Some Influences of Underground Coal Gasification on the Environment
Total Page:16
File Type:pdf, Size:1020Kb
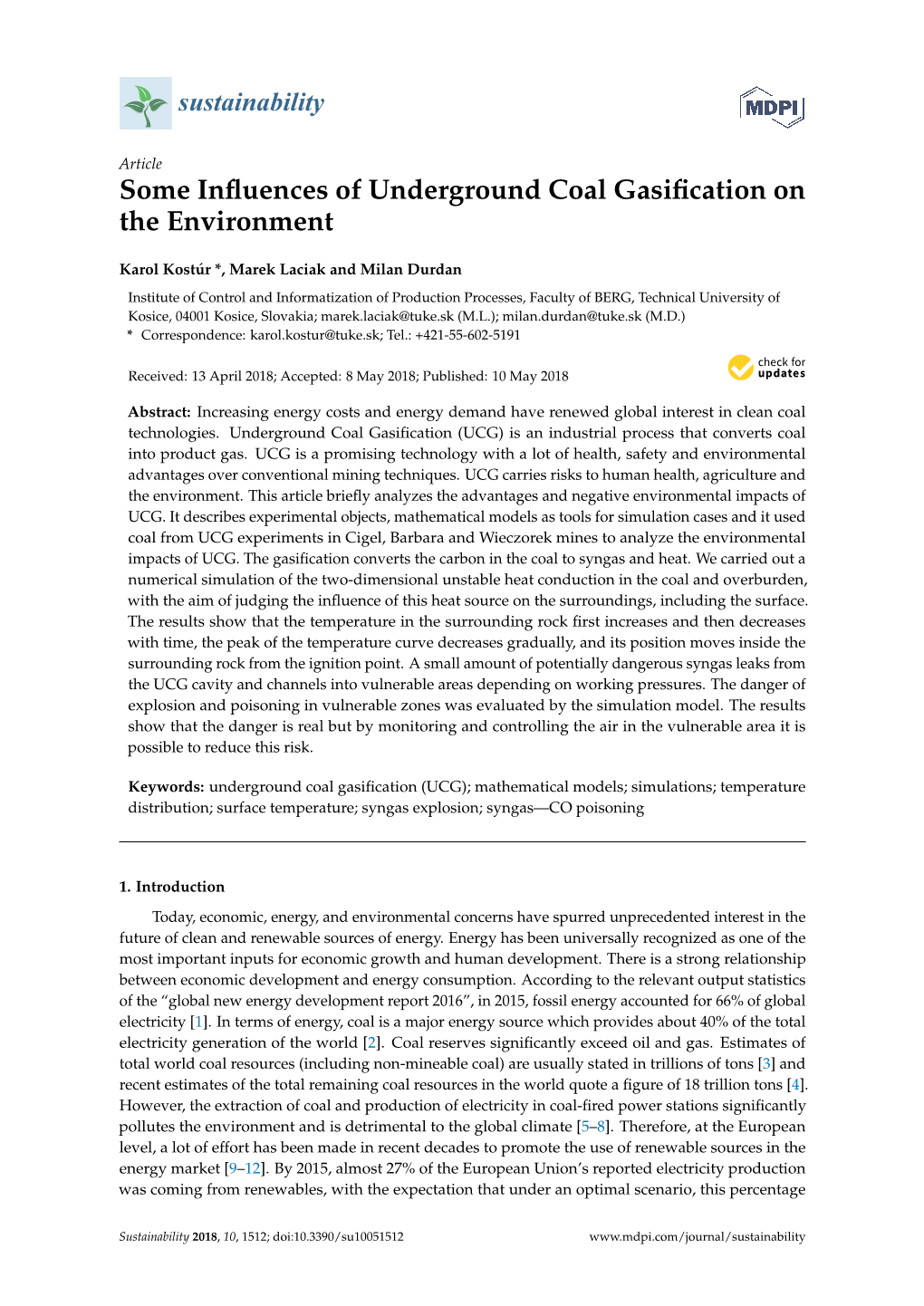
Load more
Recommended publications
-
Thesis a Modeling Tool for Household Biogas Burner
THESIS A MODELING TOOL FOR HOUSEHOLD BIOGAS BURNER FLAME PORT DESIGN Submitted by Thomas J. Decker Department of Mechanical Engineering In partial fulfillment of the requirements For the Degree of Master of Science Colorado State University Fort Collins, Colorado Summer 2017 Master’s Committee: Advisor: Thomas Bradley Jason Prapas Sybil Sharvelle Copyright by Thomas J Decker 2017 All Rights Reserved ABSTRACT A MODELING TOOL FOR HOUSEHOLD BIOGAS BURNER FLAME PORT DESIGN Anaerobic digestion is a well-known and potentially beneficial process for rural communities in emerging markets, providing the opportunity to generate usable gaseous fuel from agricultural waste. With recent developments in low-cost digestion technology, communities across the world are gaining affordable access to the benefits of anaerobic digestion derived biogas. For example, biogas can displace conventional cooking fuels such as biomass (wood, charcoal, dung) and Liquefied Petroleum Gas (LPG), effectively reducing harmful emissions and fuel cost respectively. To support the ongoing scaling effort of biogas in rural communities, this study has developed and tested a design tool aimed at optimizing flame port geometry for household biogas- fired burners. The tool consists of a multi-component simulation that incorporates three- dimensional CAD designs with simulated chemical kinetics and computational fluid dynamics. An array of circular and rectangular port designs was developed for a widely available biogas stove (called the Lotus) as part of this study. These port designs were created through guidance from previous studies found in the literature. The three highest performing designs identified by the tool were manufactured and tested experimentally to validate tool output and to compare against the original port geometry. -
Biogas Stove Design: a Short Course
Biogas Stove Design A short course Dr David Fulford Kingdom Bioenergy Ltd Originally written August 1996 Used in MSc Course on “Renewable Energy and the Environment” at the University of Reading, UK for an Advanced Biomass Module. Design Equations for a Gas Burner The force which drives the gas and air into the burner is the pressure of gas in the pipeline. The key equation that relates gas pressure to flow is Bernoulli’s theorem (assuming incompressible flow): p v2 + +z = constant ρ 2g where: p is the gas pressure (N m –2), ρ is the gas density (kg m –3), v is the gas velocity (m s –1), g is the acceleration due to gravity (9.81 m s –2) and z is head (m). For a gas, head ( z) can be ignored. Bernoulli’s theorem essentially states that for an ideal gas flow, the potential energy due to the pressure, plus the kinetic energy due to the velocity of the flow is constant In practice, with gas flowing through a pipe, Bernoulli’s theorem must be modified. An extra term must be added to allow for energy loss due to friction in the pipe: p v2 + −f ()losses = constant . ρ 2g Using compressible flow theory, flow though a nozzle of area A is: γ p γ ()γ − γ m = C ρ A 2 0 r2 (1− r 1 ) & d 0 γ − ρ 1 0 ρ where p0 and 0 are the pressure and density of the gas upstream of the = nozzle and r p1 p0 , where p1 is the pressure downstream of the nozzle. -
Storing Syngas Lowers the Carbon Price for Profitable Coal Gasification
Carnegie Mellon Electricity Industry Center Working Paper CEIC-07-10 www.cmu.edu/electricity Storing syngas lowers the carbon price for profitable coal gasification ADAM NEWCOMER AND JAY APT Carnegie Mellon Electricity Industry Center, Tepper School of Business, and Department of Engineering and Public Policy, 254 Posner Hall, Carnegie Mellon University, Pittsburgh, Pennsylvania 15213 Integrated gasification combined cycle (IGCC) electric power generation systems with carbon capture and sequestration have desirable environmental qualities, but are not profitable when the carbon dioxide price is less than approximately $50 per metric ton. We examine