Characteristics of Dref-3 Yams with Jute in Core Stronger and Longer Fibres
Total Page:16
File Type:pdf, Size:1020Kb
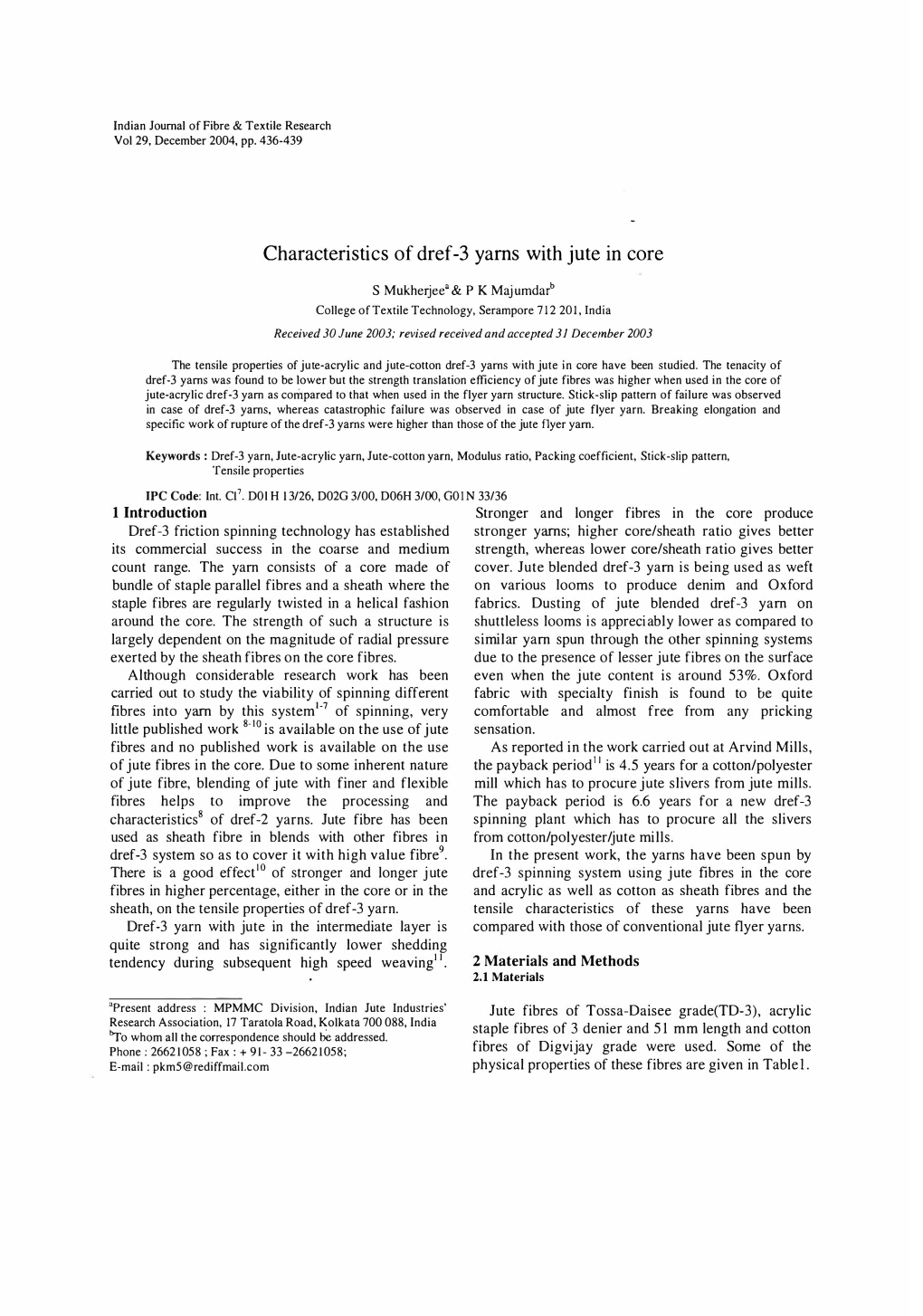
Load more
Recommended publications
-
Mohair: a Review of Its Properties, Processing and Applications
A review of its properties, processing and applications by L Hunter MOHAIR: A REVIEW OF ITS PROPERTIES, PROCESSING AND APPLICATIONS by L Hunter PhD CText FTI CSlR DIVISION OF TEXTILE TECHNOLOGY Copyright @ 1993 Division of Textile Technology All rights reserved. No part of this book may be reproduced or utilized in any form or by any means, electronic or mechanical, including photocopying, recording, or by any information storaae and retrieval svstani. without oermission in writina from the Additional copies of this book are available from the publisher and the International Mohair Association. Address all inquiries to: Division of Textile Technology PO BOX 1124 Port Elizabeth South Africa 6000 or International Mohair Association Mohair House OT 68 The Grove The Textile Institute llkley International Headquarters West Yorkshire 10 LS29 9PA Blackfriars Street England Manchester M3 5DR UK ISBN 0 7988 3717 9 Jointly published by. CSlR Oision of Textile Technofogy !ntema6oMI Mohair Associatim The Textile In?Litute Printed and bound in South Africa by NMB Printers (Pty) Ltd, Port Elizabeth CONTENTS Page 1.INTRODUCTION .............................................. 1 1.1 Preamble ............................................... 1 1.2 General Background Characteristics and Properties ........................................... 1 1.3 Historical Background..................................... 6 2. MOHAIR FIBRE GROWTH AND PRODUCTION ..................... 8 2.1 General ................................................. 8 2.2 Effect of Angora Goat Age -
Post Harvest Processing
Post Harvest Processing 78 Enzyme/Zinc Chloride Pretreatment of Short- Staple Cotton Fibres for Energy Reduction during Nano-Fibrillation by Refining Process N. Vigneshwaran1*, Vilas Karande1, G.B. Hadge1, S.T. Mhaske2 and A.K. Bharimalla1 1Nanotechnology Research Lab, Chemical and Biochemical Processing Division, Central Institute for Research on Cotton Technology, 2Department of Polymer and Surface Engineering, Institute of Chemical Technology, Matunga, Mumbai–400019, India e-mail: [email protected] Abstract—Cellulose is a renewable, biodegradable and the most abundant biopolymer available on the Earth. Natural Cellulosic fibers are synthesized mainly in plants and cellulose constitutes 40-50% of wood, 80% of flax and 90% of cotton fibers. Microfibrils are defined as the fibers of 0.1-1.0 μm diameter, with high aspect ratio and nanofibrils are at least one dimension in nanometer scale (1-100 nm). Nanofibrils of cellulose have potential use in high efficiency filters, tissue scaffolds and as reinforcing agent in composites. In this work, we have processed short-staple cotton fibres through refining process for the production of nanofibrils. The refining process, through shear force, pumps water into the secondary layer and loosens the compactness of fibrillar structure by disrupting the hydrogen bonding. To enhance the efficiency of refining process, pretreatments using enzyme / zinc chloride were developed to open up the primary layer. Cellulase enzyme pretreatment hydrolyzed the surface molecules in cellulose while zinc chloride act as a swelling agent thereby increasing the accessibility to secondary layer. Since the refining is a continuous process with very low residence time, minimum of 30 passes were required for complete fibrillation resulting in huge energy consumption. -
