Microwave Waveguide Filter with Broadside Wall Slots Shang, Xiaobang; Lancaster, Michael; Dimov, Stefan
Total Page:16
File Type:pdf, Size:1020Kb
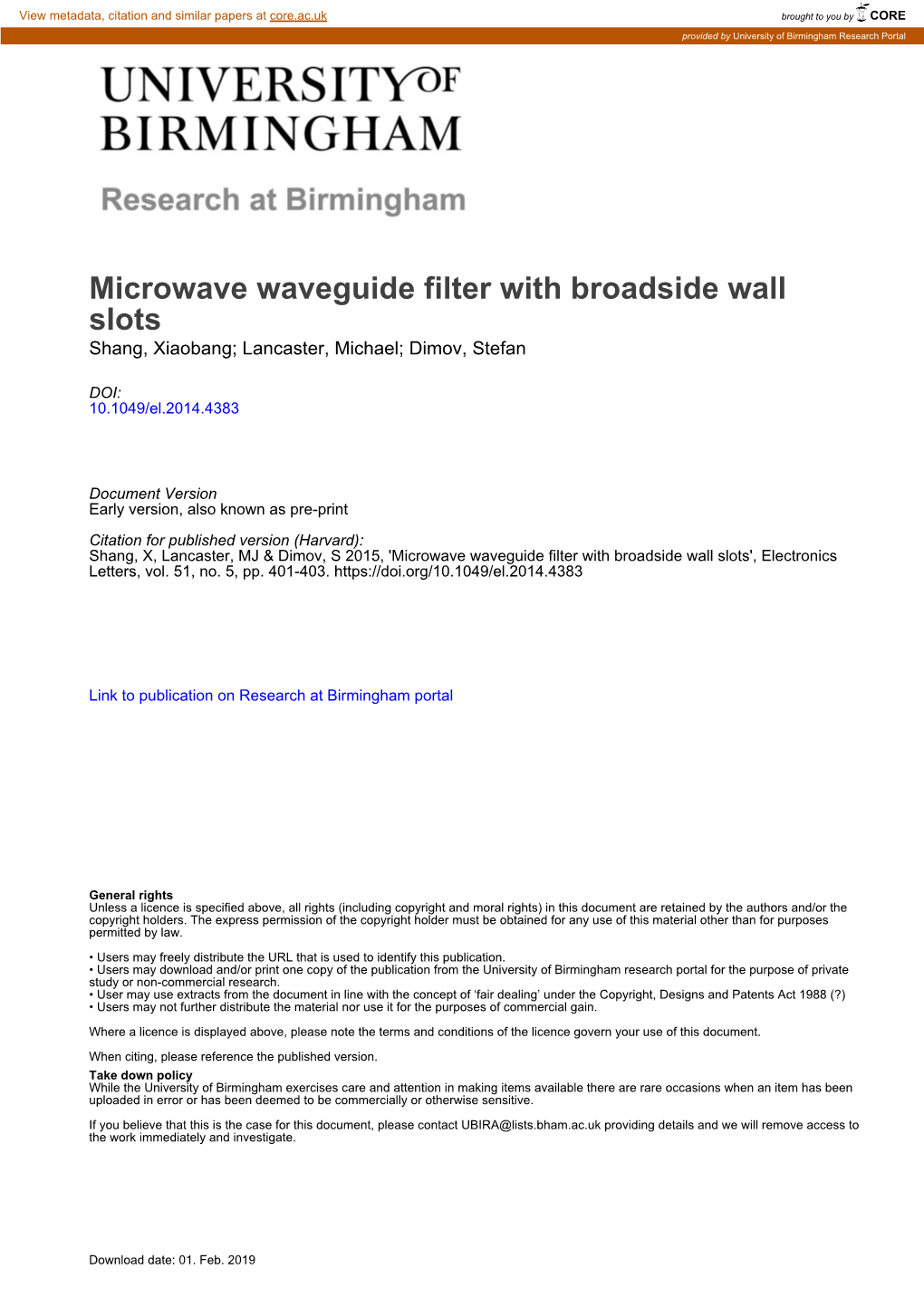
Load more
Recommended publications
-
Design of Microwave Waveguide Filters with Effects of Fabrication Imperfections
FACTA UNIVERSITATIS Series: Electronics and Energetics Vol. 30, No 4, December 2017, pp. 431 - 458 DOI: 10.2298/FUEE1704431M DESIGN OF MICROWAVE WAVEGUIDE FILTERS WITH EFFECTS OF FABRICATION IMPERFECTIONS Marija Mrvić, Snežana Stefanovski Pajović, Milka Potrebić, Dejan Tošić University of Belgrade, School of Electrical Engineering, Belgrade, Serbia Abstract. This paper presents results of a study on a bandpass and bandstop waveguide filter design using printed-circuit discontinuities, representing resonating elements. These inserts may be implemented using relatively simple types of resonators, and the amplitude response may be controlled by tuning the parameters of the resonators. The proper layout of the resonators on the insert may lead to a single or multiple resonant frequencies, using single resonating insert. The inserts may be placed in the E-plane or the H-plane of the standard rectangular waveguide. Various solutions using quarter-wave resonators and split- ring resonators for bandstop filters, and complementary split-ring resonators for bandpass filters are proposed, including multi-band filters and compact filters. They are designed to operate in the X-frequency band and standard rectangular waveguide (WR-90) is used. Besides three dimensional electromagnetic models and equivalent microwave circuits, experimental results are also provided to verify proposed design. Another aspect of the research represents a study of imperfections demonstrated on a bandpass waveguide filter. Fabrication side effects and implementation imperfections are analyzed in details, providing relevant results regarding the most critical parameters affecting filter performance. The analysis is primarily based on software simulations, to shorten and improve design procedure. However, measurement results represent additional contribution to validate the approach and confirm conclusions regarding crucial phenomena affecting filter response. -
A Capacitive Load Double-Ridge Waveguide Evanescent Mode Low-Pass Filter Fanfu Meng , Chao Yuan Guowei Chen
2nd International Conference on Advances in Energy, Environment and Chemical Engineering (AEECE 2016) A Capacitive Load Double-Ridge Waveguide Evanescent Mode Low-pass Filter Fanfu Meng 1, a, Chao Yuan2,b Guowei Chen3,c 1University of Electronic Science and Technology of China, School of Physical Electronics, Chengdu, P. R. China 2University of Electronic Science and Technology of China, School of Physical Electronics, Chengdu, P. R. China 3University of Electronic Science and Technology of China, School of Physical Electronics, Chengdu, P. R. China [email protected], [email protected], [email protected] Keywords: evanescent mode ;capacitive loading ; double-ridge waveguide;filter Abstract. In this paper, a capacitive load double-ridge waveguide evanescent mode low-pass filteris is presented. Combining electromagnetic simulation software to design ,the test results are: The filter return loss<-20dB, insertion loss>-0.6dB, out-band suppression≥40dBc at 5.5GHz and≥20dBc at 13GHz to 26 GHz, parasitic passband appears in multiples of five frequency, improving filter performance greatly. Introduction As we know waveguide,a kind of passive component, has been used widely in the field of Microwave. However, we take it as a transmission line where we are used to pay more attention to its transmission mode with avoiding cutoff state usually. With study on the waveguide cutoff mode deeply found an important application value containing evanescent mode filter which is a significant reflection.Compared traditional filter evanescent mode filter is advantage of smaller size, higher clutter suppression and farther parasitic passband preferred by engineer in practical application. Meanwhile, The capacitive loading effect refined the filter size further increating designing flexibility. -
