Formulas for Calculating the Approach to Equilibrium in Open Channel Flash Evaporators for Saline Water
Total Page:16
File Type:pdf, Size:1020Kb
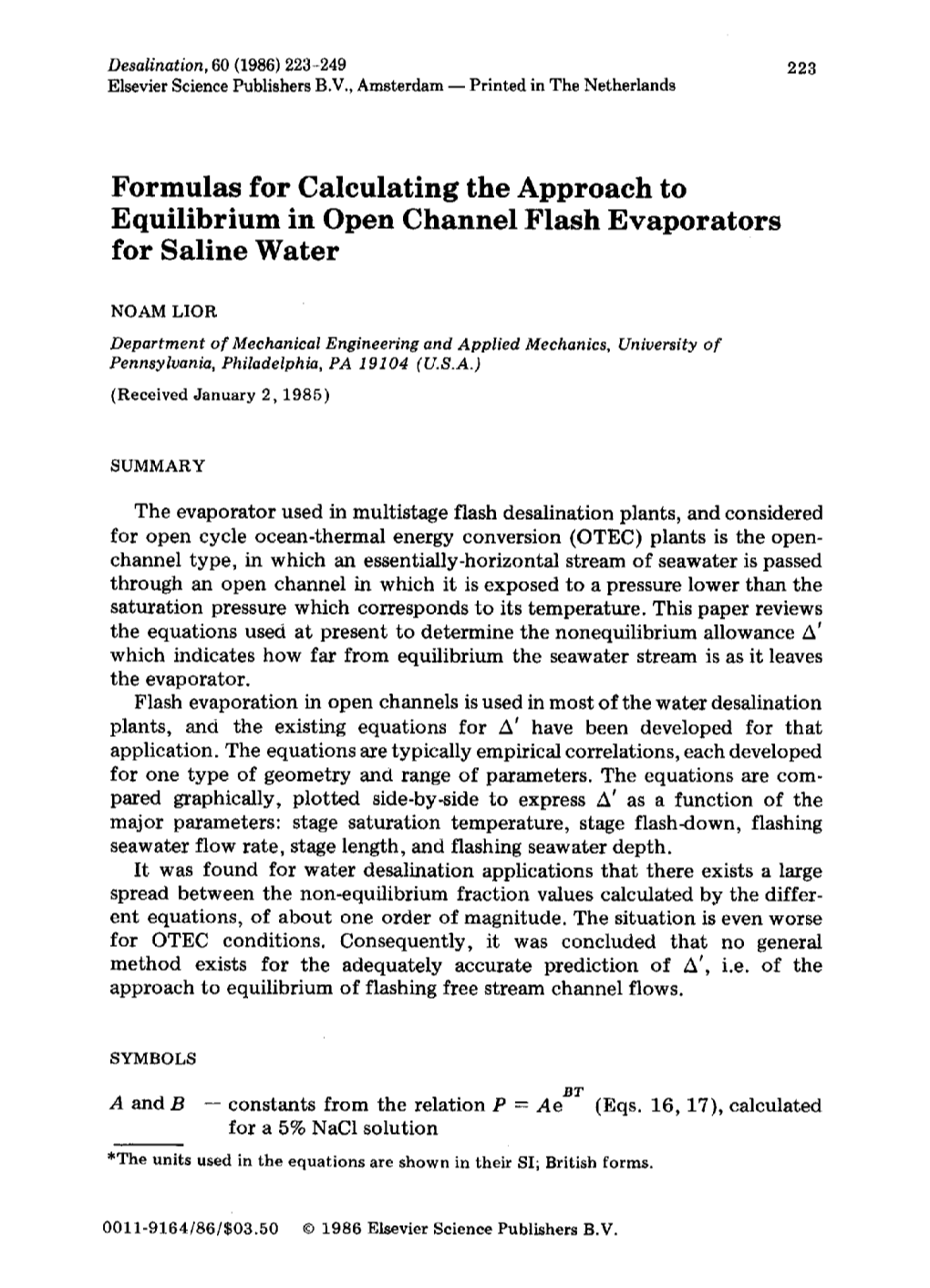
Load more
Recommended publications
-
Automobile Air Bag Inflation System Using Pressurized Carbon Dioxide Bart Adams New Jersey Institute of Technology
New Jersey Institute of Technology Digital Commons @ NJIT Dissertations Theses and Dissertations Spring 1998 Automobile air bag inflation system using pressurized carbon dioxide Bart Adams New Jersey Institute of Technology Follow this and additional works at: https://digitalcommons.njit.edu/dissertations Part of the Mechanical Engineering Commons Recommended Citation Adams, Bart, "Automobile air bag inflation system using pressurized carbon dioxide" (1998). Dissertations. 939. https://digitalcommons.njit.edu/dissertations/939 This Dissertation is brought to you for free and open access by the Theses and Dissertations at Digital Commons @ NJIT. It has been accepted for inclusion in Dissertations by an authorized administrator of Digital Commons @ NJIT. For more information, please contact [email protected]. Cprht Wrnn & trtn h prht l f th Untd Stt (tl , Untd Stt Cd vrn th n f phtp r thr rprdtn f prhtd trl. Undr rtn ndtn pfd n th l, lbrr nd rhv r thrzd t frnh phtp r thr rprdtn. On f th pfd ndtn tht th phtp r rprdtn nt t b “d fr n prp thr thn prvt td, hlrhp, r rrh. If , r rt fr, r ltr , phtp r rprdtn fr prp n x f “fr tht r b lbl fr prht nfrnnt, h ntttn rrv th rht t rf t pt pn rdr f, n t jdnt, flfllnt f th rdr ld nvlv vltn f prht l. l t: h thr rtn th prht hl th r Inttt f hnl rrv th rht t dtrbt th th r drttn rntn nt: If d nt h t prnt th p, thn lt “ fr: frt p t: lt p n th prnt dl rn h n tn lbrr h rvd f th prnl nfrtn nd ll ntr fr th pprvl p nd brphl th f th nd drttn n rdr t prtt th dntt f I rdt nd flt. -
Volatile Liquid Precursors for the Chemical Vapor Deposition (Cvd) of Thin Films Containing Tungsten
Mat. Res. Soc. Symp. Proc. Vol. 612 © 2000 Materials Research Society VOLATILE LIQUID PRECURSORS FOR THE CHEMICAL VAPOR DEPOSITION (CVD) OF THIN FILMS CONTAINING TUNGSTEN Roy G. Gordon, Seán Barry, Randy N. R. Broomhall-Dillard, Valerie A. Wagner and Ying Wang Department of Chemistry and Chemical Biology, Harvard University, Cambridge, MA 02138 ABSTRACT A new CVD process is described for depositing conformal layers containing tungsten, tungsten nitride or tungsten oxide. A film of tungsten metal is deposited by vaporizing liquid tungsten(0) pentacarbonyl 1-methylbutylisonitrile and passing the vapors over a surface heated to 400 to 500 oC. This process can be used to form gate electrodes compatible with ultrathin dielectric layers. Tungsten nitride films are deposited by combining ammonia gas with this tungsten-containing vapor and using substrates at temperatures of 250 to 400 oC. Tungsten nitride can act as a barrier to diffusion of copper in microelectronic circuits. Tungsten oxide films are deposited by adding oxygen gas to the tungsten-containing vapor and using substrates at temperatures of 200 to 300 oC. These tungsten oxide films can be used as part of electrochromic windows, mirrors or displays. Physical properties of several related liquid tungsten compounds are described. These low-viscosity liquids are stable to air and water. These new compounds have a number of advantages over tungsten-containing CVD precursors used previously. INTRODUCTION Chemical vapor deposition (CVD) is a widely-used process for forming solid materials, such as coatings, from reactants in the vapor phase. CVD processes can have many advantages: good step coverage, dense films, high deposition rates, scalability to larger areas and low cost. -
