Full Scale Bioreactor Landfill for Carbon Sequestration and Greenhouse Emission Control
Total Page:16
File Type:pdf, Size:1020Kb
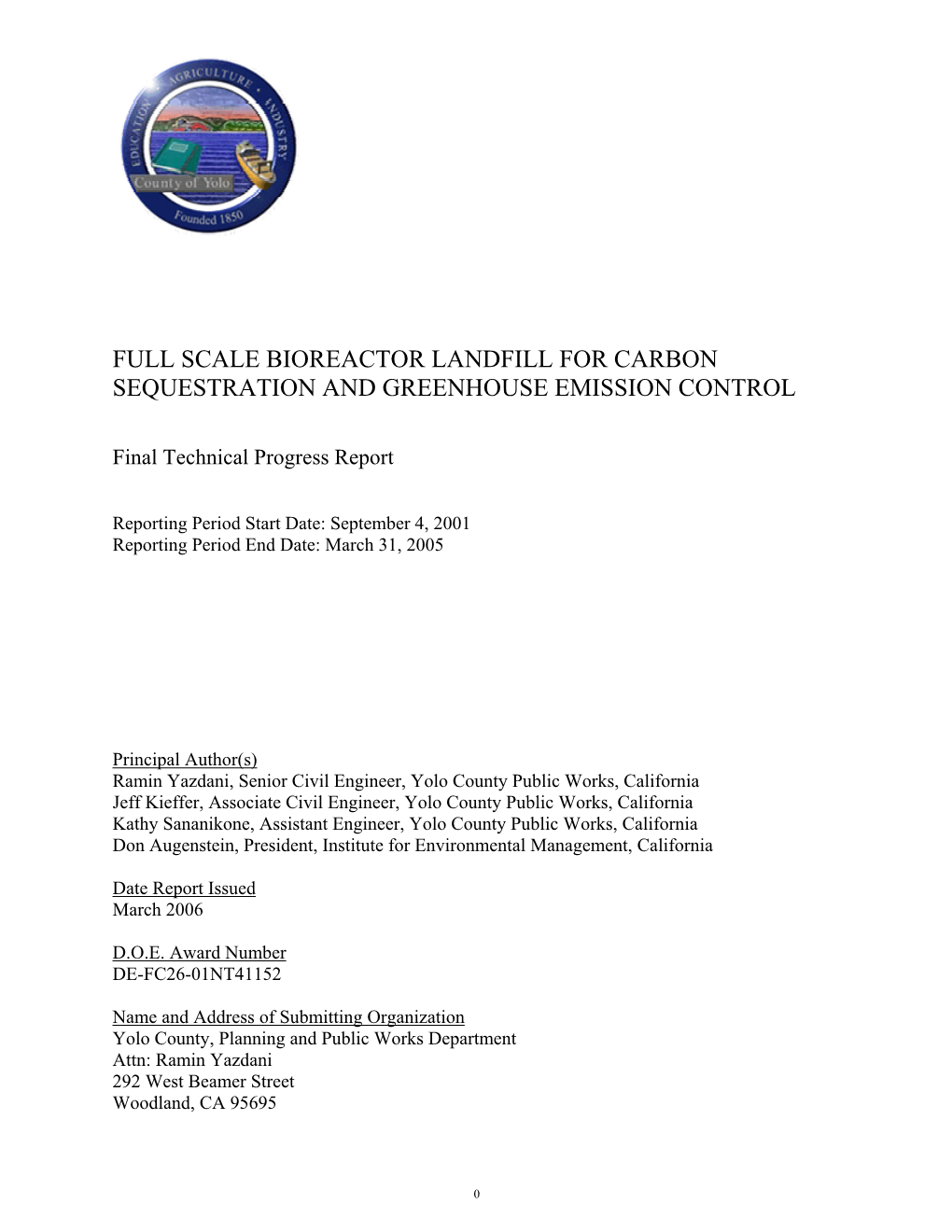
Load more
Recommended publications
-
Cost Analysis of the Impacts on Municipal Utilities and Biosolids Management to Address PFAS Contamination
Cost Analysis of the Impacts on Municipal Utilities and Biosolids Management to Address PFAS Contamination October 2020 Table of Contents Executive Summary Section 1 Background 1.1 Biosolids ................................................................................................................................................................ 1-1 Section 2 Data on Actual Costs to Wastewater and Biosolids Management Programs from PFAS 2.1 Introduction ......................................................................................................................................................... 2-1 2.2 NEBRA Survey ..................................................................................................................................................... 2-1 2.2.1 Background ............................................................................................................................................. 2-1 2.2.2 Results ...................................................................................................................................................... 2-2 2.3 Expanded Utility Survey ................................................................................................................................. 2-2 2.3.1 Background ............................................................................................................................................. 2-2 2.3.2 Results ..................................................................................................................................................... -
Assessment of the Possible Reuse of Extractive Waste Coming from Abandoned Mine Sites: Case Study in Gorno, Italy
sustainability Article Assessment of the Possible Reuse of Extractive Waste Coming from Abandoned Mine Sites: Case Study in Gorno, Italy Neha Mehta 1,2, Giovanna Antonella Dino 1,*, Iride Passarella 3, Franco Ajmone-Marsan 4, Piergiorgio Rossetti 1 and Domenico Antonio De Luca 1 1 Department of Earth Sciences, University of Turin, 10125 Torino, Italy; [email protected] (N.M.); [email protected] (P.R.); [email protected] (D.A.D.L.) 2 School of Mechanical and Aerospace Engineering, Queen’s University Belfast, Belfast, BT9 5AH, UK 3 Horizon s.r.l., 10095 Grugliasco (TO), Italy; [email protected] 4 Department of Agricultural, Forestry and Food Sciences, University of Turin, 10095 Grugliasco (TO), Italy; [email protected] * Correspondence: [email protected]; Tel.: +39-011-6705150 Received: 21 January 2020; Accepted: 17 March 2020; Published: 21 March 2020 Abstract: Supply of resources, a growing population, and environmental pollution are some of the main challenges facing the contemporary world. The rapid development of mining activities has produced huge amounts of waste. This waste, found in abandoned mine sites, provides the potential opportunity of extracting raw material. The current study, therefore, focuses on testing the validation of a shared methodology to recover extractive waste from abandoned mines, and applies this methodology to a case study in Gorno, northwest Italy. The methods focused on: (1) analyzing the impact of tailings and fine fraction of waste rock (<2 mm) on plants (Cress - Lepidium Sativum) to assess usability of both as soil additive, and (2) recovering raw materials from tailings and coarse fraction (>2 mm) of waste rock, by means of dressing methods like wet shaking table and froth flotation. -
2019 Annual Waste Prevention & Recycling Report
