Kidd Mine Pastefill Plant Operation
Total Page:16
File Type:pdf, Size:1020Kb
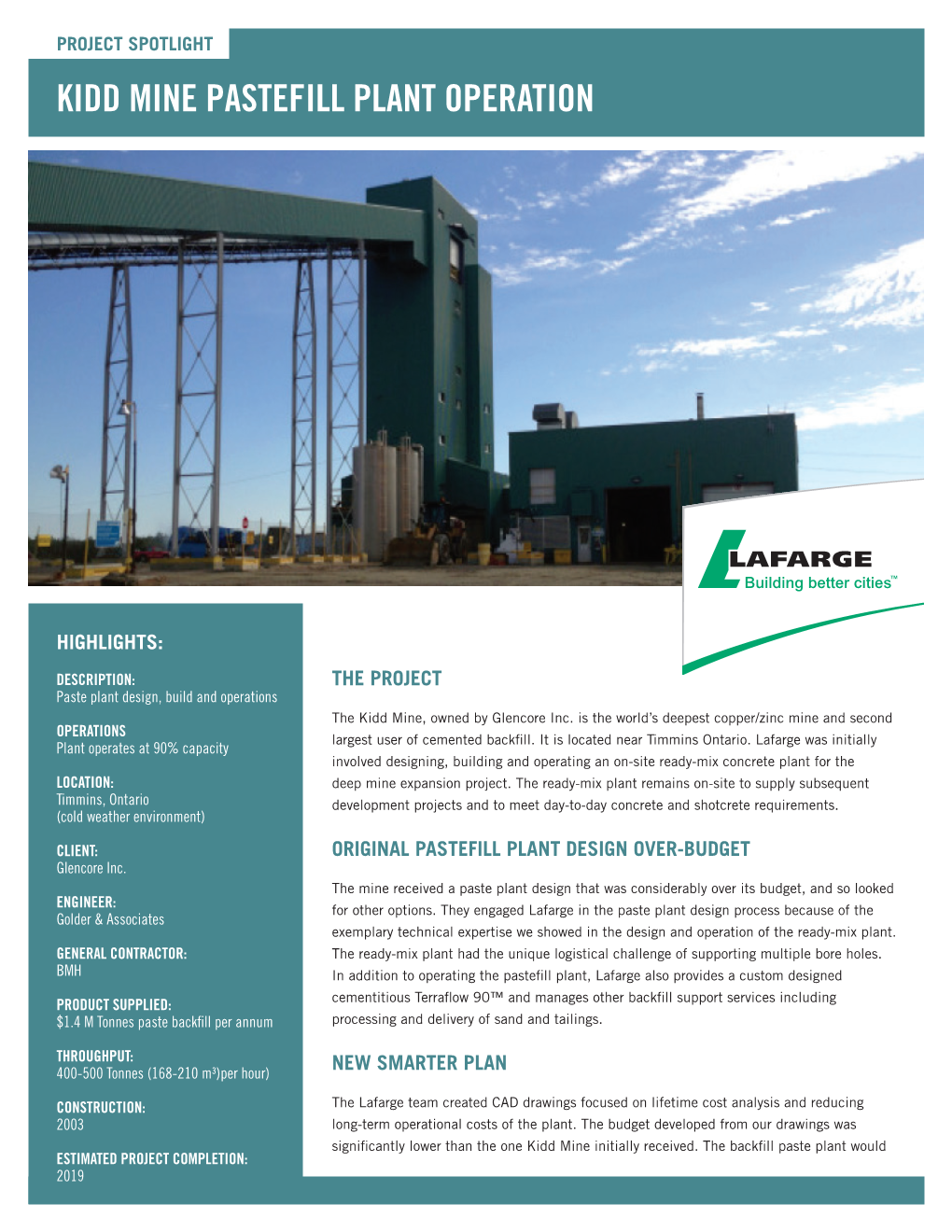
Load more
Recommended publications
-
Falconbridge Limited
Falconbridge Limited 2004 ANNUAL REPORT 2004 Financial Highlights (US$ MILLIONS, EXCEPT PER SHARE DATA) 2004 2003 Operating Highlights Revenues $ 3,070 $ 2,083 Operating income 969 301 Earnings 672 191 Cash provided by operating activities before changes in working capital 1,067 445 Capital expenditures and deferred project costs 573 370 Financial Position Cash and cash equivalents 645 298 (at December 31) Working capital 933 649 Total assets 5,118 4,172 Long-term debt 1,437 1,427 Shareholders’ equity 2,563 1,938 Return on common shareholders’ equity (ROE) 31% 11% Return on net assets 31% 13% Ratio of net debt to net debt plus equity 24% 37% Per Common Share (US$) Earnings (Basic) $ 3.71 $ 1.03 Earnings (Diluted) 3.69 1.02 Cash provided by operating activities 5.38 2.48 Book value 14.25 10.84 Shares outstanding (millions of shares) 179.8 178.8 Front cover, from left to right: RETURN ON EQUITY RETURN ON NET ASSETS SHARE PRICE 1) Nickel Rim South, Sudbury, Falconbridge achieved a Falconbridge increased its During 2004, Falconbridge Ontario, vent shaft galloway 31% return on equity in RONA to 31% in 2004, maintained an average stock price assembly of two sections 2004 exceeding its 15% surpassing its 18% target. of Cdn$31.88, 60% higher than 2) Nickel end product ROE objective. its 2003 average of Cdn$19.95. 3) Lomas Bayas, Chile 4) Nikkelverk, Norway, refinery (%) (%) (Cdn$) 37 30 30 34 25 25 31 28 20 20 GOAL 18% 25 15 GOAL 15% 15 22 2003 average stock price 10 10 19 16 5 5 13 0 0 10 00 01 02 03 04 00 01 02 03 04 2003 2004 Investment Grade Credit Ratings: Moody’s: Baa3 Standard & Poor’s: BBB– Dominion Bond Rating Service: BBB High Why Invest in Falconbridge? Right metals – nickel and copper Solid production base – upside potential Growth opportunities – within our control Growing value of scarce resources Financial strength to fund operations and growth projects NICKEL PRODUCTION COPPER PRODUCTION Falconbridge achieved Falconbridge achieved record refined nickel production of copper mine production of 100,900* tonnes in 2004. -
Falconbridge Limited 2003 Annual Report FUNDAMENTAL STRENGTH Our Operations
Falconbridge Limited 2003 Annual Report FUNDAMENTAL STRENGTH Our Operations NICKEL COPPER CORPORATE 1 Sudbury 6 Compañía Minera Doña Inés de 9 Corporate Office (Sudbury, Ontario) Collahuasi S.C.M. (44%) (Toronto, Ontario) Mines and mills nickel-copper ores; smelts (Northern Chile) 10 Project Offices nickel-copper concentrate from Sudbury’s Mines and mills copper sulphide ores into (Kone and Nouméa, New Caledonia; mines and from Raglan, and processes concentrate; mines and leaches copper Brisbane, Australia) custom feed materials. oxide ores to produce cathodes. 