Comprehensive Utilization Strategy of Huadian Oil Shales Along with Jilin’S Energy Problems and Previous Oil Shale Exploitation and Application Experiences
Total Page:16
File Type:pdf, Size:1020Kb
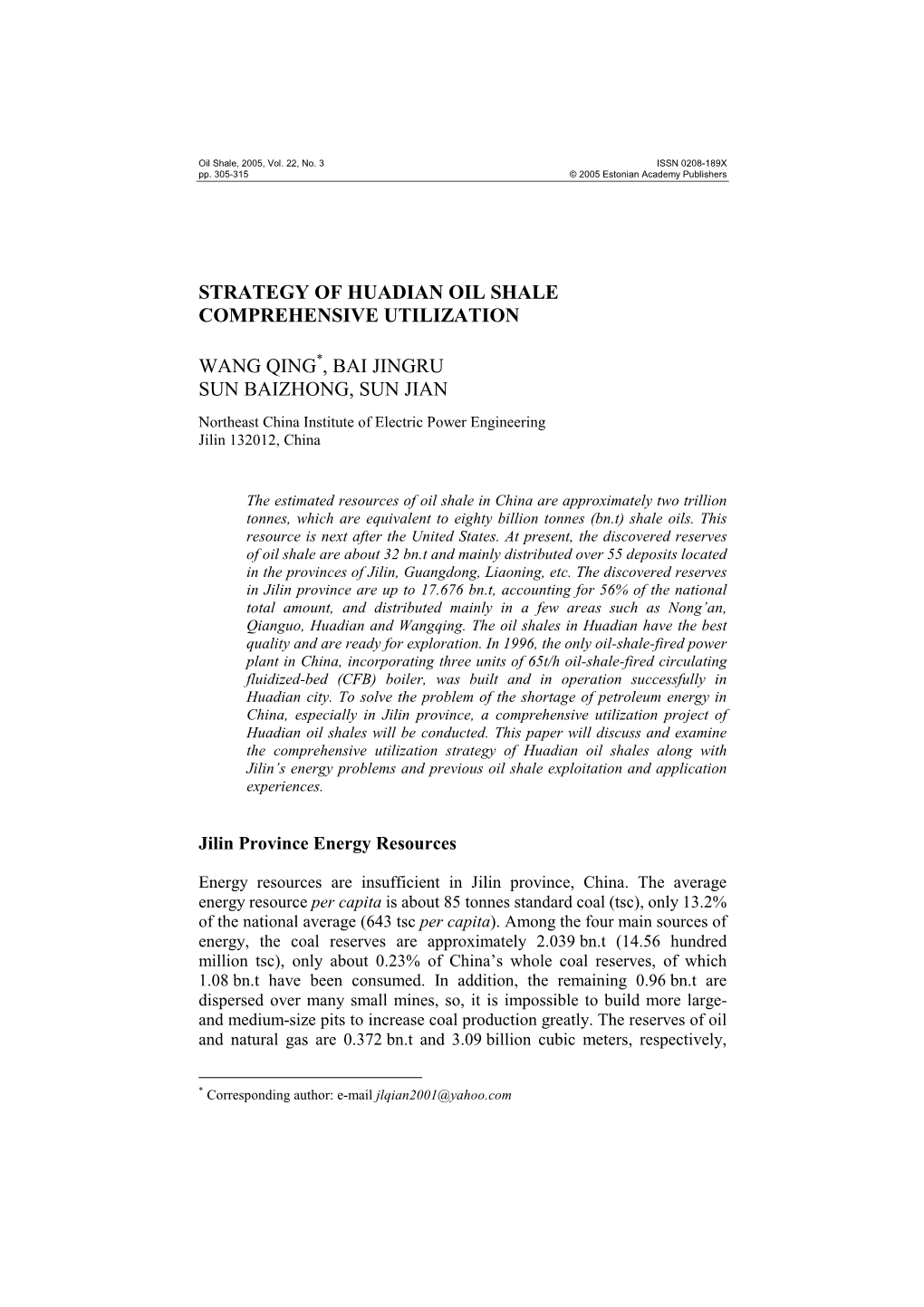
Load more
Recommended publications
-
Lithium Enrichment in the No. 21 Coal of the Hebi No. 6 Mine, Anhe Coalfield, Henan Province, China
minerals Article Lithium Enrichment in the No. 21 Coal of the Hebi No. 6 Mine, Anhe Coalfield, Henan Province, China Yingchun Wei 1,* , Wenbo He 1, Guohong Qin 2, Maohong Fan 3,4 and Daiyong Cao 1 1 State Key Laboratory of Coal Resources and Safe Mining, College of Geoscience and Surveying Engineering, China University of Mining and Technology, Beijing 100083, China; [email protected] (W.H.); [email protected] (D.C.) 2 College of Resources and Environmental Science, Hebei Normal University, Shijiazhuang 050024, China; [email protected] 3 Departments of Chemical and Petroleum Engineering, and School of Energy Resources, University of Wyoming, Laramie, WY 82071, USA; [email protected] 4 School of Civil and Environmental Engineering, Georgia Institute of Technology, Mason Building, 790 Atlantic Drive, Atlanta, GA 30332, USA * Correspondence: [email protected] Received: 18 May 2020; Accepted: 3 June 2020; Published: 5 June 2020 Abstract: Lithium (Li) is an important strategic resource, and with the increasing demand for Li, there are some limitations in the exploitation and utilization of conventional deposits such as the pegmatite-type and brine-type Li deposits. Therefore, it has become imperative to search for Li from other sources. Li in coal is thought to be one of the candidates. In this study, the petrology, mineralogy, and geochemistry of No. 21 coal from the Hebi No. 6 mine, Anhe Coalfield, China, was reported, with an emphasis on the distribution, modes of occurrence, and origin of Li. The results show that Li is enriched in the No. 21 coal, and its concentration coefficient (CC) value is 6.6 on average in comparison with common world coals. -
China's Unconventional Oil: a Review of Its Resources and Outlook for Long-Term Production
Energy xxx (2015) 1e12 Contents lists available at ScienceDirect Energy journal homepage: www.elsevier.com/locate/energy China's unconventional oil: A review of its resources and outlook for long-term production Jianliang Wang a, *, Lianyong Feng a, Mohr Steve b, Xu Tang a, Tverberg E. Gail c, Ho€ok€ Mikael d a School of Business Administration, China University of Petroleum, Beijing, China b Institute for Sustainable Futures, University of Technology Sydney, Sydney, Australia c Our Finite World, 1246 Shiloh Trail East NW, Kennesaw, GA 30144, USA d Global Energy Systems, Department of Earth Science, Uppsala University, Sweden article info abstract Article history: Due to the expected importance of unconventional oil in China's domestic oil supply, this paper first Received 9 July 2014 investigates the four types of China's unconventional oil resources comprehensively: heavy and extra- Received in revised form heavy oil, oil sands, broad tight oil and kerogen oil. Our results show that OIP (Oil-in-Place) of these 11 December 2014 four types of resources amount to 19.64 Gt, 5.97 Gt, 25.74 Gt and 47.64 Gt respectively, while TRRs Accepted 16 December 2014 (technically recoverable resources) amount to 2.24 Gt, 2.26 Gt, 6.95 Gt and 11.98 Gt respectively. Next, the Available online xxx Geologic Resources Supply-Demand Model is used to quantitatively project the long-term production of unconventional oil under two resource scenarios (TRR scenario and Proved Reserve Cumulative Pro- Keywords: þ Unconventional oil duction scenario). Our results indicate that total unconventional oil production will peak in 2068 at 0.351 Gt in TRR scenario, whereas peak year and peak production of PR (proved reserves) CP (Cu- Production modeling þ Resources mulative Production) scenario are 2023 and 0.048 Gt, significantly earlier and lower than those of TRR Chinese oil scenario. -
