Stress Analysis in Bipolar Transistors By
Total Page:16
File Type:pdf, Size:1020Kb
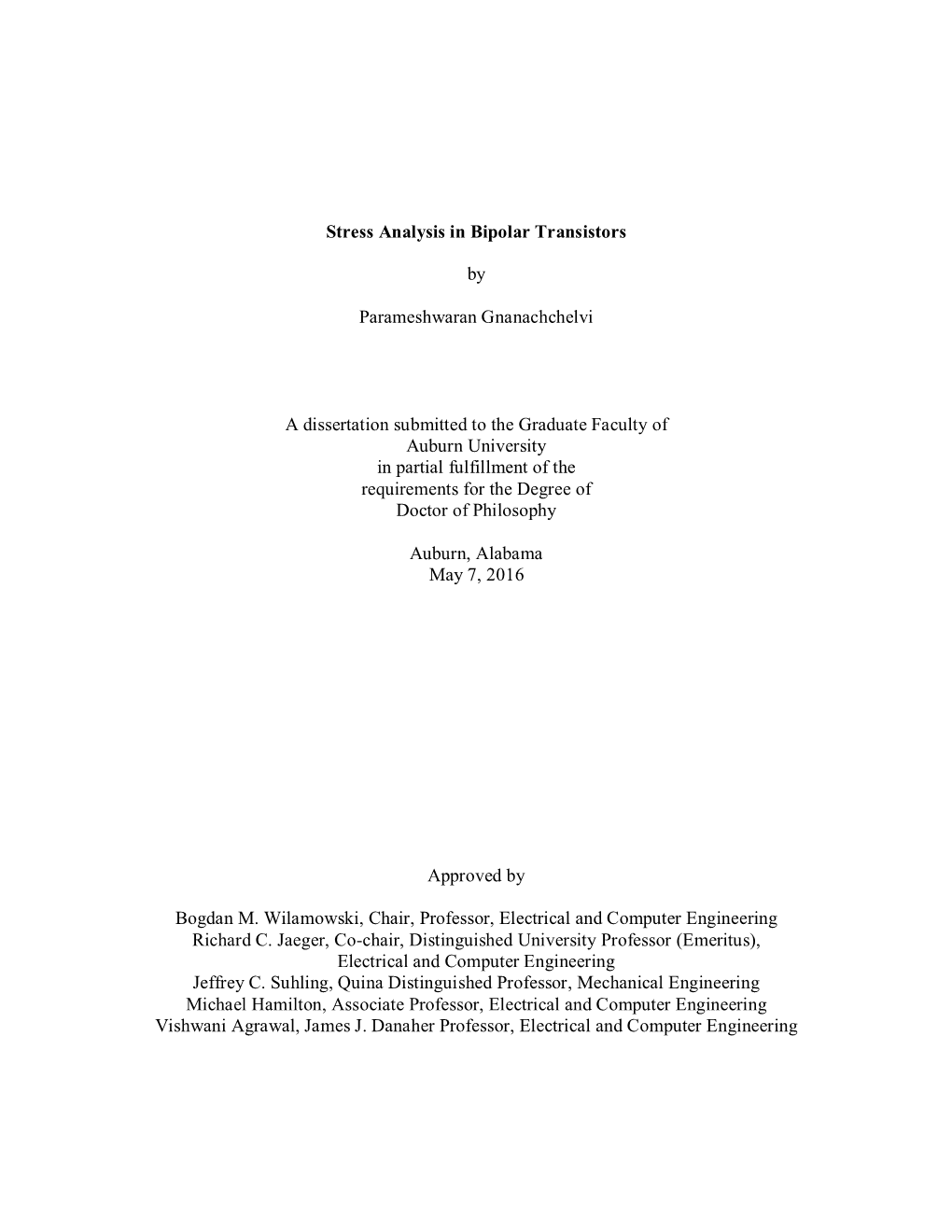
Load more
Recommended publications
-
An Apparatus for Measuring the Piezoresistivity of Semiconductors
- - --------------------- --- ~----------...., Journal of Research of the National Bureau of Standards Vol. 59 No.6, December 1957 Research Paper 2814 An Apparatus for Measuring the Piezoresistivity of Semiconductors 1 R. F. Potter 2 and W. 1. Me Kean A detailed description is given of an apparatus and procedure designed to measure t he piezoresistive effect in semiconductors over an extended temperature range. A tensile force up to 1 kilogram can be appli ed to the sample by means of a calibrated beam balance. The apparatus has been used for measurements on indium antimonide over the range 780 K to 3000 K , and tensile stresses of the order of 5 X 107 dynes per square centimeter can be applied t o samples that are cut in a special manner. In modern solid-state physics, phenomena such as a form quite analogous to that for the elastic con electrical conduction, Han effect, and optical absorp stants. The II-constants are defined as follows: tion have been studied extensively because of their direct connection with a well-developed theory of IIn = IIll, II semiconductors. More recently several other effects have been receiving an increasing amount of attention (2) by both the theorist and experimentalist; some of these are cyclotron resonance, photoelectromagnetic effect, magnetoresistivity, and piezoresistivity. The latter parameter has been studied for some X ij is the applied stress, and P is the resistivity, time in connection with m etals, but it is only in where the cubic axes are taken as the reference axes. comparatively recent years that large anisotropic The change of resistance in a material is measured changes in the resistivity with applied stress were when a stress is applied in a given direction to a measUTed for single crystals with cubic symmetry. -
Advances in Piezoresistive Probes for Atomic Force
ADVANCES IN PIEZORESISTIVE PROBES FOR ATOMIC FORCE MICROSCOPY A DISSERTATION SUBMITTED TO THE DEPARTMENT OF MECHANICAL ENGINEERING AND THE COMMITTEE ON GRADUATE STUDIES OF STANFORD UNIVERSITY IN PARTIAL FULFILLMENT OF THE REQUIREMENTS FOR THE DEGREE OF DOCTOR OF PHILOSOPHY Jonah A. Harley March 2000 ii Ó Copyright by Jonah A. Harley 2000 All Rights Reserved iii I certify that I have read this dissertation and that in my opinion it is fully adequate, in scope and quality, as dissertation for the degree of Doctor of Philosophy. __________________________________ Thomas W. Kenny (Principal Advisor) I certify that I have read this dissertation and that in my opinion it is fully adequate, in scope and quality, as dissertation for the degree of Doctor of Philosophy. __________________________________ Storrs T. Hoen I certify that I have read this dissertation and that in my opinion it is fully adequate, in scope and quality, as dissertation for the degree of Doctor of Philosophy. __________________________________ Calvin F. Quate Approved for the University Committee on Graduate Studies __________________________________ iv Abstract The atomic force microscope (AFM) is a tool that enables the measurement of precisely localized forces with unprecedented resolution in time, space and force. At the heart of this instrument is a cantilever probe that sets the fundamental limitations of the AFM. Piezoresistive cantilevers provide a simple and convenient alternative to optically detected cantilevers, and have made it easier for commercial applications to exploit the power of the force microscope. Unfortunately, piezoresistive cantilevers do not provide performance levels equal to those of the optically detected AFM. Several advances will be discussed in this work that largely erase that discrepancy, and in some cases take the capabilities of the piezoresistive cantilever beyond those of the standard AFM cantilever. -
