Pods White Paper Final
Total Page:16
File Type:pdf, Size:1020Kb
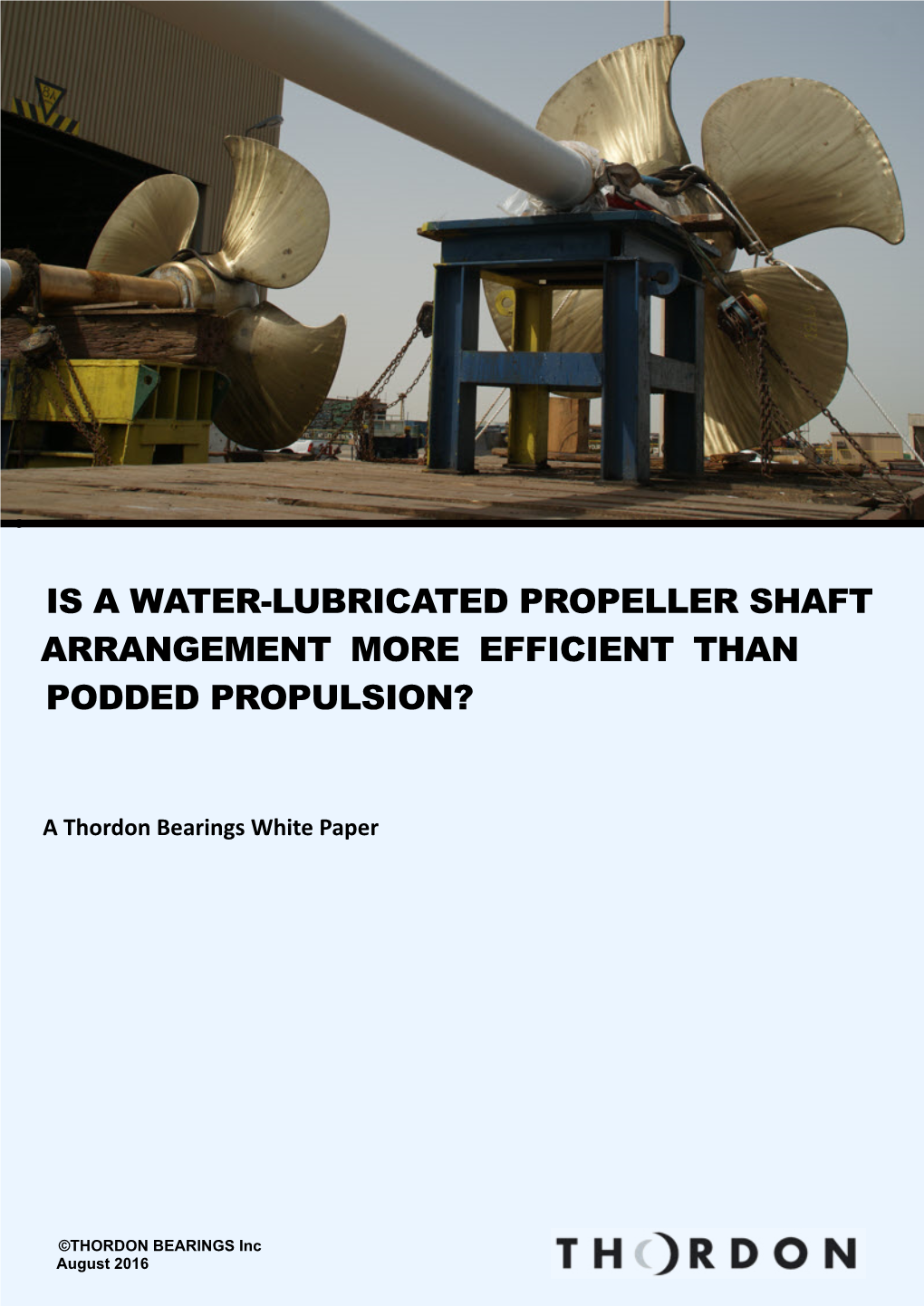
Load more
Recommended publications
-
Case 8:21-Cv-00839-SDM-AAS Document 96-1 Filed 07/06/21 Page 1 of 25 Pageid 3553
Case 8:21-cv-00839-SDM-AAS Document 96-1 Filed 07/06/21 Page 1 of 25 PageID 3553 UNITED STATES DISTRICT COURT MIDDLE DISTRICT OF FLORIDA TAMPA DIVISION STATE OF FLORIDA, Plaintiff v. Case No. 8:21-cv-839-SDM-AAS XAVIER BECERRA, Secretary of the Dep’t of Health and Human Services, et al., Defendant. THIRD DECLARATION OF CAPTAIN AIMEE TREFILETTI DEPARTMENT OF HEALTH AND HUMAN SERVICES CENTERS FOR DISEASE CONTROL AND PREVENTION I, Aimee Treffiletti, declare as follows: 1) I currently hold the position of Program Chief of the Centers for Disease Control and Prevention’s (CDC) Vessel Sanitation Program (VSP) and have served in this position since 2016. VSP is an applied environmental health program with a mission to help the cruise ship industry prevent and control the introduction, transmission, and spread of gastrointestinal illness on board cruise ships in U.S. waters. CDC is an agency within the U.S. Department of Health and Human Services (HHS). - 1 - Case 8:21-cv-00839-SDM-AAS Document 96-1 Filed 07/06/21 Page 2 of 25 PageID 3554 2) Prior to assuming my current position, I served as an Environmental Health Officer and as Assistant Deputy Program Chief in the VSP. Between 2008 and early 2020, I conducted almost 700 cruise ship public health inspections and trained over 4,000 cruise ship managers and supervisors on maritime public health principles. Based this experience, I am familiar with the cruise ship industry’s policies and practices to mitigate onboard illnesses and their response when outbreaks of illness occur on board cruise ships. -
PDF Success Story, Adventure of the Seas
ABB, Marine & Ports, Marine Services ABB’s modernization on Adventure of the Seas increases the lifetime of the vessel and secures the operational reliability. Increasing lifetime of the vessel, securing discussions about life cycle status and ABB’s solution presentations to improve the situation. The actual project was operational reliability, and enhancing the executed in eight months, which is exceptionally short for such maintainability of the vessel. an extensive project. All the works at dry dock were completed 1 day earlier than Success by collaboration scheduled and transfer trial from Grand Bahamas to Puerto Modernization scope Rico was possible to start earlier. That allowed ABB to test and The modernization project on Adventure of the Seas included tune the system to perfection without time pressure, even the upgrade of the existing PSR Cycloconverter Drive control though in normal case 48 hours of testing time is suitable. All platform to the AMC34 platform as well as the upgrade of the the sea trial tests and tuning of the new control systems were existing AC110 propulsion control platform to AC800M executed on transfer trial without need of additional sea trials. propulsion control platform. In addition to the material supply, the overall ABB scope of supply included installation work, commissioning phase and The vessel testing. Even with a tight schedule and shortened timeline ABB Adventure of the Seas was delivered in 2001 in Kvaerner Masa- was able to complete this pilot project successfully. The project Yards in Turku, Finland (today known as Meyer Turku Shipyard). team worked seamlessly together in Marine and Ports Finland, She is operated by Royal Caribbean International (RCI), and is getting support and assistance from the local ABB units in the the third vessel of the Voyager class. -
