Extraction Method of Flax Fibre and Its Uses
Total Page:16
File Type:pdf, Size:1020Kb
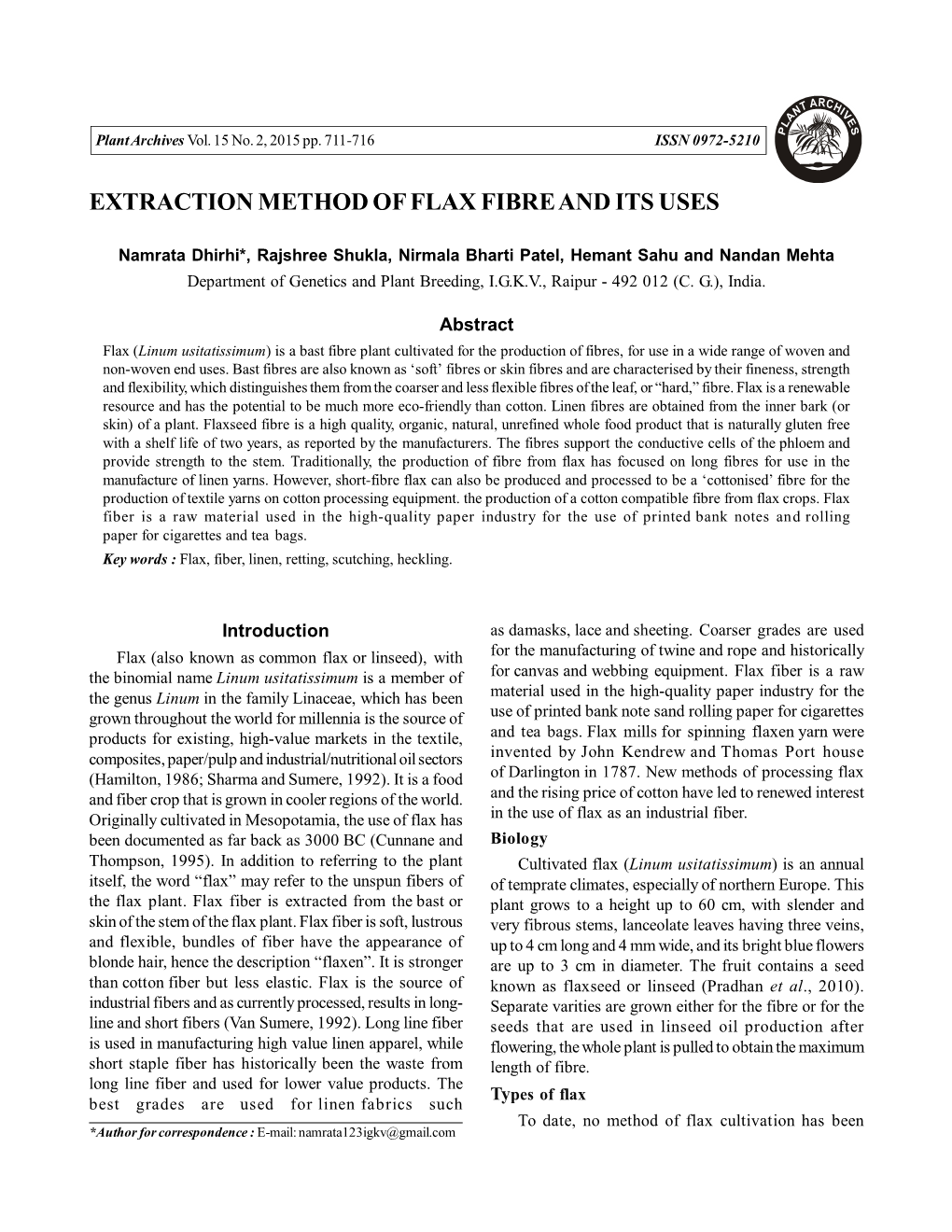
Load more
Recommended publications
-
Spinning and Winding Taro Nishimura
The_Textile_Machinery_Society_of_Japan_Textile_College_2-Day_Course_on_Cloth_Making_Introduction_to_Spinning_2014_05_22 Spinning and Winding Taro Nishimura 1. Introduction Since several thousand years ago, humans have been manufacturing linen, wool, cotton, and silk to be used as fibrous materials for clothing. In 繊維 (sen’i ), which is the word for “fiber,” the Chinese character 繊 (sen ) is a unit for decimal fractions of one ten-millionth (equal to approximately 30 Ǻ), while 維 (i) means “long and thin.” Usually, fibers are several dozen µ thick, and can range from around one centimeter long to nigh infinite length. All natural materials, with the exception of raw silk, are between several to several dozen centimeters long and are categorized as staple fibers. Most synthetic fibers are spun into filaments. Figure 1 shows how a variety of textile product forms are interrelated. Short fibers are spun into cotton (spun) yarns, whereas filaments are used just as they are, or as textured yarns by being twisted or stretched. Fabric cloths that are processed into two-dimensional forms using cotton (spun) yarns and filament yarns include woven fabrics, knit fabrics, nets, and laces. Non-woven fabrics are another type of two-dimensional form, in which staple fibers and filaments are directly processed into cloths without being twisted into yarns. Yet another two-dimensional form is that of films, which are not fiber products and are made from synthetic materials. Three-dimensional fabrics and braids are categorized as three-dimensional forms. This paper discusses spinning, or the process of making staple fibers into yarns, and winding, which prepares fibers for weaving. One-dimensional Two-dimensional Three-dimensional Natural Staple fibers Spun yarns Woven fabrics Three-dimensional materials Filaments Filament yarns Knit fabrics fabrics Synthetic Nets Braids materials Laces Non-woven fabrics Films Fig. -
Glossary of Terms
The Missing Chapter: Untold Stories of the African American Presence in the Mid-Hudson Valley Glossary of Terms Bay: A compartment in a barn, used fore storing hay or grain. Britches or Breeches: Short trousers, especially fastened below the knee. Breeches were originally made of leather, but were made of various materials. Buckskin: Leather made from a buck’s skin, could also refer to a thick smooth cotton or woolen cloth. Coating: A cloth used for making coats. Drab coloured: A dull brownish yellow or dull gray color. Felt: A fabric made of wool and hair. Fife: A small high-pitched flute without keys, often used in military and marching bands. Fustian: A coarse sturdy cloth of a cotton-linen blend; any durable fabric with a raised nap made mainly from cotton, for example, corduroy or moleskin. Gaol: is an early Modern English spelling for jail, with the same pronunciation and meaning of a place of legal detention. Grogram: A rough fabric of silk and wool with a diagonal weave. High Dutch: An eighteenth century term for German. Homespun: Spun or woven in the home; a plain coarse woolen cloth made of homespun yarn. Instant (inst.): The current calendar month. Inventory: a detailed list of things in one’s view or possession; especially, a regular survey of all goods and materials in stock. Linsey Woolsey: A coarse fabric of cotton or linen woven with wool. Low Dutch: used to signify those persons of Netherlandish descent. Manchester velvet: A fine cotton used in making dresses. The Missing Chapter: Untold Stories of the African American Presence in the Mid-Hudson Valley Nanekeen: A sturdy yellow or buff cotton cloth. -
And Interdisciplinary Nature of Textile Design Research of Linseed Fibres