Modeling Piezoresistivity in Silicon and Polysilicon
November 19, 2005 10:41 Journal of Applied Engineering Mathematics Volume 2 MODELING PIEZORESISTIVITY IN SILICON AND POLYSILICON Gary K. Johns Mechanical Engineering Department Brigham Young University Provo,Utah 84602 ABSTRACT INTRODUCTION The piezoresistive effect of silicon is often utilized in sen- Piezoresistivity is a material property that couples bulk elec- sors. Due to the crystalline nature of silicon, the sensitivity of trical resistivity to mechanical strain [1]. In other words, as a ma- the piezoresistive effect depends on many things including the terial is stretched, compressed, or distorted in any way, the elec- direction and magnitude of the applied stress and the orientation trical resistivity changes. Almost all materials have this property, of the crystallographic plane. A method of modeling the piezore- even though in some it is so small that it is virtually undetectable. sistive effect in silicon and poly crystalline silicon is presented. However, other materials show a large change in resistivity for a This mathematical model includes partial derivatives and linear relatively small strain. One of these materials is silicon. The algebra to combine basic electrical and mechanical equations to piezoresistive effect in silicon makes it a good candidate to use describe the change in resistivity as a function of stress. An ex- as a sensor. A sensor element is a device that converts one form periment was used to verify the model. The analytical solution of energy into another [2]. An element made from silicon can and experimental results agree. The model presented in this pa- be designed to be a sensor since the piezoresistive property links per is adequate to predict the behavior of a piezoresistive sensor strain energy to change in resistance (electrical energy). -
The Piezojunction Effect in Silicon, Its Consequences and Applications for Integrated Circuits and Sensors
The Piezojunction Effect in Silicon, its Consequences and Applications for Integrated Circuits and Sensors The Piezojunction Effect in Silicon, its Consequences and Applications for Integrated Circuits and Sensors PROEFSCHRIFT ter verkrijging van de graad van doctor aan de Technische Universiteit Delft, op gezag van de Rector Magnificus prof. Ir. K. F. Wakker, voorzitter van het College voor Promoties, in het openbaar te verdedigen op maandag 24 september 2001 om 10:30 uur door Fabiano FRUETT master in electric engineering, UNICAMP, Brazil geboren te São Caetano do Sul, Brazil Dit proefschrift is goedgekeurd door de promotor: Prof. dr. ir. A.H.M. van Roermund Togevoegd promotor: Dr. ir. G.C.M. Meijer Samenstelling promotiecommissie: Rector Magnificus, Technische Universiteit Delft, voorzitter Prof. dr. ir. A.H.M. van Roermund,Technische Universiteit Delft, promotor Dr. ir. G.C.M. Meijer, Technische Universiteit Delft, toegevoegd promotor Prof. dr ir. R. Puers, Katholieke Universiteit Leuven, Belgium Prof. ir. A.J.M. van Tuijl, Philips Research Laboratories, Eindhoven Dr. C.A. dos Reis Filho, Univesridade Estadual de Campinas, Brazil Prof. dr. ir. J.W. Slotboom, Technische Universiteit Delft Prof. dr. ir. J.H. Huijsing, Technische Universiteit Delft Published and distributed by: DUP Science DUP Science is an imprint of Delft University Press P.O. Box 98 2600 MG Delft The Netherlands Phone: +31 15 27 85 678 Fax: +31 15 27 85 706 E-mail: [email protected] ISBN 90-407-2226-9 Keywords: piezojunction effect, analogue integrated circuit and mechanical-stress sensor. Copyright 2001 by Fabiano Fruett All rights reserved. No part of the material protected by this copyright notice may be reproduced or utilized in any form or by means, electronic or mechanical, including photocopying, recording, or by any information storage and retrieval system, without written permission from the publisher: Delft University Press. -