Modeling and Performance of Microwave and Millimeter-Wave Layered Waveguide Filters
TELKOMNIKA , Vol. 11, No. 7, July 2013, pp. 3523 ~ 3533 e-ISSN: 2087-278X 3523 Modeling and Performance of Microwave and Millimeter-Wave Layered Waveguide Filters Ardavan Rahimian School of Electronic, Electrical and Computer Engineering, University of Birmingham Edgbaston, Birmingham B15 2TT, UK e-mail: [email protected] Abstract This paper presents novel designs, analysis, and performance of 4-pole and 8-pole microwave and millimeter-wave (MMW) waveguide filters for operation at X and Y frequency bands. The waveguide filters have been designed and analyzed based on the RF mode matching and coupled resonators design techniques employing layered technology. Thorough waveguide filters working at X-band and Y-band have been designed, analyzed, fabricated, and also tested along with the analysis of the output characteristics. Accurate designs of RF waveguides along with their filters based on the E-plane filter concept have been carried out with the ability of fitting into the layered technology in high frequency production techniques. The filters demonstrate the appropriateness in order to develop high-performance well-established designs for systems that are intended for the multi-layer microwave, millimeter- and sub-millimeter-waves devices and systems; with the potential employment in radar, satellite, and radio astronomy applications. Keywords : coupled resonator, millimeter-wave device, RF filtering function, RF waveguide filter Copyright © 2013 Universitas Ahmad Dahlan. All rights reserved. 1. Introduction The demands for extending the applications of RF waveguide devices and systems to the increasingly higher RF frequencies up to sub-millimeter-wave frequency bands have been driven by applications including astronomy, radars, and remote sensors [1]. -
Development of Tunable Ka-Band Filters
1 Development of Tunable Ka-band Filters Final Report Ben Lacroix, Stanis Courreges, Yuan Li, Carlos Donado and John Papapolymerou School of Electrical and Computer Engineering Georgia Institute of Technology Atlanta, GA 30332 2 Introduction/Summary Georgia Tech has designed several filters operating in Ka-band. These filters are built on Sapphire and use integrated BST thin films as tuning elements. The fabrication is conducted by nGimat, Inc. Four different approaches are presented in this report. The first filter is a 3-pole filter based on a CPW (Coplanar Waveguide) topology and includes 6 BST capacitors. It is built on a Sapphire substrate and tunes from 29 to 34 GHz (17%). The fractional bandwidth is about 10-12%. Insertion loss of only 2.5 dB is measured when the BST capacitors are biased with 30 V. The second CPW filter consists of two resonators whose physical/electrical lengths can be changed by coupling each resonator with an additional piece of line which acts like a loading capacitor. Therefore, the center frequency can be tuned. The measured tuning appears to be lower than expected. Several issues are discussed. The third filter is also based on a CPW topology, and uses 4 BST capacitors located at the end of the resonators in order to make the filter tune. This design is based on cross-coupled resonators. A trade-off between performance and tuning is discussed. Finally, the fourth part demonstrates the design and implementation of a two-pole, Tunable Folded Waveguide Filter (TFWF) on sapphire and with tuning provided by barium strontium titanate (BST) capacitors. -
