Chapter 6 Structural Steel Contents
Total Page:16
File Type:pdf, Size:1020Kb
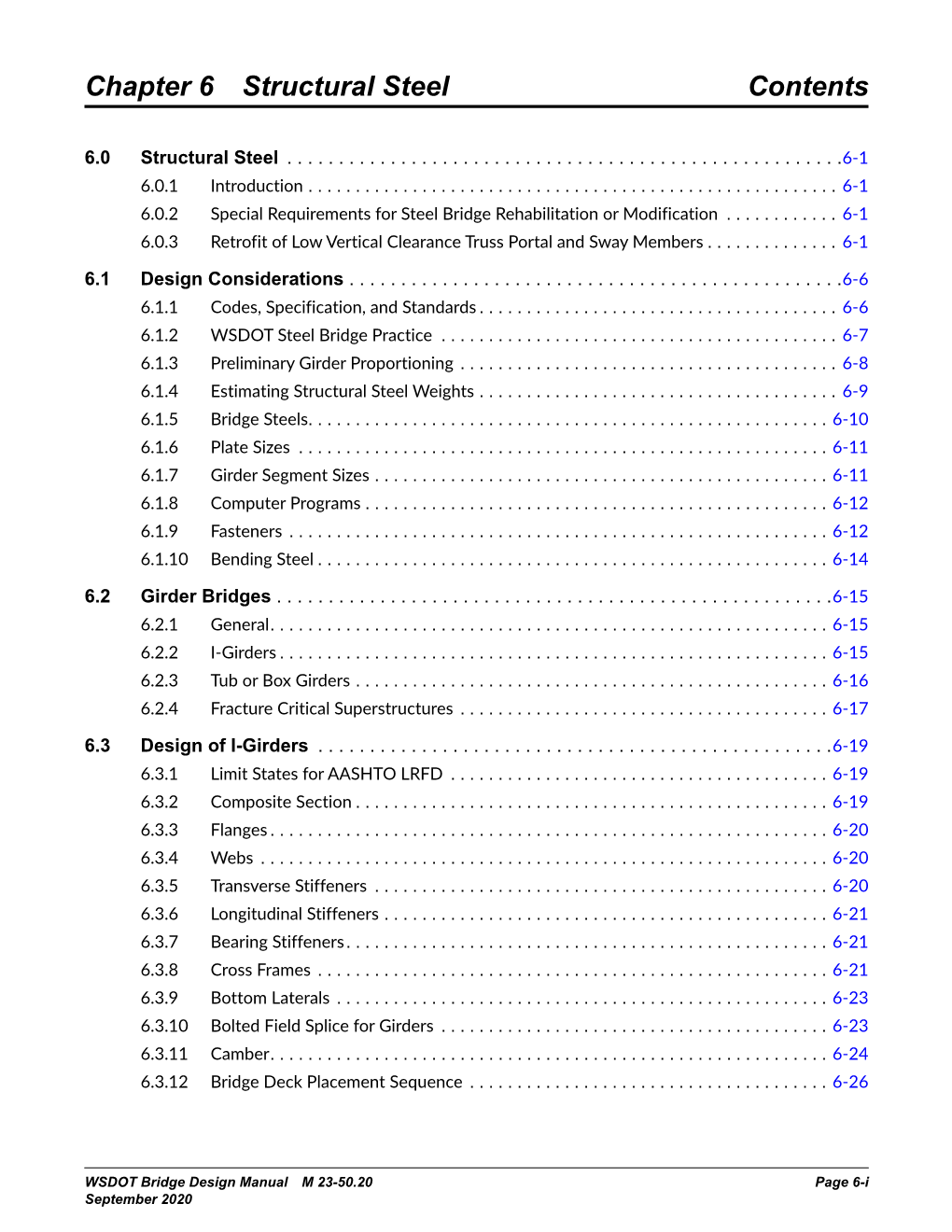
Load more
Recommended publications
-
Bridges and Applications Bridges and Applications Bridges and Applications Arch Bridges
10/23/2014 Bridges and Applications Bridges and Applications • Bridges are used to span across distances that are difficult to otherwise pass through. • Rivers • Deep gorges • Other roadways Bridges and Applications Arch Bridges • There are four basic types of bridges – Arch – Beam – Suspension – Cable‐stayed • Each type has different design and is therefore better suited to different applications 1 10/23/2014 Arch Bridges Arch Bridges • Instead of pushing straight down, the weight of an arch bridge is carried outward along the curve of the arch to the supports at each end. Abutments, carry • These supports, called the abutments, carry the load the load and keep the ends of the bridge from spreading outward. and keep the ends of the bridge from spreading outward Arch Bridges Arch Bridges • When supporting its own weight and the • Today, materials like steel and pre‐stressed weight of crossing traffic, every part of the concrete have made it possible to build longer arch is under compression. and more elegant arches. • For this reason, arch bridges must be made of materials that are strong under compression. New River Gorge, – Rock West Virginia. – Concrete 2 10/23/2014 Arch Bridges Arch Bridges • Usually arch bridges employ vertical supports • Typically, arch bridges span between 200 and called spandrels to distribute the weight of 800 feet. the roadway to the arch below. Arch Bridges One of the most revolutionary arch bridges in recent years is the Natchez Trace Parkway Bridge in Franklin, Tennessee, which was opened to traffic in 1994. It's the first American arch bridge to be constructed from segments of precast concrete, a highly economical material. -
Over Jones Falls. This Bridge Was Originally No
The same eastbound movement from Rockland crosses Bridge 1.19 (miles west of Hollins) over Jones Falls. This bridge was originally no. 1 on the Green Spring Branch in the Northern Central numbering scheme. PHOTO BY MARTIN K VAN HORN, MARCH 1961 /COLLECTION OF ROBERT L. WILLIAMS. On October 21, 1959, the Interstate Commerce maximum extent. William Gill, later involved in the Commission gave notice in its Finance Docket No. streetcar museum at Lake Roland, worked on the 20678 that the Green Spring track west of Rockland scrapping of the upper branch and said his boss kept would be abandoned on December 18, 1959. This did saying; "Where's all the steel?" Another Baltimore not really affect any operations on the Green Spring railfan, Mark Topper, worked for Phillips on the Branch. Infrequently, a locomotive and a boxcar would removal of the bridge over Park Heights Avenue as a continue to make the trip from Hollins to the Rockland teenager for a summer job. By the autumn of 1960, Team Track and return. the track through the valley was just a sad but fond No train was dispatched to pull the rail from the memory. Green Spring Valley. The steel was sold in place to the The operation between Hollins and Rockland con- scrapper, the Phillips Construction Company of tinued for another 11/2 years and then just faded away. Timonium, and their crews worked from trucks on ad- So far as is known, no formal abandonment procedure jacent roads. Apparently, Phillips based their bid for was carried out, and no permission to abandon was the job on old charts that showed the trackage at its ' obtained. -
ABSTRACT the Pdblications of the Marvel Comics Group Warrant Serious Consideration As .A Legitimate Narrative Enterprise
