Gear Hobbing Unit
Total Page:16
File Type:pdf, Size:1020Kb
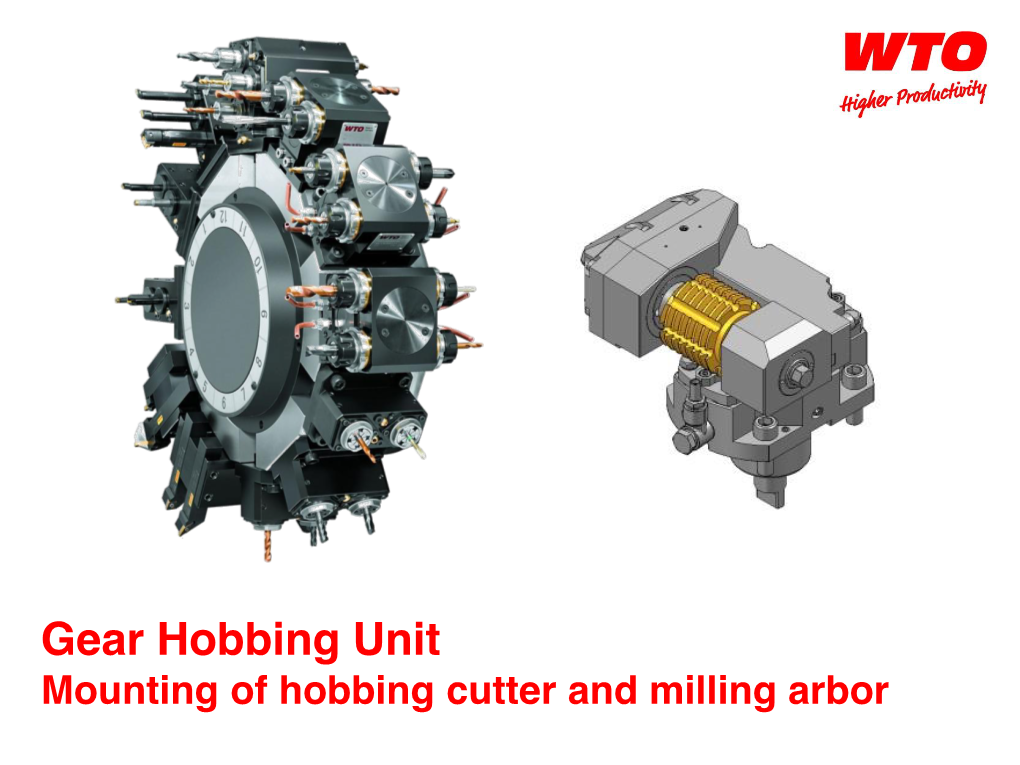
Load more
Recommended publications
-
LD HD AXLE SHAFTS.Pdf
AXLECAT 003 ™ Performance Division Light Duty Division Heavy Duty Division Quality Assurance Quality of product is the most important ingredient in sustaining a successful business. At Midwest Truck & Auto Parts, Inc.™, we take quality control very seriously. Our highly qualified quality control technicians are always up-to-date on the latest innovations to insure that the quality of our product is unsurpassed. We back all of our products with a 6 month, 50,000 mile no-nonsense warranty*. Your business is our livelihood, and we take your business seriously. The highest standards are applied in the production of our products. From machining and finishing to heat treatment, we demand the best. Motive Gear differential components are tested for acceptable tolerances, fitment and strength. Thorough tolerance and accuracy inspection of transmission and transfer case components, rebuild kits, and bearing kits. * Does not include products used in competition applications. © 2006 Midwest Truck & Auto Parts, Inc.™ TABLE OF CONTENTS LIGHT DUTY AXLE SHAFTS - FRONT TRUCK AMC® - JEEP® STYLE (ALL CHROME MOLY 4340) . .2 DANA® STYLE BLANKS (ALL CHROME MOLY 4340) . .2 FORD® STYLE (ALL CHROME MOLY 4340) . .2 FORD® STYLE STOCK REPLACEMENT . .3 GMC® STYLE (ALL CHROME MOLY 4340) . .3 GMC® STYLE STOCK REPLACEMENT . .3 IHC® STYLE (ALL CHROME MOLY 4340) . .3 LIGHT DUTY AXLE SHAFTS - REAR CAR FORD® STYLE . .4 GMC® STYLE . .4-5 LIGHT DUTY AXLE SHAFTS - REAR TRUCK AMC®-JEEP® STYLE . .6 CHRYSLER® - DODGE® - PLYMOUTH® STYLE . .7 FORD® STYLE . .7-8 GMC® STYLE . .8-10 HEAVY DUTY AXLE SHAFTS DODGE® STYLE . .11 EATON® STYLE . .11-12 FORD® STYLE . .12 GMC® STYLE . -
Grinding Your Own Lathe Tools
WEAR YOUR SAFETY GLASSES FORESIGHT IS BETTER THAN NO SIGHT READ INSTRUCTIONS BEFORE OPERATING Grinding Your Own Left Hand Right Hand Boring Tool Cutting Tool Cutting Tool Lathe Tools As with any machining operation, grinding requires the Dressing your grinding wheel is a part of maintaining the utmost attention to “Eye Protection.” Be sure to use it when bench grinder. Grinding wheels should be considered cutting attempting the following instructions. tools and have to be sharpened. A wheel dresser sharpens Joe Martin relates a story about learning to grind tools. “My by “breaking off” the outer layer of abrasive grit from the first experience in metal cutting was in high school. The wheel with star shaped rotating cutters which also have to teacher gave us a 1/4" square tool blank and then showed be replaced from time to time. This leaves the cutting edges us how to make a right hand cutting tool bit out of it in of the grit sharp and clean. a couple of minutes. I watched closely, made mine in ten A sharp wheel will cut quickly with a “hissing” sound and minutes or so, and went on to learn enough in one year to with very little heat by comparison to a dull wheel. A dull always make what I needed. I wasn’t the best in the class, wheel produces a “rapping” sound created by a “loaded just a little above average, but it seemed the below average up” area on the cutting surface. In a way, you can compare students were still grinding on a tool bit three months into the what happens to grinding wheels to a piece of sandpaper course. -
Gear Cutting and Grinding Machines and Precision Cutting Tools Developed for Gear Manufacturing for Automobile Transmissions
Gear Cutting and Grinding Machines and Precision Cutting Tools Developed for Gear Manufacturing for Automobile Transmissions MASAKAZU NABEKURA*1 MICHIAKI HASHITANI*1 YUKIHISA NISHIMURA*1 MASAKATSU FUJITA*1 YOSHIKOTO YANASE*1 MASANOBU MISAKI*1 It is a never-ending theme for motorcycle and automobile manufacturers, for whom the Machine Tool Division of Mitsubishi Heavy Industries, Ltd. (MHI) manufactures and delivers gear cutting machines, gear grinding machines and precision cutting tools, to strive for high precision, low cost transmission gears. This paper reports the recent trends in the automobile industry while describing how MHI has been