Low-Power Detection of Food Preservatives by a Novel Nanowire
Total Page:16
File Type:pdf, Size:1020Kb
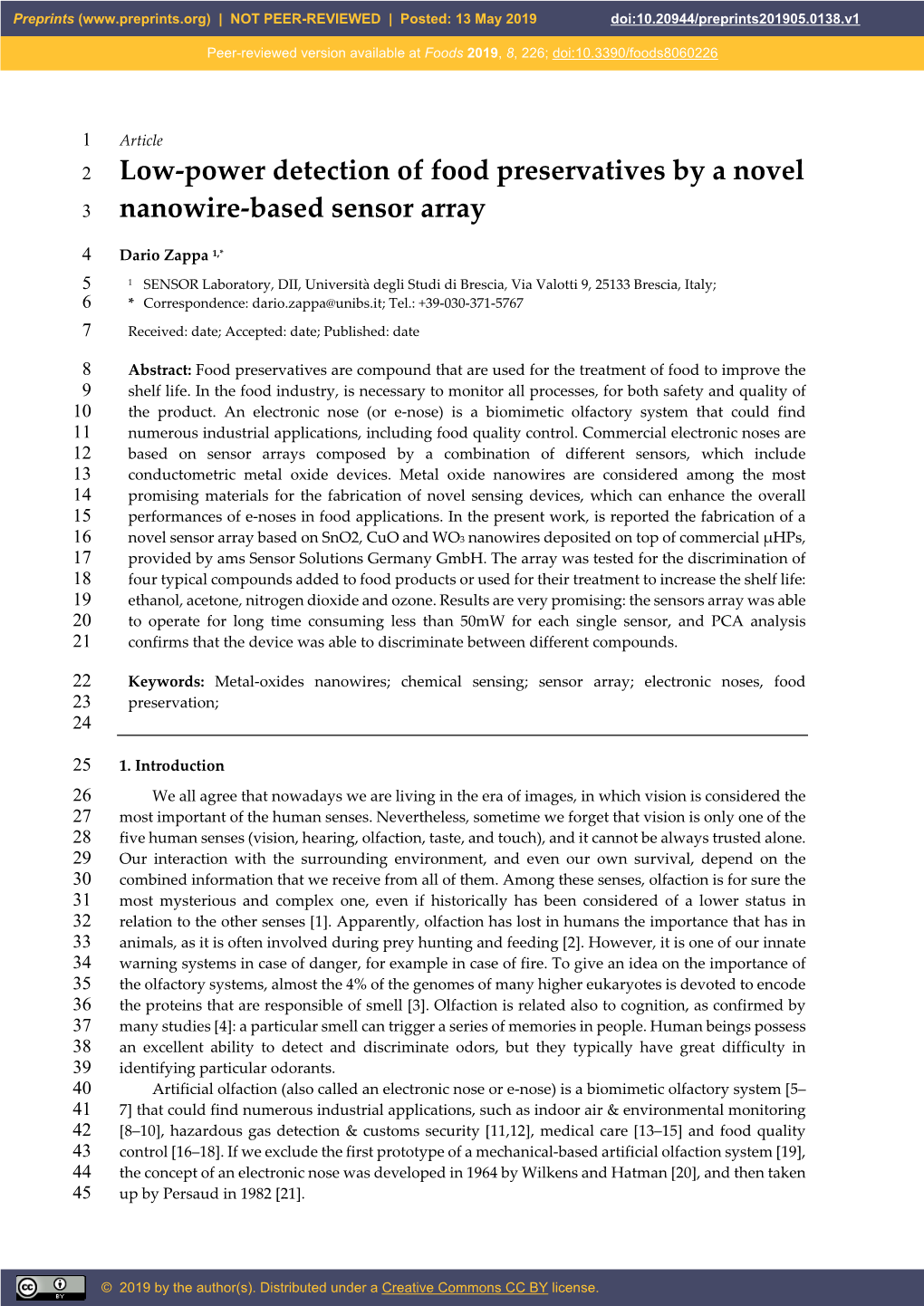
Load more
Recommended publications
-
Polymer Based Chemical Sensor Array Fabricated with Conventional Microelectronic Processes
JOURNAL OF OPTOELECTRONICS AND ADVANCED MATERIALS, Vol. 12, No. 5, May 2010, p. 1147 - 1152 Polymer based chemical sensor array fabricated with conventional microelectronic processes M. KITSARAa,b, D. GOUSTOURIDISa, E. VALAMONTESc, P. OIKONOMOUa, K. BELTSIOSb, I. RAPTISa* aInstitute of Microelectronics, NCSR “Demokritos”, 15310, Athens, Greece bMaterials Science and Engineering Dept, University of Ioannina, Ioannina 45110 Greece cElectronics Engineering Dept, TEI of Athens, Egaleo 12243, Greece A polymer array fabricated on the same substrate with conventional microelectronic processes is introduced for gas sensing applications. The process is based on photolithographic processes and takes advantage of the balance between UV exposure dose, material tone and developers used. The sensing properties of the lithographically defined films in the array were characterized for various analytes through in situ monitoring of films swelling by white light reflectance spectroscopy. The sensing responses are post processed by Principal Component Analysis and the discrimination between analytes with similar and totally different analytes is presented. (Received January 4, 2010; accepted May 26, 2010) Keywords: Chemical sensors, Polymer deposition, Photolithography, Vapor sorption, Polymer swelling 1. Introduction providing bulk absorption. Vacuum deposition techniques are also possible methods of obtaining thin polymer films One of the most important problems in chemical including mostly sputtering [13], plasma polymerization sensor fabrication is the controlled deposition of the [14]. chemically sensitive layer on the transducer [1]. This In the present work a series of photosensitive problem becomes more critical in the case of sensor arrays polymeric materials is defined on the same substrate using where different sensing materials should be deposited on conventional lithographic techniques only. -
Wearable RF Resonant Gaseous Chemical Sensor Array
Wearable RF Resonant Gaseous Chemical Sensor Array by Wei Ting Chen A thesis presented to the University of Waterloo in fulfillment of the thesis requirement for the degree of Doctor of Philosophy in Electrical and Computer Engineering Waterloo, Ontario, Canada, 2015 © Wei Ting Chen 2015 AUTHOR’S DECLARATION I hereby declare that I am the sole author of the thesis. This is the true copy of the thesis, including any required final revision, as accepted by the examiners. I understand that my thesis may be made electronically available to the public. ii ABSTRACT Biomarker detection is a major engineering goal that enables numerous applications in the fields of biomedical and law enforcement. By monitoring the conditions of the subject with a dedicated biomarker detection system, the health condition as well as other biomedical parameters of interest can be evaluated in real-time, and further preemptive measures can be taken to improve the safety and chance of survival of the subject. In the pursuit of a better biomarker monitoring system, the ubiquitous and unobtrusiveness of the sensor is proven to be a critical design factor that directly impacts the subject’s safety and the comfort level. The thesis presents the research results obtained for a novel single-port, multi-pole resonant sensor array fabricated on a novel Frame-Flex flexible substrate for a wearable epidermal ethanol sensor system in an attempt to achieve minimal obtrusiveness to the subject under testing. In this system, individual sensors carrying different functional polymers are brought together to share the same electrical input and output, and their resonance behavior along with inter-resonator coupling are captured through a single reflected array response curve (S11). -
