FIXATION of ATMOSPHERIC NITROGEN
Total Page:16
File Type:pdf, Size:1020Kb
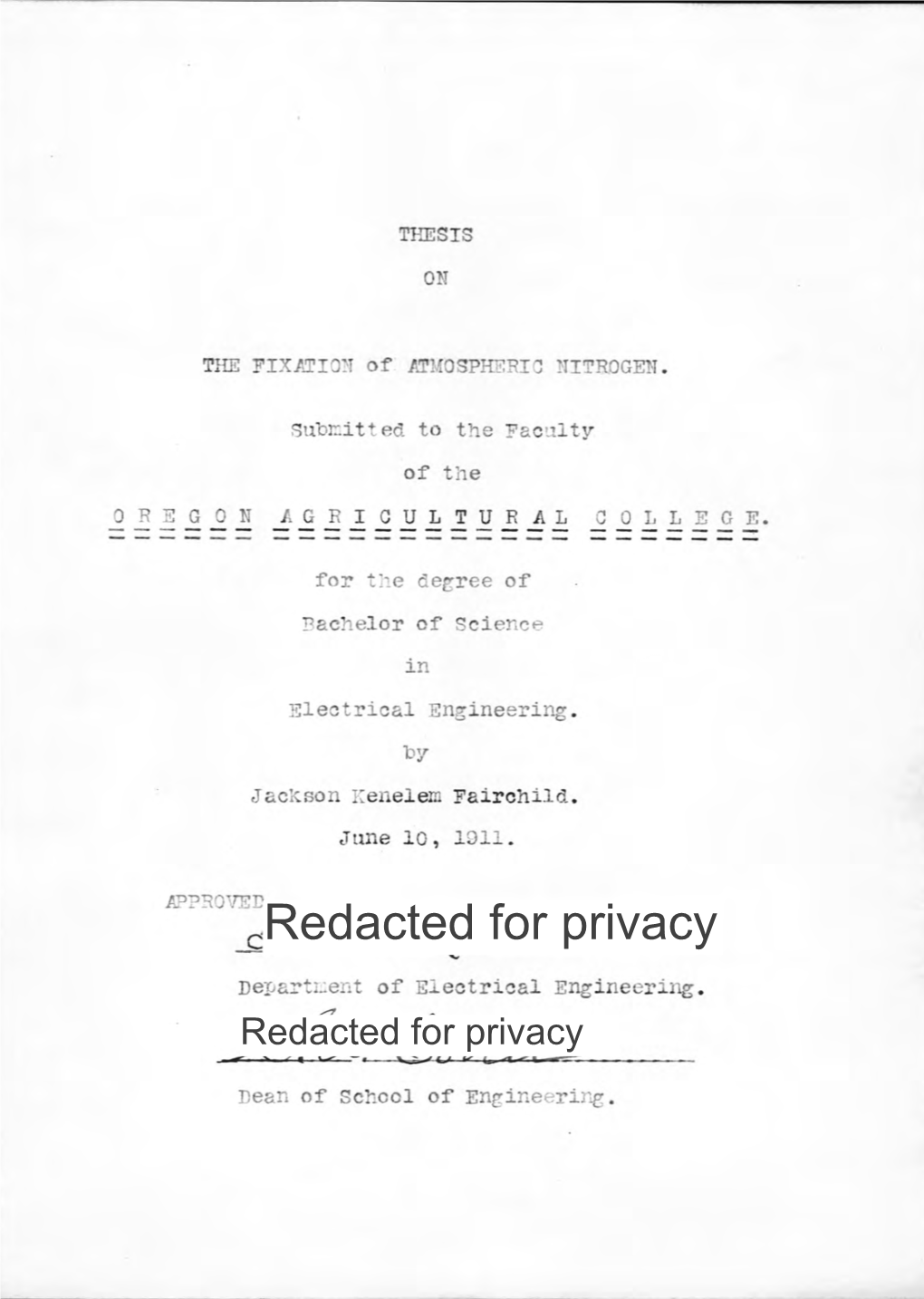
Load more
Recommended publications
-
Product Information Calcium Nitrite 94% Solution
Product Information Calcium Nitrite 94% Solution Product Description: This product is a white powder composed of 94% calcium nitrite. It is a strong oxidising agent and is highly soluble allowing it to promote hydration of minerals in cement and thus its application as an antifreeze additive in cement. Applications: Calcium nitrite is used as a metal corrosion inhibitor for steel in reinforced concrete, antifreeze in cement. It can be used as a heavy oil detergent and in thermal energy storage for air conditioning. Chemical Formula: Ca(NO2)2 CAS No. : 13780-06-8 Specifications: Parameters (units) Specifications Calcium nitrite (%) ≥ 94 Calcium nitrate (%) ≤ 5 Calcium hydroxide (%) ≤ 1.0 Moisture (%) ≤ 1.0 Water insoluble (%) ≤ 1.0 Bisley International LLC 1790 Hughes Landing Boulevard Suite 400 The Woodlands 77380 TX USA Phone number: +1 (844) 424 7539 Emergency telephone number: +1 855 237 5573 bisleyinternational.com Copyright 2021 Bisley & Co. Pty Ltd. All rights reserved Packaging: Packaging options are available upon enquiry. Storage: Product should be stored in a dry place in sealed, original packaging away from direct sunlight. Safety: For further safety information refer to product SDS available from your Bisley International contact. Disclaimer: This document is for information purposes only. Customers are responsible for testing and confirming the suitability of this product in their application. To the extent permitted by law, no warranty as to merchantability or fitness of purpose, expressed or implied, is made. Global Headquarters -
Safety Data Sheet Version 1.0 Creation Date 01/15/2015
Page 1 of 6 Safety Data Sheet Version 1.0 Creation Date 01/15/2015 www.continental-industries.com 1. PRODUCT AND COMPANY IDENTIFICATION 1.1 Product identifiers Product name : Calcium nitrite solution 1.2 Relevant identified uses of the substance or mixture and uses advised against Identified uses : Laboratory chemicals, Manufacture of substances 1.3 Details of the supplier of the safety data sheet Distributor : Continental Industries Group, Inc. 733 Third Avenue Fl. 20 New York, NY 10017 USA 1.4 Emergency telephone number Chemtel Phone # : 1-800-255-3924 International Phone # : +01-813-248-0585 2. HAZARDS IDENTIFICATION 2.1 Classification of the substance or mixture Not a hazardous substance or mixture. 2.2 GHS Label elements, including precautionary statements Not a hazardous substance or mixture. 2.3 Hazards not otherwise classified (HNOC) or not covered by GHS - none 3. COMPOSITION/INFORMATION ON INGREDIENTS 3.2 Mixtures Molecular Weight : 132.09 g/mol Component Classification Concentration Calcium nitrite CAS-No. 13780-06-8 30 - 50 % EC-No. 237-424-2 4. FIRST AID MEASURES 4.1 Description of first aid measures General advice Move out of dangerous area. Page 1 of 6 Page 2 of 6 4. FIRST AID MEASURES cont' d If inhaled If breathed in, move person into fresh air. If not breathing, give artificial respiration. In case of skin contact Wash off with soap and plenty of water. In case of eye contact Flush eyes with water as a precaution. If swallowed Never give anything by mouth to an unconscious person. Rinse mouth with water. -
Effect of a Nitrite/Nitrate-Based Accelerator on the Strength Development and Hydrate Formation in Cold-Weather Cementitious Materials