s 2019 ANNUAL WASTE PREVENTION & RECYCLING REPORT i Submitted to Seattle City Council (SCC) October 2020 [Page deliberately left blank] ii CONTENTS GLOSSARY .............................................................................................................................................................. v EXECUTIVE SUMMARY ........................................................................................................................................... 1 Purpose ...................................................................................................................................................................... 1 Key Results................................................................................................................................................................. 1 Next Steps .................................................................................................................................................................. 2 INTRODUCTION ..................................................................................................................................................... 3 Seattle’s Recycling Rate Goals ................................................................................................................................... 3 Moving Upstream ...................................................................................................................................................... 3 Annual Waste Prevention & Recycling Report.......................................................................................................... -
(Daily) Cover Material Requirements. FROM
April 30, 2004 SUBJECT: Clarification of 40 CFR 258.21, (Daily) Cover Material Requirements. FROM: Robert Springer, Director /s/ Office of Solid Waste TO: Jeff Scott, Director Waste Management Division USEPA Region IX You recently raised some questions about the daily cover material requirements at municipal landfills which operate on a continuous basis, specifically, regarding landfills that do not shut down at the end of each day. The federal regulations at 40 CFR '258.21 require that the owner/operator place daily cover on the disposed solid waste at the end of each operating day or at more frequent intervals if necessary. We received extensive comments on the proposed frequency for the daily cover requirement. Many rural communities argued for a weekly cover requirement. Others suggested that we design the daily cover requirements based on the length of time the waste is exposed (e.g., 6 to 24 hours). In the final rule, we retained the proposed language regarding cover placement at the end of each operating day. [The final rule can be found at 56 Fed. Reg. 50978, 51050-51 (Oct. 9, 1991) and the later clarification at 62 Fed. Reg. 40709-10 (July 29, 1997).] You have mentioned an issue where large commercial landfills operate continuously over a number of days. These large commercial landfills argue that they operate “around the clock” and therefore their “operating day” is something beyond a 24-hour period. It is our view, however, that the Federal regulations at 40 CFR '258.21 did not contemplate an “operating day” longer than 24 hours. -
Numerical Model of Leachate Recirculation in Bioreactor Landfills
water Article Numerical Model of Leachate Recirculation in Bioreactor Landfills with High Kitchen Waste Content Peng Zhang , Hailong Liu * , Xingyao Jiang, Hao Lv, Chunyi Cui and Zhen Huyan Department of Civil Engineering, Dalian Maritime University, Dalian 116026, China; [email protected] (P.Z.); [email protected] (X.J.); [email protected] (H.L.); [email protected] (C.C.); [email protected] (Z.H.) * Correspondence: [email protected] Abstract: Surface spraying, horizontal trenches, and vertical wells are the most common leachate recirculation system used at landfills in engineering practice. In order to quantify the efficiency of the three aforementioned recirculation systems, a hydro–biochem–mechanical-coupled model was developed in the present work, which can describe hydrodynamic and biochemical behaviors in food-waste-rich landfills. A typical landfill cell was modeled in COMSOL. The results indicate that leachate recirculation can accelerate the decomposition of municipal solid waste (MSW) with food- rich waste content, relieving acidification, improving gas generation efficiency, and consequently, increasing the early settlement in landfills. Keywords: municipal solid waste; landfill; leachate treatment; coupled model; numerical simulation Citation: Zhang, P.; Liu, H.; Jiang, X.; 1. Introduction Lv, H.; Cui, C.; Huyan, Z. Numerical Disposing of municipal solid waste (MSW) has been a worldwide environmental Model of Leachate Recirculation in issue for decades. Landfilling is a commonly used MSW management method all around Bioreactor Landfills with High the world [1,2]. Due to the biochemical reaction of degradable components in MSW, the Kitchen Waste Content. Water 2021, releasing of polluted leachate and landfill gas will be a long-term process that may take 13, 1750. -
