Soldering in Magnesium High Pressure Die Casting and Its Prevention by Surface Engineering
Total Page:16
File Type:pdf, Size:1020Kb
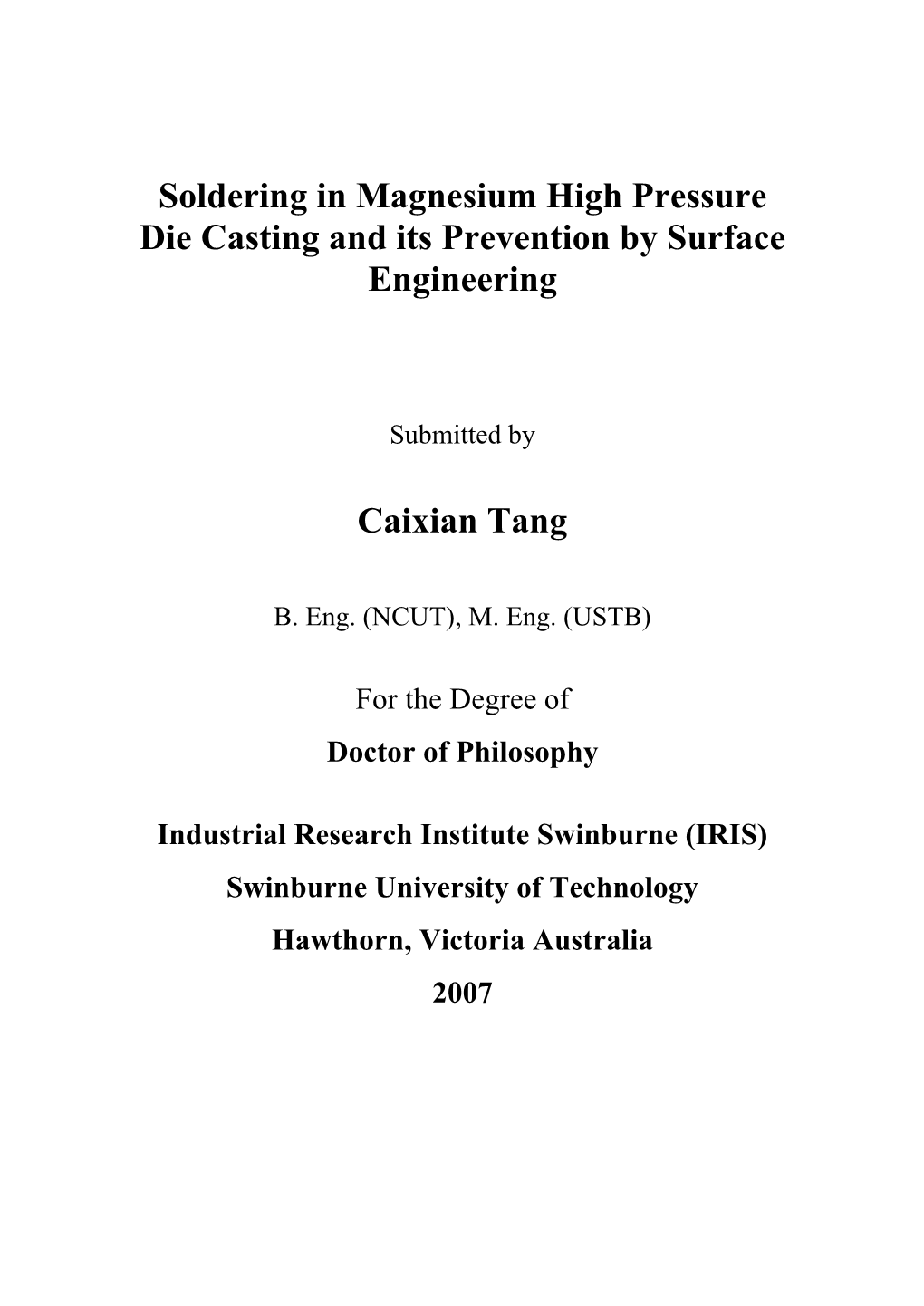
Load more
Recommended publications
-
Treatise on Combined Metalworking Techniques: Forged Elements and Chased Raised Shapes Bonnie Gallagher
Rochester Institute of Technology RIT Scholar Works Theses Thesis/Dissertation Collections 1972 Treatise on combined metalworking techniques: forged elements and chased raised shapes Bonnie Gallagher Follow this and additional works at: http://scholarworks.rit.edu/theses Recommended Citation Gallagher, Bonnie, "Treatise on combined metalworking techniques: forged elements and chased raised shapes" (1972). Thesis. Rochester Institute of Technology. Accessed from This Thesis is brought to you for free and open access by the Thesis/Dissertation Collections at RIT Scholar Works. It has been accepted for inclusion in Theses by an authorized administrator of RIT Scholar Works. For more information, please contact [email protected]. TREATISE ON COMBINED METALWORKING TECHNIQUES i FORGED ELEMENTS AND CHASED RAISED SHAPES TREATISE ON. COMBINED METALWORKING TECHNIQUES t FORGED ELEMENTS AND CHASED RAISED SHAPES BONNIE JEANNE GALLAGHER CANDIDATE FOR THE MASTER OF FINE ARTS IN THE COLLEGE OF FINE AND APPLIED ARTS OF THE ROCHESTER INSTITUTE OF TECHNOLOGY AUGUST ( 1972 ADVISOR: HANS CHRISTENSEN t " ^ <bV DEDICATION FORM MUST GIVE FORTH THE SPIRIT FORM IS THE MANNER IN WHICH THE SPIRIT IS EXPRESSED ELIEL SAARINAN IN MEMORY OF MY FATHER, WHO LONGED FOR HIS CHILDREN TO HAVE THE OPPORTUNITY TO HAVE THE EDUCATION HE NEVER HAD THE FORTUNE TO OBTAIN. vi PREFACE Although the processes of raising, forging, and chasing of metal have been covered in most technical books, to date there is no major source which deals with the functional and aesthetic requirements -
Galvalume Facts
GALVALUME FACTS Soldering Although GALVALUME® steel sheet can be soldered, the presence of a thin film of aluminum oxide on the surface makes soldering more difficult than when soldering galvanized products. When soldering is necessary, the techniques and fluxes used to solder aluminum should be used. Welding GALVALUME® steel sheet can be welded by conventional resistance and arc welding processes. The safety precautions are similar to those for hot-dip galvanized sheet. Because the surface contact resistance is low when compared with uncoated sheet, resistance welding of GALVALUME® steel sheet requires welding currents, welding times and electrode forces higher than those required for similar thicknesses of uncoated cold rolled steel. These welding parameters are similar to those normally used on galvanized steel. However, experience has shown that even more frequent electrode dressing is required, as compared with galvanized sheet, to achieve good welds. There is less fuming when welding GALVALUME® steel sheet than when welding galvanized sheet. The coating contains less zinc than a comparably thick galvanized coating. Nevertheless, adequate ventilation is required to remove the zinc oxide fumes. Fastening From a mechanical standpoint, any style of fastener suitable for use with sheet metal can be used to join GALVALUME® steel sheet to itself or to other parts, provided the fastener design is appropriate for the structural requirement of the application. The list of acceptable devices includes common fasteners like nuts and bolts, screws and rivets of all types, and special types like clamp fasteners, clips and blind screws. Corrosion characteristics of the fastener material should be carefully considered from two standpoints. -
