Using MIP for Strategic Life-Of-Mine Planning of the Lead/Zinc Stream at Mount Isa Mines
Total Page:16
File Type:pdf, Size:1020Kb
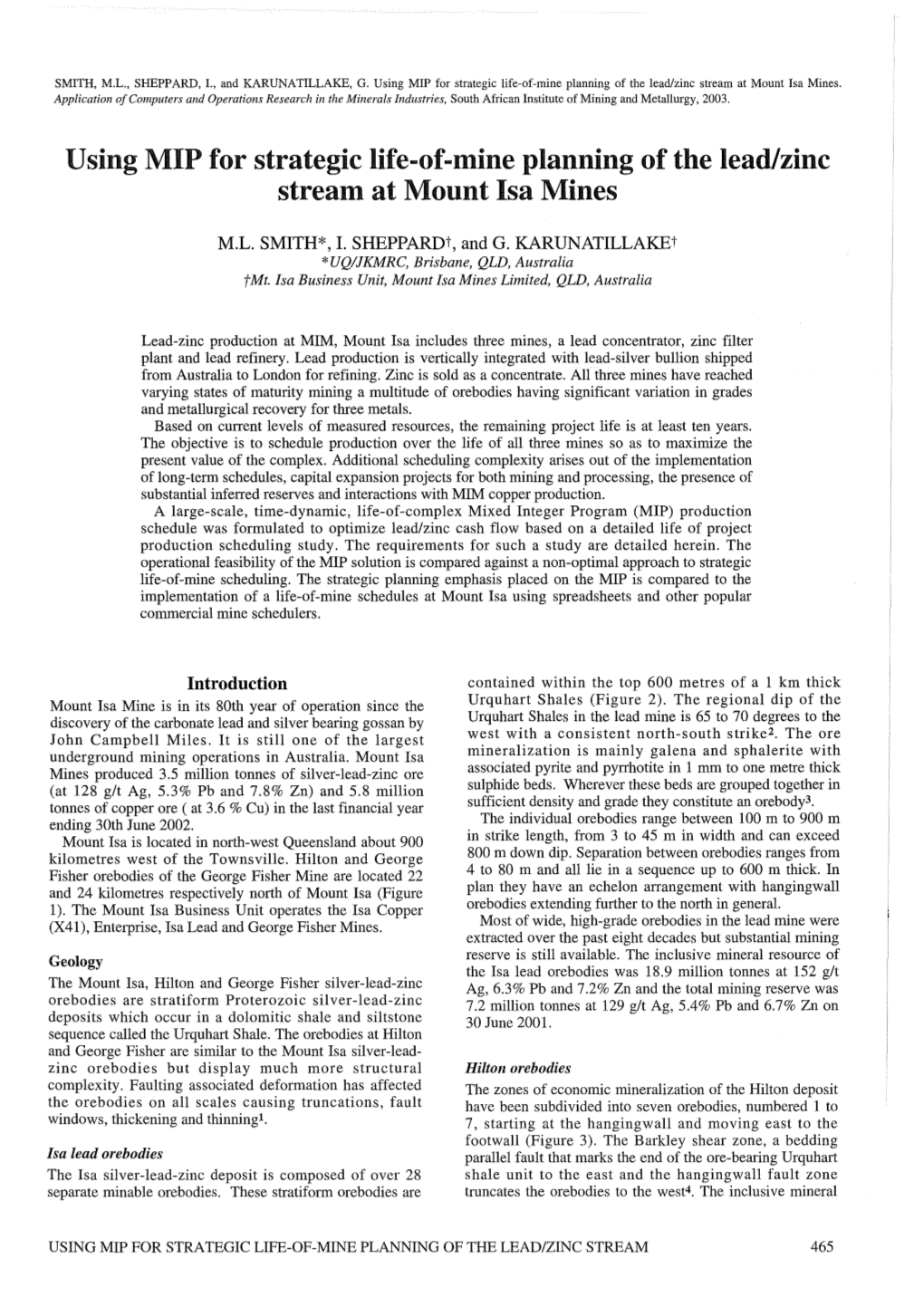
Load more
Recommended publications
-
Metalliferous Level 1 Mine Emergency Exercise 2016 George Fisher Mine
Metalliferous level 1 mine emergency exercise 2016 George Fisher Mine CS6325 12/16 Cover photo: George Fisher Mine, L72 shaft © State of Queensland, 2016 The Queensland Government supports and encourages the dissemination and exchange of its information. The copyright in this publication is licensed under a Creative Commons Attribution 3.0 Australia (CC BY) licence. Under this licence you are free, without having to seek our permission, to use this publication in accordance with the licence terms. You must keep intact the copyright notice and attribute the State of Queensland as the source of the publication. Note: Some content in this publication may have different licence terms as indicated. For more information on this licence, visit http://creativecommons.org/licenses/by/3.0/au/deed.en The information contained herein is subject to change without notice. The Queensland Government shall not be liable for technical or other errors or omissions contained herein. The reader/user accepts all risks and responsibility for losses, damages, costs and other consequences resulting directly or indirectly from using this information. Contents Preface ................................................................................................................................................... ii Summary ............................................................................................................................................... iii Objectives ............................................................................................................................................ -
Proceedings of the International Workshop on Rock Mass Classification in Underground Mining
IC 9498 INFORMATION CIRCULAR/2007 Proceedings of the International Workshop on Rock Mass Classification in Underground Mining Department of Health and Human Services Centers for Disease Control and Prevention National Institute for Occupational Safety and Health Information Circular 9498 Proceedings of the International Workshop on Rock Mass Classification in Underground Mining Edited by Christopher Mark, Ph.D., P.E., Rimas Pakalnis, P.Eng., and Robert J. Tuchman DEPARTMENT OF HEALTH AND HUMAN SERVICES Centers for Disease Control and Prevention National Institute for Occupational Safety and Health Pittsburgh Research Laboratory Pittsburgh, PA May 2007 This document is in the public domain and may be freely copied or reprinted. DISCLAIMER Mention of any company or product does not constitute endorsement by the National Institute for Occupational Safety and Health (NIOSH). In addition, citations to Web sites external to NIOSH do not constitute NIOSH endorsement of the sponsoring organizations or their programs or products. Furthermore, NIOSH is not responsible for the content of these Web sites. The views expressed by non-NIOSH authors in these proceedings are not necessarily those of NIOSH. ORDERING INFORMATION To receive documents or other information about occupational safety and health topics, contact NIOSH at NIOSH—Publications Dissemination 4676 Columbia Parkway Cincinnati, OH 45226–1998 Telephone: 1–800–35–NIOSH (1–800–356–4674) Fax: 513–533–8573 e-mail: [email protected] or visit the NIOSH Web site at www.cdc.gov/niosh DHHS (NIOSH) Publication No. 2007–128 May 2007 SAFER • HEALTHIER • PEOPLE™ CONTENTS Page Abstract .........................................................................................................................................................................1 Rock mass characterization for excavations in mining and civil engineering, by N. -
