Design and Simulation of Traction Power Supply System: Case Study of Modjo~Hawassa Line
Total Page:16
File Type:pdf, Size:1020Kb
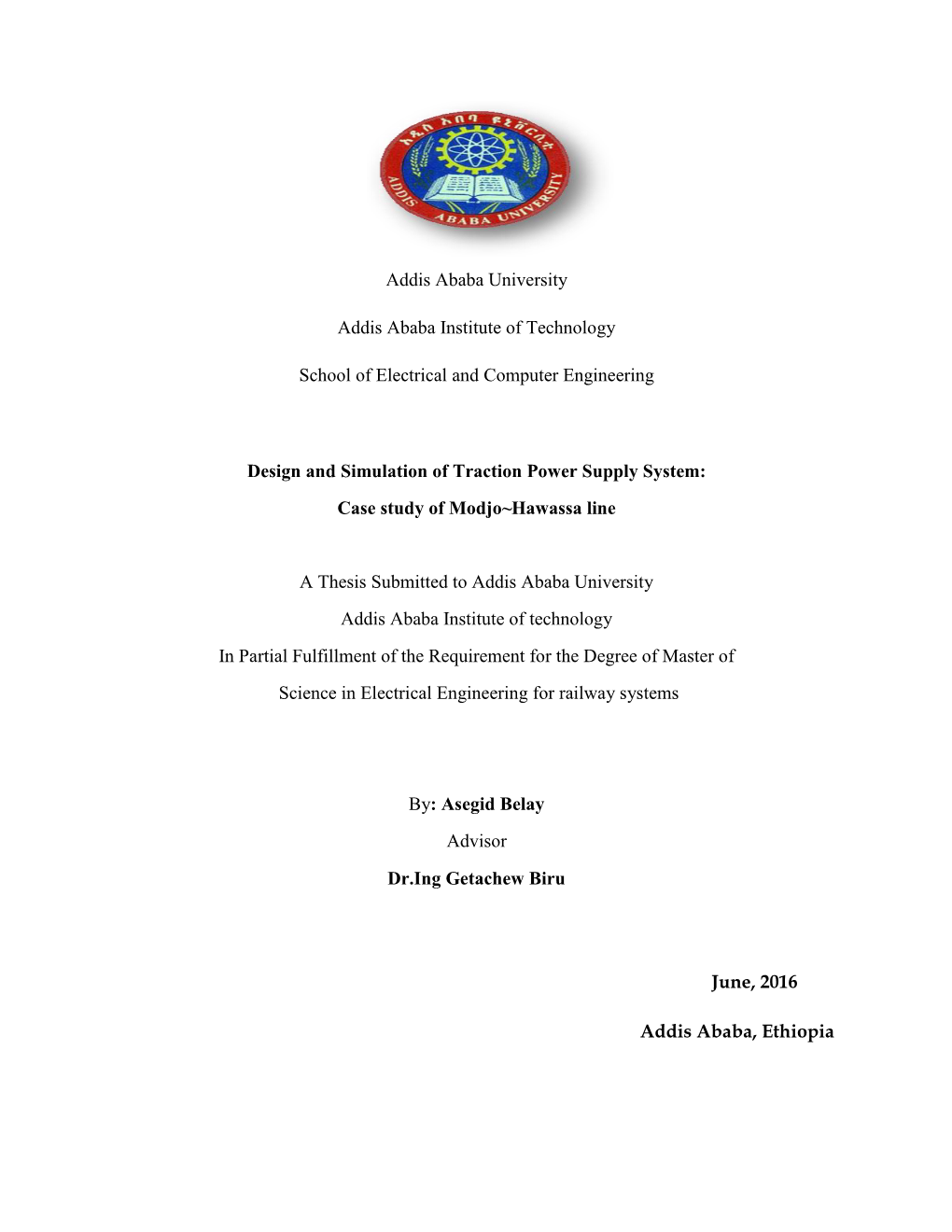
Load more
Recommended publications
-
Enginyeria Industrial Jordi Garriga Turu Comparative Study Between
Titulació: Enginyeria Industrial Autor: Jordi Garriga Turu Títol del PFC: Comparative study between an alternating current (AC) and a direct current (DC) electrification of an urban railway Directora del PFC: Meritxell Cusidó Roura Entitats col·laboradores: Convocatòria de lliurament del PFC: Gener 2015 Contingut d’aquest volum: -MEMÒRIA- Acknowledgements First of all I would like to thank Meritxell Cusidó, the director of this study and colleague, for her help, advice and dedication throughout all the study process. Her planning has helped me to structure this work properly and reach the end in the scheduled period of time. In second place I feel grateful to Mr. Antoni Maestre, of Ferrocarrils de la Generalitat de Catalunya, who has shared with me all the necessary data to perform the present study. His advices, technical knowledge and vast experience in railway technologies have helped me to comprehend better how a railway maintenance and operation is carried out. I want to thank as well all my colleagues in Sener, specially Javi and Martí, who have taken part in the consecution of this study with their technical knowledge, advice and patience. 4 Jordi Garriga Turu Comparative study between an alternating current (AC) and a direct current (DC) electrification of an urban railway Contents 1 Object of the Study ................................................................................................................ 5 2 Justification ........................................................................................................................... -
Assessment of AC Traction Substation Influence on Energy Quality in A
TECHNICAL TRANSACTIONS 12/2018 ELECTRICAL ENGINEERING DOI: 10.4467/2353737XCT.18.183.9671 SUBMISSION OF THE FINAL VERSION: 19/11/2018 Włodzimierz Jefimowski [email protected] Adam Szeląg Warsaw University of Technology, Power Engineering Institute, Electric Traction Division Assessment of AC traction substation influence on energy quality in a supplying grid Ocena oddziaływania podstacji trakcyjnej prądu przemiennego na jakość energii elektrycznej w sieci zasilającej Abstract This article presents investigations performed on a 25 kV AC system with a Scott transformer simulation model. The model includes an energy quality parameter calculation algorithm with consideration to the train timetable. The simulation results enable an analysis of the energy quality parameters at the point of connection of the traction substation to the supplying grid. The presented tool enables the simultaneous calculation of voltage unbalance and harmonic content. The article presents the results of the energy quality analysis at the substation connection point for the specific location. The simulation results of the energy quality parameters are appraised on the basis of standard EN 50160:2010. The tool may prove helpful in the process of designing electrification systems, especially in the choice of traction transformer and power electronics device mitigating an imbalance and harmonic impact. Streszczenie Keywords: AC electrification system, electric energy quality, simulation modelling, Scott transformer Artykuł przedstawia badania przeprowadzone z wykorzystaniem modelu symulacyjnego systemu zasilania prądu przemiennego 25 kV 50 Hz z transformatorem Scotta, uwzględniającym wszystkie czynniki jakości energii elektrycznej przy uwzględnieniu rozkładu jazdy pociągów. Wyniki badań pozwalają na kompleksową analizę parametrów jakości energii w punkcie przyłączenia podstacji trakcyjnej do systemu elektroenergetycznego przy uwzględnieniu rozkładu jazdy pociągów oraz rodzaju taboru. -
