Ventura County Todd Road Jail Health and Programing Unit
Total Page:16
File Type:pdf, Size:1020Kb
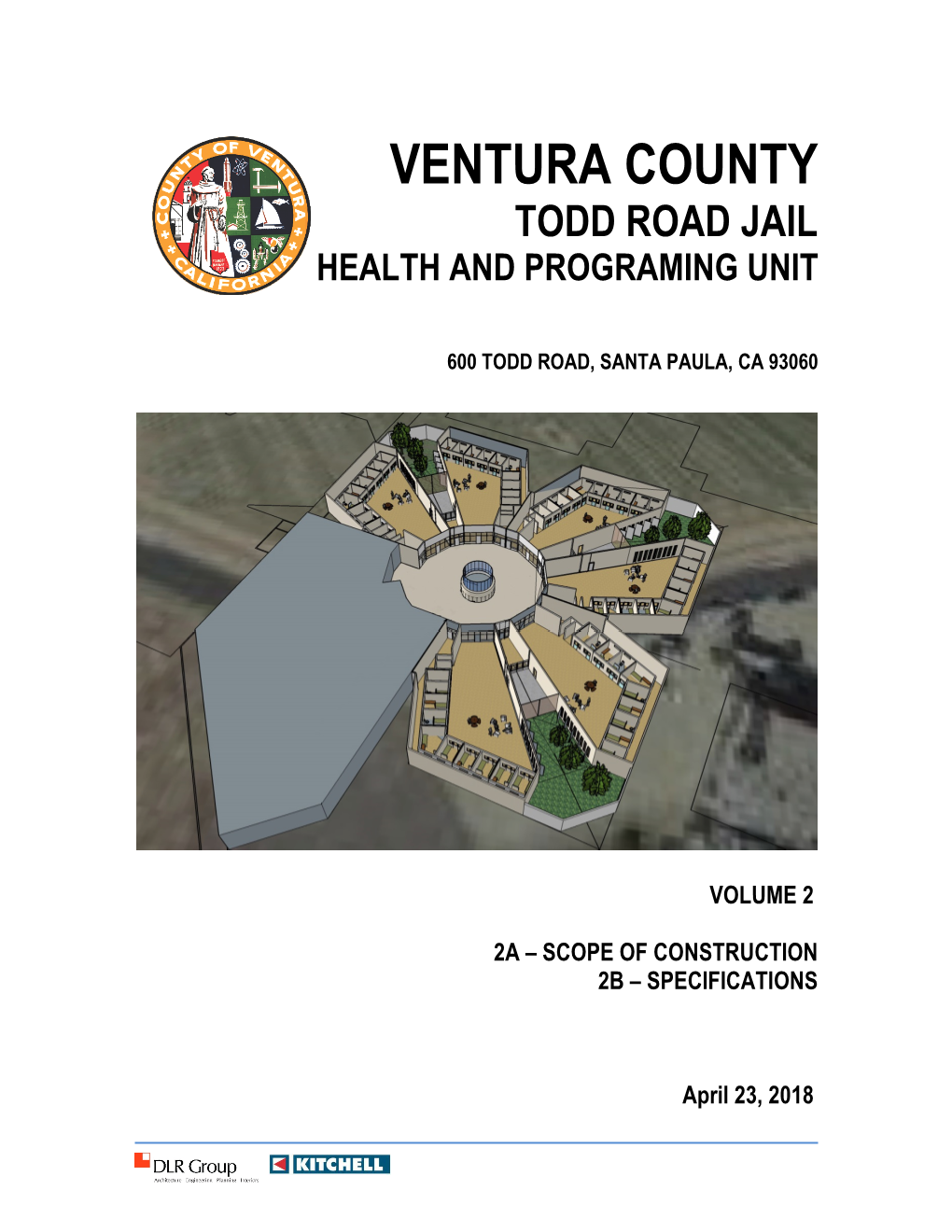
Load more
Recommended publications
-
New Fayette County Prison Volume 2 Divisions 03
SECTION 03 1000 CONCRETE FORMING AND ACCESSORIES PART 1 GENERAL 1.01 RELATED DOCUMENTS A. Drawings and general provisions of contract, including General and Supplementary Conditions and other Division 01 specification sections, apply to requirements of this Section. 1.02 SECTION INCLUDES A. Formwork for cast-in place concrete, with shoring, bracing and anchorage. B. Openings for other work. C. Form accessories. D. Form stripping. 1.03 RELATED REQUIREMENTS A. Section 03 2000 - Concrete Reinforcing. B. Section 03 3000 - Cast-in-Place Concrete. C. Section 04 2001 - Masonry Veneer: Spacing for veneer anchor reglets recessed in concrete. 1.04 REFERENCE STANDARDS A. ACI 117 - Specifications for Tolerances for Concrete Construction and Materials. B. ACI 301 - Specifications for Structural Concrete. C. ACI 318 - Building Code Requirements for Structural Concrete and Commentary. D. ACI 347R - Guide to Formwork for Concrete. E. ASTM B221 - Standard Specification for Aluminum and Aluminum-Alloy Extruded Bars, Rods, Wire, Profiles, and Tubes. F. ASTM B221M - Standard Specification for Aluminum and Aluminum-Alloy Extruded Bars, Rods, Wire, Profiles, and Tubes (Metric). G. PS 1 - Structural Plywood. 1.05 SUBMITTALS A. Shop Drawings: Indicate pertinent dimensions, materials, bracing, and arrangement of joints and ties. B. Designer's Qualification Statement. C. Design Data: As required by authorities having jurisdiction. 1.06 QUALITY ASSURANCE A. Designer Qualifications: Design formwork under direct supervision of a Professional Structural Engineer experienced in design of concrete formwork and licensed in the State in which the Project is located. 1.07 DELIVERY, STORAGE, AND HANDLING A. Deliver prefabricated forms and installation instructions in manufacturer's packaging. -
TSL-1 Appendix B Non-Government
U.S DEPARTMENT OF ENERGY TECHNICAL STANDARDS PROGRAM TSL-1 APPENDIX B: Non-Government Standards (NGS) Adopted by DOE 10 AMD 1 Standard for Portable Fire Extinguishers 2012 NESC Handbook National Electrical Safety Code(NESC) Handbook 310.2R-2013 International Concrete Repair Institute (ICRI) Selecting and Specifying Concrete Surface Preparation for Sealers, Coatings Polymer Overlays, and Concrete Repair A 112.18.1M Plumbing Fixture Fittings A 112.19.6 Hydraulic Requirements for Water Closets and Urinals AA SAA-46-516124 Anodized Architectural Aluminum AA Specifications for Aluminum Structures AA STFA-601711 The Surface Treatment and Finishing of Aluminum and Its Alloys AABC National Standard for Total System Balance Air Distribution-Hydronic Systems-Sound-Vibration- Field Surveys for Energy Audits AAHC Standards of the Accreditation Association for Ambulatory Health Care (AAAHC), Core and Adjunct Standards AAMA 1002.10 Aluminum Insulating Storm Products for Windows and Sliding Glass Doors AAMA 1002.9 Voluntary Specifications for Aluminum Combination Storm Windows for External Applications AAMA 101 Voluntary Specifications for Aluminum Prime Windows and Sliding Glass Doors AAMA 101/I.S.2 Voluntary Specifications for Aluminum, Vinyl (PVC) and Wood Windows and Glass Doors AAMA 1102.7 Voluntary Specifications for Aluminum Storm Doors AAMA 611 Anodized Architectural Aluminum AAMA 800 Sealant Specifications for Use with Architectural Aluminum AASHTO AAB Above and Beyond – The Environmental and Social Contributions of America’s Highway Programs -
