Comparison of Direct and Indirect Combustion Noise Mechanisms in a Model Combustor Matthieu Leyko, Franck Nicoud, Thierry Poinsot
Total Page:16
File Type:pdf, Size:1020Kb
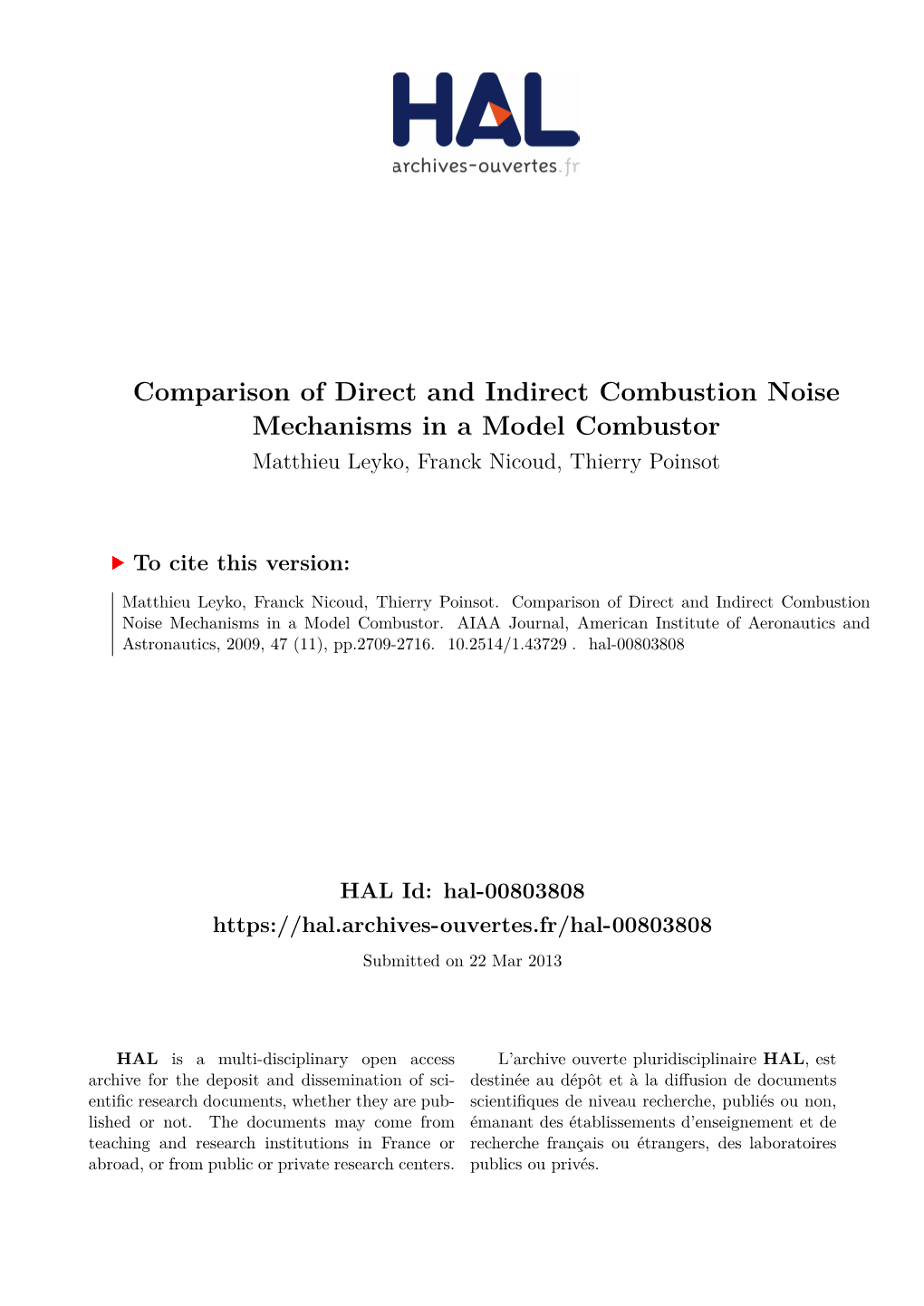
Load more
Recommended publications
-
The Response of Normal Shocks in Diffusers
1382 AIAA JOURNAL VOL.21,NO.10 The Response of Normal Shocks in Diffusers F.E.C. Culick* California Institute of Technology, Pasadena, California and T. Rogerst The Marquardt Company, Van Nuys, Calzfornia The frequency response of a normal shock in a diverging channel is calculated for application to problems of pressure oscillations in ramjet engines. Two limits of a linearized analysis arc discussed: one represents isentropic flow on both sides of a shock wave; the other may be a crude appr'l'I;imation to the influence of flow separation induced hy the wave. Numerical results arc given, and the influences of the shock wave on oscillations in the engine are discus,ed. Nomenclature L Introduction = speed of sound ECENT concern 1-4 with undesirable consequences of = admittance function, defined by Eq. (9) R longitudinal pressure oscillations in ramjet engines has = constant defined by Eq. (43) focused attention on unsteady behavior of the inlet diffuser. In extreme cases the compressive portion of an oscillation =complex wave number, k= (0C-ia)/a = Mach number may be so large as to cause the inlet to become unchoked. = pressure Thus, the effect of a pressure oscillation may be regarded as = defined by Eq. (13) an equivalent loss of pressure margin. = amplitudes of rightward and leftward traveling Although the flow is surely more complicated in actual pressure waves, respectively cases, it is convenient to begin with a simplified representation of the diffuser, and assume that under steady operating P, = defined by Eq. (29) S = cross-sectional area conditions a single normal shock exists in the divergent =time section. -
Chapter Sixteen / Plug, Underexpanded and Overexpanded Supersonic Nozzles ------Chapter Sixteen / Plug, Underexpanded and Overexpanded Supersonic Nozzles
UOT Mechanical Department / Aeronautical Branch Gas Dynamics Chapter Sixteen / Plug, Underexpanded and Overexpanded Supersonic Nozzles -------------------------------------------------------------------------------------------------------------------------------------------- Chapter Sixteen / Plug, Underexpanded and Overexpanded Supersonic Nozzles 16.1 Exit Flow for Underexpanded and Overexpanded Supersonic Nozzles The variation in flow patterns inside the nozzle obtained by changing the back pressure, with a constant reservoir pressure, was discussed early. It was shown that, over a certain range of back pressures, the flow was unable to adjust to the prescribed back pressure inside the nozzle, but rather adjusted externally in the form of compression waves or expansion waves. We can now discuss in detail the wave pattern occurring at the exit of an underexpanded or overexpanded nozzle. Consider first, flow at the exit plane of an underexpanded, two-dimensional nozzle (see Figure 16.1). Since the expansion inside the nozzle was insufficient to reach the back pressure, expansion fans form at the nozzle exit plane. As is shown in Figure (16.1), flow at the exit plane is assumed to be uniform and parallel, with . For this case, from symmetry, there can be no flow across the centerline of the jet. Thus the boundary conditions along the centerline are the same as those at a plane wall in nonviscous flow, and the normal velocity component must be equal to zero. The pressure is reduced to the prescribed value of back pressure in region 2 by the expansion fans. However, the flow in region 2 is turned away from the exhaust-jet centerline. To maintain the zero normal-velocity components along the centerline, the flow must be turned back toward the horizontal. -