Multi- and interdisciplinary nature of textile design research of linseed fibres Tiina Härkäsalmi* and Ilpo Koskinen** Aalto-University, School of Art and Design, Department of Design Hämeentie 135 C, 00560 Helsinki, Finland *e-mail: [email protected] **e-mail: [email protected] Abstract: In the future there will be an increasing need for renewable, recyclable and environmentally safety fibres, which are compatible with existing, cotton-based textile manufacturing technologies and are competitive on price and quality. In this study as a raw material the linseed fibres are used, which is almost an unexploited resource for high value end uses. This paper describes a multidisciplinary design study that consisted of three parts, a microbiological study that devel- oped a Fusart®-method for cottonizing linseed fibres, a production model study aimed at showing how the fibres could be processed in an industrial scale, and a fibre quality evaluation study. In practise it means that lustrous and soft fibres, light coloured can be produced cost-efficiently and environmentally-consciously for textiles and potential for producing high-quality bio-based mate- rial with tailored properties. Keywords: design research, material research, fungus, textile design 1. Introduction The objective of this study is to explore the suitability of linseed elementary fibres in new textile and technical applications and creating prerequisites for product design and productization. The study is based on a multidisciplinary approach to the use of flax elementary fibres where, rather than tradi- tional long-linen textile processing technology, short-fibre methods are employed. Special attention was paid to the quality requirements of rotor spinning. -
Online Appendix ∗
Necessity is the Mother of Invention: Input Supplies and Directed Technical Change ONLINE APPENDIX ∗ W. Walker Hanlon UCLA and NBER July 14, 2014 Contents A Further details on the empirical setting 1 A.1 Increase in transport costs caused by the Civil War . .1 A.2 Additional details on cotton supplies . .2 A.3 Most innovative technology categories by patent count . .2 A.4 Definitions of important textile terms . .3 A.5 Cotton textile machinery . .4 A.6 Details on the differences between cotton types . .7 A.7 Impact of ginning on cotton fiber length . .8 A.8 Example patent specifically mentioning Indian cotton . .8 ∗Author email: [email protected]. A.9 Indian cotton exports . .9 B Data appendix 9 B.1 Overview of the patent data . .9 B.2 Data on spinning technology subcategories . 11 B.3 Identifying patents related to Indian cotton . 12 B.4 Details of the British patent system between 1852 and 1883 . 13 B.5 Details on inventors in the patent database . 14 B.6 Further details on the patent quality measure data . 15 C Appendix to the Empirical Analysis Section 16 C.1 Analysis of patent data . 16 C.2 Analysis of high-quality patents . 24 C.3 Dobson & Barlow graphs . 26 D Appendix to the relative price analysis 29 D.1 Full price regression results . 33 D.2 Using the same denominator for all relative price series . 35 E Some evidence on the elasticity of substitution between cotton types 36 2 A Further details on the empirical setting A.1 Increase in transport costs caused by the Civil War The figure below shows an index of transport costs during the early part of the war constructed using the wedge between the cotton price in New Orleans, which was within the blockaded region until April of 1862, and the price in Liverpool. -
Basic of Textiles
BASIC OF TEXTILES BFA(F) 202 CC 5 Directorate of Distance Education SWAMI VIVEKANAND SUBHARTI UNIVERSITY MEERUT 250005 UTTAR PRADESH SIM MOUDLE DEVELOPED BY: Reviewed by the study Material Assessment Committed Comprising: 1. Dr. N.K.Ahuja, Vice Chancellor Copyright © Publishers Grid No part of this publication which is material protected by this copyright notice may be reproduce or transmitted or utilized or store in any form or by any means now know or here in after invented, electronic, digital or mechanical. Including, photocopying, scanning, recording or by any informa- tion storage or retrieval system, without prior permission from the publisher. Information contained in this book has been published by Publishers Grid and Publishers. and has been obtained by its author from sources believed to be reliable and are correct to the best of their knowledge. However, the publisher and author shall in no event be liable for any errors, omission or damages arising out of this information and