Returns to Scale: Concept, Estimation and Analysis of Japan's Turbulent
Total Page:16
File Type:pdf, Size:1020Kb
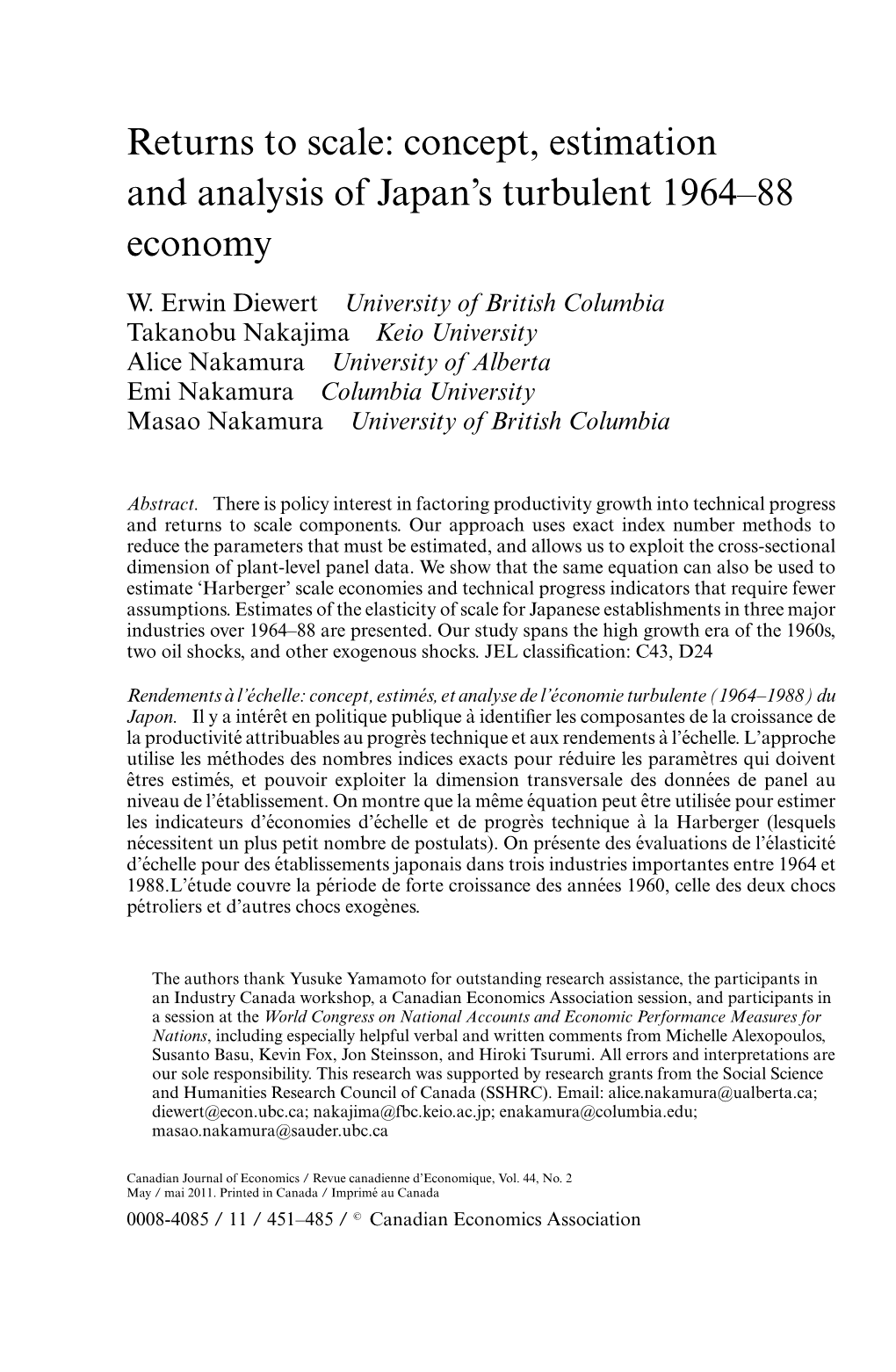
Load more
Recommended publications
-
Internal Increasing Returns to Scale and Economic Growth
NBER TECHNICAL WORKING PAPER SERIES INTERNAL INCREASING RETURNS TO SCALE AND ECONOMIC GROWTH John A. List Haiwen Zhou Technical Working Paper 336 http://www.nber.org/papers/t0336 NATIONAL BUREAU OF ECONOMIC RESEARCH 1050 Massachusetts Avenue Cambridge, MA 02138 March 2007 The views expressed herein are those of the author(s) and do not necessarily reflect the views of the National Bureau of Economic Research. © 2007 by John A. List and Haiwen Zhou. All rights reserved. Short sections of text, not to exceed two paragraphs, may be quoted without explicit permission provided that full credit, including © notice, is given to the source. Internal Increasing Returns to Scale and Economic Growth John A. List and Haiwen Zhou NBER Technical Working Paper No. 336 March 2007 JEL No. E10,E22,O41 ABSTRACT This study develops a model of endogenous growth based on increasing returns due to firms? technology choices. Particular attention is paid to the implications of these choices, combined with the substitution of capital for labor, on economic growth in a general equilibrium model in which the R&D sector produces machines to be used for the sector producing final goods. We show that incorporating oligopolistic competition in the sector producing finals goods into a general equilibrium model with endogenous technology choice is tractable, and we explore the equilibrium path analytically. The model illustrates a novel manner in which sustained per capita growth of consumption can be achieved?through continuous adoption of new technologies featuring the substitution between capital and labor. Further insights of the model are that during the growth process, the size of firms producing final goods increases over time, the real interest rate is constant, and the real wage rate increases over time. -
The Historical Role of the Production Function in Economics and Business
American Journal of Business Education – April 2011 Volume 4, Number 4 The Historical Role Of The Production Function In Economics And Business David Gordon, University of Saint Francis, USA Richard Vaughan. University of Saint Francis, USA ABSTRACT The production function explains a basic technological relationship between scarce resources, or inputs, and output. This paper offers a brief overview of the historical significance and operational role of the production function in business and economics. The origin and development of this function over time is initially explored. Several various production functions that have played an important historical role in economics are explained. These consist of some well known functions, such as the Cobb-Douglas, Constant Elasticity of Substitution (CES), and Generalized and Leontief production functions. This paper also covers some relatively newer production functions, such as the Arrow, Chenery, Minhas, and Solow (ACMS) functions, the transcendental logarithmic (translog), and other flexible forms of the production function. Several important characteristics of the production function are also explained in this paper. These would include, but are not limited to, items such as the returns to scale of the function, the separability of the function, the homogeneity of the function, the homotheticity of the function, the output elasticity of factors (inputs), and the degree of input substitutability that each function exhibits. Also explored are some of the duality issues that potentially exist between certain production and cost functions. The information contained in this paper could act as a pedagogical aide in any microeconomics-based course or in a production management class. It could also play a role in certain marketing courses, especially at the graduate level. -
Increasing Returns to Scale, Dynamics of Industrial Structure and Size Distribution of Firms†
