Application Note 915 Automotive Physical Layer SAE J1708 and The
Total Page:16
File Type:pdf, Size:1020Kb
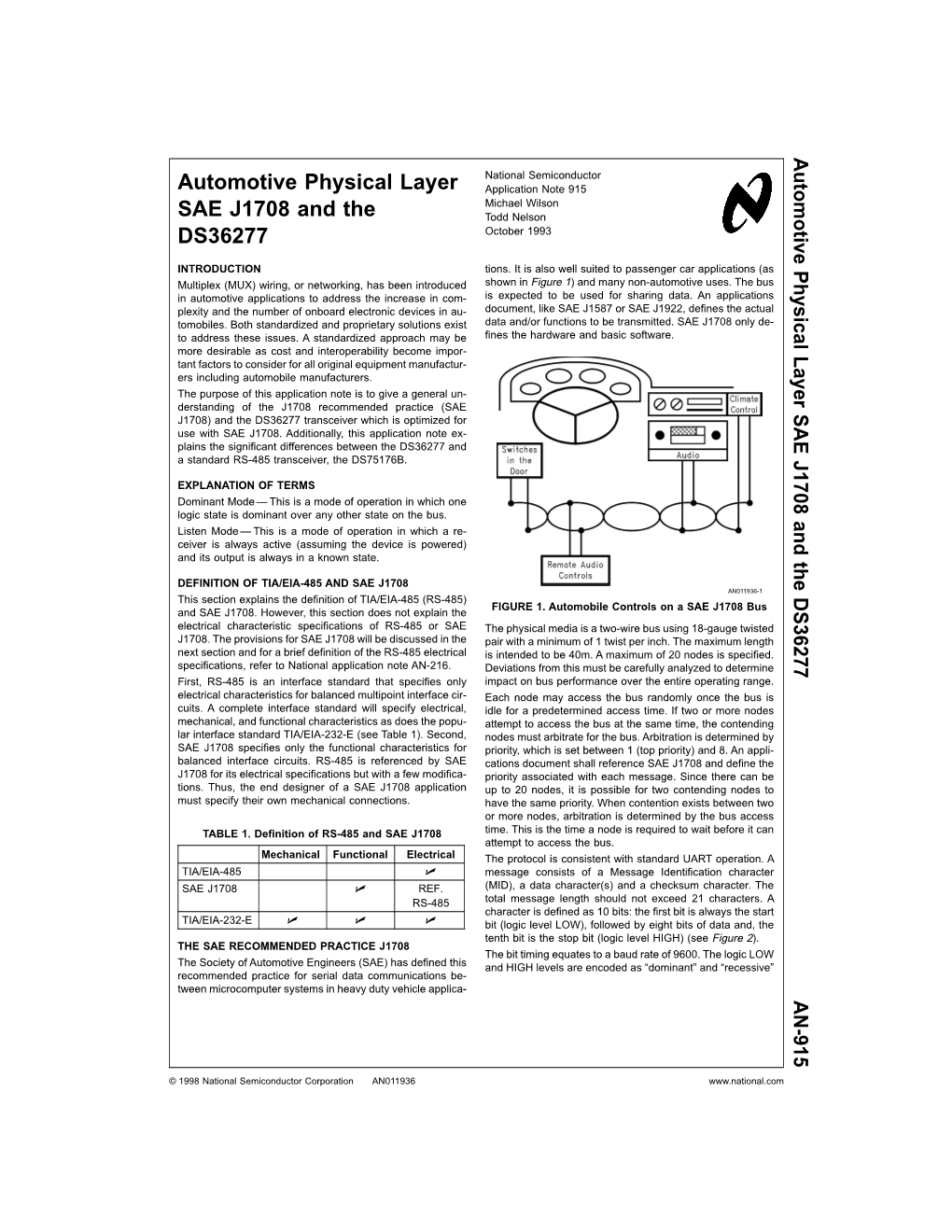
Load more
Recommended publications
-
The Problems in Fibre Optic Communication in the Communication Systems of Vehicles
TEKA Kom. Mot. i Energ. Roln. – OL PAN, 2011, 11, 363–372 THE PROBLEMS IN FIBRE OPTIC COMMUNICATION IN THE COMMUNICATION SYSTEMS OF VEHICLES Sumorek Andrzej, Buczaj Marcin Department of Computer and Electrical Engineering, Lublin University of Technology, Poland Summary. The diversifi cation of technical solutions occurred as a result of almost thirty years of evolution of the communication systems between the mechatronic systems in motor vehicles. The vehicles are equipped with the conventional cable connections between the switches and actuators as well as with advanced data exchange networks. These networks show more and more similarities to computer networks. They are the new solutions; even their classifi cation has been created a few years ago (class D). Therefore the personnel engaged in the scope of functional programming and vehicles servicing encounter the problems associated with networks operation. The purpose of the article is to present the principles of functioning of the basic networks with the medium in the form of an optical fi bre. Particular emphasis has been placed on the detection of failures consisting in the damage of communication node and optical fi bre. Key words: Media Oriented Systems Transport, Domestic Digital Bus. INTRODUCTION The systematics associated with networks classifi cation presented in the year 1994 contained 3 types of networks. Such systematics was also presented in 2007 in literature in 2007 [12]. This approach has been established as a result of the standardization introduced by SAE J1850 [5, 10]. Three classes of communication systems have been specifi ed in SAE J1850. The applications group associated with bus throughput is used as the criterion of subdivision. -
Body Builder Connectors, Schematic
BODY BUILDER INSTRUCTIONS Mack Trucks Electrical Wiring and Connections CHU, CXU, GU, TD, MRU, LR Section 3 Introduction This information provides design and function, specification and procedure details for Electrical Wiring and Connections for MACK vehicles. Note: For information on mDrive PTO installation and wiring see Section 9 PTO Installation, mDrive. Note: For information on PTO parameter programming see Section 9 PTO Parameter Programming. Unless stated otherwise, following a recommendation listed in this manual does not automatically guarantee compliance with applicable government regulations. Compliance with applicable government regulations is your responsibility as the party making the additions/modifications. Please be advised that the MACK Trucks, Inc. vehicle warranty does not apply to any MACK vehicle that has been modified in any way, which in MACK's judgment might affect the vehicles stability or reliability. Contents • “Abbreviations”, page 3 • “General Wiring Definitions”, page 4 • “Routing and Clipping Guidelines”, page 5 • “Body Builder Connectors, Schematic Examples”, page 17 • “Remote Start n Stop”, page 23 • “Remote Engine Stop”, page 24 • “Adding Auxiliary Accelerator Pedal”, page 25 • “BodyLink III”, page 26 • “Auxiliary Switch Locations (Cab)”, page 30 • “Power Connections”, page 31 • “Control Link II”, page 37 • “LR Workbrake”, page 50 Mack Body Builder Instructions CHU, CXU, GU, TD, MRU, LR USA139448393 Date 9.2017 Page 1 (94) All Rights Reserved • “Wiring J1939”, page 52 • “9-pin Diagnostic Connector”, -
Study of an Error in Engine ECU Data Collected for In-Use Emissions Testing and Development and Evaluation of a Corrective Procedure