11 Exploration Offices 2 Raglan 7 Kidd Division (Sudbury, Timmins and Toronto, Ontario; (Nunavik, Quebec) (Timmins, Ontario) Laval, Quebec; Pretoria, South Africa; Mines and mills nickel-copper ores from Mines copper-zinc ores from the Kidd Mine. Belo Horizonte, Brazil; Brisbane, open pits and an underground mine. Mills, smelts and refines copper-zinc ores Australia) from the Kidd Mine and processes Sudbury 3 Nikkelverk A/S copper concentrate and custom feed 12 Business Development (Kristiansand, Norway) materials. (Toronto, Ontario) Refines nickel, copper, cobalt, precious and platinum group metals from Sudbury, 8 Compañía Minera Falconbridge 13 Marketing and Sales Raglan and from custom feeds. Lomas Bayas (Brussels, Belgium; Pittsburgh, (Northern Chile) Pennsylvania; Tokyo, Japan) 4 Falconbridge Dominicana, C. por A. Mines copper oxide ores from an open pit; (85.26%) (Bonao, Dominican Republic) refines into copper cathode through the 14 Technology Centre Mines, mills, smelts -
Ausenco NI 43-101 Template
Crawford Nickel Sulphide Project NI 43-101 Technical Report & Preliminary Economic Assessment Ontario, Canada Effective Date: May 21, 2021 Prepared for: Canada Nickel Company Inc. 130 King St. West Suite 1900 Toronto, Ontario, M5X 1E3 Prepared by: Ausenco Engineering Canada Inc. 11 King St. West Suite 1550 Toronto, Ontario, M5H 4C7 List of Qualified Persons: Paul Staples, P.Eng., Ausenco Engineering Canada Inc. Greg Lane, FAUSIMM, Ausenco Services Pty. Ltd. Scott Jobin-Bevans, P.Geo., Caracle Creek International Consulting Inc. John Siriunas, P.Eng., Caracle Creek International Consulting Inc. David Penswick, P.Eng., Independent Mining Consultant Sheila Ellen Daniel, P.Geo., Wood Canada Ltd. Karel Van Zyl, P.Eng., Wood Canada Ltd. CERTIFICATE OF QUALIFIED PERSON L. Paul Staples I, L. Paul Staples, P.Eng., certify that I am employed as VP and Global Practice Lead with Ausenco Engineering Canada (“Ausenco”), with an office address of 855 Homer Street, Vancouver, BC. This certificate applies to the technical report titled “Crawford Nickel Sulphide Project – NI 43-101 Technical Report & Preliminary Economic Assessment” that has an effective date of May 21, 2021 (the “Technical Report”). I graduated from Queen’s University, Kingston, Ontario in 1993 with a Bachelor of Science degree in Materials and Metallurgical Engineering. I am a member in good standing of the Engineers and Geoscientists of British Columbia, Licence #47467. I have practiced my profession for 28 years continuously. I have been directly involved in many similar projects and studies in Canada and abroad. I have read the definition of “Qualified Person” set out in the National Instrument 43-101 Standards of Disclosure for Mineral Projects (“NI 43-101”) and certify that by virtue of my education, affiliation to a professional association and past relevant work experience, I fulfill the requirements to be a “Qualified Person” for those sections of the Technical Report that I am responsible for preparing. -
Ontario Must Assess the Impacts of Mines and Smelters Before They Are Built!
ONTARIO MUST ASSESS THE IMPACTS OF MINES AND SMELTERS BEFORE THEY ARE BUILT! Submission on a proposed list of projects which will be subject to the comprehensive environmental assessment requirements in Part II.3 of the Environmental Assessment Act (EAA) and will be designated in a regulation as Part II.3 projects Environmental Registry of Ontario number 019-2377 by Ontarians for a Just Accountable Mineral Strategy Commissioned by MiningWatch Canada November 5, 2020 Executive summary Before new or expanding mines, mills and smelters get their permits and are built in Ontario, we