whether an IGCC facility that operates its gasifier continuously but stores the syngas and produces electricity only when daily prices are high may be profitable at significantly lower CO2 prices. Using a probabilistic analysis, we have calculated the plant-level return on investment (ROI) and the value of syngas storage for IGCC facilities located in the US Midwest using a range of storage configurations. Adding a second turbine to use the stored syngas to generate electricity at peak hours and implementing 12 hours of above ground high pressure syngas storage significantly increases the ROI and net present value. Storage lowers the carbon price at which IGCC enters the US generation mix by approximately 25%. 1 Carnegie Mellon Electricity Industry Center Working Paper CEIC-07-10 www.cmu.edu/electricity Introduction Producing electricity from coal-derived synthesis gas (syngas) in an integrated gasification combined cycle (IGCC) facility can improve criteria pollutant performance over other coal-fueled technologies such as pulverized coal (PC) facilities [1-5] and can be implemented with carbon capture and sequestration. -
A Wood-Gas Stove for Developing Countries T
A WOOD-GAS STOVE FOR DEVELOPING COUNTRIES T. B. Reed and Ronal Larson The Biomass Energy Foundation, Golden, CO., USA ABSTRACT Through the millennia wood stoves for cooking have been notoriously inefficient and slow. Electricity, gas or liquid fuels are preferred for cooking - when they can be obtained. In the last few decades a number of improvements have been made in woodstoves, but still the improved wood stoves are difficult to control and manufacture and are often not accepted by the cook. Gasification of wood (or other biomass) offers the possibility of cleaner, better controlled gas cooking for developing countries. In this paper we describe a wood-gas stove based on a new, simplified wood gasifier. It offers the advantages of “cooking with gas” while using a wide variety of biomass fuels. Gas for the stove is generated using the “inverted downdraft gasifier” principle. In one mode of operation it also produces 20-25% charcoal (dry basis). The stove operates using natural convection only. It achieves clean “blue flame” combustion using an “air wick” that optimizes draft and stabilizes the flame position. The emissions from the close coupled gasifier-burner are quite low and the stove can be operated indoors. Keywords: inverted downdraft gasifier, domestic cooking stove, natural draft *Presented at the “Developments in Thermochemical Biomass Conversion” Conference, Banff, Canada, 20-24 May, 1996. 1 A WOOD-GAS STOVE FOR DEVELOPING COUNTRIES T. B. Reed and Ronal Larson The Biomass Energy Foundation, Golden, CO., USA 1. Introduction - 1.1. The Problem Since the beginning of civilization wood and biomass have been used for cooking. -
Combustion of Low-Calorific Waste Biomass Syngas
Flow Turbulence Combust (2013) 91:749–772 DOI 10.1007/s10494-013-9473-9 Combustion of Low-Calorific Waste Biomass Syngas Kamil Kwiatkowski · Marek Dudynski´ · Konrad Bajer Received: 7 March 2012 / Accepted: 31 May 2013 / Published online: 19 June 2013 © The Author(s) 2013. This article is published with open access at Springerlink.com Abstract The industrial combustion chamber designed for burning low-calorific syngas from gasification of waste biomass is presented. For two different gases derived from gasification of waste wood chips and turkey feathers the non-premixed turbulent combustion in the chamber is simulated. It follows from our computations that for stable process the initial temperature of these fuels must be at least 800 K, with comparable influx of air and fuel. The numerical simulations reveal existence of the characteristic frequency of the process which is later observed in high-speed cam- era recordings from the industrial gasification plant where the combustion chamber operates. The analysis of NO formation and emission shows a difference between wood-derived syngas combustion, where thermal path is prominent, and feathers- derived fuel. In the latter case thermal, prompt and N2O paths of nitric oxides formation are marginal and the dominant source of NO is fuel-bound nitrogen. Keywords Biomass · Waste · Gasification · Syngas · Turbulent combustion K. Kwiatkowski (B) · M. Dudynski´ · K. Bajer Faculty of Physics, University of Warsaw, Pasteura 7, 02-093 Warsaw, Poland e-mail: [email protected] K. Kwiatkowski · K. Bajer Interdisciplinary Centre for Mathematical and Computational Modelling, University of Warsaw, Pawinskiego´ 5a, 02-106 Warsaw, Poland M. Dudynski´ Modern Technologies and Filtration Sp. -
