Thz Tomography and Image Processing: a New Tool for Polymer and Ceramic Additive Manufacturing Quality Control
Total Page:16
File Type:pdf, Size:1020Kb
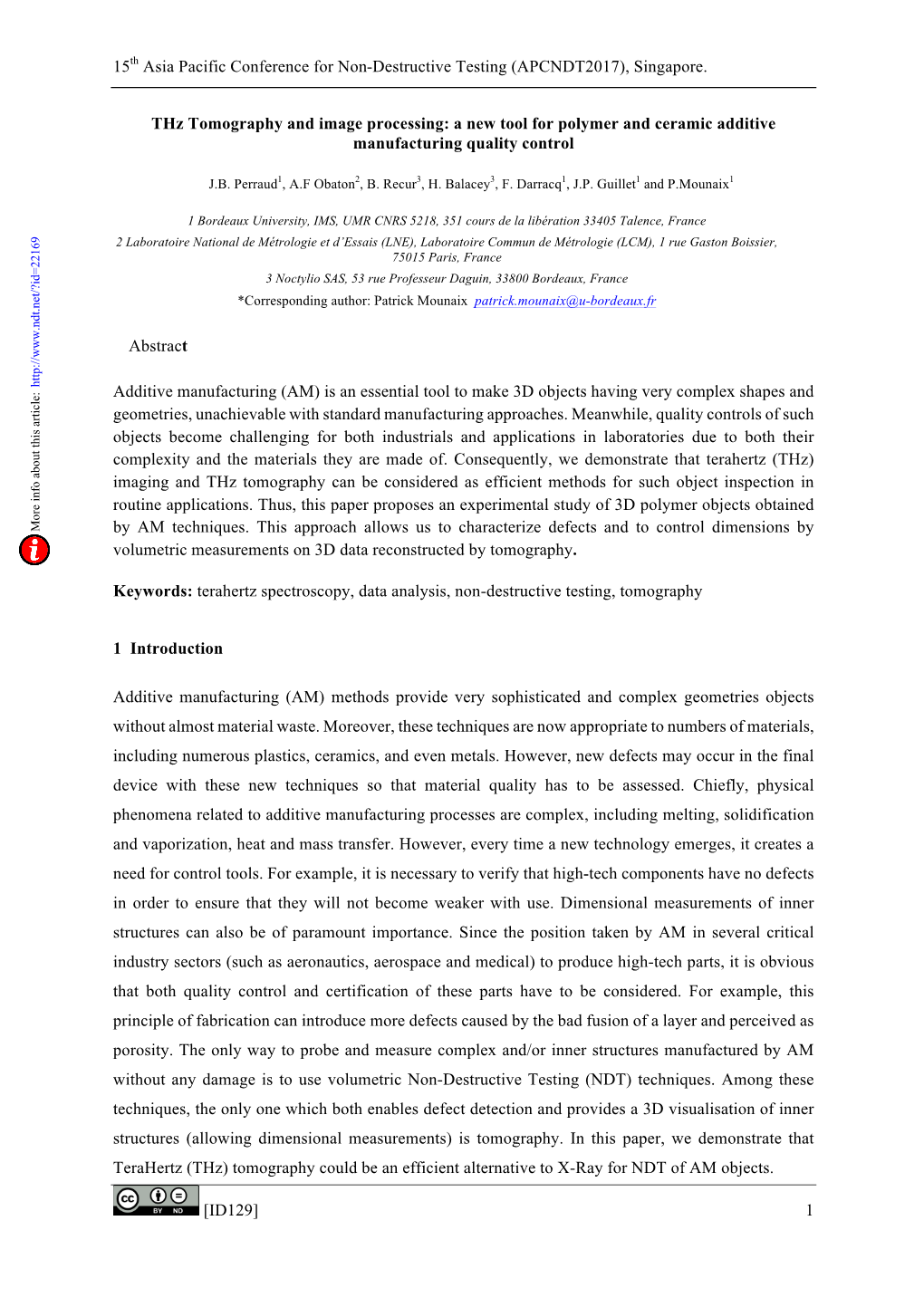
Load more
Recommended publications
-
Non-Destructive Evaluation of Aerospace Composites
Air Force Institute of Technology AFIT Scholar Theses and Dissertations Student Graduate Works 3-9-2009 Non-Destructive Evaluation of Aerospace Composites Jeremy D. Johnson Follow this and additional works at: https://scholar.afit.edu/etd Part of the Materials Science and Engineering Commons, and the Structures and Materials Commons Recommended Citation Johnson, Jeremy D., "Non-Destructive Evaluation of Aerospace Composites" (2009). Theses and Dissertations. 2450. https://scholar.afit.edu/etd/2450 This Thesis is brought to you for free and open access by the Student Graduate Works at AFIT Scholar. It has been accepted for inclusion in Theses and Dissertations by an authorized administrator of AFIT Scholar. For more information, please contact [email protected]. NON-DESTRUCTIVE EVALUATION OF AEROSPACE COMPOSITES THESIS Jeremy D. Johnson, Captain, USAF AFIT/GMS/ENP/09-M02 DEPARTMENT OF THE AIR FORCE AIR UNIVERSITY AIR FORCE INSTITUTE OF TECHNOLOGY Wright-Patterson Air Force Base, Ohio APPROVED FOR PUBLIC RELEASE; DISTRIBUTION UNLIMITED The views expressed in this thesis are those of the author and do not reflect the official policy or position of the United States Air Force, Department of Defense, or the United States Government. AFIT/GMS/ENP/09-M02 NON-DESTRUCTIVE EVALUATION OF AEROSPACE COMPOSITES THESIS Presented to the Faculty Department of Engineering Physics Graduate School of Engineering and Management Air Force Institute of Technology Air University Air Education and Training Command In Partial Fulfillment of the Requirements for the Degree of Master of Science in Materials Science Jeremy D. Johnson, BS Captain, USAF March 2009 APPROVED FOR PUBLIC RELEASE; DISTRIBUTION UNLIMITED AFIT/GMS/ENP/09-M02 NON-DESTRUCTIVE EVALUATION OF AEROSPACE COMPOSITES Jeremy D. -
Commercializing of Terahertz Imaging for Micro/Nano Scientific and Industrial Applications Dr
Commercializing of Terahertz Imaging for Micro/Nano Scientific and Industrial Applications Dr. Donald D Arnone1 1. TeraView Ltd, Cambridge UK Terahertz lies between the microwave and infrared regions of the electromagnetic spectrum. Until recently, this portion of the spectrum has been inaccessible due to lack of nanoscale sources and sensitive detectors. Terahertz light 1) passes through many common materials, 2) is non-destructive & non-invasive, and 3) is non ionizing, and hence safe. It is therefore an excellent tool for non- destructive characterization of many novel material systems. TeraView has been at the forefront of the development and commercialization of this technology. An important aspect of the commercialization of the technology has been transitioning R&D developments into systems compatible with the production line. A key challenge for TeraView in the commercialization process has been the need to simultaneously develop both products (including the associated hardware and software) as well as lucrative