need to know their impacts. The process to do this is known as environmental assessment (EA). On July 8, 2020, Government of Ontario proposed sweeping changes to the Environmental Assessment Act (EAA) as part of the omnibus COVID-19 Economic Recovery Act, Bill 197. One of these changes is to develop a list of high-risk projects that will be subject to EA. Ontario has never required new or expanding mines, mills, smelters, and refineries to undergo an assessment of their impacts on the environment, the economy, or society. Out of 31 mines and mills currently operating in Ontario, only four have gone through an EA, and only one of those was by the province; the other three were reviewed by the federal government. With one exception, mines and smelters in Sudbury, Timmins, and Kirkland Lake have never completed an EA. We are hopeful that mines and smelters will finally appear on a new Ontario list of projects that pose the most risk to us all and we welcome this opportunity to comment. -
Ontario Mine Rescue Competition Awards
Ontario Mine Rescue Competition Awards JUNE 2018 Table of Contents Provincial Championship Award (M.S.A. Trophy) John Guthrie (Special Equipment) Award Firefighting Award First Aid Award Equipment Technician Award Kirkland Lake District Onaping District Red Lake District Southern District Sudbury District Thunder Bay/Algoma District Timmins District Former District Trophies Provincial Championship Award The M.S.A. Trophy, donated by MSA Canada Ltd., has been awarded to the top team in the annual Provincial Mine Rescue Competition since 1955. A cut and polished granitoid slab with plaque rests above a silver, trapezoidal engraved scene of a linked six-man mine rescue team wearing McCaa breathing apparatus. The team is traversing a double-tracked drift, as the lead rescuer holds a Wolf flame safety lamp, while the second holds a self-rescuer. The trophy originally consisted only of the slab and the first tier with the engraving. The bottom three tiers were added. 1950 – Pamour Porcupine Gold Mines 1987 – Denison Mines Ltd. 1951 – Hallnor Mines Ltd. 1988 – Denison Mines Ltd. 1952 – Hollinger Consolidated Gold Mines Ltd. 1989 – American Barrick Resources 1953 – Falconbridge Nickel Mines Ltd. - Holt McDermott Mine 1954 – MacLeod Cockshutt Gold Mines Ltd. 1990 – Sifto Canada, Goderich Mine 1955 – Kerr Addison Gold Mines Ltd. 1991 – Placer Dome Inc., Campbell Mine 1956 – Falconbridge Nickel Mines Ltd. 1992 – Placer Dome Inc., Dome Mine - East Mine 1993 – Inco Ltd., Frood Stobie Complex 1957 – Steep Rock Iron Mines Ltd. 1994 – Inco Ltd., Levack Complex 1958 – Steep Rock Iron Mines Ltd. 1995 – Inco Ltd., Frood Stobie Complex 1959 – Algom Uranium Mines Ltd. 1996 – Falconbridge, Onaping Craig Mine - Quirke Mine 1997 – Falconbridge 1960 – Falconbridge Nickel Mines Ltd. -
Solid-Ground-2-2016.Pdf
