Design of Nonlinear Integrated Devices for Quantum Optics Applications
Total Page:16
File Type:pdf, Size:1020Kb
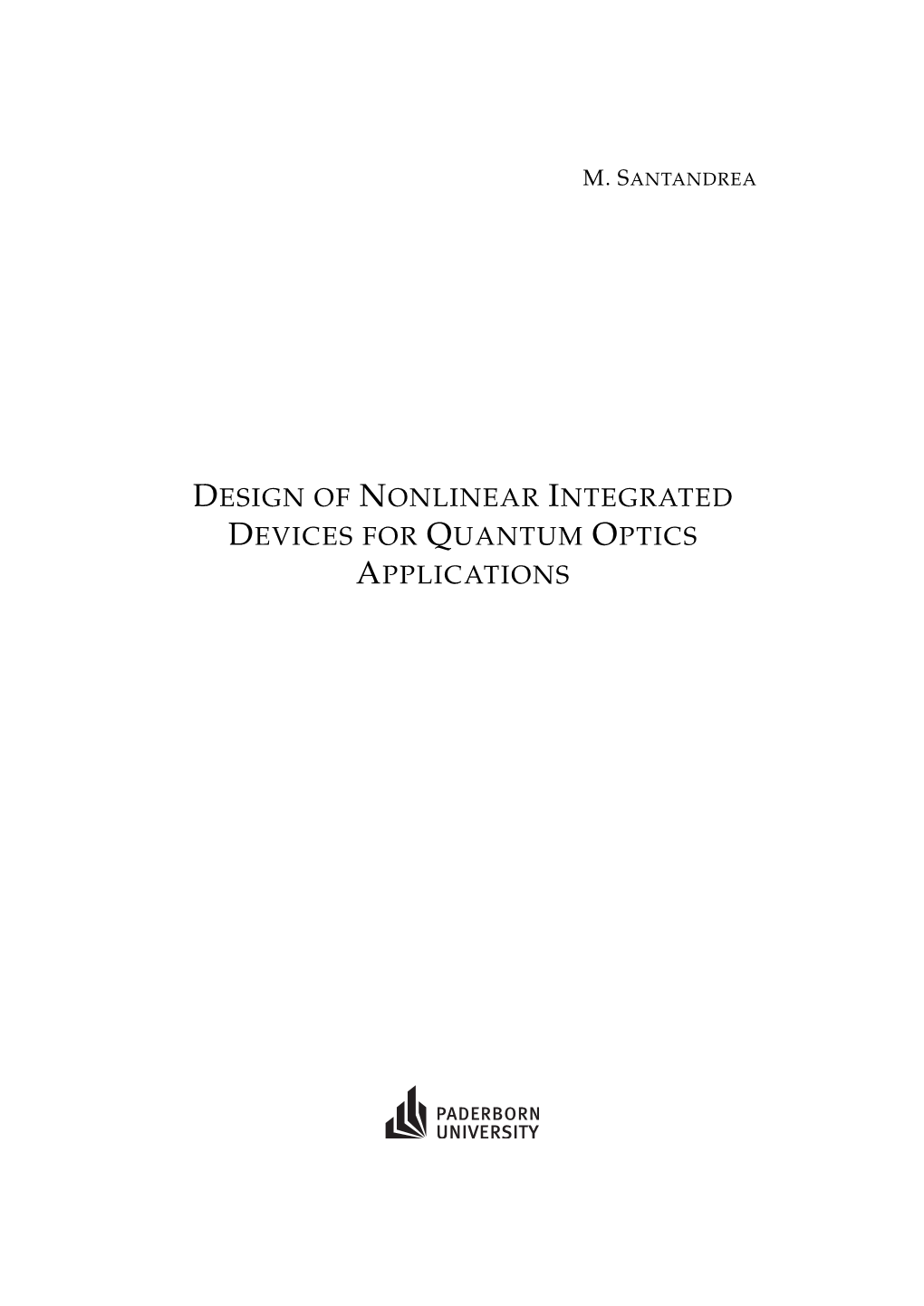
Load more
Recommended publications
-
Arxiv:1812.07904V1 [Quant-Ph] 19 Dec 2018 Tms
Pulse shaping using dispersion-engineered difference frequency generation M. Allgaier,1 V. Ansari,1 J. M. Donohue,1, 2 C. Eigner,1 V. Quiring,1 R. Ricken,1 B. Brecht,1 and C. Silberhorn1 1Integrated Quantum Optics, Applied Physics, University of Paderborn, 33098 Paderborn, Germany 2Institute for Quantum Computing, University of Waterloo, 200 University Ave. West, Waterloo, Ontario, Canada, N2L 3G1 (Dated: December 20, 2018) The temporal-mode (TM) basis is a prime candidate to perform high-dimensional quantum encod- ing. Quantum frequency conversion has been employed as a tool to perform tomographic analysis and manipulation of ultrafast states of quantum light necessary to implement a TM-based encod- ing protocol. While demultiplexing of such states of light has been demonstrated in the Quantum Pulse Gate (QPG), a multiplexing device is needed to complete an experimental framework for TM encoding. In this work we demonstrate the reverse process of the QPG. A dispersion-engineered difference frequency generation in non-linear optical waveguides is employed to imprint the pulse shape of the pump pulse onto the output. This transformation is unitary and can be more efficient than classical pulse shaping methods. We experimentally study the process by shaping the first five orders of Hermite-Gauss modes of various bandwidths. Finally, we establish and model the limits of practical, reliable shaping operation. High-dimensional encoding can potentially increase the To design a DFG pulse shaping device such as the security of quantum communication protocols as well as QPS, one has to first revisit the working principle be- the information capacity of a single photon [1, 2]. -
A Quantum Walk Control Plane for Distributed Quantum Computing In
A quantum walk control plane for distributed quantum computing in quantum networks MatheusGuedesdeAndrade WenhanDai SaikatGuha DonTowsley Abstract—Quantum networks are complex systems of quantum operations, given the fact that physical formed by the interaction among quantum processors separation directly reduces cross talk among qubits [6]. through quantum channels. Analogous to classical com- When the quantum network scenario is considered, the puter networks, quantum networks allow for the distribu- tion of quantum computation among quantum comput- complexity of distributed quantum computing extends ers. In this work, we describe a quantum walk protocol in at least two dimensions. First, physical quantum to perform distributed quantum computing in a quantum channels have a well known depleting effect in the network. The protocol uses a quantum walk as a quantum exchange of quantum data, e.g the exponential decrease control signal to perform distributed quantum operations. in channel entanglement rate with distance [7]. Second, We consider a generalization of the discrete-time coined quantum walk model that accounts for the interaction there is a demand for a quantum network protocol between a quantum walker system in the network graph capable of performing a desired distributed quantum with quantum registers inside the network nodes. The operation while accounting for network connectivity. protocol logically captures distributed quantum com- Generic quantum computation with qubits in distinct puting, abstracting hardware implementation and the quantum processors demands either the application of transmission of quantum information through channels. Control signal transmission is mapped to the propagation remote controlled gates [8] or the continuous exchange of the walker system across the network, while interac- of quantum information. -