Graduate Theses, Dissertations, and Problem Reports 2007 Study of an error in engine ECU data collected for in-use emissions testing and development and evaluation of a corrective procedure Petr Sindler West Virginia University Follow this and additional works at: https://researchrepository.wvu.edu/etd Recommended Citation Sindler, Petr, "Study of an error in engine ECU data collected for in-use emissions testing and development and evaluation of a corrective procedure" (2007). Graduate Theses, Dissertations, and Problem Reports. 1840. https://researchrepository.wvu.edu/etd/1840 This Thesis is protected by copyright and/or related rights. It has been brought to you by the The Research Repository @ WVU with permission from the rights-holder(s). You are free to use this Thesis in any way that is permitted by the copyright and related rights legislation that applies to your use. For other uses you must obtain permission from the rights-holder(s) directly, unless additional rights are indicated by a Creative Commons license in the record and/ or on the work itself. This Thesis has been accepted for inclusion in WVU Graduate Theses, Dissertations, and Problem Reports collection by an authorized administrator of The Research Repository @ WVU. For more information, please contact [email protected]. Study of an Error in Engine ECU Data Collected for In-Use Emissions Testing and Development and Evaluation of a Corrective Procedure Petr Sindler Thesis submitted to the College of Engineering and Mineral Resources at West Virginia University in partial fulfillment of the requirements for the degree of Master of Science in Mechanical Engineering Mridul Gautam, Ph.D., Chair Gregory J. -
SAE International® PROGRESS in TECHNOLOGY SERIES Downloaded from SAE International by Eric Anderson, Thursday, September 10, 2015
Downloaded from SAE International by Eric Anderson, Thursday, September 10, 2015 Connectivity and the Mobility Industry Edited by Dr. Andrew Brown, Jr. SAE International® PROGRESS IN TECHNOLOGY SERIES Downloaded from SAE International by Eric Anderson, Thursday, September 10, 2015 Connectivity and the Mobility Industry Downloaded from SAE International by Eric Anderson, Thursday, September 10, 2015 Other SAE books of interest: Green Technologies and the Mobility Industry By Dr. Andrew Brown, Jr. (Product Code: PT-146) Active Safety and the Mobility Industry By Dr. Andrew Brown, Jr. (Product Code: PT-147) Automotive 2030 – North America By Bruce Morey (Product Code: T-127) Multiplexed Networks for Embedded Systems By Dominique Paret (Product Code: R-385) For more information or to order a book, contact SAE International at 400 Commonwealth Drive, Warrendale, PA 15096-0001, USA phone 877-606-7323 (U.S. and Canada) or 724-776-4970 (outside U.S. and Canada); fax 724-776-0790; e-mail [email protected]; website http://store.sae.org. Downloaded from SAE International by Eric Anderson, Thursday, September 10, 2015 Connectivity and the Mobility Industry By Dr. Andrew Brown, Jr. Warrendale, Pennsylvania, USA Copyright © 2011 SAE International. eISBN: 978-0-7680-7461-1 Downloaded from SAE International by Eric Anderson, Thursday, September 10, 2015 400 Commonwealth Drive Warrendale, PA 15096-0001 USA E-mail: [email protected] Phone: 877-606-7323 (inside USA and Canada) 724-776-4970 (outside USA) Fax: 724-776-0790 Copyright © 2011 SAE International. All rights reserved. No part of this publication may be reproduced, stored in a retrieval system, distributed, or transmitted, in any form or by any means without the prior written permission of SAE. -
Extracting and Mapping Industry 4.0 Technologies Using Wikipedia