#2 2016 SOLIDGROUND A MAGAZINE FROM Canada: SANDVIK MINING AND ROCK TECHNOLOGY Profound productivity Sandvik DR481i: Bigger is better Intelligence: TRUST THE Higher BUCKET: learning an integrated solution Battery-driven equipment heralds the future of emissions-free underground mining. CHARGED UP WELCOME SANDVIK NEWS Riding high in Finland ................................ 5 Dear reader, PROFILE Salt of the earth ......................................... 6 THE MAIN HEADLINE on the front cover, “Charged up” (referring to our battery-trammed equipment and exhaust-free TRADE NEWS mining), can also mean “to be excited and full of energy” – and The search for Pharaohs’ gold ............... 8 that’s very much how Sandvik Mining and Rock Technology is feeling about the future of our industry, with the innovative KGHM RUDNA COPPER MINE products and services that we are bringing to the market. A total-bucket approach....................... 10 Today’s challenging market calls for ever-greater productivity BATTERY-DRIVEN EQUIPMENT and efficiency, and our focus is on supporting our customers in this drive. Just one example is the total bucket concept delivered The mission to eliminate emissions...16 to Europe’s largest copper mine, enabling a significant reduction GLENCORE KIDD BASE-METAL MINE in loader maintenance costs, optimized productivity and reduced downtime. Automation to the core ........................ 20 SANDVIK DR481i ENVIRONMENT, HEALTH AND SAFETY will always be a top Productivity through power ................ 26 priority for us, and we know that it will only continue to grow in importance across our industry. That’s why we are launching SUSTAINING SAFETY the aforementioned battery-driven mining equipment to Rod rack redesign ................................... 30 address the potential health impacts of diesel particulate matter and other underground engine INTELLIGENCE emissions – thereby also potentially helping to Education roundtable .......................... -
Tracing Ancient Hydrogeological Fracture Network Age and Compartmentalisation Using Noble Gases
Available online at www.sciencedirect.com ScienceDirect Geochimica et Cosmochimica Acta 222 (2018) 340–362 www.elsevier.com/locate/gca Tracing ancient hydrogeological fracture network age and compartmentalisation using noble gases Oliver Warr a,b,⇑, Barbara Sherwood Lollar b, Jonathan Fellowes c, Chelsea N. Sutcliffe b, Jill M. McDermott b, Greg Holland c, Jennifer C. Mabry a, Christopher J. Ballentine a a Department of Earth Sciences, University of Oxford, South Parks Road, Oxford OX1 3AN, United Kingdom b Department of Earth Sciences, University of Toronto, Toronto, Ontario, Canada c School of Earth, Atmospheric and Environmental Sciences, Williamson Building, University of Manchester, Manchester M13 9PL, United Kingdom Received 3 March 2017; accepted in revised form 16 October 2017; available online 25 October 2017 Abstract We show that fluid volumes residing within the Precambrian crystalline basement account for ca 30% of the total ground- water inventory of the Earth (> 30 million km3). The residence times and scientific importance of this groundwater are only now receiving attention with ancient fracture fluids identified in Canada and South Africa showing: (1) microbial life which has existed in isolation for millions of years; (2) significant hydrogen and hydrocarbon production via water–rock reactions; and (3) preserving noble gas components from the early atmosphere. Noble gas (He, Ne, Ar, Kr, Xe) abundance and isotopic compositions provide the primary evidence for fluid mean residence time (MRT). Here we extend the noble gas data from the Kidd Creek Mine in Timmins Ontario Canada, a volcanogenic massive sulfide (VMS) deposit formed at 2.7 Ga, in which fracture fluids with MRTs of 1.1–1.7 Ga were identified at 2.4 km depth (Holland et al., 2013); to fracture fluids at 2.9 km depth. -