market applications for Terahertz. Coatings and delamination in pharmaceutical tablets, multi-paint layers on cars and faults in semiconductors are all examples of where the technology is currently being employed by industrial end-users. Non- destructive testing of materials such as glass fibre re-enforced composites, thin film nano-materials, ferroelectrics and other functional materials represent future applications. Identifying the most lucrative opportunities from the above list via work with lead customers has been a key activity within the Company. Optimising the actual product (via hardware and software modules) with customer support has also been key to success. Case studies involving work with the pharmaceutical, semiconductor, solar, security and automotive industries will be presented to illustrate these challenges. -
Nanodevices for Thz Applications
Nanodevices for THz Applications Tomás González University of Salamanca, Spain Research Group on Semiconductor Devices THz Nanodevices at USAL Research Group on Semiconductor Devices - Modeling of nanodevices for THz applications - Design of optimized structures (feedback to technology) THz Laboratory - Detection and emission of THz radiation from plasma wave nanodevices - Time-domain spectroscopy and imaging in the THz range T. González - Nanodevices for THz Applications December 12, 2012 Research Group on Semiconductor Devices http://campus.usal.es/~gelec/ CONTACT: Prof. Tomás González ([email protected]) Staff: 8 permanent researchers, 3 post-doc, 2 students Collaborations with several EU (IEMN, Chalmers, Manchester, Montpellier, etc.) and USA Labs. (Rochester) Monte Carlo simulation of high-frequency nanodevices InGaAs/InAlAs, InAs/AlSb and GaN/AlGaN HEMTs RESEARCH LINES (FP6 project METAMOS) Advanced Si MOSFETs InGaAs based THz ballistic nanodevices (FP5 project NANOTERA ) 100nm TBJs YBJs MUX/DEMUX SSDs Coordinator of the FP7 STREP Project ROOTHz (FP7-243845) Characterization Laboratory (DC-GHz) Semiconductor Nanodevices for Room Temperature THz Emission and Detection - http://www.roothz.eu/ GaN diodes InGaAs/InAlAs diode Research Group on Semiconductor Devices EQUIPMENT Computer Clusters Probe station (Cascade M150) Keithley 4200: DC and pulsed VNA Agilent PNA-X: measurements (Keithley 4225) RF measurements up to 43.5 GHz THz Laboratory Contact: Dr. Yahya Meziani ([email protected]) Plasma-wave nanodevices A glimpse of the considered -
Calculation and Study of Graphene Conductivity Based on Terahertz Spectroscopy
J Infrared Milli Terahz Waves DOI 10.1007/s10762-017-0362-5 Calculation and Study of Graphene Conductivity Based on Terahertz Spectroscopy Xiaodong Feng1 & Min Hu 1 & Jun Zhou 1 & Shenggang Liu 1 Received: 4 December 2016 /Accepted: 22 January 2017 # Springer Science+Business Media New York 2017 Abstract Based on terahertz time-domain spectroscopy system and two-dimensional scan- ning control system, terahertz transmission and reflection intensity mapping images on a graphene film are obtained, respectively. Then, graphene conductivity mapping images in the frequency range 0.5 to 2.5 THz are acquired according to the calculation formula. The conductivity of graphene at some typical