Fatigue Characterization of Fire Resistant Syntactic Foam Core Material
Total Page:16
File Type:pdf, Size:1020Kb
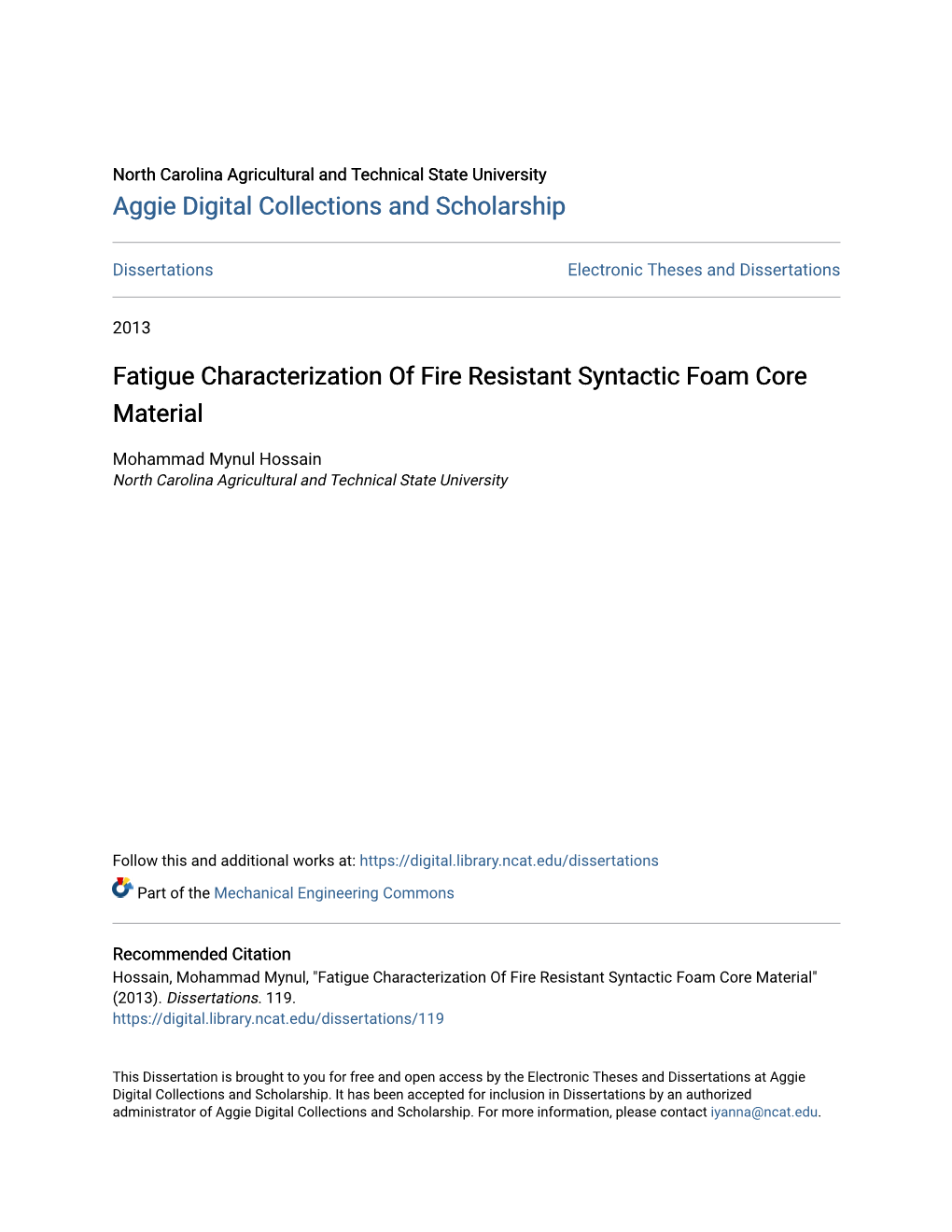
Load more
Recommended publications
-
Processing of Syntactic Foams: a Review
IARJSET ISSN (Online) 2393-8021 ISSN (Print) 2394-1588 International Advanced Research Journal in Science, Engineering and Technology CETCME-2017 “Cutting Edge Technological Challenges in Mechanical Engineering” Noida Institute of Engineering & Technology (NIET), Greater Noida Vol. 4, Special Issue 3, February 2017 Processing of Syntactic Foams: A Review Ankur Bisht1, Brijesh Gangil2 Faculty, Mechanical Engineering Dept, S.O.E.T., HNB Garhwal University, Srinagar Garhwal, Uttarakhand, India 1 Assistant Professor, Mechanical Engg, S.O.E.T., HNB Garhwal University, Srinagar Garhwal, Uttarakhand, India 2 Abstract: For structural application different types of lighter material with higher specific strength are being developed now days like honeycomb, metal foam, sandwich panels, syntactic foam etc. In this review paper the syntactic foam is discussed among all these lighter material. Syntactic foams are the materials in which micro spheres are incorporated in a matrix. In syntactic foams, the matrix is reinforced with hollow spherical particles which have a controlled systematic arrangement in the matrix. Hollow microspheres give the syntactic foam its low density, high specific strength, and low moisture absorption. Microspheres may comprise glass, polymer, carbon and ceramic or even metal. The strength of syntactic foams can be nearly equal to that of the matrix. The plateau and yield stress can be tailored over a wide range by selecting appropriate volume fraction and particle type. Metal matrix syntactic foams are expected to have better properties compared to open or closed-cell metallic foams since the former have controlled size and geometry of porosity and the ceramic shells contribute to stiffness and strength. Several preparation methods are used for preparing syntactic foam and various applications are discussed, depending on the types of matrix and reinforcement used. -
Syntactic Foam, Ceramic Microballoon, Nanoclay, Tensile Properties, Experimental Analysis
View metadata, citation and similar papers at core.ac.uk brought to you by CORE provided by Kingston University Research Repository International Journal of Composite Materials 2016, 6(1): 34-41 DOI: 10.5923/j.cmaterials.20160601.05 Investigation on Tensile Properties of Plain and Nanoclay Reinforced Syntactic Foams H. Ahmadi1,*, G. H. Liaghat1,2, H. Hadavinia2 1Department of Mechanical Engineering, Tarbiat Modares University, Tehran, Iran 2Department of Mechanical and Automotive Engineering, Kingston University, London, UK Abstract Tensile properties of plain and nanoclay reinforced epoxy matrix syntactic foams with three different sizes of ceramic microballoons are investigated experimentally. Nine series of plain syntactic foams with 20, 40 and 60 volume fractions of microballoons are prepared and tested to study the volume fraction and size effects. Also nano syntactic foams specimens with six different weight fractions of nanoclay (0, 1, 2, 3, 5 & 7%) are tested and the effect of nanoclay content on the tensile properties is investigated. In addition to tensile tests, fracture modes of all syntactic foams are considered thoroughly by using scanning electron microscopy (SEM). Keywords Syntactic foam, Ceramic microballoon, Nanoclay, Tensile properties, Experimental analysis characterization of vinyl ester/glass microballoon syntactic 1. Introduction foams. They found that specific tensile strength and specific tensile modulus of foams are comparable with their neat Application of lightweight materials is widely increased resin and are higher for some samples. Gouhe and Demei in aeronautical, marine and civil structures. Among these [15] tested four types of hollow polymer particles as filler in materials, foams with a significant weight saving have an UV-heat-cured epoxy resin. -