Compressible Flow
Chapter 4 Compressible Flow 1 9.1 Introduction • Not all gas flows are compressible flows, neither are all compressible flows gas flows. • Examples: airflows around commercial and military aircraft, airflow through jet engines, and the flow of a gas in compressors and turbines. 2 9.1 Introduction • Reminders from previous chapters: • Continuity equation • Momentum equation • Energy equation 3 9.1 Introduction • Reminders from previous chapters: • Thermodynamic relations • Ideal gas law • Isentropic flow 4 9.2 Speed of Sound and the Mach Number • Sound wave: • Travels with a velocity c relative to a stationary observer. 5 9.2 Speed of Sound and the Mach Number • Speed of Sound • Using the ideal gas law • Mach number (dimensionless velocity) 6 9.2 Speed of Sound and the Mach Number If M < 1, the flow is a subsonic flow, and if M > 1, it is a supersonic flow. Angle α of the Mach cone is given by: 7 9.2 Speed of Sound and the Mach Number 8 9.2 Speed of Sound and the Mach Number 9 9.3 Isentropic Nozzle Flow Examples: diffuser near the front of a jet engine, exhaust gases passing through the blades of a turbine, the nozzles on a rocket engine, a broken natural gas line. 10 9.3 Isentropic Nozzle Flow 1. If the area is increasing, dA > 0, and M < 1, we see that dV must be negative, that is, dV < 0. The flow is decelerating for this subsonic flow. 2. If the area is increasing and M > 1, we see that dV > 0; hence the flow is accelerating in the diverging section for this supersonic flow. -
Simulation of Critical Nozzle Flow Considering Real Gas Effects
Flomeko 2000 - IMEKO TC9 Conference Salvador, Bahia, BRAZIL 4-8 June, 2000 SIMULATION OF CRITICAL NOZZLE FLOW CONSIDERING REAL GAS EFFECTS P. Schley1, E. von Lavante2, D. Zeitz2, M. Jaeschke1, H. Dietrich3 and B. Nath3 1 Elster Produktion GmbH, Steinernstrasse 19-21, D-55252 Mainz-Kastel, Germany 2 Institute of Turbomachinery, University of Essen, D-45127 Essen, Germany 3 Ruhrgas AG, Halterner Strasse 125, D-46284 Dorsten, Germany Abstract: Critical nozzle flow is predicted for high pressure natural gas by way of numerical simulation. The CFD-program used was developed for simulating two- dimensional and axially symmetric, viscous flow. The thermodynamic properties significantly affecting nozzle flow of high pressure natural gas were computed using the AGA8-DC92 equation of state. To verify the present theoretical results, mass flow measurements of natural gas were made using the Pigsar high-pressure test rig. A comparison between theoretical and experimental results is presented for one test case. Keywords: Critical Flow Factor, Critical Nozzle, Discharge Coefficient, Natural Gas, Numerical Simulation, Real Gas 1 INTRODUCTION Critical nozzles are widely used as a reference standard in gas flow measurements. Apart from a high reproducibility of measurements, main benefits include easy handling and short adjustment times. The mass flow of the gas as described in ISO 9300 [1] involves the critical flow factor, C*, which depends on the thermodynamic properties of the gas, and the discharge coefficient, CD, determined mainly by nozzle geometry. For pure substances or air, there are relatively simple computation methods ([1],[2]) for computing the C* and CD, providing very accurate results. In the case of natural gas, the mass flow is not only a function of pressure and temperature, but also of the composition, making a theoretical description far more difficult. -
GALCIT Ludwieg Tube Ae 104B
