Colour 3D/4D Printing for Film
Total Page:16
File Type:pdf, Size:1020Kb
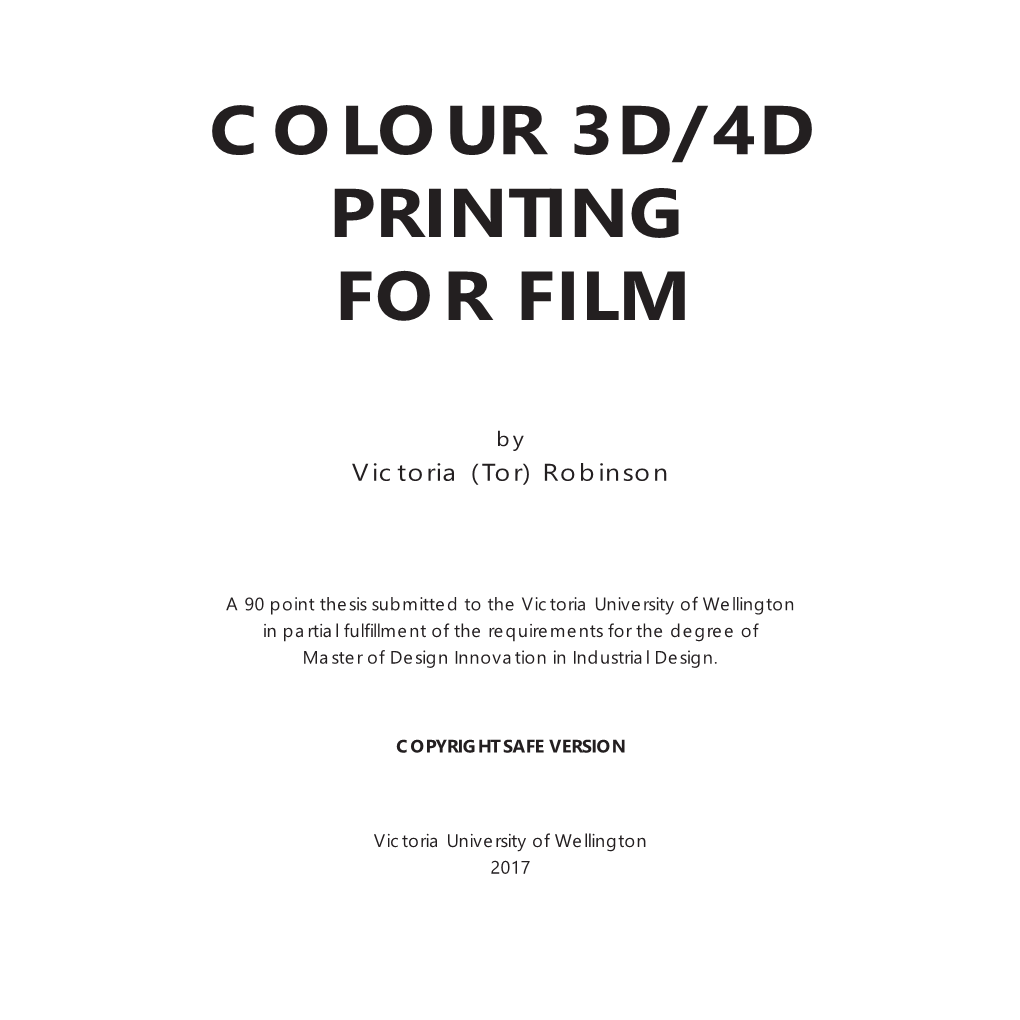
Load more
Recommended publications
-
SFU Thesis Template Files
“To Fight the Battles We Never Could”: The Militarization of Marvel’s Cinematic Superheroes by Brett Pardy B.A., The University of the Fraser Valley, 2013 Thesis Submitted in Partial Fulfillment of the Requirements for the Degree of Master of Arts in the School of Communication Faculty of Communication, Art, and Technology Brett Pardy 2016 SIMON FRASER UNIVERSITY Summer 2016 Approval Name: Brett Pardy Degree: Master of Arts Title: “To Fight the Battles We Never Could”: The Militarization of Marvel’s Cinematic Superheroes Examining Committee: Chair: Frederik Lesage Assistant Professor Zoë Druick Senior Supervisor Associate Professor Adel Iskander Supervisor Assistant Professor Michael Ma External Examiner Faculty Member Department of Criminology Kwantlen Polytechnic University Date Defended/Approved: June 16, 2016 ii Abstract The Marvel comics film adaptations have been some of the most successful Hollywood products of the post 9/11 period, bringing formerly obscure cultural texts into the mainstream. Through an analysis of the adaptation process of Marvel Entertainment’s superhero franchise from comics to film, I argue that a hegemonic American model of militarization has been used by Hollywood as a discursive formation with which to transform niche properties into mass market products. I consider the locations of narrative ambiguities in two key comics texts, The Ultimates (2002-2007) and The New Avengers (2005-2012), as well as in the film The Avengers (2012), and demonstrate the significant reorientation of the film franchise towards the American military’s “War on Terror”. While Marvel had attempted to produce film adaptations for decades, only under the new “militainment” discursive formation was it finally successful. -
Character Creation
LEARN THE ART & TECHNOLOGY OF CHARACTER CREATION 1 TABLE OF CONTENTS Mission Statement 3 History 4 Course Subjects 6 Live Webcourses 8 On-Demand Courses 12 Group Subscriptions 14 Supplemental Content 17 Our Instructors 19 Administration 21 Special Projects 23 Press 25 Testimonials 27 F.A.Q. 29 2 MISSION STATEMENT Our mission is to inspire and foster creativity. STAN WINSTON SCHOOL is the world's premiere online destination for learning the art & technology of character creation from Award-winning Industry Professionals. 3 “With Stan Winston School, Stan's philosophy of honoring the artist and celebrating imagination is being passed on to a new generation of artists.” - JAMES CAMERON, Director The Terminator, Aliens, Titanic, Avatar “I rode his cutting edge from teddy bears to aliens to dinosaurs. My world would not have been the same without Stan Winston” - STEVEN SPIELBERG, Director Jurassic Park, E.T: The Extraterrestrial, Jaws HISTORY 4 HISTORY For over 40 years, the name Stan Winston has been synonymous with innovation in the arts and sciences of character creation. A visionary pioneer, Winston helped build the foundation for many of the techniques that fill today's blockbuster films. From the “Terminator” to “Aliens,” “Predator,” “Jurassic Park,” “Iron Man,” and “Avatar,” Winston created unforgettable cinematic icons that terrify, entertain and inspire, earning him four Academy Awards in a career spanning four decades. Stan Winston School is determined to realize Winston’s vision for future generations by connecting his many protégés – themselves film industry leaders – with aspiring artists and character creators worldwide. 