Bioseparation
Total Page:16
File Type:pdf, Size:1020Kb
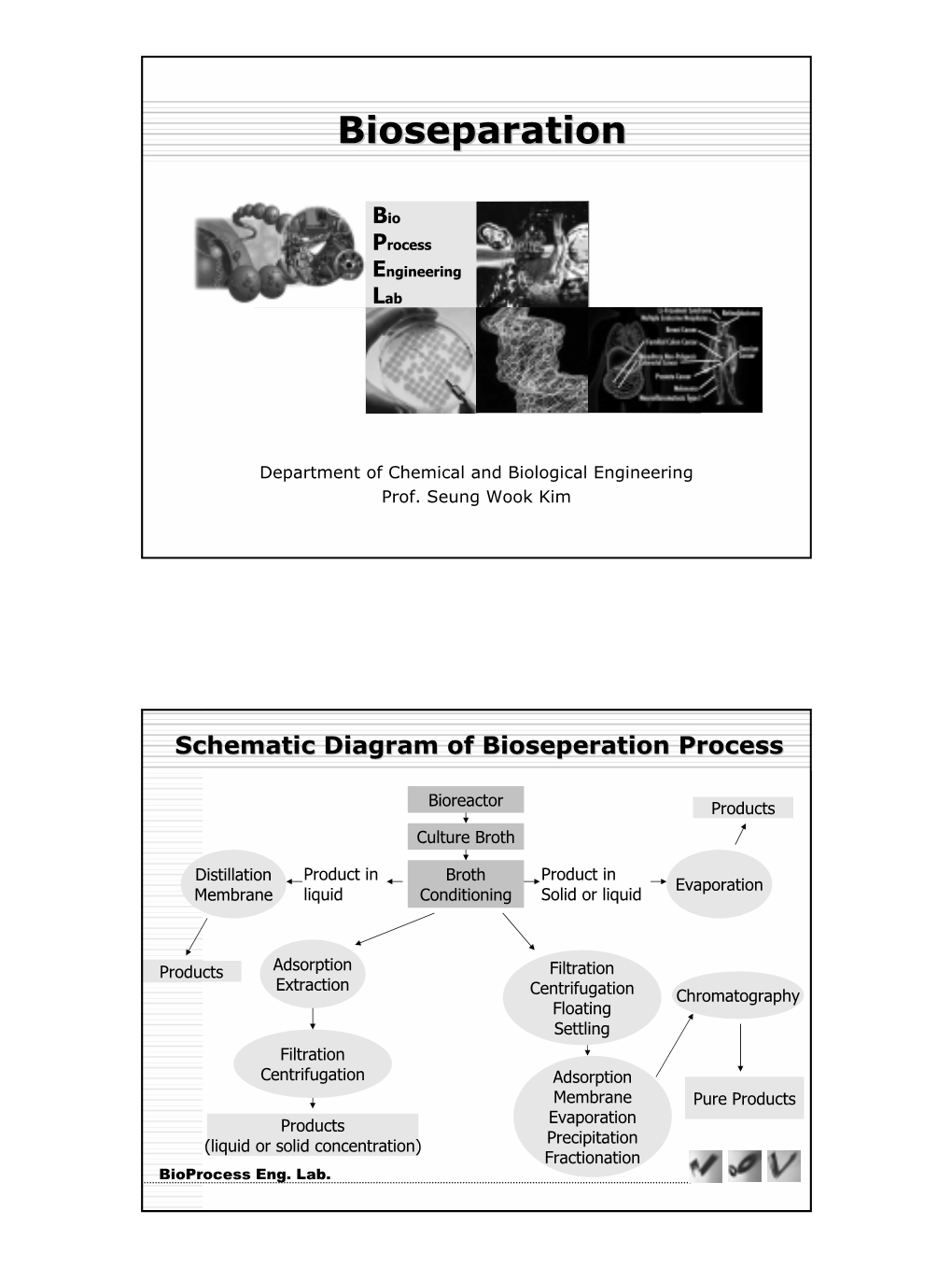
Load more
Recommended publications
-
1. Define: Unit Operation. Useful Physical Changes Occur in the Chemical Industry Is Known As a Unit Operation
INTREVIEW QUESTIONS 1. Define: Unit operation. Useful Physical changes occur in the chemical industry is known as a Unit Operation. Example: Distillation, Filtration, Drying, Extraction, Gas absorption, Crystallization, etc. 2. Define: Unit process. Useful Chemical changes with or without physical change occur in chemical industry are known as a Unit Process. Example: - Oxidation, Reduction, Alkylation, Sulfonation, Chlorination, etc. 3. Define: Boiling Point and Bubble Point. Boiling Point: -It is a temperature of a liquid at which the vapour pressure of the liquid is equal to atmospheric pressure. Bubble Point: -It is a temperature at which first bubble of vapour is formed. 4. When does liquid boil? When the vapour pressure of the liquid is equal to atmospheric pressure at that time liquid is boil. 5. Define: - Volatile Liquid. It is a tendency of a liquid to vaporize. 6. Acetone and water out of this which is more volatile and why? Acetone is more volatile than water because of boiling point of acetone (56.7 °C) is low compa re to boiling point of water (100° C) 7. What is the Relative Volatility? It is a ratio of concentration of more volatile component in vapour phase to liquid phase is called Relative Volatility 8. What is important of Relative Volatility? For separation of liquid mixture using distillation, Relative volatility should be more than 1. 9. Why is Reflux done in distillation column? and Define Reflux Ratio. For Increasing product purity. Reflux: -It is amount of distillate which is resend to distillation column is known as a reflux. Reflux Ratio: -Reflux ratio is the ratio of the portion of the overhead liquid product from a distillation column that is returned to the upper part of column to the portion of liquid collected as distillate. -
Protocols and Tips in Protein Purification
Department of Molecular Biology & Biotechnology Protocols and tips in protein purification or How to purify protein in one day Second edition 2018 2 Contents I. Introduction 7 II. General sequence of protein purification procedures 9 Preparation of equipment and reagents 9 Preparation and use of stock solutions 10 Chromatography system 11 Preparation of chromatographic columns 13 Preparation of crude extract (cell free extract or soluble proteins fraction) 17 Pre chromatographic steps 18 Chromatographic steps 18 Sequence of operations during IEC and HIC 18 Ion exchange chromatography (IEC) 19 Hydrophobic interaction chromatography (HIC) 21 Gel filtration (SEC) 22 Affinity chromatography 24 Purification of His-tagged proteins 25 Purification of GST-tagged proteins 26 Purification of MBP-tagged proteins 26 Low affinity chromatography 26 III. “Common sense” strategy in protein purification 27 General principles and tips in “common sense” strategy 27 Algorithm for development of purification protocol for soluble over expressed protein 29 Brief scheme of purification of soluble protein 36 Timing for refined purification protocol of soluble over -expressed protein 37 DNA-binding proteins 38 IV. Protocols 41 1. Preparation of the stock solutions 41 2. Quick and effective cell disruption and preparation of the cell free extract 42 3. Protamin sulphate (PS) treatment 43 4. Analytical ammonium sulphate cut (AM cut) 43 5. Preparative ammonium sulphate cut 43 6. Precipitation of proteins by ammonium sulphate 44 7. Recovery of protein from the ammonium sulphate precipitate 44 8. Analysis of solubility of expression 45 9. Analysis of expression for low expressed His tagged protein 46 10. Bio-Rad protein assay Sveta’s easy protocol 47 11. -