Date: April 22, 2003 Trip Report to Northern Europe for National
Date: April 22, 2003 Subject: Trip Report to Northern Europe for National Science Foundation project From: Richard P. Voelker Chief, Advanced Technology Office of Shipbuilding and Marine Technology To: Joseph A. Byrne Director Office of Shipbuilding and Marine Technology During March 12-27, I traveled with representatives of the National Science Foundation (Alexander Sutherland), Raytheon Polar Services Corporation (Paul Olsgaard) and Science and Technology Corporation (James St. John and Aleksandr Iyerusalimskiy) to Finland, Sweden and Germany. The purpose of the trip was to gain insight into the design and operation of their national icebreakers, many of which incorporate innovative concepts. Visits were made to the Finnish Maritime Administration (Markku Mylly) and their icebreaker BOTNICA, the Swedish Maritime Administration (Anders Backman) and their icebreaker ODEN, and the German Alfred Wegener Institute for Polar and Marine Research (Eberhard Fahrbach). Information was also obtained on the new Swedish icebreaker class VIKING and the German polar research vessel POLARSTERN. Attachment A provides some of the notes from our visit while Attachment B contains a discussion on some elements of the technical specification for the new generation research/icebreaker vessel. The trip was very valuable and provided a great start to the feasibility-level design study that MARAD has been contracted to perform for the NSF. A presentation describing this trip and some interim results from the feasibility-level design study will be made in mid-May to interested MAR-760 members. # Attachment A – Notes from the visit ---------- Briefing by Paavo Lohi - Aker Finnyards, builder of BOTNICA The bow skeg or bilge keels do not affect the flow of ice around the hull. -
Construction of a Hardware-In-The-Loop Simulator for Azipod Control System Testing
Markus Nylund Construction of a hardware-in-the-loop simulator for Azipod control system testing Thesis submitted for examination for the degree of Master of Science in Technology. Espoo 03.08.2016 Thesis supervisor: Prof. Seppo Ovaska Thesis advisor: D.Sc. (Tech.) Juha Orivuori Aalto-universitetet, PL 11000, 00076 AALTO www.aalto.fi Sammandrag av diplomarbete Författare Markus T. V. Nylund Titel Construction of a hardware-in-the-loop simulator for Azipod control system testing Examensprogram Utbildningsprogrammet för elektronik och elektroteknik Huvud-/biämne Elektronik med tillämpningar Kod S3007 Övervakare Prof. Seppo Ovaska Handledare TkD Juha Orivuori Datum 03.08.2016 Sidantal 9+90 Språk engelska Sammandrag Syftet med detta diplomarbete är att konstruera en simulator för Azipod® roderpropellern. Azipod® är ett varumärke av en roderpropeller med en elmotor som driver propellern. Hela roderenheten är belägen utanför fartygets skrov och det är möjligt att rotera roderpropellern obegränsat runt sin axel. Unikt för roderpropellrar är att drivkraften kan göras fullständigt elektriskt samt att roderpropellern är en dragande propeller till skillnad från tryckande konventionella propellrar. Dessa egenskaper ökar på ett fartygs energieffektivitet. Målet med arbetet är att bygga en (Azipod®) roderpropellersimulator och en tillhörande styrenhet som liknar fartygs styrenheter. Fokus för arbetet ligger på propulsionsstyrenheten. Simulatorn skall fungera liknande som den kommersiella produkten, men med mindre hårdvara. Fartygs styrkonsolpaneler samt alla nödvändiga mätinstrument virtualiseras. Ett extra program skapas för att möjliggöra stimulans för systemet för de virtualiserade mätinstrumenten. Detta program körs från en godtycklig dator som är uppkopplad till simulator nätverket. Simulering av Azipod® roderpropellern utförs av två sammankopplade motorer. Den ena motorn representerar en Azipod® rodermotor och den andra motorn belastar propulsionsmotorn. -