regions is fitted by Drude-Smith formula to quanti- tatively compare the transmission and reflection measurements. The results show that terahertz reflection spectroscopy has a higher signal-to-noise ratio with less interference of impurities on the back of substrates. The effect of a red laser excitation on the graphene conductivity by terahertz time-domain transmission spectroscopy is also studied. The results show that the graphene conductivity in the excitation region is enhanced while that in the adjacent area is weakened which indicates carriers transport in graphene under laser excitation. This paper can make great contribution to the study on graphene electrical and optical properties in the terahertz regime and help design graphene terahertz devices. Keywords Graphene conductivity. Terahertz spectroscopy. Drude-Smith formula . Laser excitation 1 Introduction Terahertz (THz) radiation with frequencies typically from 0.1 to 30 THz, which occupies a middle ground between microwaves and infrared waves, is becoming a hot topic in the world [1–5]. -
Review of Terahertz Pulsed Imaging for Pharmaceutical Film Coating Analysis
sensors Review Review of Terahertz Pulsed Imaging for Pharmaceutical Film Coating Analysis Décio Alves-Lima 1, Jun Song 1,2, Xiaoran Li 1, Alessia Portieri 3, Yaochun Shen 4 , J. Axel Zeitler 5 and Hungyen Lin 1,* 1 Department of Engineering, Lancaster University, Lancaster LA1 4YW, UK; [email protected] (D.A.-L.); [email protected] (J.S.); [email protected] (X.L.) 2 Department of Information Science, Nanjing Forestry University, Nanjing 210037, Jiangsu, China 3 TeraView Ltd., 1, Enterprise Cambridge Research Park, Cambridge CB25 9PD, UK; [email protected] 4 Department of Electrical Engineering and Electronics, University of Liverpool, Liverpool L69 3GJ, UK; [email protected] 5 Department of Chemical Engineering and Biotechnology, University of Cambridge, Philippa Fawcett Drive, Cambridge CB3 0AS, UK; [email protected] * Correspondence: [email protected] Received: 29 January 2020; Accepted: 2 March 2020; Published: 6 March 2020 Abstract: Terahertz pulsed imaging (TPI) was introduced approximately fifteen years ago and has attracted a lot of interest in the pharmaceutical industry as a fast, non-destructive modality for quantifying film coatings on pharmaceutical dosage forms. In this topical review, we look back at the use of TPI for analysing pharmaceutical film coatings, highlighting the main contributions made and outlining the key challenges ahead. Keywords: film coatings; TPI; terahertz; characterization 1. Introduction In pharmaceutical manufacturing, film coating on solid oral dosage forms, especially for tablets, is typically performed as the last steps of secondary manufacturing value chain. Coatings are usually applied to cores such as tablets or pellets and in some cases small particles such as crystals. -
Passively Tunable Terahertz Filters Using Liquid Crystal Cells Coated with Metamaterials
