International Journal for Scientific Research & Development
Total Page:16
File Type:pdf, Size:1020Kb
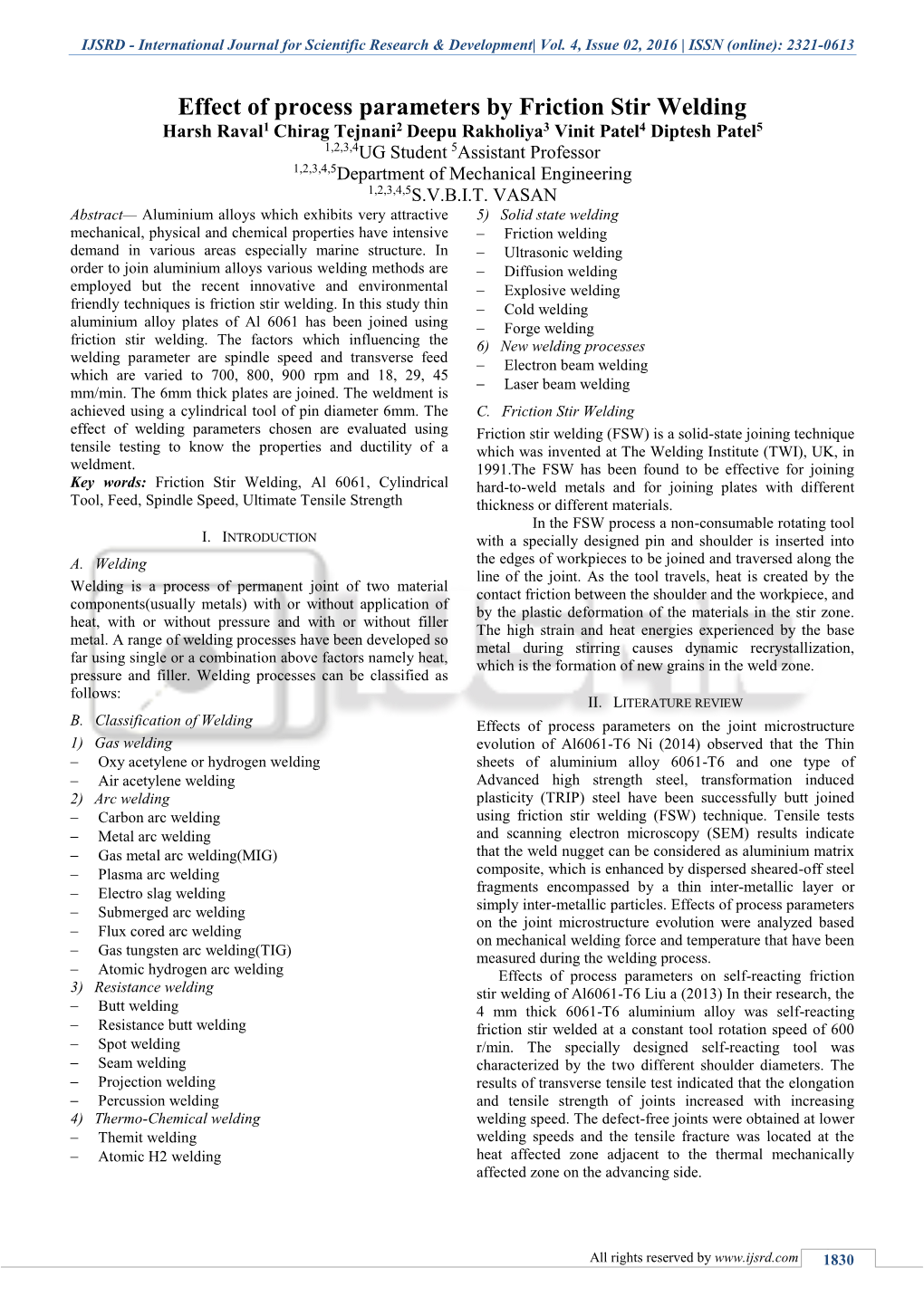
Load more
Recommended publications
-
Welding Technology a Suncam Continuing Education Course
033.pdf Welding Technology A SunCam Continuing Education Course Welding Technology By Roger Cantrell www.SunCam.com Page 1 of 35 033.pdf Welding Technology A SunCam Continuing Education Course Learning Objectives This course introduces the student to the concept of developing procedures for welding and brazing. Welding and brazing variables are introduced and some example concepts for applying each variable are highlighted to pique the student’s interest and perhaps lead to further study. Upon completion of this course, the student should be able to: • Understand the concept of creating a welding/brazing procedure • Identify several commonly used welding/brazing processes • Identify the more common welding/brazing variables • Appreciate some of the considerations for applying each variable 1.0 INTRODUCTION This course highlights the basic concepts of developing a welding or brazing procedure specification (WPS/BPS). There are a number of ways to approach this subject such as by process, base material, etc. It will be convenient to organize our thoughts in the format of ASME Section IX. The various factors that might influence weld quality are identified in ASME Section IX as "Welding Variables". "Brazing Variables" are treated in a separate part of Section IX in a manner similar to welding variables. The listing of variables for welding procedures can be found in ASME Section IX, Tables QW-252 through QW-265 (a table for each process). The layout of each table is similar to Figure No. 1. www.SunCam.com Page 2 of 35 033.pdf Welding Technology A SunCam Continuing Education Course Process Variable Variation (Description) Essential Supplementary Essential Nonessential Joint Backing X Root Spacing X Base P Number X Metal G Number X Filler F Number X Metal A Number X Continued in this fashion until all relevant variables for the subject process are listed. -
Welding Process Reference Guide
Welding Process Reference Guide gas arc welding…………………..GMAW -pulsed arc…………….……….GMAW-P atomic hydrogen welding……..AHW -short circuiting arc………..GMAW-S bare metal arc welding…………BMAW gas tungsten arc welding…….GTAW carbon arc welding……………….CAW -pulsed arc……………………….GTAW-P -gas……………………………………CAW-G plasma arc welding……………..PAW -shielded……………………………CAW-S shielded metal arc welding….SMAW -twin………………………………….CAW-T stud arc welding………………….SW electrogas welding……………….EGW submerged arc welding……….SAW Flux cord arc welding…………..FCAW -series………………………..…….SAW-S coextrusion welding……………...CEW Arc brazing……………………………..AB cold welding…………………………..CW Block brazing………………………….BB diffusion welding……………………DFW Diffusion brazing…………………….DFB explosion welding………………….EXW Dip brazing……………………………..DB forge welding…………………………FOW Flow brazing…………………………….FLB friction welding………………………FRW Furnace brazing……………………… FB hot pressure welding…………….HPW SOLID ARC Induction brazing…………………….IB STATE BRAZING WELDING Infrared brazing……………………….IRB roll welding…………………………….ROW WELDING (8) ultrasonic welding………………….USW (SSW) (AW) Resistance brazing…………………..RB Torch brazing……………………………TB Twin carbon arc brazing…………..TCAB dip soldering…………………………DS furnace soldering………………….FS WELDING OTHER electron beam welding………….EBW induction soldering……………….IS SOLDERING PROCESS WELDNG -high vacuum…………………….EBW-HV infrared soldering…………………IRS (S) -medium vacuum………………EBW-MV iron soldering……………………….INS -non-vacuum…………………….EBW-NV resistance soldering…………….RS electroslag welding……………….ESW torch soldering……………………..TS -
Lecture: 3 Classification of Welding Processes II Apart from Technical