Sedimentation and Clarification Sedimentation Is the Next Step in Conventional Filtration Plants
Sedimentation and Clarification Sedimentation is the next step in conventional filtration plants. (Direct filtration plants omit this step.) The purpose of sedimentation is to enhance the filtration process by removing particulates. Sedimentation is the process by which suspended particles are removed from the water by means of gravity or separation. In the sedimentation process, the water passes through a relatively quiet and still basin. In these conditions, the floc particles settle to the bottom of the basin, while “clear” water passes out of the basin over an effluent baffle or weir. Figure 7-5 illustrates a typical rectangular sedimentation basin. The solids collect on the basin bottom and are removed by a mechanical “sludge collection” device. As shown in Figure 7-6, the sludge collection device scrapes the solids (sludge) to a collection point within the basin from which it is pumped to disposal or to a sludge treatment process. Sedimentation involves one or more basins, called “clarifiers.” Clarifiers are relatively large open tanks that are either circular or rectangular in shape. In properly designed clarifiers, the velocity of the water is reduced so that gravity is the predominant force acting on the water/solids suspension. The key factor in this process is speed. The rate at which a floc particle drops out of the water has to be faster than the rate at which the water flows from the tank’s inlet or slow mix end to its outlet or filtration end. The difference in specific gravity between the water and the particles causes the particles to settle to the bottom of the basin. -
Crystallization of Oxytetracycline from Fermentation Waste Liquor: Influence of Biopolymer Impurities
Journal of Colloid and Interface Science 279 (2004) 100–108 www.elsevier.com/locate/jcis Crystallization of oxytetracycline from fermentation waste liquor: influence of biopolymer impurities Shi-zhong Li a,1, Xiao-yan Li a,∗, Dianzuo Wang b a Environmental Engineering Research Centre, Department of Civil Engineering, The University of Hong Kong, Hong Kong, China b Chinese Academy of Engineering, Beijing 100038, China Received 28 January 2004; accepted 17 June 2004 Available online 29 July 2004 Abstract Organic impurities in the fermentation broth of antibiotic production impose great difficulties in the crystallization and recovery of antibi- otics from the concentrated waste liquor. In the present laboratory study, the inhibitory effect of biopolymers on antibiotic crystallization was investigated using oxytetracycline (OTC) as the model antibiotic. Organic impurities separated from actual OTC fermentation waste liquor by ultrafiltration were dosed into a pure OTC solution at various concentrations. The results demonstrated that small organic molecules with an apparent molecular weight (AMW) of below 10,000 Da did not affect OTC crystallization significantly. However, large biopolymers, especially polysaccharides, in the fermentation waste caused severe retardation of crystal growth and considerable deterioration in the pu- rity of the OTC crystallized. Atomic force microscopy (AFM) revealed that OTC nuclei formed in the solution attached to the surfaces of large organic molecules, probably polysaccharides, instead of being surrounded by proteins as previously thought. It is proposed that the attachment of OTC nuclei to biopolymers would prevent OTC from rapid crystallization, resulting in a high OTC residue in the aqueous phase. In addition, the adsorption of OTC clusters onto biopolymers would destabilize the colloidal system of organic macromolecules and promote particle flocculation. -
