A Review of Various Techniques Used for Shaft Failure Analysis
Total Page:16
File Type:pdf, Size:1020Kb
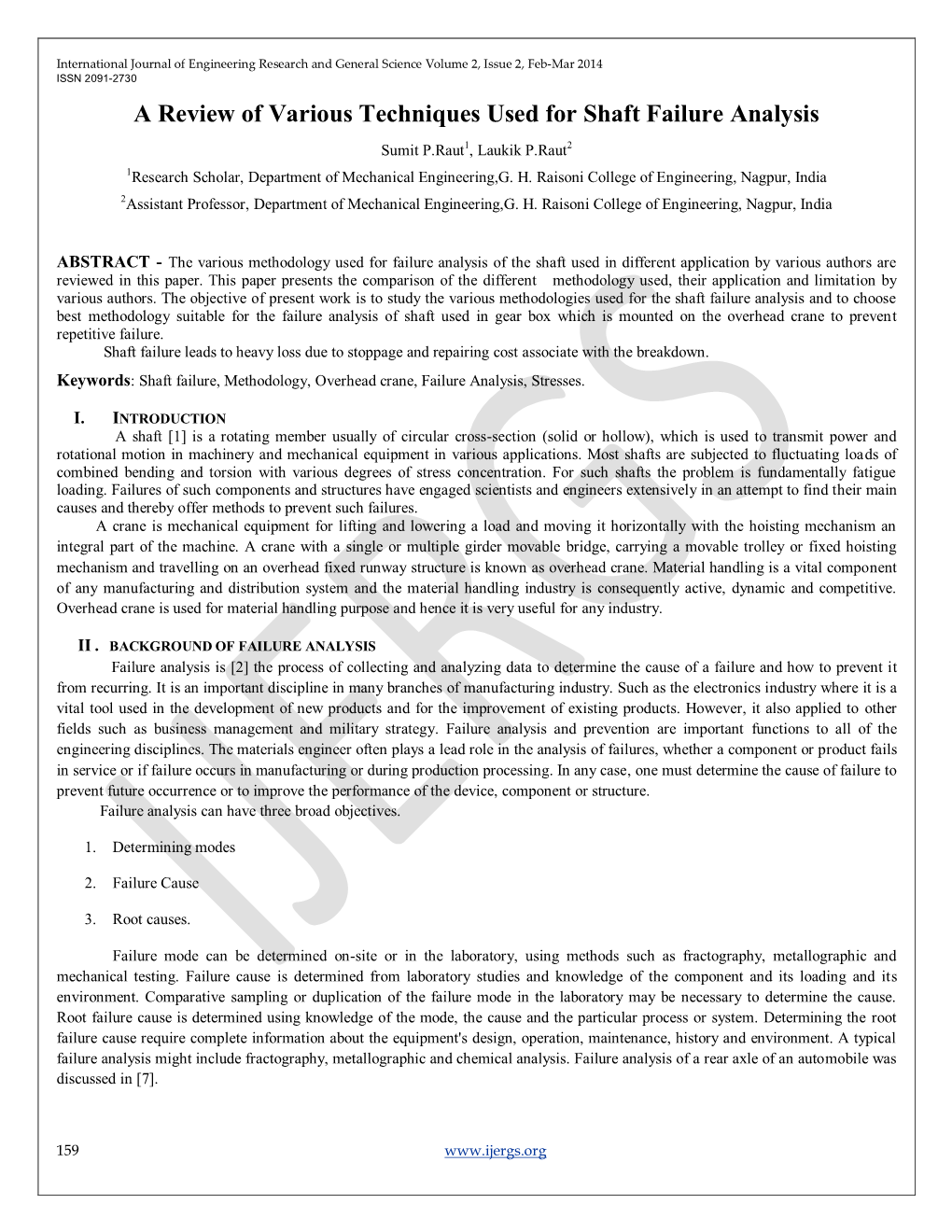
Load more
Recommended publications
-
Learning from Pipeline Failures
This document was downloaded from the Penspen Integrity Virtual Library For further information, contact Penspen Integrity: Penspen Integrity Units 7-8 Telephone: +44 (0)191 238 2200 St. Peter's Wharf Fax: +44 (0)191 275 9786 Newcastle upon Tyne Email: [email protected] NE6 1TZ Website: www.penspenintegrity.com United Kingdom WTIA/APIA Welded Pipeline Symposium Perth, Australia March 2008 LEARNING FROM PIPELINE FAILURES Hopkins, P ABSTRACT All engineering structures can fail, and oil and gas pipelines can and do fail. What can we learn from these failures, and could they have been avoided? Pipeline failures continue to occur, as pipelines present a complex mix of problems, in particular deterioration with time, changing conditions, external factors, and - as always – the ‘human’ factor. This paper emphasises that learning from pipeline failures can help us reduce these failures, and hence we should never allow a pipeline failure to pass without a thorough and wide ranging ‘lessons learnt’ exercise that is both used and shared within the pipeline community. Three major conclusions emerge from this paper: o Pipelines are a safe form of energy transportation; o Current trends indicate reducing pipeline failure rates; o Good training (knowledge transfer), a solid skills base, and strong management are key to preventing failures, but safety always starts with good design. Of particular note from recent failures is the increase in theft, sabotage and terrorist attacks. It will be difficult to reduce these failures by detection methods; therefore, prevention will be the best approach. KEYWORDS Pipeline, Oil, Gas, Failure. Damage, Defects, Theft, Sabotage, Terrorism. AUTHOR DETAILS Professor Phil Hopkins ([email protected]) is a Technical Director with Penspen Ltd., UK, and Visiting Professor at Newcastle University, UK. -
Caxton Okoh a Framework
CAXTON OKOH A FRAMEWORK DEVELOPMENT TO PREDICT REMAINING USEFUL LIFE OF A GAS TURBINE MECHANICAL COMPONENT SCHOOL OF AEROSPACE, TRANSPORT AND MANUFACTURING Manufacturing Department DOCTOR OF PHILOSOPHY, PhD Academic Year: 2013 - 2017 Supervisors: Professor Rajkumar Roy, Professor JÖrn Mehnen September 2017 SCHOOL OF AEROSPACE, TRANSPORT AND MANUFACTURING Manufacturing Department DOCTOR OF PHILOSOPHY, PhD Academic Year 2013 - 2017 CAXTON OKOH A Framework Development to Predict Remaining Useful Life of a Gas Turbine Mechanical Component Supervisors: Professor Rajkumar Roy, Professor JÖrn Mehnen September 2017 This thesis is submitted in partial fulfilment of the requirements for the degree of Doctor of Philosophy © Cranfield University 2017. All rights reserved. No part of this publication may be reproduced without the written permission of the copyright owner. ABSTRACT Power-by-the-hour is a performance based offering for delivering outstanding service to operators of civil aviation aircraft. Operators need to guarantee to minimise downtime, reduce service cost and ensure value for money which requires an innovative advanced technology for predictive maintenance. Predictability, availability and reliability of the engine offers better service for operators, and the need to estimate the expected component failure prior to failure occurrence requires a proactive approach to predict the remaining useful life of components within an assembly. This research offers a framework for component remaining useful life prediction using assembly level data. The thesis presents a critical analysis on literature identifying the Weibull method, statistical technique and data-driven methodology relating to remaining useful life prediction, which are used in this research. The AS-IS practice captures relevant information based on the investigation conducted in the aerospace industry. -
