1 In-Situ Characterization of Li-Ion Battery Electrodes Using Atomic
Total Page:16
File Type:pdf, Size:1020Kb
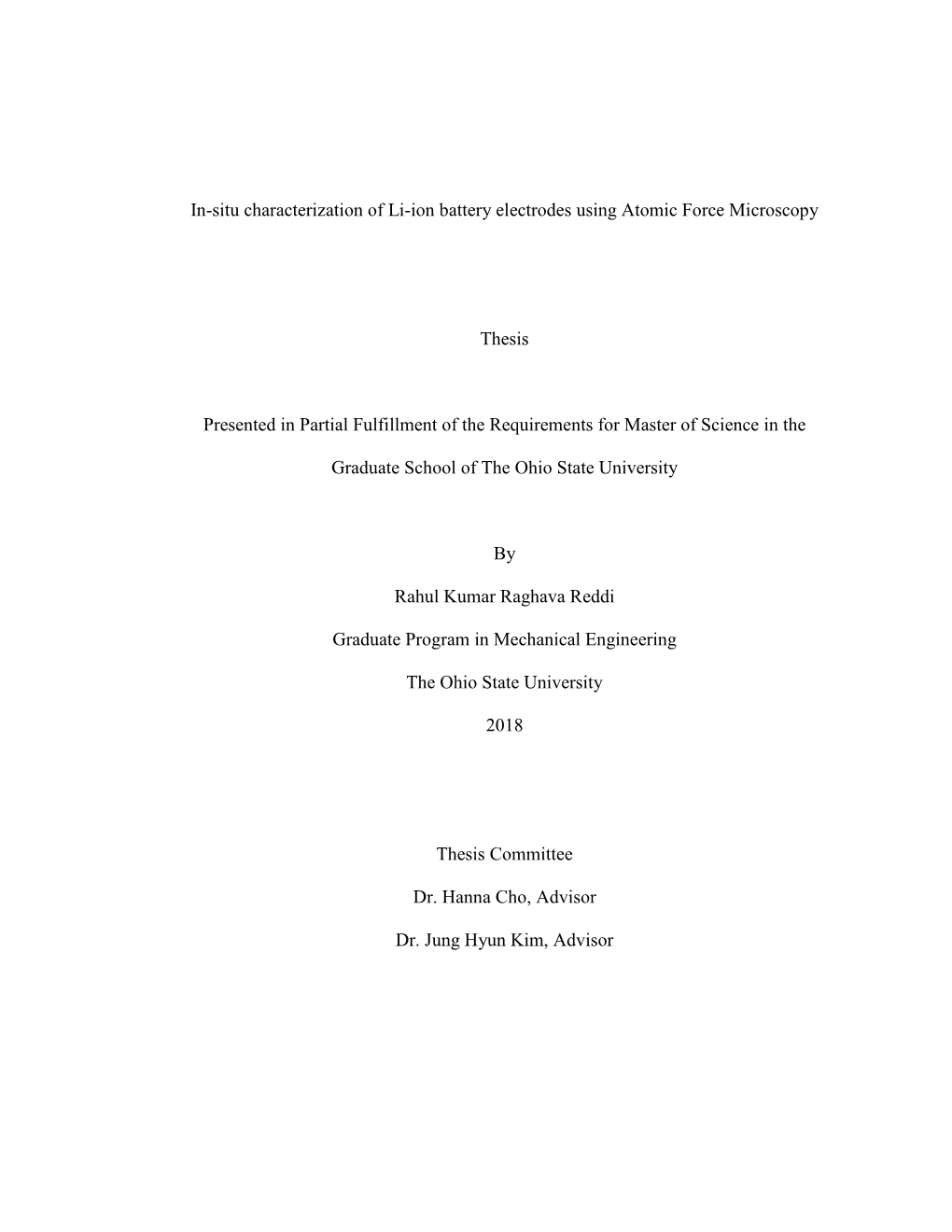
Load more
Recommended publications
-
Printed Textile-Based Ag2o–Zn Battery for Body Conformal Wearable Sensors
sensors Communication Printed Textile-Based Ag2O–Zn Battery for Body Conformal Wearable Sensors Akash Kota * , Ashish Gogia, Amy T. Neidhard-Doll and Vamsy P. Chodavarapu Department of Electrical and Computer Engineering, University of Dayton, Dayton, OH 45469, USA; [email protected] (A.G.); [email protected] (A.T.N.-D.); [email protected] (V.P.C.) * Correspondence: [email protected] Abstract: Wearable electronics are playing an important role in the health care industry. Wearable sensors are either directly attached to the body surface or embedded into worn garments. Textile- based batteries can help towards development of body conformal wearable sensors. In this letter, we demonstrate a 2D planar textile-based primary Ag2O–Zn battery fabricated using the stencil printing method. A synthetic polyester woven fabric is used as the textile substrate and polyethylene oxide material is used as the separator. The demonstrated battery achieves an areal capacity of 0.6 mAh/cm2 with an active electrode area of 0.5 cm × 1 cm. Keywords: sensor power; textile battery; stencil printing; zinc-silver oxide; battery characteristics 1. Introduction The rapid development of wearable devices is fueled by the interest from the general population for real-time health and wellness monitoring [1,2]. Various human health and Citation: Kota, A.; Gogia, A.; wellness indicators including body temperature, peripheral capillary oxygen saturation Neidhard-Doll, A.T.; Chodavarapu, (SpO2) level, electrocardiogram, calories burned, exercise outcomes, and walking steps V.P. Printed Textile-Based Ag2O–Zn can be monitored non-invasively in real time by wearable devices. Wearable devices also Battery for Body Conformal Wearable play an important role in the development of smart bandages for wound healing applica- Sensors. -
Next Generation Anodes for Lithium-Ion Batteries First Quarter Progress Eport 2019
NEXT GENE ATION ANODES Next Generation Anodes for Lithium-Ion Batteries First Quarter Progress eport 2019 Jack Vaughey, Point-of-Contact Argonne National Laboratory 9700 South Cass Avenue Argonne, IL 60439 Phone: (630) 252-8885 E-mail: [email protected] Brian Cunningham, DOE-EE E-VTO Technology Manager U.S. Department of Energy, Battery &D Phone: (202) 287-5686 E-mail: [email protected] Table of Contents Page Overview 2 Milestone FY19Q1 5 Baseline Silicon Materials 7 Composite Silicon / Graphite Electrodes Variable Temperature Performance of Silicon-Gr Composite Electrodes (ANL) 8 Silicon-containing Anodes with Extended Cycle Life and Calendar Life (PNNL) 10 Impact of Processing Conditions on Uniformity of Silicon-Gr Composite Electrodes (O NL) 13 The ole of Dispersants on Binder Selection for Silicon-Gr Composite Electrodes (O NL) 17 Composite Silicon-Sn Anodes for Lithium-Ion Batteries (LBNL) 20 High Silicon Content Electrodes Carbon-coated Silicon for Improved Electrochemical Performance in Full Cells (ANL) 23 Carbon-Coated Silicon Materials (LBNL) 26 High Silicon Content electrodes: CAMP Prototyping (ANL) 27 Cell Balancing with High Silicon Content Electrodes (ANL) 29 Silicon Surface Functionalization (ANL) 32 Lithium Inventory (ANL) 35 1 | P a g e NEXT GENE ATION ANODES Silicon Deep Dive Overview Project Introduction Silicon has received significant attention as an alternative to the graphitic carbon negative electrodes presently used in a lithium-ion battery due to its high capacity and availability. Compared to graphitic carbons, elemental silicon has nearly an order of magnitude higher capacity (~3600 mAh/g silicon vs 372 mAh/g Graphite), however, several problems have been identified that limit its utility including a large crystallographic expansion (~320%) upon full lithiation, slow lithium diffusion, and high reactivity at high states of charge. -
