A Study on Solution-Processed Y2O3 Films Modified by Atomic Layer
Total Page:16
File Type:pdf, Size:1020Kb
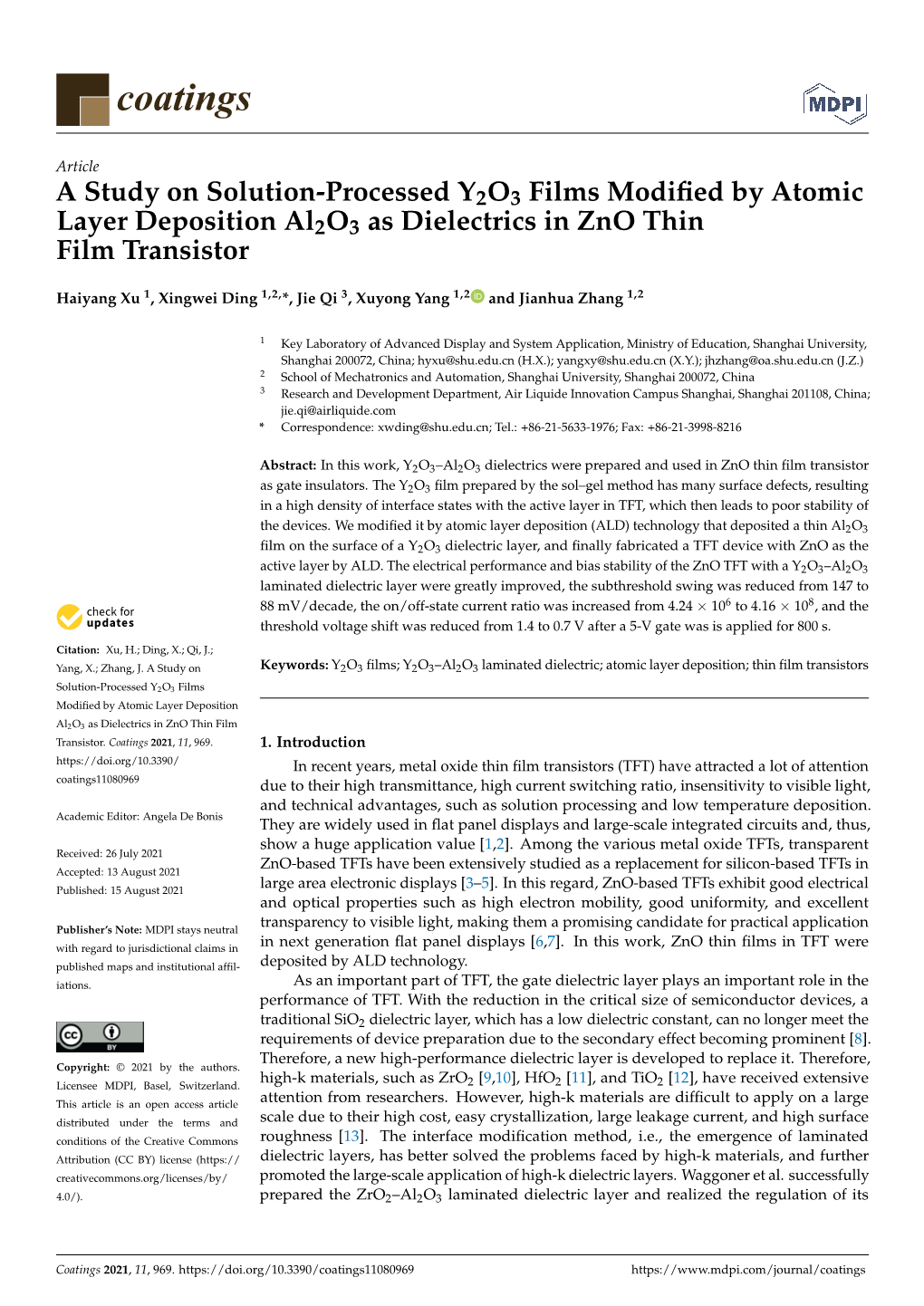
Load more
Recommended publications
-
Antireflective Coatings
materials Review Antireflective Coatings: Conventional Stacking Layers and Ultrathin Plasmonic Metasurfaces, A Mini-Review Mehdi Keshavarz Hedayati 1,* and Mady Elbahri 1,2,3,* 1 Nanochemistry and Nanoengineering, Institute for Materials Science, Faculty of Engineering, Christian-Albrechts-Universität zu Kiel, Kiel 24143, Germany 2 Nanochemistry and Nanoengineering, Helmholtz-Zentrum Geesthacht, Geesthacht 21502, Germany 3 Nanochemistry and Nanoengineering, School of Chemical Technology, Aalto University, Kemistintie 1, Aalto 00076, Finland * Correspondence: [email protected] (M.K.H.); mady.elbahri@aalto.fi (M.E.); Tel.: +49-431-880-6148 (M.K.H.); +49-431-880-6230 (M.E.) Academic Editor: Lioz Etgar Received: 2 May 2016; Accepted: 15 June 2016; Published: 21 June 2016 Abstract: Reduction of unwanted light reflection from a surface of a substance is very essential for improvement of the performance of optical and photonic devices. Antireflective coatings (ARCs) made of single or stacking layers of dielectrics, nano/microstructures or a mixture of both are the conventional design geometry for suppression of reflection. Recent progress in theoretical nanophotonics and nanofabrication has enabled more flexibility in design and fabrication of miniaturized coatings which has in turn advanced the field of ARCs considerably. In particular, the emergence of plasmonic and metasurfaces allows for the realization of broadband and angular-insensitive ARC coatings at an order of magnitude thinner than the operational wavelengths. In this review, a short overview of the development of ARCs, with particular attention paid to the state-of-the-art plasmonic- and metasurface-based antireflective surfaces, is presented. Keywords: antireflective coating; plasmonic metasurface; absorbing antireflective coating; antireflection 1. -
Design of Multi-Layer Anti-Reflection Coating for Terrestrial Solar Panel
Bull. Mater. Sci., Vol. 39, No. 3, June 2016, pp. 683–689. c Indian Academy of Sciences. DOI 10.1007/s12034-016-1195-x Design of multi-layer anti-reflection coating for terrestrial solar panel glass B GEETHA PRIYADARSHINI1,∗ and A K SHARMA2 1Nanotech Research Innovation & Incubation Centre, PSG Institute of Advanced Studies, Peelamedu, Coimbatore 641004, India 2National Centre for Photovoltaic Research & Education, Department of Electrical Engineering, Indian Institute of Technology, Bombay 400 076, India MS received 14 September 2015; accepted 10 December 2015 Abstract. To date, there is no ideal anti-reflection (AR) coating available on solar glass which can effectively trans- mit the incident light within the visible wavelength range. However, there is a need to develop multifunctional coating with superior anti-reflection properties and self-cleaning ability meant to be used for solar glass panels. In spite of self-cleaning ability of materials like TiO2 and ZnO, these coatings on glass substrate have tendency to reduce light transmission due to their high refractive indices than glass. Thus, to infuse the anti-reflective property, a low refrac- tive index, SiO2 layer needs to be used in conjunction with TiO2 and ZnO layers. In such case, the optimization of individual layer thickness is crucial to achieve maximum transmittance of the visible light. In the present study, we propose an omni-directional anti-reflection coating design for the visible spectral wavelength range of 400–700 nm, where the maximum intensity of light is converted into electrical energy. Herein, we employ the quarter wavelength criteria using SiO2,TiO2 and ZnO to design the coating composed of single, double and triple layers. -