Arxiv:2102.01176V2 [Quant-Ph] 14 Jun 2021
Probing the topological Anderson transition with quantum walks Dmitry Bagrets,1 Kun Woo Kim,1, 2 Sonja Barkhofen,3 Syamsundar De,3 Jan Sperling,3 Christine Silberhorn,3 Alexander Altland,1 and Tobias Micklitz4 1Institut f¨urTheoretische Physik, Universit¨atzu K¨oln,Z¨ulpicherStraße 77, 50937 K¨oln,Germany 2Department of Physics, Chung-Ang University, 06974 Seoul, Korea 3Integrated Quantum Optics Group, Institute for Photonic Quantum Systems (PhoQS), Paderborn University, Warburger Straße 100, 33098 Paderborn, Germany 4Centro Brasileiro de Pesquisas F´ısicas, Rua Xavier Sigaud 150, 22290-180, Rio de Janeiro, Brazil (Dated: June 15, 2021) We consider one-dimensional quantum walks in optical linear networks with synthetically intro- duced disorder and tunable system parameters allowing for the engineered realization of distinct topological phases. The option to directly monitor the walker's probability distribution makes this optical platform ideally suited for the experimental observation of the unique signatures of the one- dimensional topological Anderson transition. We analytically calculate the probability distribution describing the quantum critical walk in terms of a (time staggered) spin polarization signal and propose a concrete experimental protocol for its measurement. Numerical simulations back the realizability of our blueprint with current date experimental hardware. I. INTRODUCTION 0 푅 Low-dimensional disordered quantum systems can es- cape the common fate of Anderson localization once 푇 topology comes into play, as first witnessed at the inte- ger quantum Hall plateau transitions [1, 2]. The advent 1 of topological insulators has brought a systematic un- 푅 derstanding of topological Anderson insulators and their phase transitions [3]. The hallmark of Anderson insu- 푇 lating phase with non-trivial topology (coined 'topologi- cal Anderson insulator') is the presence of topologically 2 protected chiral edge states [4, 5]. -
Driven Quantum Walks
Driven Quantum Walks Craig S. Hamilton,1, ∗ Regina Kruse,2 Linda Sansoni,2 Christine Silberhorn,2 and Igor Jex1 1FNSPE, Czech Technical University in Prague, Bˇrehov´a7, 115 19, Praha 1, Czech Republic 2Applied Physics, University of Paderborn, Warburger Straße 100, D-33098 Paderborn, Germany In this letter we introduce the concept of a driven quantum walk. This work is motivated by recent theoretical and experimental progress that combines quantum walks and parametric down- conversion, leading to fundamentally different phenomena. We compare these striking differences by relating the driven quantum walks to the original quantum walk. Next, we illustrate typical dynamics of such systems and show these walks can be controlled by various pump configurations and phase matchings. Finally, we end by proposing an application of this process based on a quantum search algorithm that performs faster than a classical search. PACS numbers: 05.45.Xt, 42.50.Gy, 03.67.Ac Quantum walks (QW) have become widely studied the- encoded into a matrix C which describes the connections oretically [1{3] and experimentally in a variety of dif- between the different modes of the system, as well as the ferent settings such as classical optics [4{7], photons in on-site terms. The CTQW has