Problems of Handling Ships Equipped with Azipod Propulsion Systems
PRACE NAUKOWE POLITECHNIKI WARSZAWSKIEJ z. 95 Transport 2013 Lech Kobyliski Foundation for Safety of Navigation and Environment Protection PROBLEMS OF HANDLING SHIPS EQUIPPED WITH AZIPOD PROPULSION SYSTEMS The manuscript delivered, March 2013 Abstract: Large ships, mainly large cruise vessels, built during last two decades are quite often equipped with revolutionary propulsion devices known under the name AZIPODs. There are many reasons for choosing AZIPODs as main propulsion units, the main reason being excellent manoeuvring characteristics achieved. However in case of large propulsion units, having power of 15-25 MW, used for propulsion there are also some disadvantages and limitations, the last mainly related to operational factors. Handling of ships equipped with AZIPODS is different from handling conventional ships and in certain manoeuvring situations safety of the ship and of the propulsion units might be endangered.. Therefore some limitations imposed on handling procedures are necessary and it is essential that pilots and masters of ships fitted with AZIPODs must be specially trained. Keywords: ship manoeuvrability, podded propulsion, handling of ships with Azipods 1. INTRODUCTION During recent times the new type of vessel has been introduced to the world shipping fleet in large numbers. This type is passenger cruise vessel. Statistics of ships in operation and on order reveals that more than 750 ships of different size that could be defined as cruise ships are recently in operation, more than about 50 of them are large ships of more than 250 metres in length and carrying sometimes as much as 6000 passengers. According to the definition cruise ship is usually a very large passenger ship that makes a roundtrip with several en route stops and takes passengers only at the port where trip begins and ends. -
Allure of the Seas Is a Sailing City with UPS Protection
Markets Served Success Story: Royal Caribbean Vehicle / Transportation © Royal Caribbean International, STX Europe, Jouni Saaristo Allure of the Seas is a sailing city with UPS protection Location: Background science lab for children. USA "We are extremely Allure of the Seas is the Along with a variety of Segment: satisfied with both ultimate achievement in entertainment options, Allure Marine & Offshore the delivered product ship building – it is the most of the Seas is also impressive advanced cruise ship ever in terms of motor power Challenge: quality and the service built. Its sister ship Oasis of – its 100-megawatt output The ship´s operations - such as navi- the Seas, completed in 2009, corresponds to the electricity gation equipment, ship automation, provided." set the bar for the concept needs of the city of Turku, emergency power, lighting, as well - Juha Rokka, Senior and vision of a modern cruise Finland, where the ship was as commercial applications - need ship, and Allure of the Seas built. In order to maintain reliable, clean and safe power. Superintendent at Royal took energy efficiency to new operations, the ship needed Caribbean International heights. Both ships rely on reliable, clean and safe power. Solution: Eaton’s UPS protection for Eaton delivered over 20 double- passenger safety and comfort. Solution conversion, online marine UPSs to the ship. On board the ship is Challenge Eaton helped this massive the first ever marine application of Advanced technology is vessel meet its power supply Eaton’s Energy Saver System (ESS) everywhere on board the challenges with a delivery of technology, which enables the UPS world’s largest cruise ship. -