dealing with their needs as a manufacturer of the machines and cutting tools for gear production. process before heat treatment. A gear shaping machine, 1. Gear production process however, processes workpieces such as stepped gears and Figure 1 shows a cut-away example of an automobile internal gears that a gear hobbing machine is unable to transmission. Figure 2 is a schematic of the conven- process. Since they employ a generating process by a tional, general production processes for transmission specific number of cutting edges, several tens of microns gears. The diagram does not show processes such as of tool marks remain on the gear flanks, which in turn machining keyways and oil holes and press-fitting bushes causes vibration and noise. To cope with this issue, a that are not directly relevant to gear processing. Nor- gear shaving process improves the gear flank roughness mally, a gear hobbing machine is responsible for the and finishes the gear tooth profile to a precision of mi- crons while anticipating how the heat treatment will strain the tooth profile and tooth trace. -
Design Parameters for Spline Connections Dr
Design Parameters for Spline Connections Dr. Hermann J. Stadtfeld Introduction following sections present a firm guideline for each step of the Splines are machine elements that connect a shaft with a rotor. design, tolerancing and cutting tool definition. Next to transmitting torque, the spline might also be utilized The Different Spline Functions and the Required Fits to center the rotor to the shaft. It is interesting that the spline’s If a splined shaft that is, for example, the output of a trans- tooth profiles are involutes, although the involute profile does mission drive with a rotor that is mounted on its own bearings, not contribute to the torque transmission, nor is it linked to the then the function of the spline is not the centering of the rotor centering function. The reason for the involute profile is the fact but merely torque transmission. In this case, a centering func- that most external splines are manufactured by hobbing with a tion would just cause the transfer of misalignment and runout standard straight-sided, symmetric hob tooth profile that is fast between shaft and rotor, which leads to vibration and bearing and delivers good accuracy results. The internal spline has to be wear. The described connection should have backlash between manufactured with shaping or broaching, using an involute cut- the flanks and clearance between the top of the internal and ting tooth profile. The nomenclature and parameters of a typical external teeth and their adjacent roots, and use a profile fit with spline connection are presented (Fig. 1). The spline connection backlash (Fig. -
Lathe Tooling Guide
LATHE TOOLING GUIDE A reference guide to understanding how cutting tools work and which inserts they pair with. ©Tormach® 2021. All rights reserved. Specifications subject to change without notice. DS10524_Lathe_Tooling_0921B TORMACH.COM Tormach® CNC Lathe Tooling REFERENCE GUIDE To make the most of a machine purchase, it’s important to understand how cutting tools work and which inserts they pair with. Here is some background on lathe cutting tool and insert terminology: ISO/ANSI Inserts Like metric and imperial measurements standards, the U.S. has its own tool TABLE OF insert classification system; they are called American National Standards Institute (ANSI) designations. All of these ANSI classifications can be converted CONTENTS to the International Organization for Standardization (ISO) classifications, but this guide includes both for easier selection. Cutting Tool Designations 3 Turning Tools Cutting tools are easily identified by their designation, which is universal between ISO and ANSI, and, in the machine shop, tool slang often refers to 6 Boring Bars the insert shape, which is also available in the tool designation. Examples and explanations of designations are available at the start of each section. 7 Turning/ Boring Right-Hand vs. Left-Hand vs. Neutral Inserts Right-hand tools are the most commonly used, because they can be used for most turning applications, including making shoulders on the front of the workpiece. Left-handed tools are typically chosen for back turning and making 11 Grooving/ Parting sharp shoulders on the back of the workpiece. Neutral tools are ideal for Tools complex profiling, thanks to their narrow tips. Insert Shapes 12 Grooving/ Parting There are a variety of insert shapes available, but the general note is use Tool Inserts wider inserts for simple geometry and roughing passes, since they have more durability than a more narrow cutting tool, which is needed for complicated or 12 Threading Tools intricate parts. -