Bio-Based and Biodegradable Plastics – Facts and Figures Focus on Food Packaging in the Netherlands
Bio-based and biodegradable plastics – Facts and Figures Focus on food packaging in the Netherlands Martien van den Oever, Karin Molenveld, Maarten van der Zee, Harriëtte Bos Rapport nr. 1722 Bio-based and biodegradable plastics - Facts and Figures Focus on food packaging in the Netherlands Martien van den Oever, Karin Molenveld, Maarten van der Zee, Harriëtte Bos Report 1722 Colophon Title Bio-based and biodegradable plastics - Facts and Figures Author(s) Martien van den Oever, Karin Molenveld, Maarten van der Zee, Harriëtte Bos Number Wageningen Food & Biobased Research number 1722 ISBN-number 978-94-6343-121-7 DOI http://dx.doi.org/10.18174/408350 Date of publication April 2017 Version Concept Confidentiality No/yes+date of expiration OPD code OPD code Approved by Christiaan Bolck Review Intern Name reviewer Christaan Bolck Sponsor RVO.nl + Dutch Ministry of Economic Affairs Client RVO.nl + Dutch Ministry of Economic Affairs Wageningen Food & Biobased Research P.O. Box 17 NL-6700 AA Wageningen Tel: +31 (0)317 480 084 E-mail: [email protected] Internet: www.wur.nl/foodandbiobased-research © Wageningen Food & Biobased Research, institute within the legal entity Stichting Wageningen Research All rights reserved. No part of this publication may be reproduced, stored in a retrieval system of any nature, or transmitted, in any form or by any means, electronic, mechanical, photocopying, recording or otherwise, without the prior permission of the publisher. The publisher does not accept any liability for inaccuracies in this report. 2 © Wageningen Food & Biobased Research, institute within the legal entity Stichting Wageningen Research Preface For over 25 years Wageningen Food & Biobased Research (WFBR) is involved in research and development of bio-based materials and products. -
Development of Flexible and Functional Sequins Using Subtractive Technology and 3D Printing for Embroidered Wearable Textile Applications
materials Article Development of Flexible and Functional Sequins Using Subtractive Technology and 3D Printing for Embroidered Wearable Textile Applications Ramona Nolden * , Kerstin Zöll and Anne Schwarz-Pfeiffer Research Institute for Textile and Clothing, Hochschule Niederrhein-University of Applied Sciences, Webschulstraße 31, 41065 Mönchengladbach, Germany; [email protected] (K.Z.); [email protected] (A.S.-P.) * Correspondence: [email protected] Abstract: Embroidery is often the preferred technology when rigid circuit boards need to be con- nected to sensors and electrodes by data transmission lines and integrated into textiles. Moreover, conventional circuit boards, like Lilypad Arduino, commonly lack softness and flexibility. One approach to overcome this drawback can be flexible sequins as a substrate carrier for circuit boards. In this paper, such an approach of the development of flexible and functional sequins and circuit boards for wearable textile applications using subtractive and additive technology is demonstrated. Applying these techniques, one-sided sequins and circuit boards are produced using wax printing and etching copper-clad foils, as well as using dual 3D printing of conventional isolating and electri- cally conductive materials. The resulting flexible and functional sequins are equipped with surface mounted devices, applied to textiles by an automated embroidery process and contacted with a Citation: Nolden, R.; Zöll, K.; conductive embroidery thread. Schwarz-Pfeiffer, A. Development of Flexible and Functional Sequins Keywords: 3D printing; additive manufacturing; circuit boards; functional sequins; subtractive Using Subtractive Technology and 3D technology; wearable electronics Printing for Embroidered Wearable Textile Applications. Materials 2021, 14, 2633. https://doi.org/10.3390/ ma14102633 1. -