Proj. No. GOLF003-17 Quail Creek Clubhouse 00 0101
SECTION 00 0101 PROJECT TITLE PAGE PROJECT MANUAL FOR OWNER'S PROJECT NUMBER: GOLF003-17 CITY OF FAIRHOPE REPAIRS TO QUAIL CREEK CLUBHOUSE BID NO. 003-18 KARIN WILSON, MAYOR FAIRHOPE CITY COUNCIL JACK BURRELL, CITY COUNCIL PRESIDENT DATE: 11-1-2017 PREPARED BY: NEW SOUTH ARCHITECTS, INC. Proj. No. GOLF003-17 00 0101 - 1 PROJECT TITLE PAGE Quail Creek Clubhouse SECTION 00 0103 PROJECT DIRECTORY PART 1 GENERAL 1.01 SECTION INCLUDES A. Identification of project team members and their contact information. 1.02 OWNER: A. Name: City of Fairhope. Fairhope City Hall. 161 N. Section Street. Fairhope. Alabama. 36532. (251) 928-2136. B. Primary Contact: All correspondence from the Contractor to the Architect will be through this party, unless alternate arrangements are mutually agreed upon at preconstruction meeting. 1. Project Management Consultant: a. Company Name: Engineering Design Technologies, Inc.. 9786-B Timber Circle. Spanish Fort. Alabama. 36527. (251) 680-2241. 2. Project Manager: a. Title: Senior Project Manager b. Contact Person: Lawrence Wilson, P.E.,. c. Email: [email protected]. 1.03 CONSULTANTS: A. Architect: Design Professional of Record. All correspondence from the Contractor regarding construction documents authored by Architect's consultants will be through this party, unless alternate arrangements are mutually agreed upon at preconstruction meeting. 1. Company Name: New South Architects, Inc.. 5184 Caldwell Mill Rd.. Suite 204-249. Birmingham. Alabama. 35244. (205) 620-1414. 2. Primary Contact: . a. Title: Architect of Record. b. Contact Person: David R. Mugg, President. c. Email: [email protected]. B. Structural Engineering Consultant: 1. Company Name Triple Sawyer, P.E. -
Jail Door Replacement Contract Documents.Pdf
INFORMATION ONLY - NOT A PART OF THIS CONTRACT In accordance with SB 854 passed by the California State Senate on June 20, 2014, all contractors and subcontractors bidding and performing work on Public Works Projects are required to register with the Department of Industrial Relations (DIR) on an annual basis. See the Instructions to Bidders for information on California Labor Code Section 1771.1. Division 20, Chapter 6.95 of the California Health and Safety Code, in part, requires the submission of a Business Plan for Emergency Response by the operators of sites where hazardous materials are stored and handled at or above the State of California minimum reportable amounts. These amounts currently are 55 gallons of a liquid, 500 pounds of a solid, or 200 cubic feet at standard temperature and pressure for a compressed gas. (H&S Section 25507) The Shasta County Division of Environmental Health, which has been designated by the Shasta County Board of Supervisors as the administering agency for Chapter 6.95 of the California Health and Safety Code, advises that a fee may be assessed not to exceed the actual costs of processing and for inspection, if an inspection is conducted. The State of California Franchise Tax Board requires that whenever payments are made to a non- resident independent contractor in excess of $1,500 for services rendered, 7% of the gross amount must be withheld. A non-resident is anyone who is not a resident of California. An individual who comes into the state to perform a contract of short duration is considered to be a non-resident. -
Detention Doors and Frames 1