MATERIAL BALANCE NOTES Revision 3 Irven Rinard Department
MATERIAL BALANCE NOTES Revision 3 Irven Rinard Department of Chemical Engineering City College of CUNY and Project ECSEL October 1999 © 1999 Irven Rinard CONTENTS INTRODUCTION 1 A. Types of Material Balance Problems B. Historical Perspective I. CONSERVATION OF MASS 5 A. Control Volumes B. Holdup or Inventory C. Material Balance Basis D. Material Balances II. PROCESSES 13 A. The Concept of a Process B. Basic Processing Functions C. Unit Operations D. Modes of Process Operations III. PROCESS MATERIAL BALANCES 21 A. The Stream Summary B. Equipment Characterization IV. STEADY-STATE PROCESS MODELING 29 A. Linear Input-Output Models B. Rigorous Models V. STEADY-STATE MATERIAL BALANCE CALCULATIONS 33 A. Sequential Modular B. Simultaneous C. Design Specifications D. Optimization E. Ad Hoc Methods VI. RECYCLE STREAMS AND TEAR SETS 37 A. The Node Incidence Matrix B. Enumeration of Tear Sets VII. SOLUTION OF LINEAR MATERIAL BALANCE MODELS 45 A. Use of Linear Equation Solvers B. Reduction to the Tear Set Variables C. Design Specifications i VIII. SEQUENTIAL MODULAR SOLUTION OF NONLINEAR 53 MATERIAL BALANCE MODELS A. Convergence by Direct Iteration B. Convergence Acceleration C. The Method of Wegstein IX. MIXING AND BLENDING PROBLEMS 61 A. Mixing B. Blending X. PLANT DATA ANALYSIS AND RECONCILIATION 67 A. Plant Data B. Data Reconciliation XI. THE ELEMENTS OF DYNAMIC PROCESS MODELING 75 A. Conservation of Mass for Dynamic Systems B. Surge and Mixing Tanks C. Gas Holders XII. PROCESS SIMULATORS 87 A. Steady State B. Dynamic BILIOGRAPHY 89 APPENDICES A. Reaction Stoichiometry 91 B. Evaluation of Equipment Model Parameters 93 C. Complex Equipment Models 96 D. -
Review and Cost Analysis of Reverse Osmosis and Ultrafiltration
Review and cost analysis of reverse osmosis and ultrafiltration A Senior Project presented to Dr. Bruce Golden of Dairy Science California Polytechnic State University, San Luis Obispo In Partial Fulfillment of the Requirements for the Degree Bachelor of Dairy Science by Jared De Groot March, 2013 © 2013 Abstract The aim in this study was to determine whether implementing an on farm ultrafiltration system was profitable. Ultrafiltration was researched to reduce the amount of milk hauled from producer to processor. An ultrafiltration system involved milk that flowed through a semi-permeable membrane. Through this process water and small amounts of calcium and ash were pressured through the semi-permeable membrane. This permeate would then be able to feed heifers. The protein, fat, solids nonfat, and small amounts of calcium and ash were retained by the membrane. Through the process of ultrafiltration, raw milk was concentrated to three times its original concentration. With the use of ultrafiltration, the dairyman would need to one load of ultrafiltration milk instead of three loads of raw milk. The reduction in the cost of milk hauled and the feed presented to the heifers were the advantages in ultrafiltration. With the saved money on hauling and feeding of heifers, the initial costs of the system and the annual maintenance cost of the system exceed the benefits if implemented on De Groot Dairies. For the on farm ultrafiltration system to break even in ten years, the producer would need to be paid an additional $1.05 /cwt of retentate. This price included the reduced hauling cost and the money saved on the heifer ration. -
Sartorius Ultrafiltration and Protein Purification Products Brochure