materials Article Effect of a Nitrite/Nitrate-Based Accelerator on the Strength Development and Hydrate Formation in Cold-Weather Cementitious Materials Akira Yoneyama 1, Heesup Choi 1,* , Masumi Inoue 1, Jihoon Kim 2, Myungkwan Lim 3,* and Yuhji Sudoh 4 1 Department of Civil and Environmental Engineering, Kitami Institute of Technology, Hokkaido 090-8507, Japan; [email protected] (A.Y.); [email protected] (M.I.) 2 Faculty of Environmental Technology, Muroran Institute of Technology, Hokkaido 090-8585, Japan; [email protected] 3 Department of Architectural Engineering, Songwon University, Gwangju 61756, Korea 4 Basic Chemicals Department Chemicals Division, Nissan Chemical Corporation, Tokyo 103-6119, Japan; [email protected] * Correspondence: [email protected] (H.C.); [email protected] (M.L.) Abstract: Recently, there has been increased use of calcium-nitrite and calcium-nitrate as the main components of chloride- and alkali-free anti-freezing agents to promote concrete hydration in cold weather concreting. As the amount of nitrite/nitrate-based accelerators increases, the hydration of tricalcium aluminate (C3A phase) and tricalcium silicate (C3S phase) in cement is accelerated, thereby improving the early strength of cement and effectively preventing initial frost damage. Nitrite/nitrate-based accelerators are used in larger amounts than usual in low temperature areas ◦ below −10 C. However, the correlation between the hydration process and strength development in concrete containing considerable nitrite/nitrate-based accelerators remains to be clearly identified. Citation: Yoneyama, A.; Choi, H.; In this study, the hydrate composition (via X-ray diffraction and nuclear magnetic resonance), pore Inoue, M.; Kim, J.; Lim, M.; Sudoh, Y. -
Chemical Resistance 100% SOLIDS EPOXY SYSTEMS
Chemical Resistance 100% SOLIDS EPOXY SYSTEMS CHEMICAL 8300 SYSTEM 8200 SYSTEM 8000 SYSTEM OVERKOTE PLUS HD OVERKOTE HD OVERKRETE HD BASED ON ONE YEAR IMMERSION TESTING –––––––––––––––––––––––––––––––––––––––––––––––––––––––––––––––––––––––––––– Acetic Acid (0-15%) G II Acetonitrile LLG L Continuous Immersion Acetone (0-20%) LLL Acetone (20-30%) Suitable for continuous immersion in that chemical (based on LLG Acetone (30-50%) L G I ONE YEAR testing) to assure unlimited service life. Acetone (50-100%) G II Acrylamide (0-50%) LLL G Short-Term Exposure Adipic Acid Solution LLL Alcohol, Isopropyl LLL Suitable for short-term exposure to that chemical such as Alcohol, Ethyl LLG secondary containment (72 hours) or splash and spill Alcohol, Methyl LLI (immediate clean-up). Allyl Chloride LLI Allylamine (0-20%) L L I Allylamine (20-30%) L G I I Not Suitable Allylamine (30-50%) GGI Not suitable for any exposure to that chemical. Aluminum Bromide LL– Aluminum Chloride L L – Aluminum Fluoride (0-25%) L L – This chart shows chemical resistance of our various Aluminum Hydroxide LLL 1 topping materials (90 mils – ⁄4"). These ratings are based on Aluminum Iodide LL– temperatures being ambient. At higher temperatures, chemical Aluminum Nitrate LL– resistance may be effected. When chemical exposure is Aluminum Sodium Chloride L L – minimal to non-existent, a 9000 System–FlorClad™ HD or Aluminum Sulfate LLL 4600 System– BriteCast™ HD may be used. Alums L L L 2-Aminoethoxyethanol Resistance data is listed with the assumption that the material GGG has properly cured for at least four days, at recommended Ammonia – Wet L L – temperatures, prior to any chemical exposure. -
Upplementa Ecifications