Bubble Growth in Superheated Solutions with a Non-Volatile Solute
Chemical Engineering Science, Vol. 49, No.9, pp. 1301- 1)12, 1994 Copyright tJ 1994 Elsevier Science Ltd Printed in Great Britain . All rights reserved 0009- 2509/94 $6.00 + 0.00 BUBBLE GROWTH IN SUPERHEATED SOLUTIONS WITH A NON-VOLATILE SOLUTE OSAMU MIYATAKE Department of Chemical Engineering, Kyushu University, Fukuoka 812, Japan ITSUO TANAKA Division of Biological Production System, Gifu University, Gifu 501-1 I, Japan and NOAM LIOR! Department of Mechanical Engineering and Applied Mechanics, University of Pennsylvania, Philadelphia, PA 19104-6315. U.SA (First received 30 April 1993; accepted in revised form 9 September 1993) Abstract-Growth of single bubbles in a uniformly superheated binary solution containing a non-volatile solute was studied both experimentally, using an aqueous solution of NaCI at mass fractions of 0.05 and 0.20, an initial temperature range of 40-80°C and an applied initial superheat range of 1.7-16.5°C, and theoretically, with very good agreement between the experimental and theoretical results. The experimental technique developed, using an electrolytically nucleated bubble, was found to be excellent for single-bubble growth studies and photography. Some of the principal conclusions are that increasing the concentration of the non-volatile solute at a given initial solution temperature reduces the bubble growth rate when the far-field pressure is dropped to a fixed value. The effect of concentration on the bubble growth rate becomes smaller when the far-field pressure is reduced to bring the solution to either a fixed superheat, or to a fixed initial pressure difference between the bubble interior and exterior, leading to a conclusion that it is preferable to study and correlate bubble growth rates by using the superheat and this pressure difference as parameters. -
Cooling Under Vacuum
Cooling under Vacuum GEA Wiegand GmbH Table of Contents Introduction Cooling is an expensive process. Ongoing increases in Introduction 2 energy costs demand alternatives to traditional systems Comparison between compression cooling plants (mechanical compressors). More and more, flash cooling and steam jet cooling plants 2 plants offer an environmentally friendly and economical solution. Steam Jet Cooling Plants – Construction Details GEA Wiegand has more than fifty years of experience in and How They Work 3 the design and construction of flash cooling plants. Advantages of flash cooling plants 3 Vapour compression using jet pumps 4 GEA Wiegand reference plants: Flash cooling 4 water Steam Jet Cooling Plants – Types 5 aqueous nitric acid/phosphoric acid Steam jet cooling plants of compact design 5 aqueous plaster suspension Steam jet cooling plants of column design 6 calcium milk Steam jet cooling plants of bridge design 7 barium hydroxide solutions Standardised steam jet cooling plants – sizes 8 various waste waters fruit juice Installation and Control 10 milk Possible combinations 10 glue Installation alternatives 11 Control of steam jet cooling plants 12 The steam jet cooling plants may have a capacity between Heat Recovery Plants 14 approximately 10 and 20 000 kilowatts. As an example, water may be cooled down to a temperature of approxi- Criteria for the Design mately 5 °C. of Steam Jet Cooling Plants 15 Comparison between compression cooling plants and steam jet cooling plants Type of cooling plant Compression cooling plant Steam -
Modelling and Optimisation of Multi-Stage Flash Distillation and Reverse Osmosis for Desalination of Saline Process Wastewater Sources