Under High Pressure: Spherical Glass Flotation and Instrument Housings in Deep Ocean Research
PAPER Under High Pressure: Spherical Glass Flotation and Instrument Housings in Deep Ocean Research AUTHORS ABSTRACT Steffen Pausch All stationary and autonomous instrumentation for observational activities in Nautilus Marine Service GmbH ocean research have two things in common, they need pressure-resistant housings Detlef Below and buoyancy to bring instruments safely back to the surface. The use of glass DURAN Group GmbH spheres is attractive in many ways. Glass qualities such as the immense strength– weight ratio, corrosion resistance, and low cost make glass spheres ideal for both Kevin Hardy flotation and instrument housings. On the other hand, glass is brittle and hence DeepSea Power & Light subject to damage from impact. The production of glass spheres therefore requires high-quality raw material, advanced manufacturing technology and expertise in Introduction processing. VITROVEX® spheres made of DURAN® borosilicate glass 3.3 are the hen Jacques Piccard and Don only commercially available 17-inch glass spheres with operational ratings to full Walsh reached the Marianas Trench ocean trench depth. They provide a low-cost option for specialized flotation and W instrument housings. in1960andreportedshrimpand flounder-like fish, it was proven that Keywords: Buoyancy, Flotation, Instrument housings, Pressure, Spheres, Trench, there is life even in the very deepest VITROVEX® parts of the ocean. What started as a simple search for life has become over (1) they need to have pressure- the years a search for answers to basic Advantages and resistant housings to accommodate questions such as the number of spe- Disadvantages sensitive electronics, and (2) they need cies, their distribution ranges, and the of Glass Spheres either positive buoyancy to bring the composition of the fauna. -
Characterisation of Syntactic Foams for Marine Applications
CHARACTERISATION OF SYNTACTIC FOAMS FOR MARINE APPLICATIONS A Thesis submitted by Zulzamri Salleh, MSc, BSc. (Hons.) For the award of Doctor of Philosophy 2017 i ii Abstract Syntactic foams are light weight particulate composites that use hollow particles (microballoons) as reinforcement in a polymer resin matrix. High strength microballoons provide closed cell porosity, which helps in reducing the weight of the material. Due to their wide range of possible applications, such as in marine structures, it is desirable to modify the physical and mechanical properties of syntactic foams in particular to achieve both high specific compressive strength and high energy absorption with minimal or no increase in density. Based on a literature review, it was found that marine applications of syntactic foams mainly focus on mechanical properties, on light weight as buoyancy aid materials, and on enhanced thermal insulators in the deep water pipeline industry. In order to achieve all these characteristics, attention needs to be placed on the determination of the effects on wall thickness, on the radius ratio () of glass microballons and on the presence of porosity in syntactic foams. The size of these parameters can be calculated and compared with observation by using SEM micrograph machine. In this study, the specific mechanical properties, particularly compressive and tensile properties with 2-10 weight percentages (wt.%) of glass microballoons, are investigated and discussed. It is shown that the mechanical properties, particularly compressive and tensile strength, decreased when glass microballoons with vinyl ester resin were added. The effect of porosity and voids content mainly contributed to a reduction of these results and this is discussed further in this study. -