Influence of the Binder on Lithium Ion Battery Electrode Tortuosity and Performance
Journal of The Electrochemical Society OPEN ACCESS Influence of the Binder on Lithium Ion Battery Electrode Tortuosity and Performance To cite this article: Johannes Landesfeind et al 2018 J. Electrochem. Soc. 165 A1122 View the article online for updates and enhancements. This content was downloaded from IP address 129.187.254.46 on 20/01/2020 at 10:44 A1122 Journal of The Electrochemical Society, 165 (5) A1122-A1128 (2018) Influence of the Binder on Lithium Ion Battery Electrode Tortuosity and Performance Johannes Landesfeind, ∗,z Askin Eldiven, and Hubert A. Gasteiger∗∗ Chair of Technical Electrochemistry, Department of Chemistry and Catalysis Research Center, Technical University of Munich, Munich, Germany The electrochemical performance of porous graphite anodes in lithium ion battery applications is limited by the lithium ion concentration gradients in the liquid electrolyte, especially at high current densities and for thick coatings during battery charging. Beside the electrolyte transport parameters, the porosity and the tortuosity of the coating are key parameters that determine the electrode’s suitability for high power applications. Here, we investigate the tortuosity of graphite anodes using two water as well as three n-methyl-2-pyrrolidone based binder systems by analysis of symmetric cell impedance measurements, demonstrating that tortuosities ranging from ∼3–10 are obtained for graphite anodes of similar thickness (∼100 μm), porosities (∼50%) and areal capacity (∼3.4 mAh/cm2). Furthermore, selected electrodes with tortuosities of 3.1, 4.3, and 10.2 were cycled in cells with reference electrode at charging C-rates from 0.1-20 1/h, illustrating the clear correlation between electrode tortuosity and its rate capability. -
The Processing of Binder Jet Multi-Material 3D Printing to Improve Upon Material Properties
Clemson University TigerPrints All Theses Theses December 2019 The Processing of Binder Jet Multi-Material 3D Printing to Improve upon Material Properties Sara Mohammed Damas Clemson University, [email protected] Follow this and additional works at: https://tigerprints.clemson.edu/all_theses Recommended Citation Damas, Sara Mohammed, "The Processing of Binder Jet Multi-Material 3D Printing to Improve upon Material Properties" (2019). All Theses. 3224. https://tigerprints.clemson.edu/all_theses/3224 This Thesis is brought to you for free and open access by the Theses at TigerPrints. It has been accepted for inclusion in All Theses by an authorized administrator of TigerPrints. For more information, please contact [email protected]. THE PROCESSING OF BINDER JET MULTI-MATERIAL 3D PRINTING TO IMPROVE UPON MATERIAL PROPERTIES A Thesis Presented to the Graduate School of Clemson University In Partial Fulfillment of the Requirements for the Degree Master of Science Mechanical Engineering by Sara M. Damas December 2019 Accepted by: Dr. Cameron J. Turner, Committee Chair Dr. Gang Li Dr. Suyi Li ABSTRACT Additive manufacturing methods are becoming more prominent in the world of design and manufacturing due to their reduction of material waste versus traditional machining methods such as milling. As their demand rises, a need to improve their methodologies and produce higher quality products arises. The technology to 3D print has been in around since the 1970’s, and thanks to Scott Crump as of 1989, it is possible to 3D print in layers to obtain a solid component. In today’s present time, we now can multi- material 3D print. However, even though we have the technology for multi-material 3D printing, standards in this field are severely lacking. -