Lecture: 3 Classification of Welding Processes II Apart from technical factors, welding processes can also be classified on the fundamental approaches used for deposition of materials for developing a joint. This chapter presents the classification of welding processes as welding processes and allied process used for developing a joint Keywords: Welding and allied processes, approach of classification, cast weld, resistance weld, fusion weld, solid state weld 3.1 Classification of welding processes There is another way of classifying welding and allied processes which is commonly reported in literature. Various positive processes involving addition or deposition of metal are first broadly grouped as welding process and allied welding processes as under: 1. Welding processes i. Cast weld processes ii. Fusion weld processes iii. Resistance weld processes iv. Solid state weld processes 2. Allied welding processes i. Metal depositing processes ii. Soldering iii. Brazing iv. Adhesive bonding v. Weld surfacing vi. Metal spraying This approach of classifying the welding process is primarily based on the way metallic pieces are united together during welding such as Availability and solidification of molten weld metal between components being joined are similar to that of casting: Cast weld process. Fusion of faying surfaces for developing a weld: Fusion weld process Heating of metal only to plasticize then applying pressure to forge them together: Resistance weld process Use pressure to produce a weld joint in solid state only: Solid state weld process 3.2 Cast welding process Those welding processes in which either molten weld metal is supplied from external source or melted and solidified at very low rate during solidification like castings. -
Arc Welding • Electric Arc Is Produced When Current Flows Across the Air Gap Between the End of Metal Electrode and Work Surface
Arc welding • Electric arc is produced when current flows across the air gap between the end of metal electrode and work surface. • Electric discharge occurring in the air gap. • The temperature at centre of arc is 6500C. • Only 3600C is utilized for melting of metal. • Arc welding is a welding process that is used to join metal to metal by using electricity to create enough heat to melt metal, and the melted metals when cool result in a binding of the metals. • Equipments: • Transformer: To change high voltage and low amperage to a low voltage 20-80 V and high 80- 500 amps. • In arc welding, the voltage is directly related to the length of the arc, and the current is related to the amount of heat input. • Generator: Driven by motor. Generates D.C. • Rectifier: The output of step down transformer is to rectifier to converts A.C. to D.C. • Electrode: Metal stick to create arc. A.C.plant: • Simple, less cost, No moving parts, low maintenance cost, no change of polarity. • Gives smoother arc when using high current. • Not suitable for non-ferrous and thin sheets. • Electric shock is more intense. • D.C.Plant • Can be used for ferrous ,non-ferrous & thin sheets • Stable arc, fine settings are possible • Easy of operation, suitable for over head welding. • Safer to use. • More expensive, high maintenance cost, arc blow(arc is forced away from weld point). • Polarity: It indicates the direction of current flow in D.C. In D.C. 2/3 of heat is liberated from + end and 1/3 of heat is liberated from - end. -
Red Rocks Community College 1997-98 Catalog
Red Rocks Community College 1997-98 Catalog CollegeSource Career Guidance Foundation • 1-800-854-2670 • http://www.cgf.org Copyright & Disclaimer Information Copyright© 1994, 1995, 1996,1997 Career Guidance Foundation CollegeSource digital catalogs are derivitave works owned and copyrighted by Career Guidance Foundation. Catalog content is owned and copyrighted by the appropriate school. While the Career Guidance Foundation provides information as a service to the public, copyright is retained on all material. This means you may NOT: · distribute the material to others, · "mirror" or include this material on an Internet (or Intranet) server, or · modify or re-use material without the express written consent of the Career Guidance Foundation and the appropriate school. You may: · print copies of the information for your own personal use, · store the files on your own computer for personal use only, or · reference this material from your own documents. The Career Guidance Foundation reserves the right to revoke such authorization at any time, and any such use shall be discontinued immediately upon written notice from the Career Guidance Foundation. Disclaimer CollegeSource digital catalogs are converted from either the original printed catalog or electronic media supplied by each school. Although every attempt is made to ensure accurate conversion of data, the Career Guidance Foundation and the schools which provide the data do not guarantee that the this information is accurate or correct. The information provided should be used only as reference and planning tools. Final decisions should be based and confirmed on data received directly from each school. What do our students learn? First, they learn about learning. -