EMD Oil Shale Committee
EMD Oil Shale Committee EMD Oil Shale Committee Annual Report – 2015 Alan Burnham, Chair April 29, 2015 Vice-Chairs: Dr. Lauren Birgenheier (Vice-Chair – University) University of Utah Mr. Ronald C. Johnson (Vice-Chair – Government) U.S. Geological Survey Dr. Mariela Araujo (Vice-Chair – Industry) Shell International Exploration and Production Highlights Progress on oil shale continued in both the United States and around the world, but with a greater sense of urgency in countries with lesser quantities of conventional energy sources. New production capacity was brought on line in Estonia and China, and plans for production moved forward in Jordan. However, reductions and delays in development are starting to appear, particularly in the United States, due to the low price of crude oil. The current status is in flux, but it is too early to know whether we are seeing a repeat of the 1980s. In the U.S., the Utah Division of Water Quality issued a groundwater permit to Red Leaf Resources, which now has the go-ahead to establish a small-scale commercial production system based on the EcoShale process as a joint venture with Total. A challenge by environmental groups was settled by allowing access to groundwater monitoring data. However, that project is now delayed by a year or more, and the time will be used to accelerate design optimization. TomCo received temporary approval to establish a commercial operation using the EcoShale process 15 miles from the Red Leaf operation. Enefit is making progress getting permits for development of its private lands in Utah and successfully resolved a potential environmental roadblock by working with local officials, who created a conservation plan for a potentially rare plant. -
Technology Portfolio of China Liquid Fuel Industry to Address Energy Security and Environmentally Friendly Development
YSSP Report Young Scientists Summer Program Technology portfolio of China liquid fuel industry to address energy security and environmentally friendly development Bingqing Ding ([email protected]) Approved by: Supervisor: Tieju Ma, Marek Makowski and Behnam Zakeri Program: Transitions to New Technologies Date: 30 October 2020 This report represents the work completed by the author during the IIASA Young Scientists Summer Program (YSSP) with approval from the YSSP supervisor. This research was funded by IIASA and its National Member Organizations in Africa, the Americas, Asia, and Europe. This work is licensed under a Creative Commons Attribution-NonCommercial 4.0 International License. For any commercial use please contact [email protected] YSSP Reports on work of the International Institute for Applied Systems Analysis receive only limited review. Views or opinions expressed herein do not necessarily represent those of the institute, its National Member Organizations, or other organizations supporting the work. ii ZVR 524808900 Table of Contents Abstract iv Acknowledgments v About the authors v 1. Introduction 1 2. Technological options 3 3. System optimization model 4 3.1 Model framework _______________________________________________________ 4 3.2. Definition of notations ___________________________________________________ 5 3.3 Model _________________________________________________________________ 6 4. Data collection