Scanned Document
Report No. DOT/TSC-1452-3 A SURVEY OF RAILROAD AC ELECTRIFICATION SYSTEMS ,l THROUGHOUT THE WORLD Jeffrey J. LaMarca Charles M. King Alexander Kus ko January 25. 1979 Final Report Prepared for: U. S. Department of Transportation Federal Railroad Administration Office of Research and Development Washington, DC 20590 Alexander Kuske, Inc. 161 Highland Avenue Needham Heights, Mass. 02194 Technical Report Documentation Page 1. Report No. 2. Cavernm~nt Accession No. 3. Reeipient' s Catalog No. DOT/ TSC-1452-3 4. Title and Subtitle 5. Report Date "A Survey of Railroad AC Electrification Systems January 25, 1979 Throughout the World" 6. Performing Organization Code 8. P erf~rming Organization Report No. 7. Author's) LaMarca, J. J.' King, C. M., Kusko, A. 9. ?,.,forming Organization Name and Address 10. Work Unit No. (TRAIS) Alexander Kusko, Inc . ....,. 161 Highland A venue 11. Contract or Grant No. Needham Heights, MA 02194 DOT/ TSC-1452 13. Type of Report and Period Covered 12. Sponsoring Agency Nome and Address Final Report u.s. Department of Transportation July 1978 - January 1979 Federal Railroad Administratlon Office of Research and Development 14. Sponsoring Agency Code Washi_mrton DC 20!i!10 ; 15. Supplementary Notes ~:;Under contract to: u.s. Department of Transportation Technical Monitor: FrankL. Raposa Transportation Systems Center K.:>r~r1!:!l1 c;:,.,,,!:!.,..o (" !'!.,..,.., ]-,,... • r'f n"C> i\IT" n? 1 !l'J 16. Abstract . 0 This report describes the major features of various railroad electrification schemes for supplying the catenary from the source of power for ac operation. These features include: details of the pow'er source, high-voltage substation connections, substation details, catenary-to-substation connections, track sectioning methods, and any other special electrification features. -
Analysis 1520
DOCUMENT APPROVED BY THE CONTACT GROUP (28/01/2010 V1.00) ANALYSIS OF DETERMINATIVE PARAMETERS FOR MAINTAINING THE TECHNICAL AND OPERATIONAL COMPATIBILITY OF 1520 mm and 1435 mm GAUGE RAILWAY SYSTEMS AT THE CIS- EU BORDER SUBSYSTEM: POWER SUPPLY Document produced by the ORC-ERA Contact Group 2010 DOCUMENT APPROVED BY THE CONTACT GROUP (28/01/2010 V1.00) REVISIONS AND AMENDMENTS Revision and Sections Note Author date 0.00/ 19/03/2009 All Working paper, scope of application, list of FAD parameters 0.01/ 14/05/2009 4, 5 Working paper, based on materials received FAD to 14/05/2009. 0.02/ 20/05/2009 5 Working paper, based on meeting of FAD 20/05/2009. VK 0.03/ 18/09/2009 4, 5 Working paper, based on material received FAD to 18/09/2009 0.04/ 01/10/2009 5, 6 Working paper, based on meeting of FAD 01/10/2009. VK 0.05/ 18/01/2010 2, 3. 5, 6 Draft for approval at meeting of 26- FAD 28/01/2010 1.00/ 28/01/2010 2, 3, 5 Document approved by the contact group FAD VK Analysis of determinative parameters for maintaining technical and operational compatibility with 1520 mm gauge systems at the CIS-EU border. Subsystem: Energy. 1/54 DOCUMENT APPROVED BY THE CONTACT GROUP (28/01/2010 V1.00) CONTENTS 1 SCOPE OF APPLICATION. .................................................................................................................. 5 2 REGULATORY (BASELINE) DOCUMENTS ........................................................................................... 6 3 TERMS AND ABBREVIATIONS ........................................................................................................ -
A Planning Method for Electric Infrastructure to Supply Multimodal Transportation Systems