(American Association of Textile Chemists and Colorists), 217 Rain
TECIndex 11/24/2000 10:32 AM Page 543 Index AATCC (American Association of Textile Airpro, 478 Chemists and Colorists), 217 Akovali, G and Takrouri, F, 250 rain test, 296–7, 298 Akzo, 9, 30 abaca, 378 Akzo Nobel, 293 plant/fibre, generalised description, 383 Albany (US), 13 abrasion resistance, of fabrics used in Albright and Wilson, 165 transportation, 494 Alcantara, 511 accident survival, 463–5 alginate fibres, 37 acid dyes, 192–3 alginates, 411–12 Acrilan, 28 Allied Colloids, 28 acrylic fibres, 28 Allied Signal, 39, 240 dyeing, 194 Altex (Sumimoto, Japan), 229 flame-retardant additives, 242–3 aluminium oxide (or alumina) fibres, 32 gel dyeing, 203 aluminosilicate compounds, 32 acrylic polymers, LOI-char relationship with American Society for Testing Materials, 130 various flame-retardants, 244, 245 Amgard, 248 adhesive bonding, 145 Amijima, S et al., 271, 278 adhesives, in fusible interlinings, 184–5 ammonium polyphosphate (APP), 248 aerodynamic fabric transport systems, 214 Amoco Fabrics and Fibres Co., 232 aeronautics, 36–7 amorphous regions, in fibre structures, 163 aerosol protection performance, 486 Anand, S C, 113, 114, 128 Agarwal, B D and Broutman, L J, 268 Anand, S C and Garvey, S J, 236 agricultural engineering, 34–6 Anand, S C, Lawton, P J, Barlow, G and agriculture, 14–15 Hardman, E, 356 protective clothing, 484–7 anhydrous liquid ammonia treatments, air jet, weft insertion by, 91 cotton, 206–7 air jet weaving machines, 91–2 anthraquinones, in coloration, 190 air laying antifungal finishes, 171–2 batt production in nonwovens, 134–6 -
Virginia Tech Vs Clemson (9/13/1986)
Clemson University TigerPrints Football Programs Programs 1986 Virginia Tech vs Clemson (9/13/1986) Clemson University Follow this and additional works at: https://tigerprints.clemson.edu/fball_prgms Materials in this collection may be protected by copyright law (Title 17, U.S. code). Use of these materials beyond the exceptions provided for in the Fair Use and Educational Use clauses of the U.S. Copyright Law may violate federal law. For additional rights information, please contact Kirstin O'Keefe (kokeefe [at] clemson [dot] edu) For additional information about the collections, please contact the Special Collections and Archives by phone at 864.656.3031 or via email at cuscl [at] clemson [dot] edu Recommended Citation University, Clemson, "Virginia Tech vs Clemson (9/13/1986)" (1986). Football Programs. 181. https://tigerprints.clemson.edu/fball_prgms/181 This Book is brought to you for free and open access by the Programs at TigerPrints. It has been accepted for inclusion in Football Programs by an authorized administrator of TigerPrints. For more information, please contact [email protected]. — None Can Compete Batson is the exclusive U.S. agent for textile equipment from the leading textile manufacturers worldwide. Experienced people back up our sales with complete service, spare parts, technical assistance, training and follow-up. DREF 3 Friction Spinning Machine Excellent for Core Yarns and Multi-Component Yarns. Count range 3.5c.c. to 18c. c. Delivery speeds to 330 yds/min. Dornier Rapier Weaving Machine—Versatile enough to weave any fabric. Also ideally suited for short runs. State-of-the-art monitoring and control. An optimum tool for the creative weaver. -