Asymmetric Coplanar Waveguide Filter with Defected Ground Structure
Asymmetric Coplanar Waveguide Filter with Defected Ground Structure Xiaoming Li The 54th Research Institute of CETC, Shijiazhuang Hebei 050081, China [email protected] Abstract Proposed novel asymmetric coplanar waveguide filter with defected ground structure, discussed its performance with different dimensions employing conformal mapping techniques and commercial EM software CST Microwave Studio. Several filter circuits were fabricated and measured, the results showed good agreement with analysis, while the structure was proven to have good performance and design flexibilities. 1. Introduction Coplanar waveguide (CPW) is an important planar transmission line proposed by C. P. Wen in 1969 [1]. Profit from the character of single conductor plane, CPW has several advantages, such like easy on fabrication, convenient on connection with other circuit components, etc. Asymmetric coplanar waveguide (ACPW) [2] is a transmission line developed from CPW. As the name implies, ACPW has different slot width in compare with traditional CPW. CPW can be treated as special case of ACPW, and ACPW is supposed to have more design flexibilities. In recent years, ACPW got more and more attentions. Many researchers analyzed ACPW characters and studies on various ACPW applications [3-5]. Defected ground structure (DGS) [6] is a kind of slow wave structure, which is developed from photonic band-gap (PBG) [7-8] structures proposed by Yablonovitch and John S.Strong in 1987. DGS also exhibited distinguished frequency selectivity, while no extra circuit size occupied. This character is always desirable in filter applications. 2. ACPW and Asymmetric Characters The structure and parameters of ACPW is illustrated in Fig. 1. The width of center strip is wc, two slots are ws1 and ws2, respectively, the substrate has dielectric constant εr and thickness h, while the thickness of metal is t. -
Microwave Filter Design: Coupled Line Filter
MICROWAVE FILTER DESIGN: COUPLED LINE FILTER ____________ A Project Presented to the Faculty of California State University, Chico ____________ In Partial Fulfillment of the Requirements for the Degree Master of Science in Electrical and Computer Engineering Electronic Engineering Option ____________ by Michael S. Flanner 2011 Spring 2011 MICROWAVE FILTER DESIGN: COUPLED LINE FILTER A Project by Michael S. Flanner Spring 2011 APPROVED BY THE DEAN OF GRADUATE STUDIES AND VICE PROVOST FOR RESEARCH: Katie Milo, Ed.D. APPROVED BY THE GRADUATE ADVISORY COMMITTEE: _________________________________ _________________________________ Adel A. Ghandakly, Ph.D. Ben-Dau Tseng, Ph.D., Chair Graduate Coordinator _________________________________ Adel A. Ghandakly, Ph.D. PUBLICATION RIGHTS No portion of this project may be reprinted or reproduced in any manner unacceptable to the usual copyright restrictions without the written permission of the author. iii TABLE OF CONTENTS PAGE Publication Rights ...................................................................................................... iii List of Tables.............................................................................................................. v List of Figures............................................................................................................. vi Abstract....................................................................................................................... vii CHAPTER I. Introduction............................................................................................. -