Managing Thiosalts at Xstrata Copper Canada
“Managing Thiosalts at Xstrata Copper - Kidd Operations” by: David Yaschyshyn 17th Annual BC MEND ML/ARD Workshop December 1, 2010 Xstrata Copper – diverse copper assets and projects 2 Kidd Operations • Located in Timmins, Ontario • Kidd Mine and Kidd Concentrator • Copper/zinc mined since 1966 • Production reached 9,200 feet (2,800m) in 2009, making the operation the deepest base metal mine in the world • Projected mine life to 2017 • Ore processed at Kidd Concentrator using conventional flotation techniques • Copper and zinc concentrates dewatered and shipped for further refinement in Canada 3 Kidd Concentrator, Tailings Management Area • Conventional slurry tailings discharge started Porcupine River in 1966 Downstream • Thickened tailings No. 2 Tailings discharge since 1973 Thickener • Lime Treatment at Pond A and C Tailings • Settling Pond D, water Management recycled for milling C Area • Polishing Pond E Final Effluent • Treated Final Effluent Porcupine River discharged to Porcupine E D A at Hoyle River Porcupine River Concentrator Site Upstream 4 Where/When Thiosalts Occur? • Typically during grinding or flotation of sulphide ores O containing pyrite and pyrrhotite in alkaline conditions: O O S 2+ - 0 S FeS2 + 2O2 + H2O Fe + 2OH + 2S 2- Thiosulphate (S2O3 ) 0 - 2- 2- O 4S + 6OH 2S + S2O3 + 3H2O O O 3S O 2- + 2O + H O 2S O 2- + 2OH- 2 3 2 2 3 6 O S 2- 2- - O 4S2O3 + O2 + 2H2O 2S4O6 + 4OH S S O 2- • Thiosalts are a series of partially Trithionate ion (S 3O6 ) 2- oxidixed sulphur oxyanions (SxOy ) O O • Thiosalts generation tends S S O to be site-specific O S S O O Tetrathionate ion (S O 2-) 4 6 5 Thiosalts Speciation (2009-2010) 6 Why Thiosalts May Require Management? 2- • They typically oxidize until end product sulphate (SO4 ) is reached • During oxidation reactions, proton (H+) is produced. -
GLENCORE Resources and Reserves Report 2020.Xlsx
Resources & Reserves as at 31 December 2020 Contents Page number About this report 3 Definitions 5 Metals and Minerals: Copper 6 Zinc 14 Nickel 26 Ferroalloys 28 Aluminium/Alumina 32 Iron ore 33 Energy products Coal 36 Oil 46 Competent Persons 47 2 About this report We report our resources and reserves in accordance with the 2012 edition of the Copper Australasian Code for Reporting of Exploration Results, Mineral Resources and Ore The Copper Mineral Resources and Ore Reserves Statement at 31 December 2020 has Reserves (JORC Code), the 2016 edition of the South African Code for Reporting of been compiled in accordance with the JORC Code. Mineral Resources and Mineral Reserves (SAMREC), the Canadian Institute of Mining, The Mineral Resources and Ore Reserves statements have been reviewed and the Metallurgy and Petroleum (CIM) Standards on Mineral Resources and Reserves (2014 relevant data extracted and compiled by Mark Jamieson, Glencore Copper (AusIMM). edition) and the Petroleum Resources Management System (PRMS) for reporting oil and natural gas Reserves and Resources. Zinc The term ‘Ore Reserves’, as defined in Clause 