GALCIT Ludwieg Tube Ae 104b TA: Greg Smetana Lab: Guggenheim 026 Phone: [email protected] Winter 2014 1 Principles of supersonic wind tunnels Supersonic wind tunnels, like their subsonic counterparts, operate by accelerating a high pressure gas through a nozzle and into a test section where the model being tested is placed. Supersonic wind tunnels are generally divided into two categories: continuous and blow-down (sometimes called impulse) facilities. Continuous operation facilities are nearly identical in principle to subsonic tunnels: a compressor increases the pressure of the gas, the gas is accelerated through a nozzle, passes through the test section, is decelerated in a diffuser, and returns to the compressor. Blow-down facilities operate by separating the nozzle and test section from a pressurized section by a diaphragm or valve and then either breaking the diaphragm or opening the valve. The resulting pressure difference drives gas through the nozzle and through the test section, creating supersonic flow as long as the pressure in the driving chamber remains high enough. Each type has its own advantages and disadvantages. Continuous operation tunnels can perform long- duration experiments because they can often operate under steady conditions indefinitely. Because of the high speeds attained in supersonic tunnels, however, the energy consumption from a continuous supersonic wind tunnel is typically very high. Continous wind tunnels are also typically expensive to maintain because of mechanical components such as the compressor. Blow-down tunnels are by comparison very inexpensive because they often involve no moving parts and the cost associated with an experiment is limited to the cost of gas and single-experiment components as maintenance is seldom needed. -
Asymptotic Solutions for the Fundamental Isentropic Relations in Variable Area Duct Flow
University of Tennessee, Knoxville TRACE: Tennessee Research and Creative Exchange Masters Theses Graduate School 5-2006 Asymptotic Solutions for the Fundamental Isentropic Relations in Variable Area Duct Flow Esam M. Abu-Irshaid University of Tennessee, Knoxville Follow this and additional works at: https://trace.tennessee.edu/utk_gradthes Part of the Aerospace Engineering Commons Recommended Citation Abu-Irshaid, Esam M., "Asymptotic Solutions for the Fundamental Isentropic Relations in Variable Area Duct Flow. " Master's Thesis, University of Tennessee, 2006. https://trace.tennessee.edu/utk_gradthes/4479 This Thesis is brought to you for free and open access by the Graduate School at TRACE: Tennessee Research and Creative Exchange. It has been accepted for inclusion in Masters Theses by an authorized administrator of TRACE: Tennessee Research and Creative Exchange. For more information, please contact [email protected]. To the Graduate Council: I am submitting herewith a thesis written by Esam M. Abu-Irshaid entitled "Asymptotic Solutions for the Fundamental Isentropic Relations in Variable Area Duct Flow." I have examined the final electronic copy of this thesis for form and content and recommend that it be accepted in partial fulfillment of the equirr ements for the degree of Master of Science, with a major in Aerospace Engineering. Joseph Majdalani, Major Professor We have read this thesis and recommend its acceptance: Gary Flandro, Kenneth Kimble Accepted for the Council: Carolyn R. Hodges Vice Provost and Dean of the Graduate School (Original signatures are on file with official studentecor r ds.) To the Graduate Council: I am submitting herewith a thesis written by Esam M. Abu-Irshaid entitled "Asymptotic Solutions forthe Fundamental IsentropicRelations in Variable Area Duct Flow." I have examined the finalpaper copy of this thesis forform and content and recommend that it be accepted in partial fulfillment of the requirements for the degree of Master of Science, with a major in Aerospace Engineering. -