and parameter assumptions 9 4.1. Demand for diesel and gasoline ____________________________________________ 9 4.2. Feedstock prices in the base year __________________________________________ 9 5. Scenario analysis 10 5.1 Four scenarios _________________________________________________________ 10 5.2 Result under the four scenarios ___________________________________________ 11 5.2.1 Capacity configuration of different technologies __________________________ 11 5.2.2 The accumulated total system cost ____________________________________ 13 5.2.3 Sensitivity analysis _________________________________________________ 14 6. -
Elemental Characteristics of Lacustrine Oil Shale and Its Controlling Factors of Palaeo-Sedimentary Environment on Oil Yield
Acta Geochim (2018) 37(2):228–243 https://doi.org/10.1007/s11631-017-0206-y ORIGINAL ARTICLE Elemental characteristics of lacustrine oil shale and its controlling factors of palaeo-sedimentary environment on oil yield: a case from Chang 7 oil layer of Triassic Yanchang Formation in southern Ordos Basin 1 1 2 2 Delu Li • Rongxi Li • Zengwu Zhu • Feng Xu Received: 27 April 2017 / Revised: 4 July 2017 / Accepted: 20 July 2017 / Published online: 27 July 2017 Ó Science Press, Institute of Geochemistry, CAS and Springer-Verlag GmbH Germany 2017 Abstract As an important unconventional resource, oil Paleosalinity and paleohydrodynamics have an inconspic- shale has received widespread attention. The oil shale of uous influence on oil yield. the Chang 7 oil layer from Triassic Yanchang Formation in Ordos Basin represents the typical lacustrine oil shale in Keywords Elemental geochemistry Á Palaeosedimentary Á China. Based on analyzing trace elements and oil yield Main controlling factors Á Lacustrine oil shale Á Triassic Á from boreholes samples, characteristics and paleo-sedi- Ordos Basin mentary environments of oil shale and relationship between paleo-sedimentary environment and oil yield were studied. With favorable quality, oil yield of oil shale varies 1 Introduction from 1.4% to 9.1%. Geochemical data indicate that the paleo-redox condition of oil shale’s reducing condition Regarded as one of the important unconventional from analyses of V/Cr, V/(V ? Ni), U/Th, dU, and authi- resources, oil shale is a solid organic sedimentary rock genic uranium. Equivalent Boron, Sp, and Sr/Ba illustrate (Liu et al. -
YUSEI HOLDINGS LIMITED 友成控股有限公司* (Incorporated in the Cayman Islands with Limited Liability) (Stock Code: 96)
THIS CIRCULAR IS IMPORTANT AND REQUIRES YOUR IMMEDIATE ATTENTION If you are in doubt as to any aspect of this circular, the Whitewash Waiver or the action to be taken, you should consult a licensed securities dealer or registered institution in securities, a bank manager, solicitor, professional accountant, or other professional adviser. If you have sold or transferred all your shares in YUSEI HOLDINGS LIMITED, you should at once hand this document and the accompanying form to the purchaser or to the licensed securities dealer or registered institution in securities or other agent through whom the sale was effected for transmission to the purchaser. The Securities and Futures Commission of Hong Kong, Hong Kong Exchanges and Clearing Limited and The Stock Exchange of Hong Kong Limited take no responsibility for the contents of this circular, make no representation as to its accuracy or completeness and expressly disclaim any liability whatsoever for any loss howsoever arising from or in reliance upon the whole or any part of the contents of this circular. This circular appears for information purposes only and does not constitute an invitation or offer to acquire, purchase or subscribe for any securities. YUSEI HOLDINGS LIMITED 友成控股有限公司* (Incorporated in the Cayman Islands with limited liability) (Stock Code: 96) (1) CONNECTED TRANSACTION RELATING TO THE SUBSCRIPTION FOR NEW SHARES; (2) APPLICATION FOR WHITEWASH WAIVER; AND (3) NOTICE OF EGM Financial Adviser to the Company First Shanghai Capital Limited Independent Financial Adviser to the Independent Board Committee and the Independent Shareholders REORIENT Financial Markets Limited A letter from the Board is set out on pages 5 to 16 of this circular. -