Intelligent Process Optimization „Innovation Is Our Future.“ Sascha Tschiggfrei, CEO the Future Has Begun
Intelligent Process Optimization „Innovation is our future.“ Sascha Tschiggfrei, CEO The Future has begun As a global market leader, we manufacture technologically advanced high precision tool holders for turning centers and swiss type lathes that are known for high performance and long life-time. Using our new “smart” technology, our customers will be able to intelligently optimize and monitor their processes in the future. Intelligent Process State-of-the-art technology for maximum productivity. With this claim, WTO develops Optimization and produces superior precision tool holders in terms of technology and quality. Used intelligently, processes are optimized and production becomes more productive. WTO Driven Precision Tool Holders equipped with innovative „smart“ technology enable intelligent online process monitoring. “Consistent development - always one step ahead.” Karlheinz Jansen, CTO High Tech – Made in Germany From the technical design to the finished product we make no compromises when it comes to manufacturing our high precision tool holders. Permanent investment in state-of-the-art production technologies, high quality standards and a large manufacturing depth. Our products are in use worldwide, wherever precision parts are manufactured on turning centers with high productivity. „Our employees don‘t work for WTO. They work for the success of our customers.“ Daniel Sierra, Sales Director WTO Your Success is our Business Motivated employees are the basis for 100 % consistent customer focus. WTO offers its employees a state-of-the-art working environ- ment to work independently and ensures highly motivated employees in a family-owned technology company. To a large extent, WTO relies on its own highly qualified employees in order to achieve high quality standards. -
Introduction to Turning Tools and Their Application Identification and Application of Cutting Tools for Turning
Introduction to Turning Tools and their Application Identification and application of cutting tools for turning The variety of cutting tools available for modern CNC turning centers makes it imperative for machine operators to be familiar with different tool geometries and how they are applied to common turning processes. This course curriculum contains 16-hours of material for instructors to get their students ready to identify different types of turning tools and their uses. ©2016 MachiningCloud, Inc. All rights reserved. Table of Contents Introduction .................................................................................................................................... 2 Audience ..................................................................................................................................... 2 Purpose ....................................................................................................................................... 2 Lesson Objectives ........................................................................................................................ 2 Anatomy of a turning tool............................................................................................................... 3 Standard Inserts .............................................................................................................................. 3 ANSI Insert Designations ............................................................................................................. 3 Insert Materials -