Detection of Nitrogen Flow Condensation in a Hypersonic Wind-Tunnel Using a Static Pressure Probe
Detection of Nitrogen Flow Condensation in a Hypersonic Wind-Tunnel using a Static Pressure Probe Guillaume Grossir∗ and Patrick Rambaudy von Karman Institute for Fluid Dynamics, Chauss´eede Waterloo 72, 1640 Rhode-St-Gen`ese,Belgium Measurements with a slender static-pressure probe in the free-stream of the Longshot hypersonic wind-tunnel have recently been performed. They have revealed pressures larger than the theoretical values obtained with the assumption of an isentropic nozzle flow. The presence of flow condensation during the nozzle expansion is now investigated as a possible source of non-isentropicity to explain the free-stream static pressure mismatch. Different stagnation temperatures are investigated which either delay or promote flow nucleation. Standard operating conditions of the Longshot wind-tunnel are demonstrated to be free of condensation. Experiments performed with lower stagnation temperatures have success- fully promoted the condensation of nitrogen which could be detected by the static pressure probe. A weak amount of flow supersaturation has been achieved in agreement with het- erogeneous nucleation theory. The accurate performances of static pressure probes and their usefulness for the characterization of hypersonic flows are demonstrated. Nomenclature Symbols Greek c Specific heat, J=(kg:K) α Angle of attack, degrees D Static pressure probe diameter, mm ρ Flow density, kg=m3 h Flow enthalpy, J=kg σ Standard deviation k Thermal conductivity, W=(m:K) Length of the last characteristic line l projected along the nozzle axis, m Subscripts Distance along the static pressure probe L s At the stagnation point from its nosetip, mm t Stagnation condition m Mass, kg 0 p Flow pressure, Pa In the reservoir 1 Upstream a normal shock wave P_ Nozzle expansion rate parameter, s−1 2 Downstream a normal shock wave Q_ Heat flux, W=m2 1 Free-stream value t Time, ms T Flow temperature, K u Flow velocity, m=s I. -
JUN1977 Rnreceived
NASA CR-145186 EVALUATION OF HYDROGEN AS A CRYOGENIC WIND TUNNEL TEST GAS By Richard C. Haut April 1977 177-2'153 516) EVATUATION OF HYDROGEN AS (NA-SAC- TEST GAS Final A CRYOGENICRepot(1a WINDominon TUNREL ni-, Norfolk, Va° CSCL 14B Unclas 9 Report159 p HC(old AOB/MF Dlomiiofl A01 Uiv , NOSf)R 14VGG3/9 /0.)20 2g208 Prepared under Grant No. NGR 47-003-052 By OLD DOMINION UNIVERSITY Q' Norfolk, VA 23508 /r JUN1977 for rnRECEIVED NASA STh FACIUITY "I INPUT BRANCH NASA N National Aeronautics and Space Administration 1. Report No 2. Government Accession No. 3. Recipient's Catalog No. NASA CR- 145186 4 Title and Subtitle 5.Report Date EVALUATION OF HYDROGEN AS A CRYOGENIC WIND TUNNEL TEST April 1977 GAS 6 Performing Organization Code 7 Author(s) 8. Performing Organization Report No Richard C, Haut 10. Work Unit No. 9 Performing Organization Name and Address Old Dominion University 11. Contract or Grant No. Norfolk, VA 23508 NGR 47-003-052 13. Type of Report and Period Covered 12 Sponsoring Agency Name and Address Contractor Report National Aeronautics and Space Administratio4 Washington, DC 20546 14 Sponsoring AgncyCode 15. Supplementary Notes Langley Technical Monitor; Jerry B. Adcoc Final Report - R. C. Haut is a doctoral student in the Mechanical Engineering and Mechanics Department at Old Dominion University (ODU). This contractor Report is based on his Doctoral dissertation, submitted to the School of Graduate Studies at ODU. 16. Abstract A theoretical analysis of the properties of hydrogen has been made to determin( the suitability of hydrogen as a cryogenic wind tunnel test gas. -