Commonwealth of Massachusetts Department of Highways SUPPLEMENTAL SPECIFICATIONS to the 1988 Standard Specifications for Highways and Bridges ENGLISH UNITS JUNE 6, 2006 SUPPLEMENTAL SPECIFICATIONS The 1988 Standard Specifications for Highways and Bridges are amended by the following modifications, additions and deletions. These are supplemental specifications, and shall prevail over those published in the Standard Specifications for Highways and Bridges This supplement incorporates all previous Error & Addenda sheets, and Supplemental Specifications, and therefore supersede all previous supplements and addenda. ALL SECTIONS Global Changes Due to recent and anticipated moves by MassHighway Research and Materials Division, replace the words Qualified Product Listing maintained by the Research and Materials Division, 400 D Street, South Boston Ma. 02110-1953, telephone number 617-526-8686 and all variations thereof with Qualified Construction Materials List available at www.mass.gov/mhd at each occurrence. Change the words Bituminous Concrete and Class I Bituminous Concrete Type I-1 to Hot Mix Asphalt at each occurrence. Change the words Cement Concrete Masonry to Cement Concrete at each occurrence. DIVISION I GENERAL REQUIREMENTS AND COVENANTS SECTION 1.00 DEFINITION OF TERMS SUBSECTION 1.02 Abbreviations. (page 3) Revise the abbreviation list to read as follows: AASHTO – American Association of State Highway and Transportation Officials ACI – American Concrete Institute AISC – American Institute of Steel Construction AISI – American Iron -
Calcium Nitrite Solution Mrd-223
Safety Data Sheet CALCIUM NITRITE SOLUTION MRD-223 * * * Section 1 - Chemical Product and Company Identification * * * Chemical Name: Inorganic Nitrite Solution Product Use: Corrosion Inhibitor Manufacturer Information Mineral Research and Development Phone: 800-454-4805 5910 Pharr Mill Road Fax: 704-455-6507 Harrisburg, NC 28075 CHEMTREC 1-800-424-9300 US and Canadian Shipment only: 1-703-527-3887 General Comments NOTE: Emergency telephone numbers are to be used only in the event of chemical emergencies involving a spill, leak, fire, exposure, or accident involving chemicals. All non-emergency questions should be directed to customer service. * * * Section 2 - Hazards Identification * * * GHS Classification Eye Damage/Irritation, Category 2B Acute Toxicity – Oral, Category 4 GHS Label Elements Symbol(s) Signal Word WARNING Hazard Statements Causes eye irritation. Harmful if swallowed. Precautionary Statements Prevention Do not breathe dust/fume/gas/mist/vapors/spray. Wash thoroughly after handling. Do not eat, drink or smoke when using this product. Response IF IN EYES: Rinse cautiously with water for several minutes. Remove contact lenses, if present and easy to do. Continue rinsing. Get medical advice/attention. IF ON SKIN (OR HAIR): Wash with plenty of soap and water. Take off contaminated clothing and wash it before ____________________________________________________________ Page 1 of 9 Issue Date: 03/10/2017 Revision: 2.0 Print Date: March 13, 2017 Safety Data Sheet CALCIUM NITRITE SOLUTION MRD-223 reuse. If skin irritation occurs: Get medical advice/attention. IF INHALED: If inhaled, remove person to fresh air and keep comfortable for breathing. Call a POISON CENTER or doctor/physician if you feel unwell. -
Environmental Assessment Registration Blasting Agents (Emulsion) Manufacturing Plant