DETENTION DOORS AND FRAMES DETENTION DETENTION BALLISTIC SINGLE DOOR PAIR DOOR GREEN LISTED BY GUARDIAN USA-MADE GLAZING FIRE TESTING LABORATORIES CUSTOM OPTIONS: FIRE RATED POSITIVE TEMPERATURE APPROVED SMOKE RATED PRESSURE RISE WITH SAFTI FIRST GLAZING PRODUCT ADVANTAGES Tested to ASTM F1450, Standard Test Methods for Hollow Metal Swinging Door Assemblies for Detention & Correctional Facilities; and certified to meet NAAMM/HMMA 863 requirements for use in detention and correctional facilities. Complies with ASTM F1233, Standard Test Method for Security Glazing Materials and Systems; ASTM F1915, Standard Test Methods for Glazing for Detention Facilities; ASTM F1592, Standard Test Methods for Detention Hollow Metal Vision Systems; ASTM F1577, Standard Test Methods for Detention Locks for Swinging Doors; ASTM F1643, Standard Test Methods for Detention Locks for Swinging Doors; SDI A250 Specifications for Standard Steel Doors and Frames. Meets UL 752 Level 3 Ballistic ratings. All detention doors that meet F1450 are required to have UL 752 Level 3. EXAMPLES OF CDCR DOORS Depending on glazing selection, door thickness ranges from 2 in. to 4 in. Can be supplied to also meet smoke and fire ratings up to 3 hours with positive pressure. For interior or exterior applications. Listed and labeled by Guardian Fire Testing Laboratories, Inc. USA-manufactured for fast lead times and competitive pricing. 5 year manufacturer’s warranty. CDCR Door Type A CDCR Door Type C CDCR Door Type F DOOR CONSTRUCTION APPROVALS Doors and door frames are made in 14-gauge steel and ASTM F1450, ASTM F1233, ASTM F1915, ASTM 1592, insulated to meet the 450° F temperature rise door ASTM F1577, ASTM F1643, SDI A250, UL 752, UL 1784, requirements. -
Schedule 1 Statement of Requirements
SCHEDULE 1 STATEMENT OF REQUIREMENTS VALLEYVIEW PROJECT Valleyview Project Schedule 1 – Statement of Requirements Design-Build Agreement EXECUTION COPY TABLE OF CONTENTS 1. INTERPRETATION .............................................................................................................................. 1 1.1 Definitions .................................................................................................................................. 1 1.2 Overview .................................................................................................................................... 3 1.3 Acronym List .............................................................................................................................. 3 2. GENERAL ............................................................................................................................................ 8 2.1 Standards of Design and Construction ...................................................................................... 8 2.2 Indicative Design ..................................................................................................................... 14 2.3 Design Requirements .............................................................................................................. 15 3. DESIGN PRINCIPLES ....................................................................................................................... 21 3.1 Project Vision .......................................................................................................................... -
Viewweb/Contentfetcher?Commentpar