Inviscid Non-Equilibrium Flow of an Expanded Air Plasma
This dissertation has been 65-3901 microfilmed exactly as received PETRIE, Stuart Lee, 1934- INVISCID NON-EQUILIBRIUM FL O W OF AN EXPANDED AIR PLASMA. The Ohio State University, Ph.D., 1964 Engineering, aeronautical University Microfilms, Inc., Ann Arbor, Michigan INVISCID NON-EQUILIBRIUM PLOW OP AN EXPANDED AIR PLASMA DISSERTATION Presented in Partial Fulfillment of the Requirements for the Degree Doctor of Philosophy in the Graduate School of The Ohio State University By Stuart Lee Petrie, B. A.E., M. S. The Ohio State University 1964 Approved by C K > . Adviser Department of Aeronautical and Astronautical Engineering ACKNOWLEDGMENTS The author gratefully acknowledges the helpful counsel of his adviser, Dr. R. Edse, during the course of these studies. In particular, the author is grateful for the many infomative discussions with Dr. Edse concerning the interpretation of the experimental results. The author also acknowledges the constant encouragement given him by Dr. J. D. Lee, Director of The Aerodynamic Laboratory, and the cooperation shown by the staff of The Aerodynamic Labor atory. The study was supported partially by contract no. AF 33(657)-756l with the Directorate of Engineering Test, Research and Technology Division, Air Force Systems Command, United States Air Force, by contract no. AF 33(657)-11060 with the Aerospace Research Laboratories, Office of Aero space Research, United States Air Force, and by The Ohio State University under account no. 19913* ii CONTENTS PAGE ACKNOWLEDGMENTS ii CONTENTS iii LIST OP TABLES v LIST OF ILLUSTRATIONS vi I. INTRODUCTION 1 II. THEORETICAL ANALYSIS 6 A. Plow With Coupled Finite Reaction Rates 6 B. -
ME409 COMPRESSIBLE FLUID FLOW.Pdf
Course code Course Name L-T-P- Year of Credits Introduction ME409 COMPRESSIBLE FLUID FLOW 2-1-0-3 2016 Prerequisite: ME205 Thermodynamics Course Objectives: To familiarize with behavior of compressible gas flow. To understand the difference between subsonic and supersonic flow To familiarize with high speed test facilities Syllabus Introduction to Compressible Flow, Wave propagation, One dimensional steady isentropic flow, Irreversible discontinuity in supersonic flow, Flow in a constant area duct with friction (Fanno Flow), Flow through constant area duct with heat transfer (Rayleigh Flow), Compressible flow field visualization and measurement, measurement in compressible flow, Wind tunnels Ex pected outcome: The students will be able to i. Formulate and solve problems in one -dimensional steady compressible flow including: isentropic nozzle flow, constant area flow with friction (Fanno flow) and constant area flow with heat transfer (Rayliegh flow). ii. Derive the conditions for the change in pressure, density and temperature for flow through a normal shock. iii. Determine the strength of oblique shock waves on wedge shaped bodies and concave corners iv. Know the various measuring instruments used in compressible flow Data book/Gas tables: 1. Yahya S. M., Gas Tables, New Age International, 2011 2. Balachandran P., Gas Tables, Prentice-Hall of India Pvt. Limited, 2011 Text Books: 1. Balachandran P., Fundamentals of Compressible Fluid Dynamics, PHI Learning. 2006 2. Rathakrishnan E., Gas Dynamics, PHI Learning, 2014 3. Yahya S. M., Fundamentals of Compressible Flow with Aircraft and Rocket Propulsion, New Age International Publishers, 2003 References Books: 1. Anderson, Modern compressible flow, 3e McGraw Hill Education, 2012 2. Shapiro, Dynamics and Thermodynamics of Compressible Flow – Vol 1., John Wiley & Sons,1953 Course Plan End Module Contents Hours Sem. -
