washington today son Township. He called a meet- oted to settlement of the ques- ing at his home to protest the ion of zoning the tract for in- to report to the American legality and desirability of the lustrial purposes. -
Printed Graphene, Nanotubes and Silver Electrodes Comparison for Textile and Structural Electronics Applications
sensors Article Printed Graphene, Nanotubes and Silver Electrodes Comparison for Textile and Structural Electronics Applications Agnieszka Tabaczy´nska 1,*, Anna D ˛abrowska 2 and Marcin Słoma 3 1 OPTEX S.A., Oskara Kolberga 2, 26-300 Opoczno, Poland 2 Department of Personal Protective Equipment, Central Institute for Labour Protection–National Research Institute, Wierzbowa 48, 90-133 Lodz, Poland; [email protected] 3 Institute of Metrology and Biomedical Engineering, Faculty of Mechatronics, Warsaw University of Technology, Sw.´ Andrzeja Boboli 8, 02-525 Warsaw, Poland; [email protected] * Correspondence: [email protected] Abstract: Due to the appearance of smart textiles and wearable electronics, the need for electro- conductive textiles and electro-conductive paths on textiles has become clear. In this article the results of a test of developed textile electro-conductive paths obtained by applying the method of screen printing pastes containing silver nanoparticles and carbon (graphene, nanotubes, graphite) are presented. Conducted research included analysis of the adhesion test, as well as evaluation of the surface resistance before and after the washing and bending cycles. Obtained results indicated that the samples with the content of carbon nanotubes 3% by weight in PMMA on substrate made of aramid fibers (surface mass of 260 g/m2) were characterized by the best adhesion and the best resistance to washing and bending cycles. Such electro-conductive paths have potential to be used in smart clothing applications. Citation: Tabaczy´nska,A.; D ˛abrowska, A.; Słoma, M. Printed Graphene, Nanotubes and Silver Keywords: textile electronics; printed and structural electronics; electrically conductive textiles; Electrodes Comparison for Textile wearable electronics; graphene; nanoparticles; composites and Structural Electronics Applications. -
Conductive Textiles and Their Use in Combat Wound Detection, Sensing, and Localization Applications
University of Tennessee, Knoxville TRACE: Tennessee Research and Creative Exchange Masters Theses Graduate School 5-2013 Conductive Textiles and their use in Combat Wound Detection, Sensing, and Localization Applications Stephen A. Holland [email protected] Follow this and additional works at: https://trace.tennessee.edu/utk_gradthes Part of the Electrical and Electronics Commons, and the Electromagnetics and Photonics Commons Recommended Citation Holland, Stephen A., "Conductive Textiles and their use in Combat Wound Detection, Sensing, and Localization Applications. " Master's Thesis, University of Tennessee, 2013. https://trace.tennessee.edu/utk_gradthes/1627 This Thesis is brought to you for free and open access by the Graduate School at TRACE: Tennessee Research and Creative Exchange. It has been accepted for inclusion in Masters Theses by an authorized administrator of TRACE: Tennessee Research and Creative Exchange. For more information, please contact [email protected]. To the Graduate Council: I am submitting herewith a thesis written by Stephen A. Holland entitled "Conductive Textiles and their use in Combat Wound Detection, Sensing, and Localization Applications." I have examined the final electronic copy of this thesis for form and content and recommend that it be accepted in partial fulfillment of the equirr ements for the degree of Master of Science, with a major in Electrical Engineering. Aly E. Fathy, Major Professor We have read this thesis and recommend its acceptance: Benjamin J. Blalock, Jeremy H. Holleman Accepted for the Council: Carolyn R. Hodges Vice Provost and Dean of the Graduate School (Original signatures are on file with official studentecor r ds.) CONDUCTIVE TEXTILES AND THEIR USE IN COMBAT WOUND DETECTION, SENSING, AND LOCALIZATION APPLICATIONS A Thesis Presented for the Master of Science Degree The University of Tennessee, Knoxville Stephen A. -
Electrically Conductive Textile Materials—Application in Flexible Sensors and Antennas
Review Electrically Conductive Textile Materials—Application in Flexible Sensors and Antennas Mourad Krifa School of Fashion, Advanced Materials & Liquid Crystals Institute, Kent State University, Kent, OH 44240, USA; [email protected] Abstract: This paper reviews some prominent applications and approaches to developing smart fabrics for wearable technology. The importance of flexible and electrically conductive textiles in the emerging body-centric sensing and wireless communication systems is highlighted. Examples of ap- plications are discussed with a focus on a range of textile-based sensors and antennas. Developments in alternative materials and structures for producing flexible and conductive textiles are reviewed, including inherently conductive polymers, carbon-based materials, and nano-enhanced composite fibers and fibrous structures. Keywords: conductive textiles; smart fabrics; textile sensors; textile antennas; inherently conductive polymers; nanoparticles 1. Introduction Smart fabrics and wearable electronics are set to succeed portable electronics as the Citation: Krifa, M. Electrically next milestone in the modern information technology era. To be considered “smart”, a Conductive Textile textile structure must integrate the capability to sense and respond to stimuli from the envi- Materials—Application in Flexible ronment [1–5]. In the broad sense, the stimuli and response of smart textiles can be of varied Textiles 1 Sensors and Antennas. 2021, , origins, including chemical, thermal, magnetic, and electrical [1]. The latter