3.1 Functions of Condensers
Total Page:16
File Type:pdf, Size:1020Kb
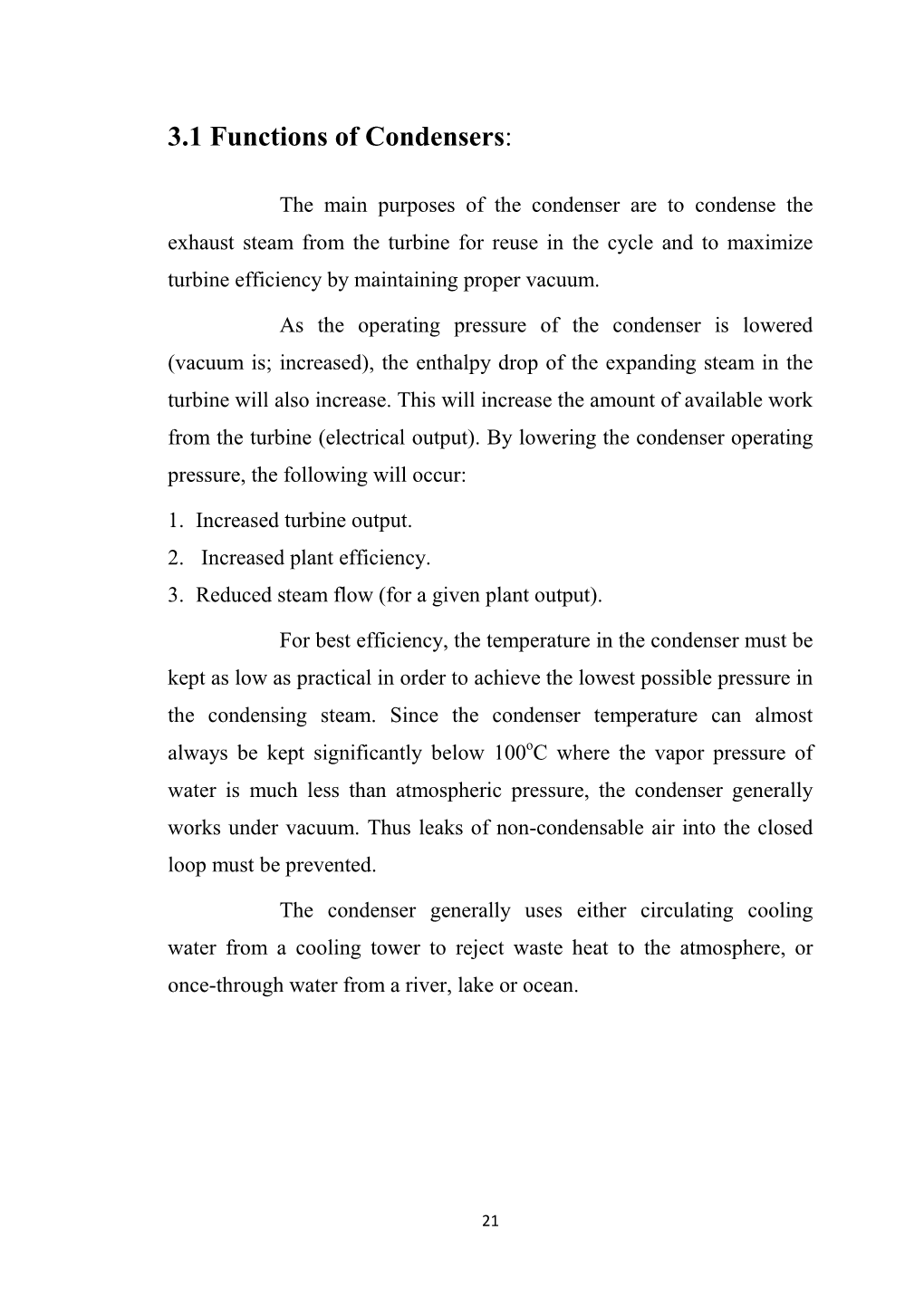
Load more
Recommended publications
-
Compressible Flows for Fluidic Control in Microdevices
COMPRESSIBLE FLOWS FOR FLUIDIC CONTROL IN MICRODEVICES by Dustin S. Chang A dissertation submitted in partial fulfillment of the requirements for the degree of Doctor of Philosophy (Chemical Engineering) in The University of Michigan 2010 Doctoral Committee: Professor Mark A. Burns, Chair Professor Robert M. Ziff Associate Professor Luis P. Bernal Associate Professor Michael Mayer © Dustin S. Chang 2010 To my mom and dad, Sweson and Chaohui, and my grandparents, Po-High and Peyuk … Thank you for all your sacrifices. ii ACKNOWLEDGEMENTS To the casual observer, a doctoral thesis may appear to be the product of a single dedicated—albeit misguided—individual after multiple years of toil. Anyone that has survived the experience will most assuredly tell you that he could not have done it without the many people who supported him along the way. Beginning long before graduate school, my family has been a constant source of encouragement, well-meaning criticism, and material support. I am hugely grateful for my aunts and uncles who never failed to go the extra mile in taking care of me, teaching me, and challenging me to improve. Aunt Hsueh-Rong, Aunt Nancy, Aunt Chao-Lin, Uncle Jeff, Aunt Tina, and Uncle Ming ... Thank you for your love. The only people potentially deserving greater appreciation than these are my mother and father and my grandparents. I have no doubt that none of my meager accomplishments would have been possible without your prayers and unconditional support, both moral and financial. I also have no doubt that all of the aforementioned people are infinitely more enamored with the idea of a Ph.D. -
Pressure and Piezometry (Pressure Measurement)
PRESSURE AND PIEZOMETRY (PRESSURE MEASUREMENT) What is pressure? .......................................................................................................................................... 1 Pressure unit: the pascal ............................................................................................................................ 3 Pressure measurement: piezometry ........................................................................................................... 4 Vacuum ......................................................................................................................................................... 5 Vacuum generation ................................................................................................................................... 6 Hydrostatic pressure ...................................................................................................................................... 8 Atmospheric pressure in meteorology ...................................................................................................... 8 Liquid level measurement ......................................................................................................................... 9 Archimedes' principle. Buoyancy ............................................................................................................. 9 Weighting objects in air and water ..................................................................................................... 10 Siphons ................................................................................................................................................... -
Aerodynamic Analysis of the Undertray of Formula 1