Characteristic and Analysis of Silicon Germanium Material As MEMS Pressure Sensor
Available online www.jocpr.com Journal of Chemical and Pharmaceutical Research, 2015, 7(1):411-415 ISSN : 0975-7384 Research Article CODEN(USA) : JCPRC5 Characteristic and analysis of silicon germanium material as MEMS pressure sensor S. Maflin Shaby Dept of Electronics and Telecommunication Engineering, Sathyabama University, Chennai, India _____________________________________________________________________________________________ ABSTRACT The silicon based pressure sensor is one of the major applications of the piezoresistive sensor. This paper focuses on the structural design and optimization of the MEMS piezoresistive pressure sensor to enhance the sensitivity. A finite element method (FEM) is adopted for designing the performance of a silicon based piezoresistive pressure sensor. Thermal as well as pressure loading on the sensor is applied to make a simulation results. In order to achieve better sensor performance, a parametric analysis is performed to evaluate the system output sensitivity of the pressure sensor. The design parameters of the pressure sensor include the location of piezoresistors and the new structural material used for designing of the piezoresistors in the membrane is poly-Silicon Germanium in which germanium is about 60%. The findings depict that proper selection of the piezoresistors location and the new structural material of the piezoresistors in the membrane can enhance the sensor sensitivity. Keywords: Piezoresistors, sensor, parametric analysis, silicon germanium, piezoresistivity, sensitivity _____________________________________________________________________________________________ INTRODUCTION The silicon based pressure sensor is one of the major applications of the piezoresistive sensor. Nowadays, silicon piezoresistive pressure sensor is a matured technology in industry and its measurement accuracy is more rigorous in many advanced applications. The fundamental concept of piezoresistive effect is the change in receptivity of a material resulting from an applied stress. -
Electromechanical Piezoresistive Sensing in Suspended Graphene
This document is the unedited Author’s version of a Submitted Work that was subsequently accepted for publication in Nano Letters, copyright © American Chemical Society after peer review. To access the final edited and published work see http://pubs.acs.org/articlesonrequest/AOR-kGn5XaTPGiC7mYUQfih3. Electromechanical Piezoresistive Sensing in Suspended Graphene Membranes A.D. Smith1, F. Niklaus1, A. Paussa2, S. Vaziri1, A.C. Fischer1, M. Sterner1, F. Forsberg1, A. Delin1, D. Esseni2, P. Palestri2, M. Östling1, M.C. Lemme1,3,* 1 KTH Royal Institute of Technology, Isafjordsgatan 22, 16440 Kista, Sweden, 2 DIEGM, University of Udine, Via delle Scienze 206, 33100 Udine, Italy 3University of Siegen, Hölderlinstr. 3, 57076 Siegen, Germany * Corresponding author: [email protected] Abstract Monolayer graphene exhibits exceptional electronic and mechanical properties, making it a very promising material for nanoelectromechanical (NEMS) devices. Here, we conclusively demonstrate the piezoresistive effect in graphene in a nano- electromechanical membrane configuration that provides direct electrical readout of pressure to strain transduction. This makes it highly relevant for an important class of nano-electromechanical system (NEMS) transducers. This demonstration is consistent with our simulations and previously reported gauge factors and simulation values. The membrane in our experiment acts as a strain gauge independent of crystallographic