Procedure 4.0—Hot Work Program (Hwp)
Hamilton College Occupational Health and Safety Procedures PROCEDURE 4.0—HOT WORK PROGRAM (HWP) 4.1 INTRODUCTION Purpose Regulations promulgated by the Occupational Safety and Health Administration (OSHA—29 CFR 1910.252— Welding, Cutting and Brazing) and the NYS Fire Code (Code Chapter 26—Hot Work) require facilities to develop procedures to protect both human health and welfare, and the facility itself, from the hazards posed by hot work in the workplace. This program is intended to provide the Hamilton College community with the guidance necessary to comply with these regulations. Scope Hamilton College is committed to providing a safe and healthful work environment for its students, employees and the greater college community. The following Hot Work Program (HWP) has been developed to eliminate or minimize risks to personnel, students, and campus facilities. While the greatest hot work risks arise from spark/slag producing activity (welding, cutting, brazing), other forms of hot work (pipe soldering, pipe thawing, etc.) may also present risks in the form of radiant heat and/or open flame. As such, certain elements of this program will pertain to all types of hot work activity, and others will only address the more dangerous activities that produce sparks. This HWP includes: • Identification of Responsibilities • Prohibited Hot Work Areas/Activities • Welding/Cutting/Brazing Authorization Process • Hot Work Permits • Special Considerations for Soldering/Other Hot Work Activities • Fire Watch • Contractors Applicability The Director of Environmental Protection, Safety & Sustainability (EPS&S) will maintain and update the College’s written Hot Work Program, and will work primarily with other relevant parties (the Physical Plant and certain academic departments) for training and compliance purposes. -
Photochemical Machining
Design Guide to Photochemical Machining A World Apart in a World of Parts This “Design Guide to Photochemical Machining” was cre- ated for those involved with the designing or purchasing of Fotofab uses a special process called Photochemical Machining. Also known as chemical etching, acid etching, or milling, this process metal parts. While it provides general guidelines, Fotofab’s offers many advantages over traditional metal fabrication methods: Technical Sales Staff is available to assist Speed you with your specifi c requirements. • Tooling can be produced rapidly. • Parts can be produced and shipped within hours of receiving a print. By designing with an awareness of our process capabilities, you will minimize Flexibility • Many intricate part geometries, like those found in fi ne resolution the cost and delivery time of your metal screens, can be photochemically machined easily and economically. parts. We are ready to work with you, • Revisions to part designs are implemented quickly and inexpensively. • Brittle metals, which often fracture during conventional stamping, are machined without diffi culty. Just tell us what you need! Repeatability • Prototype and production quantities can be made using the same process and tooling. Contents • Extremely thin metal can be machined without distortion; dimensional accuracy actually increases as metal thickness decreases. The Fotofab Process • page 4 • Physical properties of the metal, such as hardness, strength and formability, are not changed by the process. Value-Added Services • page 7 • Magnetically soft materials can be fabricated while retaining their optimum permeability. Applications • page 8 • Parts are inherently free of burrs. Material Selection • page 10 Cost Effectiveness • Tooling and set-up costs are extremely low compared to hard tooling. -