High Performance Materials for Batteries Solvay Introduction
High Performance Materials for Batteries Solvay Introduction Electrical and electronic devices as well as eco-friendly Likewise, substituting traditional vehicles with transportation have all become integral to our daily lives. environmental-friendly electric vehicles will continue to These conveniences keep us connected both to each increase as batteries become reliable. Innovative materials other and to the world around us, allowing us to work and technologies are expected to increase durability up to more efficiently while travelling safer as we reduce the 15 %, thereby adding 1 year or more to their lifetime. overall impact on the environment. The dynamic Li-Ion batteries technology roadmap brings A key factor that can either spread or limit their lot of challenges that can only be met thanks to a smart development is what’s “under the hood”: Li-Ion batteries. fit between new processing technologies and innovative materials. The power and duration of Li-Ion batteries dually determine the efficiency and reliability of smartphones, Solvay’s high-performance solutions are helping to tablets, laptops as well as other electronic devices. New address the challenges of Today and Tomorrow in a materials and technologies that extend battery life while variety of different ways: shortening charging time are in great demand. Solef® PVDF Solef® PVDF Coating Binder Solef® PVDF Binder LiTFSI Main salt or additive for electrolyte F1EC, F2EC, TAB Additives for electrolyte 2 \ High Performance Materials for Batteries Technology Roadmap 2010 2015 2020 -
Nasa Tm X-68036 a Versatile Silver Oxide-Zinc Battery
NASA TECHNICAL NASA TM X-68036 MEMORANDUM A VERSATILE SILVER OXIDE-ZINC BATTERY FOR SYNCHRONOUS ORBIT AND PLANATARY MISSIONS by Harvey J. Schwartz and Daniel G. Soltis Lewis Research Center Cleveland, Ohio t TECHNICAL PAPER proposed for presentation at Eighth International Electrical Power Sources Symposium c sponsored by the Joint Services Electrical Power Sources Corn mission Brighton, England, September 26-28, 1972 A VERSATILE SILVER OXIDE-ZINC BATTERY FOR SYNCHRONOUS ORBIT AND PLANETARY MISSONS by Harvey J. Schwartz and Daniel G. Soltis 4.- Lewis Research Center National Aeranautics and Space Administration Cleveland, Ohio, U.S.A. ABSTRACT w A new Kind of silver-zinc cell has been developed and tested under . ri (D NASA support which can withstand severe heat sterilization requirements and OD W I w does not display the traditional life limiting aspect of sinc electrodes i.e. shape change. These cells could be used on planetary lander mission which require wet-stand periods of over a year, a modest number of cycles ( 400 to 500) and may require dry heat sterilization. The weight advantage of these cells over the traditional nickel-cadmium batteries also makes it an attrac- tive alternative for synchronous orbit service where 400 to 500 cycles would be required over a 5 year period. INTRODUCTION In order to launch larger, more sophisticated, and more useful satellites and space probes, it is becoming increasingly important to make significant weight reductions in spacecraft systems to avoid overtaxing the lifting capability of available boosters. One primary candidate for weight savings is the spacecraft battery. In this respect, the silver oxide-zinc system has long been recognized as an attractive, but hitherto unsuccessful, alternative to the nickel oxide-cadmium battery. -
