Research Memorandum
Total Page:16
File Type:pdf, Size:1020Kb
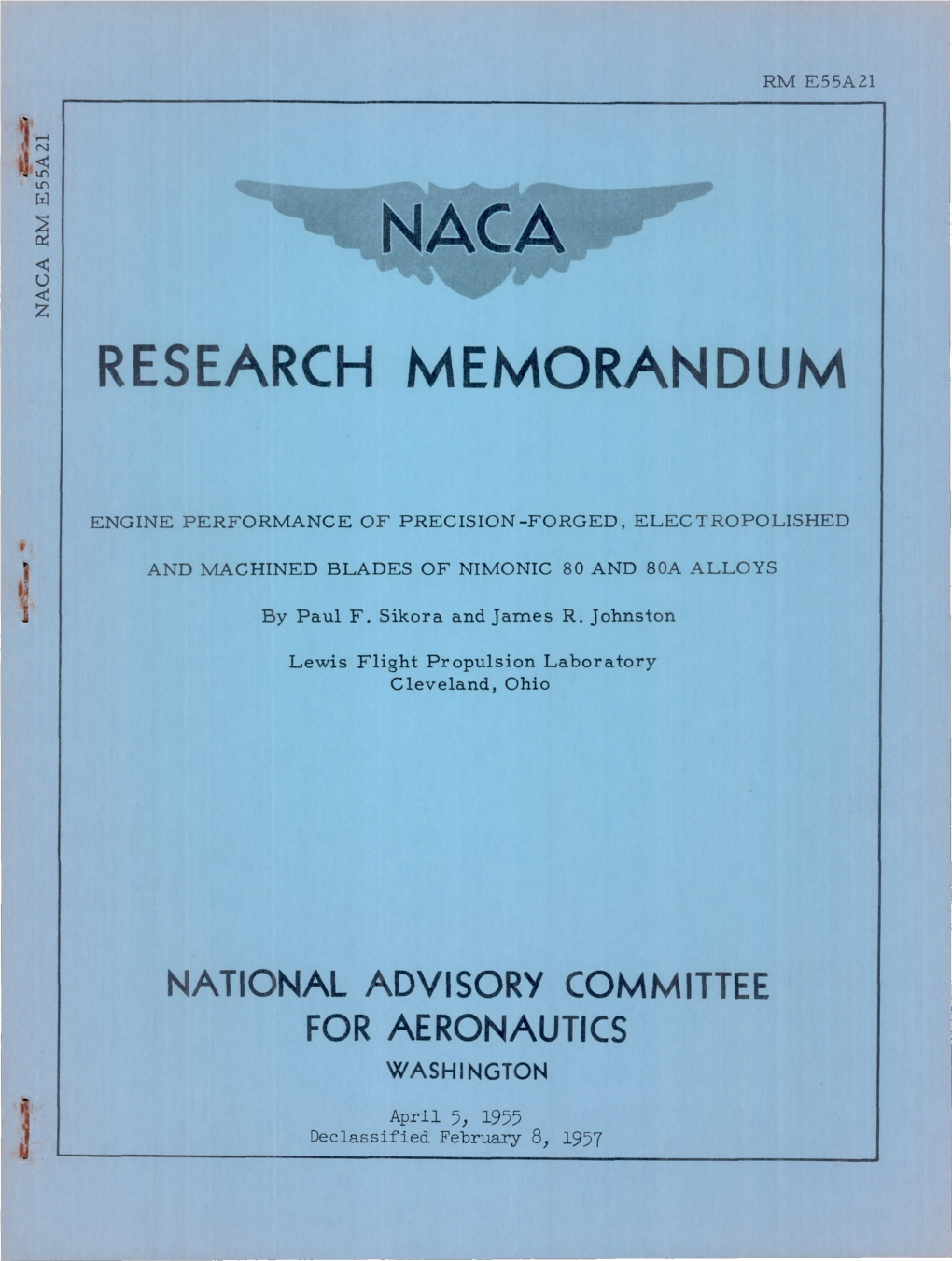
Load more
Recommended publications
-
Capabilities of Midlands Aerospace Companies 2010-2011 Midlands Capability for the World’S Aerospace Industry
Capabilities of Midlands Aerospace Companies 2010-2011 Midlands capability for the world’s aerospace industry The Midlands Aerospace Alliance is pleased to present you with the updated 20010-11 edition of our member capability directory. It has been designed to help you identify world-class Midlands partners and suppliers for your aerospace programmes and projects. The Midlands is home to one of the world’s biggest aerospace clusters, and aerospace systems designed and made in the Midlands can be found on the world’s most advanced aircraft. Leading names such as Aero Engine Controls, Goodrich, Meggitt, Moog and Rolls- Royce are major players in a region world-renowned for its core competency technologies: tTZTUFNTUIBUQPXFSBJSDSBGUoHBTUVSCJOFFOHJOFTBOEPUIFSQSPQVMTJPOTZTUFNT tTZTUFNTUIBUDPOUSPMUIFNPWJOHQBSUTPGBJSDSBGUBOEFOHJOFToFMFDUSJDBM NFDIBOJDBM electronic, hydraulic and pneumatic tTQFDJBMJTUNFUBMBOEDPNQPTJUFNBUFSJBMTUIBUFOBCMFUIFTFTZTUFNTUPQFSGPSNXJUI precision in exacting environments tTQFDJBMJTUFOHJOFFSJOHEFTJHOTFSWJDFT GBDUPSZFRVJQNFOUBOEUPPMJOH The Midlands business environment fosters the highest levels of innovation. Aerospace supply chains extend deep into our world-class advanced engineering economy. We access and invest in a dynamic skills base, with more than 45,000 skilled people working in the region’s aerospace industry. The mission of the Midlands Aerospace Alliance is to enhance cooperation between customers, suppliers and partners in the Midlands and globally, to help improve the performance of all our companies and organisations. We invite you to join us, using this directory to identify your new partners and suppliers. Dr Andrew Mair Chief Executive Midlands Aerospace Alliance The Midlands Aerospace Alliance (MAA) website provides further information and access to all MAA publications. The information in this directory is available and constantly updated, as a searchable database on the website. -
Capabilities of Midlands Aerospace Companies
Capabilities of Midlands Aerospace Companies 2017-2018 Midlands capability for the world’s aerospace industry he Midlands Aerospace Alliance is pleased to present you with the updated 2017-18 edition of our member capability directory T– which marks our fourteenth annual edition. It has been designed to help you identify world-class Midlands partners and suppliers for your aerospace programmes and projects. The Midlands is home to one of the largest aerospace clusters in the world. Aerospace technologies designed and made in the Midlands can be found on the world’s most advanced aircraft. Leading names such as Meggitt, Moog, Rolls-Royce and UTC Aerospace Systems are major players in a region renowned for its core competency technologies: • systems that power aircraft – gas turbine engines and other propulsion systems • systems that control the moving parts of aircraft and engines – electrical, mechanical, electronic, hydraulic and pneumatic • specialist metal and composite materials that enable these systems to perform with precision in exacting environments • specialist engineering design services, factory equipment and tooling. The Midlands business environment fosters the highest levels of innovation. Aerospace supply chains extend deep into our cluster’s world-class advanced engineering economy. We access and invest in a dynamic skills base, with more than 45,000 skilled people working in our aerospace industry. The mission of the Midlands Aerospace Alliance is to enhance cooperation between customers, suppliers and partners in the Midlands and globally, so that we can improve the performance of all our companies and organisations. We invite you to join us, using this directory to identify the new partners and suppliers you need to make your projects successful. -
