Optimisation of Low Cycle Fatigue Life in Turbine Rear Frame
Total Page:16
File Type:pdf, Size:1020Kb
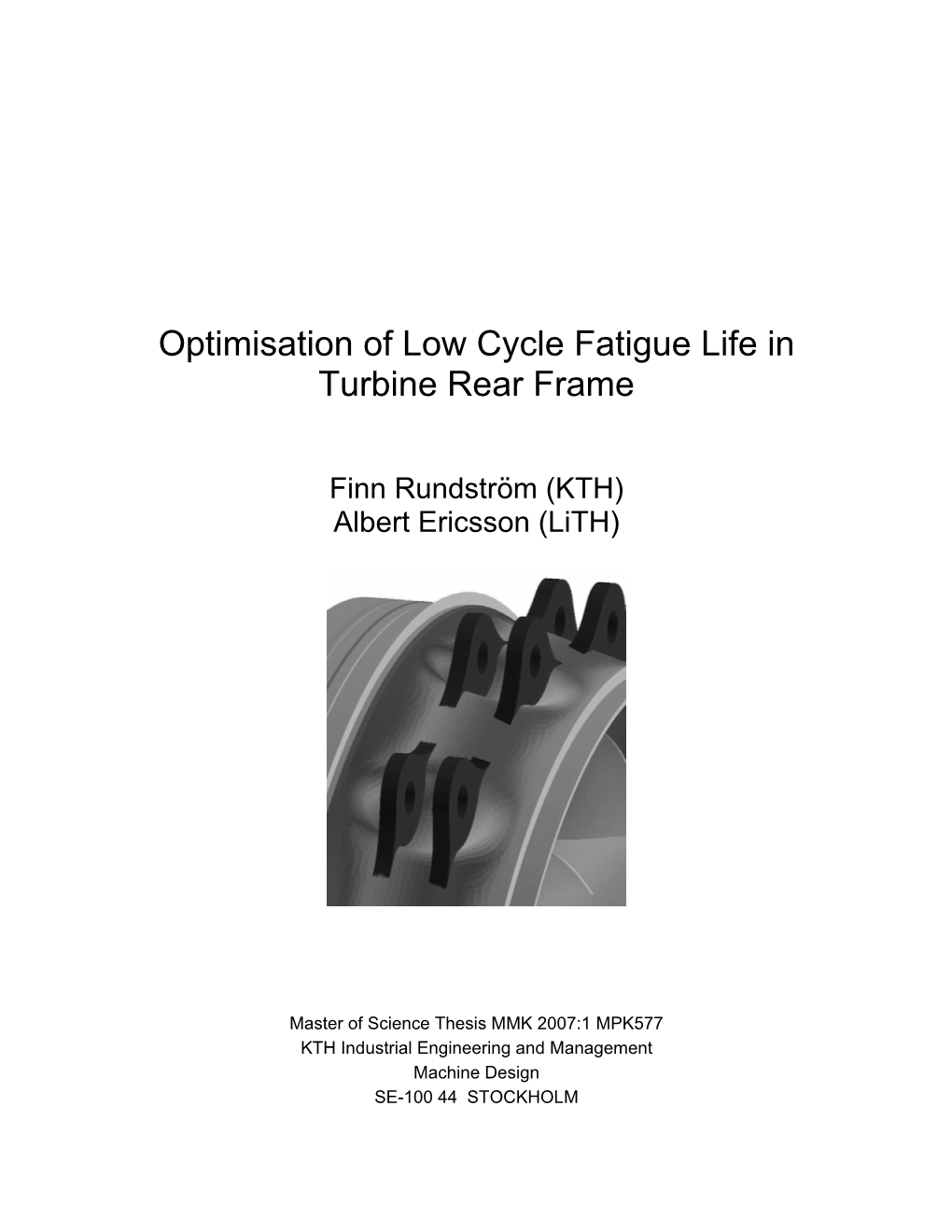
Load more
Recommended publications
-
Technical Supplements
Technical Supplements S1 The IG JAS Investment In this Technical Supplement the JAS 39 Gripen product concept is outlined, the procurement process documented, the Industry Group IG JAS presented and the critical role of the competent public procurement agency, the FMV, highlighted. S1.1 The Procurement of the JAS 39 Gripen Aircraft with Swing-Role Capabilities The JAS 39 Gripen multirole combat aircraft (J stands for fighter, A for Attack and S for Surveillance/reconnaissance) is a fourth generation aircraft that entered operational service in 1997. It replaced the Viggen, the last of which was taken out of service in 2006. JAS 39 Gripen is a combat aircraft with swing-role capabilities that can change mission in flight. This swing-role capability was unique when Gripen was launched but has later been introduced on the French Rafale and the Eurofighter. Other competing multirole aircraft first have to land to reconfigure its information, guidance, and weapons systems for a new role. Gripen was the first “unstable” aircraft in the world which meant that in order for the aircraft to be stable at all speeds and in all maneuvers many more navigation surfaces are needed than the pilot can possibly control himself to minimize air friction at each moment. He needs incredibly sophisticated computer systems support to maneuver the aircraft effectively and safely. Competing fourth generation combat aircraft are F-35/JSF (the USA, not yet (2009) delivered to market), the Eurofighter Typhoon (the UK, etc.) and Rafale (Dassault, France). JAS 39 Gripen also competes with upgraded versions of the third generation aircraft of Lockheed Martin F-16 (the USA, first delivered in 1978), Boeing F/A18 Hornet (the USA, first delivered in 1983), Dassault Mirage 2000 (France, first delivered in 1983), and Mig-29 (the former Soviet Union, first delivered in 1977). -
Global Economy
INNOVATIONS IN MATERIALS TECHNOLOGY GLOBAL ECONOMY Stainless steel saves weight, reduces emissions in autos BRIEFS Stainless steel in automotive construction can save weight and thus conserve resources without Alcan has inaugurated a compromising safety standards, according to the “Next Generation Vehicle” project, an alliance of technologically advanced leading stainless steel producers and automotive OEMs. horizontal furnace at its The project was launched at the end of 2004 with the aim of identifying potential for stainless Sierre facility in Switzerland. Its power steel in auto structures. The automotive OEMs participating in the project were Audi, BMW, Chrysler, consumption is four times Fiat, General Motors/Saab, and Ford/Volvo. The stainless steel producers involved were Thyssen lower than older furnaces, Krupp Nirosta (Germany), Outokumpu (Finland), and ArcelorMittal Stainless (France). and its closed circulation The goal was to draw up processing guidelines for stainless steels as a prerequisite for their appli- system limits its water cation. For example, this was done with reference to B-pillars, which were tested in crash simulations. consumption. The results were verified in collaboration with leading suppliers of simulation programs for metal www.alcan.com forming. The project’s findings have been summarized in design and processing guidelines. A cost model was developed in collaboration with the Massachusetts Institute of Technology. ArcelorMittal plans to invest $1.3 billion annu- This program allows different production methods and materials to be compared directly and ally in its European the optimum stainless steel solution determined. flat-bar steel production For more information: Erik Walner, ThyssenKrupp Stainless AG, Germany; tel: 49 203 52 45130; plants until 2012. -
