A Model for Numerical Simulation of Variable Stator Axial Flow Compressors
Total Page:16
File Type:pdf, Size:1020Kb
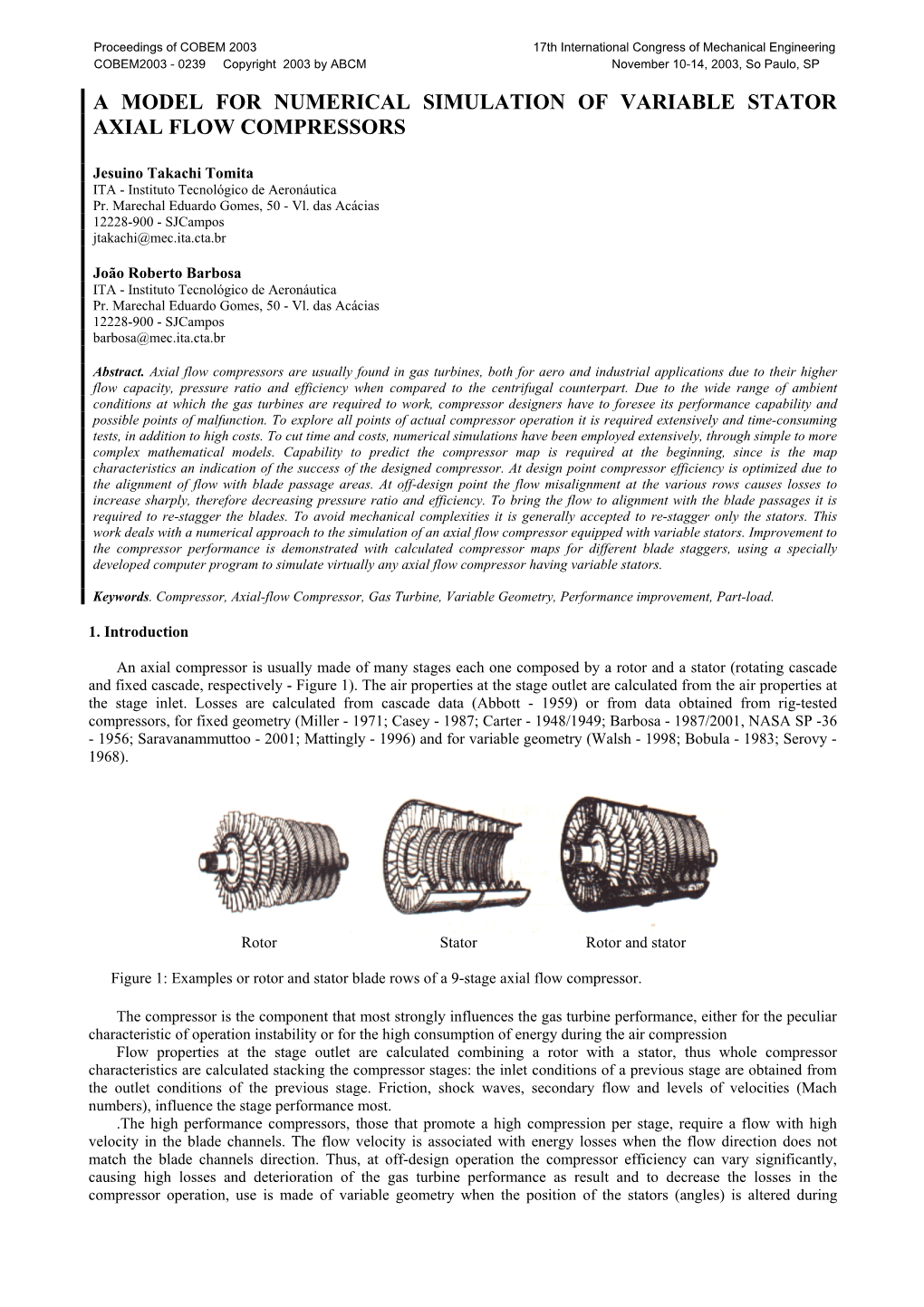
Load more
Recommended publications
-
Steady and Unsteady Performance of a Transonic Compressor Stage with Non-Axisymmetric End Walls
Steady and Unsteady Performance of a Transonic Compressor Stage with Non-Axisymmetric End Walls Dissertation Dipl.-Ing. Steffen Reising Fachgebiet für Gasturbinen, Luft- und Raumfahrtantriebe Technische Universität Darmstadt Juli 2010 Steady and Unsteady Performance of a Transonic Compressor Stage with Non-Axisymmetric End Walls Vom Fachbereich Maschinenbau an der Technischen Universität Darmstadt zur Erlangung des Grades eines Doktor-Ingenieurs (Dr.-Ing.) genehmigte Dissertation vorgelegt von Dipl.-Ing. Steffen Reising aus Alzenau in Ufr. Berichterstatter: Prof. Dr.-Ing. Heinz-Peter Schiffer Mitberichterstatter: Prof. rer. nat. Michael Schäfer Tag der Einreichung: 02. Juli 2010 Tag der mündlichen Prüfung: 19. Oktober 2010 Darmstadt 2011 D 17 Erklärung zur Dissertation Hiermit versichere ich, die vorliegende Dissertation ohne Hilfe Dritter nur mit den angegebenen Quellen und Hilfsmitteln angefertigt zu haben. Alle Stellen, die aus Quellen entnommen wurden, sind als solche kenntlich gemacht. Diese Arbeit hat in gleicher oder ähnlicher Form noch keiner Prüfungsbehörde vorgelegen. (S. Reising) Darmstadt, 02. Juli 2010 Acknowledgements This dissertation results from my three and a half years as a research assistant at the Institute of Gas Turbines and Aerospace Propulsion at Technische Universiät Darmstadt. This work is sponsored by the German Research Foundation (DFG) within the scope of the postgraduate programme ’Unsteady System Modelling of Aircraft Engines’ within an industrial collaborative research project with Rolls-Royce Deutschland Company. Foremost, I would like to thank my thesis advisor and reviewer Prof. Dr.-Ing. Heinz-Peter Schiffer for initiating the research topic, his guidance and contribution, for the many productive discussions and his confidence in my work. Gratitude also goes to Prof. Dr. -
Dr. P. Pilidis
CRANFIELD UNIVERSITY SCHOOL OF MECHANICAL ENGINEERING Ph.D. THESIS AcademicYear 1996/7 Louay ALEED VARIABLE CYCLE PROPULSION SYSTEMS FOR A SUPERSONIC CIVILTRANSPORT Supervisor: Dr. P. Pilidis April 1997 This thesis is submitted in partial fulfilment of the requirements for the Degree of Doctor of Philosophy. Summary Summary The different aspects of overall performance of three variable cycle engines (VCE) candidatesfor future supersoniccivil transport are analysedin this work. These aspects concern the design and off-design points performance, the airframe engine integration and variable geometrycompressor and turbine design and performance. The three engines are compared to a traditional turbojet. The variable compressor maps were obtained with their running lines for the whole mission profile including the transition mode from medium býpassratio to a lower bypassratio turbofan. The specific fuel consumption (SFC) of the VCEs showed a significant improvement, especially at subsonic cruise, relative to a Turbojet engine. The extent of the variable geometry on the compressor stator angles, mixing area and the nozzle throat and exit areasis evaluated. The Fuel bill is estimatedfor two standardmission profiles. The effect of installation is estimatedon an isolated nacelle. A sizing calculation is carried out for the whole nacelleincluding the intake and the nozzle. The drag due to the friction, pre-entry, afterbody and the shock waves is calculatedin order to estimated the installed performanceof the three engines. In the search of improving the VCE performanceat subsonic cruise, the use of variable geometry at the low pressure turbine for the Turbofan-Turbojet engine is investigated. The effects of varying the LP turbine guide vanes stagger angle on the engine performance and component parametersare analysed. -