specially disclaim and implied warranties or merchantability or fitness for any particular use. Published by: Publishers Grid 4857/24, Ansari Road, Darya ganj, New Delhi-110002. Tel: 9899459633, 7982859204 E-mail: [email protected], [email protected] Printed by: A3 Digital Press Edition : 2021 CONTENTS 1. Fiber Study 5-64 2. Fiber and its Classification 65-175 3. Yarn and its Types 176-213 4. Fabric Manufacturing Techniques 214-260 5. Knitted 261-302 UNIT Fiber Study 1 NOTES FIBER STUDY STRUCTURE 1.1 Learning Objective 1.2 Introduction 1.3 Monomer, Polymer, Degree of polymerization 1.4 Student Activity 1.5 Properties of Fiber: Primary & Secondary 1.6 Summary 1.7 Glossary 1.8 Review Questions 1.1 LEARNING OBJECTIVE After studying this unit you should be able to: ● Describe the Natural Fiber. -
Education Teacher’S Kit
Industrial Heritage - The Textile Industry Education Teacher’s Kit Background There is archaeological evidence of textile production in Britain from the late-prehistoric period onwards. For many thousands of years wool was the staple textile product of Britain. The dominance of wool in the British textile industry changed rapidly during the eighteenth century with the development of mechanised silk production and then mechanised cotton production. By the mid-nineteenth century all four major branches of the textile industry (cotton, wool, flax, hemp and jute and silk) had been mechanised and the British landscape was dominated by over 10,000 mill buildings with their distinctive chimneys. Overseas competition led to a decline in the textile industry in the mid-twentieth century. Today woollen production is once again the dominant part of the sector together with artificial and man-made fibres, although output is much reduced from historic levels. Innovation Thomas Lombe’s silk mill, built in 1721, is regarded as the first factory-based textile mill in Britain. However, it was not until the handloom was developed following the introduction of John Kay’s flying shuttle in 1733 that other branches of the textile industry (notably cotton and wool) became increasingly mechanised. In the second half of the eighteenth century, a succession of major innovations including James Hargreaves’s spinning jenny (1764), Richard Arkwright’s water frame (1769), his carding engine (1775), and Samuel Crompton’s mule (1779), revolutionised the preparation and spinning of cotton and wool and led to the establishment of textile factories where several machines were housed under one roof. -
PRELIMINARY TREATMENT of FIBRES, E.G. for SPINNING (Winding Or Unwinding, Conducting Or Guiding Laps, Webs, Slivers Or Roving
D01G CPC COOPERATIVE PATENT CLASSIFICATION D TEXTILES; PAPER TEXTILES OR FLEXIBLE MATERIALS NOT OTHERWISE PROVIDED FOR D01 NATURAL OR MAN-MADE THREADS OR FIBRES; SPINNING (NOTE omitted) D01G PRELIMINARY TREATMENT OF FIBRES, e.g. FOR SPINNING (winding or unwinding, conducting or guiding laps, webs, slivers or rovings in general, sliver or roving cans, depositing in sliver or roving cabs B65H; preparation of fibres for paper-making D21) NOTE Attention is drawn to the note following the title of Class D01. WARNING In this subclass non-limiting references (in the sense of paragraph 39 of the Guide to the IPC) may still be displayed in the scheme. 1/00 Severing continuous filaments or long fibres, e.g. 9/08 . by means of air draught arrangements stapling 9/10 . using foraminous cylinders (foraminous suction 1/02 . to form staple fibres not delivered in strand form cylinders for lap-forming D01G 25/00) 1/022 . {by solvents} 9/12 . Combinations of opening or cleaning machines 1/025 . {by thermic means, e.g. laser} 9/14 . Details of machines or apparatus 1/027 . {by freezing} 9/16 . Feeding arrangements (fibre-feeding apparatus 1/04 . by cutting of general application in fibre-treating machines 1/06 . Converting tows to slivers or yarns, e.g. in D01G 23/00) direct spinning (drafting arrangements, twisting 9/18 . Arrangements for discharging fibres arrangements D01H) 9/20 . Framework; Casings; Coverings; Grids 1/08 . by stretching or abrading 9/22 . Driving arrangements 1/081 . {with preferential breaking zones} 11/00 Disintegrating fibre-containing articles to obtain 1/083 . {obtained by mechanical means, e.g. -
