Owl Nest Box
Total Page:16
File Type:pdf, Size:1020Kb
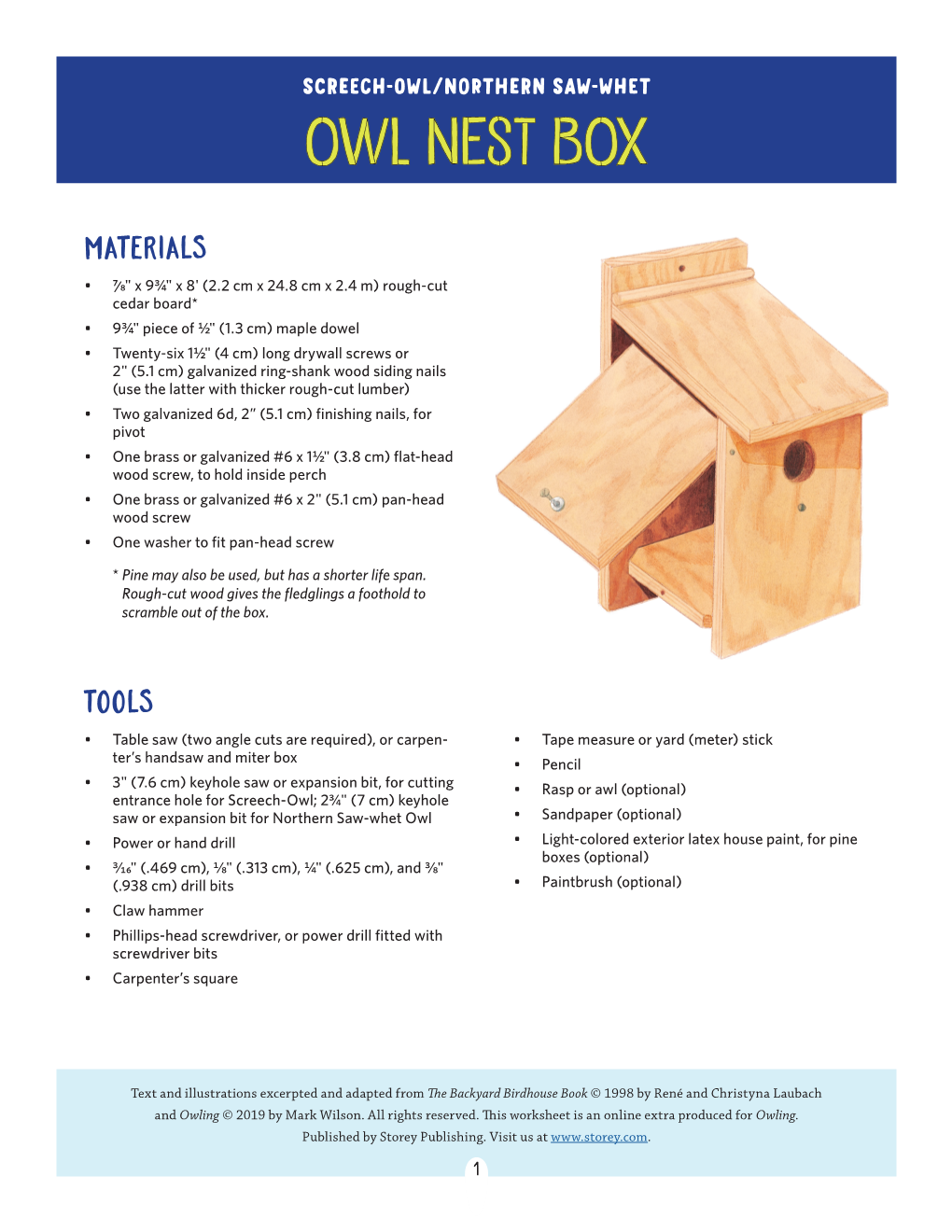
Load more
Recommended publications
-
Hand Saws Hand Saws Have Evolved to fill Many Niches and Cutting Styles
Source: https://www.garagetooladvisor.com/hand-tools/different-types-of-saws-and-their-uses/ Hand Saws Hand saws have evolved to fill many niches and cutting styles. Some saws are general purpose tools, such as the traditional hand saw, while others were designed for specific applications, such as the keyhole saw. No tool collection is complete without at least one of each of these, while practical craftsmen may only purchase the tools which fit their individual usage patterns, such as framing or trim. Back Saw A back saw is a relatively short saw with a narrow blade that is reinforced along the upper edge, giving it the name. Back saws are commonly used with miter boxes and in other applications which require a consistently fine, straight cut. Back saws may also be called miter saws or tenon saws, depending on saw design, intended use, and region. Bow Saw Another type of crosscut saw, the bow saw is more at home outdoors than inside. It uses a relatively long blade with numerous crosscut teeth designed to remove material while pushing and pulling. Bow saws are used for trimming trees, pruning, and cutting logs, but may be used for other rough cuts as well. Coping Saw With a thin, narrow blade, the coping saw is ideal for trim work, scrolling, and any other cutting which requires precision and intricate cuts. Coping saws can be used to cut a wide variety of materials, and can be found in the toolkits of everyone from carpenters and plumbers to toy and furniture makers. Crosscut Saw Designed specifically for rough cutting wood, a crosscut saw has a comparatively thick blade, with large, beveled teeth. -
How to Install
How to Install What you’ll need: Pencil • Level • Square • Compressor • Pin nailer or Finish nailer • Safety Glasses Chop Saw or handsaw with higher tooth count • Gloves • Tape Measure • Marking Chalk ¾” Headless pin Nails All items available at your local Home depot Step 1 - Estimate Materials Rewoodd Paneling is 3/8”x 5”x 12”- 48” in size, our product is tongue and grooved for easy installation. First measure the total square footage of the wall or area to be paneled. If there are any doors or windows in the space, subtract the area needed for them and divide the remaining number by 20 to determine how many boxes you need to buy. For example- 12’x12’ wall = 144 sq. ft. 144/20= 7.2. You’ll need 8 boxes. Remember to subtract sq. footage on doors and/or windows. Step 2 – Prepare the Walls When paneling over a solid back, you’ll need to make any necessary repairs first so that wall is flush and even. Step 3 - Measure and Cut the Panels Do a dry run with the panels to see how they all line up, and rearrange them as needed to get the best result. Mark the backs of the panels or lay them back down in the order they were arranged so when they are secured to the wall, it is done correctly. Start from the top and draw a few lines on the wall with a level to set up the beginning of installation. You’ll need to cut the panels to fit any type of fixture, window, or doorway. -
Squirrel Box Instructions