membranes Article Modelling and Optimisation of Multi-Stage Flash Distillation and Reverse Osmosis for Desalination of Saline Process Wastewater Sources Andras Jozsef Toth 1,2 1 Environmental and Process Engineering Research Group, Department of Chemical and Environmental Process Engineering, Budapest University of Technology and Economics, M˝uegyetemrkp. 3, H-1111 Budapest, Hungary; [email protected]; Tel.: +36-1-463-1490 2 Institute of Chemistry, University of Miskolc, Egyetemváros C/1 108, H-3515 Miskolc, Hungary Received: 9 August 2020; Accepted: 27 September 2020; Published: 28 September 2020 Abstract: Nowadays, there is increasing interest in advanced simulation methods for desalination. The two most common desalination methods are multi-stage flash distillation (MSF) and reverse osmosis (RO). Numerous research works have been published on these separations, however their simulation appears to be difficult due to their complexity, therefore continuous improvement is required. The RO, in particular, is difficult to model, because the liquids to be separated also depend specifically on the membrane material. The aim of this study is to model steady-state desalination opportunities of saline process wastewater in flowsheet environment. Commercial flowsheet simulator programs were investigated: ChemCAD for thermal desalination and WAVE program for membrane separation. The calculation of the developed MSF model was verified based on industrial data. It can be stated that both simulators are capable of reducing saline content from 4.5 V/V% to 0.05 V/V%. The simulation results are in accordance with the expectations: MSF has higher yield, but reverse osmosis is simpler process with lower energy demand. The main additional value of the research lies in the comparison of desalination modelling in widely commercially available computer programs. -
Flash Evaporation Flashing Atomization Can Occur in Liquids
Flash Evaporation experimental apparatus consists of a high pressure Flashing atomization can occur in liquids subjected tank feeding high pressure and high temperature to sudden pressure drop or sufficient superheating water to the nozzle, the liquid collecting vessel, high which leads to formation of vapor bubbles inside the speed camera and the measuring instruments at liquid. Rapid growth of bubbles is the cause of the different location of the system. The pressure is explosion of the bubble and generation of finer generated by the air above the liquid level in the tank droplets and spray. Therefore, this phenomena has which is pressurized by air pressure amplifier. This direct effect on the droplet formation and size as well apparatus, under controlled pressure and temperature as general shape of the spray. can generate a good simulation of flash evaporation In splash plate nozzles due to the high temperature in the actual splash plate nozzle. Measuring the size and pressure flashing is so likely to occur and affect and distribution of the droplets will be performed by the performance of the recovery craft boiler means of the camera and analyzing the pictures dramatically. obtained from different tests. This study is going to explore the flashing To predict the characteristics of the sheet in different evaporation in splash plate nozzles in analytical, circumstances, a theoretical approach will be experimental, and numerical ways. Studying the constructed based on theories existing in the theory and published research works related to this literature. The theory and its agreement with the area is the first step. The unknowns of the study are experimental results can enhance the legitimacy of flashing type in this nozzles, evaporation ratio, effect the results and conclusions of the study and hence a of flashing on droplet formation, size and critical step to attain the goal of the study. -