Friction Spinning-A Critical Review
Indian Journal of Fibre & Textile Research Vol. 17, December 1992, pp. 246-251 Friction spinning-A critical review N Balasubramanian The Bombay Textile Resea rch Association. L B S Marg, Ghatkopar(West), Bombay 400 088 Received 13 April 1992 The ability to achieve high twisting rates without the need to rotate the heavier mechanical elements and the low yarn tensions enable very high delivery rates with friction spinning. The soft handle of the yarn, versatility to handle all types of fibres and the core spinning facility are the other meri.ts of this system. However, the low yarn strength. high twist variability, higher hairiness and the restriction to coarser counts are the major drawbacks to be overcome before friction spinning can become commercially viable. The yarn formation is very complex as the angle of deposition of the fibres. suction level inside the drums, surface friction on the yarn tai l a nd the air turbulence have considerable influence on fibre arrangement. Fibres are highly disoriented in the yarn with loops and folds which lead to very low utilization offibre length in yarn strength. The system becomes unstable when the number of fibres in the cross-section falls below a certain level. Keywords : Core-spun yarn, Dref-2, Dref-3, Friction spinning, Master Spinner, Open-end spinning, Spinning tension I Introduction number of turns to the yarn. So, very high rates of The need to rotate the package at the twist insertion twisting can be obtained without the need to rotate rate coupled with rapid increase in spinning tension the drum at excessively high speeds. -
Course Template
Curriculum Revision for B. Tech. (Textile Technology) Programme Dept. of Textile Technology Indian Institute of Technology Delhi 2013-2014 Tentative Schedule of Undergraduate Courses (The courses in red colour are the Institute core and programme linked core courses. These slots are fixed by The Institute.) Sem Lecture lecture lecture lecture Lecture/ Other Other Other L T P TOTAL Other I Maths-1 / 2 EE / CS PH / CY Mechanics Intro. to Graphics / Language / (3-1-0)4 (3-0-2)4 (3-0-4)5 / NONE Engg / Prog Prod. Real. None (3-0-2)4 (0-0-2)1 (0-0-4)2 (0-0-4)2 II Maths-2 / 1 CS / EE CY / PH NONE / Intro to Prod Real./ Language / (3-1-0)4 (3-0-2)4 (3-0-4)5 Mechanics Engg/ Prog Graphics None (3-0-2)4 (0-0-2)1 (0-0-4)2 (0-0-4)2 III PL EA/EA PL EA/ES Poly. Chem. PL EA/ES Text. fibres HUL ?? AML120 AML130 / (3-0-0)3 AML150 / (2-0-2)3 (3-0-2)4 (3-1-2)5 (3-1-2)5 IV Yarn Manf.-I Fabric Tech. TP &F Biology Structure Yarn Manf. Fabric Prep. & (3-0-0)3 Manf. I (3-0-0)3 (3-0-2)4/ Env. Property Lab -I Manf. Lab I Finishing Lab (3-0-0)3 (2-0-0)2 (3-0-0)3 (0-0-2)1 (0-0-2)1 (0-0-3)1.5 V Yarn Manf.-II Fabric Tech. Tex. -
South Carolina Vs Clemson (11/17/1990)