Integration of Resource Recovery Into Current Waste Management Through
INTEGRATION OF RESOURCE RECOVERY INTO CURRENT WASTE MANAGEMENT THROUGH (ENHANCED) LANDFILL MINING Juan Carlos Hernández Parrodi 1,2,*, Hugo Lucas 3, Marco Gigantino 4, Giovanna Sauve 5, John Laurence Esguerra 6,7, Paul Einhäupl 5,7, Daniel Vollprecht 2, Roland Pomberger 2, Bernd Friedrich 3, Karel Van Acker 5, Joakim Krook 6, Niclas Svensson 6 and Steven Van Passel 7 1 Renewi Belgium SA/NV, NEW-MINE project, 3920 Lommel, Belgium 2 Montanuniversität Leoben, Department of Environmental and Energy Process Engineering, 8700 Leoben, Austria 3 RWTH Aachen University, Process Metallurgy and Metal Recycling, 52056 Aachen, Germany 4 ETH Zürich, Department of Mechanical and Process Engineering, 8092 Zürich, Switzerland 5 Katholieke Universiteit Leuven, Department of Materials Engineering, 3001 Leuven, Belgium 6 Linköping University, Environmental Technology and Management, 58183 Linköping, Sweden 7 Universiteit Antwerpen, Department of Engineering Management, 2000 Antwerpen, Belgium Article Info: ABSTRACT Received: Europe has somewhere between 150,000 and 500,000 landfill sites, with an estimat- 1 November 2019 Accepted: ed 90% of them being “non-sanitary” landfills, predating the EU Landfill Directive of 15 November 2019 1999/31/EC. These older landfills tend to be filled with municipal solid waste and Available online: often lack any environmental protection technology. “Doing nothing”, state-of-the- 23 December 2019 art aftercare or remediating them depends largely on technical, societal and eco- Keywords: nomic conditions which vary between countries. Beside “doing nothing” and land- Landfill mining strategies fill aftercare, there are different scenarios in landfill mining, from re-landfilling the Enhanced landfill mining waste into “sanitary landfills” to seizing the opportunity for a combined resource-re- Resource recovery covery and remediation strategy. -
The Science of Alternative Daily Cover Welcome
Blue Ridge Services Understanding ADC: The Science of Alternative Daily Cover Presented: July 31, 2012 1(c) 2012 Neal Bolton Welcome • Sarah is our organizer • We’ll do Q&A during the webinar …and at the end ©2012 Neal Bolton 2 Alternative Daily Cover www.blueridgeservices.com 1 Blue Ridge Services Presented by: Neal Bolton, P.E. Neal is a Civil Engineer with over 34 years experience in landfills and heavy construction, including several years as a heavy equipment operator. He has conducted hundreds of evaluations on the process of using Alternative Daily Cover at landfills across the U.S. and abroad. He has provided training on this topic for the EIA, SWANA, CalRecycle, KDHE, and several thousand public/private landfill operators and managers. Contact Neal at: [email protected] ©2012 Neal Bolton 3 Alternative Daily Cover Today • We’ll be §258.21 Cover material requirements. talking Except as provided in paragraph (b) of this section, the owners or operators of all MSWLF units must about cover disposed solid waste with six inches of earthen Alternatives material at the end of each operating day, or at more frequent intervals if necessary, to control disease to Daily vectors, fires, odors, blowing litter, and scavenging. Cover Soil Alternative materials of an alternative thickness (other than at least six inches of earthen material) may be approved by the Director of an approved State if the owner or operator demonstrates that the • You alternative material and thickness control disease Know…ADC vectors, fires, odors, blowing litter, and scavenging without presenting a threat to human health and the environment. -
Solid Waste Alternatives Advisory Committee