Modeling of Flash Boiling Flows in Injectors with Gasoline-Ethanol Fuel Blends
University of Massachusetts Amherst ScholarWorks@UMass Amherst Open Access Dissertations 2-2011 Modeling of Flash Boiling Flows in Injectors with Gasoline-Ethanol Fuel Blends Kshitij Deepak Neroorkar University of Massachusetts Amherst Follow this and additional works at: https://scholarworks.umass.edu/open_access_dissertations Part of the Mechanical Engineering Commons Recommended Citation Neroorkar, Kshitij Deepak, "Modeling of Flash Boiling Flows in Injectors with Gasoline-Ethanol Fuel Blends" (2011). Open Access Dissertations. 338. https://scholarworks.umass.edu/open_access_dissertations/338 This Open Access Dissertation is brought to you for free and open access by ScholarWorks@UMass Amherst. It has been accepted for inclusion in Open Access Dissertations by an authorized administrator of ScholarWorks@UMass Amherst. For more information, please contact [email protected]. MODELING OF FLASH BOILING FLOWS IN INJECTORS WITH GASOLINE-ETHANOL FUEL BLENDS A Dissertation Presented by KSHITIJ NEROORKAR Submitted to the Graduate School of the University of Massachusetts Amherst in partial fulfillment of the requirements for the degree of DOCTOR OF PHILOSOPHY February 2011 Mechanical and Industrial Engineering c Copyright by Kshitij Neroorkar 2011 All Rights Reserved MODELING OF FLASH BOILING FLOWS IN INJECTORS WITH GASOLINE-ETHANOL FUEL BLENDS A Dissertation Presented by KSHITIJ NEROORKAR Approved as to style and content by: David P. Schmidt, Chair Stephen de Bruyn Kops, Member Michael Henson, Member Ronald O. Grover, Jr., Member Donald Fisher, Department Head Mechanical and Industrial Engineering To my lovely family ACKNOWLEDGMENTS I would like to thank my advisor Prof. David Schmidt for his guidance and support during the course of this PhD. He has always given the highest priority to the development of his students’ careers, for which I will always be grateful. -
Introduction to Chemical Engineering for Lecture 7: Flash Distillation
Introduction to Chemical Engineering for Lecture 7: Flash Distillation Martin Iggland, Marco Mazzotti∗ ETH Zurich, Institute of Process Engineering, Sonneggstrasse 3, CH-8092 Zurich, Switzerland 1. Flash distillation Flash evaporation is one of the simplest separation processes. A liquid stream containing several components is partially vaporised in a ”flash drum" at a certain pressure and temperature. This results in two phases: a vapor phase, enriched in the more volatile components, and a liquid phase, enriched in the less volatile components. The fluid is pressurized and heated and is then passed through a throttling valve or nozzle into the flash drum. Because of the large drop in pressure, part of the fluid vaporizes. The vapor is taken off overhead, while the liquid drains to the bottom of the drum, where it is withdrawn. The system is called ”flash” distillation because the vaporization is extremely rapid after the feed enters the drum. Because of the intimate contact between liquid and vapor, the system in the flash chamber is very close to an equilibrium stage. Figure 1 shows a schematic drawing of a flash unit. As long as the feed consists of only 2 components, we have a binary flash. We will consider this case first, then we will see how to calculate bubble- and dew-points of binary mixtures. Further reading for this part of the lecture can ∗Corresponding author: phone +41 44 632 2456; fax +41 44 632 11 41. Email address: [email protected] (Marco Mazzotti) Preprint submitted to Script SS 2015 Figure 1: Schematic drawing of a flash distillation unit be found in chapter 2 of Wankat's "Separation Process Engineering" 1. -