Treball de Fi de Grau Grau en Enginyeria en Tecnologies Industrials Aerodynamic analysis of the undertray of Formula 1 MEMORY Autor: Alberto Gómez Blázquez Director: Enric Trillas Gay Convocatòria: Juny 2016 Escola Tècnica Superior d’Enginyeria Industrial de Barcelona Aerodynamic analysis of the undertray of Formula 1 INDEX SUMMARY ................................................................................................................................... 2 GLOSSARY .................................................................................................................................... 3 1. INTRODUCTION .................................................................................................................... 4 1.1 PROJECT ORIGIN ................................................................................................................................ 4 1.2 PROJECT OBJECTIVES .......................................................................................................................... 4 1.3 SCOPE OF THE PROJECT ....................................................................................................................... 5 2. PREVIOUS HISTORY .............................................................................................................. 6 2.1 SINGLE-SEATER COMPONENTS OF FORMULA 1 ........................................................................................ 6 2.1.1 Front wing [3] ....................................................................................................................... -
Fluid Mechanics Policy Planning and Learning
Science and Reactor Fundamentals – Fluid Mechanics Policy Planning and Learning Fluid Mechanics Science and Reactor Fundamentals – Fluid Mechanics Policy Planning and Learning TABLE OF CONTENTS 1 OBJECTIVES ................................................................................... 1 1.1 BASIC DEFINITIONS .................................................................... 1 1.2 PRESSURE ................................................................................... 1 1.3 FLOW.......................................................................................... 1 1.4 ENERGY IN A FLOWING FLUID .................................................... 1 1.5 OTHER PHENOMENA................................................................... 2 1.6 TWO PHASE FLOW...................................................................... 2 1.7 FLOW INDUCED VIBRATION........................................................ 2 2 BASIC DEFINITIONS..................................................................... 3 2.1 INTRODUCTION ........................................................................... 3 2.2 PRESSURE ................................................................................... 3 2.3 DENSITY ..................................................................................... 4 2.4 VISCOSITY .................................................................................. 4 3 PRESSURE........................................................................................ 6 3.1 PRESSURE SCALES ..................................................................... -
Fuel Injection
Fuel injection • Fuel injection is a system for mixing fuel with air in an internal combustion engine. It has become the primary fuel delivery system used in gasoline automotive engines, having almost comppyletely replaced carburetors in the late 1980s. • The carburetor was invented by Karl Benz (founder of Mercedes‐Benz) in 1885 and patented in 1886. • Carburetors were the usual fuel delivery method for almost all gasoline (petrol)‐ fuelled engines up until the late 1980s, when fuel injection became the preferred method of automotive fuel delivery. In the U.S. market, the last carbureted cars were the 1990 Oldsmo bile CtCustom CiCruiser, BikBuick EttEstate Wagon, and SbSubaru Justy, and the last carbureted light truck was the 1994 Isuzu. Elsewhere, Lada cars used carburetors until 1996. A majority of motorcycles still use carburetors due to lower cost and throttle response problems with early injection set ups, but as of 2005, many new models are now being introduced with fuel injection. Internal combustion Engines: Carburetor, Fuel injection Carburetors are still found in small engines and in older or specialized automobiles, such as those designed for stock car racing. Dr. Primal Fernando • A fuel injection system is designed and calibrated specifically for the type(s) of [email protected] fuel it will handle. Most fuel injection systems are for gasoline or diesel Ph: (081) 2393608 applications. 