Energy and Sustainability VII 213 A PLANNING METHOD FOR ELECTRIC INFRASTRUCTURE TO SUPPLY MULTIMODAL TRANSPORTATION SYSTEMS ANDRÉS E. DIEZ1, MELISSA RODRIGUEZ1, DANIEL A. ARROYAVE1, DIEGO A. MÚNERA1, JOSE V. RESTREPO1 & LUÍS E. CASTRILLON2 1Universidad Pontificia Bolivariana 2Metro de Medellín, Colombia ABSTRACT The paper presents a method to determine the proper infrastructure to supply electric energy for multimodal public transportation networks. The method integrates computational simulation tools in order to precisely calculate the power demand of each public transit system, and then, by accumulating the individual consumptions, obtain the global power system demand. The method is applied to the multimodal network operated by Metro de Medellin, which at the moment is experiencing an expansion. Keywords: electric mobility, electrical demand, transport electrification, electric transportation modes, metro, tramway, cable car, trolleybus. 1 INTRODUCTION Massive public transport systems that operate connected to an electric power grid will continue to be the core of transportation in large cities, as various research papers [1]–[4] point. Electricity supply networks will be increasingly clean because of the incorporation of renewable energies and more intelligent allowing to optimize vehicle-vehicle and vehicle- network energy exchanges. Despite the intensive work and research in developing grid-free vehicles using energy storage technologies, multimodal networks that combines different kind of electric vehicles and mobility alternatives -
The Efficiency Improving of Traction Drive Test Bench with Supercapacitor Energy Storage System
Journal of Mathematics and System Science 2 (2012) 570-575 D DAVID PUBLISHING The Efficiency Improving of Traction Drive Test Bench with Supercapacitor Energy Storage System Genadijs Zaleskis and Viesturs Brazis Institute of Industrial Electronics and Electrical Engineering, Riga Technical University, 1 Kronvalda blvd., Riga LV-1010, Latvia Received: July 03, 2012 / Accepted: August 20, 2012 / Published: September 25, 2012. Abstract: For development of passenger electrical transport, it is necessary to use energy more rationally. One of methods of vehicle power efficiency increase is installation of on-board energy storage systems. For studying of system operation, it is necessary to carry out a lot of experiments, therefore it is favorable to use the test bench and its computer model for reduction of the number of physical experiments. In this article, the results of computer modeling for the optimization of traction drive test bench by adjusting of the operation parameters of supercapacitor energy storage are described. Test bench operation is considered in cases of the energy storage system working at various selected supercapacitor initial voltages. Maximal increase of possibility of vehicle test bench regenerative braking with minimal decrease of autonomous power supply mode possibility is investigated. There is estimated the energy storage system efficiency improving measures dependence from supercapacitor operational voltage ranges. Parameters at which the minimum losses of energy are observed are revealed. Dependence of energy storage system discharge power on the most admissible supercapacitor current is established. Key words: Energy storage, supercapacitor, test bench, computer modeling, passenger electrical transport. 1. Introduction at the wrong choice of parameters or control methods therefore the computer model [12] of the bench by Further development of passenger electrical means of which it is possible to choose the most transport demands more rational use of energy. -
A Review of the Energy Efficiency Improvement in DC Railway Systems