the generic Hamiltonian, waveguide arrays [8, 9] and trapped atoms [10, 11]. They ^ X y exhibit different behaviour than classical random walks HC = Cj;ka^ja^k + h.c.; (1) due to the interference of the quantum walker [12]. The j;k quantum walk paradigm has been used to demonstrate y wherea ^j; a^j are the bosonic creation and annihilation op- that they are capable of universal quantum computing erators respectively of the walker on the jth site of the [13, 14], including search algorithms [15] and more gen- graph and the evolution of the walk is given simply by eral quantum transport problems [16, 17]. -
Curriculum Vitae Prof. Dr. Christine Silberhorn
Curriculum Vitae Prof. Dr. Christine Silberhorn Name: Christine Silberhorn Born: 19 April 1974 Research Priorities: quantum optics, properties of light, quantum communication, optical components, quantum devices Christine Silberhorn is a physicist. Her research focus is experimental quantum optics. She studies light and its exceptional properties. Together with her research group she has demonstrated many characteristic quantum properties of light. Beyond that, she develops optical systems for applications in quantum technology. Her research contributes to the understanding of quantum theory and the development of new quantum devices. Academic and Professional Career since 2010 Full Professor of Applied Physics/Integrated Quantum Optics, Paderborn University, Germany 2009 - 2010 Head of an independent Max Planck Research Group, Integrated Quantum Optics, Max Planck Institute for the Science of Light, Erlangen, Germany 2008 Habilitation in Experimental Physics, University of Erlangen-Nuremberg, Germany 2005 - 2008 Head of an independent Max Planck Junior Research Group, Integrated Quantum Optics, Max Planck Institute for Quantum Optics, Garching/Munich, Germany 2005 Research Assistant, Max Planck Research Group, Institute of Optics, Information and Photonics, Erlangen, Germany 2003 - 2004 Post-doctoral Research Assistant at University of Oxford, Clarendon Laboratory, and Junior Research Fellow at Wolfson College, Oxford, UK 2003 Doctorate, Chair of Optics, University of Erlangen-Nuremberg, Germany Nationale Akademie der Wissenschaften -
Integrated Quantum Photonics
© Paderborn University: University: © Paderborn Modern technologies for quantum photonics 1 Integrated quantum photonics Besim Mazhiqi Benni Brecht Christine Silberhorn ICTP Winter College on Optics: Integrated Quantum Optics Quantum Photonics and Information Paderborn University 13/02/2020 Christof Harald Benjamin Eigner Herrmann Brecht © Paderborn University, Besim Mazhiqi Outline Underlying concepts Device toolbox Fabrication technology HOM-on-chip circuit Why integrated (quantum) photonics? University of Tokyo, Furusawa group University of Science and Technology of China, Hefei, Pan group History ▶ „Invention“ of Integrated Optics by S.E. Miller [1] ▶ Roadmap from conventional integrated optics to „Integrated Quantum Optics“ ? Quantum quantum photon source quantum Keep ideas, but adapt them to quantum optics! [1] S.E. Milller, Bell System Technical Journal, 48, 2059 (1969) Quantum optics “on chip” ▶ Common structure to all quantum experiments ▶ One objective of the Integrated Quantum Optics group: Integrate as many components as possible (onto a single platform?) Create Detect Photons Photons Manipulate Photons Integrated quantum photonics Photonic quantum simulator Alán Aspuru-Guzik and Philip Walther, Nature Physics 8, 285–291 (2012) Integrated quantum photonics Photonic quantum simulator Advantages: • Many spatial modes available / controllable • Interferometric stability of large optical system • Compact devices; miniaturaization • „Simple“ operation • High efficiency (?) Alán Aspuru-Guzik and Philip Walther, Nature Physics 8, -