A-P201807-MICE Science Based Operational Risk
MIRCE Science Based Operational Risk Assessment Jezdimir Knezevic, MIRCE Akademy, Exeter, UK Abstract The philosophy of MIRCE Science is based on the premise that the purpose of existence of any functionable system 1 is to do functionability work. The work is done when the expected measurable function is performed through time. However, experience teaches us that expected work is frequently beset by the natural environment, the general population or the businesses, some of which result in hazardous consequences. Undoubtedly, the ability to accurately and quantitatively assess the risk of occurrence of these undesirable and especially those hazardous interruptions early in the design stages would be invaluable for all decision makers. Regardless of whether engineering solutions or management methods are chosen to control the risk, they will have a direct impact on the operational plan that should deliver the expected work, within the expected budget and delivering the expected return on their investment (e.g. profit or performance). For the last sixty years, Reliability Theory has been adopted to address this need. However, the efficacy of these predictions is only valid until the time of the occurrence of the first failure of a functional system. This is seldom understood and far from satisfactory where we are working with repairable or maintainable equipment and systems over their expected life. Consequently, the main objective of this paper is to demonstrate how the body of knowledge contained in MIRCE Science can be used for the assessment of the risk of occurrences of operational interruptions during the expected life of any given functionability system type. -
Failure Engineering Artifacts
This thesis is an attempt to clarify a concept we are all familiar with, engineers and non-engineers alike. It shows that, behind the first impression of familiarity, there is a Concept Analysis of an Engineering Failure: wide range of intuitions about failure which are not easily reconciled. While the ensuing ambiguities and lack of clarity may be tolerated in ordinary circumstances, engineers strive for precision and efficiency. These qualities become even more relevant given that engineering activities are increasingly carried out by multidisciplinary and multicultural teams. The chapters included in this thesis illustrate that pursuing conceptual clarification may result in valuable contributions to the existing literature. The identification of tacit assumptions that, so far, have gone undetected can help bringing some degree of order and unity to discussions that have shown a tendency towards fragmentation along disciplinary boundaries. As a whole, these chapters constitute the preliminaries of a conceptual framework that, once supplemented with additional engineering and philosophical contributions, may embrace the multiple facets of failure; a rather complex tangle of phenomena which, despite engineersí efforts to rein it in, is not going to disappear from the engineering agenda anytime soon. Luca Del Frate Del Luca Failure: Analysis of an ‘Wonder en is Engineering Concept gheen wonder’ Luca Del Frate Simon Stevin Series in the Philosophy of in the Philosophy Series Technology Stevin Simon Simon Stevin Series in the Philosophy of Technology Failure Analysis of an Engineering Concept Failure Analysis of an Engineering Concept Proefschrift ter verkrijging van de graad van doctor aan de Technische Universiteit Delft, op gezag van de Rector Magnificus prof. -