Increasing Returns to Scale, Dynamics of Industrial Structure and Size Distribution of Firms† Ying Fan, Menghui Li, Zengru Di∗ Department of Systems Science, School of Management, Beijing Normal University, Beijing 100875, China _______________________________________________________________________ Abstract A model is presented of the market dynamics to emphasis the effects of increasing returns to scale, including the description of the born and death of the adaptive producers. The evolution of market structure and its behavior with the technological shocks are discussed. Its dynamics is in good agreement with some empirical “stylized facts” of industrial evolution. Together with the diversities of demand and adaptive growth strategies of firms, the generalized model has reproduced the power-law distribution of firm size. Three factors mainly determine the competitive dynamics and the skewed size distributions of firms: 1. Self-reinforcing mechanism; 2. Adaptive firm grows strategies; 3. Demand diversities or widespread heterogeneity in the technological capabilities of different firms. JEL classification: L11, C61 Key words: Increasing returns, Industry dynamics, Size distribution of firms _______________________________________________________________________ Ⅰ. INTRODUCTION In the past decades, the evolutionary perspective has contributed lot to the economics (Arthur, Durlauf, and Lane, 1997; Dosi, Nelson, 1994; Aruka, 2001). The economy is studied as an evolving complex system with many features in complexity such as nonlinear interactions and emergent properties. In reality, the economic system consists † The paper has been presented in the 1st Sino-German workshop on the evolutionary economics, March, 2004, Beijing, China. The authors thank all the participants for their helpful comments and suggestions. The work is supported by the NSFC under the grant No. 70371072 and grant No. -
Returns to Scale and Size in Agricultural Economics
Returns to Scale and Size in Agricultural Economics John W. McClelland, Michael E. Wetzstein, and Wesley N. Musser Differences between the concepts of returns to size and returns to scale are systematically reexamined in this paper. Specifically, the relationship between returns to scale and size are examined through the use of the envelope theorem. A major conclusion of the paper is that the level of abstraction in applying a cost function derived from a homothetic technology within a relevant range of the expansion path may not be severe when compared to the theoretical, estimative, and computational advantages of these technologies. Key words: elasticity of scale, envelope theorem, returns to size. Agricultural economists investigating long-run scale, Euler's theorem, and the form of pro- relationships among levels of inputs, outputs, duction functions. However, the direct link be- and costs generally use concepts of returns to tween returns to size and scale is not devel- scale and size. Econometric studies which uti- oped. Hanoch investigates the elasticity of scale lize production or profit functions commonly and size in terms of variation with output and are concerned with returns to scale (de Janvry; illustrates that only at the cost-minimizing in- Lau and Yotopoulos), while synthetic studies put combinations are the two concepts equiv- of relationships between output and cost uti- alent. Hanoch further provides a proposition lize returns to size (Hall and LaVeen; Rich- stating that Frisch's "Regular Ulta-Passum ardson and Condra). However, as noted by Law" is neither necessary nor sufficient for a Bassett, the word scale is sometimes also used production technology to be associated with to mean size (of a plant). -
Price Dispersion and Increasing Returns to Scaleଝ
