High-Strain-Rate Superplasticity Materials And
Total Page:16
File Type:pdf, Size:1020Kb
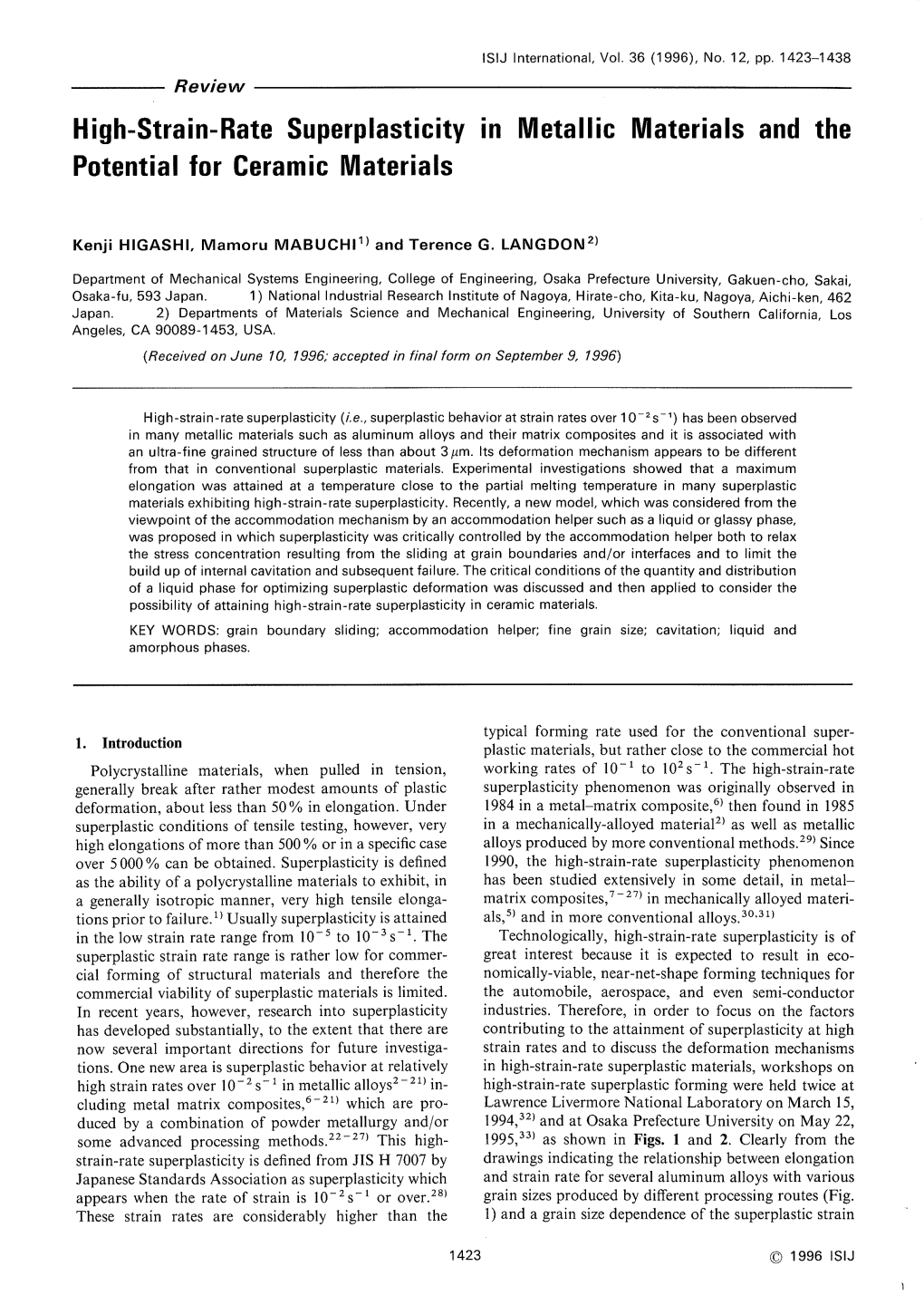
Load more
Recommended publications
-
MECHANICAL PROPERTIES of SUPERPLASTIC Al-Zn ALLOYS
MECHANICAL PROPERTIES OF SUPERPLASTIC Al-Zn ALLOYS TEAR THE TRANSITION REGION A THESIS Presented to The Faculty of the Division of Graduate Studies and Research By S. A. Hamid Ghazanfar In Dartial Fulfillment of the Requirements for the Degree Master of Science in Mechanical Engineering Georgia Institute of Technology December, 1973 MECHANICAL PROPERTIES OF SUPERPLASTIC Al-Zn ALLOYS NEAR THE TRANSITION REGION Approved: E. E. Unde rwo o d ,"' Chairman David Ka11sh E. A. Starke Date approved, by Chairman: £®' I dedicate this thesis to my loving father, who has always encouraged me in my efforts to obtain a fine education and bravely endured my absence from his side. ACKNOWLEDGMENTS The author gratefully acknowledges the advice and encouragement he received from Professor Ervin E. Underwood, especially the motivation he provided in moments of stress and anxiety. Special thanks must go to Mr. Tilden Eugene Clopton for technical advice and help in experimental set ups. Mr. A. C. Josey and Mr. George Halstead kindly allowed the author to use the machine shop. The Ball Corporation of Muncie, Indiana, was most generous in providing the Al-Zn eutectoid alloy for the research. The author also appreciates the careful and efficient typing of his thesis by Mrs. Sharon Butler. iii TABLE OF CONTENTS Page ACKNOWLEDGMENTS ii LIST OF TABLES . iv LIST OF ILLUSTRATIONS V LIST OF SYMBOLS vii SUMMARY ix Chapter I. INTRODUCTION 1 II. BACKGROUND 3 III. EXPERIMENTAL PROCEDURES 2 2 A. Material B. Mechanical Testing C. Metallography IV. EXPERIMENTAL RESULTS 31 A. Load-Elongation Curves B. True Stress-True Strain Rate Data C. -
HIGH STRAIN RATE SUPERPLASTICITY in a CONTINUOUSLY RECRYSTALLIZED Al±6%Mg±0.3%Sc ALLOY
Acta mater. Vol. 46, No. 8, pp. 2789±2800, 1998 # 1998 Acta Metallurgica Inc. Published by Elsevier Science Ltd. All rights reserved Printed in Great Britain PII: S1359-6454(97)00452-7 1359-6454/98 $19.00 + 0.00 HIGH STRAIN RATE SUPERPLASTICITY IN A CONTINUOUSLY RECRYSTALLIZED Al±6%Mg±0.3%Sc ALLOY T. G. NIEH1, L. M. HSIUNG1, J. WADSWORTH1 and R. KAIBYSHEV2 1Lawrence Livermore National Laboratory, L-369, P.O. Box 808, Livermore, CA 94551, U.S.A. and 2Institute of Metals Superplasticity Problems, Khalturina St. 39, Ufa, Bashkortostan, 450000, Russia (Received 26 September 1997; accepted 10 November 1997) AbstractÐThe superplastic properties of a cold-rolled Al±6Mg±0.3Sc alloy were studied at temperatures between 450 and 5608C and strain rates between 104 and 100 s1. The alloy was observed to exhibit super- plasticity over wide temperature (475±5208C) and strain rate ranges (0103±101 s1). It was found that the addition of Sc to Al±Mg alloys resulted in a uniform distribution of ®ne coherent Al3Sc precipitates which eectively pinned subgrain and grain boundaries during static and dynamic recrystallization. In this paper, the microstructural evolution during superplastic deformation was systematically examined using both opti- cal and transmission electron microscopy. Based upon this microstructural examination, a mechanism is proposed to explain the observed high strain rate superplasticity in the alloy. A model is also proposed that describes grain boundary sliding accommodated by dislocations gliding across grains containing coher- ent precipitates. # 1998 Acta Metallurgica Inc. 1. INTRODUCTION theory, two competing processes, GBS and dislo- There is now a great interest in developing highly- cation slip, can control deformation, as illustrated formable Al alloys, and in particular Al±Mg based in Fig. -