coatings Article Passively Tunable Terahertz Filters Using Liquid Crystal Cells Coated with Metamaterials Wei-Fan Chiang 1, Yu-Yun Lu 2, Yin-Pei Chen 2, Xin-Yu Lin 2, Tsong-Shin Lim 2, Jih-Hsin Liu 3, Chia-Rong Lee 1,* and Chia-Yi Huang 2,* 1 Department of Photonics, National Cheng Kung University, Tainan 70101, Taiwan; [email protected] 2 Department of Applied Physics, Tunghai University, Taichung 40704, Taiwan; [email protected] (Y.-Y.L.); [email protected] (Y.-P.C.); [email protected] (X.-Y.L.); [email protected] (T.-S.L.) 3 Department of Electrical Engineering, Tunghai University, Taichung 40704, Taiwan; [email protected] * Correspondence: [email protected] (C.-R.L.); [email protected] (C.-Y.H.) Abstract: Liquid crystal (LC) cells that are coated with metamaterials are fabricated in this work. The LC directors in the cells are aligned by rubbed polyimide layers, and make angles q of 0◦, 45◦, and 90◦ with respect to the gaps of the split-ring resonators (SRRs) of the metamaterials. Experimental results display that the resonance frequencies of the metamaterials in these cells increase with an increase in q, and the cells have a maximum frequency shifting region of 18 GHz. Simulated results reveal that the increase in the resonance frequencies arises from the birefringence of the LC, and the LC has a birefringence of 0.15 in the terahertz region. The resonance frequencies of the metamaterials are shifted by the rubbing directions of the polyimide layers, so the LC cells coated with the metamaterials are passively tunable terahertz filters. -
Terahertz Light Is Solving Real-World Issues
TERAVIEW Terahertz light is solving real-world issues... The Low Carbon Innovation Fund, managed by Turquoise, first invested in TeraView in December 2011. Turquoise’s Kevin Murphy was initially a board observer and was appointed a non-executive director of TeraView in July 2015. In this whitepaper, we interview Don Arnone, CEO of TeraView, who explains the benefits of applying the company’s terahertz light technology to industrial applications in the semiconductor, automotive, pharma and other industries. Originally a spin-out from Toshiba, TeraView is a world-leader in using terahertz wavelength light to scan for defects and achieve efficiencies in the production of silicon cell ingots, application of paint to cars and coating of tablets. The company is seeking to establish terahertz light as a widely-used scanning technology alongside x-ray and infrared. Kevin Murphy Director Founded in 2001, TeraView’s journey has been a long one, reflecting Turquoise International the challenges of introducing novel technology into industrial manufacturing processes. Today, the company’s shareholders include To talk to me about Samsung and Nordson Dage, both of whom are seeking to broaden the issues raised in the deployment of TeraView’s products within their organisations, and this article, feel free Low Carbon Innovation Fund which backs companies developing to contact me via email clean technologies. Headquartered in Cambridge, UK, and with [email protected] or call offices in Korea and California, TeraView employs 35 people including me on 020 7248 1506 scientific experts such as CTO Professor Sir Michael Pepper. 1 Turquoise White Paper - November 2018 TeraView Terahertz light is solving real-world production issues – and it’s just the beginning Don Arnone Don Arnone, CEO at TeraView, discusses the huge potential CEO that terahertz light offers for imaging, identifying and analysing TeraView materials, both now and in the future. -
