Citylink Tulla Widening - Existing Bulla Road Bridge North Abutment Modification Dr
Total Page:16
File Type:pdf, Size:1020Kb
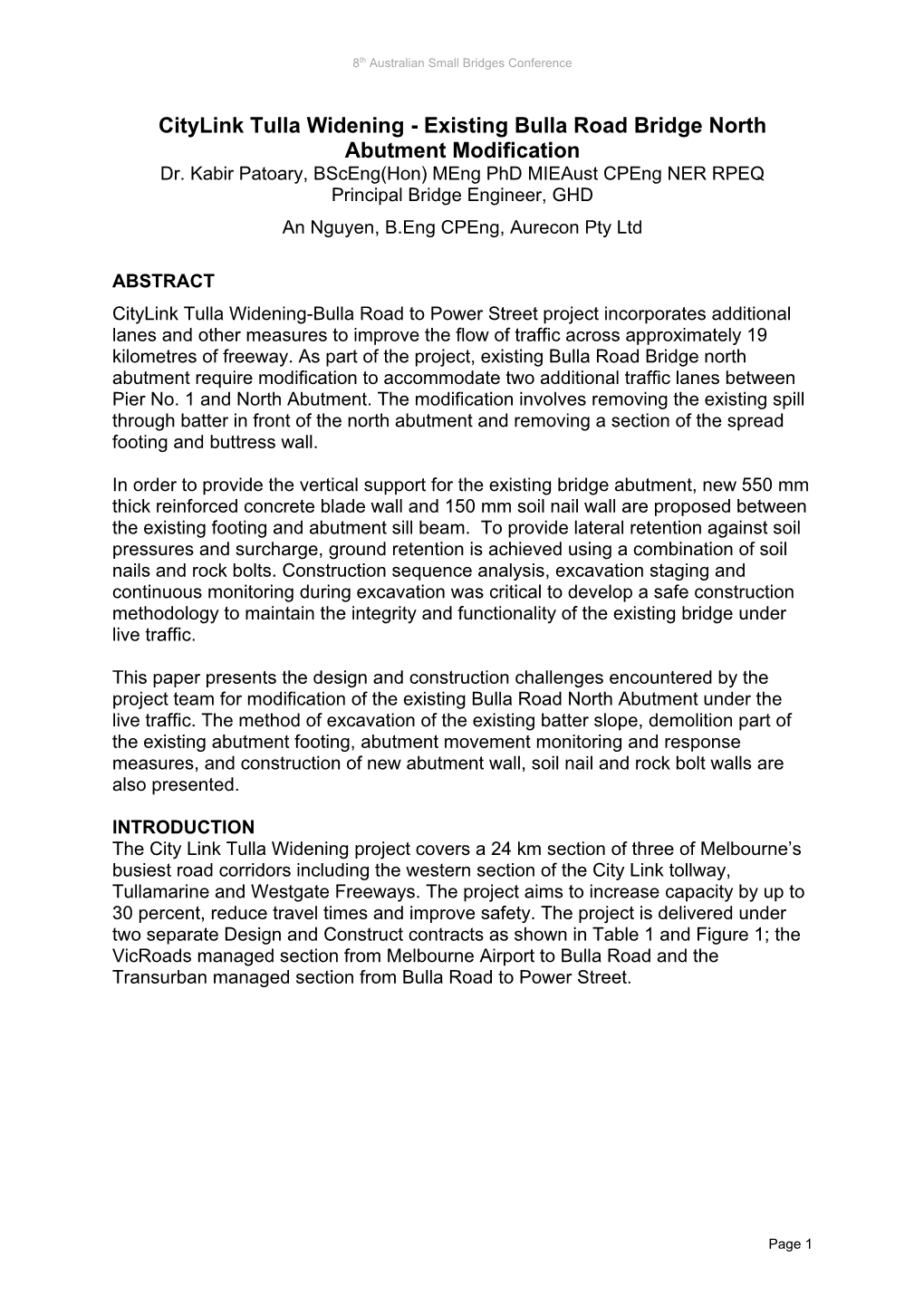
Load more
Recommended publications
-
Citylink Groundwater Management
CASE STUDY CityLink Groundwater Management Aquifer About CityLink Groundwater implications for design and construction A layer of soil or rock with relatively higher porosity CityLink is a series of toll-roads that connect major and permeability than freeways radiating outward from the centre of Design of tunnels requires lots of detailed surrounding layers. This Melbourne. It involved the upgrading of significant geological studies to understand the materials that enables usable quantities stretches of existing freeways, the construction of the tunnel will be excavated through and how those of water to be extracted from it. new roads including a bridge over the Yarra River, materials behave. The behavior of the material viaducts and two road tunnels. The latter are and the groundwater within it impacts the design of Fault zone beneath residential areas, the Yarra River, the the tunnel. A challenge for design beneath botanical gardens and sports facilities where surface suburbs and other infrastructure is getting access A area of rock that has construction would be either impossible or to sites to get that information! The initial design of been broken up due to stress, resulting in one unacceptable. the tunnel was based on assumptions of how much block of rock being groundwater would flow into the tunnel, and how displaced from the other. The westbound Domain tunnel is approximately much pressure it would apply on the tunnel walls They are often associated 1.6km long and is shallow. The east-bound Burnley (Figure 2). with higher permeability than the surrounding rock tunnel is 3.4km long part of which is deep beneath the Yarra River. -
1 /(I,,. 052 Vicrqads 1994-1995 the Honourable WR Baxter, MLC Minister for Roads and Ports 5Th Floor 60 Denmark Street Kew Vic 3101
1 /(I,,. 052 VicRQads 1994-1995 The Honourable WR Baxter, MLC Minister for Roads and Ports 5th Floor 60 Denmark Street Kew Vic 3101 Dear Minister VicRoads' Annual Report 1994-1995 I have pleasure in submitting to you, for presentation to Parliament, the Annual Report of the Roads Corporation (VicRoads) for the period 1Jul y 1994 to 30June1995. Yours sincerely COLIN JORDAN CHIEF EXECUTIVE 052 VicRoads l 994-1995 Annual report :VicR.oads Location: BK Barcode: 31010000638256 • Report from Chief Executive 4 • Improving Front-line Services 22 Corporate 6 Vehicle Registration 22 Mission Staterrent 6 Licensing 22 Advisory Board Members 6 Driver and Vehicle Information 23 Corporate Management Group 7 Other Initiatives 23 Senior Organisation Structure 7 Enhancing the Environment 24 • Managing Victoria's Road System 8 Environment Strategy 24 Major Metropolitan Road Improvements 8 Traffic Noise 24 Major Rural Road Improvements 9 Air Quality 25 The Better Roads Victoria Program 10 Enhancing theLandscape 25 • Managing Victoria's road system. Strategic Planning 11 Bicycles 25 Page 12 Federal Funding 11 • Managing for Results 26 Maintaining Roads and Bridges 12 People 26 • Improving Traffic Flow and Mobility 14 Qual ity Management 27 Traffic Management Initiatives 14 Improving Business Prcre;ses 27 Reforming Regulation 14 Benchmarking 28 Supporting Government Initiatives 17 Research and Development 28 • Enhancing Road Safety 18 Private Sector Partnership 29 Safer Roads 18 Partnership with Local Government 29 Safer Road Use 19 • Financial Management 30 Saler Vehicles 19 • Financial Statements 34 Strategy and Co-ordination 20 • Appendices 46 Legislation 46 Enhancing the environment. Page24 · Workforce Data 46 • VicRoads 1994-95 highlights. -
North Melbourne Station Melbourne