Superplastic Behavior of Friction Stir Processed ZK60 Magnesium Alloy
Materials Transactions, Vol. 52, No. 12 (2011) pp. 2278 to 2281 #2011 The Japan Institute of Metals RAPID PUBLICATION Superplastic Behavior of Friction Stir Processed ZK60 Magnesium Alloy G. M. Xie1;*, Z. A. Luo1,Z.Y.Ma2, P. Xue2 and G. D. Wang1 1State Key Laboratory of Rolling and Automation, Northeastern University, Shenyang 110819, P. R. China 2Shenyang National Laboratory for Materials Science, Institute of Metal Research, Chinese Academy of Sciences, Shenyang 110016, P. R. China Six millimeter thick extruded ZK60 magnesium alloy plate was subjected to friction stir processing (FSP) at 400 rpm and 100 mm/min, producing fine and uniform recrystallized grains with predominant high-angle grain boundaries of 73%. Maximum elongation of 1800% was achieved at a relatively high temperature of 325C and strain rate of 1 Â 10À3 sÀ1. Grain boundary sliding was identified to be the primary deformation mechanism in the FSP ZK60 alloy by superplastic data analyses and surface morphology observation. The superplastic deformation kinetics of the FSP ZK60 alloy was faster than that of the high-ratio differential speed rolled ZK60 alloy. [doi:10.2320/matertrans.M2011231] (Received July 28, 2011; Accepted September 27, 2011; Published November 16, 2011) Keywords: friction stir processing (FSP), magnesium, microstructure, superplasticity 1. Introduction superplastic deformation dominated by grain boundary sliding (GBS). ZK60 alloy is one of commercial magnesium alloys that At the present time, the investigation on the FSP aluminum exhibit sound mechanical -
Superplastic Deformation Mechanisms in Fine-Grained 2050 Al-Cu-Li Alloys
materials Article Superplastic Deformation Mechanisms in Fine-Grained 2050 Al-Cu-Li Alloys Hongping Li 1,2, Xiaodong Liu 1, Quan Sun 1, Lingying Ye 1,3,* and Xinming Zhang 1,3 1 School of Materials Science and Engineering, Central South University, Changsha 410083, China; [email protected] (H.L.); [email protected] (X.L.); [email protected] (Q.S.); [email protected] (X.Z.) 2 Shanghai Aircraft Design and Research Institute of COMAC, Shanghai 200232, China 3 Key Laboratory of Nonferrous Materials, Ministry of Education, Central South University, Changsha 410083, China * Correspondence: [email protected] Received: 18 May 2020; Accepted: 11 June 2020; Published: 14 June 2020 Abstract: The deformation behavior and microstructural evolution of fine-grained 2050 alloys at elevated temperatures and slow strain rates were investigated. The results showed that significant dynamic anisotropic grain growth occurred at the primary stage of deformation. Insignificant dislocation activity, particle-free zones, and the complete progress of grain neighbor switching based on diffusion creep were observed during superplastic deformation. Quantitative calculation showed that diffusion creep was the dominant mechanism in the superplastic deformation process, and that grain boundary sliding was involved as a coordination mechanism. Surface studies indicated that the diffusional transport of materials was accomplished mostly through the grain boundary, and that the effect of the bulk diffusion was not significant. Keywords: Al-Cu-Li alloys; superplasticity; creep diffusion; grain boundary sliding; focused ion beams 1. Introduction Al-Li alloy has a wide applicability in the field of aerospace because of its relatively low density, high elastic modulus, high specific strength, and excellent comprehensive properties [1–3]. -
Investigation of Structural-Phase States and Features of Plastic Deformation of the Austenitic Precipitation-Hardening Co-Ni-Nb Alloy