China Wind Sector
China Utilities 21 January 2016 China Wind Sector Initiation: Less is more We see multi-year headwinds for the China Wind Sector, including worsening curtailment, tariff cuts, and slowing capacity addition Wind IPPs with large existing capacities and fewer pipeline projects in Zones I and II should fare best; valuations look to be at trough levels Dennis Ip, CFA (852) 2848 4068 We prefer balanced play Huadian Fuxin and scaled play Longyuan; [email protected] wind equipment and small grid-curtailed IPPs are likely to suffer Scott Chui (852) 2848 4443 [email protected] See important disclosures, including any required research certifications, beginning on page 127 China Wind Sector: 21 January 2016 Table of contents Investment thesis ..................................................................................................... 6 Daiwa’s 1T4C approach .................................................................................................... 6 Less is more ..................................................................................................................... 7 What to expect in each of the next 3 years ....................................................................... 8 Fuxin and Longyuan are our preferred picks ..................................................................... 9 China Wind Sector outlook — 1T4C...................................................................... 10 FiT cut should enhance market efficiency ........................................................................10 -
Effects of Secondary Reaction of Primary Volatiles on Oil/Gas Yield and Quality from Oil Shale Pyrolysis
ISSN: 2638-1974 International Journal of Petrochemistry and Research Research Article Open Access Effects of Secondary reaction of Primary Volatiles on Oil/gas Yield and Quality from Oil Shale Pyrolysis Yuming Zhang1*, Rongxuan Linghu1, Lei Huang1, Liang Zhang1, Guogang Sun1 and Shu Zhang2* 1State Key Laboratory of Heavy Oil Processing, China University of Petroleum-Beijing, Beijing 102249, P.R.China 2College of Materials Science and Engineering, Nanjing Forestry University, Nanjing 210037, Jiangsu, P.R. China Article Info Abstract *Corresponding authors: The reaction behaviors of primary volatiles from oil shale pyrolysis were investigated Yuming Zhang using a two-stage reactor under different in-situ thermal reaction conditions. The secondary State Key Laboratory of Heavy Oil Processing reaction parameters, such as conversion temperature, reaction atmosphere and residence China University of Petroleum-Beijing time, were studied for their effects on the pyrolysis oil/gas yield and quality. The results Beijing 102249, P.R.China showed that the reaction temperature had a profound influence on the oil and gas yield, Tel: +86-15001296129 as indicated by the fact that the pyrolyzed shale oil and gas yield reduced by 15% (mass) E-mail: [email protected] and 20% (mass) respectively, with the temperature of 2nd stage reactor increasing from Shu Zhang ° ° College of Materials Science and 600 C to 650 C. Comparing with a nitrogen atmosphere, the liquid oil yield could enhance Engineering by 5% when steam was added as the reaction atmosphere in the second stage, and the Nanjing Forestry University corresponding oil was mainly concentrated in the gasoline and diesel distillations, that is, Nanjing 210037 boiling point <350°C. -