High Temperature Parts
AGARD-CP-317 SMaintenance in Service of High Temperature Parts II- C)3 .3 L DISTRIBUTION AND AVAILABILITY ON BACK COVER Best Available Copy AGARD-CP-317 NORTH ATLANTIC TREATY ORC iZATION ADVISORY GROUP FOR AEROSPACE RESEARCH AND DEVELOPMENT (ORGANISATION DU TRAITE DE L'ATLANTIQUE NORD) AGARD Conference Proceedings No.317 MAINTENANCE IN SERVICE OF HIGH-TEMPERATURE PARTS & Papers presented at the 53rd Meeting of the AGARD Structures and Materials Panel held in Noordwijkerhout, the Netherlands 27 September-2 October 1981. THE MISSION OF AGARD Mhe mission of' AARI) is to bring together tile leading peloRalitie,, of the NATO nations in tile fields of Neiencv- and technology relating to aerospace for the following purpose-% of scientific and technical infonnation: SExchanging .Continuously stimulating advances in the aerospace sciences relevant to strengthening thie coniion defence posture. lnpro'ing the co-operation among member nations in aerospace researclh and developmenrt: Providing scientific and tccmt,-al advice and assistance to the North Atlantic Military Committee in the field of aerospace research and de'. elopnment Rendering scicultit'ic and tc:hmeal aslIstancc. is requested. to oher NATI) bodies and to nmember nations in connection with leýsvearh and devclopnielt problelm, in tfie acro.pace field: r!'tosiding assistance to inemhbter nations for the purpose of increasing their scie ntitiL anid tech1nical pot en tiall Recollmllmlending effectisc ways for tile melmjllber nLlat.tIlo,tO Use their research and development capabilities Ifm the conut on benefit of the NAI 0 co0in t1LtN - I'lhc highest authority wit hini A(.A RI) is the National Delegates Board cowisising of officially appointcd senior representati', fiom each member nation. -
Examination of Material Variation on the Life of Gas Turbine Backing-Up Renewable Energy Sources
IOSR Journal of Mechanical and Civil Engineering (IOSR-JMCE) e-ISSN: 2278-1684,p-ISSN: 2320-334X, Volume 16, Issue 1 Ser. IV (Jan. - Feb. 2019), PP 60-68 www.iosrjournals.org Examination of Material Variation on the Life of Gas Turbine Backing-Up Renewable Energy Sources Ezeddin Ali*, Suresh Sampath, Pericles Pilidis, Saleh Mohammed Department of Power and Propulsion, School of Aerospace, Transport and Manufacturing, Cranfield University, Cranfield, Bedfordshire, MK43 0AL, UK *Corresponding Author: Ezeddin Ali Abstract: Gas turbine life and efficiencydepend on the operating environment and material performance. Material selection is of prime importance to achieve high life and efficiency. This paper focuses on the study of the effect of material properties and variation in alloy composition ofa high- pressure turbine blade on gas turbine life when works in the flexible mode as a pick-up of renewable sources.A tool has been developed wherein different scenarios can be simulated to obtain engine life consumption factors. The engine life is examined according to the different material for different operating scenarios. It is observed that blade life is highly affectedby changing material properties and moreoverit is noted that the smallchange in the mass percentage of some constituent elements of an alloy results in a significant difference in HPT blade life. Keywords: Renewable Energy; Flexibility; Power Demand; Gas Turbines; Creep-LCF life; Material Properties ; Material composition ----------------------------------------------------------------------------------------------------------------------------- -
