Historic Scotland Refurbishment Case Study 1
Total Page:16
File Type:pdf, Size:1020Kb
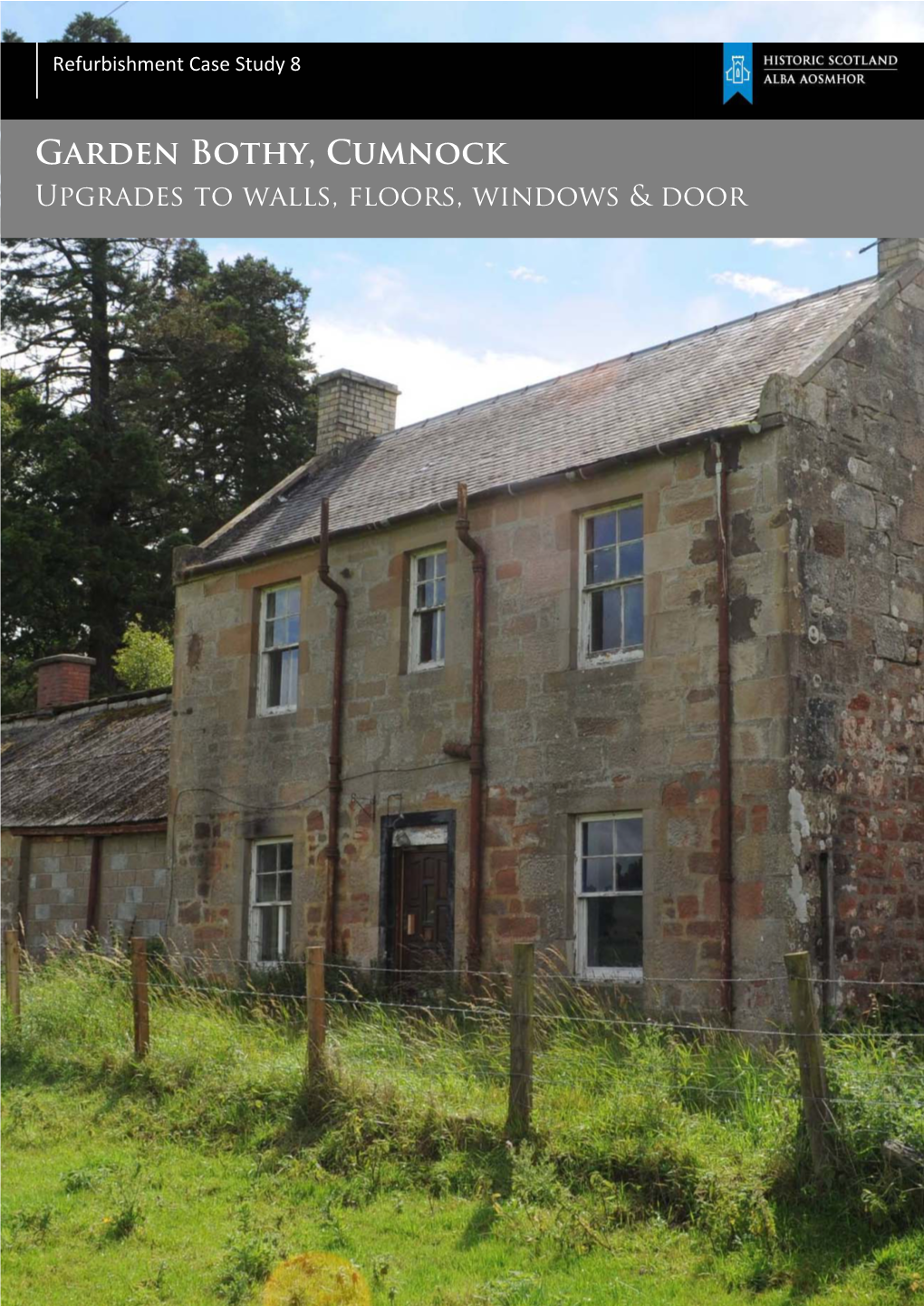
Load more
Recommended publications
-
The Influence of Sewage Sludge Content and Sintering Temperature
materials Article The Influence of Sewage Sludge Content and Sintering Temperature on Selected Properties of Lightweight Expanded Clay Aggregate Jolanta Latosi ´nska 1,* , Maria Zygadło˙ 1 and Przemysław Czapik 2 1 Faculty of Environmental Engineering, Geomatic and Energy Engineering, Kielce University of Technology, Al. Tysi ˛acleciaPa´nstwaPolskiego 7, 25-314 Kielce, Poland; [email protected] 2 Faculty of Civil Engineering and Architecture, Kielce University of Technology, Al. Tysi ˛acleciaPa´nstwa Polskiego 7, 25-314 Kielce, Poland; [email protected] * Correspondence: [email protected]; Tel.: +48-41-34-24-571 Abstract: Wastewater treatment processes produce sewage sludge (SS), which, in line with environ- mental sustainability principles, can be a valuable source of matter in the production of lightweight expanded clay aggregate (LECA). The literature on the influence of SS content and sintering tempera- ture on the properties of LECA is scarce. This paper aims to statistically evaluate the effects of SS content and sintering temperature on LECA physical properties. Total porosity, pore volume, and apparent density were determined with the use of a density analyzer. A helium pycnometer was uti- lized to determine the specific density. Closed porosity was calculated. The test results demonstrated a statistically significant influence of the SS content on the specific density and water absorption of LECA. The sintering temperature had a significant effect on the specific density, apparent density, total porosity, closed porosity, total volume of pores, and water absorption. It was proved that a broad range of the SS content is admissible in the raw material mass for the production of LECA. -
Comparitive Study on Deflouridation of Water Using LECA Balls
Published by : International Journal of Engineering Research & Technology (IJERT) http://www.ijert.org ISSN: 2278-0181 Vol. 8 Issue 05, May-2019 Comparitive Study on Deflouridation of Water using LECA Balls and Natural Bioabsorbents Babitha Peter 1Assistant Professor, Department of Civil Engineering , Ilahia College of Engineering and Technology, Kerala Aysha P Beeran Mohammed Sahal V S 2Department of Civil Engineering , 4Department of Civil Engineering , Ilahia College o f Engineering and Technology, Ilahia College of Engineering and Technology , Kerala Kerala Farha K R Swaleel Falahi 3Department Of Civil Engineering , 5Department of Civil Engineering , Ilahia College of Engineering and Technology, Ilahia College of Engineering and Technology, Kerala Kerala Abstract:- Environmental contamination due to various are affected by fluoride contamination in water. This involves chemicals and its subsequent harmful health effects in obvious about 9000 villages affecting 30 million people. forms in all living creatures including human and animal merits It must be noted that the problem of excess fluoride in serious attention worldwide. Fluoride is an essential micro drinking water is of recent origin in most parts. Digging up of element for human health. shallow aquifers for irrigation has resulted in declining levels Defluoridation refers to method of water treatment that reduces of ground water. As a result, deeper aquifers are used, and the concentration of fluoride in the water. This technique is used for the removal of excess fluoride from the aqueous solution the water in these aquifers contains a higher level of fluoride. using tamarind fruit cover and LECA balls. • To compare the fluoride removal efficiency of Fluoride is often described as a ‘double-edged sword’ as different materials on water inadequate ingestion is associated with dental caries, where as • To study the effect of pH of different materials on excessive intake leads to dental, skeletal and soft tissue fluorosis- fluoride remova l of water which has no cure. -