Industrial Productivity Training Manual
INDUSTRIAL PRODUCTIVITY TRAINING MANUAL Version 2.0 Written by: Dr. Michael R. Muller - Director, Don Kasten ©2006 Rutgers, the State University of New Jersey Table of Contents INTRODUCTION..............................................................................2 PRODUCTIVITY TOOLBOX ..............................................................5 Toolbox Introduction.....................................................................6 Productivity Metrics......................................................................9 Cost of Labor..............................................................................10 Space Optimization .......................................................................11 Productivity Questions...................................................................14 CONCEPTS FOR PRODUCTIVITY ENHANCEMENT, PART I INCREASING PIECES/PERSON/HOUR .............................................19 QUICK CHANGES......................................................................20 AR No. 1 Decrease Die Change-Out & Start-Up Times...................26 AR No. 2 Use Fixtures to Reduce Lathe Set-up Times....................32 AR No. 3 Install a Rotating Nozzle Carousel to Reduce Set-Up Times.34 AR No. 4 Employ Modular Jigs to Reduce Process Set-up Times.......36 BOTTLENECK MITIGATION.........................................................39 AR No. 5 Add Machine Operators to Reduce Production Bottleneck....41 AR No. 6 Install Refrigeration System to Cool Product...................45 AR No. 7 Replace Old Lathe -
Variable Speed 7 X 12 In. Metal Lathe
VARIABLE SPEED 7 X 12 IN. METAL LATHE Model # 3455 bit.ly/wenvideo IMPORTANT: Your new tool has been engineered and manufactured to WEN’s highest standards for dependability, ease of operation, and operator safety. When properly cared for, this product will supply you years of rugged, trouble-free performance. Pay close attention to the rules for safe operation, warnings, and cautions. If you use your tool properly and for intended purpose, you will enjoy years of safe, reliable service. NEED HELP? CONTACT US! Have product questions? Need technical support? Please feel free to contact us at: 800-232-1195 (M-F 8AM-5PM CST) [email protected] WENPRODUCTS.COM TABLE OF CONTENTS Technical Data 2 General Safety Rules 3 Specific Safety Rules For Metal Lathes 4 Electrical Information 6 Know Your Lathe 7 Assembly 8 Operation 9 Maintenance 19 Troubleshooting Guide 20 Exploded View & Parts List 22 Warranty 25 TECHNICAL DATA Model Number: 3455 Motor: 120V, 60Hz, 4A Swing Over Bed: 7 in. (180 mm) Distance Between Centers: 12 in. (300 mm) Spindle Bore: .79 in. (20 mm) Cross Slide Travel: 2-1/2 in. (65 mm) Compound Slide Travel 2.16 in. (55 mm) Speeds: 100 to 2500 RPM Spindle Taper: MT3 Tailstock Taper: MT2 Longitudinal Feed Rate: .1 to .2 mm Screw Threads: 15 to 52 TPI in 18 steps Weight: 81 lbs. 2 GENERAL SAFETY RULES Safety is a combination of common sense, staying alert and knowing how your item works. SAVE THESE SAFE- TY INSTRUCTIONS. WARNING: To avoid mistakes and serious injury, do not plug in your tool until the following steps have been read and understood. -
Gear Rolling for Production of High Gears Alireza Khodaee
Gear Rolling for Production of High Gears Alireza Khodaee Gear Rolling for Production of High Gears Alireza Khodaee Licentiate Thesis, 2015 KTH Royal Institute of Technology Industrial Engineering and Management Department of Production Engineering SE-100 44 Stockholm, Sweden TRITA-IIP-15-06 ISSN: 1650-1888 ISBN: 978-91-7595-678-7 Abstract Gears are used to transmit mechanical work from one point to another. They are widely used in different mechanisms and they are the most important components of a transmission system. Thus, it is important that they are manufactured with high precision to deliver the work with highest possible efficiency. The dominant gear production method is metal cutting, like hobbing. The gear manufacturing industry aims to replace their traditional production lines with greener processes and thereby urge engineers to think about using metal forming methods instead