BLÜCHER Marine References
BLÜCHER Marine References Country Project Shipyard Owner Vessel Type Hull no. Year Argentina Frigate Naval Shipyard Frigate Frigate Refitting 2005 Australia Australian Customs and Austal Ships Australian Customs and Border Cape Class Patrol Boat 361 2013 Border Protection Service Protection Service Australia Australian Customs and Austal Ships Australian Customs and Border Cape Class Patrol Boat 362 2013 Border Protection Service Protection Service Australia Australian Customs and Austal Ships Australian Customs and Border Cape Class Patrol Boat 363 2013 Border Protection Service Protection Service Australia Australian Customs and Austal Ships Australian Customs and Border Cape Class Patrol Boat 364 2013 Border Protection Service Protection Service Australia Australian Customs and Austal Ships Australian Customs and Border Cape Class Patrol Boat 365 2014 Border Protection Service Protection Service Australia Australian Customs and Austal Ships Australian Customs and Border Cape Class Patrol Boat 366 2014 Border Protection Service Protection Service Australia Australian Customs and Austal Ships Australian Customs and Border Cape Class Patrol Boat 367 2014 Border Protection Service Protection Service Australia Australian Customs and Austal Ships Australian Customs and Border Cape Class Patrol Boat 368 2014 Border Protection Service Protection Service Australia Australian Defence Civmec/ASC Australian Defence OPV OPV1 2019 Australia Australian Defence - ASC Shipyard Australian Defence Air Warfare Destroyer 2012 AWD Australia Australian Defence - LHD BAE Systems Australian Defence Landing Helicpoter 2012 Dock Australia Dick Smith Tenix Dick Smith Ocean Research Ulysses Blue 2005 Vessel Australia Esso West Tuna Esso Platform 1996 Australia HMAS Arunta BAE Systems Australian Defence ANZAC Frigate ANZAC 2019 Australia Jean de la Valette - Virtu Austal Ships Virtu Ferries High Speed Ferry 248 2010 Ferries Australia RNZN Tenix RNZN Ocean Research 42826 2006 Vessel Australia Taylor Bros. -
Free Free Free
CWHEREruise WILL YOU ESCAPE TO? FREE FREE FREE DRINKS GRATUITIES STATEROOM £0 PACKAGES & ON BOARD CREDIT UPGRADES DEPOSITS Cruise1st Store, Lowry Outlet, MediaCityUKON SELECTED SKY SAILINGS CHANNEL 688 TV CRUISE CHANNEL 199 REVOLUTIONISED CELEBRITY SILHOUETTE FREE FREE FREE FREE OCEANVIEW GRATUITIES $300 DRINKS ON BOARD TO VERANDA CREDIT UPGRADES ON OCEANVIEW AND ABOVE IRELAND AND ICELAND CELEBRITY SILHOUETTE • 14 NTS • 30 MAY & 05 SEPT 2020 NOW FROM ▶ Southampton ▶ St.Peter Port, Channel Islands ▶ Cork (Cobh), Ireland £1309PP ▶ Dublin, Ireland (Overnight On Board) ▶ Reykjavik, Iceland (Overnight On VERANDA FR.£1799PP Board) ▶ Akureyri, Iceland ▶ Belfast, Northern Ireland ▶ Southampton CONCIERGE FR.£1989PP NORTHERN EUROPE CAPITALS ® The Celebrity Silhouette is impressive, with chic CELEBRITY SILHOUETTE • 14 NTS • 13 JUNE & 18 JULY 2020 NOW FROM upgrades to the iconic Lawn Club, Celebrity have ▶ Southampton ▶ Copenhagen, Denmark (Overnight On Board) ▶ Stockholm, £1719PP provided more space to relax, and socialize in the Sweden ▶ Helsinki, Finland ▶ St. Petersburg, Russia (Overnight On Board) VERANDA FR.£2259PP fresh sea air, plus the Lawn Club Grill offers an ▶ Berlin (Warnemunde), Germany ▶ Arhus, Denmark ▶ Southampton CONCIERGE FR.£2449PP interactive outdoor grilling experience. After a day of adventure unwind in your own cabana-styled haven MEDITERRANEAN DELIGHTS at The Alcoves. 85% of the ship's luxurious staterooms CELEBRITY SILHOUETTE • 14 NTS • 01 AUG 2020 NOW FROM are enhanced by sweeping veranda views. £1699PP Celebrity Cruises -