Computers in Industry 100 (2018) 244–257 Contents lists available at ScienceDirect Computers in Industry journal homepage: www.elsevier.com/locate/compind Extracting and mapping industry 4.0 technologies using wikipedia T ⁎ Filippo Chiarelloa, , Leonello Trivellib, Andrea Bonaccorsia, Gualtiero Fantonic a Department of Energy, Systems, Territory and Construction Engineering, University of Pisa, Largo Lucio Lazzarino, 2, 56126 Pisa, Italy b Department of Economics and Management, University of Pisa, Via Cosimo Ridolfi, 10, 56124 Pisa, Italy c Department of Mechanical, Nuclear and Production Engineering, University of Pisa, Largo Lucio Lazzarino, 2, 56126 Pisa, Italy ARTICLE INFO ABSTRACT Keywords: The explosion of the interest in the industry 4.0 generated a hype on both academia and business: the former is Industry 4.0 attracted for the opportunities given by the emergence of such a new field, the latter is pulled by incentives and Digital industry national investment plans. The Industry 4.0 technological field is not new but it is highly heterogeneous (actually Industrial IoT it is the aggregation point of more than 30 different fields of the technology). For this reason, many stakeholders Big data feel uncomfortable since they do not master the whole set of technologies, they manifested a lack of knowledge Digital currency and problems of communication with other domains. Programming languages Computing Actually such problem is twofold, on one side a common vocabulary that helps domain experts to have a Embedded systems mutual understanding is missing Riel et al. [1], on the other side, an overall standardization effort would be IoT beneficial to integrate existing terminologies in a reference architecture for the Industry 4.0 paradigm Smit et al. -
Cybersecurity Research Considerations for Heavy Vehicles
DOT HS 812 636 December 2018 Cybersecurity Research Considerations for Heavy Vehicles Disclaimer This publication is distributed by the U.S. Department of Transportation, National Highway Traffic Safety Administration, in the interest of information exchange. The opinions, findings, and conclusions expressed in this publication are those of the authors and not necessarily those of the Department of Transportation or the National Highway Traffic Safety Administration. The United States Government assumes no liability for its contents or use thereof. If trade or manufacturers’ names are mentioned, it is only because they are considered essential to the object of the publication and should not be construed as an endorsement. The United States Gov- ernment does not endorse products or manufacturers. Suggested APA Format Citation: Stachowski, S., Bielawski, R., & Weimerskirch, A. (2018, December). Cybersecurity research considerations for heavy vehicles (Report No. DOT HS 812 636). Washington, DC: National Highway Traffic Safety Administration. 1. Report No. 2. Government Accession No. 3. Recipient's Catalog No. DOT HS 812 636 4. Title and Subtitle 5. Report Date Cybersecurity Research Considerations for Heavy Vehicles December 2018 6. Performing Organization Code 7. Authors 8. Performing Organization Report No. Stephen Stachowski, P.E. (UMTRI), Russ Bielawski (UMTRI), André Weimerskirch 9. Performing Organization Name and Address 10. Work Unit No. (TRAIS) University of Michigan Transportation Research Institute 2901 Baxter Rd Ann Arbor, MI 48109 11. Contract or Grant No. DTNH22-15-R-00101, a Vehicle Electronics Systems Safety IDIQ 12. Sponsoring Agency Name and Address 13. Type of Report and Period Covered National Highway Traffic Safety Administration Final Report 1200 New Jersey Avenue SE. -
ELM325 J1708 Interpreter