Gas Turbine Performance Deterioration
GAS TURBINE PERFORMANCE DETERIORATION by Cyrus B. Meher-Homji Chief Engineer Mustapha A. Chaker Chief Research Scientist Mee Industries Inc., Gas Turbine Division Monrovia, California and Hatim M. Motiwala President and CEO Monimax Inc. Levitown, New York Cyrus B. Meher-Homji is Chief Engineer Hatim M. Motiwala is President and of Mee Industries Inc.’s Gas Turbine CEO of Monimax Inc., in Levitown, New Division. He has 21 years of industry York, a company specializing in developing experience including gas turbine and software solutions for plant performance compressor design, troubleshooting, and monitoring. He has developed perform- engine development. Mr. Meher-Homji’s ance monitoring software that has been areas of interest are power augmentation, applied to a wide range of turbomachinery aerothermal analysis, gas turbine deterio- used on offshore platforms, thermal power ration, blade failures, and vibration plants, and large combined cycles. His analysis. Prior to joining Mee Industries, areas of interest include thermodynamic he worked as a Turbomachinery Specialist modeling of gas turbines and compressors, at Bechtel Corporation and as Director of Engineering at Boyce and aerothermal and vibration condition monitoring of Engineering International Inc. turbomachinery. Prior to starting Monimax in 1997, Mr. Motiwala Mr. Meher-Homji has a B.S. degree (Mechanical Engineering) worked as a Senior Systems Design Engineer at Boyce Engineer- from Shivaji University, an M.E. degree from Texas A&M ing International on software development of thermodynamic University, and an M.B.A. degree from the University of Houston. condition monitoring systems and high performance spectral He is a registered Professional Engineer in the State of Texas, and analysis software. -
Elements of Gas Turbine Propulsion Jackd.Mattingly
Elements of Gas Turbine Propulsion JackD.Mattingly Foreword by ' Hans von Ohain German Inventor ofthe Jet Engine GE-1014.001 GE-1014.002 ELEMENTS OF GAS TURBINE PROPULSION GE-1014.003 McGraw-Hill Series in Aer9nautical and Aerospace Engineering Consulting Editor John D. Anderson, ir., University of Maryland Anderson: Computational Fluid Dynamics: The Basics with Applications Anderson: Fundamentals of Aerodynamics Anderson: Hypersonic and High Temperature Gas Dynamics Anderson: Introduction to Flight Anderson: Modern Compressible Flow: With Historical Perspective Burton: Introduction to Dynamic Systems Analysis D'Azzo and Houpis: Linear Control System Analysis and Design Donaldson: Analysis of Aircraft Structures: An Introduction Gibson.: Principles of Composit~ Material Mechanics Kane, Likins, and Levinson: Spacecraft Dynamics Katz and Plc.itkin: Low-Speed Aerodynamics: From Wing Theory to Panel Methods Mattingly: Elements of. Gas Turbine Propulsion ~elson: Flight Stability and Automatic Control Peery and Azar: Aircraft Structures Rivello:. Theory and Analysis of Flight Structures Schlichting: Boundary Layer Theory White: Viscous Fluid Flow Wiesel: Spaceflight Dynamics GE-1014.004 McGraw-Hill Series in Mechanical Engineering Consulting Editors Jack P. Holman, Southern Methodist University John R. Lloyd, Michigan State University Anderson: Computational Fluid Kelly: Fundamentals of Mechanical Dynamics: The Basics with Applications Vibrations Anderson: Modern Compressible Flow: Kimbrell: Kinematics Analysis and With Historical Perspective -