Microarray Study of Temperature Dependent Sensitivity and Selectivity of Metal/Oxide Sensing Interfaces
Microarray study of temperature dependent sensitivity and selectivity of metal/oxide sensing interfaces J. Tiffany, R. E. Cavicchi, S. Semancik National Institute of Standards and Technology Gaithersburg, MD 20899 ABSTRACT Conductometric gas microsensors offer the benefits of ppm-level sensitivity, real-time data, simple interfacing to electronics hardware, and low power consumption. The type of device we have been exploring consists of a sensor film deposited on a "microhotplate"- a 100 micron platform with built-in heating (to activate reactions on the sensing surface) and thermometry. We have been using combinatorial studies of 36-element arrays to characterize the relationship between sensor film composition, operating temperature, and response, as measured by the device's sensitivity and selectivity. Gases that have been tested on these arrays include methanol, ethanol, dichloromethane, propane, methane, acetone, benzene, hydrogen, and carbon monoxide, and are of interest in the management of environmental waste sites. These experiments compare tin oxide films modified by catalyst overlayers, and ultrathin metal seed layers. The seed layers are used as part of a chemical vapor deposition process that uses each array element's microheater to activate the deposition of SnO2, and control its microstructure. Low coverage (2 nm) catalytic metals (Pd, Cu, Cr, In, Au) are deposited on the oxides by masked evaporation or sputtering. This presentation demonstrates the value of an array-based approach for developing film processing methods, measuring performance characteristics, and establishing reproducibility. It also illustrates how temperature-dependent response data for varied metal/oxide compositions can be used to tailor a microsensor array for a given application. -
A Possible Roadmap for NEMS Sensors
A Possible Roadmap for NEMS Sensors Cornel Cobianu and Bogdan Serban Sensors and Wireless Laboratory Bucharest Honeywell Romania SRL October 4-5th , 2011 International Symposium for Advanced Hybrid Nano-Devices Outline • Milestones of Nanotechnology Evolution • From MEMS to NEMS • Top-Down • Bottom-Up • Mixed Top-Down-Bottom-Up • Honeywell contributions • Conclusions 4-5 October 2011 International Symposium on Advanced Hybrid Nano Devices-Tokyo MilestonesMilestones ofof NanotechnologyNanotechnology EvolutionEvolution Visionary scientists : 1959 : Richard Feynman : “There is plenty of room at the bottom” 1965 : Gordon Moore : “IC complexity will double every 12 months” 1974 : Norio Taniguchi: “Nanotechnology” 1986: Eric Drexler : Engines of creation. The Coming Era of Nanotechnology” Governmental plans: 2000+ : USA’s National Nanotechnology Initiative 2011-2020 : 6 EU FET Research flagship Initiatives (ex. “Guardian Angels”) 2011-2015 : Japan :The 4th S&T Basic Plan( 2011-2015): basic research “Bottom-Up-Top-Down”- a synergetic interaction in S&T policy Why nanotechnology is important ? 4-5 October 2011 International Symposium on Advanced Hybrid Nano Devices-Tokyo MegatrandsMegatrands andand NanotechnologyNanotechnology Ageing Population Globalization Health and environment awareness Urbanization (smart-eco city) Network organizing Technology progress- Megatrends- Society Needs -Technology progress ! 4-5 October 2011 International Symposium on Advanced Hybrid Nano Devices-Tokyo NanotechnologyNanotechnology forfor Society’sSociety’s needsneeds Mihail. C. Roco “ US National Nanotechnology Initiative, 2000” and examples from us 1. Passive Nanostructures: GMR sensors Ag nano-ink for bulk applications, CNT in textile Ultradeformable nanomaterial-medicine TiO2, ZnO in sunscreen 2. Active Nanodevices and Circuits: Nanoelectronics era after 2004 3. Complex Nanomachines : Advanced Research! Future Guardian Angel 4. Productive Nanosystems: Basic research ! Future Systems of nanosystems. -