Article Investigation of Structural-Phase States and Features of Plastic Deformation of the Austenitic Precipitation-Hardening Co-Ni-Nb Alloy Aidyn Tussupzhanov 1,2,3,*, Dosym Yerbolatuly 1, Ludmila I. Kveglis 1,3 and Aleksander Filarowski 2,4,5 ID 1 S. Amanzholov East Kazakhstan State University, Department of Physics and Technology, 30 Gvardeiskoi Divisii Str. 34, 070020 Ust-Kamenogorsk, Kazakhstan; [email protected] (D.Y.); [email protected] (L.I.K.) 2 Faculty of Chemistry, Wroclaw University, F. Joliot-Curie Str. 14, 50-383 Wroclaw, Poland; aleksander.fi[email protected] 3 Polytechnical Institute of Siberian Federal University, Svobodny Ave 79, 660041 Krasnoyarsk, Russia 4 Frank Laboratory of Neutron Physics, JINR, 141-980 Dubna, Russia 5 Department of Physics, Industrial University of Tyumen, 625-000 Tyumen, Russia * Correspondence: [email protected]; Tel.: +7-777-4775878 Received: 6 November 2017; Accepted: 23 December 2017; Published: 30 December 2017 Abstract: This article presents the results of investigation of the influence of holding temperature during the quenching process on the microstructure and superplasticity of the Co-Ni-Nb alloy. Temperature-strain rate intervals of the deformation of the superplasticity effects are stated. The optimal regimes of the preliminary treatment by quenching and rolling as well as the routine of the superplastic deformation of the Co-Ni-Nb alloy are defined. The interval of the temperatures of the precipitation, morphology, composition, type and parameters of the lattice of the secondary phase, which appears after the annealing + rolling (to 90%) Co-Ni-Nb alloy, are determined. Keywords: superplasticity; superplastic deformation; Co-Ni-Nb alloy; microstructure; precipitation; secondary phase; shear transformation zone 1. -
Superplasticity in an Organic Crystal
ARTICLE DOI: 10.1038/s41467-018-06431-7 OPEN Superplasticity in an organic crystal Satoshi Takamizawa 1, Yuichi Takasaki1,2, Toshiyuki Sasaki 1 & Noriaki Ozaki1 Superplasticity, which enables processing on hard-to-work solids, has been recognized only in metallic solids. While metallic materials and plastics (polymer solids) essentially possess high plastic workability, functional crystalline solids present difficulties in molding. Organic crystals especially are fragile, in the common view, and they are far from the stage of materials development. From the viewpoint of practical application; however, organic crystals 1234567890():,; are especially attractive because they are composed of ubiquitous elements and often exhibit higher performance than metallic materials. Thus, finding superplastic deformation of organic crystals, especially in a single-crystal-to-single-crystal manner, will pave the way for their material applications. This study confirmed superplasticity in a crystal of a simple organic compound: N,N-dimethyl-4-nitroaniline. The crystal exhibits single-crystal-to-single-crystal superplastic deformation without heating. This finding of “organosuperplasticity” will con- tribute to the future design of functional solids that do not lose their crystalline quality in molding. 1 Department of Materials System Science, Graduate School of Nanobioscience, Yokohama City University, 22-2 Seto, Kanazawa-ku, Yokohama, Kanagawa 236-0027, Japan. 2 Kanagawa Institute of Industrial Science and Technology, 705-1 Shimoimaizumi, Ebina, Kanagawa 243-0435, Japan. Correspondence and requests for materials should be addressed to S.T. (email: [email protected]) NATURE COMMUNICATIONS | (2018) 9:3984 | DOI: 10.1038/s41467-018-06431-7 | www.nature.com/naturecommunications 1 ARTICLE NATURE COMMUNICATIONS | DOI: 10.1038/s41467-018-06431-7 olids deform by loading force. -
Superplasticity in Ultrafine-Grained Materials