Effects of Recycled Crushed Light Expanded Clay Aggregate on High Strength Lightweight Concrete
https://doi.org/10.33263/Materials23.311317 ISSN: 2668-5728 https://materials.international Volume 2, Issue 3, Pages 0311-0317 2020 Received: 25.05.2020 Accepted: 11.06.2020 Article Published: 15.06.2020 Effects of Recycled Crushed Light Expanded Clay Aggregate on High Strength Lightweight Concrete Ming Kun Yew 1,*, Ming Chian Yew 1, Jing Han Beh 1 1 Lee Kong Chian Faculty of Engineering & Science, UTAR, Cheras 43000 Kajang, Malaysia * Correspondence: [email protected]; [email protected]; Scopus ID: 36770106800 Abstract: Many researchers are carrying out environmentally-friendly action in the construction field, such as using recycled aggregate for sustainable development. Disposal of light expanded clay aggregate (LECA) waste into the land causes a severe impact on the environment. LECA is one of the construction materials that are broadly used for various applications. LECA has some excellent properties in its due to technical features, eco-friendly and entirely natural product with a low cost, lightweight, hardness and highly resistant to biological, chemical, and physical degradation forces. Recently, lightweight structural concrete by incorporating lightweight aggregate (LWA) is used to compensate heavy loads by reducing the overall self-weight of structure and minimize the size of the foundation simultaneously. In this study, partially replacement of high content light expanded clay aggregate (LECA) (50, 60, 70, 80, and 90%) have been used to achieve the mechanical properties of high strength LWA concrete. In this study, crushed LECA has been used to achieve compressive strength between 20 to 40 MPa with a density ranged between 1700 to 2000 kg/m3. -
Building Future
BUILDING OUR FUTURE with expanded clay EUROPEAN EXPANDED CLAY ASSOCIATIOION Expanded Clay a sustainable industry If expanded clay isn’t a sustainable Lightweight aggregate has been and resource efficient used in construction since Roman times, valued for its combination of low weight construction material, and high strength. The variability of natural then what is? lightweight aggregate remained a challenge for almost 2,000 years until the advent of industrial production processes. Expanded clay lightweight aggregate has been produced since the start of the 20th century in the United States and in Europe production started in the early 1950s. Today, expanded clay is a well-established emissions and there is a commitment to delivering lightweight aggregate suitable for a wide range further CO2 emissions under the EU Emission Trading of applications. It has proven to be a durable Scheme. Using waste that cannot be recycled or and safe material able to withstand different reused as substitutes for fossil fuels not only reduces climates all over Europe: from the Mediterranean fossil fuel consumption and contributes to a true to Scandinavia. circular economy, it also reduces CO2 emissions. The European expanded clay industry is a For every cubic metre of natural and abundant sustainable industry. It is resource efficient clay, up to five cubic metres of expanded and contributes to a competitive low carbon clay is produced. Using expanded clay saves economy. The industry is committed to energy and reduces CO2 emissions in the continuously reducing the impact of production construction and transport sectors. Its low weight and developing the properties and applications means fewer trucks and fewer journeys, thus of the material to improve its sustainability. -