Glencore 2020 Corporate Profile Australia
2020 CORPORATE PROFILE AUSTRALIA 18,720 employees and Australia’s contractors in largest Australia producer of coal to provide reliable power in Asia Cover photo: Workers in full personal protective gear at Glencore’s George Fisher Mine in north-west Queensland One of Australia’s A leading largest mining producers of technology copper, cobalt, business nickel and zinc This page: Planning tasks at Glencore’s Mount Isa Mines complex, north-west Queensland About Glencore We are one of the world’s largest natural resources companies. We own and operate a diverse mix of assets all over the world, and we’re engaged at every stage of the commodity supply chain. Global operations 160,000 Employees and contractors Diversifi ed by commodity, 60 geography Commodities across a range of metals, minerals and and activity energy sectors 3,000 Employees in marketing 1,200 Vessels on the ocean at • Fully integrated from mine any one time to customer • Presence in over 35 countries 7,000+ across 150 operating sites Long-term relationships with • Producing and marketing about suppliers and customers 60 commodities • Diversifi ed across multiple suppliers and customers www.glencore.com 2 Glencore 2020 Corporate Profi le Australia Our business model covers Metals & Minerals and Energy, which are supported by our extensive global Metals & Energy Marketing marketing network. Minerals The right Well-capitalised, commodity mix low-cost, high- for changing return assets needs • Future demand patterns • Since 2009, over US$45 billion for mature economies are has been -
Source of Sulphur and the Alteration Footprint of the George Fisher Zn-Pb-Ag Massive Sulphide Deposit, Australia
Source of sulphur and the alteration footprint of the George Fisher Zn-Pb-Ag massive sulphide deposit, Australia Dissertation zur Erlangung des Grades eines Doktors der Naturwissenschaften (doctor rerum naturalium) am Fachbereich Geowissenschaften der Freien Universität Berlin vorgelegt von: Philip Rieger Berlin, October 2020 First reviewer (Erstgutachterin): Prof. Dr. Sarah A. Gleeson Department of Earth Sciences, Freie Universität Berlin Inorganic and Isotope Geochemistry, GFZ German Research Centre of Geosciences Second reviewer (Zweitgutachter): Prof. Dr. Stephen Roberts School of Ocean and Earth Science, National Oceanography Centre, University of Southampton Doctoral Committee (Promotionsausschuss): Prof. Dr. Esther M. Schwarzenbach (Vorsitz) Department of Earth Sciences, Freie Universität Berlin Prof. Dr. Timm John Department of Earth Sciences, Freie Universität Berlin Prof. Dr. Sarah A. Gleeson Department of Earth Sciences, Freie Universität Berlin Inorganic and Isotope Geochemistry, GFZ German Research Centre of Geosciences Prof. Dr. Stephen Roberts School of Ocean and Earth Science, National Oceanography Centre, University of Southampton Dr. Joseph M. Magnall Inorganic and Isotope Geochemistry, GFZ German Research Centre of Geosciences Dr. J. Elis Hoffmann Department of Earth Sciences, Freie Universität Berlin Day of defense (Disputationsdatum): 26th of January 2021 Eidesstattliche Erklärung Ich versichere hiermit an Eides Statt, dass diese Arbeit von niemand anderem als meiner Person verfasst worden ist. Alle verwendeten Hilfsmittel wie Berichte, Bücher, Internetseiten oder ähnliches sind im Literaturverzeichnis angegeben, Zitate aus fremden Arbeiten sind als solche kenntlich gemacht. Die Arbeit wurde bisher in gleicher oder ähnlicher Form keiner anderen Prüfungskommission vorgelegt. Die Teile der Arbeit die schon veröffentlicht oder eingereicht wurden, sind im Vorwort (“Preface”) kenntlich gemacht. Weiterhin ist im Vorwort (“Preface”) dargelegt, zu welchem Teil der Arbeit andere Wissenschaftler beigetragen haben. -