Clemson University TigerPrints Football Programs Programs 1990 South Carolina vs Clemson (11/17/1990) Clemson University Follow this and additional works at: https://tigerprints.clemson.edu/fball_prgms Materials in this collection may be protected by copyright law (Title 17, U.S. code). Use of these materials beyond the exceptions provided for in the Fair Use and Educational Use clauses of the U.S. Copyright Law may violate federal law. For additional rights information, please contact Kirstin O'Keefe (kokeefe [at] clemson [dot] edu) For additional information about the collections, please contact the Special Collections and Archives by phone at 864.656.3031 or via email at cuscl [at] clemson [dot] edu Recommended Citation University, Clemson, "South Carolina vs Clemson (11/17/1990)" (1990). Football Programs. 213. https://tigerprints.clemson.edu/fball_prgms/213 This Book is brought to you for free and open access by the Programs at TigerPrints. It has been accepted for inclusion in Football Programs by an authorized administrator of TigerPrints. For more information, please contact [email protected]. ^outnfCaKoJina Seniors^ ^cuncefiwMvmo^w ndJStacy \ meStwIiiaiiStaaiu^ ^November, PICTURES ARE WORTH A THOUSAND WORDS But at -"IpptT^jt we know your bottom line is what really counts. That's why we represent the world's leading textile machinery manufacturers and provide customers with the most high-tech equipment available to the market. We offer total support with complete service, technical assistance, and on-time spare parts. After all, you want that bottom line black- not red. Got the picture? DREF 3 FRICTION SPINNING MACHINE delivers yarn to 330 ypm. FEHRER K-21 RANDOM CARDING MACHINE has weight range 2 10-200 g/m , . -
Astounding V21n05 (1938
JACK WILLIAMSON • R. Z. UALLUN . KENT CASEY Rtc. u. s. r*T. omcc^ JULY 1938 — Sensational Scientific tests prove LISTERINE CURES DANDRUFF First Science discovered the dandruff germ, , .then, that Listerine kills it. 76% got quick relief in New Jersey clinic. If dandruff has you in its attacks and kills that queer, grip, if you have tried rem- bottle-shaped germ Pity- edy after remedy in vain, rosporum ovale, which here is the most welcome causes dandruff. news you could possibly Here is proof ovaie, me germ read: that causes dan- Science discovered druff, magnified Listerine has been scien- When the dandruff germ, an many limes, tifically proved a positive astounding series of experi- cure for dandruff. ments immediately fol- marked improvement in, the Once or twice a day, just lowed. Rabbits were in- symptoms within 30 days. douse full-strength Lister- fected with dandruff. When ine on your scalp; massage treated daily with Listerine Listerine treats dandruff vigorously persistently and Antiseptic, they were cured for what it really is until every hair is bathed within two weeks on the use old-fashioned rem- in soothing, health-promot- average. Why ing antiseptic. Listerine edies which merely wash In a great midwestem away the surface symptoms skin clinic, a group of dan- of dandruff temporarily? druff sufferers applied the Listerine Antiseptic actual- daily Listerine treatment. ly cures dandruff, by killing A substantial number of the germ itself. these Listerine users ob- Start ridding scalp tained marked relief within your of dandruff today. Stop the the first two weeks on the average. -
Furman Vs Clemson (9/10/1988) Clemson University