energies Review A Review of the Energy Efficiency Improvement in DC Railway Systems Mihaela Popescu * and Alexandru Bitoleanu Department of Electromechanics Environment and Applied Informatics, Faculty of Electrical Engineering, University of Craiova, 200585 Craiova, Romania; [email protected] * Correspondence: [email protected] Received: 14 February 2019; Accepted: 18 March 2019; Published: 21 March 2019 Abstract: This study is focused on the topical issue of increasing the energy efficiency in DC railway systems, in the context of global concerns for reducing the CO2 emissions by minimizing the energy consumption and energy loss. The main achievements in this complex issue are synthesized and discussed in a comprehensive review, emphasizing the implementation and application of the existing solutions on concrete case studies. Thus, all specific subtopics related to the energy efficiency are covered, starting with power quality conditioning and continuing with the recovery of braking energy, of which a large part is lost in the classic DC-traction substations. The solutions of onboard and wayside storage systems for the braking energy are discussed and compared, and practical examples are given. Then, the achievements in transforming the existing DC-traction substations in reversible substations with capabilities of power quality improvement are systematically reviewed by illustrating the main results of recent research on this topic. They include the equipment available on the market and solutions validated through implementations on experimental models. Through the results of this extensive review, useful reference and support are provided for the research and development focused on energy efficient traction systems. Keywords: DC-traction; energy efficiency; power quality; braking energy recovery; onboard energy storage; wayside energy storage; reversible substation 1. -
Traction Power Supply Substations
Simulation Model for Driving Dynamics, Energy Use and Power Supply RUI SEQUEIRA DE FIGUEIREDO (Licenciado em Engenharia Eletrotécnica) Dissertação para a obtenção do grau de Mestre em Engenharia Eletrotécnica – ramo de Energia Orientador: Professor Doutor Miguel Cabral Ferreira Chaves Júri: Presidente: Professor Doutor José Manuel Prista do Valle Cardoso Igreja Vogais: Professor Doutor Miguel Cabral Ferreira Chaves Professor Doutor Paulo José Duarte Landeiro Gamboa Março de 2015 Resumo Descritivo da Dissertação de Mestrado Resumo O objetivo deste trabalho é o de simular a interação entre o sistema de alimentação de tração elétrica e o planeamento dos veículos de tração. Para efetuar a simulação do sistema de tração elétrica foram utilizados modelos bem como métodos de cálculo simplificados para a dinâmica de condução e uso de energia do veículo e para o sistema de alimentação elétrico da rede de energia. Preliminarmente houve necessidade de efetuar uma análise detalhada aos softwares comerciais existentes com o intuito de se poderem analisar as diversas aplicações bem como as demais funcionalidades. Os modelos e os métodos de cálculo utilizados pelos mesmos foram igualmente objeto de estudo sendo de igual modo caracterizados. A maioria das aplicações existentes usam normalmente dois tipos de modelos (macroscópico ou microscópico). Embora o modelo microscópico apresente maior complexidade será este que reproduz a operação real do sistema ao longo do tempo. Conforme foi referido anteriormente os métodos de calculo estudados tiveram como principal objetivo a obtenção do conhecimento de interligação do sistema do veículo de tração com o sistema de alimentação de tração elétrica. Verificou-se que os softwares comerciais usam primariamente métodos interativos. -