DOCU§ENT RESUME ED 190 980 CS 005 088 AOTHOR Palumbo, Don'ald TITLE The use of, Comics as an Approach to Introducing the Techniques and Terms of Narrative to Novice Readers. PUB DATE Oct 79 NOTE 41p.: Paper' presented at the Annual Meeting of the Popular Culture Association in the South oth, Louisville, KY, October 18-20, 19791. EDFS PRICE MF01/PCO2 Plus Postage." DESCRIPTORS Adolescent Literature:,*Comics (Publications) : *Critical Aeading: *English Instruction: Fiction: *Literary Criticism: *Literary Devices: *Narration: Secondary, Educition: Teaching Methods ABSTRACT The pdblications of the Marvel Comics Group warrant serious consIderation as .a legitimate narrative enterprise. While it is obvious. that these comic books can be used in the classroom as a source of reading material, it is tot so obvious that these comic books, with great economy, simplicity, and narrative density, can be used to further introduce novice readers to the techniques found in narrative and to the terms employed in the study and discussion of a narrative. The output of the Marvel Conics Group in particular is literate, is both narratively and pbSlosophically sophisticated, and is ethically and morally responsible. Some of the narrative tecbntques found in the stories, such as the Spider-Man episodes, include foreshadowing, a dramatic fiction narrator, flashback, irony, symbolism, metaphor, Biblical and historical allusions, and mythological allusions.4MKM1 4 4 *********************************************************************** * Reproductions supplied by EDRS are the best that can be made * * from the original document. * *********************************************************************** ) U SOEPANTMENTO, HEALD.. TOUCATiONaWELFARE NATIONAL INSTITUTE CIF 4 EDUCATION THIS DOCUMENT was BEEN N ENO°. DOCEO EXACTLY AS .ReCeIVED FROM Donald Palumbo THE PE aSON OR ORGANIZATIONORIGuN- ATING T POINTS VIEW OR OPINIONS Department of English STATED 60 NOT NECESSARILY REPRf SENT OFFICIAL NATIONAL INSTITUTE OF O Northern Michigan University EDUCATION POSITION OR POLICY CO Marquette, MI. -
BRIDGE DETAILING GUIDE August 2018
BRIDGE DETAILING GUIDE August 2018 BRIDGE DIVISION Table of Contents Chapter 1: Overview Section 1 — Overview .......................................................................................................... 1-2 Chapter 2: Department Specific Information Section 1 — Introduction ...................................................................................................... 2-2 Section 2 — Bridge Related Glossary .................................................................................. 2-3 Section 3 — Bridge Standards ............................................................................................ 2-10 Section 4 — Map Information ............................................................................................ 2-11 County Map .................................................................................................................................... 2-11 District and Headquarters Map ....................................................................................................... 2-12 County/Distrcit Listing ................................................................................................................... 2-13 Section 5 — Information Sheet for Structural Design ........................................................ 2-15 Section 6 — Specification/Special Provision Usage .......................................................... 2-16 Section 7 — Plan Sheet Set ................................................................................................ 2-17 -
Steel Bridge Design Handbook
U.S. Department of Transportation Federal Highway Administration Steel Bridge Design Handbook Design Example 2A: Two-Span Continuous Straight Composite Steel I-Girder Bridge ArchivedPublication No. FHWA-IF-12-052 - Vol. 21 November 2012 Notice This document is disseminated under the sponsorship of the U.S. Department of Transportation in the interest of information exchange. The U.S. Government assumes no liability for use of the information contained in this document. This report does not constitute a standard, specification, or regulation. Quality Assurance Statement The Federal Highway Administration provides high-quality information to serve Government, industry, and the publicArchived in a manner that promotes public understanding. Standards and policies are used to ensure and maximize the quality, objectivity, utility, and integrity of its information. FHWA periodically reviews quality issues and adjusts its programs and processes to ensure continuous quality improvement. Steel Bridge Design Handbook Design Example 2A: Two-Span Continuous Straight Composite Steel I-Girder Bridge Publication No. FHWA-IF-12-052 - Vol. 21 November 2012 Archived Archived Technical Report Documentation Page 1. Report No. 2. Government Accession No. 3. Recipient’s Catalog No. FHWA-IF-12-052 - Vol. 21 4. Title and Subtitle 5. Report Date Steel Bridge Design Handbook Design Example 2A: Two-Span November 2012 Continuous Straight Composite Steel I-Girder Bridge 6. Performing Organization Code 7. Author(s) 8. Performing Organization Report No. Karl Barth, Ph.D. (West Virginia University) 9. Performing Organization Name and Address 10. Work Unit No. HDR Engineering, Inc. 11 Stanwix Street 11. Contract or Grant No. Suite 800 Pittsburgh, PA 15222 12. -