ELM325 J1708 Interpreter Description Features With the advent of electronic engine controls, • Supports both SAE J1587 and J1922 many vehicles also adopted some form of diagnostic • High speed RS232 interface tools to help monitor their operation. As more modules began to be used in vehicles, there was • Works with standard RS485 transceivers also a need for the devices to share information • Fully configurable with AT commands rather than each independently obtain this from separate sensors. • Wide operating voltage range (1.8 to 5.5V) In the 1980’s, the SAE J1708 standard was • Low power CMOS design created to provide a specification for a common data bus to be used in heavy duty vehicles. It used RS485 wiring (already proven to be reliable in noisy environments), and a UART-based low speed data Connection Diagram format. The SAE J1587 standard followed a few PDIP and SOIC years later to describe the mechanism by which (top view) messages and data should be sent between vehicle modules. The ELM325 allows a PC or similar device to be VDD 1 14 VSS used to monitor and query devices on a J1708 data XT1 2 13 RO bus, using simple commands that can be sent from almost any terminal program. It is able to work with XT2 3 12 RE either the J1587 or the J1922 data formats. InvDE 4 11 DE RS232 Rx 5 10 J Tx LED Applications RS232 Tx 6 9 J Rx LED • Diagnostic trouble code readers RS Rx LED 7 8 RS Tx LED • Heavy duty vehicle scan tools • Teaching aids • ECU Simulators Block Diagram 3.58 MHz InvDE XT12 3 XT2 4 Timing and Control 13 RO RS232 Rx 5 RS232 J1708 11 DE Interface Interface RS232 Tx 6 J1587/1922 Interpreter 12 RE RS Rx LED 7 10 J Tx LED RS Tx LED 8 9 J Rx LED ELM325DSA Elm Electronics – Circuits for the Hobbyist 1 of 31 www.elmelectronics.com ELM325 Contents Electrical Information Copyright and Disclaimer.............................................................2 Pin Descriptions.......................................................................... -
Santa Barbara Metropolitan Transit District AIM System MASTER
Santa Barbara Metropolitan Transit District AIM System MASTER AGREEMENT with CLEVER DEVICES LTD. THIS AGREEMENT is entered into by and between Santa Barbara Metropolitan Transit District, an incorporated transit district under Sections 95000, et seq. of the California Public Utilities Code ("MTD"), and Clever Devices Ltd., a New York corporation ("Contractor"), at Santa Barbara, California, as of the later date set forth below the signatures executing this Agreement. WHEREAS: A. MTD desires to engage Contractor for acquisition, implementation, and maintenance of various Intelligent Transportation Systems (ITS) which are collectively referred to as the AVL & ITS Management System or the AIM System (the "Project"); B. Contractor represents that it has the knowledge and experience to carry out the Project, and desires to carry out the Project pursuant to the terms and conditions hereof, and; C. Based upon the representations made by Contractor, MTD desires to retain the services of Contractor to carry out the aforesaid Project, upon the within terms and conditions. NOW, THEREFORE, for valuable consideration, the receipt and sufficiency of which are hereby acknowledged, the parties do hereby agree as follows: 1. Effect of Recitals. The foregoing recitals are hereby made express provisions of this Agreement. 2. FTA Provisions. Not applicable to this agreement. 3. Public Works Provisions. This Project is subject to the State of California Provisions for Public Works Projects, which is attached hereto as Exhibit A and incorporated herein by this reference. 4. Technical Specifications. MTD issued on October 2, 2013, the AVL & ITS Management (AIM) System Specifications (the "Technical Specifications") contained in the Request for Proposals for AVL & ITS Management Systems (AIM). -