Section 5, Lecture 1: Review of Idealized Nozzle Theory
Section 5, Lecture 1:! Review of Idealized Nozzle Theory Summary of Fundamental Properties and Relationships Taylor Chapter 4, Material also taken from Sutton and Biblarz, Chapter 3 1 MAE 5540 - Propulsion Systems Thermodynamics Summary R • Equation of State: p = ρR T − R = u g g M w - Ru = 8314.4126 J/°K-(kg-mole) - Rg (air) = 287.056 J/°K-(kg-mole) • Relationship of Rg to specific heats cp = cv + Rg • Internal Energy and Enthalpy h = e + Pv ⎛ de ⎞ ⎛ dh ⎞ cv = ⎜ ⎟ cp = ⎜ ⎟ ⎝ dT ⎠ v ⎝ dT ⎠ p 2 MAE 5540 - Propulsion Systems Thermodynamics Summary (2) R • Equation of State: p = ρR T − R = u g g M w - Ru = 8314.4126 J/°K-(kg-mole) - Rg (air) = 287.056 J/°K-(kg-mole) • Relationship of Rg to specific heats cp = cv + Rg • Internal Energy and Enthalpy h = e + Pv ⎛ de ⎞ ⎛ dh ⎞ cv = ⎜ ⎟ cp = ⎜ ⎟ ⎝ dT ⎠ v ⎝ dT ⎠ p 3 MAE 5540 - Propulsion Systems Thermodynamics Summary (3) R • Equation of State: p = ρR T − R = u g g M w - Ru = 8314.4126 J/°K-(kg-mole) - Rg (air) = 287.056 J/°K-(kg-mole) • Relationship of Rg to specific heats cp = cv + Rg • Internal Energy and Enthalpy h = e + Pv ⎛ de ⎞ ⎛ dh ⎞ cv = ⎜ ⎟ cp = ⎜ ⎟ ⎝ dT ⎠ v ⎝ dT ⎠ p 4 MAE 5540 - Propulsion Systems Thermodynamics Summary (4) • Speed of Sound for calorically Perfect gas c = γ RgT • Mathematic definition of Mach Number V M = γ RgT 5 MAE 5540 - Propulsion Systems Thermodynamics Summary (5) • First Law of Thermodynamics, reversible process de = dq − pdv dh = dq + vdp • First Law of Thermodynamics, isentropic process (adiabatic, reversible) de = − pdv dh = vdp 6 MAE 5540 - Propulsion Systems -
The Design of a 2D Supersonic Nozzle for Use in Wind Tunnels [Pdf]
Design of a Two-Dimensional Supersonic Nozzle for use in Wind Tunnels a project presented to The Faculty of the Department of Aerospace Engineering San José State University in partial fulfillment of the requirements for the degree Master of Science in Aerospace Engineering by Yousheng Deng May 2018 approved by Dr. Fabrizio Vergine Faculty Advisor © 2018 Yousheng Deng ALL RIGHTS RESERVED The Designated Project Advisor(s) Approves the Thesis Titled DESIGN OF A TWO-DIMENSIONAL SUPERSONIC NOZZLE FOR USE IN WIND TUNNELS by Yousheng Deng APPROVED FOR THE DEPARTMENT OF AEROSPACE ENGINEERING SAN JOSÉ STATE UNIVERSITY May 2018 Dr. Fabrizio Vergine Department of Aerospace Engineering Advisor ABSTRACT DESIGN OF A TWO-DIMENSIONAL SUPERSONIC NOZZLE FOR USE IN WIND TUNNELS By Yousheng Deng This paper outlines the theory, process, and verification of the design of a two- dimensional nozzle. Fundamental concepts of isentropic and non-isentropic flows are reviewed. Then a gradual-expansion nozzle is designed using the two-dimensional method of characteristics, modified to include a gradual expansion section. Inviscid CFD simulations are then ran to verify the final nozzle is capable of accelerating the flow to the wanted supersonic speed without any shocks. Viscous simulations are then ran to account for boundary layer effects on the walls. ACKNOWLEDGEMENTS I would like to sincerely thank my parents for their endless support and encouragement over the course of this project. I would also like to thank my advisor, Dr. Fabrizio Vergine, for his knowledge and guidance throughout this project. Table of Contents List of Symbols .............................................................................................................................. iv List of Figures ................................................................................................................................. v List of Tables ................................................................................................................................