Clemson University TigerPrints Football Programs Programs 1988 Furman vs Clemson (9/10/1988) Clemson University Follow this and additional works at: https://tigerprints.clemson.edu/fball_prgms Materials in this collection may be protected by copyright law (Title 17, U.S. code). Use of these materials beyond the exceptions provided for in the Fair Use and Educational Use clauses of the U.S. Copyright Law may violate federal law. For additional rights information, please contact Kirstin O'Keefe (kokeefe [at] clemson [dot] edu) For additional information about the collections, please contact the Special Collections and Archives by phone at 864.656.3031 or via email at cuscl [at] clemson [dot] edu Recommended Citation University, Clemson, "Furman vs Clemson (9/10/1988)" (1988). Football Programs. 195. https://tigerprints.clemson.edu/fball_prgms/195 This Book is brought to you for free and open access by the Programs at TigerPrints. It has been accepted for inclusion in Football Programs by an authorized administrator of TigerPrints. For more information, please contact [email protected]. $2.00 September 10, 1988 Clemson Football *88 i \i\ii<sin Clemson vs. Furman Memorial Stadium Bullish Blockers MANGE YOU WORTHY OF THE BEST? Batson is the exclusive U.S. agent for textile equipment from the leading textile manufacturers worldwide. Experienced people back up our sales with complete service, spare parts, technical assistance, training and follow-up. DREF 3 FRICTION SPINNING MACHINE delivers yarn to 330 ypm. i FEHRER K-21 RANDOM CARDING MACHINE has weight range ^ 2 10-200 g/m , production speedy | m/min. rttfjfm 1 — •• fj := * V' " VAN DE WIELE PLUSH WEAVING MACHINES weave apparel, DORNIER RAPIER WEAVING MACHINES are upholstery, carpet. -
Industria Textila No 1 2016
Industria Textila˘ ISSN 1222–5347 1/2016 Editatã în 6 nr./an, indexatã ºi recenzatã în: Edited in 6 issues per year, indexed and abstracted in: Revistã cotatã ISI ºi inclusã în Master Journal List a Institutului pentru Science Citation Index Expanded (SciSearch®), Materials Science ªtiinþa Informãrii din Philadelphia – S.U.A., începând cu vol. 58, Citation Index®, Journal Citation Reports/Science Edition, World Textile nr. 1/2007/ Abstracts, Chemical Abstracts, VINITI, Scopus, Toga FIZ technik ISI rated magazine, included in the ISI Master Journal List of the Institute ProQuest Central of Science Information, Philadelphia, USA, starting with vol. 58, no. 1/2007 ŞERİFE ŞAFAK, ŞEBNEM DÜZYER, ESRA KARACA COLEGIUL Evaluarea biocompatibilității nanofibrelor pe bază de fibroină realizate DE REDACTIE:¸ prin electrofilare pentru aplicații medicale 3–9 Dr. ing. EMILIA VISILEANU HUA QIU, QIAOLI LUAN, HONGXIA JIANG, YUYE FU, JIHONG LIU cerc. şt. pr. I – EDITOR ŞEF Efectul unghiului de orientare a aerului prin duză cu vârtej asupra Institutul Naţional de Cercetare-Dezvoltare performanței firului realizat pe maşina de filat cu inele 10–16 pentru Textile şi Pielărie – Bucureşti Dr. ing. CARMEN GHIŢULEASA ERHAN KENAN ÇEVEN, HÜSEYİN AYTAŞ cerc. şt. pr. I Studiu asupra parametrilor care influențează proprietățile de abraziune Institutul Naţional de Cercetare-Dezvoltare și frecare ale firelor compozite cu conținut de fir metalic 17–24 pentru Textile şi Pielărie – Bucureşti Prof. dr. GELU ONOSE R. BEFRU BÜYÜKBAYRAKTAR cerc. şt. pr. I Studiu asupra sarcinii de deformare a diverselor tipuri de țesături 25–32 Universitatea de Medicină şi Farmacie „Carol Davila“ – Bucureşti RAŞIT ARSOY, İBRAHIM ÜÇGÜL Prof. dr. ing. -
Duke Vs Clemson (10/17/1992)