The Investigation of Organic Binder Effect on Morphological Structure Of
S S symmetry Article The Investigation of Organic Binder Effect on Morphological Structure of Ceramic Membrane Support Mohamed Boussemghoune 1,2, Mustapha Chikhi 1, Yasin Ozay 2, Pelin Guler 3, Bahar Ozbey Unal 4 and Nadir Dizge 2,* 1 Department of Environfmental Engineering, Salah Boubnider Constantine 3 University, Constantine 25000, Algeria; [email protected] (M.B.); [email protected] (M.C.) 2 Department of Environmental Engineering, Mersin University, Mersin 33343, Turkey; [email protected] 3 Department of Nanotechnology and Advanced Materials, Mersin University, Mersin 33343, Turkey; [email protected] 4 Department of Environmental Engineering, Gebze Technical University, Kocaeli 41440, Turkey; [email protected] * Correspondence: [email protected] Received: 24 March 2020; Accepted: 1 May 2020; Published: 6 May 2020 Abstract: In this study, we investigated the effect of different organic binders on the morphologic structure of ceramic membrane support. Natural raw clay material (kaolin) was used as the main mineral for ceramic membrane support. The physical and chemical properties of kaolin powder and the supports were identified by X-ray fluorescence (XRF), X-ray diffraction (XRD), Fourier-transform infrared spectroscopy (FTIR), Brunauer–Emmett–Teller (BET), thermo gravimetric analysis (TGA), scanning electron microscopy (SEM), particle size and zeta potential distribution. Based on the XRF test, the main composition of kaolin powder was SiO2 (47.41%) and Al2O3 (38.91%), while the rest were impurities. The FTIR spectra showed the functional groups of Si-O and Al-O. The XRD diffractogram of natural raw clay powder identified kaolinite and nacrite were the main mineral phase whereas muscovite and quartz were detected in small quantities in the sample. -
Development of an Alternative Binder for Lithium Ion Batteries Based on Epoxy Resin F
Development of an alternative binder for lithium ion batteries based on epoxy resin F. Bunzel*, M. Wagner*, E. Stammen* and K. Dilger* *Technische Universität Braunschweig, Institute of Joining and Welding, Braunschweig, Germany, [email protected] ABSTRACT volume expansion of the electrode material from which macroscopic shear forces result by which the contact of the The development of batteries for the e-mobility particle in the active material between them, the contact continuously creates new challenges for the researchers. To between active material and binder and further the contact improve the performance of lithium ion batteries, different of the binder with the substrate deterioates and thus the approaches might be considered. Therefore the Institute of electron conductivity strongly decreases [1-2]. Joining and Welding (ifs) focuses its research on the To raise the life cycle of a lithium ion battery, the development of alternative binders for active materials. degradation mechanisms described above must be Hence, different reactive adhesive systems were prevented. One way of doing this is to substitute the characterized on the basis of acrylates, epoxy resins and generally used binder. However, this binder must show silicones with different curing mechanisms and were several requirements. On the one hand the binder in a examined for the use as a binder. However, epoxy resins in lithium ion battery must provide the mechanical stability of particular showed a good performance. On account of the the electrode, on the other hand it must guarantee the possibility of being able to adjust the properties of epoxy bonding of the particles of electrochemically active resins to a certain extent, this system was investigated in components to each other as well as to the current collector. -