orientation and allows for aggressive size scalability. When compared with conventional pressure sensors, the sensors have orders of magnitude higher sensitivity per unit area. Keywords: graphene, pressure sensor, piezoresistive effect, nanoelectromechanical systems (NEMS), MEMS 2 Graphene is an interesting material for nanoelectromechanical systems (NEMS) due to its extraordinary thinness (one atom thick), high carrier mobility 1,2, a high Young’s modulus of about 1 TPa for both pristine (exfoliated) and chemical vapor deposited (CVD) graphene.3,4 Graphene is further stretchable up to approximately 5 6 20%. -
A Model for Predicting the Piezoresistive Effect in Microflexures Experiencing Bending and Tension Loads
Brigham Young University BYU ScholarsArchive Faculty Publications 2008-02-07 A Model for Predicting the Piezoresistive Effect in Microflexures Experiencing Bending and Tension Loads Gary K. Johns [email protected] Larry L. Howell [email protected] Brian D. Jensen Timothy W. McLain [email protected] Follow this and additional works at: https://scholarsarchive.byu.edu/facpub Part of the Mechanical Engineering Commons BYU ScholarsArchive Citation Johns, Gary K.; Howell, Larry L.; Jensen, Brian D.; and McLain, Timothy W., "A Model for Predicting the Piezoresistive Effect in Microflexures Experiencing Bending and Tension Loads" (2008). Faculty Publications. 202. https://scholarsarchive.byu.edu/facpub/202 This Peer-Reviewed Article is brought to you for free and open access by BYU ScholarsArchive. It has been accepted for inclusion in Faculty Publications by an authorized administrator of BYU ScholarsArchive. For more information, please contact [email protected], [email protected]. 226 JOURNAL OF MICROELECTROMECHANICAL SYSTEMS, VOL. 17, NO. 1, FEBRUARY 2008 A Model for Predicting the Piezoresistive Effect in Microflexures Experiencing Bending and Tension Loads Gary K. Johns, Larry L. Howell, Fellow, ASME, Brian D. Jensen, Member, ASME,and Timothy W. McLain, Senior Member, IEEE Abstract—This paper proposes a model for predicting the or a membrane). In the proposed integrated piezoresistive self- piezoresistive effect in microflexures experiencing bending sensing devices, however, rather than the piezoresistive element stresses. Linear models have long existed for describing piezore- being part of the flexure, it is the flexure. The loading condi- sistivity for members in pure tension and compression. However, extensions of linear models to more complex loading conditions tions for such sensors are more complex than pure tension or do not match with experimental results. -
Research of Piezo-Resistive and Piezoelectric Sensor Sanming Feng A
3rd International Conference on Mechatronics and Industrial Informatics (ICMII 2015) Research Of Piezo-resistive And Piezoelectric Sensor a b,* c Sanming Feng ,Wenjie Tian , Bo Ma Beijing Information Science and Technology University 100101,Beijing,China [email protected], b [email protected], [email protected] * Corresponding Author Keywords: pressure sensor; tantalum nitride; PVDF; circuit Abstract. The basic principle and application of piezo-resistive and piezoelectric are expounded. Also the method of deposition of tantalum nitride on the glass to fabricate piezo-resistive pressure sensor, and the method of a plurality of piezoelectric thin film in parallel to form a high sensitivity sensor are introduced. Besides, a power supply circuit and corresponding processing circuit are designed. The output voltage of the piezo-resistive pressure sensor is liner with respect to the pressure. The output of the charge is liner with the pressure of piezoelectric sensor first, then tends to saturation and presents less change. The sensitivity of piezoelectric sensor is up to 103 orders of magnitude, with a higher sensitivity. Introduction Sensor is the first threshold