Superalloys for High Temperatures—A Primer
© 2002 ASM International. All Rights Reserved. www.asminternational.org Superalloys: A Technical Guide (#06128G) Chapter 1 Superalloys for High Temperatures—a Primer How and When to Use This Chapter in the field, check the table of contents and index for valuable insights into what you can It is always difficult to locate concise but find in each succeeding chapter. precise information on a subject. Executives and managers, particularly in industries using few superalloys, often need just basic infor- Some History mation with the least extraneous or amplify- ing data. Purchasing agents or communica- Designers have long had a need for tions experts need a modest knowledge base stronger, more corrosion-resistant materials to do their jobs more appropriately. The en- for high-temperature applications. The stain- gineer may need more detail but still just a less steels, developed and applied in the sec- quick refresher about alloy types and design ond and third decades of the 20th century, to start. The ability to lay hands on enough served as a starting point for the satisfaction practical information to solve problems or of high-temperature engineering require- answer questions about the superalloys is the ments. They soon were found to be limited basis for this book. The ability to know in their strength capabilities. The metallurgi- enough to ask questions and/or delve further cal community responded to increased needs into the superalloy field is the basis for this by making what might be termed ‘‘super-al- chapter! loys’’ of stainless varieties. Of course, it was The primer provided in this chapter sup- not long before the hyphen was dropped and ports such needs as those described previ- the improved iron-base materials became ously by providing a concise overview of the known as superalloys. -
Examination of Material Variation on the Life of Gas Turbine Backing-Up Renewable Energy Sources
IOSR Journal of Mechanical and Civil Engineering (IOSR-JMCE) e-ISSN: 2278-1684,p-ISSN: 2320-334X, Volume 16, Issue 1 Ser. IV (Jan. - Feb. 2019), PP 60-68 www.iosrjournals.org Examination of Material Variation on the Life of Gas Turbine Backing-Up Renewable Energy Sources Ezeddin Ali*, Suresh Sampath, Pericles Pilidis, Saleh Mohammed Department of Power and Propulsion, School of Aerospace, Transport and Manufacturing, Cranfield University, Cranfield, Bedfordshire, MK43 0AL, UK *Corresponding Author: Ezeddin Ali Abstract: Gas turbine life and efficiencydepend on the operating environment and material performance. Material selection is of prime importance to achieve high life and efficiency. This paper focuses on the study of the effect of material properties and variation in alloy composition ofa high- pressure turbine blade on gas turbine life when works in the flexible mode as a pick-up of renewable sources.A tool has been developed wherein different scenarios can be simulated to obtain engine life consumption factors. The engine life is examined according to the different material for different operating scenarios. It is observed that blade life is highly affectedby changing material properties and moreoverit is noted that the smallchange in the mass percentage of some constituent elements of an alloy results in a significant difference in HPT blade life. Keywords: Renewable Energy; Flexibility; Power Demand; Gas Turbines; Creep-LCF life; Material Properties ; Material composition ----------------------------------------------------------------------------------------------------------------------------- -