2 North Melbourne Station Melbourne e c T r e t s n u M t S Victoria St h g t t r t S S t S u S n l d b V l ic to r a ria i S n e y t o f r h o w t s s t a r D o t o L e S b d b n A A Silk P L l a Miller St u r e n s Spe S nce t r S Miller St R t a i t lw S a l y l P e l w a Dy d t non R S 2 NORTH MELBOURNE t S h g r u b y r D Ire lan d S t Pl s t k S ic d r D o f s t o b b T A a i t L a ne e A n dd a er L ley it S a t T t S e k w a H e n a L n e d d a M R a i lw t a S y n e P d l o R 0 50 100 200 300 Mtetres Image © Data source: DEDJTR, Aerial Imagery, 2015. Vicmap DELWP, Data, 2015 S Fo ey ot nl North Melbournesc Station opened in 1859 and is a ta ray S 0 50 Rd100 200 300 major interchange station servicing the Craigieburn,Metres Flemington Racecourse, Sunbury, Upfield, Werribee Document Path: G:\31\33036\GIS\Maps\Working\31-33036_001_OtherStationSiteFootprints300mAerial_20cm.mxd and Williamstown lines. -
Victoria Harbour Docklands Conservation Management
VICTORIA HARBOUR DOCKLANDS CONSERVATION MANAGEMENT PLAN VICTORIA HARBOUR DOCKLANDS Conservation Management Plan Prepared for Places Victoria & City of Melbourne June 2012 TABLE OF CONTENTS LIST OF FIGURES v ACKNOWLEDGEMENTS xi PROJECT TEAM xii 1.0 INTRODUCTION 1 1.1 Background and brief 1 1.2 Melbourne Docklands 1 1.3 Master planning & development 2 1.4 Heritage status 2 1.5 Location 2 1.6 Methodology 2 1.7 Report content 4 1.7.1 Management and development 4 1.7.2 Background and contextual history 4 1.7.3 Physical survey and analysis 4 1.7.4 Heritage significance 4 1.7.5 Conservation policy and strategy 5 1.8 Sources 5 1.9 Historic images and documents 5 2.0 MANAGEMENT 7 2.1 Introduction 7 2.2 Management responsibilities 7 2.2.1 Management history 7 2.2.2 Current management arrangements 7 2.3 Heritage controls 10 2.3.1 Victorian Heritage Register 10 2.3.2 Victorian Heritage Inventory 10 2.3.3 Melbourne Planning Scheme 12 2.3.4 National Trust of Australia (Victoria) 12 2.4 Heritage approvals & statutory obligations 12 2.4.1 Where permits are required 12 2.4.2 Permit exemptions and minor works 12 2.4.3 Heritage Victoria permit process and requirements 13 2.4.4 Heritage impacts 14 2.4.5 Project planning and timing 14 2.4.6 Appeals 15 LOVELL CHEN i 3.0 HISTORY 17 3.1 Introduction 17 3.2 Pre-contact history 17 3.3 Early European occupation 17 3.4 Early Melbourne shipping and port activity 18 3.5 Railways development and expansion 20 3.6 Victoria Dock 21 3.6.1 Planning the dock 21 3.6.2 Constructing the dock 22 3.6.3 West Melbourne Dock opens -
Victoria Government Gazette No
Victoria Government Gazette No. S 207 Friday 22 December 2000 By Authority. Victorian Government Printer SPECIAL Melbourne City Link Act 1995 NOTICE UNDER SECTION 71(1) Under section 71(1)(a) of the Melbourne City Link Act 1995 (Òthe ActÓ), Transurban City Link Limited ABN 65 070 810 678 (the relevant corporation in relation to the Link road) specifies the following toll zones on the Link road: Toll Zone Area on the Link road 4 That part of the Link road being the Domain Tunnel and that part of the Link road leading into that Tunnel between the eastern portal of that Tunnel and Punt Road, other than that part of the Link road - (a) being the eastbound carriageways of the Link road; (b) between Punt Road and the exit to Boulton Parade; and (c) comprising Boulton Parade. 5 That part of the Link road being the Burnley Tunnel and that part of the Link road leading out of that Tunnel between the eastern portal of that Tunnel and Burnley Street. 6 That part of the Link road being the eastbound carriageways between Punt Road and Burnley Street other than that part of the Link road being the Burnley Tunnel and that part of the Link road leading out of that Tunnel between the eastern portal of that Tunnel and Burnley Street. 7 That part of the Link road between Burnley Street and Punt Road and including that part of the Link roadÑ (a) between Punt Road and the exit to Boulton Parade, other than the eastbound carriageways; and (b) comprising Boulton Parade, other than: (i) the eastbound carriageways between Burnley Street and Punt Road; and (ii) that part of the Link road being the Burnley Tunnel and that part of the Link road leading out of that Tunnel between the eastern portal of that Tunnel and Burnley Street. -