Step-by-Step Instructions on How to Make: Squirrel Boxes Materials: -3/4” untreated pine or cedar board, 8’ x 10’ (one 8’ plank will make one box and 10” wide wood is really 9 ½”, sometime even 9 ¼” so ask for true dimensions) -2” galvanized wood screws -sandpaper -hinges (2 small ones per box) -water-based wood stain (optional but recommended) Tools: -work surface where wood can be secured while sawing or drilling -circular saw* -jig saw* -sander * -drill and drill-bits* -goggles (for when using power tools) -gloves (optional but helpful for when handling wood) -paintbrushes -hammer (for creating “toe holds” on front piece) Instructions: *Before using power tools, make sure you read all tool instructions and follow safety guidelines to ensure proper use and safety. 1. Cut wood (most hardware stores, like the Home Depot, will do the cutting for you, just show them the template; however, they will only make cuts going one direction, so other additional cutting will have to be done yourself) 2. Make additional cuts (slants and holes) using saw. 3. Sand all rough edges with a sander until they are smooth and not splintery. •Steps 4 through 6 are optional but highly recommended to extend the life of the cage and make it easier to clean. 4. Paint all pieces of wood, including all the edges, with 1 coat of water-based stain. 5. Let stain dry. 6. Repeat steps 4 & 5 for second coat of stain. 7. Assemble bottom and sides to make a box, if some pieces are too long and don’t fit together quite right you can trim them with a circular saw. -
STANLEY® FATMAX® Tri-Material Hand Saws with Bladearmor® Coating
STANLEY® FATMAX® TRI-MaterIAL HAND SAWS WITH BLADEARMOR® COatING ■ Tri-material handle for comfort and durability. SAW ■ New handle design improves ease of cut by 25%*. ■ Triple Ground Tooth Technology 4X** sharper for fast cuts. S ■ Induction hardened teeth for long life. ■ BladeArmor® coating helps reduce friction while cutting. Product # Blade Length (in) Points Per Inch Teeth Per Inch 20-046 15 12 11 20-047 20 12 11 FMHT20218 26 12 11 *Compared to previous model. **Compared to traditional tooth saws. STANLEY® FATMAX® BOX SAW ■ Blade is 15% thicker than conventional saws for straighter cuts with less binding. ■ SharpTooth™ Saw Technology uses three cutting surfaces to cut 50% faster than conventional STANLEY® hand saws. ■ Induction-hardened teeth stay sharp up to 5X longer than standard teeth. ■ Thick, ergonomically designed grip resists slipping and adds comfort. ■ Back of saw can be used to mark 45° and 90° angles. Product # Blade Length (in) Points Per Inch Teeth Per Inch 20-045 15 9 8 STANLEY® SHARPTOOTH® CUSHION GRIP SAWS ■ SharpTooth™ saw technology uses three cutting surfaces to cut 50% faster than conventional STANLEY® hand saws. ■ Induction-hardened teeth stay sharp up to 5X longer than standard teeth. ■ Ergonomically designed one-piece handle. Product # Blade Length (in) Points Per Inch Teeth Per Inch 20-526 15 12 11 20-527 20 12 11 STANLEY® Heavy-DUTY SHARPTOOTH® WOOD HANDLE SAWS ■ Aggressive multipurpose saw for fast cutting. ■ SharpTooth™ Saw Technology uses three cutting surfaces to cut 50% faster than conventional STANLEY® hand saws. ■ Induction-hardened teeth stay sharp up to 5X longer than standard teeth. -