Volume 4 – Issue #71
https://gusskinnerconsulting.com/ Volume 4 – Issue #71 https://www.gphsconsulting.com/ The cruise industry has long acknowledged the cumulative negative impact of illness outbreaks. COVID-19 presents a frightful situation. From a public health perspective, though, we shift from Distress to Redress and Address. Leader-SHIP is the newsletter that interweaves media articles and cruise industry responses to provide guidance on actions being taken against the novel coronavirus. It negates forces of disruption and decline with measures for steadfastness ultimately having you enhance the practice of public health in your own life and of those around you. PLEASE NOTE THIS ISN’T A COMPLETE LISTING OF MEDIA ARTICLES BUT A SNAPSHOT ONLY. In this Issue: - How Carnival Cruise Line Will Begin to Phase-in Cruises in August - Carnival cancels all North American cruises through July, no restart date set for New Orleans - Carnival Dangles $28-a-Night Fares for Planned Aug. 1 Restart - Cruise companies reveal whether over 70's will be banned from future sailings - Carnival to Resume Some Cruise Sailings in August After Months long Pause - Carnival Cruise Line Says It's Canceling Alaska Sailings - Gov’t denies claim of monetary request to quarantine ship workers - European Ports Open Giving Hope for Some Sailings Later This Year - Frustration as Passengers Struggle for Months Without Cruise Refunds - GAC and F-drones to develop drones for delivering supplies to vessels - Royal Caribbean Details Massive Plan to Get Crew Home - Portsmouth Marine Terminal to -
World Wide References Agip UK Tiffany Alba Bahrain Aluminium
World Wide References Agip UK Tiffany Alba Bahrain Aluminium. Alliance Refining Company Marine Terminal 3 Alliance Refining Company Production Unit North 2 American Exploration Brazos 440B American Exploration South Marsh Island 133 Atwood Oceanics Atwood Hunter Bergesen D.Y. Offshore ASA Berge Hus Bergesen D.Y. Offshore ASA Bergesen Enterprise Britannia Oil Operator Britannia Bluewater Energy Haewene Brim BP Clair BP/AIOC DUQ Platform Carnival Cruise Lines Carnival Celebration Carnival Cruise Lines Carnival Conquest Carnival Cruise Lines Carnival Destiny Carnival Cruise Lines Carnival Dream Carnival Cruise Lines Carnival Ecstasy Carnival Cruise Lines Carnival Fantasy Carnival Cruise Lines Carnival Fascination Carnival Cruise Lines Carnival Freedom Carnival Cruise Lines Carnival Elation Carnival Cruise Lines Carnival Glory Carnival Cruise Lines Carnival Holiday Carnival Cruise Lines Carnival Imagination Carnival Cruise Lines Carnival Inspiration Carnival Cruise Lines Carnival Legend Carnival Cruise Lines Carnival Liberty Carnival Cruise Lines Carnival Miracle Carnival Cruise Lines Carnival Paradise Carnival Cruise Lines Carnival Pride Carnival Cruise Lines Carnival Sensation Carnival Cruise Lines Carnival Splendor Carnival Cruise Lines Carnival Spirit Carnival Cruise Lines Carnival Triumph Carnival Cruise Lines Carnival Valor Carnival Cruise Lines Carnival Victory Celebrity Cruises Celebrity Solstice Celebrity Cruises Celebrity Equinox Centrica Rough 3B Color Line Bohus Color Line Christian IV Color Line Color Fantasy Color Line Color -
Allure of the Seas® 2021–2022 CARIBBEAN ADVENTURES