Next-Generation Anodes for Li-Ion Batteries: Fundamental Studies Of
NEXT GENERATION ANODES FOR LI-ION BATTERIES FUNDAMENTAL STUDIES OF SI-C MODEL SYSTEMS drhgfdjhngngfmhgmghmghjmghfmf ROBERT KOSTECKI 2016 U.S. DOE HYDROGEN and FUEL CELLS PROGRAM and VEHICLE TECHNOLOGIES OFFICE ANNUAL MERIT REVIEW AND PEER EVALUATION MEETING Project ID:ES262 This presentation does not contain any proprietary, confidential, or otherwise restricted information Next Generation Anodes for Li-ion Batteries Fundamental Studies of Si-C Model Systems • This presentation describes coordinated research task within the five National Laboratory consortium to develop practical Si-based Li-ion negative electrode. (Ref. ES261) • The primary objective of this effort is to provide basic understanding and effective mitigation of key R&D barriers to implementation of silicon-based anodes. • The technical approach involves fundamental diagnostic studies of basic properties of the Si anode active and passive components in model systems. Timeline Budget . Start: October 1, 2015 FY16 Total Funding: $4000K – Kickoff: January, 2016 . End: September 30, 2018 2 The Silicon-Carbon Composite Electrode Jones at al., Experimental Mechanics, 2014, 54, 971 • Si/C composite electrode is a complex multicomponent electrochemical systems that incorporate widely dissimilar phases in physical, electrical and ionic contact. • Basic properties of constituent phases determine the behavior of the composite electrode and the entire Li-ion battery system. 3 3 The Silicon-Carbon Composite Electrode Credit: Yi Cui, Stanford University • Si/C composite electrode is a complex multicomponent electrochemical systems that incorporate widely dissimilar phases in physical, electrical and ionic contact. • Basic properties of constituent phases determine the behavior of the composite electrode and the entire Li-ion battery system. 4 4 The Silicon-Carbon Composite Electrode Abarbanel et al., J. -
Pelletization of Catalysts Supported on Activated Carbon
A. F. Orrego-Romero et al.; Revista Facultad de Ingeniería, No. 78, pp. 38-47, 2016 Revista Facultad de Ingeniería, Universidad de Antioquia, No. 78, pp. 38-47, 2016 Pelletization of catalysts supported on activated carbon. A Case Study: clean synthesis of dimethyl carbonate from methanol and CO2 Preparación de catalizadores de carbón activado estructurados. Un caso de estudio: síntesis limpia de dimetil carbonato a partir de metanol y CO2 Andrés Felipe Orrego-Romero, Oscar Felipe Arbeláez-Pérez, Felipe Bustamante-Londoño*, Aída Luz Villa Holguín Grupo de Investigación Catálisis Ambiental, Departamento de Ingeniería Química, Facultad de Ingeniería, Universidad de Antioquia. Calle 70 # 52-21. A. A. 1226. Medellín, Colombia. ARTICLE INFO ABSTRACT: The synthesis of Cu-Ni bimetallic catalyst supported on pellets of activated Received May 18, 2015 carbon using carboxymethylcellulose (CMC) as a binder is reported. The effect of preparation Accepted October 28, 2015 conditions, such as binder concentration, AC/binder ratio, temperature, and pyrolysis heating rate on the surface area of the pellets, was evaluated. Cu and Ni metals were incorporated on the pellets by conventional incipient wetness impregnation. The support and the synthesized catalysts were characterized using N2 adsorption, H2-TPR, XRD and SEM-EDS techniques. The pelletized catalysts were evaluated for the direct synthesis of dimethyl carbonate DMC (case study). An improved catalytic activity (e.g., ca. 20% increase in conversion) in structured KEYWORDS pelletized catalyst in comparison to the powdered catalyst was found. Dimethyl carbonate, pellets, activated carbon, CO2, Cu-Ni catalysts RESUMEN: Se presenta la síntesis del catalizador bimetálico de Cu-Ni soportado en pellets de carbón activado utilizando carboximetilcelulosa (CMC) como agente aglutinante. -