Report on the Physics Department FAU Erlangen
Report on the Physics Department FAU Erlangen October 2013 www.physik.fau.de Contents Contents .............................................................. 1 Introduction ......................................................... 3 Structure and Evolution of the Department ... 3 Research Topics ................................................... 5 Astroparticle Physics ....................................... 6 Condensed Matter Physics .............................. 9 Biophysics ...................................................... 14 Optics ............................................................. 18 Light-Matter Interface ................................... 21 Theoretical Physics ........................................ 24 Physics didactics ............................................ 28 Teaching ............................................................ 29 Outreach ............................................................ 34 Statistics and Overview ..................................... 36 Faculty ............................................................... 41 Junior Research Groups ................................... 130 1 2 Introduction Structure and Evolution of the De- partment This report is designed to present the current status (in 2013) of the Department of Physics at The Department of Physics (the Department) the Friedrich-Alexander Universität Erlangen- currently consists of 16 chairs (four in theoretical Nürnberg (FAU), which is the second largest uni- and twelve in experimental physics) and several versity in -
Fabrication Limits of Waveguides in Nonlinear Crystals and Their Impact
New J. Phys. 21 (2019) 033038 https://doi.org/10.1088/1367-2630/aaff13 PAPER Fabrication limits of waveguides in nonlinear crystals and their OPEN ACCESS impact on quantum optics applications RECEIVED 25 September 2018 Matteo Santandrea , Michael Stefszky , Vahid Ansari and Christine Silberhorn REVISED 7 December 2018 Integrated Quantum Optics, Paderborn University, Warburgerstr. 100, D-33098, Paderborn, Germany ACCEPTED FOR PUBLICATION E-mail: [email protected] 16 January 2019 Keywords: integrated quantum optics, parametric downconversion, squeezing, fabrication imperfections, nonlinear optics, frequency PUBLISHED encoding 28 March 2019 Original content from this work may be used under Abstract the terms of the Creative Commons Attribution 3.0 Waveguides in nonlinear materials are a key component for photon pair sources and offer promising licence. solutions to interface quantum memories through frequency conversion. To bring these technologies Any further distribution of fi this work must maintain closer to every-day life, it is still necessary to guarantee a reliable and ef cient fabrication of these attribution to the devices. Therefore, a thorough understanding of the technological limitations of nonlinear author(s) and the title of the work, journal citation waveguiding devices is paramount. In this paper, we study the link between fabrication errors of and DOI. waveguides in nonlinear crystals and the final performance of such devices. In particular, we first derive a mathematical expression to qualitatively assess the technological limitations of any nonlinear waveguide. We apply this tool to study the impact of fabrication imperfections on the phasematching properties of different quantum processes realized in titanium-diffused lithium niobate waveguides. Finally, we analyse the effect of waveguide imperfections on quantum state generation and manipulation for few selected cases. -