Geology of the Chang 7 Member Oil Shale of the Yanchang Formation of the Ordos Basin in Central North China
Downloaded from http://pg.lyellcollection.org/ by guest on September 26, 2021 Review article Petroleum Geoscience Published Online First https://doi.org/10.1144/petgeo2018-091 Geology of the Chang 7 Member oil shale of the Yanchang Formation of the Ordos Basin in central north China Bai Yunlai & Ma Yuhua* Northwest Branch of Research Institute of Petroleum Exploration and Development (NWGI), PetroChina, Lanzhou 730020, Gansu, China * Correspondence: [email protected] Abstract: We present a review of the Chang 7 Member oil shale, which occurs in the middle–late Triassic Yanchang Formation of the Ordos Basin in central north China. The oil shale has a thickness of 28 m (average), an area of around 30 000 km2 and a Ladinian age. It is mainly brown-black to black in colour with a laminar structure. It is characterized by average values of 18 wt% TOC (total organic carbon), 8 wt% oil yield, a 8.35 MJ kg−1 calorific value, 400 kg t−1 hydrocarbon productivity and kerogen of type I–II1, showing a medium quality. On average, it comprises 49% clay minerals, 29% quartz, 16% feldspar and some iron oxides, which is close to the average mineral composition of global shale. The total SiO2 and Al2O3 comprise 63.69 wt% of the whole rock, indicating a medium ash type. The Sr/Ba is 0.33, the V/Ni is 7.8, the U/Th is 4.8 and the FeO/Fe2O3 is 0.5, indicating formation in a strongly reducing, freshwater or low-salinity sedimentary environment. Multilayered intermediate-acid tuff is developed in the basin, which may have promoted the formation of the oil shale. -
Energy Markets in China and the Outlook for CMM Project
U.S. EP.NSII Coalbed Methane Energy Markets in China and the Outlook for CMM Project Development in Anhui, Chongqing, Henan, Inner Mongolia, and Guizhou Provinces Energy Markets in China and the Outlook for CMM Project Development in Anhui, Chongqing, Henan, Inner Mongolia, and Guizhou Provinces Revised, April 2015 Acknowledgements This publication was developed at the request of the U.S. Environmental Protection Agency (USEPA), in support of the Global Methane Initiative (GMI). In collaboration with the Coalbed Methane Outreach Program (CMOP), Raven Ridge Resources, Incorporated team members Candice Tellio, Charlee A. Boger, Raymond C. Pilcher, Martin Weil and James S. Marshall authored this report based on feasibility studies performed by Raven Ridge Resources, Incorporated, Advanced Resources International, and Eastern Research Group. 2 Disclaimer This report was prepared for the U.S. Environmental Protection Agency (USEPA). This analysis uses publicly available information in combination with information obtained through direct contact with mine personnel, equipment vendors, and project developers. USEPA does not: (a) make any warranty or representation, expressed or implied, with respect to the accuracy, completeness, or usefulness of the information contained in this report, or that the use of any apparatus, method, or process disclosed in this report may not infringe upon privately owned rights; (b) assume any liability with respect to the use of, or damages resulting from the use of, any information, apparatus, method, or process -
Building a Better Mousetrap: Patenting