of the information system, which is responsible for collecting information. Sensor technology, communication technology and computer technology have become the three pillars of modern information technology [1], is an important basis for the information industry, so the importance of sensor technology is self-evident. At present, the sensor industry in China is small, and the application scope is narrow. Therefore, we need to change the concept, the research and development of the sensor is developed by a single sensor, which is transformed into a new type of high integration. -
Piezoresistance in Silicon and Its Nanostructures Author
Title: Piezoresistance in Silicon and its nanostructures Author: A. C. H. Rowe Affiliation: Physique de la matière condensée, Ecole Polytechnique, CNRS Address: Route de Saclay, 91128 Palaiseau, France Email: [email protected] Telephone: +33 (0)1 6933 4787 Best figure representation of work: Figure 4 Keywords: piezoresistance, Silicon, nanowires Abstract: Piezoresistance (PZR) is the change in the electrical resistivity of a solid induced by an applied mechanical stress. Its origin in bulk, crystalline materials like Silicon, is principally a change in the electronic structure which leads to a modification of the charge carriers’ effective mass. The last few years have seen a rising interest in the PZR properties of semiconductor nanostructures, motivated in part by claims of a giant PZR in Silicon nanowires more than two orders of magnitude bigger than the known bulk effect. This review aims to present the controversy surrounding claims and counter-claims of giant PZR in Silicon nanostructures by summarizing the major works carried out over the last 10 years. The main conclusions to be drawn from the literature are that i) reproducible evidence for a giant PZR in un-gated nanowires is limited, ii) in gated nanowires giant PZR has been reproduced by several authors, iii) the giant effect is fundamentally different from either the bulk Silicon PZR or that due to quantum confinement, the evidence pointing to an electrostatic origin, iv) released nanowires tend to have slightly larger PZR than un-released nanowires, and v) insufficient work has been performed on bottom-up grown nanowires to be able to rule out a fundamental difference in their properties when compared with top-down nanowires. -
Piezoelectric and Piezoresistive Instrumentation By: Kris Hyblova, Abby Covrig, Kyron Heinrich
3/4/20 Piezoelectric and Piezoresistive Instrumentation By: Kris Hyblova, Abby Covrig, Kyron Heinrich Direct Piezoelectric Effect 1 3/4/20 Inverse Piezoelectric Effect Piezoelectric Materials Materials • Single Crystal: • Quartz, Lithium Niobate (LiNbO3), and Lithium Tantalate (LiTaO3) • Surface Acoustic Wave devices (SAWs), dynamic pressure sensors • PolyCrystal: • Barium titanate (BaTiO3), Piezoelectric Pb(Ti,Zr)O3 solid solutions (PZT) ceramics • Polymers: • Polyvinylidene difluoride (PVDF) • Drawn and stretched to polar phase 2 3/4/20 Piezoelectric properties General Purpose Pressure Sensor • Measurement Range: 200 psi (1379 kPa) • Sensitivity: (±15%) 25 mV/psi (3.6 mV/kPa) • Low Frequency Response: (-5%) 0.5 Hz • Resonant Frequency: >=500 kHz (>=500 kHz) • Electrical Connector: 10-32 Coaxial Jack • Weight: 0.21 oz (6.0 gm) 3 3/4/20 Sensors • Piezoelectric sensors are required for specific applications • turbulence, blast, ballistics, and engine combustion • (Not good for static pressure applications ) What is Piezoresistive Effect? • Material: semi-conductors (mainly silicon) • A stress changes the resistivity of the material The Piezoresistive Effect: Change in the electrical resistivity of a semiconductor or metal when mechanical strain is applied. 4 3/4/20 Example • Strain Gauge • Silicon • adding various elements -> Regions with more or less electrons • Changes resitivity in certain areas • N and P sections create sensing 'wires' DMP333 High Range Precision Pressure Transmitter (incorporates a silicon piezoresistive sensing element) -