05/09/16 05/09/16 Rc-Upf Dmc Rc
UPF PROJECT PROCEDURE Title: UPF WELDING AND CUTTING SAFETY Document Number: UPF-CP-225WCS Revision: 000 Page: 1 of 13 Prepared by: . 05/09/16 . Brian Garrett, Date BNI UPF ES&H Lead Approved by: . 05/09/16 . Ed Kelley, Date BNI UPF ES&H Manager Approved by: . 05/09/16 . Gary Hagan, Date UPF ES&H Manager Concurrence by: . 05/09/16 . Lynn Nolan, Date UPF Manager of Construction . 05/10/16 . James W. Sowers, Date UPF Quality Assurance Manager 05/11/16 Effective Date RC-UPF DMC This document has been reviewed by a Y-12 DC / RC-UPF DMC UCNI-RO and has been determined to be 05/10/16 15:15 UNCLASSIFIED and contains no UCNI. This review 05/10/16 15:32 does not constitute clearance for Public Release. Name:________________________ Date:__________05/09/16 UPF-CP-225WCS Revision 00 Page 2 of 13 UPF Welding and Cutting Safety Revision History Revision Reason/Description of Change Initial issue. 000 UPF-CP-225WCS Revision 00 Page 3 of 13 UPF Welding and Cutting Safety Table of Contents 1.0 PURPOSE ..................................................................................................................................4 2.0 GENERAL ..................................................................................................................................4 Description ....................................................................................................................4 Acronyms .......................................................................................................................4 Definitions ......................................................................................................................4 -
Basic Metallurgy
Welding Welding or more generally Joining involves putting two or more pieces together in such a way that they behave as a single piece. This may involve applying some kind of pressure or heat or both to the pieces to be joined together. Welding provides metallurgical continuity, while mechanical joining process like riveting does not provide metallurgical continuity. Definition Localized coalescence of metals produced either by heating the material to the required welding temperature, with or without the application of pressure or by the application of pressure alone, with or without the use of filler materials.” Advantages of Welding • Welding has proved to be most efficient way of creating new shapes. There is maximum saving of the material. • It is suitable for single or one off piece or for large numbers of similar jobs. • Individual components produced by different shaping route such as forging, rolling or casting can joined together by welding. • Very large to small components can be made by welding. • Riveting and bolting involves material wastages as it leads to heavier structures. • Riveted joints are prone to fatigue failures and crevice corrosion attack. • Welding methods are open for automation and use of ROBOTS. Classification of Welding a) Fusion Welding processes: Fusion welding is carried out by simultaneous melting of the edges of the pieces to be joined, allowing the molten metal to mix together and solidify as a single piece to bridge the gap between two components, thus melted and solidified metal becomes part of the joint. Additional molten metal can be added either through electrodes or through filler metal. -
Welding Operations, I