28 of the JORC Code, has the same The Zinc Mineral Resource and Ore Reserve Statement at 31 December 2020 has been meaning as ‘Mineral Reserves’ as defined in the CIM Definition Standards for Mineral compiled in accordance with the JORC Code. Resources and Mineral Reserves. The Mineral Resource and Ore Reserve statements have been reviewed and the relevant data extracted and compiled by Aline Cote, Glencore Zinc (OGQ). Overview Nickel The resource and reserve data in the following tables are as at 31 December 2020, The Canadian and New Caledonian Mineral Resources and Mineral Reserves estimates unless otherwise noted. -
Case Studies 15 YEARS of Deep Success
TITAN 24 DC/IP & MT Case Studies 15 YEARS of Deep Success Copper Mtn Kemess Some of our TITAN clients… Barrick Gold Corp. o Dept. of Energy (Nevada) Noranda/Falconbridge Inc. o FNX Mining Company Inc. Placer Dome Inc. o Breakwater Resources Tribute Minerals Inc. o New Gold Barker Minerals Inc. o MILPO The O.T. Mining Corporation o Almaden Minerals Lionore Mining International Ltd. o New Nadina Explorations De Beers Consolidated Mines Limited o Mining Ventures Brazil Apollo Gold Corporation o Denison Mines NADR Corporation o Malbex Resources Kennecott Exploration Company o Areva Resources Cameco Corporation o Northland Resources Ontzinc Corporation o Inmet Mining Goldcorp Inc. o Boxxer Gold Newmont Mining Corporation o Copper Mountain Mining Corp. Wallbridge Mining Company Limited o Ormat Technologies Inco Limited o Huckleberry Mines Dept. of Energy (Nevada) o Castillian Resources FNX Mining Company Inc. o Vale Argentina Kennecott Exploration Company o Romios Gold Resources Cameco Corporation o Northern Freegold Ontzinc Corporation o Xstrata Copper Goldcorp Inc. o Rosemont Copper Newmont Mining Corporation o Regulus Resources Wallbridge Mining Company Limited o Agnico-Eagle Mines Inco Limited o Kazakhmys Exploration Contents Case studies… Porphyry Uranium Copper Mountain Athabasca Basin, AREVA New Nadina Athabasca Basin, Dennison Kemess, BC VMS Copper/Gold Buchan's, Nfld Red Chris, BC Kidd Creek, Ontario Trek, BC Halfmile, NewBrunswick Carlin Trend, Nevada Nickel Shear System Gold Offset dyke, Sudbury North Country Gold, Nunavut Diamonds Gralheira, Portugal Jwaneng, Botswanna Greenstone, Ontario Epithermal Gold Chelopech, Bulgaria Case Study: Copper Mountain, BC Copper Mountain Mine- Porphyry Exploration Objectives o To confirm continuity of mineralization between the pits. -
Ontario Falconbridge Limited 10050 Highway 101 East Post Office Box, No
CONTENT COPY OF ORIGINAL Ministry Ministère AMENDED CERTIFICATE OF APPROVAL of the de INDUSTRIAL SEWAGE WORKS Environment l’Environnement NUMBER 9831-72BH7Y Issue Date: May 16, 2007 Ontario Falconbridge Limited 10050 Highway 101 East Post Office Box, No. 2002 Timmins, Ontario P4N 7K1 Site Location: Kidd Metallurgical Site Lot 1, Concession 1, Hoyle City of Timmins, District of Cochrane You have applied in accordance with Section 53 of the Ontario Water Resources Act for approval of: modifications to the sewage works consisting of the Pastefill Tailings Pipeline from Kidd Metsite to Kidd Minesite, Jarosite Pond Area, Buffalo Paddock Area and the Tailings Management Area (TMA) for the collection, transmission, treatment and