Eps Quantum Electronics Prizes
EPS QUANTUM ELECTRONICS PRIZES EPS Quantum Electronics Prize in the category “Fundamental Aspects” Anne L’Huillier, Lund University, Sweden The 2019 prize for fundamental aspects of Quantum Electronics and Optics is awarded to Anne L’Huillier in recognition of her pioneering experimental and theoretical contributions to attosecond pulse trains using high harmonics, which form the basis of today’s successful field of attosecond science. Anne L’Huillier is a Swedish/French researcher in attosecond science. She was born in Paris in 1958, studied at the Ecole Normale Supérieure in mathematics and physics and defended her doctorat d’état ès Sciences Physiques de l’Université Paris VI, in 1986. She was then permanently employed as researcher at the Commissariat à l’Energie Atomique, in Saclay, France until 1995. She was postdoctoral researcher at Chalmers Institute of Technology, Gothenburg (1986), University of Southern Cal- ifornia (1988), and visiting scientist at the Lawrence Livermore National Laboratory (1993). In 1995, she moved to Lund University, Sweden and became full professor in 1997. She was elected to the Royal Swedish Academy of Sciences in 2004. Her research, which includes both theory and experiment, deals with the interaction between atoms and intense laser light, and in particular the generation of high-order harmonics of the laser light, which, in the time domain, consist of trains of attosecond pulses. Currently, her research group works on attosecond source development and optimization as well as on applications, for example, concerning the measurement of photoionization dynamics in atomic systems. 2 The European Physical Society is delighted to announce the 2019 winners of its senior prizes in Quantum Electronics and Optics. -
Table of Contents
Table of Contents Schedule-at-a-Glance . 2 FiO + LS Chairs’ Welcome Letters . 3 General Information . 5 Sponsoring Society Booths . 6 Stay Connected Conference Materials . 7 FiO + LS Conference App . 7 Plenary Session/Visionary Speakers Plenary Presentations . 8 Visionary Speakers . 9 Awards, Honors and Special Recognitions OSA 2017 Awards and Honors . 12 APS/DLS 2017 Awards and Honors . 14 OSA Foundation 2017 Prizes and Special Recognitions . 14 Science & Industry Showcase (Poster Sessions, E-Posters, Rapid-fire Oral Presentations, Exhibits) . 16 FiO 2017 Participating Companies . 17 Special Events . 18 FiO + LS Committee . 21 Explanation of Session Codes . 23 FiO + LS Agenda of Sessions . 23 FiO + LS Abstracts . 28 Key to Authors and Presiders . 85 Program updates and changes may be found on the Conference Program Update Sheet distributed in the attendee registration bags . Check the Conference App for regular updates . OSA and APS thank the following sponsors for their generous support of this meeting: FiO + LS 2017 • 17–21 September 2017 1 Conference Schedule-at-a-Glance Note: Dates and times are subject to change. Check the conference app for regular updates. All times reflect eastern time zone. Sunday Monday Tuesday Wednesday Thursday 17 September 18 September 19 September 20 September 21 September GENERAL Registration 15:00–18:00 07:00–18:00 07:00–17:30 07:00–17:30 07:30–11:30 Speaker Preparation Room 15:00–18:00 07:00–17:30 07:00–17:30 07:00–17:30 07:30–11:30 WORKinOPTICS .com Kiosks & E-Center 15:00–18:00 07:00–17:30 07:00–17:30 -