National Fire Protection Association Report https://submittals.nfpa.org/TerraViewWeb/ContentFetcher?commentPar... Second Revision No. 6633-NFPA 101-2019 [ Global Comment ] Throughout Chapter 40 and Chapter 42 and any associated annex material change the term "flammable and combustible liquid" to "ignitable (flammable and combustible) liquid". Submitter Information Verification Committee: SAF-IND Submittal Date: Mon Jul 15 10:31:19 EDT 2019 Committee Statement Committee This correlates the NFPA 101 terminology with changes to NFPA 30 terminology. Since NFPA Statement: 30 is the expert document, NFPA 101 is updating the terminology to match. Response SR-6633-NFPA 101-2019 Message: Ballot Results This item has passed ballot 30 Eligible Voters 6 Not Returned 23 Affirmative All 1 Affirmative with Comments 0 Negative with Comments 0 Abstention Not Returned Almannai, Ali Birchler, Donald C. Culp, Christopher Johnson, Aaron Jones, Adam C. Richardson, Dennis A. Affirmative All Cummings, Ryan Cusimano, Alberto Dacus, Sheldon Dale, Stephen E. Dawe, Nicholas A. Desrosier, John Dudley, Jeffry T. Page 1 of 373 1 of 367 10/21/2019, 3:45 PM National Fire Protection Association Report https://submittals.nfpa.org/TerraViewWeb/ContentFetcher?commentPar... Early, Rob Hanson, Robert E. Humble, Jonathan Klein, Andrew S. Krantz, Sr., Neal W. Laberge, Todd Lozano-Rosales, Roberto McLaughlin, Patrick A. Pierrottie, Jerald Pruett, Scot Sheldon, Steven A. Skinker, Cleveland B. Swiecicki, Bruce J. Tabar, David C. White, Michael S. Wren, Carl D. Affirmative with Comment Olsen, Brian L. Introduction of the term does little to advance regulatory compliance or improve safety. Significant effort will be required to retrain those within the oil and gas sector and to update terminology use throughout the industry. -
January 2019
U.S. Army Corps of Engineers U.S. Navy Naval Facilities Engineering Command U.S. Air Force Civil Engineer Center U.S. National Aeronautics and Space Administration Unified Master Reference List (UMRL) January 2019 UNIFIED MASTER REFERENCE LIST (UMRL) This document lists publications referenced in the Unified Facilities Guide Specifications (UFGS) of the Corps of Engineers (USACE), the Naval Facilities Engineering Command (NAVFAC), the Air Force Civil Engineer Center (AFCEC), and the guide specifications of the National Aeronautics and Space Administration (NASA). The listing is current to the date of this publication. This version of the UMRL may contain more than one version of a single reference. This is part of the integration of NASA fully into the UFGS system. Future versions will contain only a single version of each reference. The UMRL lists issuing organizations alphabetically by name and not by acronym. In some cases more than one organization may use the same acronym. If a listed reference does not have a designator assigned by the issuing organization, a designator for the document has been established for use within SpecsIntact. Where a reference has a joint designation (example: ANSI/BHMA), the UMRL usually lists the reference under the proponent organization (example: The proponent of ANSI/BHMA A156.1 is BHMA; therefore the reference in the UMRL is under BHMA). This procedure simplifies referencing and ordering of joint documents, and specification sections should cite such reference publications using the same designations used in the UMRL. Acronyms of major proponent organizations listed in the UMRL which have joint publications with other standards organization are as follows: Proponent Joint With Organization ASME ANSI ASTM AASHTO BHMA ANSI EIA ANSI IEEE ANSI NEMA ANSI NFPA ANSI Guide Specification section UFGS-01 42 00 SOURCES FOR REFERENCE PUBLICATIONS includes all organizations listed in the UMRL. -
Volume 33, Issue 21 Virginia Register of Regulations June 12, 2017 2295 PUBLICATION SCHEDULE and DEADLINES