4R6ev. Adv. Mater. Sci. 54 (2018) 46-55 M. Kawasakiand T.G. Langdon SUPERPLASTICITY IN ULTRAFINE-GRAINED MATERIALS Megumi Kawasaki1 and Terence G. Langdon2 1School of Mechanical, Industrial and Manufacturing Engineering, Oregon State University, Corvallis, OR 97331-6001, U.S.A. 2Materials Research Group, Department of Mechanical Engineering, University of Southampton, Southampton SO17 1BJ, U.K. Received: June 18, 2018 Abstract. Superplasticity refers to the ability of a polycrystalline solid to exhibit a high elongation, of at least 400% or more, when testing in tension. The basic characteristics of superplastic flow are now understood and a theoretical model is available to describe the flow process both in conventional superplastic materials where the grain sizes are a few micrometers and in ultrafine- grained materials processed by severe plastic deformation where the grain sizes are in the submicrometer range. This report describes the basic characteristics of superplastic metals, gives examples of flow in ultrafine-grained materials, demonstrates the use of deformation mechanism mapping for providing a visual display of the flow processes and provides a direct comparison with the conventional model for superplastic flow. The report also describes the potential for using nanoindentation to obtain detailed information on the flow properties using only exceptionally small samples. 1. INTRODUCTION by Underwood [3], drew world-wide attention to the unusual properties of superplastic materials. A few When polycrystalline solids are pulled in tension, years later it became clear that superplastic alloys they generally exhibit necking and then they fail at provided a potential for forming smooth and com- relatively low elongations. Under some special cir- plex shapes from sheet metals [4] and this was the cumstances, however, it is possible to achieve re- significant step that initiated the process of markably high elongations without the occurrence superplastic forming as a viable manufacturing tool. -
On the Common Origin of Structural Superplasticity in Different Classes of Materials
ORenv t.h Aed cv.o Mmamteorn. Socriig. i5n4 o (f2 s0t1ru8c) t1u-r1a3l superplasticity in different classes of materials 1 ON THE COMMON ORIGIN OF STRUCTURAL SUPERPLASTICITY IN DIFFERENT CLASSES OF MATERIALS K.A. Padmanabhan1 and M. Raviathul Basariya2 1Research and Innovation Advisory Board, Tata Consultancy Services (TCS) & Research Advisor, TCS & Aditya Birla S&T Company, IIT-Madras Research Park, Taramani, Chennai 600013, India 2Independent Researcher; formerly of IIT-BHU, Varanasi and Anna University, Chennai, India Received: April 23, 2018 Abstract. The present model starts with an assumption that grain/ interphase boundary sliding (GBS) that is dominant during optimal superplastic flow is slower than the accommodation processes of dislocation emission from sliding boundaries, highly localized diffusion in the boundary regions and/ or grain rotation that are present as a concomitant of the GBS process. When boundary sliding develops to a mesoscopic scale (of the order of a grain diameter or more), by the alignment of contiguous boundaries, plane interface formation/ mesoscopic boundary sliding is observed. Significant and simultaneous sliding along different plane interfaces and their interconnection can lead to large scale deformation and superplasticity. The accommodation steps, being faster than GBS, do not enter the strain rate equation. Mathematical development of these ideas using transition state theory results in a transcendental strain rate equation for steady state optimal superplastic flow, which when solved numerically helps one to describe the phenomenon quantitatively in terms of two constants, the activation energy for the rate controlling process, F0 and the threshold stress needed to be overcome for the commencement of mesoscopic boundary sliding, 0.The analysis also explains quantitatively texture randomization as a function of superplastic strain. -