The Future of Gasification
STRATEGIC ANALYSIS The Future of Gasification By DeLome Fair coal gasification projects in the U.S. then slowed significantly, President and Chief Executive Officer, with the exception of a few that were far enough along in Synthesis Energy Systems, Inc. development to avoid being cancelled. However, during this time period and on into the early 2010s, China continued to build a large number of coal-to-chemicals projects, beginning first with ammonia, and then moving on to methanol, olefins, asification technology has experienced periods of both and a variety of other products. China’s use of coal gasification high and low growth, driven by energy and chemical technology today is by far the largest of any country. China markets and geopolitical forces, since introduced into G rapidly grew its use of coal gasification technology to feed its commercial-scale operation several decades ago. The first industrialization-driven demand for chemicals. However, as large-scale commercial application of coal gasification was China’s GDP growth has slowed, the world’s largest and most in South Africa in 1955 for the production of coal-to-liquids. consistent market for coal gasification technology has begun During the 1970s development of coal gasification was pro- to slow new builds. pelled in the U.S. by the energy crisis, which created a political climate for the country to be less reliant on foreign oil by converting domestic coal into alternative energy options. Further growth of commercial-scale coal gasification began in “Market forces in high-growth the early 1980s in the U.S., Europe, Japan, and China in the coal-to-chemicals market. -
CAST IRON STOVE and DIRECT-VENT (FREESTANDING FIREPLACE HEATER) BURNER SYSTEM OWNER’S OPERATION and INSTALLATION MANUAL for More Information, Visit
CAST IRON STOVE AND DIRECT-VENT (FREESTANDING FIREPLACE HEATER) BURNER SYSTEM OWNER’S OPERATION AND INSTALLATION MANUAL For more information, visit www.desatech.com SCIVFC/PSCIVFC VCIS/PVCIS VH series Stove SERIES STOVE Series Stove "VICTOR HEARTH™" "AMITY™" "OXFORD™" NATURAL GAS BURNER SYSTEM MODEL SDVBND PROPANE/LP GAS BURNER SYSTEM MODEL SDVBPD REMOTE READY IMPORTANT: This direct-vent burner system must be installed into approved cast iron stove bodies, models SCIVFC/PSCIVFC/VCIS/PVCIS/VH series ONLY. WARNING: If the information in this manual is not followed WARNING: Improper instal- exactly, a fire or explosion may result causing property lation, adjustment, alteration, damage, personal injury, or loss of life. service, or maintenance can cause injury or property dam- FOR YOUR SAFETY age. Refer to this manual for Do not store or use gasoline or other flammable vapors and correct installation and op- liquids in the vicinity of this or any other appliance. erational procedures. For as- sistance or additional infor- mation consult a qualified in- FOR YOUR SAFETY staller, service agency, or the WHAT TO DO IF YOU SMELL GAS gas supplier. • Do not try to light any appliance. • Do not touch any electrical switch Installation and service must • Do not use any phone in your building. be performed by a qualified • Immediately call your gas supplier from a neighbor’s installer, service agency, or phone. Follow the gas supplier’s instructions. the gas supplier. • If you cannot reach your gas supplier, call the fire department. This appliance may be installed in an aftermarket*, permanently located, manufactured (mo- bile) home, where not prohibited by state or local codes. -
Next Generation Coal Gasification Technology