disposal of: tailings from the Concentrator; Jarosite Residue from the Zinc Plant, co-deposited with tailings or pumped directly to the Jarosite Pond Facility; Neutralized Weak Acid from the Zinc and Copper Acid Plants, co-deposited with tailings or pumped directly to the TMA; waste water collected from the jarosite pond containment area; waste water generated from the Process Plants, via various site ditches and holding ponds; lime treatment sludge generated by the tailings treatment process and the Kidd Mine Water Treatment process; granulated slag generated by the Copper Smelter; metal-bearing sludge and residue generated from periodic cleaning or decommissioning of process equipment; treated effluent from sanitary sewage treatment plants; site drainage, including seepage water from the TMA collected within a perimeter seepage collection ditch system; stormwater from the Buffalo Paddock Area; minewater inputs from the Porcupine Joint Venture Hoyle Pond Mine; and disposal of the CamChib tailings, waste rock and ponded tailings water in the Tailings Management Area, as follows: - approximately 3,000 cubic metres of ponded tailings water from the CamChib Mine Site; and - approximately 24,000 tonnes of tailings and 10,000 tonnes of waste rock from the CamChib Mine Site. -
Envisioning Opportunities Our Operations
FALCONBRIDGE LIMITED Annual Report 2002 ENVISIONING OPPORTUNITIES OUR OPERATIONS NICKEL Raglan NICKEL Nunavik Territory, Canada Nikkelverk COPPER NICKEL Kristiansand, Kidd Creek Norway Sudbury Timmins, Canada Sudbury, Canada FERRONICKEL Falcondo Bonao, Dominican Republic COPPER NICKEL Collahuasi COPPER Koniambo Santiago, Iquique, Lomas Bayas New Northern Chile Antofagasta, Caledonia Northern Chile NICKEL COPPER CORPORATE Sudbury (Sudbury, Ontario) Compañía Minera Doña Inés de Corporate Office (Toronto, Ontario) • Mines and mills nickel-copper ores Collahuasi S.C.M. (44%) (Santiago, Iquique Project Offices (Kone and Nouméa, from four mines (Craig, Fraser, Lindsley and Northern Chile) New Caledonia; Brisbane, Australia) and Lockerby); smelts nickel-copper • Mines and mills copper sulphide ores concentrate from Sudbury’s mines and into concentrate; mines and leaches Exploration Offices (Sudbury, Timmins from Raglan, and processes custom copper oxide ores to produce cathodes. and Toronto, Ontario; Laval, Quebec; feed materials. Pretoria, South Africa; Belo Horizonte, Brazil; Kidd Mining Division (Timmins, Ontario) Brisbane, Australia) Raglan (Rouyn-Noranda, Nunavik, Quebec) • Mines copper-zinc ores from the • Mines and mills nickel-copper ores from Kidd Mine. Business Development (Toronto, Ontario) open pits and an underground mine. • Searches worldwide for attractive Kidd Metallurgical Division investment opportunities to support Nikkelverk A/S (Kristiansand, Norway) (Timmins, Ontario) Falconbridge’s business plans. • Refines nickel, copper, cobalt, precious • Mills, smelts and refines copper-zinc and platinum group metals from ores from the Kidd Mine and processes Marketing and Sales (Brussels, Belgium; Sudbury, Raglan and from custom feeds. Sudbury copper concentrate and custom Pittsburgh, Pennsylvania; Tokyo, Japan) feed materials, including some • Markets and sells nickel, cobalt and other Falconbridge Dominicana, C.