Use of Expanded Clay Aggregate (Eca) in Precast Concrete Segments
USE OF EXPANDED CLAY AGGREGATE (ECA) IN PRECAST CONCRETE SEGMENTS Copyright © 2017 Rivashaa Eco Design Solutions P. LTD. All rights reserved Use Of Expanded Clay Aggregate (ECA) In Precast Concrete Segments: Past years, using Expanded Clay Expanded Clay Aggregate (ECA) Aggregate (ECA) in a precast precast concrete has made an concrete seemed to have greatly incredible impact in construction displaced in-situ concrete and it’s works and this has been now the most commonly used in ascertain by numerous construction, by providing better researches that have been quality, reduced labor and faster conducted. construction. Copyright © 2017 Rivashaa Eco Design Solutions P. LTD. All rights reserved Use Of Expanded Clay Aggregate (ECA) In Precast Concrete Segments: This research is centered on One of the major prides of Expanded Clay Aggregate (ECA) mechanical and physical structural engineers is making precast concrete reduce properties of light-weight use of light weight structural reinforced concrete buildings structural high-strength concrete concrete in their constructions. dead load, without losing the on- using Expanded Clay Aggregate demand compressive strength of (ECA) in precast concrete the material. segments, i.e. partition walls and floors. Copyright © 2017 Rivashaa Eco Design Solutions P. LTD. All rights reserved Use Of Expanded Clay Aggregate (ECA) In Precast Concrete Segments: Using Expanded Clay Aggregate Using Expanded Clay Aggregate Expanded Clay Aggregate (ECA) (ECA) structural concrete results (ECA) facilitates the carrying and precast concrete decreasing in higher safety against installment of precast concrete density and weight produces earthquake and other seismic elements. great changes which enhance hazards. many properties of concrete, both in placement and application. -
LECA) in a Geotechnical View and Its Application on Greenhouse and Greenroof Cultivation
INTERNATIONAL JOURNAL OF GEOLOGY Issue 4, Volume 2, 2008 A Study on Light Expended Clay Aggregate (LECA) in a Geotechnical View and its Application on Greenhouse and Greenroof Cultivation Siamak Boudaghpour, and Shervin Hashemi biodegradable, non combustible and has excellent sound and Abstract— Increasing population in the world increases the thermal insulation properties. demand of housing and it causes destroying pasture lands and This material is an incredibly versatile material, and is jungles immethodically. It also causes soil attrition in every country utilized in an ever-increasing number of applications. of the world. In this way, the demand of making flowerbeds in the In the construction industry, it is used extensively in the inner and outer parts of the building increases. But expending production of lightweight concrete blocks as well as both a method of making these flowerbeds as they need an environment to sound and thermal insulation material, and flue & chimney keep the plant and also not to be harmful for the plant and environment and also they are needed to be light and economical. lining material. According to our studies, LECA has some specific properties LECA used in structural backfill against foundations, which can be apply as a suitable material. In this study, first the retaining walls, bridge abutments etc., can reduce earth LECA and its suitable properties has been introduced in a geological pressure by 75% compared with conventional materials, and and geotechnical view. Then the LECA application on greenhouse also increases stability while reducing settlement and land cultivation has been reviewed and a new method of making green deformation. -