Mathematical Modelling of Heat Exchange in Flash Tank Heat Exchanger Cascades
Mathematics-in-Industry Case Studies Journal, Volume 5, pp. 43-58 (2013) Mathematical modelling of heat exchange in flash tank heat exchanger cascades Andrei Korobeinikov ∗ John McCarthy y Emma Mooney z Krum Semkov x James Varghese { Abstract. Flash tank evaporation combined with a condensing heat ex- changer can be used when heat exchange is required between two streams, where at least one of these streams is difficult to handle (tends severely to scale, foul, causing blockages). To increase the efficiency of heat exchange, a cascade of these units in series can be used. Heat transfer relationships in such a cascade are very complex due to their interconnectivity; thus the impact of any changes proposed is difficult to predict. Moreover, the distribution of loads and driving forces at different stages and the number of designed stages faces tradeoffs which require fundamental understanding and balances. This paper addresses these problems, offering a mathematical model of a single unit composed of a flash tank evaporator combined with a condensing heat exchanger. This model is then extended for a chain of such units. The pur- pose of this model is an accurate study of the factors influencing efficiency of the system (maximizing heat recovery) and evaluation of the impact of an alteration of the system, thus allowing for guided design of new or redesign of existing systems. Keywords. Heat exchange, alumina production, the Bayer process, energy efficiency, energy management ∗Centre de Recerca Matematica, Campus de Bellaterra, Edifici C, 08193 Bellaterra, Barcelona, Spain. ako- [email protected] yMathematics Department, Box 1146, Washington University, St. Louis, MO 63130, USA. -
A Simulation Model of Spray Flash Desalination System
Proceedings of the 17th World Congress The International Federation of Automatic Control Seoul, Korea, July 6-11, 2008 A Simulation Model of Spray Flash Desalination System Satoru Goto ∗ Yuji Yamamoto ∗ Takenao Sugi ∗∗ Takeshi Yasunaga ∗∗Yasuyuki Ikegami ∗∗Masatoshi Nakamura ∗ ∗ Department of Advanced Systems Control Engineering, Saga University Honjomachi, Saga 840-8502, Japan (Tel: +81-952-28-8643; Fax: +81-952-28-8666; e-mail: [email protected]) ∗∗ Institute of Ocean Energy, Saga University Honjomachi, Saga 840-8502, Japan Abstract: In this paper, a simulation model of a spray flash desalination system is proposed. In the spray flash desalination system, the freshwater is made from the evaporation-condensation process, i.e., evaporation of warm surface seawater in a flash chamber and condensation of the generated vapor by deep cool seawater. A simulation model of the spray flash desalination system is constructed by using physical relations such as the energy conservation law and the mass conservation law. Simulation results of the proposed simulation model are compared with the experimental results of an experimental plant of the splay flash desalination system, and it shows the effectiveness of the proposed simulation model. Keywords: spray flash; desalination system; simulation model; mass conservation law; energy conservation law 1. INTRODUCTION by using the spray flash evaporation. Since the spray flash desalination method can be generated freshwater with small temperature differences, the performance analysis of the hybrid Water issue is a serious problem in the world because of the cycle with Ocean Thermal Energy Conversion (OTEC) has influence of the rapid increase in population, global warming, been examined. -