SUBCOURSE EDITION OD1651 8 WELDING OPERATIONS, I WELDING OPERATIONS, I SUBCOURSE NO. OD1651 United States Army Combined Arms support Command Fort Lee, Virginia 23801-1809 6 Credit Hours GENERAL The purpose of this course is to introduce the basic requirements involved in metal-arc welding operations. The scope of this subcourse consists of describing the classification of electrodes and their intended uses; describing automotive welding processes, materials and identification processes; describing the methods of destructive and nondestructive testing of welds and troubleshooting procedures; describing the type and techniques of joint design; and describing the theory, principles, and procedures of welding armor plate. Six credit hours are awarded for successful completion of this subcourse. Lesson 1 ELECTRODES CLASSIFICATION AND INTENDED USES; AUTOMOTIVE WELDING PROCESSES, MATERIALS, AND IDENTIFICATION PROCESSES; METHODS OF DESTRUCTIVE AND NONDESTRUCTIVE TESTING OF WELDS AND TROUBLESHOOTING PROCEDURES; TYPES AND TECHNIQUES OF JOINT DESIGN; AND THE THEORY, PRINCIPLES, AND PROCEDURES OF WELDING ARMOR PLATE i WELDING OPERATIONS I - OD1651 TASK 1: Describe the processes for identifying electrodes by classification, and intended uses; and the automotive welding processes, materials, and identification processes; and the types and techniques of joint design. TASK 2: Describe the theory, principles, and procedures of welding armor plate; and methods of destructive and nondestructive testing of welds, and troubleshooting procedures. ii WELDING -
Chapter-1 Introduction
Chapter-1 Introduction Introduction:- One of the main functions of the Engineering Works is joining of the parts. Collectively this joining is called Fastening. Fastening is generally two type are- 1. Temporary Fastening: In this process of fastening, the parts are ready to separation. Ex-Nut and Bolts, Nut and screws, Nuts and studs are all temporary fastenings. 2. Permanent Fastening: In this process of fastening the parts not likely to require separate. Ex-Welding. 3. Semi-permanent Fastening: In this process of fastening the parts are semi separable. 4. Ex-Soldering, Brazing and Riveting. 1 Chapter-2 2.1 Definition:- The welding is a process of joining two similar or dissimilar metals by fusion or without fusion, with or without the application of pressure and with or without filler metal. [3] During fusion a solid union or a compact mass is formed. If filler material is similar with the base material then this type of welding is called homogenous welding and if filler material is different from base material then it is heterogenous welding, where filler material is given should have low melting temperature. 2.2. Types of welding:- The overall welding process shown in chart below 2 The welding is broadly divided into the two groups: I. Pressure welding or diffusion welding: this welding process is done under pressure without additional filler metals. It is classified as- a) Hot pressure welding and b) cold pressure welding 2nd state 1st state 2nd 4 II. Fusion or non-pressure welding: This process is done with additional filler metals. It is classified as a) Gas welding, b) Thermit welding, c) Electroslage welding, d) Electron beam welding, e) Laser beam welding and f) Arc welding. -
Solid State Welding and Application in Aeronautical Industry
ISSN 2303-4521 PERIODICALS OF ENGINEERING AND NATURAL SCIENCES Vol. 4 No. 1 (2016) Available online at: http://pen.ius.edu.ba Solid State Welding and Application in Aeronautical Industry Enes Akca*, Ali Gursel International University of Sarajevo Faculty of Engineering and Natural Sciences Sarajevo, Bosnia and Herzegovina [email protected], [email protected] Abstract In this study solid state welding andapplication in aeronautic industryhave been researched. The solid state welding technicisused in the industrial production fields such as aircraft, nucleer, space industry, aeronautic industry, ect., actually solid state welding is a process by which similar and dissmilar metals can be bonded together. Hence a material can be created as not heavy but strong strength. Beside, advantages and disasvantages of solid state welding have been discussed. Also the diffusion welding and friction welding which belong to the solid state welding is obsevered in aeronautic industry. Keywords: solid state welding, aeronautic industry,diffusion welding, dissimilar materials 1 Introduction Welding is a metal joining process which produces Disadvantages of Solid State