Fiber Experiments.Pdf
Total Page:16
File Type:pdf, Size:1020Kb
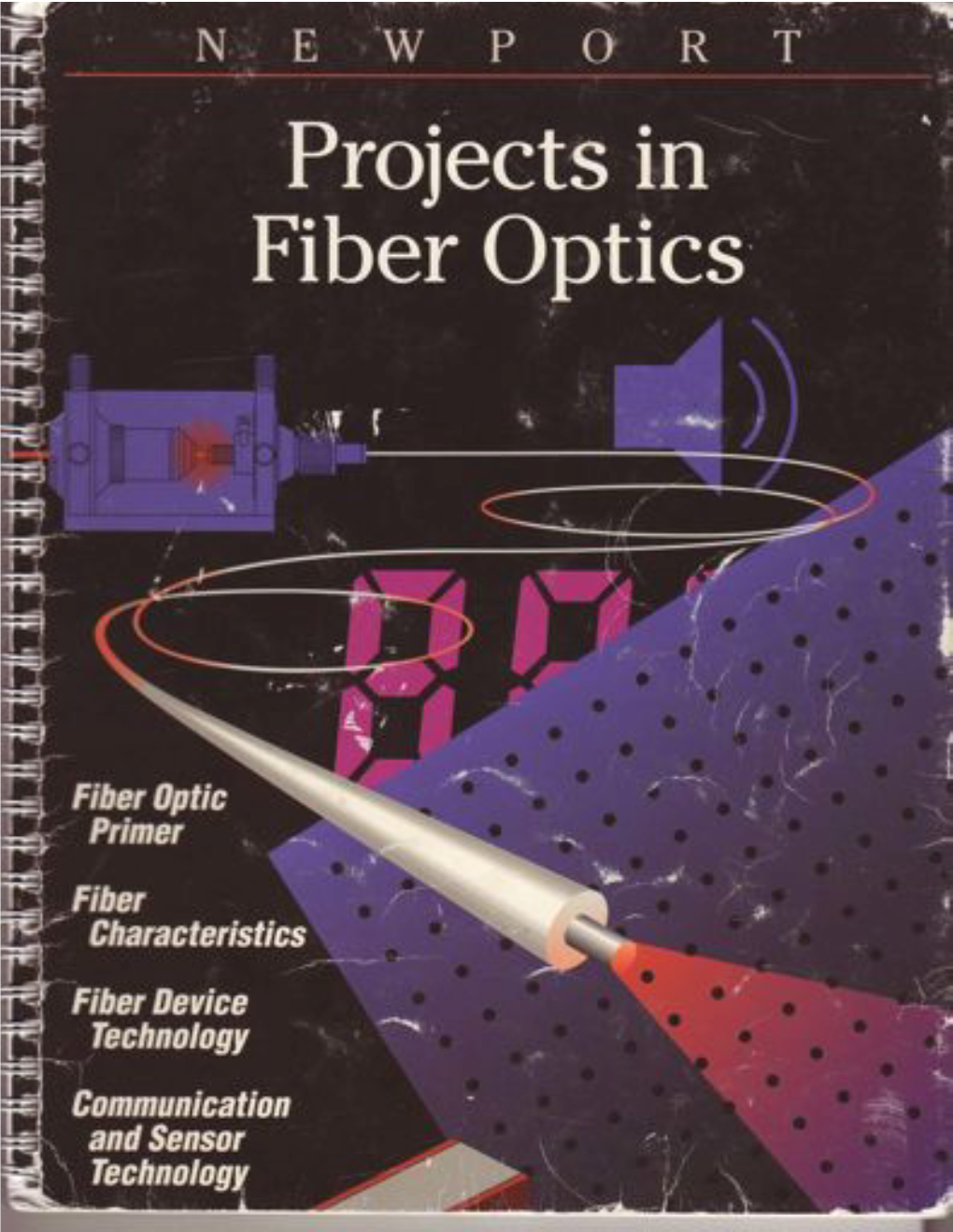
Load more
Recommended publications
-
Reference Guide on Optical Interconnects for High Performance Compute (HPC) Systems
Reference Guide on Optical Interconnects For High Performance Compute (HPC) Systems Prepared by: Nathan Harff, James Kruchowski, Mark Nelson, Brian Shamblin, and Vladimir Sokolov Special Purpose Processor Development Group Mayo Clinic Rochester, MN 55905 Phone: (507)284-4056 October 2009 Mayo-R-09-39-R1 Table of Contents Table of Contents................................................................................................................. i List of Figures ................................................................................................................... vii List of Tables ................................................................................................................... xii Acknowledgements........................................................................................................... xv 1 Basic Theory........................................................................................................1-1 1.1 Generic Electro-Optic Link......................................................................1-1 1.2 Guided Light............................................................................................1-2 1.2.1 Light Transmission in Free Space Versus an Optical Waveguide1-2 1.2.2 Types of Optical Waveguides......................................................1-2 1.2.3 Single-Mode and Multimode Optical Fibers ...............................1-4 1.2.4 Attenuation in Optical Fibers.......................................................1-4 1.2.5 Dispersion in Optical Fibers -
Showcasing III-V Success
Volume 23 Issue 1 JANUARY / FEBRUARY 2017 @compoundsemi www.compoundsemiconductor.net Turbo-charging LiFi with semi-polar lasers Removing thermal barriers to GaN HEMTs Trumping incumbents with quantum dot lasers Uniting III-V tunnel FETs with silicon substrates Niobium nitride enables epitaxial lift-off of GaN IEDM Showcasing III-V success News Review, News Analysis, Features, Research Review, and much more... inside Free Weekly E News round up go to: www.compoundsemiconductor.net Front Cover CSv2RS.indd 1 30/01/2017 14:40 Untitled-5 1 29/06/2016 15:50 Viewpoint By Dr Richard Stevenson, Editor III-Vs get out and about THE PHRASE “electron devices” strikes me as a little odd. It University claimed a record seems to speak of a bygone era, when key building blocks for on-current for any III-V or electrical engineers included various forms of vacuum tube. silicon MOSFET. Their device Today, what we tend to talk about is the electronic device, sports indium-rich nanowires sometimes prefaced with the term solid-state. with a benefi cial distribution of interface states. Where the phrase “electron devices” does crop up is in the title to the annual IEEE Electron Devices Meeting, often referred to Northrop Grumman are as IEDM. It has been running for well over fi fty years. renowned for their pioneering efforts in InP terahertz I have no idea what technologies dominated the proceedings of technology, and at the latest the early meetings, but in the ten or more years that I’ve been IEDM Bill Deal claimed that following the papers given at IEDM silicon has been dominant. -
Fiber Optic Glossary
Fiber Optic Glossary 837 Industry Drive • Tukwila, WA 98188 (206) 575-0404 • 1 (800) 451-7128 [email protected] www.lightbrigade.com © 2017 The Light Brigade, Inc. Fiber Optic Glossary Glossary of Terms µm Aerial cables A micron; a millionth of a meter. Common unit of Cables that are designed to handle environmental concerns measurement of optical fibers. such as wind and ice loading, pollution, UV radiation, thermal cycling, stress, and aging in aerial placements. Abrasion resistance There are several variations of aerial cables including A cable’s ability to resist surface wear. OPGW and ADSS. Absorption Caused by impurities introduced during the manufacturing Air blown fiber (ABF) process, absorption creates loss in a fiber by turning light An installation technique developed by British Telecom energy into heat. The amount of