Attachment I
ATTACHMENT I OVERVIEW OF VALUE-ADDING TO F QUEENSLAND MINERALS APRIL 1999 I.— OVERVIEW OF VALUE ADDING TO QUEENSLAND MINERALS Prepared by Project Development & Facilitation Division Department of State Development In Conjunction with the Department of Mines and Energy April 1999 — — LW. I z.L...J’2 TJZU TABLE OF CONTENTS ALUMINIUM 1 MA CN1l’CTTTM 8 COPPER 8 NICKEL 8 LEAD 8 ZINC 8 SILVER 8 COAL 8 ENERGY - 9 ENERGY - OIL CHAT r 10 ENERGY - PETROLEUM OIT 11 114 MINERAL SANDS - TITANIP 12 GOLD 13 LIMESTnNTI’ 14 PHOSPHATE ROC~ 15 REFERENCES 16 ALUMINIUM Current Status Mining Extent of Processing Manufacturing Global Outlook Aluminium: QAL Gladstone: Boyne Island Aluminium Smelter (Boyne Smelters Source: ABARE 1999 Comalco —30.3% Limited) (Gladstone): • World Bauxite Production Alumina Production Alcan — 21.4% Tolling operation with Comalco having approx 55% PechineyResources — 20% shareholding, rest being Japanese interests — 1997 - 125,863 kt 1997 - 46,739 kt Kaiser Australia — 28.3% 2003 - 140,000 kt 2004 - 55,215 kt Sumitomo, Marubeni, SLM, Kobe, YKK, Ryowa • World’slargest alumina refinery with a capacity of • Capacity 490,000 tpa • Primary Aluminium 3.65 Mtpa. • 3potlines Production • 10% of world’s alumina from bauxite mined at • Largest in Australia 1997 - 21,803 kt Weipa. • 4~ largest in world 2004 - 26,353 kt • Employs appiox 1200 Proposed Comalco Alumina Refinery under Manufacturing: Australia: evaluation by Comalco • Aichitectumi Al pmduct manufacturu(eg. Al doors, • Bauxite Production Bauxite Exports windows framesetc.) hadaturnoverof$516M. inQld 1997 - 43,000 kt 1997 - 4737 kt in1996 andemployment ofapprox. 3900. 2004 - 55,000 kt 2004-6183kt • Alumina Production Alumina Exports Vertical Integration 1997 - 13,252 kt 1997 - 11,011 kt • QId has the only fully integratedAluminium - 2004 - 13,126 kt 2004 16,460 kt industry in Aust with bauxite mined at Weipa, an • Primary Aluminium Primary Aluminium alumina refinery at Gladstone and an aluminium Production Exports smelter at Boyne Island near Gladstone. -
The Mineral Industry of Australia in 2002
THE MINERAL INDUSTRY OF AUSTRALIA By Travis Q. Lyday Australia continued its position as one of the world’s leading Government Policies and Programs minerals-producing nations in 2002, and this position should hold well into the future owing to the world’s largest economic Australia is governed at the national level by the demonstrated resources (EDRs) (mineral resources for which Commonwealth Parliament and at the State and Territory levels profitable extraction or production is possible at current prices) by governments whose jurisdiction is restricted to that State of lead, nickel, mineral sands, tantalum, uranium, and zinc. or Territory. The powers of the Commonwealth Government EDRs are approximately equal to reserves (U.S. Bureau of are defined in the Australian Constitution, and any power Mines and U.S. Geological Survey 1980). Additionally, its level not defined is given to or is the responsibility of the State or of EDR is within the top 6 worldwide for 11 additional mineral