Performance Prediction and Simulation of Gas Turbine Engine Operation (La Pr´Evision Des Performances Et La Simulation Du Fonctionnement Des Turbomoteurs)
RTO-TR-044 AC/323(AVT-018)TP/29 NORTH ATLANTIC TREATY ORGANISATION RTO-TR-044 RESEARCH AND TECHNOLOGY ORGANISATION BP 25, 7 RUE ANCELLE, F-92201 NEUILLY-SUR-SEINE CEDEX, FRANCE RTO TECHNICAL REPORT 44 Performance Prediction and Simulation of Gas Turbine Engine Operation (La pr´evision des performances et la simulation du fonctionnement des turbomoteurs) Report of the RTO Applied Vehicle Technology Panel (AVT) Task Group AVT-018. Published April 2002 Distribution and Availability on Back Cover This page has been deliberately left blank Page intentionnellement blanche RTO-TR-044 AC/323(AVT-018)TP/29 NORTH ATLANTIC TREATY ORGANISATION RESEARCH AND TECHNOLOGY ORGANISATION BP 25, 7 RUE ANCELLE, F-92201 NEUILLY-SUR-SEINE CEDEX, FRANCE RTO TECHNICAL REPORT 44 Performance Prediction and Simulation of Gas Turbine Engine Operation (La pr´evision des performances et la simulation du fonctionnement des turbomoteurs) Report of the RTO Applied Vehicle Technology Panel (AVT) Task Group AVT-018. The Research and Technology Organisation (RTO) of NATO RTO is the single focus in NATO for Defence Research and Technology activities. Its mission is to conduct and promote cooperative research and information exchange. The objective is to support the development and effective use of national defence research and technology and to meet the military needs of the Alliance, to maintain a technological lead, and to provide advice to NATO and national decision makers. The RTO performs its mission with the support of an extensive network of national experts. It also ensures effective coordination with other NATO bodies involved in R&T activities. RTO reports both to the Military Committee of NATO and to the Conference of National Armament Directors. -
Experimental Development of Compressor and Turbine Performance Maps for Turbomachinery
Experimental Development of Compressor and Turbine Performance Maps for Turbomachinery Aerospace Engineering Department California Polytechnic State University, San Luis Obispo by, Michael W. Green April, 2010 © 2010 Michael W. Green Experimental Development of Compressor and Turbine Performance Maps for Turbomachinery Michael W. Green 1 California Polytechnic State University, San Luis Obispo, CA, 93407 Turbomachinery performance maps are used to reveal the on and off design performance of compressors and turbines. These maps plot the component’s pressure ratio versus the corrected flow rate for multiple engine rotor speeds. In this experiment, a Boeing T50-BO-8A converted turbojet engine was operated at a wide variety of rotor speeds with orifice plates of different sizes to vary the flow rate. The corrected flow rate through the turbojet ranged from 1.32 to 2.55 lb/s. The pressure ratios for the compressor and turbine ranged from 2.0 to 4.3 and from 1.7 to 4.3, respectively. The resulting performance maps showed the correct overall trend of increasing flow rate and pressure ratio with higher rotor speeds. However, the individual speed lines were very inconsistent and lacked discernable trends. It was concluded that bench testing the compressor and turbine components is the ideal way to develop the performance maps. Table of Figures ............................................................................................................................................................. 2 Nomenclature ............................................................................................................................................................... -
Prediction of Non-Uniform Distorted Flows, Effects on Transonic Compressor Using CFD, Regression Analysis and Artificial Neural Networks