Materials for Gas Turbines – an Overview
13 Materials for Gas Turbines – An Overview Nageswara Rao Muktinutalapati VIT University India 1. Introduction Advancements made in the field of materials have contributed in a major way in building gas turbine engines with higher power ratings and efficiency levels. Improvements in design of the gas turbine engines over the years have importantly been due to development of materials with enhanced performance levels. Gas turbines have been widely utilized in aircraft engines as well as for land based applications importantly for power generation. Advancements in gas turbine materials have always played a prime role – higher the capability of the materials to withstand elevated temperature service, more the engine efficiency; materials with high elevated temperature strength to weight ratio help in weight reduction. A wide spectrum of high performance materials - special steels, titanium alloys and superalloys - is used for construction of gas turbines. Manufacture of these materials often involves advanced processing techniques. Other material groups like ceramics, composites and inter-metallics have been the focus of intense research and development; aim is to exploit the superior features of these materials for improving the performance of gas turbine engines. The materials developed at the first instance for gas turbine engine applications had high temperature tensile strength as the prime requirement. This requirement quickly changed as operating temperatures rose. Stress rupture life and then creep properties became important. In the subsequent years of development, low cycle fatigue (LCF) life became another important parameter. Many of the components in the aero engines are subjected to fatigue- and /or creep-loading, and the choice of material is then based on the capability of the material to withstand such loads. -
Metropolitan Vickers, the Gas Turbine, and the State: a Socio
Metropolitan Vickers, the Gas Turbine, and the State: A Socio- Technical History, 1935-1960 A thesis submitted to the University of Manchester for the degree of Doctor of Philosophy in the Faculty of Life Sciences 2012 Jakob Whitfield Contents List of Tables: .................................................................................................................................. 5 List of Figures .................................................................................................................................. 5 Abstract ........................................................................................................................................... 6 Declaration ...................................................................................................................................... 7 Copyright Statement ....................................................................................................................... 7 Acknowledgements ......................................................................................................................... 8 Acronyms, Initialisms, and Abbreviations Used ............................................................................ 10 Introduction ........................................................................................................................... 12 Metropolitan Vickers .................................................................................................................... 13 Historiography of the jet engine -
Analytical Comparative Study of Gas Turbine Blade Materials