Thz Pulsed Imaging in Biomedical Applications
Review THz Pulsed Imaging in Biomedical Applications Annalisa D’Arco 1,* , Marta Di Fabrizio 2 , Valerio Dolci 1,2,3, Massimo Petrarca 1,3 and Stefano Lupi 2,4 1 INFN-Section of Rome ‘La Sapienza’, P.le Aldo Moro 2, 00185 Rome, Italy; [email protected] (V.D.); [email protected] (M.P.) 2 Physics Department, University of Rome ‘La Sapienza’, Piazzale Aldo Moro 5, 00185 Rome, Italy; [email protected] (M.D.F.); [email protected] (S.L.) 3 SBAI-Department of Basic and Applied Sciences for Engineering, Physics, University of Rome ‘La Sapienza’, Via Scarpa 16, 00161 Rome, Italy 4 INFN-LNF Via E. Fermi 40, 00044 Frascati, Italy * Correspondence: [email protected] Received: 13 December 2019; Accepted: 24 March 2020; Published: 1 April 2020 Abstract: Recent advances in technology have allowed the production and the coherent detection of sub-ps pulses of terahertz (THz) radiation. Therefore, the potentialities of this technique have been readily recognized for THz spectroscopy and imaging in biomedicine. In particular, THz pulsed imaging (TPI) has rapidly increased its applications in the last decade. In this paper, we present a short review of TPI, discussing its basic principles and performances, and its state-of-the-art applications on biomedical systems. Keywords: terahertz spectroscopy; terahertz time-domain spectroscopy; terahertz pulsed imaging; near-field imaging; biomedical imaging; cancer diagnosis; endoscopy 1. Introduction The increasing request for diagnosis techniques in the biomedical area, able to provide morphological, chemical and/or functional information for early, noninvasive and label-free detection, has led to hard cooperation in different scientific fields. -
Homeland Security, Medical, Pharmaceutical and Non-Destructive Testing Applications of Terahertz Radiation
Applications of THz Radiation – APS March Meeting, March 23, 2005 Homeland Security, Medical, Pharmaceutical and Non-destructive Testing Applications of Terahertz Radiation Colin Baker [email protected] [email protected] Overview z Introduction to terahertz z Techniques – imaging and spectroscopy z Applications of terahertz light Medical Non-destructive testing Pharmaceutical Security z Conclusions TeraView The Terahertz Company • Founded April 2001 Cambridge, England • Exclusive focus on terahertz technology and applications – 30+ staff • Close relationship with Cavendish Laboratory, Cambridge University • Developed world’s first portable terahertz imager & spectrometer • Focus markets medical imaging, pharmaceuticals, security screening, non-destructive testing TeraView’s TPI range What is Terahertz? Micro- Ultra- Infra- Terahertz Milli- wave and X Ray violet Visible metre red gap Radio 1019Hz 1018Hz 1017Hz 1016Hz 1015Hz 1014Hz 1013Hz 1012Hz 1011Hz 1010Hz • Terahertz region 300 GHz – 10 THz (1 mm – 30 micron) • Until recently – inaccessible due to lack of sources and detectors • Key properties: z Penetrates clothing, leather, paper, plastics, packing materials z Materials identification using characteristic