ENVIRONMENTAL ASSESSMENT REGISTRATION BLASTING AGENTS (EMULSION) MANUFACTURING PLANT Newfoundland Hard-Rok Inc. Environmental Assessment Registration Form NAME OF UNDERTAKING: Newfoundland Hard-Rok Inc. Blasting Agent (Emulsion) Manufacturing Plant Corner Brook, NF PROPONENT: (i) Name of Corporation Body: Newfoundland Hard-Rok Inc. (ii) Address: P.O. Box 605 25 Union Street Corner Brook, NL A2H 6G1 P.O. Box 8776, Stn. “A” 21 Pippy Place St. John’s, NL A1B 3T2 (iii) Chief Executive Officer: Mr. Carl W. Foss, President Telephone: 709-639-9179 Fax: 709-639-7303 (iv) Principal contact person for Carl W. Foss, President purpose of environmental assessment Newfoundland Hard-Rok Inc. Environmental Assessment THE UNDERTAKING: The purpose of the undertaking is the construction and operation of a blasting agent (emulsion) manufacturing plant near Corner Brook, Newfoundland. (i) Nature of Undertaking: The Manufacturing Plant will produce an Emulsion Blasting Agent, which is primarily use in quarry blasting, road building, site development and mining. The two primary components used to manufacture the emulsion are ammonium nitrate and no. 2 diesel fuel oil. The plant will produce a bulk emulsion which is pumped into 20 tonne bulk tankers. The tankers are then used to transport the finished product to our satellite storage site near Northwest Brook or used for temporary storage on site. The product will then be transferred from the tankers via pumps to our bulk re-pump trucks and then delivered to the blast holes for loading. (ii) Purpose of the Undertaking: Newfoundland Hard-Rok Inc. is the exclusive distributor for Dyno Nobel Inc., for all of Newfoundland & Labrador. -
Calcium Nitrite Solution Msds Id: Mrd-112
Material Safety Data Sheet Material Name: CALCIUM NITRITE SOLUTION MSDS ID: MRD-112 * * * Section 1 - Chemical Product and Company Identification * * * Chemical Name: Inorganic Nitrite Solution Product Use: Corrosion Inhibitor Manufacturer Information Mineral Research and Development Phone: 800-454-4805 5910 Pharr Mill Road Fax: 704-455-6507 Harrisburg, NC 28075 Emergency # 1-800-424-9300 General Comments NOTE: Emergency telephone numbers are to be used only in the event of chemical emergencies involving a spill, leak, fire, exposure, or accident involving chemicals. All non-emergency questions should be directed to customer service. * * * Section 2 - Hazards Identification * * * Emergency Overview This product is a clear, light-yellow to colorless solution with a slight sweet odor. This product may cause methemoglobinemia upon ingestion characterized by cyanosis, headache, dizziness, fatigue, nausea, vomiting, drowsiness, stupor, coma and rarely death. This product is irritating to the eyes, respiratory system and skin. This product is an aqueous solution which will not burn. However, if evaporated to dryness this product is an oxidizer and can sustain combustion. Potential Health Effects: Eyes Contact with the eyes can cause moderate irritation. Symptoms may include discomfort or pain and redness. Severe over exposure can result in swelling of the conjunctiva along with tissue damage which may lead to blindness. Potential Health Effects: Skin This product is irritating to the skin. Depending on the duration of contact, symptoms will include reddening, discomfort, irritation, and possible tissue damage. Repeated contact with this material may produce dermatitis. Potential Health Effects: Ingestion This product may be harmful or fatal if swallowed. If ingested, this product will immediately cause burns to the mouth, throat, esophagus and possibly the digestive tract. -
Fundamental Understanding of Nox Sequestration