Lowpass Filter Design for Space Applications in Waveguide Technology Using Alternative Topologies
ESCUELA TECNICA´ SUPERIOR DE INGENIER´IA DE TELECOMUNICACION´ UNIVERSIDAD POLITECNICA´ DE CARTAGENA Proyecto Fin de Carrera Lowpass filter design for space applications in waveguide technology using alternative topologies AUTOR: Diego Correas Serrano DIRECTOR: Alejandro Alvarez´ Melc´on CODIRECTOR: Fernando Quesada Pereira Cartagena, Enero 2013 Author Diego Correas Serrano Author's email [email protected] Director Alejandro Alvarez´ Melc´on Director's email [email protected] Co-director Fernando Quesada Pereira Title Lowpass filter design for space applications in waveguide technology using alternative topologies Summary The main goal of this project is to study the possibility of utilizing topologies based on curved surfaces (metallic posts) to realize low pass filters in waveguide technologies, as an alternative to the traditional implementation based on rectangular irises, in order to obtain devices that present a higher multipaction threshold. In the first chapters, the theoretical synthesis techniques utilized are explained. Understanding the synthesis of the different types of filter polynomials and prototype networks is necessary in order to precisely design filters with a predictable frequency response. The commercial package HFSS will be used for the design and verification of the filters, controlling its operation with scripts in order to automate the design process. Degree Ingeniero de Telecomunicaci´on Department Tecnolog´ıas de la Informaci´on y la Comunicacion Submission date January 2013 3 Contents 1 Introduction 13 2 Synthesis of the filter function 17 2.1 Polynomial forms of the transfer and reflection parameters. 17 2.2 Alternating pole method for determination of the denominator poly- nomial E(s) . 21 2.3 Chebyshev filter functions of the first kind . -
Analysis and Design of Microwave Reconfigurable Filters in Esiw Technology
FACULTY OF ENGINEERING AND SUSTAINABLE DEVELOPMENT ANALYSIS AND DESIGN OF MICROWAVE RECONFIGURABLE FILTERS IN ESIW TECHNOLOGY Mar´ıa Trinidad Julia´ Morte 910411-T308 Juan Rafael Sanchez´ Mar´ın 911111-T275 September 2015 Master’s Thesis in Electronics “After climbing a great hill, one only finds that there are many more hills to climb.” Nelson Mandela To my brother, wherever you are you will be always proud of me. JR Acknowledgement We would like to thank to our supervisor Prof. Carmen Bachiller for the continuous sup- port of our Master’s Thesis and related research, for her patience, motivation, and immense knowledge. Her guidance helped us in all the time of research and writing of this thesis. We could not have imagined having a better supervisor. Furthermore, we reserve our biggest thanks to our families for encouraging us in our experience in Gavle.¨ They have been always supporting us throughout writing this thesis and in our life in general. Juanra and Mar´ıa Abstract Microwave filters are essential components in high frequency communication systems. The features required for these devices are increasing due to the increase in frequency, caused by the saturation of the electromagnetic spectrum. Among these features, the need for low cost devices with a reduced mass and volume and the need to integrate them with the current planar technology are highlighted. In addition, it is interested to have reconfigurable devices, that is, they can adjust their frequency response, replacing the need of multiple devices. So far, metallic waveguide filters have been used, but lately Substrate Intregated Waveguide (SIW) technology has appeared, and within this family, the innovative Empty Substrate Integrated Waveguide (ESIW). -