Ultrafiltration & Protein Purification Products Fisher Scientific Contents General Information General Information Protein Purification Major Uses for Ultrafiltration 4 Vivapure® Ion Exchange Protein Purification Products 52 Process Alternatives 5 Vivawell Vac Vacuum Manifold Membrane Characteristics 6 Systems 55 Membrane Selection 7 Vivawell Vac 8-strip plate 57 Protein Concentration Vivapure® mini & maxiprep Purification Kits 59 Centrifugal Filtration Protein Concentration Vivapure® mini|maxiprep Protein Vivaspin 500 8 A & G Spin Columns 60 24-Well Ultrafiltration Frame 10 Vivapure® mini|maxiprep MC Spin Vivaspin 2 12 Columns 62 Centrisart I 15 Vivaspin 4 18 Vivapure Anti-HSA/IgG Kits 64 Vivaspin 6 20 Vivapure C18 65 Vivaspin 15 22 Vivaspin 15R 24 Virus Purification and Concentration Vivaspin 20 26 Vivaclear 29 Vivapure® Virus Purification and Concentration Kits 66 Pressure-Fugation DNA Concentration Vivacell 70 30 Adenovirus Purification with Vivacell 100 33 AdenoPACK Kits 67 Vivapure® AdenoPACK 20 68 Gas Pressure Filtration Vivapure® AdenoPACK 100 69 Vivacell 250 36 Vivapure® AdenoPACK 500 71 Tangential Flow Filtration Lentivirus Purification with Vivaflow 50 38 LentiSELECT Kit 73 Vivaflow 200 40 Vivapure® LentiSELECT 40 74 Solvent Adsorption Vivapore 2, 5, 10|20 43 Vivapure® LentiSELECT 500 75 Protein Purification Ultrafiltration Membrane Discs 45 Vivapure® LentiSELECT 1000 76 DNA Concentration Application Notes 77 Vivacon® 500 47 1. Desalting and Buffer Exchange with Vivaspin Centrifugal Concentrators 79 Vivacon® 250 2. Treatment -
State-Of-The-Art Water Treatment in Czech Power Sector
membranes Article State-of-the-Art Water Treatment in Czech Power Sector: Industry-Proven Case Studies Showing Economic and Technical Benefits of Membrane and Other Novel Technologies for Each Particular Water Cycle Jaromír Marek Department of Chemistry, Faculty of Science, Humanities and Education, Technical University of Liberec, Studentská 1402/2, 461 17 Liberec, Czech Republic; [email protected]; Tel.: +420-732-277-183 Abstract: The article first summarizes case studies on the three basic types of treated water used in power plants and heating stations. Its main focus is Czechia as the representative of Eastern European countries. Water as the working medium in the power industry presents the three most common cycles—the first is make-up water for boilers, the second is cooling water and the third is represented by a specific type of water (e.g., liquid waste mixtures, primary and secondary circuits in nuclear power plants, turbine condensate, etc.). The water treatment technologies can be summarized into four main groups—(1) filtration (coagulation) and dosing chemicals, (2) ion exchange technology, (3) membrane processes and (4) a combination of the last two. The article shows the ideal industry-proven technology for each water cycle. Case studies revealed the economic, technical and environmental advantages/disadvantages of each technology. The percentage of Citation: Marek, J. State-of-the-Art technologies operated in energetics in Eastern Europe is briefly described. Although the work is Water Treatment in Czech Power conceived as an overview of water treatment in real operation, its novelty lies in a technological model Sector: Industry-Proven Case Studies of the treatment of turbine condensate, recycling of the cooling tower blowdown plus other liquid Showing Economic and Technical waste mixtures, and the rejection of colloidal substances from the secondary circuit in nuclear power Benefits of Membrane and Other plants. -
Unit Operations for Bioprocess Engineers