5 “The amount and breadth of educational material provided by SWSCA is really remarkable.” - ANDREW LEE, Student Stan Winston School of Character Arts “It's too bad they don't offer an Academy Award for arts education, you guys would get it. -
Terminator Genisys – Pressbook Italiano
Terminator Genisys – pressbook italiano 1 Terminator Genisys – pressbook italiano PARAMOUNT PICTURES e SKYDANCE PRODUCTIONS Presentano Con ARNOLD SCHWARZENEGGER, JASON CLARKE, EMILIA CLARKE, JAI COURTNEY, J.K. SIMMONS MATTHEW SMITH, e BYUNG-HUN LEE. Regia di ALAN TAYLOR Sceneggiatura di LAETA KALOGRIDIS & PATRICK LUSSIER Prodotto da DAVID ELLISON e DANA GOLDBERG Produttori Esecutivi BILL CARRARO, LAETA KALOGRIDIS, PATRICK LUSIER, MEGAN ELLISON e ROBERT CORT Direttore della Fotografia KRAMER MORGENTHAU, ASC Uscita Italiana: 9 Luglio 2015 Durata del Film: 119 minuti Il materiale fotografico è disponibile sul sito www.upimedia.com http://www.terminatorgenisys.it/ twitter.com/universalpicsit Facebook: www.facebook.com/TerminatorGenisys.IT Ufficio Stampa Universal Pictures International Italy: Cristina Casati – [email protected] Marina Caprioli – [email protected] Simone Raineri – [email protected] 2 Terminator Genisys – pressbook italiano Note di Produzione Quando John Connor (Jason Clarke), leader della resistenza umana, spedisce indietro nel tempo nel 1984 il Sergente Kyle Reese (Jai Courtney) per proteggere Sarah Connor (Emilia Clarke) e salvaguardare il futuro, un evento inaspettato crea una frattura nella linea temporale. Così, il Sergente Reese si ritroverà in un passato nuovo e sconosciuto, in cui dovrà fronteggiare improbabili alleati, tra cui un nuovo terminator T-800, il Guardiano (Arnold Schwarzenegger), nuovi pericolosi nemici, ed una nuova missione inaspettata: Per ripristinare il futuro ... Paramount Pictures e Skydance Productions presentano "Terminator Genisys", con Arnold Schwarzenegger, Jason Clarke, Emilia Clarke, Jai Courtney, J.K. Simmons Matthew Smith, e Byung-hun Lee. "Terminator Genisys" è diretto da Alan Taylor, e scritto da Laeta Kalogridis e Patrick Lussier. E' prodotto da David Ellison e Dana Goldberg. -
The Massive Adventures of Massive Guy : the Orange Avenger Unleashed Pdf, Epub, Ebook
THE MASSIVE ADVENTURES OF MASSIVE GUY : THE ORANGE AVENGER UNLEASHED PDF, EPUB, EBOOK David Newton Zimmerman | 128 pages | 06 Jun 2013 | Createspace Independent Publishing Platform | 9781484935828 | English | none The Massive Adventures of Massive Guy : The Orange Avenger Unleashed PDF Book The thing with Galactus is, though, his size and cosmic nature means that he never engages in hand to hand combat; nor does he need to. Sweeper uncredited Jasmine With Avengers Disassembled What If? After a brief career in propaganda and saving his best friend, Rogers begins to take the fight to the evil forces of the Nazi organization HYDRA and its dictatorial leader Red Skull, who seeks a source of dangerous power to help him destroy the world. Savage Avengers 16 Duggan , Zircher. Scared Spectator uncredited. Agent Maria Hill. Civilian uncredited. By Ana Dumaraog Nov 01, That may start to come close to describing Thanos, who is often considered one of the biggest Marvel villains ever created. Warpath will next be seen in the upcoming "Weapon X" series. Sign In. Brownstown, MI. Cell Home Work. Agent uncredited Mayank Bhatter History of the Marvel Universe. Tall Thug M'laah Kaur Singh Beer Garden Patron uncredited Caleb Pieplow New York Police Officer in Firefight uncredited. Of course, the Hulk got nothing but 7 s in every one of his trading card appearances. Also known as the Mad Titan, Thanos was responsible for the near destruction of his own home planet and his people. That didn't last long, however. Loading Something is loading. Don't let his size fool you. Museum Gala Patron uncredited Josh Heileman Limo Driver uncredited Todd Manes In that second Thor movie, Jane Foster absorbed the Aether into her body after she made physical contact with it. -
2015 Feature Film Production Study Follows the Same Methodology and Tracks the Feature Films Released Theatrically Within the U.S.1 During the 2015 Calendar Year
2015 FEATURE FILM STUDY ABOUT THIS REPORT For the last three years, FilmL.A. Research has endeavored to track the movies released in 2013, 2014 and now 2015 to determine where they were filmed, why they filmed in the locations they did and how much was spent to produce them. The 2015 Feature Film Production Study follows the same methodology and tracks the feature films released theatrically within the U.S.1 during the 2015 calendar year. Where possible, FilmL.A. tracks primary and secondary filming locations, primary and secondary locations for postproduction/visual effects (VFX) work, production spending and jobs. Total box-office revenues reached a record high in 2015, with global box office ticket sales hitting $38 billion. For the third 6255 W. Sunset Blvd. year in a row, despite more than 700 movies released in 2015, a 12th Floor relative handful accounted for most of the global revenue. The Hollywood, CA 90028 top 50 films of 2015 pulled in $22.4 billion worldwide; the top 25 films raked in almost $18 billion and just the top five films took in $7.8 billion. In 2015, only two of the top 25 films at the worldwide http://www.filmla.com/ box-office (Taken 3 and Maze Runner: The Scorch Trials) had @FilmLA budgets below $70 million; none had budgets below $40 million. Most of the films were produced between 2013 and 2015. From FilmLA an economic perspective, these are valuable projects, costing FilmLAinc significant sums to produce and employing many people during production. CREDITS: Of the 109 movies (see Appendix A for complete list) released by the Majors and Mini-Majors, reported production budgets ranged Research Analyst: from $1 million to over $300 million. -
Vanarts at Vancouver ACM SIGGRAPH SPARK FX Festival 2009
