The Effect of Coal Properties on Carbonization Behaviour and Strength of Coke Blends
Total Page:16
File Type:pdf, Size:1020Kb
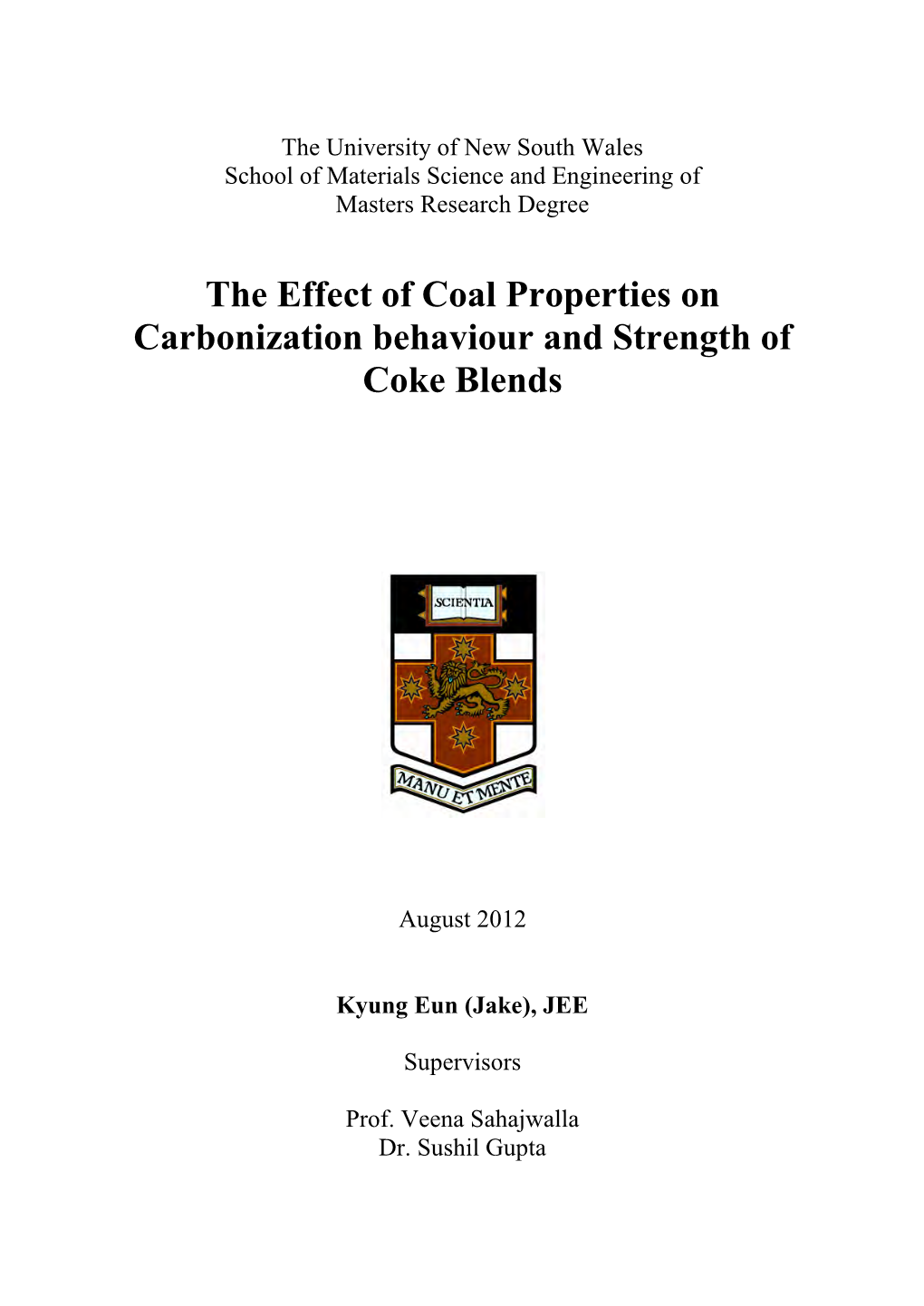
Load more
Recommended publications
-
Petrographic and Vitrinite Reflectance Analyses of a Suite of High Volatile Bituminous Coal Samples from the United States and Venezuela
Petrographic and vitrinite reflectance analyses of a suite of high volatile bituminous coal samples from the United States and Venezuela Open-File Report 2008-1230 U.S. Department of the Interior U.S. Geological Survey U.S. Department of the Interior Dirk A. Kempthorne, Secretary U.S. Geological Survey Mark D. Myers, Director U.S. Geological Survey, Reston, Virginia 2008 For product and ordering information: World Wide Web: http://www.usgs.gov/pubprod Telephone: 1-888-ASK-USGS For more information on the USGS—the Federal source for science about the Earth, its natural and living resources, natural hazards, and the environment: World Wide Web: http://www.usgs.gov Telephone: 1-888-ASK-USGS Suggested citation: Hackley, P.C., Kolak, J.J., 2008, Petrographic and vitrinite reflectance analyses of a suite of high volatile bituminous coal samples from the United States and Venezuela: U.S. Geological Survey Open-File Report 2008-1230, 36 p., http://pubs.usgs.gov/of/2008/1230. Any use of trade, product, or firm names is for descriptive purposes only and does not imply endorsement by the U.S. Government. Although this report is in the public domain, permission must be secured from the individual copyright owners to reproduce any copyrighted material contained within this report. ii Contents Introduction ........................................................................................................................................................................1 Methods ..............................................................................................................................................................................1 -
Characterization of Macerals in Coal Fines Using Image Analysis Technique
CORE Metadata, citation and similar papers at core.ac.uk ProvidedYrlitlls/Yi by eprints@NML "o , I,6 i, m * di ♦riaYiYYYi1MiMIY^bIY+ ^ ♦^tllll^iitr^ a• n, ""Bill "'srlM1 t* o m 64MfWI4I"* 1"60/001tIY - i i it ISB.A Processing of-Fines (2) f ils. P $Ilrnr(,a ha) vva, R. Silt, Jr and ,S'- G. Gnmt (imJ CJ ^ti'dlf-Jw i,chc'Jj rn-R3t 007. Indio. 2000. pp. 1./ 24 Characterization of macerals in coal fines using image analysis technique P. YERRISWAMY, O. P. MODI, K. K. RAO' and T. C. RAO Regional Research Laboratory (CS!R), Bhopal, India 'Bar-katull as Unircr.srty, Bhopal, hreha ABSTRA(_"I' Coal is an aggregate of heterogeneous substance consisting of various or aiiic cemsti-tnents so called nuacerals along with inorganic mutter. These inacerals have been broadly classified into three major maceral groups i.e. vitrirrite, exirrite (liptinite) and inertinite. Coal-frnes of size less than 0.5 ntnr, collected from Aloorridih coal washerl•. was used in the present stud. These coal fates were subjected to size anals•sis and sink-float ctnalt'sis. The products obtained at different size and density fractions were mounted in resin + hardener mixture using .standard sample preparation technique and polished- The polished samples were examined tender- microscope interfaced wvith image analyzer: Results indicate that size and density fractions have a significc-rnt influence on the changes in the maceral concentrations. The same has been discussed in terms of physical coal cleaning, process. Key words Macerals, linage anahvsis and Kelsev certrrifi,'crl jig. -