Battery Technology Comparison IEEE 2020
Industrial Battery Comparison Safety Precautions MSDS Sheets identify chemical hazards Use double insulated tools No smoking or open flames Avoid arcing near the battery Wear personal protective equipment Avoid wearing metal objects Ensure battery area ventilation is operable Neutralize static buildup 2 Saft proprietary information – Confidential SAFT, now proud part of the TOTAL Group* SAFT DEVELOPS AND MANUFACTURES ADVANCED-TECHNOLOGY BATTERY SOLUTIONS FOR MULTIPLE APPLICATIONS ON A GLOBAL SCALE . Diversified base of industries 35% 32% North . Broad portfolio of technologies Europe (Ni-based, Primary Lithium and Lithium-ion) America 33% Asia, MEA, . Leadership positions on 75-80% of Latam revenue base (Industrial Standby, Metering, Aviation, Rail, Defense, Satellites) * SAFT is part of TOTAL new division, “Gas, Renewables & Power”, since September 1st, 2016 100 $921M* 9.7% +4,100 +3,000 years of history revenue FY 2017 invested in R&D people customers 3 *Using an exchange rate of 1.24 Saft proprietary information – Confidential Leading Oil & Gas companies rely on Saft International & National Oil and Gas Companies 4 Saft proprietary information – Confidential 1 Battery Basics 2 Battery History 3 Chemistries and Construction 4 Battery Comparison 5 Choosing the Right Technology 5 Saft proprietary information – Confidential BATTERY BASICS 6 Saft proprietary information – Confidential Battery Composition A battery is an electrochemical energy storage device. Energy Storage Active Material Electrolyte = + 7 Saft proprietary information – Confidential Stationary Battery Cell Components Substrate Bones of the battery. Physical structure inside the battery that houses the active materials. (May or may not be made of the same material as the active material) Active Material The muscles of the battery. -
BAO TONG USA INC. Dba TYSONIC BATTERY 1032 EAST MAIN ST., ALHAMBAR, CA 91801 626-289-5962(PH) 626-576-2503(FAX)
BAO TONG USA INC. dba TYSONIC BATTERY 1032 EAST MAIN ST., ALHAMBAR, CA 91801 626-289-5962(PH) 626-576-2503(FAX) Specification of GNC160 NI-CD BATTERY PACK FOR LACMTA TRAINS 1.0 Battery Type GNC160 NI-CD BATTERY PACK The battery shall be constituted of open (vented), low maintenance sintered / pbe nickel-cadmium cells, and shall comply with IEC 60623, fourth edition, 2001-09. The cells shall be connected in series or parallel into crates / trays. 2.0 Plates The positive plate shall be of the sintered type obtained by sintering a paste of nickel powder, mixed with deionized water, onto a thin perforated nickel-plated strip followed by chemical impregnation of nickel hydroxide onto a porous nickel structure. The negative plate shall be of the plastic bonded type obtained by a coating of slurry consisting of cadmium oxide mixed with a plastic binder onto a thin perforated nickel-plated strip. Graphite shall not be used in the plates. All nickel-plated steel plate tabs shall be seam welded onto the plates to ensure high current transfer and maximum strength. The cell plate groups shall be bolted to the positive and negative terminal posts accordingly. 3.0 Electrolyte: The electrolyte shall be an aqueous solution of potassium hydroxide (KOH) containing additives; the density of electrolyte is 1.25g/cm3. 4.0 Separators: Type: PPAT. The cell separator shall be a multi-layer type consisting of a micro-porous polymer and non-woven felt to provide an optimum balance between performance, reliability and long life, and to also act as a barrier between the + / - plates to prevent the oxygen generated by the positive plate from reaching the negative plate.