Clemson University TigerPrints Football Programs Programs 1992 Duke vs Clemson (10/17/1992) Clemson University Follow this and additional works at: https://tigerprints.clemson.edu/fball_prgms Materials in this collection may be protected by copyright law (Title 17, U.S. code). Use of these materials beyond the exceptions provided for in the Fair Use and Educational Use clauses of the U.S. Copyright Law may violate federal law. For additional rights information, please contact Kirstin O'Keefe (kokeefe [at] clemson [dot] edu) For additional information about the collections, please contact the Special Collections and Archives by phone at 864.656.3031 or via email at cuscl [at] clemson [dot] edu Recommended Citation University, Clemson, "Duke vs Clemson (10/17/1992)" (1992). Football Programs. 219. https://tigerprints.clemson.edu/fball_prgms/219 This Book is brought to you for free and open access by the Programs at TigerPrints. It has been accepted for inclusion in Football Programs by an authorized administrator of TigerPrints. For more information, please contact [email protected]. m Raw Material To Finished Product Batson has the equipment! TEMAFA - Equipmentforfiber reclamation. DORNIER - The Universal weaving machine. Airjet and VOUK - Draw Frames, Combers, Lappers, Automatic rigid rapier. Transport systems. SOHLER - Traveling blowing and vacuuming systems. DREF 2 AND DREF 3 - Friction spinning system. 6ENKINGER - Material handling systems. FEHRER - NL 3000: Needling capabilities up to 3000 - take-ups inspection systems. strokes per minute. ALEXANDER Offloom and HACOBA - Complete line of warping and beaming LEMAIRE - Warp transfer andfabric transfer printing. machinery. FONGS - Equipmentfor piece and package dyeing. KNOTEX - Will tie all yarns. -
Development of an Advanced Personal Protection Equipment Fabric for Protection Against Slashes
DEVELOPMENT OF AN ADVANCED PERSONAL PROTECTION EQUIPMENT FABRIC FOR PROTECTION AGAINST SLASHES BY KARTHICK KANCHI GOVARTHANAM B.Tech (Textile Technology); M.Sc (Advanced Materials) A thesis submitted in partial fulfilment of the requirements of the University of Bolton for the degree of Doctor of Philosophy June 2012 This thesis is dedicated to my late father, mother, brother my beloved wife and daughter for their love, endless support and encouragement DECLARATION This dissertation has been submitted in partial fulfilment for the award of Doctor of Philosophy in Technical Textiles at the University of Bolton, United Kingdom. I hereby confirm that the work contained in this dissertation is my own and that the work or contributions of others have been fully acknowledged. ________________ _________________________________ Date Karthick Kanchi Govarthanam ABSTRACT Knife is the most commonly used single weapon in the UK, being 32% of the weapons employed in a violent incident. Studies reveal that majority (63.3%) of the knife inflicted wounds were slash type and could be disfiguring or life threatening if the blood vessels are ruptured. The stab resistant armours that are currently available do not protect the arms, neck and face as they are very rigid and heavy to be worn comfortably for everyday use for security personnel and are also expensive for the civilian population. During the research programme, various composite yarns consisting of; a) blends of Spectra® (Ultra High Molecular Weight Polyethylene), glass and polyamide; b) Stainless steel core with wraps of Dyneema® (Ultra High Molecular Weight Polyethylene) and polyester; and c) Kevlar®, in different compositions, were thoroughly investigated to determine the most appropriate yarn for the slash proof materials.