Welding: coalescence of metals by heating them to suitable Internal stresses, distortions and changes of micro- temperatures with or without the application of pressure structure in the weld region, or by the application of pressure alone, and with or Harmful effects: light, ultra violate radiation, fumes, without the use of filler material. Basically, welding is high temperature, used for making permanent joints. It is used in the manufacture of automobile bodies, aircraft frames, Also there are many kinds of welding processes; railway wagons, machine frames, structural works, tanks, Arc welding; furniture, boilers, general repair work and ship building. -
Friction Stir Welding Parameter Optimization
Vol-4 Issue-1 2018 IJARIIE-ISSN(O)-2395-4396 Friction Stir Welding Parameter Optimization Gaurav Tatpurkar1, Mahesh Sangale2, Sudhir Sanap3, Sumit Pagare4,A.H.Karwande5 1 Student, Mechanical Department, SND COLLAGE OF ENGINEERING & RESEARCH CENTER YEOLA, NASHIK-423401, Maharashtra, India 2 Student, Mechanical Department, SND COLLAGE OF ENGINEERING & RESEARCH CENTER YEOLA, NASHIK-423401, Maharashtra, India 3 Student, Mechanical Department, SND COLLAGE OF ENGINEERING & RESEARCH CENTER YEOLA, NASHIK-423401, Maharashtra, India 4 Student, Mechanical Department, SND COLLAGE OF ENGINEERING & RESEARCH CENTER YEOLA, NASHIK-423401, Maharashtra, India 5Asst.Professor in Mechanical Department, SND COLLAGE OF ENGINEERING & RESEARCH CENTER YEOLA, NASHIK-423401, Maharashtra, India ABSTRACT The focus of the research work will be concentrated in the mechanical performance and the stir zone microstructure by FSW butt welded part having 150mm × 50mm × 5mm thick sheet 5000 series aluminum alloy 6061 and 150mm × 50mm × 5mm thick The same sheet using tool steel material having taper tool pin profile. And same specimen plates having size (150mm × 50mm × 5mm) welded by Oxyacetylene welding process. All the testing of welded part will be tested by ASTM standard. In this work, (UTM), Inverted Microscope (IM) to get the microstructure properties. Keyword: -Friction stir welding (FSW), oxy-acetylene gas welding , stir 1. INTRODUCTION Welding is a fabrication process used to join materials, usually metals or thermoplastics, together. During welding, the work pieces to be joined are melted at the joining interface and usually a filler material is added to form a weld pool of molten material that solidifies to become a strong joint. In contrast, Soldering and Brazing do not involve melting the work piece but rather a lower melting point material is melted between the work pieces to bond them together. -
Welding Health and Safety
Welding Health and Safety Welding Health and Safety SS-832 June 2018 SS-832 | June 2018 Page | 1 Welding Health and Safety Table of contents Introduction ....................................................................................................3 What is welding? .............................................................................................3 Welding and cutting processes ........................................................................3 Types of electrodes .........................................................................................5 Health hazards ................................................................................................5 Hazard controls ...............................................................................................9 Confined spaces…………………………………………………………………………………….11 Oxygen-fuel gas welding and cutting ..............................................................12 Equipment maintenance………………………………………………………………………….12 Specific requirements……………………………………………………………………………..12 Arc welding and cutting ..................................................................................15 Resistance welding .........................................................................................15 Appendix A: definitions ...................................................................................16 Appendix B: common metals and compounds .................................................17 Appendix C: common welding gases ...............................................................19