1 2 Gas Review November 1913 Well, lets see if we can figure it out…… Used on tractors, boats, and stationary engines, including the Waterloo -
Flow Measurment by Venturi Meter and Orifice Meter
FLOW MEASUREMENT BY VENTURI METER AND ORIFICE METER Objectives: To find the coefficient of discharge of a venturi meter To find the coefficient of discharge of an orifice meter Theory: Venturi meter The venturi meter has a converging conical inlet, a cylindrical throat and a diverging recovery cone (Fig.1). It has no projections into the fluid, no sharp corners and no sudden changes in contour. Flowrate Q Inlet Throat Diameter D1 Diameter D2 Velocity V1 Velocity V2 Area of cross-section Area of cross-section S1 S2 Fig. 1 Venturi meter The converging inlet section decreases the area of the fluid stream, causing the velocity to increase and the pressure to decrease. At the centre of the cylindrical throat, the pressure will be at its lowest value, where neither the pressure nor the velocity will be changing. As the fluid enters the diverging section, the pressure is largely recovered lowering the velocity of the fluid. The major disadvantages of this type of flow detection are the high initial costs for installation and difficulty in installation and inspection. The Venturi effect is the reduction in fluid pressure that results when a fluid flows through a constricted section of pipe. The fluid velocity must increase through the constriction to satisfy the equation of continuity, while its pressure must decrease due to conservation of energy: the gain in kinetic energy is balanced by a drop in pressure or a pressure gradient force. An equation for the drop in pressure due to Venturi effect may be derived from a combination of Bernoulli’s principle and the equation of continuity. -
Road Vehicle Aerodynamic Design Underbody Influence
Chalmers University of Technology RRooaadd VVeehhiiccllee AAeerrooddyynnaammiicc DDeessiiggnn UUnnddeerrbbooddyy iinnfflluueennccee Team 2 Martín Oscar Taboada Di Losa [email protected] Dennys Enry Barreto Gomes [email protected] Bartosz Bien [email protected] Sascha Oliver Netuschil [email protected] Torsten Hensel [email protected] 1 Index Introduction ………………………………………..…….…………………………………. 3 Ground effect …………………………………….….……………………………………… 4 Examples of application in racing cars …………..…………………………………………. 6 Street cars ……………………………………..…………………………………………….. 8 Problems with the underbody effects …………….………………………………………… 11 References …………………………………………………………………………………… 12 2 1. Introduction [1.1] In the 1960s the use of soft rubber compounds and wider tyres, pioneered particularly by Lotus, demon- strated that good road adhesion and hence cornering ability was just as important as raw engine power in producing low lap times. It was found surprising that the friction or slip resistance force could be greater than the contact force between the two surfaces, giving a coefficient of friction greater than 1. The maxi- = ⋅ mum lateral force on a tyre is related to the down load by: Fy k N [1.1], where k is the maximum lat- eral adhesion or cornering coefficient, and is dependant on the tyre-road contact. Besides on the tyre and the suspension tuning, there is another factor in which is possible to work: the normal force. There are several alternatives to increase the down load: • increasing the mass of the vehicle: this effectively increase the maximum lateral force that the vehi- cle can handle, but doesn’t improve at all the cor- nering characteristics, due to the fact that the cen- tripetal forces generated in a turn are given by the v 2 following formula: F = m ⋅ a = m ⋅ [1.2] c c r which, for a given radius and tangential speed, is only dependant on the mass of the vehicle, so the increase in mass means that the centripetal force required increases by an equal amount; Fig. -