Sensors and Actuators a 319 (2021) 112519
Sensors and Actuators A 319 (2021) 112519 Contents lists available at ScienceDirect Sensors and Actuators A: Physical journal homepage: www.elsevier.com/locate/sna Active atomic force microscope cantilevers with integrated device layer piezoresistive sensors ∗ Michael G. Ruppert , Andrew J. Fleming, Yuen K. Yong University of Newcastle, Callaghan, NSW 2308, Australia a r t i c l e i n f o a b s t r a c t Article history: Active atomic force microscope cantilevers with on-chip actuation and sensing provide several advan- Received 8 October 2020 tages over passive cantilevers which rely on piezoacoustic base-excitation and optical beam deflection Received in revised form 7 December 2020 measurement. Active microcantilevers exhibit a clean frequency response, provide a path-way to mini- Accepted 18 December 2020 turization and parallelization and avoid the need for optical alignment. However, active microcantilevers Available online 18 January 2021 are presently limited by the feedthrough between actuators and sensors, and by the cost associated with custom microfabrication. In this work, we propose a hybrid cantilever design with integrated piezoelec- Keywords: tric actuators and a piezoresistive sensor fabricated from the silicon device layer without requiring an Atomic force microscopy additional doping step. As a result, the design can be fabricated using a commercial five-mask microelec- Active cantilevers tromechanical systems fabrication process. The theoretical piezoresistor sensitivity is compared with Microelectromechanical systems (MEMS) Piezoelectric actuators finite element simulations and experimental results obtained from a prototype device. The proposed Piezoresistive sensors approach is demonstrated to be a promising alternative to conventional microcantilever actuation and deflection sensing. -
Technology Brief 4: Resistors As Sensors Piezoresistive Sensors
56 TECHNOLOGY BRIEF 4: RESISTORS AS SENSORS Technology Brief 4: Resistors as Sensors The relationship between the voltage across a conductor and the current through it is given by Ohm’s law, V = IR. The resistance R of the conductor accounts for the reduction in the electrons’ velocities due to collisions with the much larger atoms of the conducting material (see Technology Brief 3 on page 38). The question is: What happens to R if we disturb the atoms of the conductor by applying an external, non-electrical stimulus, such as heating or cooling it, stretching or compressing it, or shining light on it? Through proper choice of materials, we actually can modulate (change) the magnitude of R by applying such external stimuli, and this forms the basis of many common sensors. Piezoresistive Sensors In 1856, Lord Kelvin discovered that applying a mechanical load on a bar of metal changed its resistance. Over the next 150 years, both theoretical and practical advances made it possible to describe the physics behind this effect in both conductors and semiconductors. The phenomenon is referred to as the piezoresistive effect (Fig. TF4-1) and is used in many practical devices to convert a mechanical signal into an electrical one. Such sensors (Fig. TF4-2) are called strain gauges. Piezoresistive sensors are used in a wide variety of consumer applications, including robot toy “skins” that sense force, microscale gas-pressure sensors, and micromachined accelerometers that sense acceleration. They all use piezoresistors in electrical circuits to generate a signal from a mechanical stimulus. In its simplest form, a resistance change R occurs when a mechanical pressure P (N/m2) is applied along the axis of the resistor (Fig.