Development of Cross-Reactive Sensors Array: Practical
i DEVELOPMENT OF CROSS-REACTIVE SENSORS ARRAY: PRACTICAL APPROACH FOR ION DETECTION IN AQUEOUS MEDIA Yuanli Liu A Dissertation Submitted to the Graduate College of Bowling Green State University in partial fulfilment of the requirements for the degree of DOCTOR OF PHILOSOPHY December 2012 Committee: Dr. Pavel Anzenbacher, Advisor Dr. Junfeng Shang Graduate Faculty Representative Dr. Peter Lu Dr. Thomas H. Kinstle ii ABSTRACT Dr. Pavel Anzenbacher Jr., Advisor Chemical sensing platforms that can sensitively, rapidly and accurately detect specific chemical species in various operating media are of great importance, especially in complex aqueous environments. Chemical sensor array coupled with chemometrics methods provide an impressive option for high performance chemical sensing. The efforts of this dissertation focus on the application of fluorimetric sensors array in ions detection in complex aqueous media. This dissertation first presents the various signal transduction mechanisms that involve in optical chemosensor design. The sensing elements are created by embedding chemosensors into polymer matrix, then they are arrayed in microtiter plate containing multiple wells. The chemometrics methods used for analyzing the multivariate signal arising from the sensor array are introduced in detail. In the part of practical application of sensors array. The first work aims to detect ions in water by a simple sensors array contains six off-the shelf chemosensors. It turns out that the sensors array is able to recognize cations, anions and ion-pairs with recognition efficiency (6:35) and higher than 93% classification accuracy in water at a wide range of pH (5-9). Such a high discrimination capacity was generally achieved only with structurally complex chemical sensors. -
Applications and Advances in Bioelectronic Noses for Odour Sensing
Applications and Advances in Bioelectronic Noses for Odour Sensing The MIT Faculty has made this article openly available. Please share how this access benefits you. Your story matters. Citation Dung, Tran et al. "Applications and Advances in Bioelectronic Noses for Odour Sensing." Sensors 18, 1 (January 2018): 103 © 2018 The Authors As Published http://dx.doi.org/10.3390/s18010103 Publisher Multidisciplinary Digital Publishing Institute Version Final published version Citable link http://hdl.handle.net/1721.1/119445 Terms of Use Creative Commons Attribution Detailed Terms http://creativecommons.org/licenses/by/4.0/ sensors Review Applications and Advances in Bioelectronic Noses for Odour Sensing Tran Thi Dung 1,2,†, Yunkwang Oh 1,3,†, Seon-Jin Choi 4,5 ID , Il-Doo Kim 5, Min-Kyu Oh 3,* ID and Moonil Kim 1,2,6,* 1 Hazards Monitoring Bionano Research Center (HMBRC), Korea Research Institute of Bioscience and Biotechnology (KRIBB), 125 Gwahak-Ro, Yuseong-Gu, Daejeon 34141, Korea; [email protected] (T.T.D.); [email protected] (Y.O.) 2 Department of Nanobiotechnology, Korea University of Science and Technology (UST), 217 Gajeong-Ro, Yuseong-Gu, Daejeon 34113, Korea 3 Department of Chemical and Biological Engineering, Korea University, 145 Anam-Ro, Sungbuk-Gu, Seoul 02841, Korea 4 Department of Chemistry, Massachusetts Institute of Technology, 77 Massachusetts Avenue, Cambridge, MA 02139, USA; [email protected] or [email protected] 5 Department of Materials Science and Engineering, Korea Advanced Institute of Science and Technology (KAIST), 291 Daehak-Ro, Yuseong-Gu, Daejeon 34141, Korea; [email protected] 6 Department of Pathobiology, College of Veterinary Medicine Nursing & Allied Health (CVMNAH), Tuskegee University, Tuskegee, AL 36088, USA * Correspondence: [email protected] (M.-K.O.); [email protected] (M.K.); Tel.: +82-42-8798-447 (M.K.); Fax: +82-42-8798-594 (M.K.) † These authors contributed equally to this work. -