In Situ Investigations of Simultaneous Two‐Layer Slot Die Coating of Component‐Graded Anodes for Improved High‐Energy Li
FULL PAPER www.entechnol.de In Situ Investigations of Simultaneous Two-Layer Slot Die Coating of Component-Graded Anodes for Improved High- Energy Li-Ion Batteries Ralf Diehm,* Jana Kumberg, Christopher Dörrer, Marcus Müller, Werner Bauer, Philip Scharfer, and Wilhelm Schabel emission-free vehicles.[2] Studies show a The use of thicker electrodes can contribute to a reduction in cell costs. However, need of more than 1 TWh of production the properties of the electrode must be kept in view to be able to meet the capacity by 2025, which represents a signif- [3] performance requirements. Herein, the possibility of simultaneous multilayer slot icant increase in production capacity. In addition, further cost reduction and die coating is investigated to improve the electrode properties of medium- and improvement of the electrode properties high-capacity anodes. The stable coating window of the two-layer slot die coating are also necessary. One concept is to reduce process is investigated to produce property-graded multilayer electrodes. Electrodes costs by manufacturing thick electrodes. with different styrene–butadiene rubber (SBR) gradients are investigated with Due to the higher electrode capacity, the regard to adhesive force and electrochemical performance. An increase in the number of electrodes and associated inac- tive materials such as collector foils and adhesive force of up to 43.5% and an increase in the discharge capacity is separators in the battery cell are saved. observed. The energy density is also increased by saving inactive materials. Previous investi- gations have shown that thick electrodes lose capacities especially at higher charging 1. Introduction and discharging rates.[4] The production of two-layer coatings with a graded electrode might lower this problem. -
Oxide-Based Electric-Double-Layer Thin-Film Transistors on a Flexible Substrate
The University of Manchester Research Oxide-Based Electric-Double-Layer Thin-Film Transistors on a Flexible Substrate DOI: 10.1109/LED.2017.2768822 Document Version Accepted author manuscript Link to publication record in Manchester Research Explorer Citation for published version (APA): Cai, W., Zhang, J., Wilson, J., Ma, X., Wang, H., Zhang, X., Qian Xin, & Song, A. (2017). Oxide-Based Electric- Double-Layer Thin-Film Transistors on a Flexible Substrate. IEEE Electron Device Letters, 38(12), 1680-1683. https://doi.org/10.1109/LED.2017.2768822 Published in: IEEE Electron Device Letters Citing this paper Please note that where the full-text provided on Manchester Research Explorer is the Author Accepted Manuscript or Proof version this may differ from the final Published version. If citing, it is advised that you check and use the publisher's definitive version. General rights Copyright and moral rights for the publications made accessible in the Research Explorer are retained by the authors and/or other copyright owners and it is a condition of accessing publications that users recognise and abide by the legal requirements associated with these rights. Takedown policy If you believe that this document breaches copyright please refer to the University of Manchester’s Takedown Procedures [http://man.ac.uk/04Y6Bo] or contact [email protected] providing relevant details, so we can investigate your claim. Download date:27. Sep. 2021 > REPLACE THIS LINE WITH YOUR PAPER IDENTIFICATION NUMBER (DOUBLE-CLICK HERE TO EDIT) < 1 Oxide-Based Electric-Double-Layer Thin-Film Transistors on a Flexible Substrate Wensi Cai, Jiawei Zhang, Joshua Wilson, Xiaochen Ma, Hanbin Wang, Xijian Zhang, Qian Xin, and Aimin Song, Senior Member, IEEE over large area. -