Journal of Economic Behavior & Organization 73 (2010) 406–417 Contents lists available at ScienceDirect Journal of Economic Behavior & Organization journal homepage: www.elsevier.com/locate/jebo Price dispersion and increasing returns to scaleଝ David M. Levy a, Michael D. Makowsky b,∗ a Department of Economics, George Mason University, United States b Department of Economics, Towson University, United States article info abstract Article history: We present a model in which price dispersion allows the market to remain competitive Received 28 April 2008 in the long run amidst increasing returns to scale. The model hinges upon turnover in the Received in revised form 7 October 2009 productive technology-leading firm, price dispersion resultant of Stigler’s logic of rational Accepted 9 October 2009 search, and limited excludability of knowledge. Price dispersion, traditionally viewed as Available online 23 October 2009 an efficiency loss derivative of imperfect information in the market protects competition from being destroyed by innovation and increasing returns to scale. Bankruptcy occurs in JEL classification: a form similar to the gambler’s ruin. The model requires no entry or replacement of failed C63 L11 firms. The number of active firms in a market reaches a stationary state increasing with, O33 and contingent on, search costs. D83 © 2009 Elsevier B.V. All rights reserved. Keywords: Increasing returns to scale Price dispersion Search “Professor Chamberlin was right in concluding that perfect competition is a poor instrument in analyzing selling costs. His results might have been more informative, however, if he had chosen to drop the assumption that the economy was stationary, rather than the assumption that the economy was competitive.” – George J. -
The Conflict Between General Equilibrium and the Marshallian
Munich Personal RePEc Archive The Conflict Between General Equilibrium and the Marshallian Cross Saglam, Ismail and Zaman, Asad September 2010 Online at https://mpra.ub.uni-muenchen.de/40275/ MPRA Paper No. 40275, posted 26 Jul 2012 13:32 UTC The Conflict Between General Equilibrium and the Marshallian Cross By Ismail Saglam1 and Asad Zaman2 Abstract. There is a conflict in the mechanism for price determination used in a Marshallian partial equilibrium supply and demand framework and the Walrasian general equilibrium framework. It is generally thought that partial equilibrium is a simplified approximation to the complexities of the general model. The goal of this paper is to show that there is a strong conflict between the two models – intuitions and heuristics suggested by partial equilibrium are contradicted by extensions to the general equilibrium case. We review the literature on the conflict and also provide a very simple model where partial equilibrium analysis fails completely. Several intuitively plausible remedies fail to restore partial equilibrium results. We show that Marshallian analysis can be made to work only under rather stringent conditions requiring joint production with low fixed costs and decreasing returns resulting in identical production proportions by all producers. 1Corresponding author. [email protected], Department of Economics, TOBB University of Economics and Technology. [email protected], International Institute of Islamic Economics, International Islamic University. 1 Introduction Today most economic analysis as well as the majority of elementary textbooks explain price determinations via the partial equilibrium method, which gained its distinction with the publication of the first edition of Principles of Economics in 1890 by Alfred Marshall. -
Resource Limitations, the Demand for Education and Economic Growth--A Macroeconomic View
DOCUMENT RESUME ED 053 282 VT 010 927 AUTHOR Stam, Jerome M. TITLE Resource Limitations, the Demand for Education and Economic Growth--A Macroeconomic View. INSTITUTION Michigan State Univ., East Lansing. Dept. of Agricultural Economics. SPONS AGENCY Economic Research Service (DOA), Washington, D.C. REPORT NO AER-147 PUB DATE Aug 69 NOTE 32p. EDRS PRICE EDRS Price MF-$0.65 HC-$3.29 DESCRIPTORS *Economic Development, *Economic Factors, *Human Resources, *Input Output Analysis, *Models ABSTRACT To develop a theoretical framework for explaining the observed change in demand for human skill and knowledge that occurs with economic growth, a macroeconomic analysis was made of economic variables which are influenced by political, social, and cultural factors. In the three-dimensional framework, total output (Y) of all final goods and services produced in the economy during one specified time period is treated as a function of three inputs, capital (K), labor (L), and natural resources (R). Because the framework contains only four variables, an entire economy can be theoretically