Territory, which is similar to the U.S. Constitution. Thus, all commodities—bauxite, black coal, brown coal, cobalt, copper, matters that relate to mineral resources and their production gem and near-gem diamond, gold, iron ore, lithium, manganese are State and Territory issues. Except for the Australian ore, and rare-earth oxides. Australia’s gross domestic product Capital Territory (that is, the capital city of Canberra and (GDP) grew at a rate of 3.6% in 2002 at constant prices and environs), all Australian States and Territories have identified increased to about $558.9 billion from the 2001 figure of $531 mineral resources and established mineral industries. -
2019 Corporate Profile Australia
2019 CORPORATE PROFILE AUSTRALIA One of the 18,000 Australia’s largest buyers employees and largest coal of grain and contractors in producer oilseeds from Australia Australian One of growers Australia’s largest producers of copper, zinc, nickel and cobalt Glencore’s Mount Isa Mines operation About Glencore We are one of the world’s largest natural resources companies. Our business covers Metals and We own and operate a diverse mix of mining, metals processing Minerals, Energy and Agriculture, and agricultural assets all over the world, and we’re engaged at which are supported by our extensive Metals and Energy Agriculture every stage in the commodity supply chain. global marketing network. minerals Global operations 158,000 Uniquely Employees and contractors The right diversifi ed by Well-capitalised, commodity mix commodity, low-cost, high- 90 for changing Commodities across three geography and return assets needs business segments activity 3,000 Employees in marketing 1,200 Vessels on the ocean at any one time • Fully integrated from mine • Future demand patterns for • Since 2009, over US$40 billion to customer maturing economies are likely has been invested in our global to favour mid-and late-cycle industrial assets • Presence in 50 countries across commodities 7,000+ 150 operating sites • Low-cost, long-life assets in many of Long-term relationships with • Major producer of later cycle the world’s premier mining districts suppliers and customers • Producing and marketing more commodities including the support sustainable long-term -
2019 Corporate Profile Australia
2019 CORPORATE PROFILE AUSTRALIA One of the 18,000 Australia’s largest buyers employees and largest coal of grain and contractors in producer oilseeds from Australia Australian One of growers Australia’s largest producers of copper, zinc, nickel and cobalt Glencore’s Mount Isa Mines operation About Glencore We are one of the world’s largest natural resources companies. Our business covers Metals and We own and operate a diverse mix of mining, metals processing Minerals, Energy and Agriculture, and agricultural assets all over the world, and we’re engaged at which are supported by our extensive Metals and Energy Agriculture every stage in the commodity supply chain. global marketing network. minerals Global operations 158,000 Uniquely Employees and contractors The right diversifi ed by Well-capitalised, commodity mix commodity, low-cost, high- 90 for changing Commodities across three geography and return assets needs business segments activity 3,000 Employees in marketing 1,200 Vessels on the ocean at any one time • Fully integrated from mine • Future demand patterns for • Since 2009, over US$40 billion to customer maturing economies are likely has been invested in our global to favour mid-and late-cycle industrial assets • Presence in 50 countries across commodities 7,000+ 150 operating sites • Low-cost, long-life assets in many of Long-term relationships with • Major producer of later cycle the world’s premier mining districts suppliers and customers • Producing and marketing more commodities including the support sustainable long-term -