Roofinox Soldering
Roofinox Soldering Soldering is the creation of a durable but detachable joining of two metals by melting a filling metal into a joint. This soft soldering process requires temperatures below 842°F, the typical soldering temperature for stainless steel tin-sol- der is around 480°F. Due to its specific surface Roofinox® stainless steel is readily solderable. The surfaces to be joined must be free of grease, dirt or other foreign matter. Stainless steel requires some adaptations such as a different flux than for copper and zinc. With the use of proper flux, techniques and tools Roofinox is easily solderable and provides durable water- proofing joints. By observing the following points, you will achieve an outstanding soldering quality. For durable and clean soldering joints the following tools are required: • Soldering iron with soldering bit • Solder (30 %, 40 %, 50 % solder possible) • Soldering stone / ammoniac stone (pure ammoniac, no tinned ammoniac stone) • Flux - Roofinox FLM • Flux brush • Cleaning tissue • Fresh water Flux For Roofinox and Roofinox tin-plated fluxes based on phosphoric acid are suitable. Not suitable are fluxes based on hydro- chloric acid or dilute hydrochloric acid or containing chloride ions. The industry offers a range of soldering fluxes suitable for stainless steel. Best results are achieved with Roofinox FLM. Roofinox FLM guarantees sufficient removal of the thin passive layer and prevents its renewed formation during soldering. They provide optimal wetting and cleanliness of the soldering area. If the soldered joint will be subjected to particular stress, please contact us. Conducting a solder test is recommended before beginning the job to ensure that the desired result will be achieved. -
Current State of Semi-Solid Net-Shape Die Casting
Review Current State of Semi-Solid Net-Shape Die Casting Plato Kapranos Department of Materials Science & Engineering, The University of Sheffield, Sir Robert Hadfield Building, Mappin Street, Sheffield S1 3J, UK; [email protected]; Tel.: +44(0)1142225509 Received: 7 November 2019; Accepted: 25 November 2019; Published: 2 December 2019 Abstract: Semi-solid processing of alloys is nearing the end of its fifth decade in existence. This promising manufacturing route has undergone a number of changes over the past five decades and apart from certain successful industrial applications, it appeared that it had become a niche technology with limited applications, notably in the automotive and consumer product markets. Nevertheless, despite the strong competition of traditional casting and in particular die-casting processes, and the emergence of Additive Manufacturing (AM), there seems to be a resurgence in demand for Net-Shape Die Casting of Semi-solid alloys as testified by the high numbers of delegates at the 14th SSM Conference at Shenzhen, China in September 2018. What follows is a brief review of the historical development of the process as well as more recent developments with an eye to future prospects. Keywords: SSM Die-casting (SSMDC); SSM feedstock; SSM applications; thixoforming; non- dendritic microstructures; industrial applications of SSMDC 1. Introduction Semi-solid metal processing (SSP) covers all the manufacturing routes involving materials processed in their semi-solid state. These technologies are known for taking advantage of the thixotropic behavior of metal alloys (discovered by Spencer et al. [1]) to permit a liquid-like slurry filling of a die/mold resulting in improved properties of the final products. -