Towards a Theory of Superplasticity
Towards a theory of superplasticity Egorushkin V.a, Ponomarev A.a,b a Institute of Strength Physics and Materials Science of SB RAS, 2/4 Akademichesky Av., Tomsk 634055, Russia b National Research Tomsk Polytechnic University, 30 Lenin Avenue, 634050 Tomsk, Russia E-mail: [email protected] Abstract This work deals with an investigation of general principles of superplasticity (SP) in deformed materials. It is shown that a non-linear, wave plastic deformation is the basic process for all plastic deformation phenomena; it makes an individual contribution into these phenomena, allows describing them from the same standpoints, and offers a way to follow the relationship between the physics of defects and the mechanics of plasticity. It is to be noted that macro and meso defects – discontinuities in the vector fields of macro and meso elastic displacements, are no less fundamental than are the microdefects – dislocations and disclinations; it is the latter which form the process of localized macrodeformation. General mechanisms of this process are analyzed in this study. Relying on the concepts of non-equilibrium thermodynamics, a constitutive equation of superplastic state is obtained, which relates the strain rate, its rotational modes, local irreversible stresses, temperature, and density of heat and mass transfer. Special cases and their derived relations are analyzed. It is shown that SP is determined by plastic equilibrium concurrent with the composition and structure fluctuations. An expression is obtained for the superplastic flow velocity, containing three terms: velocity of wave plastic macroprocess, increased by fluctuations, velocity prescribed by the gradient of external sources (diffusion, etc.), and velocity of the delayed intragranular slip. -
On the Mechanisms of Superplasticity in Ti-6Al-4V
Acta Materialia 105 (2016) 449e463 Contents lists available at ScienceDirect Acta Materialia journal homepage: www.elsevier.com/locate/actamat Full length article On the mechanisms of superplasticity in Tie6Ale4V * E. Alabort a, P. Kontis b, D. Barba a, K. Dragnevski a, R.C. Reed a, a Department of Engineering Science, University of Oxford, Parks Road, Oxford, OX1 3PJ, United Kingdom b Department of Materials, University of Oxford, Parks Road, Oxford, OX1 3PH, United Kingdom article info abstract Article history: Surface observations are used to elucidate the deformation mechanisms responsible for the superplastic Received 28 September 2015 effect in Tie6Ale4V. High-temperature in-situ tests for tensile and shear deformation modes are per- + Received in revised form formed in the scanning electron microscope at temperatures in excess of 700 C. Grain boundary sliding 1 December 2015 is predominant; the micro-mechanics of accommodation are consistent with the dislocation-based Accepted 2 December 2015 Rachinger theory. The volume fraction of b plays a crucial role. For temperatures greater than 850 C, Available online xxx the a grains remain unaffected; cavitation is minimal and slip bands needed for dislocation-based ac- commodation are detected in the b phase but are absent in a. At this temperature, grain neighbour Keywords: + Superplasticity switching is observed directly under shear deformation. At a temperature lower than 850 C, the b Titanium alloys volume fraction is lower and a different mechanism is observed: slip bands in a and cavitation are found Grain boundary sliding to accommodate grain boundary sliding. In addition, an increase in the a phase intragranular dislocation In-situ activity triggers the formation of subgrains and dynamic recrystallisation, consistent with the Rachinger + Scanning electron microscopy dislocation creep effect. -