Energy Absorption Performance of Eco-Core – a Syntactic Foam
Energy Absorption Performance of Eco-Core – A Syntactic Foam Raghu Panduranga1 and Kunigal N. Shivakumar2 North Carolina A&T State University, Greensboro, NC, 27411 and Larry Russell, Jr.3 U. S. Army Research Office, Research Triangle Park, NC 27709 Eco-Core is a fire resistant material that was made using large volume of Cenosphere and small volume of high char yield binder by syntactic process. This material has superior mechanical, excellent fire and toxicity properties and ideally suited for composite sandwich structures. The cellular structure of the core offers energy absorption capability against shock and impact. This paper assesses the energy absorption of Eco-Core as well as its modification by surface coating with polyurea and impregnation by polyurethane. Nomenclature σc = compression strength εc = failure strain εcrush = crushing strain Efoam = foam modulus Esolid = solid modulus EEA = energy absorption parameter I. Introduction ORE materials are used extensively throughout the composites industry to fabricate lightweight and stiff C sandwich structures. The sandwich structure offers an order of magnitude increased flexural stiffness compared to the solid laminates. The typical use of core materials is in sandwich construction consisting of top and bottom face sheets and middle core material. The face sheets are comparatively thin and are made of a material of high strength and stiffness. The core is relatively thick and provides stiffness and strength in the direction normal to the plane of the face sheet. In sandwich construction the face sheets carry the bending stresses and core carries the compression and shear stresses.1-3 A variety of core materials are used in the composites industry. -
Thermophysical Properties of Multifunctional Syntactic Foams Containing Phase Change Microcapsules for Thermal Energy Storage
polymers Article Thermophysical Properties of Multifunctional Syntactic Foams Containing Phase Change Microcapsules for Thermal Energy Storage Francesco Galvagnini *, Andrea Dorigato, Luca Fambri , Giulia Fredi and Alessandro Pegoretti Department of Industrial Engineering and INSTM Research Unit, University of Trento, Via Sommarive 9, 38123 Trento, Italy; [email protected] (A.D.); [email protected] (L.F.); [email protected] (G.F.); [email protected] (A.P.) * Correspondence: [email protected] Abstract: Syntactic foams (SFs) combining an epoxy resin and hollow glass microspheres (HGM) feature a unique combination of low density, high mechanical properties, and low thermal con- ductivity which can be tuned according to specific applications. In this work, the versatility of epoxy/HGM SFs was further expanded by adding a microencapsulated phase change material (PCM) providing thermal energy storage (TES) ability at a phase change temperature of 43 ◦C. At this aim, fifteen epoxy (HGM/PCM) compositions with a total filler content (HGM + PCM) of up to 40 vol% were prepared and characterized. The experimental results were fitted with statistical models, which resulted in ternary diagrams that visually represented the properties of the ternary systems and simplified trend identification. Dynamic rheological tests showed that the PCM increased the Citation: Galvagnini, F.; Dorigato, A.; viscosity of the epoxy resin more than HGM due to the smaller average size (20 µm vs. 60 µm) and Fambri, L.; Fredi, G.; Pegoretti, A. that the systems containing both HGM and PCM showed lower viscosity than those containing only Thermophysical Properties of one filler type, due to the higher packing efficiency of bimodal filler distributions. -