Microprocessor Control Systems of Light Rail Vehicle Traction Drives
THESIS ON POWER ENGINEERING, ELECTRICAL ENGINEERING, MINING ENGINEERING D25 MICROPROCESSOR CONTROL SYSTEMS OF LIGHT RAIL VEHICLE TRACTION DRIVES MADIS LEHTLA TALLINN 2006 Faculty of Power Engineering Department of Electrical Drives and Power Electronics TALLINN UNIVERSITY OF TECHNOLOGY Dissertation was accepted for the commencement of the degree of Doctor of Technical Science on July 6, 2006 Supervisor: Juhan Laugis, Prof., Dr.Sc., Department of Electrical Drives and Power Electronics, Tallinn University of Technology Opponents: Professor Nikolai Iljinski, Dr.Sc., Moscow University of Power Engineering, Russia Professor Johannes Steinbrunn, Dr.-Ing., Dr.h.c. Thammasat University, Thailand; Kempten University of Applied Sciences, Germany Tõnu Pukspuu, Ph.D, Chairman of Board, SystemTest Ltd., Estonia Commencement: September 11, 2006 Declaration: Hereby I declare that this doctoral thesis is my original investigation and achievement, submitted for the doctoral degree at Tallinn University of Technology, has not been submitted for any degree or examination. Madis Lehtla, ................................... Copyright Madis Lehtla 2006 ISSN 1406-474X ISBN 9985-59-642-0 PREFACE This work relates to a long-term research experience at the department of Electrical Drives and Power Electronics in the field of drives in electrical transport. I would like to thank all of my colleagues who were involved in the research or development work of electrical drives in 1998-2006. I would like to thank in particular my supervisor professor Juhan Laugis and colleague Jüri Joller who faced the main difficulties at project start-up and helped to solve practical problems encountered in the application of results on trams. The application of the drive with a new and original power circuit was possible thanks to support from Mr. -
Optimising Power Management Strategies for Railway Traction Systems by Shaofeng Lu
Optimising Power Management Strategies for Railway Traction Systems by Shaofeng Lu A thesis submitted to The University of Birmingham for the degree of DOCTOR OF PHILOSOPHY School of Electronic, Electrical and Computer Engineering College of Engineering and Physical Sciences The University of Birmingham, UK October 2011 University of Birmingham Research Archive e-theses repository This unpublished thesis/dissertation is copyright of the author and/or third parties. The intellectual property rights of the author or third parties in respect of this work are as defined by The Copyright Designs and Patents Act 1988 or as modified by any successor legislation. Any use made of information contained in this thesis/dissertation must be in accordance with that legislation and must be properly acknowledged. Further distribution or reproduction in any format is prohibited without the permission of the copyright holder. Abstract Railway transportation is facing increasing pressure to reduce the energy demand of its vehicles due to increasing concern for environmental issues. This thesis presents studies based on improved power management strategies for railway traction sys- tems and demonstrates that there is potential for improvements in the total system energy efficiency if optimised high-level supervisory power management strategies are applied. Optimised power management strategies utilise existing power sys- tems in a more cooperative and energy-efficient manner in order to reduce the total energy demand. In this thesis, three case studies in different research scenarios have been conducted. Under certain operational, geographic and physical constraints, the energy con- sumed by the train can be significantly reduced if improved control strategies are implemented. -