Chemical and Physical Structural Studies on Two Inertinite-Rich Lump
CHEMICAL AND PHYSICAL STRUCTURAL STUDIES ON TWO INERTINITE-RICH LUMP COALS. Nandi Malumbazo A thesis submitted in fulfilment of the requirements for the degree of Doctor of Philoso- phy in the School of Chemical and Metallurgical Engineering at the University of the Witwatersrand. Johannesburg, 2011 DECLARATION I, Nandi Malumbazo, declare that the thesis entitled: “CHEMICAL AND PHYSICAL STRUCTURAL STUDIES ON TWO INER- TINITE-RICH LUMP COALS” is my own work and that all sources I have used or quoted have been indicated and ac- knowledged by means of references. Signature: ……………………………………………………………….. Date:………………………………………………………………………… Page i ABSTRACT ABSTRACT Two Highveld inertinite-rich lump coals were utilized as feed coal samples in order to study their physical, chemical structural and petrographic variations during heat treat- ment in a packed-bed reactor unit combustor. The two feed lump coals were selected as it is claimed that Coal B converts at a slower rate in a commercial coal conversion process when compared to Coal A. The reason for this requires detailed investigation. Chemical structural variations were determined by proximate and coal char CO2 reactiv- ity analysis. Physical structural variations were determined by FTIR, BET adsorption methods, XRD and 13C Solid state NMR analysis. Carbon particle type analysis was con- ducted to determine the petrographic constituents of the reactor generated samples, their maceral associations (microlithotype), and char morphology. This analysis was undertaken with the intention of tracking the carbon conversion and char formation and consumption behaviour of the two coal samples within the reactor. Proximate analysis revealed that Coal A released 10 % more of its volatile matter through the reactor compared to Coal B. -
Vitrinite Recycling: Diagnostic Criteria and Reflectance Changes During Weathering and Reburial
Vitrinite recycling: diagnostic criteria and reflectance changes during weathering and reburial. Pierre Nzoussi - Mbassani, Yoann Copard, Jean-Robert Disnar To cite this version: Pierre Nzoussi - Mbassani, Yoann Copard, Jean-Robert Disnar. Vitrinite recycling: diagnostic criteria and reflectance changes during weathering and reburial.. International Journal of Coal Geology, Elsevier, 2005, 61, pp.223-239. 10.1016/j.coal.2004.08.002. hal-00023485 HAL Id: hal-00023485 https://hal-insu.archives-ouvertes.fr/hal-00023485 Submitted on 23 May 2006 HAL is a multi-disciplinary open access L’archive ouverte pluridisciplinaire HAL, est archive for the deposit and dissemination of sci- destinée au dépôt et à la diffusion de documents entific research documents, whether they are pub- scientifiques de niveau recherche, publiés ou non, lished or not. The documents may come from émanant des établissements d’enseignement et de teaching and research institutions in France or recherche français ou étrangers, des laboratoires abroad, or from public or private research centers. publics ou privés. Vitrinite recycling: diagnostic criteria and reflectance changes during weathering and reburial P. Nzoussi-Mbassani, Y. Copard and J.R. Disnar Institut des Sciences de la Terre d'Orléans (ISTO- UMR 6113 du CNRS, Université d'Orléans, Bâtiment de Géosciences, 45067 Orléans cedex 2, France Keywords: Recycled vitrinite; Autochthonous vitrinite; Vitrinite reflectance; Senegalese basin; Ardèche margin; Weathering Abstract The aim of this study was first to review or even identify reliable diagnostic criteria to distinguish recycled and autochthonous vitrinite particles and, second, to examine and try to explain the impact of weathering and reburial on optical changes (reflectance) of recycled material. -