A Review on Superplastic Forming of Ti-6Al-4V Alloy
JournalMaterials of Science Alloys andand Technology Compounds AA Review Review on on Superplastic Superplastic Forming Forming of of Ti-6Al-4V Ti-6Al-4V Alloy Alloy --Manuscript Draft-- Manuscript Number: MST16321 Full Title: A Review on Superplastic Forming of Ti-6Al-4V Alloy Article Type: Review Keywords: Superplastic forming; Superplasticity; Ti-6Al-4V; Microstructure; Multi step forming dies Corresponding Author: Sai Pratyush Akula, B.E. Mechanical Engineering Birla Institute of Technology and Science Hyderbad, Telangana INDIA Corresponding Author Secondary Information: Corresponding Author's Institution: Birla Institute of Technology and Science Corresponding Author's Secondary Institution: First Author: SaiAkhil Pratyush Agnihotri Akula First Author Secondary Information: Order of Authors: SaiAkhil Pratyush Agnihotri Akula AkhilSai Akula Agnihotri Pratyush AmitAmit Kumar Gupta Order of Authors Secondary Information: Abstract: This paper presents a review on the superplastic forming of Ti-6Al-4V alloy, which has been used to manufacture parts of complex shapes and geometries. This paper outlines the major work carried out on this front in the past three decades. It covers various aspects related to experimental setups, including the manufacture of dies and their modifications to maintain alloy thickness uniformity after forming. A detailed study of the process parameters has also been done to note the most important physical conditions required for successful forming. This is followed by the influence of microstructure, modern applications of superplastic forming of different titanium alloys and is concluded with an insight into the future work and progress in this field. Additional Information: Question Response Please state the novelty of your 1. Elaborates on the latest advancements in the field of SPF of Ti-6Al-4V submission by providing (at least) four 2. -
A High-Strain-Rate Superplasticity of the Al-Mg-Si-Zr-Sc Alloy with Ni Addition
materials Article A High-Strain-Rate Superplasticity of the Al-Mg-Si-Zr-Sc Alloy with Ni Addition Andrey Mochugovskiy, Anton Kotov , Majid Esmaeili Ghayoumabadi, Olga Yakovtseva and Anastasia Mikhaylovskaya * Department of Physical Metallurgy of Non-Ferrous Metals, National University of Sciences and Technology “MISIS”, 4 Leninskiy ave. 4, 119049 Moscow, Russia; [email protected] (A.M.); [email protected] (A.K.); [email protected] (M.E.G.); [email protected] (O.Y.) * Correspondence: [email protected]; Tel.: +7-(495)-6384480 Abstract: The current study analyzed the effect of Ni content on the microstructure and superplastic deformation behavior of the Al-Mg-Si-Cu-based alloy doped with small additions of Sc and Zr. The superplasticity was observed in the studied alloys due to a bimodal particle size distribution. The coarse particles of eutectic origin Al3Ni and Mg2Si phases with a total volume fraction of 4.0–8.0% and a mean size of 1.4–1.6 µm provided the particles with a stimulated nucleation effect. The L12– structured nanoscale dispersoids of Sc- and Zr-bearing phase inhibited recrystallization and grain growth due to a strong Zener pinning effect. The positive effect of Ni on the superplasticity was revealed and confirmed by a high-temperature tensile test in a wide strain rate and temperature limits. In the alloy with 4 wt.% Ni, the elongation-to-failure of 350–520% was observed at 460 ◦C, in a strain rate range of 2 × 10−3–5 × 10−2 s−1. Keywords: superplasticity; aluminum alloys; transition metals; dispersoids; particle-stimulated nucleation Citation: Mochugovskiy, A.; Kotov, A.; Esmaeili Ghayoumabadi, M.; Yakovtseva, O.; Mikhaylovskaya, A.