Queensland Mines Inspectorate Annual Performance Report 2010–11 CS0864 09/11
Employment, Development Economic Innovation and Department of Commissioner for Mine Safety and Health Queensland Mines Inspectorate Annual Performance Report 2010–11 CS0864 09/11 © The State of Queensland, Department of Employment, Economic Development and Innovation, 2011. Except as permitted by the Copyright Act 1968, no part of the work may in any form or by any electronic, mechanical, photocopying, recording, or any other means be reproduced, stored in a retrieval system or be broadcast or transmitted without the prior written permission of the Department of Employment, Economic Development and Innovation. The information contained herein is subject to change without notice. The copyright owner shall not be liable for technical or other errors or omissions contained herein. The reader/user accepts all risks and responsibility for losses, damages, costs and other consequences resulting directly or indirectly from using this information. Cover: Inspectors of Mines Chris Skelding and Lionel Smith at the Redlands Quarry Control Room. September 2011 The Honourable Stirling Hinchliffe, MP Minister for Employment, Skills and Mining 41 George Street Brisbane Qld 4000 Dear Minister In accordance with section 73E(1) of the Coal Mining Safety and Health Act 1999 I am pleased to submit to you the Mine Safety and Health Commissioner’s annual performance report for the year ending 30 June 2011. Yours sincerely Stewart Bell Commissioner for Mine Safety and Health Commissioner for Mine Safety and Health | Annual Report 2010–2011 i ii Commissioner -
The Mineral Industry of Australia in 2005
2005 Minerals Yearbook AUSTRALIA U.S. Department of the Interior June 2007 U.S. Geological Survey THE MINERAL INDUSTRY OF AUSTRALIA By Staff The Commonwealth of Australia is a country that is part of South Australia was under bankable feasibility study. In 2005, Oceania, which is located between the Indian Ocean and the Australia exported 1.3 Mt of copper concentrates. Owing to the South Pacific Ocean. The country’s land mass is 7,617,930 country’s increased output, exports of copper concentrates were square kilometers (km2) and encompasses the continent of expected to increase during the next several years. Australia’s Australia and adjacent islands, including King Island and refined copper output was about 450,000 t/yr, and output Tasmania, Lord Howe Island, and Macquarie Island. Owing to capacity was expected to increase to about 500,000 t/yr in 2007 its large mineral resources, Australia was one of the world’s because of the 20,000-t/yr expansion project underway at the leading mineral producing countries. The country ranked among Townsville copper refinery and the 15,000-t/yr greenfield Lady the top 10 countries worldwide in the production of bauxite, Annie project underway at Queensland. Australia exported coal, cobalt, copper, gem and near-gem diamond, gold, iron ore, more than 300,000 t/yr of refined copper (Australian Bureau of lithium, manganese ore, niobium, rare earths, and uranium. Agricultural and Resource Economics, 2006a, p. 155). Gold.—Australia’s gold mine output ranked second in the Commodity Review world after the Republic of South Africa. -
Annual Report