Selection and Use of Nest Sites by Barn Owls in Norfolk, England
j Raptor Res. 28(3):149-153 ¸ 1994 The Raptor ResearchFoundation, Inc. SELECTION AND USE OF NEST SITES BY BARN OWLS IN NORFOLK, ENGLAND PAUL N. JOHNSON The Durrell Instituteof Conservationand Ecology,The University,Canterbury, Kent CT2 7NX United Kingdom AI•STR•CT.--Between1989 and 1993 reproductionwas monitoredat 96 barn owl (Tyro alba) breeding sitesin England. Nestswere locatedin tree cavities,buildings, and nest boxesin farm buildingsand maturetrees. Many of the sitesother than nestboxes used by owls were of human origin, but the number of thosedeclined during the courseof the study due to deteriorationof human-madestructures and competitionfrom otherspecies. Nest boxesincreased the populationdensity from 15 breedingpairs/100 km2 to 27 pairs.Over the studyperiod, pairs usingnest boxes produced significantly larger clutchesthan at other sites,but the numberof fledglingswas not significantlydifferent amongtypes of nest sites. KEY WORDS: barn owl; breedingecology; England; human-altered habitats; nest boxes; Tyro alba. Selecci6ny usode sitiosde nidificaci6npor Tyroalba en Norfolk, Inglaterra RESUMEN.--Entre1989 y 1993 semonitore6 la reproducci6nen 96 sitiosreproductivos de Tyroalba. Los nidosse localizaron en cavidadesde firboles,edificios, cajas anideras en construccionesagricolas y firboles madufos.Mucho de estossitios, aparte de las cajasanideras, usados por T. alba fueron de origen humano, peroel nfimerode ellosdeclin6 durante el cursodel estudiodebido al deteriorode las estructurasartificiales y a la competenciacon otras especies.Las cajasanideras incrementaron la densidadpoblacional de 15 parejasreproductivas/100 km 2 a 27 parejas.En el periodode estudio,las parejasque usaronlas cajas aniderasprodujeron nidadas significativamentemils grandesqueen otros sitios, pero el nfimero de volantonesno fue significativamentediferente entre los distintostipos de sitios. [Traducci6n de Ivan Lazo] The barn owl (Tyro alba) is currentlyclassified box studieshas been criticized by Moller (1989, as vulnerable in northwest Norfolk, England by 1992). -
Wood Duck Nest Box Design & Assembly Directions
Wood Duck Nest Box Design & Assembly Directions Instructions, Illustrations & Photos Courtesy of MWDI and Scott Jasion, Harford County Chapter, Ducks Unlimited Side door opening design for easy mounting & monitoring access light-weight, field-proven effectiveness Design can be easily converted to a top lid opening by keeping the door panel in one piece and permanently attachin to sides; add hinge to roof instead of attaching. Design can also be converted to an “east-west” side door by cutting the door panel into “thirds”, by attaching the upper and lower portions and then by adding a hinged piece in the middle as desired height. Materials Needed for One Box 10-foot, 10” wide board (ideally cypress or cedar for longevity) High quality wood, #2 grade, rough cut one side One – 12-14” x 3-4” exit ladder Nominal 10” width and 1” thickness Hardware cloth (rat wire), small mesh, curved in 12” boards can easily be used, adhere to the same length center to form slight hump, easier ladder use by dimensions. ducklings. Other lumber is also feasible but other hardwoods will Trim or fold