Victoria Class 1 Load Carrying Vehicle and Special Purpose Vehicle Mass and Dimension Exemption Notice 2019 (No
Commonwealth of Australia Gazette Published by the Commonwealth of Australia GOVERNMENT NOTICES HEAVY VEHICLE NATIONAL LAW Victoria Class 1 Load Carrying Vehicle and Special Purpose Vehicle Mass And Dimension Exemption Notice 2019 (No. 1) PART 1: PRELIMINARY Purpose 1. The purpose of this Notice is to exempt the categories of Class 1 Heavy Vehicles specified in this Notice from— a) the prescribed mass requirements specified in the Notice; and b) the prescribed dimension requirements specified in the Notice. Authorizing provisions 2. This Notice is made under section 117 of the Heavy Vehicle National Law (HVNL) as in force in each state or territory (HVNL). Title 3. This Notice may be cited as the Victoria Class 1 Load Carrying Vehicle and Special Purpose Vehicle Mass And Dimension Exemption Notice 2019 (No. 1). Commencement 4. This Notice comes into operation on 10 February 2019. Expiry 5. This Notice expires on 9 February 2024. Definitions 6. Unless otherwise stated, words and expressions used in this Notice have the same meanings as those defined in the HVNL. 7. In this Notice, “Class 1 OSOM Route Access Lists” means the Victorian Class 1 Oversize and Overmass (OSOM) Route Access Lists referenced in Appendix 1; “Hume Freeway” means the Hume Freeway between Thomastown and the NSW border and includes the Hume Highway at Kalkallo; “main road” means a road described in the Victorian Class 1 OSOM Route Access Lists; Victoria Class 1 Load Carrying Vehicle and Special Purpose Vehicle Mass And Dimension Exemption Notice 2019 (No. 1) Page 1 -
East-West Road Travel 32 L Investing in Transport - Overview
31 l east-west road travel 32 l investing in transport - overview Travel patterns in Melbourne are changing. More and more The EWLNA has found that: people are travelling to and from the central city during peak • There is substantial demand for cross city travel, with periods; more people are moving around the city outside these particularly strong growth in travel from the west to the east periods; and more people are making trips across the city. and south-east. The combined impact of these trips is higher traffi c volumes and greater congestion on roads in the city’s inner and middle • Transport options for travel across the city are seriously suburbs, as well as signifi cant bottlenecks on both the road and congested. rail networks. • While the Monash-CityLink-West Gate freeway upgrade will The EWLNA has found a strong and growing demand for relieve pressure along this corridor, the extra capacity being east-west road travel in Melbourne – a demand that existing provided on the route will be fully taken up during peak infrastructure will be unable to meet without a very substantial periods within a relatively short time. increase in congestion. • With the exception of the Monash-CityLink-West Gate Modelling undertaken for the EWLNA confi rms what every freeway, the east-west roads within the EWLNA Study Area person travelling across Melbourne knows: that the increasing are disconnected and poorly suited to effi ciently moving high demand for travel, the escalating urban freight task and the volumes of traffi c across the city. growing number of cars on Melbourne’s roads are generating • Congestion on key east-west routes – and the accompanying greater levels of congestion on major cross city routes. -
Height Clearance Under Structures for Permit Vehicles