Sintered Calcined Clay As an Alternative Coarse Aggregate for Asphalt Pavement Construction
Open Journal of Civil Engineering, 2015, 5, 281-288 Published Online September 2015 in SciRes. http://www.scirp.org/journal/ojce http://dx.doi.org/10.4236/ojce.2015.53028 Sintered Calcined Clay as an Alternative Coarse Aggregate for Asphalt Pavement Construction Cleudinei Lopes da Silva1, Hidembergue Ordozgoith da Frota2, Consuelo Alves da Frota1 1Department of Civil Engineering, Federal University of Amazonas, Manaus, Brazil 2Department of Physics, Federal University of Amazonas, Manaus, Brazil Email: [email protected] Received 21 May 2015; accepted 11 August 2015; published 14 August 2015 Copyright © 2015 by authors and Scientific Research Publishing Inc. This work is licensed under the Creative Commons Attribution International License (CC BY). http://creativecommons.org/licenses/by/4.0/ Abstract The aim of this study is to search for a substitute for the natural coarse aggregate in various re- gions of the world, such as Amazon-Brazil, where this type of material is lacking. The asphalt binder AC 50/70 is mixed with an aggregate obtained from the sinterization of a calcined clay (SACC) as a possible alternative to coarse aggregate material for the construction of asphalt pavements in tropical zones. The dynamic modulus |E*| of this mixture was measured under strain control mode and in tension control mode. The results are compared with those obtained from AC 50/70 mixed with pebbles, which is currently used as the coarse aggregate in this region. For pavements that work at high temperatures, such as 40˚C, and low frequencies, the mixture with SACC appears to be a viable alternative to coarse aggregate material for the construction of as- phalt pavements in tropical zones. -
Final Report on the Use of Lightweight Aggregate in Flexible Pavements
FINAL REPORT ON THE USE OF LIGHTWEIGHT AGGREGATE IN FLEXIBLE PAVEMENTS by Bob M. Gallaway Research Engineer and William J. Harper Assistant Research Engineer Research Report Number 51-4 (Final) Use of Lightweight Aggregates Research Study Number 2-14-63-51 Sponsored by The Texas Highway Department in cooperation with u. S. Department of Transportation Federal Highway Administration Bureau of Public Roads August, 1967 Texas Transportation Institute Texas A&M University College Station, Texas TABLE OF CONTENTS Page LIST OF TABLES ........................................ iii LIST OF FIGURES ....................................... iv ABSTRACT ............................................ v SUMMARY AND CONCLUSIONS ................................ 1 Sununary 1 Coverstone Applications .............................. 2 Hot-Mix Asphalt Paving Mixtures 3 General Reconunendations 5 INTRODUCATION ......................................... 7 Condition Survey 8 Field Observations 10 REFERENCES AND SELECTED BIBLIOGRAPHY 22 APPENDIX 26 The opinions, findings, and conclusions expressed in this publication are those of the authors and not necessarily those of the Bureau of Public Roads. LIST OF TABLES TABLES I Summary of Lightweight Aggregate Seals and Surface Treatments on Texas Highways (July, 19 6 7) ......•....• 9 II Summary to 1967 Seal Coat Condition Survey, District 18 . 11 Table II, page 2 . 12 -iii- LIST OF FIGURES FIGURE 1. Expanded shale coverstone after three years of service. 13 2. Close-up of surface shown in Figure 1. 13 3. US 80 West of Abilene. Expanded shale coverstone after 5 years of service and 8000 vpd (both directions). 14 4. Close-up taken in the wheel path of pavement shown in Figure 3. 14 5. Expanded shale coverstone on traveled roadway. Crushed limestone on shoulder. 15 6. Color contrast of limestone shoulders and expanded shale on traveled roadway. -