Viewpoint Sharing Entanglement Without Sending It
Physics 6, 132 (2013) Viewpoint Sharing Entanglement without Sending It Christine Silberhorn University of Paderborn, D-33098 Paderborn, Germany Published December 4, 2013 Three new experiments demonstrate how entanglement can be shared between distant parties without the need of an entangled carrier. Subject Areas: Quantum Information A Viewpoint on: Experimental Distribution of Entanglement with Separable Carriers A. Fedrizzi, M. Zuppardo, G. G. Gillett, M. A. Broome, M. P. Almeida, M. Paternostro, A. G. White, and T. Paterek Phys. Rev. Lett. 111, 2013 – Published December 4, 2013 Distributing Entanglement with Separable States Christian Peuntinger, Vanessa Chille, Ladislav Mišta, Jr., Natalia Korolkova, Michael Förtsch, Jan Korger, Christoph Marquardt, and Gerd Leuchs Phys. Rev. Lett. 111, 2013 – Published December 4, 2013 Experimental Entanglement Distribution by Separable States Christina E. Vollmer, Daniela Schulze, Tobias Eberle, Vitus Händchen, Jaromír Fiurášek, and Roman Schnabel Phys. Rev. Lett. 111, 2013 – Published December 4, 2013 To challenge the limited understanding of the then- tasks as quantum teleportation, efficient quantum com- young quantum theory, Einstein, Podolsky, and Rosen munication, fundamental tests of quantum physics, and constructed, in 1935, their EPR Gedankenexperiment, long-distance quantum cryptography. in which they introduced entangled states that exhibit The quantum correlations associated with entangle- strange correlations over macroscopic distances [1]. By ment are not the only type of correlations that can occur now we have learned that entangled states are an ele- in quantum systems. In order to give a rigorous def- ment of physical reality. They lie at the heart of quan- inition of the “entangled” correlations, separable states tum physics and can, in fact, be used as a powerful re- have been introduced as the converse of entanglement [5]. -
Dr. Peter P. Rohde, Beng (Hons I), Phd
Dr. Peter P. Rohde, BEng (Hons I), PhD Contact details E-mail (personal): [email protected] E-mail (secure): [email protected] E-mail (work): [email protected] Keybase: keybase.io/peter rohde Telegram: t.me/peter rohde Skype: peter rohde Homepage: www.peterrohde.org ORCID: orcid.org/0000-0002-5814-7289 arXiv: bit.ly/2UcYCdu LinkedIn: www.linkedin.com/in/peterrohde YouTube: www.youtube.com/user/prohde81/videos Google Scholar: bit.ly/1pCHT3K SoundCloud: soundcloud.com/peter-rohde Mission The biological evolution of the human race is reaching a plateau. The only mechanism for us to ad- statement vance further is via technology. The 20th century was that of the transistor, gifting us unprecedented progress as a species, on an exponential trajectory. However, that trajectory is rapidly approaching saturation. The 21st century will usher in entirely new technologies, far beyond just incremental de- velopments in our current ones. Quantum technology will be one of them, transforming the world as profoundly as the transistor did. My mission is to contribute to the realisation of this, propelling the human race into the future, benefiting all of humanity, blind to demographics and national borders. Together we will make the future — Carpe futurum. Ad astra per alas fideles. Scientia potentia est. Executive ARC Future Fellow – AU$1,024,302 (2016-2020) summary Lead author & editor of book “The Quantum Internet – A New Frontier” (accepted for publica- tion by Cambridge University Press, 2019) 49 publications in international peer-reviewed