Analysis of the SAE J1708 Protocol Raine Saastamoinen
Volvo Construction Equipment AB Component Division Analysis of the SAE J1708 protocol Raine Saastamoinen Bachelor thesis report May - Juli 2008 School of Innovation Design and Engineering Mälardalen University, Västerås, Sweden Supervisor and Examiner: Johan Stärner Supervisors at company: Nils-Erik Bånkestad and Jarmo Talvén “ Engineers does’nt buy solutions they create them” LeCroy comersial 2 Abstract Component Division at Volvo Construction Equipment, develops electronic control units (ECU) to be used in entrepreneur machines. In an operating vehicle there are several ECU’s communicating with each other to make everything work as a complete. There are two main network protocols in use to solve different communication needs. One of them is using the SAE J1708 physical layer protocol in transmitting of the actual bits when exchanging information. Manufacturing of the units are made by external suppliers.Up to date, there is a lack of good tools, to verify that delivered components conforms to the J1708 specifications. WaveRunner 104 MXi, is an advanced digital oscilloscope with scripting possibilities. It has been used in this thesis work to find out, whether suitable or not to solve this problem. This thesis shows that analysis is possible and most important of all, in future potential of being a great tool for verification. 3 Acknowledgements Thanks to my supervisors Nils-Erik Bånkestad and Jarmo Talvén at VCE Component Division for professional guidance. Pushing me in the right direction when stumbeling into difficulties (especially after that important meeting the very first week). My supervisor at Mälardalen University, Johan Stärner, a friendly professional for support and important advices. -
An Overview of CAN-BUS Development, Utilization, and Future Potential in Serial Network Messaging for Off-Road Mobile Equipment Hannah M
Chapter An Overview of CAN-BUS Development, Utilization, and Future Potential in Serial Network Messaging for Off-Road Mobile Equipment Hannah M. Boland, Morgan I. Burgett, Aaron J. Etienne and Robert M. Stwalley III Abstract A Controller Area Network (CAN) is a serial network information technology that facilitates the passing of information between Electronic Control Units (ECUs, also known as nodes). Developed by BOSCH in 1986 to circumvent challenges in harness-connected systems and provide improved message handling in automo- biles, the CAN interface allows broadcast communication between all connected ECUs within a vehicle’s integrated electronic system through distributed control and decentralized measuring equipment. Since the early uses of CAN in car engine management, improvements in bitrate, bandwidth, and standardization protocols (such as ISO 11898 and SAE J1939) have led to CAN utilization in various industry applications, such as factory automation, aviation, off-highway vehicles, and telematics. Alternative wired and wireless technologies have been used to connect and network with CAN-BUS (such as Ethernet, Bluetooth, Wi-Fi, ZigBee, etc.), further expanding the diversity of applications in which the serial network is employed. In this chapter, the past, present, and prospective future developments of CAN technology, with focused attention on applications in the agricultural and off-road sectors are broadly examined. CAN technology fundamentals, standards creation, modern day uses, and potential functionalities and challenges specific to CAN in the wake of precision agriculture and smart farming are discussed in detail. Keywords: CAN-BUS, Serial Network, Agricultural Sector, Electronic Control Units 1. Introduction and Background A Controller Area Network (CAN) in a vehicle or machine is analogous to the nervous system of a living organism. -