Allure of the Seas® 2021–2022 CARIBBEAN ADVENTURES Nobody does the tropics like Royal Caribbean — and in 2021-2022 we’re going bold in the tropics, with all four Oasis Class ships sailing from Florida, plus returning winter season favorites like Vision of the Seas® and Rhapsody of the Seas®. Set sail on epic getaways from Galveston and San Juan. Visit unforgettable ports like Virgin Gorda and St. Lucia. And enjoy more stops at our game- changing private destination, Perfect Day at CocoCay — and these adventures are available to book now. ITINERARY SAIL DATE PORT OF CALL 7-Night Eastern Caribbean August 8, 2021 Orlando (Port Canaveral), Florida • Cruising & Perfect Day (Overnight) • Philipsburg, St. Maarten • Charlotte Amalie, St. Thomas • Cruising • Perfect Day at CocoCay • Orlando (Port Canaveral), Florida 7-Night Western Caribbean August 15, 2021 Orlando (Port Canaveral), Florida • Cruising • & Perfect Day Costa Maya, Mexico • Roatan, Honduras • Cozumel, Mexico • Cruising • Perfect Day at CocoCay • Orlando (Port Canaveral), Florida 7-Night Eastern Caribbean August 22, 2021 Orlando (Port Canaveral), Florida • Cruising & Perfect Day (Overnight) • Basseterre, St. Kitts & Nevis • Charlotte Amalie, St. Thomas • Cruising • Perfect Day at CocoCay • Orlando (Port Canaveral), Florida 7-Night Western Caribbean August 29, 2021 Orlando (Port Canaveral), Florida • Nassau, & Perfect Day September 12, 26, 2021 Bahamas • Cruising • Falmouth, Jamaica • October 10, 24, 2021 Labadee, Haiti • Cruising • Perfect Day at CocoCay • Orlando (Port Canaveral), Florida 7-Night Eastern Caribbean September 5, 19, 2021 Orlando (Port Canaveral), Florida • Cruising & Perfect Day October 3, 17, 31, 2021 Book your next adventure today! Features vary by ship. All itineraries are subject to change without notice. -
MV Carnival Legend
Marine Safety Investigation Unit INTERIM SAFETY INVESTIGATION REPORT 201912/035 REPORT NO.: 201912/035 December 2020 The Merchant Shipping MV Carnival Legend (Accident and Incident Safety Investigation) Regulations, Allision with MV Carnival Glory, while moored 2011 prescribe that the sole in the port of Cozumel, Mexico objective of marine safety investigations carried out in 20 December 2019 accordance with the regulations, including analysis, conclusions, and recommendations, which either result from them or are part of the process thereof, shall be the prevention of future marine accidents and incidents through the ascertainment of SUMMARY causes, contributing factors and circumstances. On 20 December 2019 at about On board Carnival Glory, the Moreover, it is not the purpose 0846LT, whilst Carnival allision affected the aft guest of marine safety investigations carried out in accordance with Legend was berthed at Puerto lounge where guests were present these regulations to apportion blame or determine civil and Maya pier no. 1, Carnival Glory at the time. Six guests suffered criminal liabilities. was manoeuvring into the port. injuries, with one requiring Carnival Glory was hospital treatment. Carnival NOTE approaching pier no. 2, when Glory sustained structural This interim safety investigation report is not written with her starboard quarter allided damage to her starboard quarter, litigation in mind and pursuant to Regulation 13(7) of the with Carnival Legend’s bow. in way of the aft guest lounge. Merchant Shipping (Accident and Incident Safety Investigation) Regulations, Carnival Legend sustained This document is an interim 2011, shall be inadmissible in any judicial proceedings whose scratches and indentation to her safety investigation report, purpose or one of whose purposes is to attribute or port bow.