Beläggningsanalys Av Motorprovningen Vid Volvo Aero
Examensarbete LITH-ITN-KTS-EX--05/003--SE Beläggningsanalys av motorprovningen vid Volvo Aero Corporation Fredrik Bark 2005-01-28 Department of Science and Technology Institutionen för teknik och naturvetenskap Linköpings Universitet Linköpings Universitet SE-601 74 Norrköping, Sweden 601 74 Norrköping LITH-ITN-KTS-EX--05/003--SE Beläggningsanalys av motorprovningen vid Volvo Aero Corporation Examensarbete utfört i kommunikation- och transportsystem vid Linköpings Tekniska Högskola, Campus Norrköping Fredrik Bark Handledare Tomas Mars Examinator Martin Rudberg Norrköping 2005-01-28 Datum Avdelning, Institution Date Division, Department Institutionen för teknik och naturvetenskap 2005-01-28 Department of Science and Technology Språk Rapporttyp ISBN Language Report category _____________________________________________________ x Svenska/Swedish Examensarbete ISRN LITH-ITN-KTS-EX--05/003--SE Engelska/English B-uppsats _________________________________________________________________ C-uppsats Serietitel och serienummer ISSN x D-uppsats Title of series, numbering ___________________________________ _ ________________ _ ________________ URL för elektronisk version http://www.ep.liu.se/exjobb/itn/2005/kts/003/ Titel Title Beläggningsanalys av motorprovningen vid Volvo Aero Corporation Författare Author Fredrik Bark Sammanfattning Abstract Detta är resultatet av en studie som har utförts vid motorprovningen på Volvo Aero Corporation i Trollhättan. Motorprovningen provar flygplansmotorer, komponenter till dessa och rymddetaljer samt utför underhåll och utveckling av Volvo Aeros testceller, TC. Till dessa testceller kommer ett antal olika motormodeller för prov snarast möjligt. Motorprovningen står nu inför vissa större beslut om att eventuellt lägga ner en av testcellerna och överföra dess motorer till en annan testcell. Motorprovningen har idag inget verktyg för att mäta hur stor kapacitet de olika testcellerna har, och om denna nerläggning då är möjlig. -
Volvo Aero to Partner with Pratt & Whitney on Geared Turbofan™ Engine
Press Information Volvo Aero to Partner with Pratt & Whitney on Geared Turbofan™ Engine Volvo Aero has entered into an agreement with aircraft engine manufacturer Pratt & Whitney to join P&W’s Geared Turbofan™ engine program. Under this arrangement, Volvo Aero will be responsible for three major components for both the Mitsubishi Regional Jet (MRJ) and the Bombardier CSeries aircraft engines. The Geared Turbofan engine will be a product unique in the aircraft industry, bringing double-digit reductions in fuel burn, environmental emissions, engine noise and operating costs. For Volvo Aero, the agreement is expected to result in sales of SEK 50 billion during 40 years, the largest involvement in a commercial engine program ever. Two years ago, Volvo Aero and Pratt & Whitney signed an agreement to demonstrate new technology for the new Geared Turbofan engine. Since then, Volvo Aero has worked to develop advanced light weight technologies for the new engine concept. Volvo Aero brings expertise in turbine exhaust case technology to development of the Geared Turbofan engine. According to the agreement, Volvo Aero will participate as a partner in design, development, production and aftermarket in this engine project, with overall responsibility for the Intermediate Case and Turbine Exhaust Case as well as Low Pressure Turbine Shaft production responsibility. “We are delighted to have reached this agreement with Pratt & Whitney, not least because we know that this engine will contribute to improving the environment by reducing fuel consumption, emissions and noise,” says Olof Persson, President of Volvo Aero. “Participating in an engine concept that has excellent prospects for enhancing our current program portfolio in this thrust region of the engine market is also an important sign of success for Volvo Aero. -