Mastercan V-GATE
MasterCAN CC MasterCAN V-GATE MasterCAN C 232/485 Minsk, April 2013 Full range of vehicle operational data in a friendly format is a ready solution for safe and uninterrupted data reception from onboard vehicle buses for GPS/GLONASS fleet monitoring and vehicle fuel control management. 2 Operational Principle and Application of MasterCAN Vehicle Data Interfaces CAN bus (SAE J1939) and J1708 (SAE J1587) data reading; selecting and arranging parameters into messages that are easy to read and process on telematics terminals; CAN 2.0B, RS-232, and RS-485 output messages; reading and totalizing data from several DUT-E CAN fuel level sensors and sending corresponding output messages. 3 simple installation with contactless readers and that are included with the product; safe integration of several digital vehicle buses; less terminal customization time due to filtering of unnecessary data; direct onboard power supply – no need to use additional power supply units. 4 MasterCAN Models CC C 232/485 V-GATE Input Interface (protocol) CAN (SAE J1939) CAN (SAE J1939) CAN (SAE J1939) and J1708 (SAE J1587) Output Interface (protocol) CAN 2.0B (SAE J1939) RS-232 and RS-485 CAN 2.0B (SAE J1939) and RS-232 (ASCII/Modbus/DUT-E COM) (ASCII/Modbus/DUT-E COM) 5 Contents of MasterCAN Output Messages MasterCAN models with CAN output interface transmit FMS messages without changing them, and also form Telematics messages that include the most important vehicle operation parameters. MasterCAN models with RS-232 and RS-485 output interfaces either transmit vehicle operation parameters at request from a terminal (Modbus protocol) or do this in an automated mode in text format (ASCII protocol). -
John Kerrigan of the Procurement and SCM Department at [email protected] Or 215.580.8360
October 30, 2015 To Whom It May Concern: This letter constitutes Addendum No. 8 to SEPTA RFP No. 15-00086-AJFK for 40-Foot Low-Floor, Diesel-Electric Hybrid Transit Buses. Addendum No. 8 consists of the following change: 1. Addendum Change Tracker for Addendum 8 2. Section 6 – 40’ Hybrid Technical Specification Addendum No. 8 must be acknowledged by updating and signing the Acknowledgement of Addenda Form and including such within your RFP Technical Proposal. The Proposal Due Date has been extended until Close of Business on Friday, November 6, 2015. Any inquiries regarding this Addendum must be directed to John Kerrigan of the Procurement and SCM Department at [email protected] or 215.580.8360. Sincerely, John Kerrigan John Kerrigan Contract Administration Procurement and SCM Department Addendum No. 8 Change # Subject Specification Section Page # Change 1 AVM Section 6, TS 9.9.7.5 132 Added call-out for On Demand/Live Look-in 2 Engine Cooling Section 6, TS 7.7.1.1 42 Added Coolant Sensor Language Request for Proposal April 2015 RFP 15-00086-AJFK Southeastern Pennsylvania Transportation Authority SECTION 6: 40’ LOW FLOOR DIESEL-ELECTRIC HYBRID BUS TECHNICAL SPECIFICATION .................................................................. 1 TS 1. Scope ................................................................................................................................ 1 TS 2. Definitions ........................................................................................................................ 1 TS 2.1 Abbreviations................................................................................................................