[Rao et al., 1(1): June, 2014] ISSN: 2349-6193 IJESMR International Journal of Engineering Sciences & Management Research ANALYTICAL COMPARATIVE STUDY OF GAS TURBINE BLADE MATERIALS USED IN MARINE APPLICATIONS USING FEA TECHNIQUES V.NagaBhushana Rao*1, I.N.Niranjan Kumar2, B.Vamsi Krishna3, N.Madhulata4, M.Anudeep5 *1 Department of Marine Engineering, Andhra University College of Engineering, INDIA 2 Department of Marine Engineering, Andhra University College of Engineering, INDIA 3Department of Mechanical Engineering, Raghu Institute of Technology, Visakhapatnam, INDIA 4Department of Marine Engineering, PRIME Engineering College, Visakhapatnam, INDIA 5Department of Mechanical Engineering, Raghu Institute of Technology, Visakhapatnam, INDIA *Correspondence Author: [email protected] Keywords: Gas turbine blade, Materials, Modeling. Structural Analysis, Thermal Analysis. ABSTRACT The turbine blades are responsible for extracting energy from the high temperature gas produced by the combustor. Operating the gas turbine blade at high temperatures would provide better efficiency and maximum work output. These turbine blades are required to withstand large centrifugal forces, elevated temperatures and are operated in aggressive environments. To survive in this difficult environment, turbine blades often made from exotic materials. A key limiting factor in gas turbine engines is the performance of the materials available for the hot section of the engine especially the gas turbine blades. In this paper, three materials such as Nimonic alloy, Super alloy and titanium aluminium have been considered for the purpose of performance analysis. The turbine blade under evaluation belongs to the first stage rotor blade of a two -stage gas turbine. The turbine blade data was obtained using CMM and its 3D solid model is created by using CATIA V5R21software. -
Superalloys, the Most Successful Alloy System of Modern Times-Past, Present, and Future
SUPERALLOYS, THE MOST SUCCESSFUL ALLOY SYSTEM OF MODERN TIMES - PAST, PRESENT AND FUTURE Art Kracke Vice President Business Technology ATI Allvac Abstract The deep roots of superalloys go back to 1907, although the term ‘super-alloy’ is believed to have first been used in the mid 1940s to refer to cobalt-base alloys such as Vitallium and nickel- base Waspaloy®. During the past 50 years, much alloy, hot working, heat treating and process development has occurred, enabling many of the end use technologies we know today. This presentation will discuss some of the history of the superalloy industry related to the superalloys 718, Waspaloy and their derivatives, including ATI 718Plus® alloy. The presentation will then describe the wide range of manufacturing techniques used for the production of superalloys, available product forms and end-use applications. Concluding the presentation will be a discussion on what advancements we are likely to see in the future. Introduction Superalloys are successful today because they have solved pressing demands for durability and strength in machines and systems that were barely imaginable a hundred years ago. Superalloys have helped us conquer air and space, plumb the depths of the earth and ocean, and address many other challenges of modern life. As such, they deserve to have their story told. The nature of this industry, however, makes the telling a challenging task. Its history is one of many small events and inventions that took place across the boundaries of nations, industries and countries. Many individuals contributed to the state of the art today, and only a few left their names in the scattered records. -
The Development of the Whittle Turbojet