FUNDAMENTAL UNDERSTANDING OF NOX SEQUESTRATION CAPACITY AND PATHWAYS IN NANO-TIO2 ENGINEERED CEMENTITIOUS MATERIALS A Dissertation Presented to The Academic Faculty by Qingxu Jin In Partial Fulfillment of the Requirements for the Degree Doctor of Philosophy in the School of Civil and Environmental Engineering Georgia Institute of Technology December 2019 COPYRIGHT © 2019 BY QINGXU JIN FUNDAMENTAL UNDERSTANDING OF NOX SEQUESTRATION CAPACITY AND PATHWAYS IN NANO-TIO2 ENGINEERED CEMENTITIOUS MATERIALS Approved by: Dr. Kimberly E. Kurtis, Advisor Dr. Emily Grubert School of Civil and Environmental School of Civil and Environmental Engineering Engineering Georgia Institute of Technology Georgia Institute of Technology Dr. Lawrence F. Kahn Dr. Jeffrey W. Bullard School of Civil and Environmental Zachry Department of Civil and Engineering Environmental Engineering Georgia Institute of Technology Texas A&M University Dr. Yuanzhi Tang School of Earth and Atmospheric Sciences Georgia Institute of Technology Date Approved: November 1st, 2019 ACKNOWLEDGEMENTS I would like to express my utmost gratitude to my advisor Dr. Kimberly Kurtis for her insightful and priceless guidance and tutelage throughout my Ph.D. studies at Georgia Tech. I would not be able to finish my Ph.D. and become the researcher I am today without her continuous support and confidence in me all these years. I am very fortunate to have her as my advisor. I am also grateful for my thesis committee members, Dr. Lawrence Kahn, Dr. Yuanzhi Tang, and Dr. Emily Grubert, for their support and advice on both of my experimental work and dissertation writing. I want to give special thanks to an additional thesis committee member and former supervisor at National Institute of Standards and Technology (NIST), Dr. -
How DCI Works
ENGINEERING BULLETIN 5 DCI® How DCI works This engineering bulletin describes the role of corrosion inhibitors, and the way DCI® Corrosion Inhibitor controls the corrosion of steel reinforcement in concrete. The theory of corrosion is described in DCI Engineering Bulletin 1, What is Corrosion?. This bulletin is most informative if the reader has a basic understanding of corrosion or reads Engineering Bulletin 1 first. DCI Corrosion Inhibitor is a calcium nitrite-based solution. Calcium nitrite, Ca(NO2)2, is a well known inhibitor for systems requiring corrosion protection. Studies of structures in long-term service and extensive field and labora tory tests confirm its effectiveness in concrete. The Problem corrosion protection for all embedded steel and other metals. Unlike other inhibitors, calcium nitrite does not have Due to the high pH of concrete, steel in concrete is any negative effects on the physical properties of concrete. surrounded by a natural layer of iron oxide called the DCI corrosion inhibitor is classified as an ASTM C494 passivating layer, which protects the iron from rusting. Type C admixture. In the absence of aggressive ions such as chloride ions, corrosion of reinforcement does not take place. As Calcium nitrite protects steel in concrete by assisting chloride ions from saltwater or the natural defense that is already present. In an alkaline de-icing chemical reach the steel, however, they environment, steel forms an oxide from iron (Fe), oxygen undermine the oxide layer and the iron rusts. (O) and hydroxide ions (OH–). Initially, the oxide is formed with ferrous ions (Fe++). The ions are generated according In the protective ferric oxide layer that forms around to the equation: the reinforcing steel or prestressed strand, there are micro scopic ferrous oxide defects (Figure 1). -
Chemical Resistance: Deco-Fleck