edges to prevent injury to ducklings add significant weight. from sharp wire points. Softwoods require treatment and will not last as long. Plastic gutter guard will also works well. Cut with scissors. Premium wood glue. Apply liberally to all seams, splits and knot areas. Will 1 ½” stainless steel or galvanized staples, insure boxes hold up much longer than those without ¼” narrow crown, 18 gauge glue. for use in compressed air staple gun. 1 ½” stainless steel, ribbed, cedar shake nails may also Tools Needed be used with hammer or 1 ½" screws. -
Making a Southern Flying Squirrel (SFS) Nest Box: a Few Steps but Lots of Details by Don Althoff 2020
Making a Southern Flying Squirrel (SFS) Nest Box: A Few Steps But Lots of Details By Don Althoff 2020 Knock…and you may find someone home! Plug and check behind the door A “cut” hickory…the SFS is the only species in our region to have this distinctive entry into Flying squirrel box half full a hickory nut. Larger tree of ‘cut’ hickory nuts…a sure squirrels are able to crush sign of SFS in your woods these hard shelled nuts Basics 2 You need one (1) board per box: 1” x 8” x 8-ft white board (aka pine/spruce/fir) Screws or nails. 2” 2 carriage bolts/nuts/washers ¼” diameter, 2 ½” long You need 1-pair of hinges. 1 ½” will do. You need ¼” x ¼” hardware cloth/screen mesh (get 24” wide roll. A 5 ft. long roll will yield 10 screens) 2 carriage bolts +nuts +washers ¼” diameter, 2 ½” long Hook & eyelet 1 ½” is suffcient Electrical outlet plate 1 ½” opening to keep larger species of squirrels (i.e., red, gray, and fox) out of the box 3 Cutting & Assembly Tips 4 Pay attention to grain. Look at the end of your boards. Face outside Always have the curve facing to the inside Face inside Suggest you use 1 ½” paddle bit to make side hole. Drill about ¾ way through on one side, then flip over board and drill from other side to complete hole. This reduces tear- out/splintering on one side For left side (box door side facing you), use strip from piece you just cut to create the inner strip piece. -
Build a Plane That Cuts Smooth and Crisp Raised Panels With, Against Or Across the Grain – the Magic Is in the Spring and Skew
Fixed-width PanelBY WILLARD Raiser ANDERSON Build a plane that cuts smooth and crisp raised panels with, against or across the grain – the magic is in the spring and skew. anel-raising planes are used Mass., from 1790 to 1823 (Smith may to shape the raised panels in have apprenticed with Joseph Fuller doors, paneling and lids. The who was one of the most prolific of the profile has a fillet that defines early planemakers), and another similar Pthe field of the panel, a sloped bevel example that has no maker’s mark. to act as a frame for the field and a flat Both are single-iron planes with tongue that fits into the groove of the almost identical dimensions, profiles door or lid frame. and handles. They differ only in the I’ve studied panel-raising planes spring angles (the tilt of the plane off made circa the late 18th and early 19th vertical) and skew of the iron (which centuries, including one made by Aaron creates a slicing cut across the grain to Smith, who was active in Rehoboth, reduce tear-out). The bed angle of the Smith plane is 46º, and the iron is skewed at 32º. Combined, these improve the quality of cut without changing the tool’s cutting angle – which is what happens if you skew Gauges & guides. It’s best to make each of these gauges before you start your plane build. In the long run, they save you time and keep you on track. Shaping tools. The tools required to build this plane are few, but a couple of them – the firmer chisel and floats – are modified to fit this design. -