HYDRON-UNIPRESS, Ltd
HYDRON-UNIPRESS, Ltd. Manufacturer of the equipment for the tin/lead industry ul. Wólczańska 257, 93-035 Łódź, Poland fax:+4842-684 75 06, tel.: +4842-640 25 46 [email protected] www.hydrononline.com REMARK : Hydron-Unipress, Ltd., of Lódz , Poland, is a corporation organized and existing under the laws of Poland. All information presented in this paper should be considered as an offer for further discussion and negotiation between all concerned parties on the principle of equality and mutual benefit. The technical data given in this offer may undergo modification as a result of technical improvements. Hydron-Unipress, Ltd. (fax +4842-847-506, tel. +4842-402-546(7))_________________________________Production Program OFFER'S SCOPE If your desire is to start your own manufacturing program in the field of solder making business the HYDRON-UNIPRESS Ltd. is happy to offer you : COMPLETE TECHNOLOGICAL LINE for manufacturing of FLUX CORED and SOLID SOLDER BARS, ANODES and WIRES starting from the process of solder alloy preparation and with an annual output of 200ton, 400ton or more HiTech, specialized, INDIVIDUAL EQUIPMENT for manufacturing of FLUX CORED and SOLID FINE and ULTRAFINE SOLDER WIRES from 0.118"/3.0mm down to 0.002"/0.05mm in diameter for electronic, microelectronic, electromechanic, automotive and lighting industries, non-toxic, LEAD-FREE SOLDERS for drink water piping soldering, LEAD PROFILES for stained-glass windows and Tiffany art, ANODES and BARS for galvanic bath and wave soldering, and many others applications Participation in JOINT VENTURES for solder making business Any other form of COOPERATION desired being of the mutual interest. -
Improving the Performance of Magnesium Alloys for Automotive Applications
High Performance and Optimum Design of Structures and Materials 531 Improving the performance of magnesium alloys for automotive applications R. O. Hussein & D. O. Northwood Department of Mechanical, Automotive and Materials Engineering, University of Windsor, Canada Abstract Magnesium and its alloys are attractive to the automotive industry for their inherent light-weight which leads to highly fuel-efficient design. However, due to a low melting temperature (650°C), magnesium has relatively poor elevated temperature mechanical properties, e.g., creep. This has, therefore, restricted its use in applications such as engine components. Magnesium is also a highly reactive metal and has inherently poor corrosion and wear resistance. Improved corrosion and wear performance can be obtained through alloying and microstructural engineering. However, for enhanced corrosion and tribological properties, the use of surface engineering techniques involving coatings is mandatory. Plasma Electrolytic Oxidation (PEO), also known as “Micro-Arc Oxidation (MAO)”, has been used to successfully produce oxide layers on magnesium alloys with excellent tribological and corrosion resistant properties. By controlling the PEO process parameters, uniform, relatively pore-free and well adhered coatings can be produced which can provide adequate corrosion protection. The coating requirements for good tribological properties are somewhat different than for good corrosion performance. However, good tribological performance combined with good corrosion performance can -