To Volvo Aero Corporation for R &Amp
17.11.2009 EN Official Journal of the European Union L 301/41 COMMISSION DECISION of 17 June 2009 on the State aid C 33/08 (ex N 732/07) to Volvo Aero Corporation for R & D, which Sweden intends to implement (notified under document C(2009) 4542) (Only the Swedish version is authentic) (Text with EEA relevance) (2009/838/EC) THE COMMISSION OF THE EUROPEAN COMMUNITIES mail between managers of the beneficiary. This supple mentary information was submitted on 19 June 2008. Having regard to the Treaty establishing the European Community, and in particular the first subparagraph of (3) By letter of 16 July 2008 the Commission notified to Article 88(2) thereof, Sweden its decision to initiate proceedings pursuant to Article 88(2) of the EC Treaty on the above mentioned measure. The decision of the Commission to initiate proceedings has been published in the Official Journal of Having regard to the Agreement on the European Economic the European Union ( 2). The Commission invited interested Area, and in particular Article 62(1)(a) thereof, parties to submit their observations on the measure. Sweden submitted observations on 17 October 2008. Having called on interested parties to submit their comments 1 pursuant to those provisions ( ), (4) By fax dated 28 October 2008, Fred Bodin, the former President and CEO of Volvo Aero, submitted obser vations. By letter of 31 October 2008, GE Aviation submitted observations. By e-mail dated 3 November Having regard to those comments, 2008, the IF Metalworkers union of Volvo Aero submitted observations. Whereas: (5) By letter of 3 November 2008 the Commission has forwarded these observations to the Swedish authorities, which submitted comments on 12 December 2008. -
Volvo Aero Norway to Be Supplier to the General Electric Engine for the Joint Strike Fighter (JSF)
Press Information Volvo Aero Norway to be supplier to the General Electric engine for the Joint Strike Fighter (JSF) Volvo Aero Norway has signed an agreement with General Electric to produce two key components for the F136 engine in the US F-35 Joint Strike Fighter (JSF) aircraft. The agreement covers the development phase and that Volvo Aero Norway will be the exclusive supplier of these components. The components for the F136 engine that Volvo Aero Norway will supply are the aft compressor case and the forward compressor case. “We are very satisfied with Volvo Aero Norway’s continued involvement in the F136 engine program,” says Jean Ludon-Rodgers, General Electric FET. “Its expertise within component manufacturing is a valuable addition to the group of renowned international aircraft engine companies that will participate in developing this engine in world class.” “Volvo Aero Norway is highly pleased that General Electric selected us as the supplier of the compressor cases for the F136. The agreement is an important milestone for Volvo Aero Norway,” says Reidar Lyse, President of Volvo Aero Norway. “It strengthens the company’s position in one of the most important military programs in many years. The components also fit well in the company’s strategic product portfolio.” The first components will be delivered during 2007. The Joint Strike Fighter is expected to be the predominant fighter aircraft in the decades immediately ahead. The estimated sales volume is more than 5000 aircraft. The aircraft will be certified with two engines, the F135 from Pratt & Whitney and the F136 from General Electric. -