Coal Characteristics
CCTR Indiana Center for Coal Technology Research COAL CHARACTERISTICS CCTR Basic Facts File # 8 Brian H. Bowen, Marty W. Irwin The Energy Center at Discovery Park Purdue University CCTR, Potter Center, 500 Central Drive West Lafayette, IN 47907-2022 http://www.purdue.edu/dp/energy/CCTR/ Email: [email protected] October 2008 1 Indiana Center for Coal Technology Research CCTR COAL FORMATION As geological processes apply pressure to peat over time, it is transformed successively into different types of coal Source: Kentucky Geological Survey http://images.google.com/imgres?imgurl=http://www.uky.edu/KGS/coal/images/peatcoal.gif&imgrefurl=http://www.uky.edu/KGS/coal/coalform.htm&h=354&w=579&sz= 20&hl=en&start=5&um=1&tbnid=NavOy9_5HD07pM:&tbnh=82&tbnw=134&prev=/images%3Fq%3Dcoal%2Bphotos%26svnum%3D10%26um%3D1%26hl%3Den%26sa%3DX 2 Indiana Center for Coal Technology Research CCTR COAL ANALYSIS Elemental analysis of coal gives empirical formulas such as: C137H97O9NS for Bituminous Coal C240H90O4NS for high-grade Anthracite Coal is divided into 4 ranks: (1) Anthracite (2) Bituminous (3) Sub-bituminous (4) Lignite Source: http://cc.msnscache.com/cache.aspx?q=4929705428518&lang=en-US&mkt=en-US&FORM=CVRE8 3 Indiana Center for Coal Technology Research CCTR BITUMINOUS COAL Bituminous Coal: Great pressure results in the creation of bituminous, or “soft” coal. This is the type most commonly used for electric power generation in the U.S. It has a higher heating value than either lignite or sub-bituminous, but less than that of anthracite. Bituminous coal -
Lecture 32: Coke Production
NPTEL – Chemical – Chemical Technology II Lecture 32: Coke production 32.1 Introduction Coal is used as fuel for electric power generation, industrial heating and steam generation, domestic heating, rail roads and for coal processing. Coal composition is denoted by rank. Rank increases with the carbon content and decreases with increasing oxygen content. Many of the products made by hydrogenation, oxidation, hydrolysis or fluorination are important for industrial use. Stable, low cost, petroleum and natural gas supplies has arose interest in some of the coal products as upgraded fuels to reduce air pollution as well as to take advantage of greater ease of handling of the liquid or gaseous material and to utilize existing facilities such as pipelines and furnaces. 32.2 Coking of coal Raw material is Bituminous coal. It appears to have specific internal surfaces in the range of 30 to 100m2/g. Generally one ton of bituminous coal produces 1400 lb of coke. 10 gallons of tar. Chemical reaction:- 4(C3H4)n nC6H6 + 5nC + 3nH2 + nCH4 Coal Benzene Coke Lighter hydrocarbon Joint initiative of IITs and IISc – Funded by MHRD Page 1 of 9 NPTEL – Chemical – Chemical Technology II Process flow sheet: Illustrated in Figure. Figure 32.1 Flow sheet of coking of coal 32.3 Functional role of each unit (Figure 32.1): (a) Coal crusher and screening: At first Bituminous coal is crushed and screened to a certain size. Preheating of coal (at 150-250˚C) is done to reduce coking time without loss of coal quality. Briquetting increases strength of coke produced and to make non - coking or poorly coking coals to be used as metallurgical coke. -
Proposal for Development of Dry Coking/Coal