VanArts at Vancouver ACM SIGGRAPH SPARK FX Festival 2009 SPARK FX 09 10 Films, 18 Speaking Events, 6 Days, 1 Fantastic Festival January 21 - January 26, 2009 http://siggraph.ca/events/archive/2009/01/SPKFX09TMP.php VanArts had an impressive presence at this year’s premier Vancouver Visual Effects festival, now in its 2nd year, and the festival had an equally impressive impact on VanArts. VanArts faculty members Ken Priebe, Admissions Director, and Doug Smith, VFX Department Head, (bios below,) were heavily involved in the organizing and managing of SPARK ’09 as members of the various committees that were responsible for creating the event, and the school itself was the sole academic sponsor in the show. VanArts students were by far the largest single organization represented in the ranks of volunteers, with VFX 10 students Belinda Fung, Erwin Dumoulin and Blair Richmond doing everything from hanging banners to tearing tickets. VanArts VFX Department TA Max Schroeder helped Ken Priebe staff the newly redesigned VanArts booth in the theatre lobby, assisting throngs of potential students, as well as coordinating most of the VanArts contributions to the event. VanArts faculty were also roaming the stage as well, as Compositing Supervisor Mike Adkisson, (bio below,) and VFX Department Head Doug Smith sat on the panel sessions “VFX in Vancouver” and “Pipedreams: In Search of the Perfect Production Solution,” respectively, and Admissions Director and stop-motion animation expert Ken Priebe introduced the film “The 7th Voyage of Sinbad.” Best -
Careers in Entertainment Art for Secondary School Students
Careers In Entertainment Art For Secondary School Students © Alex Nice About This online event provides art, design Video access will also be available Research by the global consulting The international line-up includes artists and media students and teachers with for 6 weeks following the event. group Price Waterhouse Cooper who have contributed to commercials, access to the techniques, experiences Registration will allow for content to shows that over the next five years television productions, Academy and career pathways of some of be viewed in the classroom or watched Australia’s total entertainment and Award winning films, and AAA games the world’s leading entertainment by individuals. media market is forecast to grow including Star Trek, Avatar, Captain artists in your own school. This event from $38.9b in 2015 to $47.4b in America, The Avengers, Jungle Book, willhelp understand how to create Curated specifically for secondary 2020”…. in a large part due to good Hunger Games, Thor, Harry Potter, Star digital environemnts, props, vehicles, schools students who have a passion performance by the box office and Wars: The Force Unleashed, Uncharted spaceships, characters, creatures and for drawing, illustration, 3D design interactive games, especially from 4, Cloverfield amongst others. Working vfx. and may be interested in forging a digital in-game purchases. as VFX artists, art directors, creature viable career creating content for film, designers, environment artists and The event will be live streamed on television, games, commercials, virtual ‘For content creators is it an age of directors they will share their own March 31st 2017 from 10.30am to realiity and other digital applications. -
24 on Tour Guide Fokus