The Manufacture and Uses of Expanded Clay Aggregate
The manufacture and uses of expanded clay aggregate Thursday 15 November 2012 SCI HQ, London Xavier Kestemont, Argex 1 ARGEX expanded clay Manufacture - Location in BE Kruibeke sourcing LWA’s properties & Normative references Typical end uses Concrete LAC/LWAC SCC Argex 1965…. 2 ARGEX expanded clay Manufacture - Source material – EN13055 sourcing LWA’s properties & “lightweight aggregates Normative references Typical end uses manufactured from Concrete LAC/LWAC natural source materials” SCC Specific LWA material = Expanded clay Argex = Argile expansée Argex is made from clay, which is expanded at high temperature to create individual granules, each of which has a hard ceramic shell that surrounds a perfect honeycomb core 3 Clay pit.. factory 4 ARGEX expanded clay Production process Manufacture - sourcing LWA’s properties & Normative references Typical end uses Extraction & Concrete LAC/LWAC clay preparation SCC 10001000 tonstons clayclay // dayday 5 ARGEX expanded clay Manufacture - Expansion – rotary kiln sourcing LWA’s properties & Normative references Typical end uses Concrete LAC/LWAC SCC 7575 mm –– 55 mm ǾǾ–– 11001100 °°CC 6 ARGEX expanded clay Manufacture - Sieving & storage (silo & sourcing outside) LWA’s properties & Normative references Typical end uses Concrete LAC/LWAC SCC 450.000450.000 mm³³ // yearyear 7 ARGEX expanded clay Aggregates / CE Manufacture - sourcing SIZE LOOSE BULK PARTICLE LWA’s properties & Types (d/D - mm) DENSITY DENSITY (ρrd) Normative references (kg/m³) (kg/m³) Typical end uses Normal Rounded AR 0/2-800 -
Physical and Chemical Studies of the Oil Sludge Hydrocarbon Composition and the Prospects for Their Use in the Technology of Expanded Clay Production
News of the Academy of sciences of the Republic of Kazakhstan N E W S OF THE NATIONAL ACADEMY OF SCIENCES OF THE REPUBLIC OF KAZAKHSTAN SERIES CHEMISTRY AND TECHNOLOGY ISSN 2224-5286 https://doi.org/10.32014/2020.2518-1491.77 Volume 5, Number 443 (2020), 28 – 37 UDC 691-405.8 CSCSTI 67.09.35 K.A. Bisenov, R.A. Narmanova, N.O. Appazov Korkyt Ata Kyzylorda University, Kyzylorda, Kazakhstan. E-mail: [email protected], [email protected], [email protected] PHYSICAL AND CHEMICAL STUDIES OF THE OIL SLUDGE HYDROCARBON COMPOSITION AND THE PROSPECTS FOR THEIR USE IN THE TECHNOLOGY OF EXPANDED CLAY PRODUCTION Abstract. The article presents the results of gas chromatographic studies of the oil sludge hydrocarbon composition, physical and chemical and heat-producing properties, which enabled to assess the potential of oil sludge as raw materials, their assortment predisposition and possible manufacturability. It has been established that the main physical and chemical characteristics of the organic part from the averaged samples of oil sludge are similar in properties to raw materials for the production of kerosene-diesel fractions. The expediency of the use of oil sludge and weakly bloating clay materials in the production technology of the popular construction material – expanded clay is substantiated. The results of experimental studies on the development of light and porous heat insulating material by granulation method are presented herein. It is shown that oil sludge from a high viscous state is transferred to a loose conglomerate with a moisture content of 12–15% by co-mixing with finely dispersed sand dune, which ensures uniform distribution when mixed with the basic mass. -