DISTRIBUTED PROPULSION and TURBOFAN SCALE EFFECTS Anders Lundbladh Volvo Aero Corporation S-46181 Trollhättan, Sweden [email protected]
View metadata, citation and similar papers at core.ac.uk brought to you by CORE provided by Chalmers Publication Library 1 ISABE-2005-1122 DISTRIBUTED PROPULSION AND TURBOFAN SCALE EFFECTS Anders Lundbladh Volvo Aero Corporation S-46181 Trollhättan, Sweden [email protected] Tomas Grönstedt Chalmers University Sweden ABSTRACT ps Propulsion System, i.e. exclusive of airframe drag effect on intake pressure recovery A coupled aircraft and engine model is used to evaluate the fuel consumption and mission weight of distributed propulsion aircraft. The engine cycle is INTRODUCTION optimized for the installation to show the ultimate performance of each propulsion alternative. The A conventional subsonic transport aircraft is effect of higher specific fuel consumption for smaller equipped with two to four turbofan engines. The engines is weighed against the potentially lower trend from the fifties until now has favored the twin installation weight and higher integration efficiency underwing engine configuration. An alternative is to of distributed propulsion. use a large number of engines. This concept can broadly be described as distributed propulsion. Nomenclature More than four engines have been used in the past for reasons of reliability and unavailability of V Velocity relative to the aircraft sufficiently large engines (compare e.g. the “Spruce T Total propulsive thrust Goose” and the B-52). Reliability concerns also led P Propulsive power to the requirement that an ocean crossing aircraft D Drag must have at least three engines, although the number FHV Fuel Heating Value of routes affected by this has decreased due to W Mass flow ETOPS qualification of twin engine aircraft. -
Aerospace Propulsion from Insects to Spaceflight
AEROSPACE PROPULSION FROM INSECTS TO SPACEFLIGHT Ulf Olsson Volvo Aero Corporation Vice president Technology (ret) - 2 - Olsson,Ulf Aerospace Propulsion from Insects to Spaceflight Copyright © 2006 by Volvo Aero Corporation. 1st Edition 2006 published Heat and Power Technology, KTH, Stockholm, Sweden. 2nd Edition April 2012 PREFACE This book is an introduction to the theory and history of aerospace propulsion. It describes how this specific technology has reached its present form and how it may develop in the future. To understand the technical parts, the reader is assumed to know about thermodynamics and aerodynamics at university level but no prior knowledge of aerospace propulsion technologies is required. For those wishing to go directly to the mathematics, a number of calculation schemes are given in the text as Appendices to various Chapters. They make it possible to write computer programs for performance estimates of the various types of engines. A number of exercises are included at the end of the different chapters. Solutions to the examples are provided in a separate Chapter at the end of the book together with the relevant equations being used. This can be used as a short handbook to the most important equations. For the reader specifically interested in the history of propulsion, a separate guide to the main topics and the most famous names is given under Contents below. Historical notes are also underlined in the text to be easily located. Ulf Olsson April 2012 ii iii CONTENTS Preface 0. Introduction Page 1 1. The balloons lighter than air 5 2. Newton and the reaction force 11 3. -