Next generation coal gasification technology Ian Barnes CCC/187 ISBN 978-92-9029-507-5 September 2011 copyright © IEA Clean Coal Centre Abstract Worldwide, a small number of integrated gasification combined cycle power plants (IGCC), based on high-efficiency coal gasification technologies, are operated commercially or semi-commercially, a few more are under construction, and a number of demonstration projects, some including carbon capture and sequestration (CCS), are at an advanced stage of planning. Various coal gasification technologies are embodied in these plants including different coal feed systems (dry or slurry), fireproof interiors walls (fire brick or water-cooled tubes), oxidants (oxygen or air), and other factors. Many of these designs are now several decades old but new cycles and systems are emerging to further improve the efficiency of the coal gasification process. This report draws upon the published literature and commentary from experts in industry and academia working in the coal gasification sector to present and summarise recent developments. Acknowledgements The author is grateful for useful discussions and advice freely given by industry and academic professionals. In particular, the contributions of the following are acknowledged: Dr Kourosh E Zanganeh CANMET Dr Manabu Hirata NEDO Mr John Davison IEAGHG Dr John Griffiths Jacobs Ms Jenny Tennant NETL Mr David Butler Canadian Clean Power Coalition Mr Ronald L Schoff EPRI Acronyms and abbreviations AC air compressor ADT acid gas dewpoint temperature AHAT humid air -
Ground-Water Contamination at an Inactive Coal and Oil Gasification Plant Site, Gas Works Park, Seattle
GROUND-WATER CONTAMINATION AT AN INACTIVE COAL AND OIL GASIFICATION PLANT SITE, GAS WORKS PARK, SEATTLE, WASHINGTON By G.L. Turney and D.F. Goer1itz U.S. GEOLOGICAL SURVEY Water-Resources Investigations Report 88-4224 Prepared in cooperation with the CITY OF SEATTLE, DEPARTMENT OF PARKS AND RECREATION Tacoma, Washington 1989 DEPARTMENT OF THE INTERIOR MANUEL LUJAN, JR., Secretary U.S. GEOLOGICAL SURVEY Dallas L. Peck, Director For additional information Copies of this report may be write to: purchased from: District Chief U.S. Geological Survey U.S. Geological Survey Books and Open-File Reports Section 1201 Pacific Avenue, Suite 600 Box 25425, Fed. Center, Bldg. 810 Tacoma, Washington 98402-4384 Denver, Colorado 80225 CONTENTS Page Abstract------------------------------------------------------ 1 Introduction-------------------------------------------------- 2 Background------------------------------------------------ 3 Purpose and scope----------------------------------------- 5 Data collection and laboratory procedures--------------------- 6 Well installation----------------------------------------- 6 Sample collection----------------------------------------- 6 Laboratory analyses--------------------------------------- 8 Hydrogeologic setting----------------------------------------- 11 Contaminant concentrations and mechanisms affecting their distribution------------------------------------------------- 17 Organic compounds in ground water and soils--------------- 17 Volatile organic compounds in soil gas-------------------- 23 Weathering -
Development of Oxy-Fuel IGCC System
2nd Oxyfuel Combustion Conference Development of oxy-fuel IGCC system Jun Inumaru, Yuso Oki*, Saburo Hara, Makoto Kobayashi, Kenji Tan-no, Shiro Kajitani CRIEPI,2-6-1Nagasaka,Yokosuka,240-0196,Japan Keywords:Oxy-fuel; Coal gasification; IGCC; CO2 recirculation; CCS Abstract CO2 emission control is significant issue as a countermeasure for a global warming problem. Utility companies are required to reduce CO2 emission from thermal power stations and make various efforts to improve thermal efficiency and to utilize carbon neutral fuels such as biomass fuels. CCS (CO2 capture and storage) technology is regarded as one method to reduce CO2 emission, but CCS required great decrease of thermal efficiency. As amount of fossil fuel on the globe is so restricted, it is important to keep high thermal efficiency as high as possible, in order to utilize valuable fossil fuel effectively. This project plans to develop innovative gasification technology with CO2 capture, which can keep thermal efficiency as high as state of the art IGCC plant, namely more than 40% (HHV). This is to gasify coal with mixed gas of O2 and recycled CO2 flue gas, just like oxy-fuel combustion system. We expect following two merits. First merit is to simplify the system. As the CO2 concentration in exhaust gas is almost 100%, this system doesn’t require CO2 separation unit. So no steam is required to bleed from steam cycle in order to maintain absorber for CO2, therefore thermal efficiency is kept high even after capturing CO2. We expect another merit in this system. Generally speaking, CO2 gas works as gasifying agent for coal, so high CO2 concentration improves gasification performance of gasifier. -