Design Example: Two-Span Continuous Straight Wide-Flange
U.S. Department of Transportation Federal Highway Administration Steel Bridge Design Handbook Design Example 2B: Two-Span Continuous Straight Composite Steel Wide-Flange Beam Bridge ArchivedPublication No. FHWA-IF-12-052 - Vol. 22 November 2012 Notice This document is disseminated under the sponsorship of the U.S. Department of Transportation in the interest of information exchange. The U.S. Government assumes no liability for use of the information contained in this document. This report does not constitute a standard, specification, or regulation. Quality Assurance Statement The Federal Highway Administration provides high-quality information to serve Government, industry, and the publicArchived in a manner that promotes public understanding. Standards and policies are used to ensure and maximize the quality, objectivity, utility, and integrity of its information. FHWA periodically reviews quality issues and adjusts its programs and processes to ensure continuous quality improvement. Steel Bridge Design Handbook Design Example 2B: Two-Span Continuous Straight Composite Steel Wide-Flange Beam Bridge Publication No. FHWA-IF-12-052 - Vol. 22 November 2012 Archived Archived Technical Report Documentation Page 1. Report No. 2. Government Accession No. 3. Recipient’s Catalog No. FHWA-IF-12-052 - Vol. 22 4. Title and Subtitle 5. Report Date Steel Bridge Design Handbook Design Example 2B: Two-Span November 2012 Continuous Straight Composite Steel Wide-Flange Beam Bridge 6. Performing Organization Code 7. Author(s) 8. Performing Organization Report No. Karl Barth, Ph.D. (West Virginia University) 9. Performing Organization Name and Address 10. Work Unit No. HDR Engineering, Inc. 11 Stanwix Street 11. Contract or Grant No. Suite 800 Pittsburgh, PA 15222 12. -
Truss Bridges
2009 Bridges and Structures Outline • Introduction of Project Organizers and Program o Overall Concept of the half day o Images of Bridges in NH, ME and MA that are examples of the 5 Bridge Designs Beam Bridge Arch Bridge Truss Bridge Suspension Bridge Cable-Stayed Bridge o Images of existing bridges other students / groups have done • Call off participants 1 through 5 o Creating 5 Groups (1 Group for each Bridge Design which creates 4 individuals per Bridge Design.) If more than 20 individuals, then count 1 thru 7 or 8 to create two or three more groups. There will then be 2 of the same bridge types for some of the 5 Bridge Designs. • Package of information for Groups o Groups to review material (Bridge to be wide enough to accept bricks) o Groups to discuss their Bridge o Groups to draw out their Bridge Design o Groups to divide into two sub-groups Cutting Assembly • Presentation of Bridges by Groups (short narrative as to-) o Type of Bridge o Design solution • Test of Weight that each bridge can handle o Groups document their thoughts on their Bridge • Awards / Overview of how and why bridges worked / did not work Materials: Balsa Wood Package for each Bridge Type Group 3’ long sticks maximum String / rope, Glue (Sobo,) Exacto knives, packing tape Other: Bricks or other items for weight Scale for measuring weight units Camera to document before, during and after bridge testing Two sawhorses for bridge weight test American Institute of Architects New Hampshire Chapter Schedule • Introduction of Team Members and Program: 10 minutes o Overall Concept of the Day: 10 minutes o Images of Bridges in NH, ME and MA that are examples of the 5 Bridge Designs 4 minutes Beam Bridge Arch Bridge Truss Bridge Suspension Bridge Cable-Stayed Bridge o Images of existing bridges other students / groups have done 4 minutes • Call off participants 1 through 5 8 minutes o Creating 5 Groups (1 Group for each Bridge Design which creates 4 individuals per Bridge Design.) If more than 20 individuals, then count 1 thru 7 or 8 to create two or three more groups. -