CHEMICAL RESISTANCE DECO-FLECK ® SERIES 224 Tnemec Company, Inc. 6800 Corporate Drive Kansas City, Missouri 64120-1372 +1 816-483-3400 www.tnemec.com © December 16, 2019 by Tnemec Company, Inc. Chem224 Page 1 of 19 CHEMICAL RESISTANCE DECO-FLECK ® | SERIES 224 COMMON PROBLEM AREAS FOR COATINGS AND SOLUTIONS Problem: Coating Solution: Points of failure Carefully and due to thin spots fully coat in coating Problem: Rough Pinhole Solution: Uneven Undercut Grind smooth welds Problem: Gaps between Solution: plates, coating Continuous can not cover welds Problem: Gaps between Solution: plates, coating Continuous can not cover welds Problem: Coating Sharp surface Solution: contours create Round the thin spots in contours coating Problem: Skip welding Solution: creates gaps Continuous that coating welds can not cover Problem: Skip welding Solution: creates gaps Continuous that coating welds can not cover 2 channels back to back IMPORTANT: Definitions for the terms and acronyms used in this guide to describe the recommended exposures, along with other important information, can be found on the cover page of this guide or by contacting Tnemec Technical Service. Coatings should not be applied in a chemical exposure environment until the user has thoroughly read and understood the product information and full project details have been discussed with Tnemec Technical Service. Tnemec Company, Inc. 6800 Corporate Drive Kansas City, Missouri 64120-1372 +1 816-483-3400 www.tnemec.com © December 16, 2019 by Tnemec Company, Inc. Chem224 Page 2 of 19 CHEMICAL RESISTANCE DECO-FLECK ® | SERIES 224 ¹ Product is NOT suitable for direct or indirect food contact. Intended Use and temperature information relates to product’s performance capabilities only. -
The Fundamental Study on the Expansion and Shrinkage Behaviors of Concrete Using Nitrite-Based Accelerator Miwa Iwasawa , Masumi
The fundamental study on the expansion and shrinkage behaviors of concrete using nitrite-based accelerator Miwa Iwasawa1), Masumi Inoue2), Heesup Choi3) and Yuhji Sudoh4) 1), 2), 3) Department of Civil and Environmental Engineering, Kitami Institute of Technology, Kitami, Japan 4) Chemicals Division. Basic Chemicals Department, Nissan Chemical Industries, Ltd., Tokyo, Japan 1) [email protected] ABSTRACT In the preparation of concrete that can withstand cold weather conditions, a non- freezing agent is added to prevent initial frost damage by simplified curing and promote strength development at an early stage. In general, a nitrite-based accelerator is used as the main component of this non-freezing agent. When a large proportion of accelerator is used, expansion and shrinkage of the concrete are increased as hydration of C3S (alite, 3CaO·SiO2) and C2S (belite, 2CaO·SiO2) is promoted from the beginning. If the transformation of the concrete becomes big, it will affect the durability for crack propagation in the long term. In this study, we conducted fundamental research to clarify the effect of a large amount of nitrite-based accelerator on the expansion and shrinkage characteristics and strength development of concrete. As the addition amount of nitrite-based accelerator was increased, the hydration of the cement was rapidly promoted, and the expansion increased from over a long period, even after curing in an environment with temperature at -10 °C environment; the amount of C–S–H gel produced by the hydration eventually exceeded the amount of Ca(OH)2. Moreover, the void structure ratio gradually decreased. These changes were found to greatly affect the strength development of concrete.