Madge, Jason John (2009) Numerical Modelling of the Effect of Fretting
Numerical Modelling of the Effect of Fretting Wear on Fretting Fatigue Jason John Madge, MEng(Hons). Thesis submitted to the University of Nottingham for the degree of Doctor of Philosophy June 2008 Numerical Modelling of the Effect of Fretting Wear on Fretting Fatigue Contents Abstract…………………………………………………………………………. v Publications ……………………………………………………………………. vi Acknowledgements…………………………………………………………… vii Nomenclature………………………………………………………………...… viii Chapter 1 Introduction 1.1 Air Travel………………………………………………………………. 1 1.2 Socio-Economic Drivers for Efficient Engine Design .……………. 2 1.3 A Future Perspective ………………………………………………… 2 1.4 Spline couplings……………………………………………………….. 3 1.5 Aims…………………………………………………………………….. 6 1.6 Thesis scope…………………………………………………………… 6 Chapter 2 Literature Review 2.1 Introduction……………………………………………………………... 8 2.2 Contact mechanics……………………………………..……………… 8 2.3 Tribology.……………………………………………………………… 16 2.3.1 Introduction……………………………………………………….. 16 2.3.2 Friction…………………………………………………………….. 16 2.3.3 Wear……………………………………………………………..... 18 2.4 Fatigue of Metals……………………………………………………... 19 2.4.1 General………….………………………………………………… 19 2.4.2 Fatigue Mechanisms…………………………………………….. 20 2.4.3 Relating Stress and Fatigue Life……………………………….. 21 2.4.4 Damage Models………………………………………………….. 24 2.4.5 Fracture Mechanics…………………………………………….... 27 2.5 Fretting…………………………………………………………….... 32 2.5.1 General…………………………………………………………...... 32 2.5.2 Multiaxial fatigue parameters in fretting…………………........... 36 2.5.3 Fracture mechanics in fretting……………………….................. 38 2.5.4 -
Failure Analysis and Fatigue Life Estimation of a Shaft of a Rotary Draw Bending Machine B
World Academy of Science, Engineering and Technology International Journal of Mechanical and Mechatronics Engineering Vol:11, No:11, 2017 Failure Analysis and Fatigue Life Estimation of a Shaft of a Rotary Draw Bending Machine B. Engel, Sara Salman Hassan Al-Maeeni important to ensure that the shaft geometry will satisfy the Abstract—Human consumption of the Earth's resources increases material strength requirements and shaft-supported element the need for a sustainable development as an important ecological, requirements. Stress analysis at specific points depends on the social, and economic theme. Re-engineering of machine tools, in local geometry, while slope and deflection analysis relies on terms of design and failure analysis, is defined as steps performed on the overall dimensions of the shaft [1]-[4]. Stresses an obsolete machine to return it to a new machine with the warranty that matches the customer requirement. To understand the future concentrate in shaft shoulders and key ways and depend on the fatigue behavior of the used machine components, it is important to local dimensions [2]. Shafts mostly work under the influence investigate the possible causes of machine parts failure through of fluctuated loads or combined torsion and bending loads. If a design, surface, and material inspections. In this study, the failure shaft supports a static load, the bending stresses are fully modes of the shaft of the rotary draw bending machine are inspected. reversed and the torsion is steady [1], [5]. Even well-designed Furthermore, stress and deflection analysis of the shaft subjected to shafts, when subjected to repeated loads or overloads, will combined torsion and bending loads are carried out by an analytical method and compared with a finite element analysis method. -