VOL. 33 ISS. 21 PUBLISHED EVERY OTHER WEEK BY THE VIRGINIA CODE COMMISSION JUNE 12, 2017 VOL TABLE OF CONTENTS Register Information Page ......................................................................................................................................... 2295 Publication Schedule and Deadlines ....................................................................................................................... 2296 Petitions for Rulemaking ............................................................................................................................................ 2297 Notices of Intended Regulatory Action ................................................................................................................. 2299 Regulations ....................................................................................................................................................................... 2300 3VAC5-70. Other Provisions (Final) ..................................................................................................................................... 2300 4VAC20-720. Pertaining to Restrictions on Oyster Harvest (Final) ...................................................................................... 2300 4VAC20-910. Pertaining to Scup (Porgy) (Final) .................................................................................................................. 2301 4VAC20-950. Pertaining to Black Sea Bass (Final) ............................................................................................................. -
Tarrant County – Juvenile Center Project 2701 Kimbo Road Fort Worth, Texas 76111
For: Tarrant County – Juvenile Center Project 2701 Kimbo Road Fort Worth, Texas 76111 Re: Addendum #3R1 Dated August 26, 2019 Documents: HDR Addendum #3 – Dated August 20, 2019 Pre-Bid RFI #2 – Dated 8/22/19 Pre-Bid RFI #8R1 – Dated 8/26/19 Bid Date: Due to the above two (2) Pre-Bid RFI’s being updated/issued the Bid Date is revised to: 2:00 p.m. Tuesday, September 3, 2019 For the following scopes only: Division 11 - Detention Equipment Division 28A – Security and Detention Equipment ADDENDUM NO. 3 DATE: August 20th 2019 PROJECT: Tarrant County Juvenile Center Project 2701 Kimbo Road Fort Worth Texas, 76111 HDR Project No. 10071184 NOTICE: THIS ADDENDUM IS ISSUED BY ARCHITECT TO ALL KNOWN INDIVIDUALS, FIRMS OR CORPORATIONS WHO HOLD BIDDING AND CONTRACT DOCUMENTS FOR ABOVE LISTED PROJECT. THIS ADDENDUM IS HEREBY MADE A PORTION OF BIDDING AND CONTRACT DOCUMENTS, AS APPROPRIATE. ACKNOWLEDGE RECEIPT OF THIS ADDENDUM IN APPROPRIATE SPACE ON BID FORM. HDR ARCHITECTURE, INC. Project Number 10071184 Tarrant County August 20, 2019 Juvenile Center Project COVER (AD-3) - 1 Project Number 10071184 Tarrant County August 20, 2019 Juvenile Center Project COVER (AD-3) - 2 ADDENDUM 3 INDEX PAGE Revisions to Project Manual ................................................................................................................... Attachments: Specifications ADDENDUM 2 REVISIONS TO PROJECT MANUAL 1.1 GENERAL NOTE A. If paragraph has changed by this addendum, entire page (or entire section) has been reprinted. “AD” helps indicate line changed. Contractor is responsible for review of entire page to determine all changes made within paragraph. B. The following Documents or Sections have changed: 1. Section 11 19 00 Detention Equipment Project Number 10071184 Tarrant County August 20, 2019 Juvenile Center Project COVER (AD-3) - 3 Tarrant County Juvenile Center Project Construction Documents Project Manual 100% Construction Documents AD #3 August 20, 2019 HDR Project No.