AKTUELL FOKUS EDITING ANIMATION COMPOSITING COLOR AUDIOSTEREO 3D MAKING OF GUIDE ON TOUR 24 WWW.DIGITALPRODUCTION.COM DDP1003_024-030_Ironman2.inddP1003_024-030_Ironman2.indd 002424 113.04.20103.04.2010 114:54:564:54:56 AUSGABE 03|10 FOKUS | VISUAL EFFECTS DDieie MMachtacht dderer VVisualisual EffectsEffects Es gibt kaum noch einen aktuellen Film, der ohne den Einsatz von Spezialeffekten und VFX aus- kommt. Immer öfter werden komplette Sets, wie etwa die Kommandobrücke der Enterprise in Star Trek, komplett digital erstellt oder die Ork-Horden aus „Der Herr der Ringe“ computeranimiert und intelligent via Rechner gelenkt. Nicht selten ist heute der CGI-Anteil höher als der der realen Bilder. Eines ist klar: VFX sind aus dem Kino der heutigen Zeit nicht mehr mehr wegzudenken. ktuelle Vertreter des VFX-Genres sind beispiels- lungen der DP-Redaktion (Seite 31). Diese Filme dürfen weise „Iron Man 2“ (Making of ab Seite 26), bei dem Sie nicht verpassen, wenn Sie in diesem Jahr die Creme Aunter anderem Rüstungen und Waffen von Freund de la Creme der Spezialeffekte sehen möchten. und Feind digital erstellt wurden. Besonders erfreulich Aber auch wenn sich Regisseure, Produzenten und aus deutscher Sicht ist, dass der Platzhirsch der Bran- Studios immer wieder aufs Neue mit einem Effekt-Feuer- che, George Lucas‘ Studio Industrial Light & Magic, für werk zu übertreffen versuchen, muss nicht immer alles, die Produktion von „Iron Man 2“ auf ein Studio mit deut- was gerne gesehen wird, zwangsläufi g digital sein. Nach schen Wurzeln aufmerksam wurde und Pixomondo meh- „Coraline“ aus dem Jahr 2009 gibt es ab dem 13. Mai 2010 rere Shots beisteuern konnte. -
Flyer-Non Members.Qxp
A Decade of Digital Day...and Counting SASATURDATURDAYY,, JULJULYY 2828th Panels and Presentations 9:30 a.m. to 5:15 p.m.. Followed by Wrap Party in Atrium Registration & Lobby Exhibits Open at 8:30 a.m. DGA • 7920 Sunset Blvd. • Los Angeles Registration Fee: $35 Includes continental breakfast, box lunch and For more information call DGA Wrap Party in DGA Atrium hosted by Dolby Special Projects at (310) 289-2088 PANELS AND PRESENTATIONS (Programming subject to change) CUTTING EDGE APPS WHAT’S NEW IN PROFESSIONAL NON-HUMAN CHARACTERS Moderator: Randal Kleiser, Director, Grease, PROGRAMMING FOR THE WEB Creating Creatures: Physical or Digital? Honey, I Shrunk the Audience, The Nina Foch Presented by the DGA Presented by the DGA Course for Filmmakers and Actors. Independent Directors Committee AD/UPM VFX/Digital Technology Committee • Choosing 3D InterOcular in Post Presented by: A discussion with the directors and producers of Panelists: David Breaux, Character Animator, Sean Fairburn, CEO, MIO 3D. WIGS, the new digital channel featuring world-class Pixomondo (Terra Nova, Hunger Games, Iron Man 2, • Prometheus: Creative Color Grading for the 3D talent in original series, short films, documentaries Thor) • J. Alan Scott, Live Action Animatronic Effects Feature Presented by: Stephen Nakamura, and other content. Supervisor/Co-Owner, Legacy Effects (Bourne Director of Feature Films, Company 3. Legacy, Muppets, Snow White and the Huntsman) • Panelists: Effie Brown, Producer, In The Cut, Bill Westenhofer, Visual Effects Supervisor, • Navigating the Cloud: Development Through Rocket Science, Real Women Have Curves • Rhythm & Hues (Life of Pi, Golden Compass) • Tom Distribution Presented by: Jeff Maynard, Partner, Rodrigo Garcia, Director/Writer/Producer, WIGS, Woodruff, Jr., Character Effects Designer, Creator Vici Post Solutions and Andrew Zuk, CEO, Vici Post In Treatment, Six Feet Under, Carnivàle • Lesli Solutions.