Terahertz spectra z 3-D imaging capability z Non-ionizing - no damage to body or cells Photoconductive THz generation V bias GaAs device 90 fs NIR laser pulse Emitted THz pulse Photoconductive THz detection I GaAs device 90 fs NIR laser pulse THz pulse Basics of THz Pulsed Imaging • TPI provides for time of flight analysis, as well as producing spectral information. • A proportion of the incident pulse will be reflected back whenever there is a change in the refractive index. • Reconstruction of the multiple detected pulses permits depth profiling. X-Y raster scanning builds a 3D image. -
Electronic Device Failure Analysis a Resource for Technical Information and Industry Developments 2015 Winners
NOVEMBER 2016 | VOLUME 18 | ISSUE 4 edfas.org ELECTRONIC DEVICE FAILURE ANALYSIS A RESOURCE FOR TECHNICAL INFORMATION AND INDUSTRY DEVELOPMENTS 2015 WINNERS a b c d e f SUPERCONDUCTING SINGLE-PHOTON LVI AND LVP APPLICATIONS IN IN-LINE SCAN CHAIN FAILURE ANALYSIS DETECTOR ENABLES TIME-RESOLVED EMISSION TESTING OF LOW-VOLTAGE SCALED ICs EMERGING TECHNIQUES FOR 2-D/2.5-D/ 3-D TECHNOLOGY: FAILURE ANALYSIS 3-D PACKAGE FAILURE ANALYSIS: EOTPR, 3-D X-RAY, AND PLASMA FIB NOVEMBER 2016 | VOLUME 18 | ISSUE 4 edfas.org ELECTRONIC DEVICE FAILURE ANALYSIS A RESOURCE FOR TECHNICAL INFORMATION AND INDUSTRY DEVELOPMENTS 2015 WINNERS PAGE 59 a b c d e f SUPERCONDUCTING SINGLE-PHOTON LVI AND LVP APPLICATIONS IN IN-LINE DETECTOR ENABLES TIME-RESOLVED 4 SCAN CHAIN FAILURE ANALYSIS 16 EMISSION TESTING OF LOW-VOLTAGE SCALED ICs EMERGING TECHNIQUES FOR 2-D/2.5-D/ 3-D TECHNOLOGY: FAILURE ANALYSIS 3-D PACKAGE FAILURE ANALYSIS: EOTPR, 24 CHALLENGES 30 3-D X-RAY, AND PLASMA FIB 1 NOVEMBER 2016 | VOLUME 18 | ISSUE 4 edfas.org ELECTRONIC DEVICE ANALYSIS DEVICE FAILURE ELECTRONIC FAILURE ANALYSIS A RESOURCE FOR TECHNICAL INFORMATION AND INDUSTRY DEVELOPMENTS 4 LVI and LVP Applications in In-Line Scan Chain Failure Analysis Zhigang Song and Laura Safran This article discusses the combination of laser voltage imaging and laser voltage probing to improve the failure 4 16 analysis success rate for in-line scan chain logic macro diagnosis. 4 NO. 18 VOLUME | 16 Superconducting Single-Photon Detector Enables Time-Resolved Emission Testing of Low-Voltage Scaled ICs Andrea Bahgat Shehata, Franco Stellari, and Peilin Song Time-resolved optical probing techniques remain an indis- pensable tool for increasing fault localization speed and accuracy. -
Terahertz Time Domain Spectroscopy and Fresnel Coefficient Based Predictive Model
Wright State University CORE Scholar Browse all Theses and Dissertations Theses and Dissertations 2012 Terahertz Time Domain Spectroscopy and Fresnel Coefficient Based Predictive Model Justin C. Wheatcroft Wright State University Follow this and additional works at: https://corescholar.libraries.wright.edu/etd_all Part of the Physics Commons Repository Citation Wheatcroft, Justin C., "Terahertz Time Domain Spectroscopy and Fresnel Coefficient Based edictivPr e Model" (2012). Browse all Theses and Dissertations. 