applied sciences Article Prediction of Non-Uniform Distorted Flows, Effects on Transonic Compressor Using CFD, Regression Analysis and Artificial Neural Networks Muhammad Umer Sohail 1,2,* , Hossein Raza Hamdani 2, Asad Islam 3,4 , Khalid Parvez 2, Abdul Munem Khan 2, Usman Allauddin 5, Muhammad Khurram 1 and Hassan Elahi 6 1 Department of Mechanical Engineering, National University of Technology, Islamabad 44000, Pakistan; [email protected] 2 Department of Aeronautics & Astronautics, Institute of Space Technology, Islamabad 44000, Pakistan; [email protected] (H.R.H.); [email protected] (K.P.); [email protected] (A.M.K.) 3 School of Energy and Power Engineering, Beihang University, Beijing 100191, China; [email protected] 4 Department of Mechanical and Aerospace Engineering, Air University, Islamabad 44000, Pakistan 5 Department of Mechanical Engineering, NED University of Engineering & Technology, Karachi 75270, Pakistan; [email protected] 6 Department of Mechanical and Aerospace Engineering, Sapienza University of Rome, 00185 Rome, Italy; [email protected] * Correspondence: [email protected]; Tel.: +92-344-5266-876 Featured Application: Development of a transonic compressor instability prediction tool un- der distorted inlet flow conditions using extensive CFD runs for a supervised learning dataset. Citation: Sohail, M.U.; Hamdani, ANN with optimal algorithm and different regression learning has been selected to produce all- H.R.; Islam, A.; Parvez, K.; Khan, inclusive transonic compressor rotor performance and behavior at different inlet conditions. A.M.; Allauddin, U.; Khurram, M.; Elahi, H. Prediction of Non-Uniform Abstract: Non-uniform inlet flows frequently occur in aircrafts and result in chronological distortions Distorted Flows, Effects on Transonic of total temperature and total pressure at the engine inlet. -
The Dynamics of Stall and Surge Behavior in Axial-Centrifugal Compressors
The Dynamics of Stall and Surge Behavior in Axial-Centrifugal Compressors by William T. Cousins Dissertation submitted to the Faculty of the Virginia Polytechnic Institute and State University in partial fulfillment of the requirements for the degree of DOCTOR OF PHILOSOPHY in Mechanical Engineering Walter F. O’Brien, Chairman Eugene F. Brown Milt W. Davis, Jr. Wing F. Ng Joseph A. Schetz December 2, 1997 Blacksburg, Virginia Key Words: Compressor, Stall, Surge, Unsteady-Flow, Dynamics, Axial, Centrifugal Copyright 1997, William T. Cousins The Dynamics of Stall and Surge Behavior in Axial-Centrifugal Compressors by William T. Cousins Committee Chairman: Walter F. O’Brien Department of Mechanical Engineering ABSTRACT The phenomena of stall and surge in axial-centrifugal compressors is in- vestigated through high-response measurements of both the pressure field and the flowfield throughout the surge cycle. A unique high-response forward-facing and aft-facing probe provides flow information. Several axial-centrifugal com- pressors are examined, both in compressor rigs and engines. Extensive dis- cussion is presented on the differences in axial and centrifugal rotors and their effect on the system response characteristics. The loading parameters of both are examined and data is presented that shows the increased tolerance of the centrifugal stage to instability. The dynamics of the compressor blade response are shown to be related to the transport time of a fluid particle moving through a blade passage. The data presented provides new insight into the dynamic in- teractions that occur prior to and during stall and surge. In addition, the incep- tion of rotating stall and the inception of surge are shown to be the same phe- nomena.