Waveguide Filter Tutorial
Waveguide Filter Tutorial Julius O. Smith III Center for Computer Research in Music and Acoustics (CCRMA) Department of Music, Stanford University, Stanford, California 94305 USA Abstract This tutorial was adapted from the conference paper “Waveguide Filter Tutorial,” by J.O. Smith, Proceedings of the International Computer Music Conference (ICMC-87), pp. 9–16, Champaign-Urbana, 1987, Computer Music Association. Contents 1 Introduction 2 2 Reduction to Standard Forms 2 3 Power-Normalized Waveguide Filters 5 4 Conclusions 6 1 1 Introduction Digital Waveguide Filters (DWF) have proven useful for building computational models of acoustic systems which are both physically meaningful and efficient for digital synthesis. The physical interpretation opens the way to capturing valued aspects of real instruments which have been difficult to obtain by more abstract synthesis techniques. Waveguide filters were derived for the purpose of building reverberators using lossless building blocks [6], but any linear acoustic system can be approximated using waveguide networks. For example, the bore of a wind instrument can be modeled very inexpensively as a digital waveguide [7]. Similarly, a violin string can be modeled as a digital waveguide with a nonlinear coupling to the bow [7]. When the basic model is physically meaningful, it is often obvious how to introduce nonlinearities correctly, thus leading to realistic behaviors far beyond the reach of purely analytical methods. A basic feature of DWF building blocks is the exact physical interpretation of the contained digital signals as traveling pressure waves or velocity waves. A byproduct of this formulation is the availability of signal power defined instantaneously with respect to both space and time. -
X Band Tx Reject Waveguide Bandpass Filter Design for Satellite Communication Systems
X BAND TX REJECT WAVEGUIDE BANDPASS FILTER DESIGN FOR SATELLITE COMMUNICATION SYSTEMS A THESIS SUBMITTED TO THE GRADUATE SCHOOL OF NATURAL AND APPLIED SCIENCES OF MIDDLE EAST TECHNICAL UNIVERSITY BY IREM˙ ÇELEBI˙ IN PARTIAL FULFILLMENT OF THE REQUIREMENTS FOR THE DEGREE OF MASTER OF SCIENCE IN ELECTRICAL AND ELECTRONICS ENGINEERING JANUARY 2018 Approval of the thesis: X BAND TX REJECT WAVEGUIDE BANDPASS FILTER DESIGN FOR SATELLITE COMMUNICATION SYSTEMS submitted by IREM˙ ÇELEBI˙ in partial fulfillment of the requirements for the de- gree of Master of Science in Electrical and Electronics Engineering Department, Middle East Technical University by, Prof. Dr. Gülbin Dural Ünver Dean, Graduate School of Natural and Applied Sciences Prof. Dr. Tolga Çiloglu˘ Head of Department, Electrical and Electronics Engineering Prof. Dr. Seyit Sencer Koç Supervisor, Electrical and Electronics Eng. Dept., METU Examining Committee Members: Prof. Dr. ¸Sim¸sekDemir Electrical and Electronics Engineering Department, METU Prof. Dr. Seyit Sencer Koç Electrical and Electronics Engineering Department, METU Prof. Dr. Özlem Aydın Çivi Electrical and Electronics Engineering Department, METU Assoc. Prof. Dr. Lale Alatan Electrical and Electronics Engineering Department, METU Prof. Dr. Ayhan Altınta¸s Electrical and Electronics Eng. Dep., Bilkent University Date: January 11, 2018 I hereby declare that all information in this document has been obtained and presented in accordance with academic rules and ethical conduct. I also declare that, as required by these rules and conduct, I have fully cited and referenced all material and results that are not original to this work. Name, Last Name: IREM˙ ÇELEBI˙ Signature : iv ABSTRACT ÇELEBI,˙ IREM˙ M.S., Department of Electrical and Electronics Engineering Supervisor : Prof. -