Tensile and Compressive Properties of Epoxy Syntactic Foams Reinforced by Short Glass Fiber
Indian Journal of Engineering & Materials Sciences Vol. 24, August 2017, pp. 283-289 Tensile and compressive properties of epoxy syntactic foams reinforced by short glass fiber Wei Yu*, Hailong Xue & Meng Qian Key Laboratory of Mechanical Reliability for Heavy Equipments and Large Structures of Hebei Province, Yanshan University, Qinhuangdao 066004, China Received 22 April 2015; accepted 29 March 2017 The hollow glass microsphere/epoxy resin syntactic foams reinforced by short glass fibers are fabricated. The microsphere is constant 5% weight ratio to the epoxy resin matrix and the fibers with weight ratio to the resin matrix are 5%, 10%, 20% and 30%. Their mechanical properties are studied by uniaxial compression test and tension test. The compressive deformation morphology and tensile fracture surfaces of syntactic foams are investigated. It is obtained that the compressive and tensile strength of syntactic foams are enhanced by adding fibers, and the 10% fiber weight ratio is found to be much more efficient, which shows 70% and 49% higher compressive strength and tensile strength respectively than that of syntactic foams without fiber content. However, the strength decreases with further addition of glass fiber beyond 10% weight ratio. The reason of strength enhancements is discussed. The compressive and tensile moduli are also enhanced by adding fibers. The ductility of composites is found to decrease with larger fiber filling. Keywords : Syntactic foams, Epoxy, Hollow glass microsphere, Glass fiber The composite of hollow particle filled polymer is mechanical properties and thermal properties by called syntactic foams. Hollow particles are usually experiment. It is shown that the tensile strength, made up of glass, ceramic, materials. -
E-SPHERES® Hollow Ceramic Microspheres
E-SPHERES® Hollow Ceramic Microspheres TECHNICAL DATA APPLICATION: ENGINEERED SYNTACTIC FOAM DESCRIPTION: Advanced functional additive and reinforcing filler with spherical hollow structure and ceramic composition. Its main characteristics are lightness, high compressive strength, thermal resistance (high melting point), chemically unreactive or inert and unique off-white colour. APPLICATION: E-SPHERES® Hollow Ceramic Microspheres (HCM) are utilised in the manufacturing of syntactic foam (synthesized composite materials). E-SPHERES® improve value and performance of products and manufacturing processes by delivering lower density, higher specific strength (strength divided by density), lower coefficient of thermal expansion, and, in some cases, radar or sonar transparency, and potential cost reduction. Typical applications include: Deep-sea buoyancy foams Cores for sandwich panels Helicopter and airplane components Blast mitigating materials Thermoforming plug assist tooling Sporting goods such as bowling balls, Radar transparent materials tennis rackets Acoustically attenuating materials Thermal insulating panels These are only examples of possible applications. ADVANTAGES VALUE IN USE Density and weight reduction thanks to volume displacement by low density functional filling material Increased stiffness due to high compressive strength and optimum filling of interspacial voids Improved impact resistance owing to its capacity to absorb energy and vibration within the binder matrix Improved synthesizing act as miniature bearings -