analyzed. Thus, to demonstrate how the need for human skill and knowledge is generated, an analysis of economic development reveals that as more complex forms of non-human capital are required, more human capital is also require .The demand for human skill and knowledge is largely a function of factor disproportions among the basic inputs, K, Le and R which generate certain basic forces. (SB) '' yenrrn rICo 141 LC uJ Agricultural Economics Report REPORT NO. 147 AUGUST 1969 RESOURCE LIMITATIONS, THE DEMAND FOR EDUCATION AND ECONOMIC GROWTH-A MACROECONOMIC VIEW U.S. DEPARTMENT OF HEALTH, EOUCATION & WELFARE OFFICE OF EOUCATION THIS DOCUMENT HAS BEEN REPRODUCED EXACTLY AS RECEIVED FROM THE PERSON OR ORGANIZATION ORIGI iATING IT. -
Marginal Rate of Technical Substitution
Review of Consumer Choice 1 1. Consumer’s problem • Which factors determine consumer’s choice? 2. Single consumer’s demand function 3. What happens when some variables change? • Income changes • Price changes • Why is this important? 4. Example of an economic model: • Difference between exogenous and endogenous variables. • Role of the assumptions New topic: Producer’s Choice 2 Key question: Price What factors influence supply? Supply 700 Eu • 400 Eu • 0 600 1500 Quantity Firm’s decisions 3 Each firm has to decide 1. To operate or not? 2. Which product(s) to produce? 3. Which materials and in which combinations to use? 4. How many units to produce? Production Function 4 Resources, such as labor and capital equipment, that firms use to manufacture goods and services are called inputs or factors of production. The amount of goods and services produced by the firm is the firm’s output. The production function gives the maximum amount of output the firm can produce for any given quantity of inputs. Production Function 5 The production function gives the maximum amount of output the firm can produce for any given quantity of inputs. Example: One input 1 Q f (L) L2 Q = f(L) D 7 • 4 • C Labor 16 49 Example 6 Suppose that a firm produces only with labor and the production function is 푄 = 퐹 퐿 = 퐿 That is, L units of labor produce 퐿 units of output. If the firm has to pay a wage of w=$10 for each unit of labor and can sell each unit of output for the price p=$10, how many units will the firm produce? Production Function 7 Ipad 2: • The tablet itself is assembled in China (and by the end of 2011 also in Brazil) by Taiwan-based Foxconn. -
Economics 101A (Lecture 15)
Economics 101A (Lecture 15) Stefano DellaVigna March 9, 2017 Outline 1. Cost Minimization: Example 2. Cost Curves and Supply Function 1 Cost Minimization: Example Continue example above: = ( )= • Cost minimization: • min + = What is the return to scale for this example? • Increase of all inputs: (z) with scalar, 1 • How much does input increase? • — Decreasing returns to scale: for all z and 1 (z) (z) — Constant returns to scale: for all z and 1 (z)= (z) — Increasing returns to scale: for all z and 1 (z) (z) Returns to scale depend on + 1: ( )= • ≶ () () = + = + ( ) Solutions: • — Optimal amount of labor: 1 + −+ ∗ ( )= µ¶ Ã ! — Optimal amount of capital: 1 + −+ ∗ ( )= = µ¶ Ã ! 1 + + = µ¶ Ã ! Check various comparative statics: • — ∗ 0 (technological progress and unem- ployment) — ∗ 0 (more workers needed to produce more output) — ∗ 0∗ 0 (substitute away from more expensive inputs) Parallel comparative statics for • ∗ Cost function • ( )=∗ ( )+∗ ( )= 1 + + − + = ⎡ ³ ´ ⎤ µ¶ + ⎢ + ⎥ ⎢ ⎥ ⎣ ³ ´ ⎦ Define := −+ + + • ³ ´ ³ ´ Cost-minimizing output choice: • 1 + max − µ¶ First order condition: • 1 (+) 1 −+ =0 − + µ¶ Second order condition: • 1 2(+) 1 1 ( + ) −+ − 2 − + + µ¶ When is the second order condition satisfied? • Solution: • — + =1(CRS): S.o.c.equalto0 ∗ Solution depends on ∗ For produce ∗ ∗ →∞ For = produce any [0 ) ∗ ∗ ∈ ∞ For produce =0 ∗ ∗ — + 1 (IRS): S.o.c. positive ∗ Solution of f.o.c. is a minimum! ∗ Solution is ∗ ∗ →∞ Keep increasing production since higher pro- ∗ duction is associated with higher returns — + 1 (DRS): s.o.c. negative. OK! ∗ Solution of f.o.c. is an interior optimum ∗ This is the only "well-behaved" case under per- ∗ fect competition Here can define a supply function ∗ 2CostCurves Nicholson, Ch. 10, pp. 341-349; Ch. -