THE AMERICAN SOCIETY OF MECHANICAL ENGINEERS 345 E. 47th St., New York, N.Y.10017 97-GT-528 The Society shall not be response* for statements or opinions advancedin papers or clitussion at meetings of the Society or of its Divisions or Sections, or printed In its publications. Discussion is printed only if the paper is published in an ASME Journal. Authorization to photocopy material for Internal or personal use under circumstance not falling within the fair use. provisions of the Copyright Act is granted by ASME to libraries and other users registered with the Copyright Clearance Center (CCC) Transacticcal Reporting Senrice provided that the base fee of $0.30 • per page is paid direcby to the CCC, 27 Congress Street Salem MA 01970. Requests for special pemlission or bulk reproduction shadd be addressed to the ASME Teetotal Pubistting Department Copyright 0 1997 by ASME All Rights Reserved Printed in U.S.A Downloaded from http://asmedigitalcollection.asme.org/GT/proceedings-pdf/GT1997/78682/V001T01A012/2408878/v001t01a012-97-gt-528.pdf by guest on 23 September 2021 , 111 11111111,11 1)111111111 THE DEVELOPMENT OF THE WHITTLE TURBOJET Cyrus B. Meher-Homji Bechtel Corporation Houston, Texas. ABSTRACT The history of jet propulsion starts with the inventions of Hero of Alexandria (circa AD 60) who developed the first Sir Frank Whittle passed away on August 8, 1996 at the age of reaction type turbine. In 1791 John Barber invented a Watt type 89, in Maryland. His work in developing the turbojet can truly beam engine driven by a primitive gas turbine via reduction be said to represent one of the greatest mechanical engineering gearing. -
Oxidation Behavior of Two Nickel-Base Superalloys Used As Elevated Temperature Valves in Spark Ignited Engines and Diesel Exhaust Recirculation (Egr) Applications
Superalloys 2004 Edited by K.A. Green, T.M. Pollock, H. Harada, T.E. Howson, R.C. Reed, J.J. Schirra, and S, Walston TMS (The Minerals, Metals & Materials Society), 2004 OXIDATION BEHAVIOR OF TWO NICKEL-BASE SUPERALLOYS USED AS ELEVATED TEMPERATURE VALVES IN SPARK IGNITED ENGINES AND DIESEL EXHAUST RECIRCULATION (EGR) APPLICATIONS S. Sinharoy and S. L. Narasimhan Eaton Corporation - Engine Air Management Operations; 19218 B Drive South; Marshall, MI 49068, USA Keywords: Isothermal oxidation, Oxide formation kinetics, Internal combustion engine Abstract stoichiometric fuel-air combustion and EGR for emission reduction and by the use of turbo-boosting systems in land and air With trends towards higher performance, fuel economy and vehicles powered by ICEs. In this article, oxidation behavior of natural resource conservation, alternative fuels being considered two nickel-base superalloys, Nimonic 90TM* and Pyromet 751TM** by the automotive industry pose special demands on internal (similar to Inconel 751TM*), at 870 oC and 930 oC are presented combustion engine (ICE) exhaust valve materials. Similar and discussed. Inconel 751 is a commonly used nickel-base demands are expected in exhaust gas recirculation (EGR) systems exhaust valve superalloy used in both gasoline and diesel ICEs, for gasoline ICEs and now being introduced in heavy-duty diesel while Nimonic 90 has been primarily limited to heavy-duty diesel engines. With application of high temperature combustion fuels applications for higher fatigue strength. This study was such as propane and hydrogen, one of the key requirements of an undertaken to evaluate an appropriate alloy to meet the challenges exhaust valve material – oxidation resistance, is discussed in this of high temperature oxidation resistance demands of alternate fuel study for two nickel-base superalloys.