SEPTEMBER 2007 Height Clearance Under Structures for Permit Vehicles INFORMATION BULLETIN Height Clearance A vehicle must not travel or attempt to travel: Under Structures for (a) beneath a bridge or overhead Permit Vehicles structure that carries a sign with the words “LOW CLEARANCE” or This information bulletin shows the “CLEARANCE” if the height of the clearance between the road surface and vehicle, including its load, is equal to overhead structures and is intended to or greater than the height shown on assist truck operators and drivers to plan the sign; or their routes. (b) beneath any other overhead It lists the roads with overhead structures structures, cables, wires or trees in alphabetical order for ready reference. unless there is at least 200 millimetres Map references are from Melway Greater clearance to the highest point of the Melbourne Street Directory Edition 34 (2007) vehicle. and Edition 6 of the RACV VicRoads Country Every effort has been made to ensure that Street Directory of Victoria. the information in this bulletin is correct at This bulletin lists the locations and height the time of publication. The height clearance clearance of structures over local roads figures listed in this bulletin, measured in and arterial roads (freeways, highways, and metres, are a result of field measurements or main roads) in metropolitan Melbourne sign posted clearances. Re-sealing of road and arterial roads outside Melbourne. While pavements or other works may reduce the some structures over local roads in rural available clearance under some structures. areas are listed, the relevant municipality Some works including structures over local should be consulted for details of overhead roads are not under the control of VicRoads structures. -
Final Submission – Western Distributor Tunnel Project EES Process by (Dr) Pat Love, Geoff Hjorth, Marlene Monahan, Jacob Holley, Jenny Harrison
1 Final Submission – Western Distributor Tunnel Project EES Process By (Dr) Pat Love, Geoff Hjorth, Marlene Monahan, Jacob Holley, Jenny Harrison 1. Achieving the Project Objectives 1.1 Why are we doing this project? (slide 3) The EES identifies four objectives as targets that this project is designed to meet: (3) Improve transport performance in M1 Corridor Reduce reliance on West Gate Bridge Improve freight access to the Port of Melbourne Improve community amenity on local streets in inner west All of these are worthy goals. If transport is understood in its broadest sense – road, rail and active transport - then improving connectivity and providing transport options and building in network resilience is important for our long-term economic sustainability and liveability. However, this submission holds that this project of itself will not achieve all these aims. It is essentially a road project. It is transport in its narrowest definition. The addition of cycling infrastructure is window- dressing, and will not of itself ensure that more people of the M1 Corridor take up more active transport options, such as walking and cycling. The WDA presentation did not allude to any other city in the world taking these or similar steps to solve the future problems of amenity, transport connectivity and resilience. Melbourne is not the only city in the world with a traffic congestion problem. Is London proposing to build urban freeway through Shoreditch to the City? Is New York building an expressway through Manhattan? Not since Jane Jacobs defeated Robert Moses in protecting the Village. Where were references either in the EES or in the Business Case to the successful examples of cities other than Australia’s east coast capitals and US car-dependent mega-sprawl cities? The short answer is, there are none. -
2022 FIREBALL WORLD CHAMPIONSHIPS Hosted by the Royal Geelong Yacht Club
2022 FIREBALL WORLD CHAMPIONSHIPS Hosted by the Royal Geelong Yacht Club www.rgyc.com.au www.visitgeelongbellarine.com.au February 2022 Photo: Andrew Davies FIREBALL WORLD CHAMPIONSHIPS GEELONG 2022 On behalf of our Australian Fireball Sailors (IFAA) I’d like to welcome your interest about the next Fireball World Championship to be held at Royal Geelong Yacht Club (RGYC), near Melbourne, Australia. The organising team comprising RGYC and local IFAA leaders are going full steam ahead to make arrangements for an exciting and well planned regatta. They are leaving no stone unturned to have great race management, reliable end to end boat transport logistics, accommodation and transport information that provides plenty of options and a social program to cater for sailors and their family and friends. When