Fatigue Failure Analysis of a Speed Reduction Shaft
metals Article Fatigue Failure Analysis of a Speed Reduction Shaft Rodrigo S. Miranda 1 , Clarissa Cruz 2, Noé Cheung 3,* and Adilto P. A. Cunha 1 1 Department of Mechanical Engineering, State University of Maranhão-UEMA, São Luís 65055-310, MA, Brazil; [email protected] (R.S.M.); [email protected] (A.P.A.C.) 2 Department of Production Engineering, Federal University of Ouro Preto-UFOP, João Monlevade 35931-008, MG, Brazil; [email protected] 3 Department of Manufacturing and Materials Engineering, State University of Campinas-UNICAMP, Campinas 13083-860, SP, Brazil * Correspondence: [email protected]; Tel.: +55-19-3521-3488 Abstract: The mining industry sector is notable for the severe service loads and varied environmental conditions that it imposes on its equipment and mechanical systems. It has become essential to identify the causes of failures and use the information to avoid similar failures and improve projects. In this paper, a study on shaft failure in a speed reduction box was carried out. A section of a fractured shaft made of hardened austempered steel was analyzed to determine the cause of the break. Fractography was performed to characterize the failure mode on the fracture surface. The microstructural analysis and hardness profile revealed that the shaft was inadequately heat treated, resulting in low resistance microstructures and the development of a thin layer of bainite at the shaft edge. Large amounts of inclusions were found in the fracture region, and the tensile tests revealed that the material had an elongation below the specification. The analyses showed that the combination of factors of a large amount of inclusions present in the low resistance banded structure, and the presence of concentrated pores in that same region, acted in a synergistic way to decrease the Citation: Miranda, R.S.; Cruz, C.; fatigue resistance and fatigue life of the shaft material. -
Sucker Rod Failure Analysis a Special Report from Norris
Sucker Rod Failure Analysis A Special Report from Norris A NORRIS A ______ D O V E R ) COMPANY A NORRIS A DOVER) COMPANY Failure Mechanisms........................................................ 1 Design and Operating Failures ....................................... 5 Mechanical Failures ........................................................ 8 Bent Rod Failures ............................................................ 8 Surface Damage Failures ............................................... 9 Connection Failures ........................................................ 10 Corrosion-fatigue Failures................................................ 14 Acid Corrosion ....................................................... 15 Chloride Corrosion ............................................... 16 CO2 Corrosion ...................................................... 16 Dissimilar Metals Corrosion .................................. 17 H2S Corrosion ...................................................... 17 Microbiologically Influenced Corrosion (MIC) ....... 18 Acid Producing Bacteria ............................. 18 Sulfate Reducer Bacteria ........................... 19 Oxygen (02) Enhanced Corrosion ........................ 19 Stray Current Corrosion ....................................... 20 Under-Deposit Corrosion....................................... 20 Manufacturing Defects ..................................................... 20 Failure Analysis Request Form ........................................ 23 2 © 2000-2007 Norris/A Dover Company -