Design of a Radio Frequency Waveguide Diplexer for Dual-Band Simultaneous Observation at 210-375 Ghz
30th International Symposium on Space THz Technology (ISSTT2019), Gothenburg, Sweden, April 15-17, 2019 Design of a Radio Frequency Waveguide Diplexer for Dual-band Simultaneous Observation at 210-375 GHz. Sho Masui, Shota Ueda, Yasumasa Yamasaki, Koki Yokoyama, Nozomi Okada, Toshikazu Onishi, Hideo Ogawa, Yutaka Hasegawa, Kimihiro Kimura, Takafumi Kojima, Alvaro Gonzalez observe molecular clouds in nearby star-forming regions and Abstract—The 1.85-meter telescope has been operated at along the Galactic Plane in 12CO, 13CO, and C18O (J = 2-1) (e.g., Nobeyama Radio Observatory to observe molecular clouds in [1][2]). Now, we are planning to relocated the 1.85-m telescope 12 13 18 nearby Garactic Plane in CO, CO, C O(J = 2-1). We are to Atacama site (nearly 2,400 m) and to newly install a dual- planning to relocate the telescope to the Atacama site (~2,400 m) band simultaneous observation of CO lines at J = 2-1 and J = and to newly install a dual-band simultaneous observation of CO lines at J = 2-1 and J = 3-2. To achieve this observation, we have 3-2. As a receiver system for dual-band simultaneous designed a radio frequency waveguide diplexer to separate 211- observation, we are developing radio frequency waveguide 275 GHz (ALMA band 6) and 275-373 GHz (ALMA band 7). The multiplexer in 210-375 GHz (the fractional bandwidth is 58.8% basic idea is to apply the waveguide frequency-separation- when its center frequency is 280.6 GHz). This multiplexer filter (FSF) [2], which has been successfully used for astronomical consists of ( α ) wideband waveguide diplexer (Fig. -
An RF-MEMS-Based Digitally Tunable SIW Filter in X-Band for Communication Satellite Applications
applied sciences Article An RF-MEMS-Based Digitally Tunable SIW Filter in X-Band for Communication Satellite Applications Abbas El Mostrah 1, Andrei Muller 2, Jean-François Favennec 2,*, Benjamin Potelon 2,* , Alexandre Manchec 1, Eric Rius 2 ,Cédric Quendo 2 , Yann Clavet 1, Francis Doukhan 3 and Johann Le Nezet 3 1 Elliptika, Gouesnou, Rue Gustave Zédé, 29200 Brest, France; [email protected] (A.E.M.); [email protected] (A.M.); [email protected] (Y.C.) 2 Laboratoire des Sciences et Techniques de l’Information, de la Communication et de la Connaissance (Lab-STICC), Université de Brest, 6 avenue Le Gorgeu, CS 93837, 29238 Brest, France; [email protected] (A.M.); [email protected] (E.R.); [email protected] (C.Q.) 3 Direction Générale de l’Armement (DGA), Route de Laillé, 35131 Bruz, France; [email protected] (F.D.); [email protected] (J.L.N.) * Correspondence: [email protected] (J.-F.F.); [email protected] (B.P.) Received: 12 March 2019; Accepted: 30 April 2019; Published: 4 May 2019 Abstract: This paper presents a digitally tunable SIW (substrate integrated waveguide) filter designed for X-band, based on RF-MEMS (radio frequency micro-electrical-mechanical systems) technology. Four commercial off-the-shelf RF-MEMS single-pole single-throw (SPST) switches were directly mounted on the upper surface of the filter, with metallic tuning posts specifically located within each cavity to define the potential achievable frequency range. Fabricated on standard alumina substrate, the design of the filter and the biasing network enabled fine digital frequency control of up to four functional states by the inclusion of wire bondings between each switch and the substrate.