Ie1iect.Ion of Low Current Short Grc.Uits
L'EJC-5®E R--jl E IR- Sli RESE E Lr®IPjVE Ie1iect.ion of Low Current Short Grc.uits CP NATIONAL RESEARCCOUNCIL TRANSPORTATION RESEARCH BOARD EXECUTIVE COMMITTEE 1984 Officers Chairman JOSEPH M. CLAPP, Senior Vice President. Roadway Express. Inc Vice Chairman JOHN A. CLEMENTS. Commwioner, New Hampshire Department of Public Works and Highways Secretary - THOMAS B. DEEN, Executive Director. Transportation Research Board Members RAY A. BARNHART, Federal Highway Administrator. (1.5 Department of Transportation (cx officio) Past Chairman. 1983) LAWRENCE D. DAHMS. Executive Director. Metropolitan Transportation Commission. Berkeley. California (cx officio, MICHAEL J. FENELLO. Acting Federal Aviation Administrator, U.S. Department of Transportation (cx officio) FRANCIS B. FRANCOIS, Executive Director. American Association of State Highway and Transportation Officials (cx officio) WILLIAM I. HARRIS, JR., Vice President for Research and Test Department, Association of American Railroads (cx officio) DARRELL V MANNING, Director, Idaho Transportation Department (cx officio, Past Chairman 1982) RALPH STANLEY, Urban Mass Transportation Administrator. U.S. Department of Transportation (cx officio) DIANE STEED, National Highway Traffic Safety Administrator. US Department of Transportation (cx officio) DUANE BERENTSON, Secretary. Washington State Department of Transportation JOHN R. BORCHERT, Regents Professor. Department of Geography. University of Minnesota LOWELL K. BRIDWELL, Secretary. Maryland Department of Transportation ERNEST E. DEAN, Executive Director. Dallas/Fort Worth Airport MORTIMER L. DOWNEY, Deputy Executive Director for Capital Programs, Metropolitan Transportation Authority. New York ALAN G. DUSTIN, President and Chief Executive Officer. Boston and Maine Corporation MARK G. GOODE, Engineer-Director. Texas State Department of Highways and Public Transportation LESTER A. HOEL, Hamilton Pvfessor, Chairman. Department of Civil Engineering. -
15-00101-Ajeb Addendum 2.Pdf
Questions and Answers RFP No. 15-00101-AJEB Addendum #2 RFP Section Number (page) Question Answer Is SEPTA hosting another TPSS site visit? If so, can you please A TPSS site visit was held on September 10th, and all RFP-holders 1 General: site visit forward information ASAP? were notified. 1. This refers to any means of transportation the contractor will It is stated on page 7 of the RFP that automobile liability use. coverage should be not less than $5 million combined single limit per claim. 2 General: Insurance 2. We will need to see evidence of the required insurance from the Does this referred to firm-owned vehicles only? Please clarify coverage contractor with whom SEPTA has the agreement. for non-owned vehicles and firms providing services that do not use onsite vehicles (i.e. all in the office…). As a result of the likely disruption of normal business operations during the Pope’s visit towards the end of September, will SEPTA entertain The proposal due date will be extended 2 weeks to October 14th. 3 General: proposal extension changing the due date for the proposal from 30 September to 7 October? Would SEPTA consider a proposal due date extension by one week to allow sufficient time for incorporation of potential RFP changes due to Please see response to question #3. 4 General: proposal extension question responses, as well as potential Papal visit impacts to production? Does SEPTA envision any upgrades to the existing control center No. 5 General: Control Center systems (i.e. City Power SCADA) as part of this effort? Does the scope of work include evaluating the catenary structures No.