7-Zhong FINAL (Do Not Delete) 5/18/2016 10:17 PM RED GOLD: THE LEGAL FRAMEWORK GOVERNING FOREIGN INVESTMENTS IN CHINA’S OIL INDUSTRY Jackie Zhong* I. INTRODUCTION ................................................................. 654 II. BACKGROUND ................................................................... 655 A. A Brief Look at China’s Oil Industry ........................ 655 B. A Brief Look at Foreign Investments in China.......... 658 III. A CLOSER LOOK AT FOREIGN INVESTMENTS IN CHINESE OIL .................................................................................... 661 A. Oil Ownership and Upstream Production ................ 663 B. Petroleum-Related Laws and Regulations ................ 665 C. Laws and Regulations Governing Foreign Investment ................................................................. 670 D. Implementing the Mineral Resources Law ................ 672 E. When Investing in the Chinese Oil Market ............... 674 F. Dispute Resolution ..................................................... 678 G. A Brief Discussion of Taxes and Fees ........................ 681 H. Guarding Against Corruption ................................... 684 IV. CONCLUSION ..................................................................... 686 “So valuable is black gold to our very way of life that wars have been waged for it...” -BLACK GOLD: THE STORY OF OIL IN OUR LIVES- * Jackie Zhong is a 2016 Juris Doctor candidate at the University of Houston Law Center. She received a Bachelor of Arts in English/Creative Writing -
Organic Geochemistry and Elements Distribution in Dahuangshan Oil Shale, Southern Junggar Basin: Origin of Organic Matter and Depositional Environment
International Journal of Coal Geology 115 (2013) 41–51 Contents lists available at SciVerse ScienceDirect International Journal of Coal Geology journal homepage: www.elsevier.com/locate/ijcoalgeo Organic geochemistry and elements distribution in Dahuangshan oil shale, southern Junggar Basin: Origin of organic matter and depositional environment Shu Tao a,b,⁎, Dazhen Tang a, Hao Xu a, Jianlong Liang a, Xuefeng Shi c a Coal Reservoir Laboratory of National CBM Engineering Center, School of Energy Resources, China University of Geosciences (Beijing), Beijing 100083, China b Coalbed Methane Resources and Reservoir Formation Process Key Laboratory of Ministry of Education, China University of Mining and Technology, Xuzhou 221116, China c CNOOC Energy Technology & Services-Oilfield Engieering Research Institute, Tianjin 300452, China article info abstract Article history: The Dahuangshan oil shale, located in the northern Bogda Mountain, on the southern margin of the Junggar Received 3 March 2013 Basin, was deposited in a Late Permian lacustrine environment. A combined investigation of element and Received in revised form 14 May 2013 organic geochemistry was performed to define the source rock potential, the paleoenvironment, and source Accepted 16 May 2013 of the organic matter. Thick sequences of oil shales with an average thickness of 638 m were deposited in Available online 25 May 2013 Lucaogou Formation which mainly consists of oil shale, argillaceous dolomite, silty claystone, tuff, limestone, and dolomitic marl. A spot of plant stem fossils and abundance of pyrite crystals, fishtail and fish skeleton can Keywords: Geochemistry also be found there. Rare earth elements Analyzed oil shale samples from Dahuangshan area are characterized by high total organic carbon (TOC) con- Paleoenvironment tents (5.6–34.75%), S2 (22.65–199.25 mg HC/g rock), hydrogen index (HI, 359–1068 mg HC/g TOC), and oil Oil shale yield (4.9–26.6%), indicating the oil shales have excellent source rock potential.