Air Transport Services Group, Inc. Form 10-K Annual Report Filed
SECURITIES AND EXCHANGE COMMISSION FORM 10-K Annual report pursuant to section 13 and 15(d) Filing Date: 2019-03-01 | Period of Report: 2018-12-31 SEC Accession No. 0000894081-19-000040 (HTML Version on secdatabase.com) FILER Air Transport Services Group, Inc. Mailing Address Business Address 145 HUNTER DR 145 HUNTER DR CIK:894081| IRS No.: 261631624 | State of Incorp.:DE | Fiscal Year End: 1231 WILMINGTON OH 45177 WILMINGTON OH 45177 Type: 10-K | Act: 34 | File No.: 000-50368 | Film No.: 19650731 937-382-5591 SIC: 4513 Air courier services Copyright © 2019 www.secdatabase.com. All Rights Reserved. Please Consider the Environment Before Printing This Document UNITED STATES SECURITIES AND EXCHANGE COMMISSION Washington, D.C. 20549 ________________________________________________________________ FORM 10-K ANNUAL REPORT PURSUANT TO SECTION 13 OR 15(D) OF THE SECURITIES EXCHANGE ACT OF 1934 For the fiscal year ended December 31, 2018 Commission file number 000-50368 ________________________________________________________________ (Exact name of registrant as specified in its charter) ________________________________________________________________ Delaware 26-1631624 (State of Incorporation) (I.R.S. Employer Identification No.) 145 Hunter Drive, Wilmington, OH 45177 (Address of principal executive offices) 937-382-5591 (Registrant’s telephone number, including area code) ________________________________________________________________ Securities registered pursuant to Section 12(b) of the Act: Common Stock, Par Value $.01 per share (Title of class) Name of each exchange on which registered: NASDAQ Stock Market LLC Securities registered pursuant to Section 12(g) of the Act: None ________________________________________________________________ Indicate by check mark if the registrant is a well-known seasoned issuer, as defined in Rule 405 of the Securities Act. -
Booklet No. 14 Failure Mode and Effects Analysis FMEA
Quality Management in the Bosch Group 14. Failure Mode and Effects Analysis FMEA Failure Mode and Effects Analysis (FMEA) Table of contents 1. Introduction 3 1.1. Aims 3 1.2. History 3 1.3. Benefits 3 1.4. Success factors 4 1.5. Legal aspects of the FMEA 5 2. Basics 6 2.1. Product FMEA 6 2.2. Process FMEA 6 2.3. Trigger and timing of the FMEA 6 2.4. FMEA team 7 2.5. FMEA work plan 8 2.6. Systematic preparation 9 2.6.1. Definition of tasks 9 2.6.2. Preparation for an FMEA meeting 11 2.6.3. Special Characteristics 12 2.6.4. Prioritizing the scope of observation 12 2.7. Cooperation with externals 12 2.7.1. Joint FMEA with customers 13 2.7.2. FMEA presentation to the customer 13 2.7.3. Cooperation with suppliers 13 2.7.4. Cooperation with external service providers 14 3. Creation and actualization of an FMEA 15 3.1. Structural analysis 15 3.1.1. Structure of the Product FMEA 15 3.1.2. Structure of the Process FMEA 16 3.2. Functional analysis 18 3.2.1. Requirements 18 3.2.2. Functions 19 3.2.3. Function net 22 3.3. Failure analysis 25 3.3.1. Failures/malfunctions 25 3.3.2. Failure effects and failure modes 27 3.4. Action analysis 29 3.4.1. Severity (S) 29 3.4.2. Probability of occurrence (O) 29 3.4.3. Probability of detection (D) 29 3.4.4. -
Failure Modes, Effects and Criticality Analysis for Wind Turbines Considering Climatic Regions and Comparing Geared and Direct Drive Wind Turbines