we held the Australian Championship at RGYC in Feb 2019 we found most people could stay within walking distance of the club. There were plenty of restaurants and pubs just 1-2 blocks away from the club. The environment created a great opportunity to do some post race socialising at the club and then wander off in groups to explore and taste the variety of options available for dinner. During the regatta we experienced everything from light and tricky shifting breezes, champagne sailing at 12 -16 knots and stronger winds. The nearby coast, home to Bell’s Beach surfing and the Great Ocean Road offers a wealth of holiday options for people able to extend their stay to enjoy a longer visit to Australia in summer. We look forward to welcoming you to Geelong in 2022. -
TTF Rapid Buses, Road & Rail (Melbourne Airport)
RAPID BUSES, ROAD AND RAIL GROUND TRANSPORT SOLUTIONS TO MEET MELBOURNE AIRPORT’S PASSENGER GROWTH TO 2050 JULY 2013 Membership of Tourism & Transport Forum Tourism & Transport Forum (TTF) is a national, member-funded CEO forum, advocating the public policy interests of 200 leading corporations and institutions in the Australian tourism, transport, aviation and investment sectors For further information please contact: Justin Wastnage | Director, Aviation Policy | [email protected] Martin Gray | Policy Officer |[email protected] Contents EXECUTIVE SUMMARY ............................................................................................... 4 Ensuring transport choice for Melbourne Airport ................................................................ 4 SUMMARY OF RECOMMENDATIONS ....................................................................... 6 List of figures ........................................................................................................................................................... 6 MELBOURNE AIRPORT – THE NEXT 30 YEARS ............................................................ 7 Forecast demand .................................................................................................................... 7 ACCESSING MELBOURNE AIRPORT .......................................................................... 8 Internal airport transport ......................................................................................................... 8 Broader road network ............................................................................................................ -
City Road Master Plan
Part Three Master Plan actions In this part you will find: • The design proposals for each action in the Master Plan 1. TRANSFORM CITY ROAD WEST INTO A GREAT CENTRAL city street Understanding City Road West Connections to the City of Port ‘The intersection at Phillip and Fishermans Bend are a key City Road West (between Clarendon consideration for the design proposals in Clarke Street is poorly Street and Power Street) is a local this section. marked and is in need street and can be enhanced significantly of a crossing.’ to make it safer, more attractive and To make it easier to demonstrate the welcoming. proposed changes in the master plan, City Road West has been shown in @gj_win, resident The master plan proposes to transform two sections either side of Kings Way: (20 February 2014) this section of City Road into a great Clarendon Street to Queens Bridge central city street. With an increasing Street and Queens Bridge Street to number of residential apartments, Boyd Power Street. Community Hub and tram and bus services in this location, this part of The existing conditions of City Road and City Road is the centre of an evolving changes proposed in this master plan community (see figure 3.1). are outlined on pages 42 to 55. Traffic volumes in City Road West are significantly lower than City Road East as it does not perform the same role as the bypass to the Burnley Tunnel. This means there are greater opportunities to transform City Road West into a great central city street. ALEXANDRA AVENUE N ST KILDA ROAD CITY ROAD NGV SOUTHBANK BOULEVARD