of the traditional metal cutting solutions when possible. Gear rolling is an interesting metal forming method that can be an alternative method to fabricate gear wheels. Research on gear rolling firstly came into interest around 2000. Very few papers are published that covers the development of the method and its limitations and advantages. Almost all of these publications considered rolling of gear wheels with small modules. The focus of this study will be on application of gear rolling for gear wheels with large module (over 3 mm) where the amount of deformation is much larger than found in previous studies. In this thesis the Finite Element Method has been used to simulate and predict the results of rolling of high gears. In addition to that experiments were performed to validate the numerical results and develop the modelling technique for further investigations. -
Manufacuting Technology
ME 6402 -Manufacturing Technology - II IV Sem / II Year B.E. (Mechanical Engineering) Department of Mechanical Engineering R.M.K.ENGINEERINGCOLLEGE R.S.M. Nagar, Kavaraipettai – 601 206. UNIT I - THEORY OF METAL CUTTING INTRODUCTION: CUTTING TOOL: SINGLE POINT CUTTING TOOL: NOMENCLATURE SINGLE POINT TOOL: MECHANICS OF METAL CUTTING: TYPES OF CHIPS: COOLANT OR CUTTING FLUIDS OR EMULSIONS: FUNCTIONS OR USES OF COOLANTS OR CUTTING FLUIDS: TYPICAL PROPERTIES OF TOOL MATERIALS: ------------------------------X-------------------------------- UNIT-II - CENTRE LATHE AND SPECIAL PURPOSE LATHE INTRODUCTION: TYPES OF LATHE: SPEED LATHE: CENTRE LATHE OR ENGINE LATHE: BENCH LATHE: TOOL ROOM LATHE: CAPSTAN AND TURRET LATHE: SPECIAL PURPOSE LATHE: AUTOMATIC LATHE: CONSTRUCTION OF LATHE MACHINE: BED: HEAD STOCK: TAIL STOCK: CARRIAGE: THREAD CUTTING MECHANISM: ACCESSORIES AND ATTACHMENTS OF LATHE: SPECIFICATION OF LATHE: LATHE OPERATIONS: TAPERS AND TAPER TURNING: TAPER TURNING BY SWIVELLING THE COMPOUND REST: TAPER TURNING ATTACHMENT METHOD: TAPER TURNING WITH TAILSTOCK SET OVER METHOD: FORM TOOL METHOD: TAPER TURNING WITH DOUBLE HEADS: THREAD CUTTING: DRILLING ON A LATHE: CUTTING SPEED: FEED: ---------------------------X------------------------------ UNIT-III, OTHER MACHINE TOOLS DRILLING INTRODUCTION: CONSTRUCTION OF DRILLING MACHINE: TYPES OF DRILLING MACHINE: PORTABLE DRILLING MACHINE: SENSITIVE DRILLING MACHINE: UPRIGHT DRILLING MACHINE: RADIAL DRILLING MACHINE: GANG DRILLING MACHINE: MULTIPLE-SPINDLE DRILLING MACHINE: TYPES OF DRILLS: TWIST DRILL -
Making a Cylindrical Mandrel on a Metal Lathe by John Huth, Lucas Pemberton and Greg Beckwith
Making a Cylindrical Mandrel on a Metal Lathe by John Huth, Lucas Pemberton and Greg Beckwith Sometimes our work quality and speed increases when thee lath bed true, it is possible to make a serviceable we have a mandrel that is precision-sized to the part we cylindrical mandrel by adding a follower rest to your are trying to repair. lathe carriage. The follower rest supports the stock as it is being cut, the contact point being quite close Shorter lengths of precision cylindrical mandrels (1/2” to the tool bit contact point. Since the follower rest is to 4 inch lengths) are easy to produce on a metal lathe. attached to the carriage, it naturally follows the tool bit Your set up is dependent upon the mandrel length: Our up the stock, ensuring a good, dimensionally consistent rule of thumb on set up is: if the stock you are cutting finished product. extends from the chuck less than 3X the diameter, no end support is required; when the stock extension from Here are some tips: the chuck exceeds three times the stock diameter, a live center is required. Without live center support two things can happen: 1. your stock will flex excessively resulting in an inconsistent dimension and finish, or 2. If spinning fast enough, your stock will become a serious danger as centrifugal force whips it into a right angled weapon that could tear flesh and/or break off as a • Make certain your tools are sharp. Dull tools greatly increase the forces causing deflection • For mandrels, we often cut soft standard steels such as 12L14 or 303 stainless steel • The follower rest needs to contact the stock only very.