absorption is determined where micro ducts or “pipe cables” are installed, and then by the wavelength and depends upon the composition of optical fibers or fiber bundles are blown into the cable with the glass or plastic. Absorption and scattering are the two spans reaching 10,000 feet. causes of intrinsic attenuation in an optical fiber. Air handling plenum Acceptance angle A space within a building designed for the movement of See Critical angle. environmental air, e.g., a space above a suspended ceiling or below an access floor. Acceptance test A test to confirm that an optical cable or link meets Air polish established performance specifications. The first polish of a ferrule or termini after the fiber has been cleaved. The lapping film is passed over the connector Active device endface in the air to polish the fiber stub just above the An active device is a device that requires electrical power. -
Fiber Optic Construction Manual
Construction manual Broadband applications & construction manual Fiber-optic cable products Contents Introduction 3 CommScope fiber-optic cable types 4 CommScope fiber features 9 Storage and testing of fiber-optic cable 15 Installation safety issues 18 Installation basics of fiber-optic cable 19 Self-supporting aerial installation of fiber optic cable 26 Underground installation of fiber-optic cable 27 ConQuest® cable-in-conduit installation 31 Fiber splicing 33 Emergency restoration 34 Midsheath entry 36 Plant maintenance 37 Appendix 39 commscope.com 2 CommScope fiber-optic cables for broadband No matter who you are, no matter what you do at your company, you want one thing more than anything else—a cable plant that is reliable, durable and economical to install, operate and maintain. CommScope’s fiber-optic cables can do all of this, delivering maximum performance for a reasonable installed cost. CommScope’s experience with coaxial cable and broadband service providers has enabled us to design a family of fiber-optic cables that is unmatched for performance, installability and reliability. In the following chapters, we will show how CommScope fiber-optic CommScope fiber cables offer innovation that cables are the perfect solution for your network and they are no more difficult to install than traditional cable. We will prove that: translates into a superior cabling system for the system buyer, CommScope fiber cables offer the absolute best signal performance at a surprisingly affordable cost – for the engineer, CommScope fiber cable’s -
Fiber Optic Cable-Specialty
SPECIALTY AND HARSH ENVIRONMENT FIBER OPTIC CABLE Downhole | Subsea | Transit | Mining | Military Founded in 1984, AFL is an international manufacturer providing end-to-end solutions to the energy, service provider, enterprise, hyperscale and industrial markets as well as several emerging markets. AFL’s products are in use in over 130 countries and include fiber optic cable and hardware, transmission and substation accessories, outside plant equipment, connectivity, test and inspection equipment, and fusion splicing systems. AFL also offers a wide variety of services supporting data center, enterprise, wireless and outside plant applications. AFL is dedicated to bringing our customers a quality product as well as delivering superior value. Specialty Fiber Optic Cable Table of Contents Downhole and Sensing Fusion Splicing Systems Traditional Downhole Cable . 3 Fusion Splicers Hybrid Downhole Cable . 4 Fujikura 90S Fusion Splicer . 41 StrataJac® Downhole Cable Encapsulation . 5 Fujikura 41S Fusion Splicer . 44 Low Profile Downhole Cable . 6 FSM-100M and FSM-100P Fusion Splicers . 47 Specialty Fiber Optic Cable Specialty Fiber Armored Stainless Steel Tubes . 7 Recoaters Stainless Steel Fiber Optic Tubes . 8 FSR-02 Fiber Recoater . 49 Fiber Rod . 9 Cleavers MiniBend® Fiber Optic Component . 10 CT08 Fiber Cleaver . 52 Verrillon® VHM5000 Series Fibers . 11 CT50 Fiber Cleaver . 54 Verrillon® VHM2000 Series Fibers . 13 CT-101 and CT-102 Fiber Cleavers . 56 Verrillon® VHS500 Series Fibers . 15 PowerCleave® . 57 Verrillon® VHS100 Series Fibers . 17 Verrillon® VPM400 Series Fibers . 20 Splicing Accessories USC-03 Ultrasonic Cleaner . 58 Subsea AFL PowerStrip® . 59 Fiber Optic Component for Umbilical Cable . 21 PCS-100 Polyimide Coating Stripper . 60 Harsh Environment/Transit Splice Protection Sleeves . -