Electronic Nose and Its Applications: a Survey
International Journal of Automation and Computing 17(2), April 2020, 179-209 DOI: 10.1007/s11633-019-1212-9 Electronic Nose and Its Applications: A Survey Diclehan Karakaya Oguzhan Ulucan Mehmet Turkan Department of Electrical and Electronics Engineering, Izmir University of Economics, Izmir 35330, Turkey Abstract: In the last two decades, improvements in materials, sensors and machine learning technologies have led to a rapid extension of electronic nose (EN) related research topics with diverse applications. The food and beverage industry, agriculture and forestry, medi- cine and health-care, indoor and outdoor monitoring, military and civilian security systems are the leading fields which take great ad- vantage from the rapidity, stability, portability and compactness of ENs. Although the EN technology provides numerous benefits, fur- ther enhancements in both hardware and software components are necessary for utilizing ENs in practice. This paper provides an ex- tensive survey of the EN technology and its wide range of application fields, through a comprehensive analysis of algorithms proposed in the literature, while exploiting related domains with possible future suggestions for this research topic. Keywords: Artificial intelligence, machine learning, pattern recognition, electronic nose (EN), sensors technology. 1 Introduction aromas with a chemical electronic sensor array was primarily mentioned in [12] and then in [13] in the early All kinds of innovation are possible with inspiration. 1980s. However, the EN concept could not be actualized As image processing is inspired by the sense of sight, the at that time due to limitations in the sensors technology. electronic nose (abbreviation EN, enose, e-nose) – also In the late 1990s then, the term “electronic nose” was known as an odor sensor, aroma sensor, mechanical nose, mentioned in [14]. -
Towards a Chemiresistive Sensor-Integrated Electronic Nose: a Review
Sensors 2013, 13, 14214-14247; doi:10.3390/s131014214 OPEN ACCESS sensors ISSN 1424-8220 www.mdpi.com/journal/sensors Review Towards a Chemiresistive Sensor-Integrated Electronic Nose: A Review Shih-Wen Chiu and Kea-Tiong Tang * Department of Electrical Engineering, National Tsing Hua University/No. 101, Sec. 2, Kuang-Fu Road, Hsinchu 30013, Taiwan; E-Mail: [email protected] * Author to whom correspondence should be addressed; E-Mail: [email protected]; Tel.: +886-3-516-2178; Fax: +886-3-571-5971. Received: 7 August 2013; in revised form: 28 September 2013 / Accepted: 9 October 2013 / Published: 22 October 2013 Abstract: Electronic noses have potential applications in daily life, but are restricted by their bulky size and high price. This review focuses on the use of chemiresistive gas sensors, metal-oxide semiconductor gas sensors and conductive polymer gas sensors in an electronic nose for system integration to reduce size and cost. The review covers the system design considerations and the complementary metal-oxide-semiconductor integrated technology for a chemiresistive gas sensor electronic nose, including the integrated sensor array, its readout interface, and pattern recognition hardware. In addition, the state-of-the-art technology integrated in the electronic nose is also presented, such as the sensing front-end chip, electronic nose signal processing chip, and the electronic nose system-on-chip. Keywords: metal-oxide semiconductor; conductive-polymer; sensing front-end; electronic nose signal processing chip; electronic nose system-on-chip (SoC) 1. Introduction Olfaction is one of the five major human senses (vision, hearing, olfaction, taste, and touch). -