Controlling the Alignment of Polyimide for Liquid Crystal Devices
Chapter 5 Controlling the Alignment of Polyimide for Liquid Crystal Devices Shie-Chang Jeng and Shug-June Hwang Additional information is available at the end of the chapter http://dx.doi.org/10.5772/53457 1. Introduction Liquid crystal (LC) devices have been popular for use in photonics products, such as displays for mobile phones, televisions and computers. As shown in Fig. 1, a typical LC device consists of a thin LC layer sandwiched between a pair of indium tin oxide (ITO) conducting glass substrates with a cell gap of few micrometers. Polyimide (PI) as a polymeric material characterized by its outstanding mechanical, thermal and electrical properties at moderate high temperature has been widely applied in the LC displays (LCDs) industry as the alignment layers to align LC molecules in a certain orientation and conformation with a specific pretilt angle, the angle between the director of the LC molecules and the PI alignment layer. The pretilt angle is very important and required for LC devices to obtain a defect-free alignment and also to improve their electro-optical performance, such as driving voltage, response time, color performance and viewing angle. However, the applications of conventional PIs in LCDs are limited by a small tuning range of pretilt angle (~ few degrees) either by controlling the rubbing depth or the number of rubbings (Paek et al., 1998). Substrate PI alignment layer LC Pretilt angle Figure 1. The typical structure of a liquid crystal device. The pretilt angle of an LCD is either near zero degrees or 90 degrees for using the conventional homogeneous and homeotropic PI materials, respectively. -
Intermediate Layers in Tandem Organic Solar Cells Yongbo Yuan University of Nebraska-Lincoln
University of Nebraska - Lincoln DigitalCommons@University of Nebraska - Lincoln Mechanical & Materials Engineering Faculty Mechanical & Materials Engineering, Department Publications of 2011 Intermediate Layers in Tandem Organic Solar Cells Yongbo Yuan University of Nebraska-Lincoln Jinsong Huang University of Nebraska-Lincoln, [email protected] Gang Li Solarmer Energy, Inc. Follow this and additional works at: http://digitalcommons.unl.edu/mechengfacpub Part of the Mechanics of Materials Commons, Nanoscience and Nanotechnology Commons, Other Engineering Science and Materials Commons, and the Other Mechanical Engineering Commons Yuan, Yongbo; Huang, Jinsong; and Li, Gang, "Intermediate Layers in Tandem Organic Solar Cells" (2011). Mechanical & Materials Engineering Faculty Publications. 189. http://digitalcommons.unl.edu/mechengfacpub/189 This Article is brought to you for free and open access by the Mechanical & Materials Engineering, Department of at DigitalCommons@University of Nebraska - Lincoln. It has been accepted for inclusion in Mechanical & Materials Engineering Faculty Publications by an authorized administrator of DigitalCommons@University of Nebraska - Lincoln. Green, Vol. 1 (2011), pp. 65–80 Copyright © 2011 De Gruyter. DOI 10.1515/GREEN.2011.009 Review Intermediate Layers in Tandem Organic Solar Cells Yongbo Yuan,1 Jinsong Huang1; and Gang Li2 cost solar photovoltaic solution and attracts significant aca- demic and industry research. The low cost of OPV comes 1 Department of Mechanical Engineering, University of from several intrinsic advantages of this technology: (a) or- Nebraska-Lincoln, Lincoln, NE 68588 ganic materials are abundant; progress in organic chemistry 2 Solarmer Energy, Inc., El Monte, CA 91731 forms a solid base for material innovation; (b) OPV materi- als have much higher absorption coefficients than silicon, which leads to typical OPV active layer thickness in the Abstract. -