Machining Magnesium – Datasheet
DATASHEET DATASHEET • Machining Magnesium 254 † Magnesium is the lightest structural metal and Table 1. Relative power and comparative machinability of metals. exhibits excellent machinability. Some of the AISI - B1112 Relative advantages of machining magnesium compared to Metal machinability power other commonly used metals include: index (%) Magnesium alloys 1.0 500 • Low power required – approximately 55% of that Aluminium alloys 1.8 300 required for Al Mild steel 6.3 50 • Fast machining – employing the use of high cutting speeds, large feed rates and greater depths of cut Titanium alloys 7.6 20 • Excellent surface finish – extremely fine and smooth surface achieved Speeds, feeds and depths of cut • Well broken chips – due to the free-cutting qualities of magnesium The potential for high speed machining of • Reduced tool wear – leading to increased tool life magnesium alloys is usually only limited by the stability of the component in the clamping device, To fully exploit and enjoy the advantages of chip extraction or the rotation speed or accuracy machining magnesium, it is important that the unique limits of the tool or machine. Some relative cutting characteristics of the metal are understood. speeds using HSS tools are given in Table 2. Cutting speeds are also dependant on the tool material. Cutting power and machinabilty Higher speeds can be enjoyed with the use of carbide or poly-crystalline diamond (PCD) tooling. The mean specific cutting force (ks1.1) of magnesium is 280 N/mm2, this is much lower than that of In general, cutting speeds are between aluminium (approx 640 N/mm2). The result of this 200 – 1800 m/min with feed rates greater than means that there is a reduced load on the cutter and 0.25 mm/rev for turning and boring operations. -
Soldering Guidelines for Land Grid Array Packages Application Note 61
Soldering Guidelines for Land Grid Array Packages Application Note 61 Summary The objective of this application note is to provide Peregrine Semiconductor customers with general guidelines for the soldering and assembly of land grid array (LGA) packages. Precise process development and designed experimentation are needed to optimize specific appli- cation/performance. Introduction LGAs are grid array packages with terminal pads on the bottom surface. These are leadless packages with electrical connections made via lands on the bottom side of the component to the surface of the connecting substrate (PCB, ceramic, LTCC, etc.). The LGA is typically made with organic laminate or PC board as substrate with nickel-gold (NiAu)-plated termina- tions. Other component termination plating or substrate might be used based on application. The LGA solder interconnect is formed solely by solder paste applied at board assembly because there are no spheres attached to the LGA. This results in a lower standoff height of approximately 0.06 mm to 0.10 mm, which is favored for portable product applications. The lower standoff height also allows more space above the package for heatsink solution or for thin form factor application. LGA eliminates the risk that customers receive packages with damaged or missing solder spheres due to shipping and handling. Reflow soldering of LGA assemblies provides mechanical, thermal and electrical connections between the component leads or terminations and the substrate surface mount land pattern. Solder paste may be applied to the surface mount lands by various methods, such as screen printing and stencil printing. Peregrine Semiconductor LGA packages are categorized as surface mount components (SMCs). -