Modernization of the Czech Air Force
Calhoun: The NPS Institutional Archive Theses and Dissertations Thesis Collection 2001-06 Modernization of the Czech Air Force. Vlcek, Vaclav. http://hdl.handle.net/10945/10888 NAVAL POSTGRADUATE SCHOOL Monterey, California THESIS MODERNIZATION OF THE CZECH AIR FORCE by Vaclav Vlcek June 2001 Thesis Advisor: Raymond Franck Associate Advisor: Gregory Hildebrandt Approved for public release; distribution is unlimited. 20010807 033 REPORT DOCUMENTATION PAGE Form Approved OMBNo. 0704-0188 Public reporting burden for this collection of information is estimated to average 1 hour per response, including the time for reviewing instruction, searching existing data sources, gathering and maintaining the data needed, and completing and reviewing the collection of information. Send comments regarding this burden estimate or any other aspect of this collection of information, including suggestions for reducing this burden, to Washington headquarters Services, Directorate for Information Operations and Reports, 1215 Jefferson Davis Highway, Suite 1204, Arlington, VA 22202-4302, and to the Office of Management and Budget, Paperwork Reduction Project (0704-0188) Washington DC 20503. 1. AGENCY USE ONLY (Leave blank) 2. REPORT DATE 3. REPORT TYPE AND DATES COVERED June 2001 Master's Thesis 4. TITLE AND SUBTITLE : MODERNIZATION OF THE CZECH AIR FORCE 5. FUNDING NUMBERS 6. AUTHOR(S) Vaclav VIcek 8. PERFORMING 7. PERFORMING ORGANIZATION NAME(S) AND ADDRESS(ES) ORGANIZATION REPORT Naval Postgraduate School NUMBER Monterey, CA 93943-5000 9. SPONSORING / MONITORING AGENCY NAME(S) AND ADDRESS(ES) 10. SPONSORING / MONITORING N/A AGENCY REPORT NUMBER 11. SUPPLEMENTARY NOTES The views expressed in this thesis are those of the author and do not reflect the official policy or position of the Department of Defense or the U.S. -
On the Design of Energy Efficient Aero Engines Some Recent Innovations
THESIS FOR THE DEGREE OF DOCTOR OF PHILOSOPHY in Thermo and Fluid Dynamics On the Design of Energy Efficient Aero Engines Some Recent Innovations By Richard Avellán Department of Applied Mechanics CHALMERS UNIVERSITY OF TECHNOLOGY Göteborg, Sweden, 2011 On the Design of Energy Efficient Aero Engines: Some Recent Innovations Richard Avellán © RICHARD AVELLÁN, 2011. ISBN 978-91-7385-564-8 Doktorsavhandlingar vid Chalmers tekniska högskola Ny serie nr 3245 ISSN 0346-718X Department of Applied Mechanics Chalmers University of Technology SE-412 96 Gothenburg Sweden Telephone + 46 (0)31-772 1000 Cover: [Artist’s impression of a future energy efficient aircraft driven by counter-rotating propeller engines. Source: Volvo Aero Corporation] Printed at Chalmers Reproservice Göteborg, Sweden On the Design of Energy Efficient Aero Engines Some Recent Innovations By Richard Avellán Division of Fluid Dynamics Department of Applied Mechanics Chalmers University of Technology SE-412 96 Göteborg Abstract n the light of the energy crisis of the 1970s, the old aerospace paradigm of flying higher and I faster shifted towards the development of more energy efficient air transport solutions. Today, the aeronautical research and development community is more prone to search for innovative solutions, in particular since the improvement rate of change is decelerating somewhat in terms of energy efficiency, which still is far from any physical limits of aero engine and aircraft design. The Advisory Council for Aeronautics Research in Europe has defined a vision for the year of 2020 for aeronautical research in Europe which states a 50% reduction in CO2, 80% reduction in NOx and a 50% reduction in noise. -