623. https://corescholar.libraries.wright.edu/etd_all/623 This Thesis is brought to you for free and open access by the Theses and Dissertations at CORE Scholar. It has been accepted for inclusion in Browse all Theses and Dissertations by an authorized administrator of CORE Scholar. For more information, please contact [email protected]. TERAHERTZ TIME-DOMAIN SPECTROSCOPY AND FRESNEL COEFFICIENT BASED PREDICTIVE MODEL A thesis submitted in partial fulfillment of the requirements for the degree of Master of Science By JUSTIN C. WHEATCROFT B.S., Kent State University, 2009 2012 Wright State University WRIGHT STATE UNIVERSITY GRADUATE SCHOOL August 31, 2012 I HEREBY RECOMMEND THAT THE THESIS PREPARED UNDER MY SUPERVISION BY Justin C. Wheatcroft ENTITLED Terahertz time domain spectroscopy and Fresnel coefficient based predictive model BE ACCEPTED IN PARTIAL FULFILLMENT OF THE REQUIREMENTS FOR THE DEGREE OF Master of Science. ________________________________ Jason A. Deibel, Ph.D. Thesis Director ________________________________ Committee on Final Examination Douglas T. Petkie, Ph.D. Chair, Department of Physics ________________________________ Jason A. Deibel, Ph.D. ________________________________ Douglas T. Petkie, Ph.D. ________________________________ Gregory Kozlowski, Ph.D. ________________________________ Andrew Hsu, Ph.D. Dean, Graduate School ABSTRACT Wheatcroft, Justin C. -
Characterization of Ceramic Composite Materials Using Terahertz Non-Destructive Evaluation Techniques
Wright State University CORE Scholar Browse all Theses and Dissertations Theses and Dissertations 2012 Characterization of Ceramic Composite Materials Using Terahertz Non-Destructive Evaluation Techniques Lindsay Owens Wright State University Follow this and additional works at: https://corescholar.libraries.wright.edu/etd_all Part of the Physics Commons Repository Citation Owens, Lindsay, "Characterization of Ceramic Composite Materials Using Terahertz Non-Destructive Evaluation Techniques" (2012). Browse all Theses and Dissertations. 598. https://corescholar.libraries.wright.edu/etd_all/598 This Thesis is brought to you for free and open access by the Theses and Dissertations at CORE Scholar. It has been accepted for inclusion in Browse all Theses and Dissertations by an authorized administrator of CORE Scholar. For more information, please contact [email protected]. CHARACTERIZATION OF CERAMIC COMPOSITE MATERIALS USING TERAHERTZ NON-DESTRUCTIVE EVALUATION TECHNIQUES A thesis submitted in partial fulfillment of the requirements for the degree of Master of Science By LINDSAY OWENS B.S., Wright State University, 2010 2012 Wright State University WRIGHT STATE UNIVERSITY GRADUATE SCHOOL June 14, 2012 I HEREBY RECOMMEND THAT THE THESIS PREPARED UNDER MY SUPERVISION BY Lindsay Owens ENTITLED Characterization Of Ceramic Composite Materials Using Teraherts Non-Destruction Evaluation Techniques BE ACCEPTED IN PARTIAL FULFILLMENT OF THE REQUIREMENTS FOR THE DEGREE OF Master of Science. Jason A. Deibel, Ph.D. Thesis Director Lok C. Lew Yan Voon, Ph.D. Department Chair Jason A. Deibel, Ph.D. Douglas T. Petkie, Ph.D. Gary Farlow, Ph.D. Andrew Hsu, Ph.D. Dean, Graduate School Owens, Lindsay. M.S. Department of Physics, Wright State University, 2012. Characterization of Ceramic Composite Materials using Terahertz Non-Destructive Evaluation Techniques.