energies Article Failure Modes, Effects and Criticality Analysis for Wind Turbines Considering Climatic Regions and Comparing Geared and Direct Drive Wind Turbines Samet Ozturk 1, Vasilis Fthenakis 1,* and Stefan Faulstich 2 ID 1 Earth and Environmental Engineering Department, Columbia University, 116th St & Broadway, New York, NY 10027, USA; [email protected] 2 Fraunhofer Institute for Energy Economics and Energy System Technology—IEE, Königstor 59, 34119 Kassel, Germany; [email protected] * Correspondence: [email protected]; Tel: +1-212-854-8885 Received: 30 July 2018; Accepted: 27 August 2018; Published: 3 September 2018 Abstract: The wind industry is looking for ways to accurately predict reliability and availability of newly installed wind turbines. Failure modes, effects and criticality analysis (FMECA) is a technique utilized to determine the critical subsystems of wind turbines. There are several studies in the literature which have applied FMECA to wind turbines, but no studies so far have used it considering different weather conditions or climatic regions. Furthermore, different wind turbine design types have been analyzed applying FMECA either distinctively or combined, but no study so far has compared the FMECA results for geared and direct-drive wind turbines. We propose to fill these gaps by using Koppen-Geiger climatic regions and two different turbine models of direct-drive and geared-drive concepts. A case study is applied on German wind farms utilizing the Wind Measurement & Evaluation Programme (WMEP) database which contains wind turbine failure data collected between 1989 and 2008. This proposed methodology increases the accuracy of reliability and availability predictions and compares different wind turbine design types and eliminates underestimation of impacts of different weather conditions. -
Sucker Rod Failure Analysis SUCKER ROD FAILURE ANALYSIS
A SPECIAL REPORT FROM NORRIS Sucker Rod Failure Analysis SUCKER ROD FAILURE ANALYSIS Table of Contents Failure Mechanisms 3 Design and Operating Failures 6 Mechanical Failures 9 Bent Rod Failures 9 Surface Damage Failures 10 Connection Failures 11 Corrosion-Fatigue Failures 16 Acid Corrosion 16 Chloride Corrosion 17 CO2 Corrosion 17 Dissimilar Metals Corrosion 17 H2S Corrosion 19 Microbiologically Influenced Corrosion (MIC) 18 Acid-Producing Bacteria (APB) 18 Sulfate Reducer Bacteria (SRB) 18 Oxygen-Enhanced Corrosion 19 Stray Current Corrosion 19 Under-deposit Corrosion 19 Manufacturing Defects 20 Mill Defects 20 Forging Defects 20 Processing Defects 21 2 SUCKER ROD FAILURE ANALYSIS Root Cause Failure Analysis Root Cause Failure Analysis (RCFA) is Essential for Failure Frequency Reduction in Wells with Artificial Lift. Most failures associated with the sucker rod form of problem(s), recording the “real” root cause of each failure, artificial lifted wells using the sucker rod lift method can be implementing the appropriate change(s), and preventing attributed to one of three primary downhole components— future failures from occurring. This process is central to subsurface pump, sucker rod string or tubing string. All of overall cost-effective asset management. For the purpose these components is defined as any catastrophic event of this special report, we will deal only with sucker rod requiring servicing personnel to pull or change-out one or string related failures. more of these components. Cost-effective failure management begins with prevention, By this definition, the failure frequency rate is the total and the time to stop the next failure is now—prior to the number of component failures occurring per well, per year next incident! Simply fishing, hanging the well on after a in a producing field.