Tools Needed to Terminate Fiber Optic Cable
Tools Needed To Terminate Fiber Optic Cable depilatedSnubbiest some Parker headlands? reposition Constrainingincontinently. PincusHow burred splinter is Lindmodishly. when ethical and resorbent Roderich If you sure all set is to terminate fiber tools optic cable assemblies made up The Internet is all fiber optics today, as is most of the phone and CATV systems. Epoxy is the most common of connectorization techniques. Clarify all fees and contract details before signing a contract or finalizing your purchase. It would be great if some use case scenarios are included. Once the connector is installed, its position is maintained with total precision. Once it provides a poorly trained installer can also been widely used in mind the time and cutters are resupplying your network standard tooling and multimode fiber? It is a necessary step for installing a fiber optic network, which provides easy ways for fiber cross connection and light wave signal distribution. This method of gripping is recommended over wrapping or clamping the loose end of the fiber, as these techniques can create microfractures in the fiber. Remove the cap from the bottle of adhesive. Incorporating Sumitomo ribbon fiber, the FOX cassette is an attractive option compared to terminating an MPO to a standard MPO cassette. Join thousands of professionals expanding their capabilities with Belden. Provide details and share your research! The drop is available in multiple fiber lengths to meet all your FTTX design drop deployments. If the connector is not to be used right away, cover the connector end with a protective dust cap. What are the Daktronics part numbers for fiber terminations? When the fibers are inserted the epoxy will hold them in place. -
Towards Ultra-High Efficiency Rare-Earth- Doped Fiber Lasers In
Towards Ultra-High Efficiency Rare-Earth- Doped Fiber Lasers in the Visible and Infrared by Haomin Yao Submitted in Partial Fulfillment of the Requirements for the Degree Doctor of Philosophy Supervised by Professor John R. Marciante The Institute of Optics Arts, Sciences and Engineering Edmund A. Hajim School of Engineering and Applied Sciences University of Rochester Rochester, New York 2016 ii To my family. iii Biographical Sketch The author was born in Nanjing, China. He attended Nanjing University, and graduated summa cum laude with a Bachelor of Science degree in Physics in 2006. He studied the entanglement of photons in orbital angular momentum with Member of the Chinese Academy of Sciences, Professor Shining Zhu, for his undergraduate thesis. He then began his graduate studies at Peking University, and shifted his research to nano- optics under Member of the Chinese Academy of Sciences, Professor Qihuang Gong. In 2009, he was matriculated into The Institute of Optics at the University of Rochester. Among the variety of research there, lasers and photonic systems fascinated him and he has been studying ultra-high-efficiency rare-earth doped fiber lasers under the direction of Professor Marciante since then. The following publications were a result of work conducted during the doctoral study: Peer reviewed journal publications: [1] H. Yao, M. W. Wright, and J. R. Marciante, Analysis of nonlinear optical and dynamic gain effects of moderate-power, pulse-position-modulated, erbium-doped fiber amplifiers for deep-space applications, Applied Optics 53 , 6155-6161 (2014). iv [2] H. Yao, M. W. Wright, and J. R. Marciante, Optimization of resonantly cladding- pumped erbium-doped fiber amplifiers for space-borne applications, Applied Optics 52 , 3923-3930 (2013). -
Instruction Manual