Building Practices and Carpenters' Tools That Created Alexandria's Kent Plantation House
Building Practices and Carpenters' Tools That Created Alexandria's Kent Plantation House By N. H. Sand and Peter Koch SouthernForest ExperimentStation Forest Service. U. S. Departmentof Agriculture I t is the year 1796or thereabouts. ily, and he succeeds so well that designed and made with good Louisiana is a Spanish colony with the dwelling still remains sound and materials. French traditions and culture. attractive after 175 years, a very Now known (from a later owner) Pierre Baillio II, of a prominent great age for a house in America. asthe Kent PlantationHouse, Bail- French family, has a sizeable grant To reach it takes good luck-escape lio's home has recently beenmade of land along the Red River near from fire, flood and the Civil War. into a museum in Alexandria, a a small town called EI Rapido. Continuous occupancy and the care short distance from where it was Baillio undertakes to have a that goes with it also helps. Most originally constructed. There it house built for himself and his fam- of all, the house must be soundly standsas testimony to the skins of early Louisiana carpenter crafts- men. In contrast to architects, who seemto leapinto print with no great difficulty, carpenters are a silent tribe. They come to the job with their tool chests, exercise many skins of construction and some of design, and then pass on. Often their works are their only record. Occasionally some tools survive and, after generationsof neglectand abuse,these may find their way int() antique shopsor museums. Thus it is difficult to speakin de- tail of the builders of any given house. -
American Kestrel Nest Box Monitoring Guidelines
American Kestrel Nest Box Monitoring Guidelines Phase 1: Pre-season check Shortly before the kestrels are due to return (early March), you should do a pre-season check to get the box ready and ensure that it is in good order. 1. Open – If the box was closed for the winter to prevent squirrels, sparrows, and starlings from using it, open it now. 2. Lining – Line the bottom of the box with a few inches of pine shavings or wood chips. Do not use sawdust, as it will not insulate the eggs properly, and do not use cedar shavings, as these are toxic to young birds. 3. Inspection – Inspect the box and its mounting pole. Do any parts appear cracked or broken? This is the time when a replacement box can be erected – once the season starts, it will be much harder. Phase 2: Early breeding season During the early breeding season (from late March onward), all that needs be done is to assess whether the box has been selected by kestrels. One hour-long visit every two weeks should be sufficient. If the box is likely to be taken over by House Sparrows or starlings, weekly visits should be made to check for these invasives. If kestrels are seen going in and out of the box, you may well have nesting kestrels. If squirrels, starlings, or House Sparrows are seen, the box may have been invaded. Observe for a time, and if you determine that another animal is using the box, wait for the adult animals to leave. Once the adults are outside, simply close the box. -