The First Plant Bast Fibre Technology: Identifying Splicing in Archaeological Textiles
Archaeological and Anthropological Sciences (2019) 11:2329–2346 https://doi.org/10.1007/s12520-018-0677-8 ORIGINAL PAPER The first plant bast fibre technology: identifying splicing in archaeological textiles Margarita Gleba1 & Susanna Harris2 Received: 2025 May 20172018 /Accepted: 2625 July 20182018 /Published online: 25 July 2018 # The Author(s) 2018 Abstract Recent research into plant bast fibre technology points to a Neolithic European tradition of working fibres into threads by splicing, rather than draft spinning. The major issue now is the ability of textile specialists and archaeobotanists to distinguish the technology of splicing from draft-spun fibres. This paper defines the major types of splicing and proposes an explicit method to observe, identify and interpret spliced thread technology. The identification of spliced yarns is evaluated through the examination of textiles from Europe, Egypt and the Near East. Through the application of this method, we propose that the switch from splicing to draft spinning plant fibres occurred much later than previously thought. The ramifications of this shift in plant processing have profound implications for understanding the chaîne opératoire of this ubiquitous and time-consuming technology, which will have to be factored into social and economic reconstructions of the past. Keywords Plant bast fibre . Splicing . Spinning . Technology . SEM . Identification method Introduction 25 years, however, research into a different yarn-making technology has developed based on the Pharaonic Egyptian Fibre technologies: from plant to thread textile finds—it is known as splicing, a term that in fact subsumes a variety of related techniques (Leuzinger and Plant bast fibre products, such as linen textiles, have a Rast-Eicher 2011). -
(A) Machinery, Plant, Vehicles ; (B) Construction of Buildings ; Basic Data on the Essential Characteristics of Industry Were Co
Official Journal of the European Communities 201 13.8.64 OFFICIAL JOURNAL OF THE EUROPEAN COMMUNITIES 2193/64 COUNCIL DIRECTIVE of 30 July 1964 concerning co-ordinated annual surveys of investment in industry ( 64/475/EEC ) THE COUNCIL OF THE EUROPEAN ECONOMIC Article 2 COMMUNITY, For the purposes of this Directive, an industry shall Having regard to the Treaty establishing the Euro be defined by reference to the 'Nomenclature of Indus pean Economic Community, and in particular Article tries in the European Communities' ( NICE). 1 In the 213 thereof ; case of small undertakings the survey may be carried out by random sampling. Having regard to the draft submitted by the Com Article 3 Whereas in order to carry out the tasks entrusted to it under the Treaty the Commission must have at its The figures to be recorded shall be those in respect disposal annual statistics on the trend of investment of annual investment expenditure ( including plant in the industries of the Community ; constructed by the undertakings themselves), broken Whereas in the industrial survey for 1962 comparable down as follows : basic data on the essential characteristics of industry ( a ) Machinery, plant, vehicles ; were collected for the first time ; whereas such a ( b) Construction of buildings ; census cannot be carried out frequently ; whereas annual statistics concerning certain basic matters ( c) Purchase of existing buildings and of land . cannot however be dispensed with for the intervening Investments of a social nature shall , where possible, be years -
Reference for Spinning, Dyeing and Finishing of Milk Fiber