'Venturi Effect' in Passage Ventilation Between Two Non-Parallel Buildings
Revisiting the ‘Venturi effect’ in passage ventilation between two non-parallel buildings Article Accepted Version Li, B., Luo, Z., Sandberg, M. and Liu, J. (2015) Revisiting the ‘Venturi effect’ in passage ventilation between two non-parallel buildings. Building and Environment, 92 (2). pp. 714-722. ISSN 0360-1323 doi: https://doi.org/10.1016/j.buildenv.2015.10.023 Available at http://centaur.reading.ac.uk/45708/ It is advisable to refer to the publisher’s version if you intend to cite from the work. See Guidance on citing . To link to this article DOI: http://dx.doi.org/10.1016/j.buildenv.2015.10.023 Publisher: Elsevier All outputs in CentAUR are protected by Intellectual Property Rights law, including copyright law. Copyright and IPR is retained by the creators or other copyright holders. Terms and conditions for use of this material are defined in the End User Agreement . www.reading.ac.uk/centaur CentAUR Central Archive at the University of Reading Reading’s research outputs online Revisiting the ‘Venturi effect’ in passage ventilation between two non-parallel buildings Biao Li1,2, Zhiwen Luo2,* , Mats Sandberg3, Jing Liu1,4 1School of Municipal and Environmental Engineering, Harbin Institute of Technology, China 2School of Built Environment, University of Reading, Reading, United Kingdom 3KTH Research School, University of Gävle, Sweden 4State Key Laboratory of Urban Water Resource and Environment, Harbin Institute of Technology, China *Corresponding Email: [email protected] Keywords: Ventilation capacity, urban environment, non-parallel passage, Venturi effect, pedestrian wind This manuscript includes 12 figures and 0 tables. Abstract: A recent study conducted by Blocken et al. -
Bernoulli Applications Venturi Meter
15/02/2016 Bernoulli Applications Venturi Meter A Venturi meter is used to measure the flow rate through a tube. It is based on the use of the Venturi effect, the reduction of fluid pressure that results when a fluid runs through a constricted section of pipe. It is called after Giovanni Battista Venturi (1746-1822), an Italian physicist. Look at the construction in figure: - we assume the flow is smooth and effectively inviscid, ie. friction is negligible. - the fluid is incompressible, and has density r throughout the pipe. - downstream we have a flow through a pipe section of area A1, with a flow velocity v1, and pressure p1. - in the narrow section with area A2, the fluid flows with flow speed v2, and has accompanying pressure p2. - as a result the two meters indicate the difference in pressure by means of a height difference h. 1 15/02/2016 Venturi Meter To find the pressure difference between the downstream flow and the pipe narrow, we invoke 1) the Bernoulli theorem and 2) the continuity equation. The latter assures that the rate of fluid flow through any section remains constant, ie. mass is preserved. 1) Bernoulli Theorem: pp11 12vv22 2212 as the flow is horizontal, we do not have to take into account the gravity term. 2) Continuity equation: Av11 Av 2 2 Combining both equations, we find for the pressure difference in the two parts of the pipe: 2 1 2 A1 pp12 v1 2 1 2 A2 Venturi Meter To read of the pressure difference between the two locations 1 and 2 in the fluid, we use the height difference h between the fluid level in the vertical tubes. -
Fluid Dynamics in the Past-Period of Nearly Three Centuries Have Missed Out!!