Use of Electronic Noses for Diagnosis of Digestive and Respiratory Diseases Through the Breath
biosensors Review Use of Electronic Noses for Diagnosis of Digestive and Respiratory Diseases through the Breath Carlos Sánchez 1,2 , J. Pedro Santos 1 and Jesús Lozano 3,* 1 Institute of Physics Technology and Information (CSIC), 28006 Madrid, Spain; [email protected] (C.S.); [email protected] (J.P.S.) 2 Up Devices and Technologies, 28021 Madrid, Spain 3 Industrial Engineering School, University of Extremadura, 06006 Badajoz, Spain * Correspondence: [email protected]; Tel.: +34-924-289-300 Received: 12 January 2019; Accepted: 21 February 2019; Published: 28 February 2019 Abstract: The increased occurrence of chronic diseases related to lifestyle or environmental conditions may have a detrimental effect on long-term health if not diagnosed and controlled in time. For this reason, it is important to develop new noninvasive early diagnosis equipment that allows improvement of the current diagnostic methods. This, in turn, has led to an exponential development of technology applied to the medical sector, such as the electronic nose. In addition, the appearance of this type of technology has allowed the possibility of studying diseases from another point of view, such as through breath analysis. This paper presents a bibliographic review of past and recent studies, selecting those investigations in which a patient population was studied with electronic nose technology, in order to identify potential applications of this technology in the detection of respiratory and digestive diseases through the analysis of volatile organic compounds present in the breath. Keywords: electronic nose; gas sensors; biomarkers; diseases; digestive system; respiratory system; volatile organic compounds; breath 1. Introduction The relationship between aromas present in the breath and disease has been known by doctors for a several hundred years. -
An Integrated Chemical Sensor Array Using Carbon Black Polymers and a Standard Cmos Process
AN INTEGRATED CHEMICAL SENSOR ARRAY USING CARBON BLACK POLYMERS AND A STANDARD CMOS PROCESS Jeffrey A. Dickson’, Michael S. Freund’, Nathan S. Lewis’, Rodney M. Goodman’ ’ Department of Electrical Engineering ‘Department of Chemistry California Institute of Technology Pasadena, California 9 1125 even wearable chemical sensor arrays that rival the detection and ABSTRACT discrimination capabilities of mammalian olfaction. We have developed a new chemical sensor array by combining polymer-based chemiresistors with a standard integrated circuit DESIGN AND FABRICATION technology. We fabricated an array of addressable chemical sen- sor sites in a CMOS process, and then performed a post-processing The sensor consists of an array of individually addressable electri- step of electroless gold to create sensor contacts. We create sen- cal contacts, on which a polymer/carbon black mixture is sors by spraying a mixture of nonconductive polymers and carbon deposited. The sensor technology is well suited to integration with black particles onto the sensor sites. We demonstrate that an array on-chip circuitry. The array allows each sensor to be individually of diverse chemical sensors can perform discrimination of odors. addressed. INTRODUCTION Figure 1 shows the schematic of the unit sensor cell. The cell con- sists of a switch transistor and decoding logic. The availability of This paper describes the development of an array of chemical sen- only two metals layers in the IC process required transistors at sors. The sensors are based on the polymer approach of Lewis et each sensor cell to perform decoding. This circuitry (Ml-M4) al.[l, 21 employing carbon black and non-conducting polymers. -