Swicofil AG Textile Services Gerliswilstr. 23 CH-6021 Emmenbrücke Reference for Spinning, Dyeing and Finishing of milk fiber 1. Spinning technological process (example of yarn with 163tex) Scutching A002D---A006B---A036C (card wire) Carding A186D Drawing FA302 (two lines) Roving A454G Spinning FA502 Winding 2. Main technical measure for each process 1). Pretreatment As seen in Table 1, the mass specific resistance of milk protein fiber is larger, so the pretreatment before scutching is more important. After opening bales, the milk protein fiber needs some water and antistatic agent. Based on the tests of fiber property and the choice of antistatic agents, the moisture regain of pure spinning with milk protein fiber is controlled about 16%, and the add-on of chosen composite antistatic agent is about 1%. Meanwhile, the relative humidity in the workshop is controlled within 68~70% to reduce the electrostatic influence. 2). Process of opening and picking With good uniformity and less impurity, the milk protein fiber is bulky and it is easy to open, and the friction coefficient between fibers is low, and the cohesion force is relatively weaker. Thus, the process of opening and picking should adopt the process of precise picking, less beating and low speed. During production, the height of the beater in the grab machine stretched rib is 2.5mm, and the picking should be precise and the blending should be uniform. In the opening machine model A036C, the card beater is adopted to reduce fiber damage and the constant volume of laps should be smaller to avoid neps during opening and picking so the lap quality can be stable. -
Notes from the Flax Presentation by Bruce Engebertson April 29, 2017
notes from the Flax Presentation by Bruce Engebertson April 29, 2017 Bruce began spinning wool at age 10, despite the fact that no one in his immediate family had any background in spinning. A chance referral led him to Ester Kromaki about 25 years ago, and she taught him the traditional Finnish techniques for growing, processing, spinning, and weaving flax. He says his linen knowledge is firmly based in the Finnish traditions and that "he doesn't know a variety of methods but the ones he knows, he knows well." The flax plant is an annual that dies in the winter. It is a "greedy" plant which will take lots of nutrients, so it's best not to plant it in soil that has been exhausted by other crops like corn. Flax is best in full sun and protected from the wind. It is relatively free from insect pests and will even keep potato bugs away (so plant near potatoes!). Prepare the seed bed by spading up the area to be seeded (in our case, approximately 3 ft by 3 ft) and adding in some cow manure or other fertilizer. Make sure the area is free of weeds when you seed. Seed flax when the lilacs just begin blooming. The seed should be spread thickly -- about 5 to 7 seeds for a thumbprint (of course, this depends on the size of your -- hopefully green -- thumb). Do not plant in rows. Divide the seeds in half and sow half in one direction and the other half if the other direction. If the soil is the same color as the seeds, you can add sand to the mix so you'll have an idea of how the seeds are being spread out. -
My Linen Legacy a Tale on Women's Strength
My Linen Legacy A Tale on Women’s Strength Words by Marta Bahillo Photography by Adrià Cañameras My grandmother was like linen: robust, hard to get, She always talked about watching for the ‘brown beautiful and practical. little ball’ to come out in order to know when it She lived in Chaveán, a very small village in was ready. These brown little balls are the seeds. Galicia, North West Spain, by the highest mountain When they are brown and the stem turns yellow of the area, in a house that she had inherited from her it is time to harvest the plant. In order to get the great grandparents. She was wealthy enough never to maximum length of fibre for the linen, the plants have cattle, but she loved cultivating linen. From flax were never mown but uprooted: the longer the to cloth: for many years it was an obligatory process. stems, the longer the fibres and longer fibres meant And she made sure I knew about it. Ever since I can better quality. This laborious process, now done by remember, during each of my summer visits, she machine, was performed by hand right up until the told me the story of the linen process. end of the Second World War. I was the eldest granddaughter and now I know Once the harvesting was over, the real work how important that story was to her. It was a story began. The stalks were left to dry for weeks in the of community, a story of women´s hard work and open summer air.