Date: November 28, 2017 To: Solid Waste Alternatives Advisory Committee (SWAAC) From: Tim Collier, Chair – Solid Waste Fee and Tax Exemption Policy Evaluation Subcommittee Subject: Subcommittee Fee and Tax Policy Recommendations This memorandum outlines the recommendations of the Solid Waste Fee and Tax Exemption Policy Evaluation Subcommittee (the “subcommittee”) that was tasked with evaluating Metro’s current solid waste fee and tax exemption policies and making recommendations on whether Metro should consider any changes to those policies. These recommendations were developed after discussions at five subcommittee meetings as detailed in the meeting summary documents provided as Attachments A through E. Subcommittee Purpose The purpose of the subcommittee was to determine if Metro’s current solid waste fee and tax exemption policies are achieving the public benefits, goals, and objectives of the solid waste system. Subcommittee Membership On March 8, 2017, the Solid Waste Alternatives Advisory Committee (SWAAC) appointed the subcommittee consisting of 13 members representing industry, government, advocacy groups, and the general public. The subcommittee included the following members: • Tim Collier, Chair (non-voting) – Metro • Terrell Garrett - Greenway Recycling • Mark Hope – Tire Disposal and Recycling • Reba Crocker – City of Milwaukie • Dave Claugus – Pioneer Recycling Services • Vern Brown – Environmentally Conscious Recycling • Matt Cusma – Schnitzer Steel • Audrey O’Brien – DEQ • Bill Carr – Waste Management • Janice Thompson -
Bioreactor Landfills: Experimental and Field Results
Waste Management 22 (2002) 7–17 www.elsevier.nl/locate/wasman Bioreactor landfills: experimental and field results Mostafa Warith Ryerson Polytechnic University, 350 Victoria Street, Toronto, Ontario, Canada M5B 2K3 Received 8 August 2000; received in revised form 29 January 2001; accepted 31 January 2001 Abstract Bioreactor landfills allow a more active landfill management that recognizes the biological, chemical and physical processes involved in a landfill environment. This paper presents the results of an experimental study carried out to determine the effect of solid waste size, leachate recirculation and nutrient balance on the rate of municipal solid waste (MSW) biodegradation. Higher rates of MSW biodegradation eventually cause a reduction of the contaminant life span of the landfill and decrease in the cost of long term monitoring. The study indicated that the smaller the size of the MSW the faster the biodegradation rate of the waste. In addition, the paper presents the results of leachate recirculation on solid waste biodegradation in a full-scale landfill site, which is located in Nepean, Ontario, Canada. The leachate was recirculated into the landfilled solid waste for 8 years through infiltration lagoons. Similar results to those obtained in the laboratory scale experiments were noted. The average pH of the leachate in the early stages of recirculation was on the acidic range of the pH scale, however, the pH value was in the range of 7–8 after 2 years of leachate recirculation. The concentration of chloride remained fairly constant at about 1000 mg/l during the leachate recirculation period. A decreasing trend of the organic load, measured as biological oxygen demand and chemical oxygen demand, was observed. -
Joint Technical Document, MSW Landfill B-19, Kettleman Hills
JOINT TECHNICAL DOCUMENT MSW LANDFILL B-19, KETTLEMAN HILLS FACILITY KINGS COUNTY, CALIFORNIA VOLUME 1 OF 2 June 2016 Prepared for: Chemical Waste Management, Inc. 35251 Old Skyline Road Kettleman City, California 93239 Original prepared by: EMCON/OWT, Inc. 1326 North Market Boulevard Sacramento, California 95834-1912 Project No.: 833760.02000000 JOINT TECHNICAL DOCUMENT MSW LANDFILL B-19, KETTLEMAN HILLS FACILITY KINGS COUNTY, CALIFORNIA PROFESSIONAL ENGINEERING CERTIFICATION This revision to the JTD was prepared under the supervision and direction of the undersigned. This report was prepared consistent with current and generally accepted geologic and environmental consulting principles and practices that are within the limitations provide herein. Scott Sumner, P.E. Engineering Manager, RCE 49769 B-19 JTD JUNE 2016 ii Table of Contents ________________________________________________ Title Page ............................................ ……………………………………………………………………………... i Professional Engineering Certification ……………………………………………………………………………... ii List of Figures ............................................................................................................................................... vii List of Appendices ........................................................................................................................................ vii CalRecycle/SWB Index………………………………………………………………………………………………viii 1.0 Introduction .................................................................................................................................... -
Cost of Organic Waste Technologies: a Case Study for New Jersey
AIMS Energy, 3 (3): 450–462. DOI: 10.3934/energy.2015.3.450 Received date 28 June 2015, Accepted date 30 August 2015, Published date 15 September 2015 http://www.aimspress.com/ Research article Cost of organic waste technologies: A case study for New Jersey Gal Hochman 1,*, Shisi Wang 1, Qing Li 1, Paul D. Gottlieb 1, Fuqing Xu 2 and Yebo Li 2 1 Rutgers University, New Brunswick, NJ 08901, USA 2 The Ohio State University, Ohio 44691 * Correspondence: [email protected]; Tel: +1-848-932-9142 Abstract: This paper evaluates the benefits of converting food waste and manure to biogas and/or fertilizer, while focusing on four available waste treatment technologies: direct combustion, landfilling, composting, and anaerobic digestion. These four alternative technologies were simulated using municipal-level data on food waste and manure in New Jersey. The criteria used to assess the four technologies include technological productivity, economic benefits, and impact on land scarcity. Anaerobic digestion with gas collection has the highest technological productivity; using anaerobic digesters would supply electricity to nearly ten thousand families in New Jersey. In terms of economic benefits, the landfill to gas method is the least costly method of treating waste. In comparison, direct combustion is by far the most costly method of all four waste-to-energy technologies. Keywords: Organic waste; manure; combustion; land-fill gas; aerobic composting; anaerobic digestion 1. Introduction Population growth and urbanization yield an increase in the generation and disposal of waste. On average, each person in the U.S. produces 1.5 kilograms of municipal solid waste (MSW) per day. -
Solid Waste in Washington State, 16Th Annual Status Report
Solid Waste In Washington State Sixteenth Annual Status Report Solid Waste and Financial Assistance Program December 2007 Publication #07-07-048 Solid Waste in Washington State Sixteenth Annual Status Report Prepared by: Washington State Department of Ecology Solid Waste and Financial Assistance Program December 2007 Publication No. 07-07-048 This report and the supporting database information can be accessed at: http://www.ecy.wa.gov/programs/swfa/solidwastedata/ For additional copies of this document, contact: Department of Ecology Solid Waste & Financial Assistance Program PO Box 47600 Olympia, WA 98504-7600 Telephone: (360) 407-6900 The Department of Ecology is an equal opportunity agency and does not discriminate on the basis of race, creed, color, disability, age, religion, national origin, sex, marital status, disabled veteran's status, Vietnam Era veteran's status or sexual orientation. If you need this publication in another format, please call the Solid Waste & Financial Assistance Program at (360) 407-6900. Persons with hearing loss can call 711 for Washington Relay Service. Persons with a speech disability can call 877-833-6341. Table of Contents Acknowledgments .........................................................................................................................................v Chapter I Issues Facing Solid Waste...........................................................................................................1 Beyond Waste ........................................................................................................................................1