Research Progresses of Flash Evaporation in Aerospace Applications
Hindawi International Journal of Aerospace Engineering Volume 2018, Article ID 3686802, 15 pages https://doi.org/10.1155/2018/3686802 Review Article Research Progresses of Flash Evaporation in Aerospace Applications Wei Ma,1 Siping Zhai,2 Ping Zhang ,2 Yaoqi Xian,2 Lina Zhang,1 Rui Shi,1 Jiang Sheng,1 Bo Liu,1 and Zonglin Wu1 1Science and Technology on Space Physics Laboratory, Beijing 100076, China 2School of Mechanical and Electrical Engineering, Guilin University of Electronic Technology, Guilin 541004, China Correspondence should be addressed to Ping Zhang; [email protected] Received 7 June 2018; Accepted 10 October 2018; Published 17 December 2018 Academic Editor: André Cavalieri Copyright © 2018 Wei Ma et al. This is an open access article distributed under the Creative Commons Attribution License, which permits unrestricted use, distribution, and reproduction in any medium, provided the original work is properly cited. Liquid is overheated and evaporated quickly when it enters into the environment with lower saturation pressure than that corresponding to its initial temperature. This phenomenon is known as the flash evaporation. A natural low-pressure environment and flash evaporation have unique characteristics and superiority in high altitude and outer space. Therefore, flash evaporation is widely used in aerospace. In this paper, spray flash evaporation and jet flash evaporation which are two different forms were introduced. Later, key attentions were paid to applications of flash evaporation in aerospace. For example, the flash evaporation has been used in the thermal control system of an aircraft and the propelling system of a microsatellite and oil supply system of a rocket motor. -
Energy Management Through Condensate and Flash Steam Recovery Systems
ENERGY MANAGEMENT THROUGH CONDENSATE AND FLASH STEAM RECOVERY SYSTEMS. A CASE STUDY OF NZOIA SUGAR COMPANY. SOLOMON B. AMWAYI1 (B. Tech. Chemical & Process Engineering) 1Production Department, Nzoia Sugar Co. Ltd, Box 285Bungoma-Kenya Correspondent author Email: [email protected] or [email protected] Tel: +254721808663 ABSTRACT. Condensate and flash steam recovery system is one of the most crucial energy management systems in any industry. Globally, there has been a push for green energy consumption and conservation. The cost of steam rises with the increase in energy prices and so does the value of condensate. This recovery system has been applied by Nzoia Sugar Company in a continuous energy management improvement strategy. The aim is to reduce the three tangible costs of producing steam: fuel/energy costs, Boiler water make-up & sewage treatment, and lastly, boiler water chemical treatment. The steam and condensate system flow diagram was used to undertake the mass and energy balances to determine the amount of energy savings realized. The thermodynamic calculations were applied to determine the energy requirement and savings for the entire system.There has been great energy savings from this system amounting to 201470498KJ. The amount of condensate recovered is at 158430.22 Kg/Hr with heat energy of 59936.1884 KJ. Recommendations made if well adopted would reduce heat losses from the current 5% to 2% or below in the foreseeable future. Key word: Condensate, Flash steam, Heat energy savings 1 1.0 INTRODUCTION. Energy management includes planning and operation of energy-related production and consumption units. This is spearheaded by resource conservation, climate protection and cost savings, while the users have permanent access to the energy they need.