Gripen Surpasses 100,000 Flight Hours Volvo Aero's Engine Safest in The
Press Information Gripen surpasses 100,000 flight hours Volvo Aero’s engine safest in the world The Gripen aircraft surpassed the 100,000-hour market during the week. It was during a flight over a snowy Östergötland landscape, with Saab’s Chief Test Pilot Mats Thorbiörnsson and a Colonel in the South African Air Force at the controls, that the historic milestone was surpassed. Notably in this context is that during these 100,000 hours the Gripen was not involved in an engine- related accident or serious incident. This ought to be unique for all air forces worldwide. Ever since its maiden flight, the Saab test team has carefully tracked each hour flown. The same strict logging was carried out by the Swedish Air Force, by Gripen’s customers in Hungary, Czech Republic, pilot training in the UK and in South Africa. As a result, it was known that this week the 100,000th hour was near. On the morning of January 28, the magic milestone was surpassed. There was no plan for any big ceremony. In March, the first Gripen aircraft will be placed in active service in South Africa and the flight test program is in full swing. At Volvo Aero, it was concluded that the first 100,000 hours was surpassed without a single engine-related accident or incident. “I think this must be a hard record to beat for a single-engine application,” says Rune Hyrefeldt, head of Military Program management at Volvo Aero. The engine in the Gripen, the RM12, is based on the General Electric F404 that Volvo Aero’s and GE’s engineers adapted for the Gripen’s needs in the 1980s. -
MTU Aero Engines (MTX.DE) Investment Memo Date: 6/11/2020; Closing Stock Price: €154.4 (EUR)
MTU Aero Engines (MTX.DE) Investment Memo Date: 6/11/2020; Closing stock price: €154.4 (EUR) Disclaimer This report is for informational purposes only and does not constitute an offer to sell, solicitation to buy, or a recommendation for any security, or as an offer to provide advisory or other services in any jurisdiction in which such offer, solicitation, purchase or sale would be unlawful under the securities laws of such jurisdiction. Any offer to sell is done exclusively through the fund's Private Placement Memorandum. Past performance may not be indicative of any future results. No current or prospective client should assume that the past performance of any investment or investment strategy referenced directly or indirectly herein will perform in the same manner in the future. Different types of investments and investment strategies involve varying degrees of risk—all investing involves risk—and may experience positive or negative growth. Nothing herein should be construed as guaranteeing any investment performance. Investment funds advised by LRT Capital Management, LLC may maintain positions in the securities discussed within. The views presented here are subject to risk and uncertainties. The views presented herein may change without notice. For more information contact [email protected]. Overview MTU Aero Engines (“MTU”) operates in the aerospace engine market as an engine sub-system supplier and an independent provider of maintenance, repair, and overhaul services (MRO). MTU’s business is broken down into three divisions – commercial OEM business, military OEM business, and commercial MRO business. MTU’s revenues are split 40/60 between new engine manufacturing and MRO services, respectively.