G 13.1 Guidelines for Steel Girder Bridge Analysis.Pdf
G13.1 Guidelines for Steel Girder Bridge Analysis 2nd Edition American Association of State Highway Transportation Officials National Steel Bridge Alliance AASHTO/NSBA Steel Bridge Collaboration Copyright © 2014 by the AASHTO/NSBA Steel Bridge Collaboration All rights reserved. ii G13.1 Guidelines for Steel Girder Bridge Analysis PREFACE This document is a standard developed by the AASHTO/NSBA Steel Bridge Collaboration. The primary goal of the Collaboration is to achieve steel bridge design and construction of the highest quality and value through standardization of the design, fabrication, and erection processes. Each standard represents the consensus of a diverse group of professionals. It is intended that Owners adopt and implement Collaboration standards in their entirety to facilitate the achievement of standardization. It is understood, however, that local statutes or preferences may prevent full adoption of the document. In such cases Owners should adopt these documents with the exceptions they feel are necessary. Cover graphics courtesy of HDR Engineering. DISCLAIMER The information presented in this publication has been prepared in accordance with recognized engineering principles and is for general information only. While it is believed to be accurate, this information should not be used or relied upon for any specific application without competent professional examination and verification of its accuracy, suitability, and applicability by a licensed professional engineer, designer, or architect. The publication of the material contained herein is not intended as a representation or warranty of the part of the American Association of State Highway and Transportation Officials (AASHTO) or the National Steel Bridge Alliance (NSBA) or of any other person named herein, that this information is suitable for any general or particular use or of freedom from infringement of any patent or patents. -
Lesson Plan – Primary Pensacola Bay Bridge Replacement Project Goes to School Program 2017/18 Primary School Edition
PENSACOLA BAY BRIDGE REPLACEMENT PROJECT GoesGoes toto School!School! Gumdrop Bridge Lesson Plan – Primary Pensacola Bay Bridge Replacement Project Goes to School Program 2017/18 Primary School Edition Any teacher, school, or school district may reproduce this for classroom use without permission. This work may not be sold for profit. Concept by Pensacola Bay Bridge Specialty Outreach Team Version 1804 PENSACOLA BAY BRIDGE REPLACEMENT PROJECT Gumdrop Bridge Lesson Plan ELEMENTARY GRADE LEVELS Introduction: As an early introduction to architecture and engineering elementary school students may build a gumdrop bridge. Making a gumdrop bridge that is well designed means students using simple geometric shapes along with flexible joints, can create a structure that is deceptively strong and will not collapse under pressure. One bridge design that is common employs a pattern of squares and triangles that repeats. However, students are allowed to experiment to find the building strategy that suits their aesthetic preferences and class requirements. Students will be encouraged during the exercise to: • Demonstrate what types forces influence a bridge’s design • Design and build a model bridge that reaches the largest span bearing in mind the given constraints • Design and build a model that is able to hold the maximum amount of weight under given constraints. This lesson plan is meant to serve as a resource for teachers. Specifically, you will find supplemental classroom materials (both in-class worksheets, videos and student activity sheets) that are engaging for students and easy for you to implement, as well as applicable and relevant to the benefit of the new Pensacola Bay Bridge. -
Impact of Overhang Construction on Girder Design November 2009; Revised May 2010 6