Unit Operations for Bioprocess Engineers Chenming (Mike) Zhang Department of Biological Systems Engineering Virginia Polytechnic Institute and State University Blacksburg, VA 24061 Abstract Unit Operations in Biological Systems Engineering was introduced into the curriculum at Virginia Tech in 2000. It is a lecture and laboratory combined course. The lectures and experiments covered in the course had a narrow focus before the author took over in 2002. To broaden the education for students selecting the Bioprocess Engineering option within the curriculum, the author has revised the content of the course to give the students an opportunity to understand that different unit operations can be applied in various industries, namely food, biochemical, and biotechnology. The experiments have been decreased from 14 to 8 so the students could have a better grasp of the theories and applications. Students’ responses showed that it is important to design the experiments in a way to stimulate their desire to learn and perform. The author found that it is possible to give the students a better view of the various unit operations in bioprocess engineering. Page 9.1342.1 Page 1 Introduction As defined by Shuler and Kargi (2002), “Bioprocess engineers are engineers working to apply the principles of various disciplines, such as chemical, mechanical, electrical, and industrial, to processes based on using living cells or subcomponents of such cells.” In other words, bioprocess engineers are engineers who process biological materials to produce useful goods for society. Without question, bioprocess engineering is a broad-based engineering discipline. As educators, it is our job to broaden the view of the students, so they can take advantage of numerous, diverse job opportunities presented to them when they finish their BS degree. -
Coagulation-Flocculation As a Submerged Biological Filter Pre-Treatment with Landfill Leachate
Coagulation-flocculation as a submerged biological filter pre-treatment with landfill leachate A. Gálvez Perez1,2, A. Ramos1,2,3, B. Moreno1,2,3 & M. Zamorano Toro1,2 1Department of Civil Engineering, Granada University, Spain 2MITA Research Group 3Institute of Water Research Abstract Landfill leachate may cause environmental problems if it is not properly managed and treated. An appropriate treatment process of landfill leachate often involves a combination of physical, chemical and biological methods to obtain satisfactory results. In this study, coagulation-flocculation was proposed as a pre- treatment stage of partially stabilized landfill leachate prior to submerged biological filters. Several coagulants (ferric, aluminium or organic) and flocculants (cationic, anionic or non-ionic) were assayed in jar-test experiments in order to determine optimum conditions for the removal of COD and total solids. Among the cationic flocculants, that of highest molecular weight and cationicity (CV/850) showed highest removal efficiencies (15% COD and 8% TS). Organic and aluminium coagulants showed better results than ferric coagulants. Coagulant removal efficiencies were between 9% and 17% for COD and between 10% and 15% for TS. Doses of 1 ml/l of coagulant were preferred. Some combinations of coagulant and flocculant enhanced the process. The best combinations obtained were FeCl3+A30.L, Ferriclar+A20.L, SAL8.2+A30.L and PAX-18+A30.L, which presented COD removal efficiencies between 24% and 37% with doses between 10 and 18 ml/l. Keywords: landfill leachate, coagulation-flocculation, submerged biological filter pre-treatment. Waste Management and the Environment II, V. Popov, H. Itoh, C.A. Brebbia & S. -
PROTEIN a CHROMATOGRAPHY – the PROCESS ECONOMICS DRIVER in Mab MANUFACTURING