Evaluation of Horticulture Applications of Light Expanded
EVALUATION OF HORTICULTURE APPLICATIONS OF LIGHT EXPANDED CLAY AGGREGATES Except where reference is made to the work of others, the work described in this thesis is my own or was done in collaboration with my advisory committee. This thesis does not include proprietary or classified information. ______________________________ Jeremy Martin Pickens Certificate of Approval: ______________________________ ______________________________ Charles H. Gilliam Jeff L. Sibley, Chair Professor Alumni Professor Horticulture Horticulture ______________________________ ______________________________ Glenn B. Fain John W. Olive Assistant Professor Director Ornamental Horticulture Horticulture Research Center, Mobile, AL ______________________________ Joe F. Pittman Interim Dean Graduate School EVALUATION OF HORTICULTURE APPLICATIONS OF LIGHT EXPANDED CLAY AGGREGATES Jeremy Martin Pickens A Thesis Submitted to the Graduate Faculty of Auburn University in Partial Fulfillment of the Requirements for the Degree of Master of Science Auburn, Alabama May 10, 2008 EVALUATION OF HORTICULTURE APPLICATIONS OF LIGHT EXPANDED CLAY AGGREGATES Jeremy Martin Pickens Permission is granted to Auburn University to make copies of this thesis at its discretion, upon request of individuals or institutions and at their expense. The author reserves all publication rights. ________________________ Signature of Author ________________________ Date of Graduation iii VITA Jeremy Martin Pickens, brother of John Pickens, and son of Larry and Ramona Pickens of Grand Bay, AL, was born on February 4, 1983 in Mobile Alabama. He graduated in May 2001 from Mobile Christian School in Mobile, AL. Upon entering Auburn University Fall Semester of 2001, he enrolled in the College of Agriculture and earned a Bachelor of Science degree in Horticulture in December 2005. Jeremy continued his time at Auburn University to pursue a Master’s Degree in Horticulture. -
Water Runoff Properties for Expanded Clay LWA in Green Roofs
Water Runoff Properties for Expanded Clay LWA in Green Roofs Anders Olof Eriksson Geotechnics and Geohazards Submission date: June 2013 Supervisor: Arnfinn Emdal, BAT Norwegian University of Science and Technology Department of Civil and Transport Engineering NORWEGIAN UNIVERSITY OF SCIENCE AND TECHNOLOGY DEPARTMENT OF CIVIL AND TRANSPORT ENGINEERING Report Title: Date: 07.06.2013 Number of pages (incl. appendices): 96 Water Runoff Properties for Expanded Clay LWA in Green Roofs Master Thesis X Project Work Name: Anders Eriksson Professor in charge/supervisor: Arnfinn Emdal Other external professional contacts/supervisors: Arnstein Watn and Jan Ove Busklein Abstract: A lightweight aggregate (LWA) is a material that has a lower density than rock aggregates. There are many civil engineering application possibilities for LWA. A potential field of application for expanded clay LWA is as a storm water retaining layer in green roofs. In order to design reliable structures of green roofs, more knowledge about the characteristics of the material is needed. The purpose of this master thesis was to test if the software SEEP/W is an appropriate tool for simulation of water runoff from a green roof, designed with expanded clay LWA. The numerical modeling was not performed for all types of expanded clay LWA, but on crushed Leca® 4-10mm and round 10- 20mm alone. To test if SEEP/W is advisable tool for simulating water flow in expanded clay LWA, a back calculation of a laboratory experiment was done. The purpose of back calculating the experiment is to calibrate a numerical model and then use it for a full scale ideal roof.