Organic Electronics
2007 VOLUME 2 NUMBER 3 TM Organic Electronics Organic Materials For Thin Film Transistors Polymers for Plastic Electronics Fullerene-Based Semiconductors Organic Light-Emitting Devices Light-Emitting Polymers Printed circuits for a cleaner and brighter future. sigma-aldrich.com Introduction Welcome to the third installment of Material Matters™ for 2007 focusing on Organic TM Electronics. Started over 30 years ago with the discovery that organic molecules can act as electrical conductors, this field is on the verge of the first commercially Vol. No. 3 successful applications. Low-cost manufacturing methods and compatibility with flexible substrates are two of the exciting features of plastic electronics. One day soon, these attributes may enable disposable RFID tags made from interconnected organic field-effect transistors (OFETs), or large-area photovoltaic cells (PVs) painted on Aldrich Chemical Co., Inc. building roofs and economically replaced every other year to match color preferences Sigma-Aldrich Corporation of homeowners. Bright, high-resolution flat-screen displays made from organic light- 6000 N. Teutonia Ave. emitting diodes (OLEDs) are closest to commercial success, but remain expensive and Milwaukee, WI 53209, USA power-hungry relative to the entrenched technologies. Steady advances in the quality and variety of available organic conductors, as well as a fundamental understanding of materials physics and device engineering, enabled progress from early polymer To Place Orders conductors to the present day OFETs and OLEDs. Telephone 800-325-3010 (USA) In this issue, Professor Zhenan Bao (Stanford University) describes organic materials FAX 800-325-5052 (USA) Introduction essential for making better OFETs. The article is accompanied by a selection of p-type and n-type semiconductors as well as polymer dielectrics available from Sigma-Aldrich. -
The Path to Ubiquitous and Low-Cost Organic Electronic Appliances on Plastic
review article The path to ubiquitous and low-cost organic electronic appliances on plastic Stephen R. Forrest Princeton Institute for the Science and Technology of Materials (PRISM), Department of Electrical Engineering, Princeton University, Princeton, New Jersey 08544, USA ........................................................................................................................................................................................................................... Organic electronics are beginning to make significant inroads into the commercial world, and if the field continues to progress at its current, rapid pace, electronics based on organic thin-film materials will soon become a mainstay of our technological existence. Already products based on active thin-film organic devices are in the market place, most notably the displays of several mobile electronic appliances. Yet the future holds even greater promise for this technology, with an entirely new generation of ultralow-cost, lightweight and even flexible electronic devices in the offing, which will perform functions traditionally accomplished using much more expensive components based on conventional semiconductor materials such as silicon. nterest in organic electronics stems from the ability to deposit developed to maintain the very low costs inherent in these material organic films on a variety of very-low-cost substrates such as systems. The promise of organic electronics through the production glass, plastic or metal foils, and the relative ease of processing of ubiquitous, low-cost and robust devices filling niches not of the organic compounds that are currently being engineered occupied by silicon-based electronics should become readily appar- by hundreds of chemists. The most advanced organic elec- ent through the understanding of the unique properties that Itronic systems already in commercial production are high- characterize these potentially high-performance materials. -