Stanley Hand Tools Catalog
SAW SELECTION GUIDE MATERIALS APPLICATIONS WOOD METAL PLASTIC ROOFING FRAMING DRYWALL FINISH WORK HANDLE TYPE BLADE LENGTH Saws WOOD FLOORING POINTS PER INCH CROWN MOLDING PANEL SAWS FatMax® Saw w/ BladeArmor™ Coating 20-046, 20-047 15" & 20" 9 Wood/ Rubber X X X X FatMax® Saw 20-045 15" 9 Wood/ Rubber X X X X Fine Finish Saw w/Rubber Grip 20-526, 20-527 15" & 20" 12 Rubber/ Plastic X X X X X Heavy Duty Saw 15-085, 15-087 15" & 20" 9 Wood X X X X Fine Finish Saw 15-086, 15-088, 20-065 15", 20", & 26" 12 Wood X X X X X Heavy Duty Saw - Resharpenable 15-334, 15-335 15" & 20" 9 Wood X X X X General Purpose Saw 15-579, 15-580 15" & 20" 9 Plastic X X X X SPECIALTY SAWS Drywall Saw 15-025 15" 9 Wood X X X X Compact Fine Finish Saw 20-221 10" 12 Wood X X X X X Compass Saw 15-100 12" 8 Wood X X Compass Saw w/Plastic Handle 15-351 12" 8 Plastic X X Reversing Backsaw 15-252 10" 15 Wood X X Miter Box Saw 15-673 14" 12 Wood X X X X Miter Box Saw w/Plastic Handle 15-509 12" 13 Plastic X X X X MultiPurpose Saw - 3 in 1 20-092 6", 8", & 10" 10, 12, & 24 High Strength Nylon X X X X X X X MultiPurpose Saw - Nest of Saws 15-090 6", 8", & 10" 24, 10, & 12 Plastic X X X X X X X Folding Pocket Saw 15-333 8" 10 Plastic X X MultiPurpose Saw - 4-Way™ 15-275 6" N/A Metal X X X X X Flush Cut Pull Saw 20-331 4-3/4" 23 Plastic X X X JAB SAWS FatMax® Drywall Saw 20-556 6" 9 Rubber X X Drywall Saw w/Cushion Grip 15-556 6" 7 Plastic X X Drywall Saw 15-206 6" 7 Wood X X MultiPurpose Saw - Cushion Grip 20-220 N/A N/A Plastic X X HACKSAWS FatMax® High Tension Hacksaw -
1. Hand Tools 3. Related Tools 4. Chisels 5. Hammer 6. Saw Terminology 7. Pliers Introduction
1 1. Hand Tools 2. Types 2.1 Hand tools 2.2 Hammer Drill 2.3 Rotary hammer drill 2.4 Cordless drills 2.5 Drill press 2.6 Geared head drill 2.7 Radial arm drill 2.8 Mill drill 3. Related tools 4. Chisels 4.1. Types 4.1.1 Woodworking chisels 4.1.1.1 Lathe tools 4.2 Metalworking chisels 4.2.1 Cold chisel 4.2.2 Hardy chisel 4.3 Stone chisels 4.4 Masonry chisels 4.4.1 Joint chisel 5. Hammer 5.1 Basic design and variations 5.2 The physics of hammering 5.2.1 Hammer as a force amplifier 5.2.2 Effect of the head's mass 5.2.3 Effect of the handle 5.3 War hammers 5.4 Symbolic hammers 6. Saw terminology 6.1 Types of saws 6.1.1 Hand saws 6.1.2. Back saws 6.1.3 Mechanically powered saws 6.1.4. Circular blade saws 6.1.5. Reciprocating blade saws 6.1.6..Continuous band 6.2. Types of saw blades and the cuts they make 6.3. Materials used for saws 7. Pliers Introduction 7.1. Design 7.2.Common types 7.2.1 Gripping pliers (used to improve grip) 7.2 2.Cutting pliers (used to sever or pinch off) 2 7.2.3 Crimping pliers 7.2.4 Rotational pliers 8. Common wrenches / spanners 8.1 Other general wrenches / spanners 8.2. Spe cialized wrenches / spanners 8.3. Spanners in popular culture 9. Hacksaw, surface plate, surface gauge, , vee-block, files 10.