Development of Coking/Coal Gasification Concept to Use Indiana Coal for the Production of Metallurgical Coke, Liquid Transportation Fuels, Fertilizer, and Bulk Electric Power Phase II Final Report September 30, 2007 Submitted by Robert Kramer, Ph.D. Director, Energy Efficiency and Reliability Center Purdue University Calumet Table of Contents Page Executive Summary ………………………………………………..…………… 3 List of Figures …………………………………………………………………… 5 List of Tables ……………………………………………………………………. 6 Introduction ……………………………………………………………………… 7 Process Description ……………………………………………………………. 11 Importance to Indiana Coal Use ……………………………………………… 36 Relevance to Previous Studies ………………………………………………. 40 Policy, Scientific and Technical Barriers …………………………………….. 49 Conclusion ………………………………………………………………………. 50 Appendix ………………………………………………………………………… 52 2 Executive Summary Coke is a solid carbon fuel and carbon source produced from coal that is used to melt and reduce iron ore. Although coke is an absolutely essential part of iron making and foundry processes, currently there is a shortfall of 5.5 million tons of coke per year in the United States. The shortfall has resulted in increased imports and drastic increases in coke prices and market volatility. For example, coke delivered FOB to a Chinese port in January 2004 was priced at $60/ton, but rose to $420/ton in March 2004 and in September 2004 was $220/ton. This makes clear the likelihood that prices will remain high. This effort that is the subject of this report has considered the suitability of and potential processes for using Indiana coal for the production of coke in a mine mouth or local coking/gasification-liquefaction process. Such processes involve multiple value streams that reduce technical and economic risk. Initial results indicate that it is possible to use blended coal with up to 40% Indiana coal in a non recovery coke oven to produce pyrolysis gas that can be selectively extracted and used for various purposes including the production of electricity and liquid transportation fuels and possibly fertilizer and hydrogen. -
Application of Organic Petrography in North American Shale Petroleum Systems: a Review
International Journal of Coal Geology 163 (2016) 8–51 Contents lists available at ScienceDirect International Journal of Coal Geology journal homepage: www.elsevier.com/locate/ijcoalgeo Application of organic petrography in North American shale petroleum systems: A review Paul C. Hackley a, Brian J. Cardott b a U.S. Geological Survey, MS 956 National Center, 12201 Sunrise Valley Dr, Reston, VA 20192, USA b Oklahoma Geological Survey, 100 E. Boyd St., Rm. N-131, Norman, OK 73019-0628, USA article info abstract Article history: Organic petrography via incident light microscopy has broad application to shale petroleum systems, including Received 13 April 2016 delineation of thermal maturity windows and determination of organo-facies. Incident light microscopy allows Received in revised form 10 June 2016 practitioners the ability to identify various types of organic components and demonstrates that solid bitumen Accepted 13 June 2016 is the dominant organic matter occurring in shale plays of peak oil and gas window thermal maturity, whereas Available online 16 June 2016 oil-prone Type I/II kerogens have converted to hydrocarbons and are not present. High magnification SEM obser- Keywords: vation of an interconnected organic porosity occurring in the solid bitumen of thermally mature shale reservoirs Organic petrology has enabled major advances in our understanding of hydrocarbon migration and storage in shale, but suffers Thermal maturity from inability to confirm the type of organic matter present. Herein we review organic petrography applications Shale petroleum systems in the North American shale plays through discussion of incident light photographic examples. In the first part of Unconventional resources the manuscript we provide basic practical information on the measurement of organic reflectance and outline Vitrinite reflectance fluorescence microscopy and other petrographic approaches to the determination of thermal maturity. -