Technical Report Documentation Page 1. Report No. 2. Government 3. Recipient’s Catalog No. FHWA/TX-10/0-5706-1 Accession No. 4. Title and Subtitle 5. Report Date Impact of Overhang Construction on Girder Design November 2009; Revised May 2010 6. Performing Organization Code 7. Author(s) 8. Performing Organization Report No. Seongyeong Yang, Todd Helwig, Rich Klingner, Michael 0-5706 Engelhardt, and Jeremiah Fasl 9. Performing Organization Name and Address 10. Work Unit No. (TRAIS) Center for Transportation Research 11. Contract or Grant No. The University of Texas at Austin 0-5706-1 1616 Guadalupe, Suite 4.202 Austin, Texas 78701-1255 12. Sponsoring Agency Name and Address 13. Type of Report and Period Covered Texas Department of Transportation Technical Report Research and Technology Implementation Office September 2006–August 2009 P.O. Box 5080 Austin, TX 78763-5080 14. Sponsoring Agency Code 15. Supplementary Notes Project performed in cooperation with the Texas Department of Transportation and the Federal Highway Administration. 16. Abstract Economical constraints on the design of bridges usually necessitate the use of as few girders as possible across the bridge width. The girders are typically uniformly spaced transversely with the deck extending past the fascia girders, thereby resulting in an overhang. While designers commonly employ rules of thumb with regard to the geometry of the overhang, these rules of thumb generally address only the deck in-service strength and deflection requirements, and the effect due to construction load is not considered. In particular, the impact of the overhang on fascia girder behavior during construction is not well understood. -
Wisdot Bridge Manual Chapter 24 – Steel Girder Structures
WisDOT Bridge Manual Chapter 24 – Steel Girder Structures Table of Contents 24.1 Introduction ...................................................................................................................... 5 24.1.1 Types of Steel Girder Structures ............................................................................... 5 24.1.2 Structural Action of Steel Girder Structures .............................................................. 5 24.1.3 Fundamental Concepts of Steel I-Girders ................................................................. 5 24.2 Materials ........................................................................................................................ 11 24.2.1 Bars and Plates ...................................................................................................... 12 24.2.2 Rolled Sections ....................................................................................................... 12 24.2.3 Threaded Fasteners ............................................................................................... 12 24.2.3.1 Bolted Connections ......................................................................................... 13 24.2.4 Quantity Determination ........................................................................................... 14 24.3 Design Specification and Data ....................................................................................... 15 24.3.1 Specifications ........................................................................................................ -
Justice League: Origins
JUSTICE LEAGUE: ORIGINS Written by Chad Handley [email protected] EXT. PARK - DAY An idyllic American park from our Rockwellian past. A pick- up truck pulls up onto a nearby gravel lot. INT. PICK-UP TRUCK - DAY MARTHA KENT (30s) stalls the engine. Her young son, CLARK, (7) apprehensively peeks out at the park from just under the window. MARTHA KENT Go on, Clark. Scoot. CLARK Can’t I go with you? MARTHA KENT No, you may not. A woman is entitled to shop on her own once in a blue moon. And it’s high time you made friends your own age. Clark watches a group of bigger, rowdier boys play baseball on a diamond in the park. CLARK They won’t like me. MARTHA KENT How will you know unless you try? Go on. I’ll be back before you know it. EXT. PARK - BASEBALL DIAMOND - MOMENTS LATER Clark watches the other kids play from afar - too scared to approach. He is about to give up when a fly ball plops on the ground at his feet. He stares at it, unsure of what to do. BIG KID 1 (yelling) Yo, kid. Little help? Clark picks up the ball. Unsure he can throw the distance, he hesitates. Rolls the ball over instead. It stops halfway to Big Kid 1, who rolls his eyes, runs over and picks it up. 2. BIG KID 1 (CONT’D) Nice throw. The other kids laugh at him. Humiliated, Clark puts his hands in his pockets and walks away. Big Kid 2 advances on Big Kid 1; takes the ball away from him.