CORPORATE PROFILE AUSTRALIA Diversified. Dedicated. Driven. About Glencore Highly diversified Active at every stage of the commodity chain to maximise value +90 50 COMMODITIES COUNTRIES Global scale 90 150 155,000 OFFICES SITES PEOPLE Unique market insight Long-term relationships with broad base of suppliers and customers 4,000 40+ for bindingShort page EMPLOYEES IN MARKETING YEARS EXPERIENCE Glencore is one of the world’s largest and most diversified producers, processors and marketers of natural resources. We market commodities sourced from our own and third party production and deliver these to a global customer base, which includes the automotive, steel, power generation, oil and food processing industries. Our business covers three broad sectors: Metals and Minerals, Energy Products and Glencore Agriculture, which are all supported by our extensive global marketing network. More information is available at www.glencore.com www.glencore.com.au Contents ABOUT GLENCORE 1 Our Australian operations’ contribution 2 The history of our business in Australia 3 Our role and focus areas 4 A unique business model METALS AND MINERALS 7 Copper 9 Zinc 10 Nickel 11 Glencore Technology ENERGY PRODUCTS 13 Coal 15 Oil 17 AGRICULTURE 18 MARKETING OUR PRODUCTS IN SOCIETY 19 Copper 20 Zinc 21 Nickel 22 Coal 23 Agriculture 24 Supporting regional Australia Short page for bindingShort page Our Australian operations Australia is an important part of our global business. We’ve operated here for nearly 20 years and hold significant interests in a range of commodity industries across all mainland states and the Northern Territory. Headquartered in Sydney, we are a major Australian Most of our investments are highly capital intensive, employer, with about 15,600 people working across long-term and require a stable and predictable industries that include coal, copper, cotton, grain and investment environment. -
Mine to Market
No.153 May/June 2017 MINE TO MARKET New Copper IsaSmelt Ernest Henry underground celebrates underground mine truck joins 30 years since team achieves George Fisher development two years Lost fl e e t Time Injury free Mine to Market No. 153 • May/June 2017 OPERATIONS HEALTH AND SAFETY Work experience creates opportunities for young people . 15 George Fisher Mine welcomes new Two years LTI free for Ernest Henry underground truck . 1 Mining’s underground team . 3 Record partnerships in $31 million GCPNQ program . 16 Mount Isa Mines’ copper concentrator SafeSpine program reduces the risk increases copper output . 2 of soft tissue injuries . 7 Support your community through workplace giving . 18 Glencore Technology celebrates Keep your heart healthy . 24 30 years of the copper ISASMELT™ Mount Isa Mines gives trade career technology . 4 ENVIRONMENT tips to local students . 22 Townsville Port Operations improve Keeping track of our valuable OUR PEOPLE resources every step of the way . 6 storm water management system . 6 Archie Macpherson’s Story . 12 New rock breakers help break down COMMUNITY underground ineffi ciencies . .14 NOTICES Community Assistance Program Glencore at a glance: CSA MINE, continues to deliver benefi ts to our Announcements, Calendar of Events . 25 Cobar, New South Wales, Australia . 21 north Queensland communities . 8 MineX showcases regional mining industry . 10 CONTACT THE From the COOs EDITOR Karissa Hewitt , via email In May, two of our people were honoured at socio-economic contribution to Indigenous karissa.hewitt @glencore.com. au or phone 07 4744 2979. the 2017 Queensland Resources Council (QRC) people and communities. Indigenous Awards in Brisbane.