REINFORCEMENT of SYNTACTIC FOAM with Sic NANOPARTICLES
REINFORCEMENT OF SYNTACTIC FOAM WITH SiC NANOPARTICLES by Debdutta Das A Thesis submitted to The Faculty of The College of Engineering and Computer Science In Partial Fulfillment of the Requirements for the Degree of Master of Science Florida Atlantic University Boca Raton, Florida December 2009 ACKNOWLEDGEMENT I would like to thank Dr. Hassan Mahfuz for his direction, assistance and guidance in the preparation of this thesis. I also wish to thank the members of the supervisory committee, Dr. Palaniswamy Ananthakrishnan and Dr. Francisco Presuel-Moreno, for their valuable recommendations and suggestions. Financial support in the form of a research assistantship from the Office of Naval Research is gratefully acknowledged. I would like to thank my nanolab members for their valuable support. I would sincerely thank my family for their advice and support. Lastly, I would like to acknowledge a sincere appreciation of the above mentioned for the experience that is the foundation of future endeavors. iii ABSTRACT Author: Debdutta Das Title: Reinforcement of Syntactic Foam with SiC nanoparticles Institution: Florida Atlantic University Thesis Advisor: Dr. Hassan Mahfuz Degree: Master of Science Year: 2009 In this investigation, polymer precursor of syntactic foam has been reinforced with SiC nanoparticles to enhance mechanical and fracture properties. Derakane 8084 vinyl ester resin was first dispersed with 1.0 wt% of SiC particles using a sonic cavitation technique. In the next step, 30.0 wt% of microspheres (3M hollow glass borosilicate, S-series) were mechanically mixed with the nanophased vinyl ester resin, and cast into rectangular molds. A small amount of styrene was used as dilutant to facilitate mixing of microspheres. -
A Flexible Syntactic Foam for Shock Mitigation
North Carolina Agricultural and Technical State University Aggie Digital Collections and Scholarship Dissertations Electronic Theses and Dissertations 2011 A Flexible Syntactic Foam For Shock Mitigation JOGI C. GOWDA North Carolina Agricultural and Technical State University Follow this and additional works at: https://digital.library.ncat.edu/dissertations Recommended Citation GOWDA, JOGI C., "A Flexible Syntactic Foam For Shock Mitigation" (2011). Dissertations. 1. https://digital.library.ncat.edu/dissertations/1 This Dissertation is brought to you for free and open access by the Electronic Theses and Dissertations at Aggie Digital Collections and Scholarship. It has been accepted for inclusion in Dissertations by an authorized administrator of Aggie Digital Collections and Scholarship. For more information, please contact [email protected]. A FLEXIBLE SYNTACTIC FOAM FOR SHOCK MITIGATION by JOGI C. GOWDA A dissertation submitted to the graduate faculty in partial fulfillment of the requirements for the degree of DOCTOR OF PHILOSOPHY Department: Mechanical Engineering Major: Mechanical Engineering Advisor: Dr. Kunigal Shivakumar North Carolina A&T State University Greensboro, North Carolina 2011 ABSTRACT Gowda, Jogi. A FLEXIBLE SYNTACTIC FOAM FOR SHOCK MITIGATION. (Major Advisor Dr. Kunigal Shivakumar), North Carolina Agricultural and Technical State University. This dissertation focused on the development and assessment of flexible microballoons filled elastomeric foam for shock mitigation applications. The overall goal of the research was to develop a flexible syntactic foam that has controllable bulk modulus, compressibility and shock mitigation characteristics and to validate these characteristics by experiments. Elastomer LP-2 with solid manganese dioxide and uncured BJO-093 hollow Pµb were chosen for making the syntactic foam. Hand mixing and room temperature curing was used to make foams of 0 to 30% weight of filler, which amounts to 0 to 60% of volume of the filler. -