ACHIEVING ULTRAFINE GRAINS in Mg AZ31B-O ALLOY by CRYOGENIC FRICTION STIR PROCESSING and MACHINING
University of Kentucky UKnowledge Theses and Dissertations--Manufacturing Systems Engineering Manufacturing Systems Engineering 2011 ACHIEVING ULTRAFINE GRAINS IN Mg AZ31B-O ALLOY BY CRYOGENIC FRICTION STIR PROCESSING AND MACHINING Anwaruddin Mohammed University of Kentucky, [email protected] Right click to open a feedback form in a new tab to let us know how this document benefits ou.y Recommended Citation Mohammed, Anwaruddin, "ACHIEVING ULTRAFINE GRAINS IN Mg AZ31B-O ALLOY BY CRYOGENIC FRICTION STIR PROCESSING AND MACHINING" (2011). Theses and Dissertations--Manufacturing Systems Engineering. 1. https://uknowledge.uky.edu/ms_etds/1 This Master's Thesis is brought to you for free and open access by the Manufacturing Systems Engineering at UKnowledge. It has been accepted for inclusion in Theses and Dissertations--Manufacturing Systems Engineering by an authorized administrator of UKnowledge. For more information, please contact [email protected]. STUDENT AGREEMENT: I represent that my thesis or dissertation and abstract are my original work. Proper attribution has been given to all outside sources. I understand that I am solely responsible for obtaining any needed copyright permissions. I have obtained and attached hereto needed written permission statements(s) from the owner(s) of each third-party copyrighted matter to be included in my work, allowing electronic distribution (if such use is not permitted by the fair use doctrine). I hereby grant to The University of Kentucky and its agents the non-exclusive license to archive and make accessible my work in whole or in part in all forms of media, now or hereafter known. I agree that the document mentioned above may be made available immediately for worldwide access unless a preapproved embargo applies. -
Annual Report of Solikamsk Magnesim Works 2014 the Main Part
Annual Report of Solikamsk Magnesim Works 2014 The main part ANDREI B. KUDLAI ADOPTED BY: Annual General Assembly of Shareholders Of JSC Solikamsk Magnesium Works Protocol № 1 of « 09 » June 2015 Provisionally Approved by: The Board of Directors Of JSC Solikamsk Magnesium Works Protocol № 5 of «05» May 2015 JOINT-STOCK COMPANY “SOLIKAMSK MAGNESIUM WORKS” ANNUAL REPORT 2014 General Director ________________ Sergei B. Shalaev (signature) Solikamsk 2015 1 Page TABLE OF CONTENT LETTER TO SHAREHOLDERS 3 MISSION OF THE COMPANY 4 GENERAL COMPANY’S INFORMATION 5 History in Brief 5 Solikamsk Magnesium Works in Brief 6 Registration Data 7 Auditor of the Company 7 Register-keeper of the Company 7 Authorized Capital of the Company 8 Shareholders of the Company 8 Market Capitalization of the Company 8 Subsidiaries (Dependent Entities) of the Company 9 SMW’s Membership in Organizations & Associations 10 PRIORITY ACTIVITIES OF THE COMPANY 10 REPORT OF THE BOARD CONCERNING PROGRESS IN THE COMPANY’S PRIORITY ACTIVITIES 10 Financial Overview 10 Performance by Operations 14 Magnesium Operations 14 Rare Metals Operations 16 Niobium Compounds 17 Tantalum Compounds 18 Compounds of Rare Earths 19 Titanium Sponge & Compounds 20 Chemical Operations 21 Usage of Raw Materials & Energy Resources 22 Technical Development & IT-Technologies 22 Compliance of Management System with International Requirements 23 Compliance with International Code of Conduct for the Industry 23 Integrated Management System of the Company & Due Diligence on Trade with “Conflict Minerals”