The 2021 Flexible and Printed Electronics Roadmap
UC San Diego UC San Diego Previously Published Works Title The 2021 flexible and printed electronics roadmap Permalink https://escholarship.org/uc/item/4xz53786 Journal Flexible and Printed Electronics, 6(2) ISSN 2058-8585 Authors Bonnassieux, Y Brabec, CJ Cao, Y et al. Publication Date 2021-06-01 DOI 10.1088/2058-8585/abf986 Peer reviewed eScholarship.org Powered by the California Digital Library University of California Flexible and Printed Electronics TOPICAL REVIEW • OPEN ACCESS The 2021 flexible and printed electronics roadmap To cite this article: Yvan Bonnassieux et al 2022 Flex. Print. Electron. 6 023001 View the article online for updates and enhancements. This content was downloaded from IP address 76.167.211.152 on 20/05/2021 at 06:57 Flex. Print. Electron. 6 (2022) 023001 https://doi.org/10.1088/2058-8585/abf986 Flexible and Printed Electronics ROADMAP The 2021 flexible and printed electronics roadmap OPEN ACCESS Yvan Bonnassieux1, Christoph J Brabec2,3,4, Yong Cao5, Tricia Breen Carmichael6, Michael L Chabinyc7, 8 9 9,10 11 12 RECEIVED Kwang-Ting Cheng , Gyoujin Cho , Anjung Chung , Corie L Cobb , Andreas Distler , Hans- 19 October 2020 Joachim Egelhaaf2,12, Gerd Grau13, Xiaojun Guo14, Ghazaleh Haghiashtiani15, Tsung-Ching Huang16, REVISED 17,18 19 20 21,22 5 9 March 2021 Muhammad M Hussain , Benjamin Iniguez , Taik-Min Lee , Ling Li , Yuguang Ma , Dongge Ma5, Michael C McAlpine15,23, Tse Nga Ng24, Ronald Österbacka25, Shrayesh N Patel26, Jun- ACCEPTED FOR PUBLICATION 5 27 28 29 30,31 32 19 April 2021 biao Peng , Huisheng Peng , Jonathan Rivnay , Leilai Shao , Daniel Steingart , Robert A Street , 33,34 34 6 PUBLISHED Vivek Subramanian , Luisa Torsi and Yunyun Wu 17 May 2021 1 CNRS, Ecole´ polytechnique, IP Paris, Palaiseau, France 2 Friedrich-Alexander University Erlangen-Nürnberg, Institute of Materials for Electronics and Energy Technology (i-MEET), Original content from Martensstr. -
Metal Oxide Layer in Organic Solar Cells
Metal oxide layer in organic solar cells Doctoral Thesis vorgelegt von Haiyan Sun angefertigt in der Arbeitsgruppe Hybrid Nanostructures Prof. Dr. Lukas Schmidt-Mende Fakultät für Physik Ludwig-Maximilians-Universität München Juni 19, 2012 Erstgutachter: Prof. Dr. Lukas Schmidt-Mende Zweitgutachter:Prof. Dr. Alexander Högele Datum der muendlichen Pruefung: 09.08.2012 Contents Abstract ............................................................................................................................................. v List of Abbreviations ........................................................................................................................ ix 1 Introduction .................................................................................................................................... 1 1.1 Solar cells working principles ............................................................................................. 3 1.1.1 Organic photovoltaic materials ................................................................................ 3 1.1.2 Donor-acceptor concept ........................................................................................... 4 1.1.3 Charge generation .................................................................................................... 5 1.1.4 Morphology in organic solar cells ............................................................................ 8 1.1.5 Recombination mechanisms ..................................................................................