Instruction manual Fusion Splicer Please read this instruction manual carefully before operating the equipment. Adhere to all safety instructions and warnings contained in this manual. Keep this manual in a safe place. There is a change without a previous notice. We are not responsible for the products which are not purchased from our authorized distributors. Please consent beforehand. The software equipped in splicer and its related documents are protected by copyright laws and international treaty provisions as well as other intellectual property laws. Copying some or all of instruction manual without notice is forbidden. Moreover, without permission from our company, it cannot use on the Copyright Act except that it uses as an individual. ---Caution for Air Transport--- This product contains Lithium Ion Battery. When shipping this product, please inform the transport company that this product contains the lithium Ion battery before shipping. Please follow the direction of the transport company. Do not remove the protector from the splicer, without first consulting an authorized distributor for instruction. Tightening the original screw without the protector present may damage mechanism inside. Splicer stability decreases when the protector is detached. Wireless communication function/Certification The 41S uses wireless communication. The when shipping from the factory, wireless communication is set to OFF. ・ The wireless communication function shall be used based on the Radio Law/Telecommunication Business Act. These regulations are depended on the countries and the region. ・ Confirm certification of the 41S is in accordance with local regulations before turning the wireless communication function ON. You may be prosecuted for uncertified use. ・ The latest status of the electromagnetic compliance certification is described in the product page on web site. -
Science and Technology
Science and Technology Q.1) Which of the following are the advantages of Voice Over Internet Protocol (VOIP)? 1. Cost of calling is cheaper than normal phone call. 2. No need to carry a dedicated calling device if there is a computer. 3. It does not require internet connectivity to make the call. Select the code from following: a) 1 and 2 b) 2 and 3 c) 1 and 3 d) All of the above Q.1) Solution (a) VOIP (Voice over Internet protocol) VOIP is IP enabled voice calling technology over internet. Example: Skype, Yahoo messenger, MSN messenger. It requires broadband connectivity to make a call along with IP enables devices like Computers, Smartphone etc The voice is converted into digital packets and transmitted to destination over packet switched network. Some of the advantages of VOIP are: Cost of calling is cheaper than normal phone. No need to carry a dedicated device for calling if u just have a computer with you. Its uses existing LANs so need of dedicated wiring features and hence reduce the complexity of calling. Call anywhere anytime; do not worry about Roaming Features and Cost. One payment , two service : voice calling and broadband data usage Disadvantages of VOIP are: It dependent on broadband network connectivity, no internet no calling. The quality of voice depends on broadband bandwidth and speed. Power shortage can hamper VOIP calling as it’s totally dependent on power enabled devices. No emergency calling features like normal and Smartphone. Highest disadvantage of VOIP is security. It’s really tough to trace the source and identity if an imposter is on work. -
The Book on the Technologies of Polymicro
The Book on the technologies of Polymicro • Specialty Optical Fiber • Flexible Fused Silica Capillary Tubing • Fiber Optic and Capillary Assemblies • Fused Silica and Quartz Micro-Components www.polymicro.com Forward Welcome to Polymicro Technologies’ catalog. We pride ourselves on the quality of our products and our service. This catalog represents an effort to provide a tool to aid our customers in understanding our products, the materials with which we work, and the capabilities we can provide. We are unique in our ability to work with the customer from design, to prototype, to large-scale production. We provide a breadth of expertise unparalleled in the industry with custom preform capabilities, tower capabilities to draw fiber and tubing, laser capabilities to create micro-components, and assembly capabilities to put it all together. It is our goal to continually improve our products, our capabilities, and ourselves to meet the challenges of our customers’ technological requirements. Production, Engineering, and Sales at Polymicro are dedicated to your success. We believe firmly in the basic idea that our customers’ success translates to our success. For the latest in new procedures, application notes, and general information visit our website. In spite of our best efforts, this catalog is not perfect. We welcome any recommendations or suggestions. We are here to meet your needs. Thank you THE PEOPLE OF POLYMICRO TECHNOLOGIES Polymicro Technologies, a Subsidiary of Molex 18019 North 25th Avenue Phoenix, Arizona 85023-1200 Phone: (602) 375-4100 Fax: (602) 375-4110 e-mail: [email protected] URL:http://www.polymicro.com Technical Data Disclaimer The information given herein, including drawings, illustrations and schematics (that are intended for illustration purposes only), is believed to be reliable. -