On the Fundamental Difference Between Coal Rank and Coal Type
International Journal of Coal Geology 118 (2013) 58–87 Contents lists available at ScienceDirect International Journal of Coal Geology journal homepage: www.elsevier.com/locate/ijcoalgeo Review article On the fundamental difference between coal rank and coal type Jennifer M.K. O'Keefe a,⁎, Achim Bechtel b,KimonChristanisc, Shifeng Dai d, William A. DiMichele e, Cortland F. Eble f,JoanS.Esterleg, Maria Mastalerz h,AnneL.Raymondi, Bruno V. Valentim j,NicolaJ.Wagnerk, Colin R. Ward l, James C. Hower m a Department of Earth and Space Sciences, Morehead State University, Morehead, KY 40351, USA b Department of Applied Geosciences and Geophysics, Montan Universität, Leoben, Austria c Department of Geology, University of Patras, 265.04 Rio-Patras, Greece d State Key Laboratory of Coal Resources and Safe Mining, China University of Mining and Technology, Beijing 100083, China e Department of Paleobiology, Smithsonian Institution, Washington, DC 20013-7012, USA f Kentucky Geological Survey, University of Kentucky, Lexington, KY 40506, USA g School of Earth Sciences, The University of Queensland, QLD 4072, Australia h Indiana Geological Survey, Indiana University, 611 North Walnut Grove, Bloomington, IN 47405-2208, USA i Department of Geology and Geophysics, College Station, TX 77843, USA j Department of Geosciences, Environment and Spatial Planning, Faculty of Sciences, University of Porto and Geology Centre of the University of Porto, Rua Campo Alegre 687, 4169-007 Porto, Portugal k School Chemical & Metallurgical Engineering, University of Witwatersrand, 2050, WITS, South Africa l School of Biological, Earth and Environmental Sciences, University of New South Wales, Sydney, Australia m University of Kentucky, Center for Applied Energy Research, 2540 Research Park Drive, Lexington, KY 40511, USA article info abstract Article history: This article addresses the fundamental difference between coal rank and coal type. -
THE GUIDE to SOLID FUELS This Leaflet Will Tell You All You Need To
THE GUIDE TO SOLID FUELS This leaflet will tell you all you need to know about: • The different solid fuels available and their suitability for the various types of appliances • Smoke control legislation • Buying solid fuel • Hints on getting the best from your fuel and appliance Choice of Fuel There are a great many different solid fuels for sale. Your choice will be based on a number of criteria, the most important of which will be the type of appliance you will be burning the fuel on and whether or not you live in a smoke control area (see page 4). Fuels for open fires Housecoal The most traditional fuel for open fires is housecoal. It is available in various sizes e.g. Large Cobbles, Cobbles, Trebles and Doubles. The larger sizes are usually a little more expensive than Doubles size. Housecoal comes from mines in Britain and other parts of the world, most notably Columbia and Indonesia. The coal may be sold by the name of the colliery it comes from e.g. Daw Mill, the port of entry e.g. Merseyport or a merchant’s own brand name, e.g. Stirling. Coal merchants also frequently sell the coal by grade – 1, 2 and 3 or A, B and C; 1 and A being the best quality. Wood Wood and logs can be burnt on open fires. They should be well-seasoned and preferably have a low resin content. You should not use any wood that has any kind of coating on the surface e.g. varnish or paint, as harmful gases may be emitted on burning. -