Laterally Extended Atomically Precise Graphene Nanoribbons With
University of Nebraska - Lincoln DigitalCommons@University of Nebraska - Lincoln Faculty Publications -- Chemistry Department Published Research - Department of Chemistry 2017 Laterally extended atomically precise graphene nanoribbons with improved electrical conductivity for efficient gas sensing Mohammad Mehdi Pour University of Nebraska - Lincoln Andrey Lashkov Gagarin State Technical University of Saratov Adrian Radocea University of Illinois at Urbana-Champaign Ximeng Liu University of Illinois at Urbana-Champaign Tao Sun University of Illinois at Urbana-Champaign See next page for additional authors Follow this and additional works at: http://digitalcommons.unl.edu/chemfacpub Part of the Analytical Chemistry Commons, Medicinal-Pharmaceutical Chemistry Commons, and the Other Chemistry Commons Pour, Mohammad Mehdi; Lashkov, Andrey; Radocea, Adrian; Liu, Ximeng; Sun, Tao; Lipatov, Alexey; Korlacki, Rafal A.; Shekhirev, Mikhail; Aluru, Narayana R.; Lyding, Joseph W.; Sysoev, Victor; and Sinitskii, Alexander, "Laterally extended atomically precise graphene nanoribbons with improved electrical conductivity for efficient gas sensing" (2017). Faculty Publications -- Chemistry Department. 115. http://digitalcommons.unl.edu/chemfacpub/115 This Article is brought to you for free and open access by the Published Research - Department of Chemistry at DigitalCommons@University of Nebraska - Lincoln. It has been accepted for inclusion in Faculty Publications -- Chemistry Department by an authorized administrator of DigitalCommons@University of -
Paper-Derived Ammonia Sensors Integrating a Natural Deep Eutectic Solvent
Clemson University TigerPrints All Theses Theses May 2020 Paper-Derived Ammonia Sensors Integrating A Natural Deep Eutectic Solvent Makenzie Leigh Reynolds Clemson University, [email protected] Follow this and additional works at: https://tigerprints.clemson.edu/all_theses Recommended Citation Reynolds, Makenzie Leigh, "Paper-Derived Ammonia Sensors Integrating A Natural Deep Eutectic Solvent" (2020). All Theses. 3280. https://tigerprints.clemson.edu/all_theses/3280 This Thesis is brought to you for free and open access by the Theses at TigerPrints. It has been accepted for inclusion in All Theses by an authorized administrator of TigerPrints. For more information, please contact [email protected]. PAPER-DERIVED AMMONIA SENSORS INTERGRATING A NATURAL DEEP EUTECTIC SOLVENT A Thesis Presented to the Graduate School of Clemson University In Partial Fulfillment of the Requirements for the Degree Master of Science Chemistry by Makenzie L. Reynolds May 2020 Accepted by: Carlos D. Garcia, Committee Chair W. Bill Pennington R. Kenneth Marcus ABSTRACT Ammonia is a naturally-occurring gas, present throughout the atmosphere at sub-ppb concentrations. As result of various processes, significantly higher concentrations can be found in the areas surrounding industrial and agricultural operations. In such cases, the presence of NH3 in air not only is associated with a very pungent odor and potential toxicity but can also affect the environment, animals, plants, and humans. Aiming to provide a simple platform to monitor NH3 in air, a paper-derived gas sensor, integrating a natural deep eutectic solvent (NADES) was developed. The herein described paper-derived ammonia gas sensor was fabricated using direct laser scribing, to form a carbon-based interdigitated array.