PROCESS Application Note PROTEIN A CHROMATOGRAPHY – THE PROCESS ECONOMICS DRIVER IN mAb MANUFACTURING THE OPTIMIZATION OF THE PROTEIN A CAPTURE STEP IN DOWNSTREAM PROCESSING PLATFORMS CAN CONSIDER- ABLY IMPROVE PROCESS EFFICIENCY AND ECONOMICS OF INDUSTRIAL ANTIBODY MANUFACTURING. PARAMETERS LIKE RESIN REUSE AND ITS CAPACITY CONTRIBUTE CONSIDERABLY TO THE PRODUCTION COSTS. THE USE OF A HIGH CAPACITY PROTEIN A RESIN CAN IMPROVE THE PROCESS EFFICIENCY AND ECONOMICS. THIS PAPER PRESENTS THE KEY FEATURES OF A NEW CAUSTIC STABLE PROTEIN A RESIN PROVIDING EXTREMELY HIGH IgG BINDING CAPACITIES. Biopharmaceuticals represent an ever growing important Protein A affinity resins are dominating the Cost of Goods part of the pharmaceutical industry. The market for recom- (COGs) of mAb manufacturing. Bioreactors at the 10.000 L binant proteins exceeded $ 100 billion in 2011 with a scale operating at a titer of about 1g/L typically generate contribution of 45% sales by monoclonal antibodies (mAbs) costs of $ 4-5 million (2). Therefore the Protein A capturing (1). The introduction of the first mAb biosimilars in Europe step is the key driver to improve process economics. Besides raised the competitive pressure in an increasingly crowded the capacity of the resin, life time and cycle numbers market place. The industry faces challenges, such as patent significantly contribute to the production costs in mAb expirations accompanied by approvals of corresponding manufacturing. biosimilars, failures in clinical trials/rejections or the refusal of health insurers to pay for new drugs. Today, the IgG binding capacities of most Protein A resins are in the range of 30-50 g/L, offering significant advantages These challenges force the industry to minimize risk and time- for the processing of high-titer feedstreams when compared to-market and to proceed more cautiously. -
Making Downstream Processing Continuous and Robust a Virtual Roundtable S
BIOPROCESS TECHNICAL Making Downstream Processing Continuous and Robust A Virtual Roundtable S. Anne Montgomery, Cheryl Scott, and Peter Satzer, with Margit Holzer, Miriam Monge, Ralph Daumke, and Alexander Faude urrent biomanufacturing is driven to pursue continuous processing for cost reduction and increased productivity, Cespecially for monoclonal antibody (MAb) production and manufacturing. Although many technologies are now available and have been implemented in biodevelopment, implementation for large-scale production is still in its infancy. In a lively roundtable discussion at the BPI West conference in Santa Clara, CA (11 March 2019), participants touched on a number of important issues still to be resolved and technologies that are still in need of implementation at large scale. Below, moderator Peter Satzer (senior scientist RENTSCHLER BIOPHARMA (WWW.RENTSCHLER-BIOPHARMA.COM) with the Austrian Center of Industrial Biotechnology, Vienna) summarizes key points raised in that session. Based on Requirements for integration without the need for hold his highlights, BPI asked a number of Continuous Downstream tanks between unit operations requires industry representatives to comment on further exploration. those points further, and their Applications Chromatography Operations: Some responses follow. by Peter Satzer unit operations such as flow-through chromatography and single-pass, Minimizing Buffer and Hold Tanks: One tangential-flow filtration (SPTFF) can be critical parameter is integration of unit integrated easily into a continuous Product Focus: Biologics operations on manufacturing shop downstream process scheme at any floors using minimum numbers of point because they offer constant inflow Process Focus: Downstream buffer tanks and hold tanks. The benefit and outflow of material. Such operations processing of continuous manufacturing can be can be called truly or fully continuous.