Maceral Types and Quality of Coal in the Tuli Coalfield: a Case
applied sciences Article Maceral Types and Quality of Coal in the Tuli Coalfield: A Case Study of Coal in the Madzaringwe Formation in the Vele Colliery, Limpopo Province, South Africa Elelwani Denge * and Christopher Baiyegunhi Department of Geology and Mining, University of Limpopo, Private Bag X1106, Sovenga 0727, South Africa; [email protected] * Correspondence: [email protected] Featured Application: Authors are encouraged to provide a concise description of the specific application or a potential application of the work. This section is not mandatory. Abstract: The Madzaringwe Formation in the Vele colliery is one of the coal-bearing Late Palaeozoic units of the Karoo Supergroup, consisting of shale with thin coal seams and sandstones. Maceral group analysis was conducted on seven representative coal samples collected from three existing boreholes—OV125149, OV125156, and OV125160—in the Vele colliery to determine the coal rank and other intrinsic characteristics of the coal. The petrographic characterization revealed that vitrinite is the dominant maceral group in the coals, representing up to 81–92 vol.% (mmf) of the total sample. Collotellinite is the dominant vitrinite maceral, with a total count varying between 52.4 vol.% (mmf) and 74.9 vol.% (mmf), followed by corpogelinite, collodetrinite, tellinite, and pseudovitrinite with a Citation: Denge, E.; Baiyegunhi, C. count ranging between 0.8 and 19.4 vol.% (mmf), 1.5 and 17.5 vol.% (mmf), 0.8 and 6.5 vol.% (mmf) Maceral Types and Quality of Coal in the Tuli Coalfield: A Case Study of and 0.3 and 5.9 vol.% (mmf), respectively. The dominance of collotellinite gives a clear indication Coal in the Madzaringwe Formation that the coals are derived from the parenchymatous and woody tissues of roots, stems, and leaves. -
C) an Introduction to Coal Quality
Chapter C The National Coal Resource Assessment An Introduction to Coal Quality Overview By Stanley P. Schweinfurth1 Click here to return to Volume Table of Contents Chapter C of The National Coal Resource Assessment Overview Edited by Brenda S. Pierce and Kristin O. Dennen U.S. Geological Survey Professional Paper 1625–F 1U.S. Geological Survey, Reston, Virginia 20192 This report, although in the USGS Professional Paper series, is available only on CD–ROM U.S. Department of the Interior U.S. Geological Survey U.S. Department of the Interior KEN SALAZAR, Secretary U.S. Geological Survey Suzette M. Kimball, Acting Director U.S. Geological Survey, Reston, Virginia: 2009 For more information on the USGS—the Federal source for science about the Earth, its natural and living resources, natural hazards, and the environment, visit http://www.usgs.gov or call 1-888-ASK-USGS For an overview of USGS information products, including maps, imagery, and publications, visit http://www.usgs.gov/pubprod To order this and other USGS information products, visit http://store.usgs.gov Any use of trade, product, or firm names is for descriptive purposes only and does not imply endorsement by the U.S. Government. Although this report is in the public domain, permission must be secured from the individual copyright owners to reproduce any copyrighted materials contained within this report. Suggested citation: Schweinfurth, S.P., 2009, An introduction to coal quality, in Pierce, B.S., and Dennen, K.O., eds., The National Coal Resource Assessment Overview: U.S. Geological Survey Professional Paper 1625–F, Chapter C, 16 p.