(SNG) Through Underground Coal Gasification Process
energies Article Large-scale Experimental Investigations to Evaluate the Feasibility of Producing Methane-Rich Gas (SNG) through Underground Coal Gasification Process. Effect of Coal Rank and Gasification Pressure Krzysztof Kapusta 1,* , Marian Wiatowski 1 , Krzysztof Sta ´nczyk 1, Renato Zagoršˇcak 2 and Hywel Rhys Thomas 2 1 Główny Instytut Górnictwa (Central Mining Institute), 40-166 Katowice, Poland; [email protected] (M.W.); [email protected] (K.S.) 2 Geoenvironmental Research Centre (GRC), School of Engineering, Cardiff University, Cardiff CF24 3AA, UK; ZagorscakR@cardiff.ac.uk (R.Z.); thomashr@cardiff.ac.uk (H.R.T.) * Correspondence: [email protected]; Tel.: +48-32-3246535; Fax: +48-32-3246522 Received: 10 February 2020; Accepted: 10 March 2020; Published: 13 March 2020 Abstract: An experimental campaign on the methane-oriented underground coal gasification (UCG) process was carried out in a large-scale laboratory installation. Two different types of coal were used for the oxygen/steam blown experiments, i.e., “Six Feet” semi-anthracite (Wales) and “Wesoła” hard coal (Poland). Four multi-day gasification tests (96 h continuous processes) were conducted in artificially created coal seams under two distinct pressure regimes-20 and 40 bar. The experiments demonstrated that the methane yields are significantly dependent on both the properties of coal (coal rank) and the pressure regime. The average CH4 concentration for “Six Feet” semi-anthracite was 15.8%vol. at 20 bar and 19.1%vol. at 40 bar. During the gasification of “Wesoła” coal, the methane concentrations were 10.9%vol. and 14.8%vol. at 20 and 40 bar, respectively. The “Six Feet” coal gasification was characterized by much higher energy efficiency than gasification of the “Wesoła” coal and for both tested coals, the efficiency increased with gasification pressure. -
Micro-Gasification: Cooking with Gas from Dry Biomass
Micro-gasification: cooking with gas from dry biomass Published by: Micro-gasification: cooking with gas from dry biomass An introduction to concepts and applications of wood-gas burning technologies for cooking 2nd revised edition IV Photo 0.1 Typical fl ame pattern in a wood-gas burner, in this case a simple tin-can CONTENTS V Contents Figures & Tables........................................................................................................................................ VI Acknowledgements .............................................................................................................................VIII Abbreviations .............................................................................................................................................. X Executive summary ...........................................................................................................................XIII 1.0 Introduction ......................................................................................................................................1 1.1 Moving away from solid biomass? .................................................................................................. 2 1.2 Developing cleaner cookstoves for solid biomass? ................................................................... 5 1.3 Solid biomass fuels can be used cleanly in gasifier cookstoves! ...................................... 6 1.4 Challenges go beyond just stoves and fuels ...............................................................................