1. Turbulence cause by frictional force is produced. (Just like blowing a bottle) 2. The centrifugal force attempts to throw fluid’s molecules out of their orbits. 3. The fluid’s molecules are drawn from the U-shaped tube by frictional force. 4. When the fluid moves faster, the turbulence is stronger. 5. The centrifugal force is also stronger. 6. More of the fluid’s molecules are drawn from the U-shaped tube. Because of gravity, the frictional force is always present which creates the invisible actions described above and cause low pressure which lifts the liquid in the U-shaped tubes. The liquid levels do not indicate the pressure of the moving fluid. Bernoulli’s Principle stated that “A moving fluid has low pressure-the faster a fluid moves, the lower its pressure” is widely misunderstood and mistakes! Seeing is no believing under this circumstance!! The moving fluid is unable to display its pressure in the U-shaped tubes because the centrifugal forces above the turbulences are the active barriers of the U-shaped tubes. More exactly, some molecules of the moving fluid will be dropped in (U-shaped tube) and some will be thrown out, keeping them balanced to the liquid’s weight. Keep in mind: Unlike a pressure tank, measuring the Pressure of Flowing Fluids is totally different! The measuring equipments must not possess any pockets, holes or pilot-tubes exposed to the flow that generate turbulences and cause false readings. Instead, the turbulence and impact prevention device must be in used no matter what kind of the pressure measuring-equipment is used. -
Fluid Dynamics - Equation Of
Fluid dynamics - Equation of Fluid statics continuity and Bernoulli’s • What is a fluid? principle. Density Pressure • Fluid pressure and depth Pascal’s principle Lecture 4 • Buoyancy Archimedes’ principle Dr Julia Bryant Fluid dynamics • Reynolds number • Equation of continuity web notes: Fluidslect4.pdf • Bernoulli’s principle • Viscosity and turbulent flow flow1.pdf flow2.pdf • Poiseuille’s equation http://www.physics.usyd.edu.au/teach_res/jp/fluids/wfluids.htm Fluid dynamics REYNOLDS NUMBER A British scientist Osborne Reynolds (1842 – 1912) established that the nature of the flow depends upon a dimensionless quantity, which is now called the Reynolds number Re. Re = ρ v L / η ρ density of fluid v average flow velocity over the cross section of the pipe L characteristic dimension η viscosity pascal 1 Pa = 1 N.m-2 Re = ρ v L / η -3 -1 newton 1 N = 1 kg.m.s-2 [Re] ≡ [kg.m ] [m.s ][m] 1 Pa.s = kg.m.s-2 . m-2 .s [Pa.s] ≡ kg x m x m x s2.m2 = [1] m3 s kg.m.s Re is a dimensionless number As a rule of thumb, for a flowing fluid Re < ~ 2000 laminar flow ~ 2000 < Re < ~ 3000 unstable laminar to turbulent flow Re > ~ 2000 turbulent flow Consider an IDEAL FLUID Fluid motion is very complicated. However, by making some assumptions, we can develop a useful model of fluid behaviour. An ideal fluid is Incompressible – the density is constant Irrotational – the flow is smooth, no turbulence Nonviscous – fluid has no internal friction (η=0) Steady flow – the velocity of the fluid at each point is constant in time. -
Importance of Fluids for the Circulation of Blood, Gas Movement, and Gas Exchange
MCAT-3200184 book October 29, 2015 11:12 MHID: 1-25-958837-8 ISBN: 1-25-958837-2 CHAPTER 2 Importance of Fluids for the Circulation of Blood, Gas Movement, and Gas Exchange Read This Chapter to Learn About ➤ Fluids at Rest ➤ Fluids in Motion ➤ Circulatory System ➤ Gases his chapter reviews an important topic of physics: fluids. Fluids is a term that Tdescribes any substance that flows—a characteristic of both liquids and gases. Flu- ids possess inertia, as defined by their density, and are thus subject to the same physical interactions as solids. All of these interactions as they pertain to fluids at rest and fluids in motion as well as practical examples related to human physiology are discussed in this chapter. FLUIDS AT REST Density and Specific Gravity Density, ρ, is a physical property of a fluid, given as mass per unit volume, or ρ = mass = m unit volume V 35 MCAT-3200184 book October 29, 2015 11:12 MHID: 1-25-958837-8 ISBN: 1-25-958837-2 36 UNIT I: Density represents the fluid equivalent of mass and is given in units of kilograms per Physical kg g g cubic meter , grams per cubic centimeter , or grams per milliliter . Foundations of m3 cm3 mL Biological Systems Density, a property unique to each substance, is independent of shape or quantity but is dependent on temperature and pressure. Specific gravity (Sp. gr.) of a given substance is the ratio of the density of the substance ρ ρ sub to the density of water w,or ρ density of substance sub Sp.