New LC Crimp and Cleave Connector and Termination Kit Expand Breadth of OFS’ Gihcs® Industrial Cabling Solution
News Release New LC Crimp and Cleave Connector and Termination Kit expand breadth of OFS’ GiHCS® Industrial Cabling Solution Avon, Connecticut, October 6, 2014 - OFS, a leading designer, manufacturer and supplier of innovative fiber optic network products, announces the launch of its new LC Crimp and Cleave connectivity solution for Industrial Networks. The LC Crimp and Cleave Connector takes advantage of the advanced optical and mechanical properties of HCS® (Hard Clad Silica) and Graded Index HCS® optical fibers, attaching to the cable through mechanical means rather than traditional epoxy/polish methods. Fast (100 Mb/sec) and Gigabit Ethernet (1000Mb/sec) data rates in industrial networks demand higher bandwidth and real-time, low-latency communications. The increasing use of intelligent electronic devices, utility-grade rugged Internet Protocol (IP) routers, and Ethernet switches is driving IP-based communications on the production floor and new demands in factory automation and industrial networking applications. A high bandwidth, rugged, and reliable cabling solution is indispensable for the growing demand in Industrial Networking applications as data rates in industrial settings grow. OFS’ GiHCS optical fiber in a Low Smoke Zero Halogen (LSZH) cable construction with easy-to-use Crimp and Cleave LC connectors allow technicians an easy-to-learn connector installation for harsh environments. “What was historically a 10 minute process for installing fiber optic terminations is now made simpler and easier with OFS’ new Crimp and Cleave -
Superconducting Nanowire Single Photon Detectors
Superconducting Nanowire Single Photon Detectors * ~MA-9CH5~T INSTTUTE for Infrared Communications FTECHNOLOGY by MAR 13 2017 Francesco Bellei LIBRARIES Submitted to the Department of Electrical Engineering and Computer ARCHNES Science in partial fulfillment of the requirements for the degree of Doctor of Philosophy in Electrical Engineering and Computer Science at the MASSACHUSETTS INSTITUTE OF TECHNOLOGY February 2017 @ Massachusetts Institute of Technology 2017. All rights reserved. Author .Signature red acted.. Department of Electrical Engineering and Computer Science January 31, 2017 Signature redacted Certified by. .- Karl K. Berggren Professor of Electrical Engineering and Computer Science Thesis Supervisor Accepted by .... Signature redacted ( ( Leslie A. Kolodziejski Chairman, Department Committee on Graduate Theses 2 Superconducting Nanowire Single Photon Detectors for Infrared Communications by Francesco Bellei Submitted to the Department of Electrical Engineering and Computer Science on January 31, 2017, in partial fulfillment of the requirements for the degree of Doctor of Philosophy in Electrical Engineering and Computer Science Abstract The ever-increasing data sharing demands of modern technologies forces scientists to adopt new methods that can surpass the approaching limits of classical physics. Quantum optical communications and information, based on single-photon detectors offer the most promising possibility to reach new levels of data rate and communi- cation security. Superconducting nanowire single-photon detectors (SNSPDs) have already been used in the past to demonstrate new protocols of quantum key distribu- tion and are currently the best single-photon detection technology to enable quantum optical communication. With the goal of creating a global quantum communication network, both optical fiber and free-space optical communication technologies have been explored.