A Self Healing Smart Syntactic Foam Based Grid Stiffened Sandwich Structure
Louisiana State University LSU Digital Commons LSU Doctoral Dissertations Graduate School 2009 A self healing smart syntactic foam based grid stiffened sandwich structure Manu Kuruvila John Louisiana State University and Agricultural and Mechanical College, [email protected] Follow this and additional works at: https://digitalcommons.lsu.edu/gradschool_dissertations Part of the Mechanical Engineering Commons Recommended Citation John, Manu Kuruvila, "A self healing smart syntactic foam based grid stiffened sandwich structure" (2009). LSU Doctoral Dissertations. 822. https://digitalcommons.lsu.edu/gradschool_dissertations/822 This Dissertation is brought to you for free and open access by the Graduate School at LSU Digital Commons. It has been accepted for inclusion in LSU Doctoral Dissertations by an authorized graduate school editor of LSU Digital Commons. For more information, please [email protected]. A SELF HEALING SMART SYNTACTIC FOAM BASED GRID STIFFENED SANDWICH STRUCTURE A Dissertation Submitted to the Graduate Faculty of Louisiana State University and Agricultural and Mechanical College in partial fulfillment of the requirements for the degree of Doctor of Philosophy in The Department of Mechanical Engineering by Manu Kuruvila John B.Tech, Mahatma Gandhi University, India, 2001. M.S., Tuskegee University, 2004. December 2009 ACKNOWLEDGEMENTS I would like to extend my heartfelt gratitude and thanks to Dr. Guoqiang Li, my major professor for his guidance and support provided during the course of this research work and the confidence he had in me. This work would not have been possible without his extensive help, valuable insight and time he invested in this research work. He has been my constant inspiration and mentor for both my course work and research work. -
United States Patent [191 [11] Patent Number: 4,595,623 '
UnitedO States Patent [191 [11] Patent Number: 4,595,623 ' Du Pont et a1; [45] Date of Patent: Jun. 17, 1986 [54] FIBER-REINFORCED SYNTACI‘IC FOAM 3,730,920 5/ 1973 D’Alessandro 521/54 COMPOSITES AND METHOD OF FORMING 3,849,350 11/1974 Matsko . .. 521/54 SAME 4,005,033 l/1977 Georgeau et a1. 521/54 4,031,059 6/1977 Strauss . .. 521/54 [75] Inventors: Preston S. Du Pont, Northridge; 4,107,134 8/1978 Dawans . .. 521/54 Janet E, Freeman, Pasadena; Robert 4,112,179 9/1978 Maccalous et al. 521/54 E. Ritter, Palos Verdes Estates; Alois 1:; gall?klf - - - - - - - - - - ' - - wlmna'm’- Palos Verdes’ an of cam‘' 4,363,883, , 12/1982 Gaglianiag 1am eet aal. .... .,1. 521/54 [73] Assignee: Hughes Aircraft Company, Los 4,410,639 10/1983 Bouley ........ .. 521/54 Angeles, Calif. 4,412,012 10/1983 Bouley et a1. 521/54 4,447,565 5/1984 Lula et a1. ........................... .. 521/54 [21] App]. No.: 607,847 ' Primary Examiner—-M0rton Foelak [22] Flled: May 79 1984 Attorney, Agent, or Firm-M. E. Lachman; A. W. [51] 1111.01.33 .............................................. .. B32B 3/00 Karambelas [52] US. Cl. .................................. .. 428/195; 428/209; [57] ABSTRACI‘ 521/54; 521/82; 521/99; 521/134; 521/135; _ _ _ _ _ 521/136; 521/138; 523/213; 523/219 Fiber-remforced syntactic foam composites having a [58] Field of Search ................ .. 521/54; 523/218, 219; 10W speci?c gravity and a low coefficient of thermal 423/195, 209 expansion suitable for forming lightweight structures _ for spacecraft applications are prepared from a mixture [56] References cued of a heat curable thermosetting resin, hollow micro U.S.