Growth and Ideas
Growth and Ideas Prof. Lutz Hendricks Econ520 February 19, 2021 1 / 29 Questions 1. How does TFP growth come about? 2. What types of policies could manipulate long-run growth? The dominant view today: Innovation (the production of new "ideas") is what drives TFP growth. 2 / 29 Objectives In this section you will learn: 1. how ideas differ from ordinary goods (non-rivalry) 2. how non-rivalry generates scale effects 3. how scale effects make sustained growth possible 3 / 29 Ideas We take the view that productivity growth is due to new "ideas". Ideas are broadly defined to include: I Designs for new products: the microchip, the steam engine,... I New ways of organizing production: Walmart, the assembly line. Key assumption: Ideas are produced like other goods. I By profit maximizing firms. I The profit of innovation is the rent of owning a patent. The stock of knowledge is a form of capital. 4 / 29 Non-rivalry How then do ideas differ from physical capital? I they are produced by investing goods I they are accumulated over time There is just one difference: non-rivalry 5 / 29 Non-rivalry Most goods are rival I only a limited number of people can use a good at the same time I examples: cars, computers, ... Ideas can be used by many at the same time. I software, music I product designs (blueprints) I production methods (just-in-time production, assembly line). 6 / 29 Why Does Non-rivalry Matter? We know: capital accumulation cannot sustain growth. We will show: Accumulation of non-rival “knowledge capital” can sustain growth. -
202ARE Lecture Notes
ARE 202: Welfare: Tools and Applications Spring 2018 Thibault FALLY Lecture Notes 05 – Production and Industry Equilibrium ARE202 - Lec 05 - Production 1 / 38 Production side Topics for a brief intro: Returns to scale : crucial in applied micro, growth, development, trade Producer surplus and profits as measure of welfare in partial eq. Industry equilibrium with free entry : yields zero profits in long term, and other implications for aggregate production function, etc. Beyond firms: I want to talk about equilibrium on factor markets and return to factors Putting firms and factors together: “Production Possibility Frontier” Imperfect competition: monopoly pricing and monopolistic competition ARE202 - Lec 05 - Production 2 / 38 Plan A- Tools 1) Returns to scale 2) Producer surplus and duality in supply side 3) Industry equilibrium with free entry 4) Equilibrium on factor markets 5) Monopolistic competition B- Illustration Costinot and Donaldson (2016): Illustrate how to recover PPF and equilibrium prices in Agriculture from output and sales data across US counties, and how to infer gains from economic integration and productivity improvements (1880-1997) ARE202 - Lec 05 - Production 3 / 38 Returns to scale Consider production function Y = f (L1, L2, ... ) with inputs Lf Constant returns to scale (CRS): f (λL1, λ L2, ... ) = λF (L1, L2, ... ) for any λ > 0 CRS, increasing or decreasing returns to scale? f (L) = aL − b? ρ ρ 1 f (L, K) = [ aLL + aK K ] ρ ? f (L, K) = aL αK β? 2 log f (L, K) = aL log L + aK log K + aKL (log K − log L) ? (see also translog production functions) IRS often modeled with a fixed cost (see IRS example above) In these examples: elasticity of substitution between K and L? ARE202 - Lec 05 - Production 4 / 38 Returns to scale CRS often assumed in macro or trade (see later slides with free entry) Note: Any DRS industry can be re-interpreted as CRS: Just add a specific factor (hypothetical or not). -
Increasing Returns and Unemployment Theory
Increasingreturns and unemploymenttheory Increasingreturns and the foundationsof unemploymenttheory: an explanation MARTIN L. WEITZMAN I would like to express my gratitudeto the contributorsfor their stimu- lating comments and to the editor for kindly providing me with an opportunityto reply. There is much in the comments with which I agree, and from which I have learned. I certainlywish I had expressed myself more clearly on certain points in the article. I hope that my remarks here will help to clarify some of these points. At first I thoughtI would replyto each commentby addressing,more or less systematically and exhaustively,the specific issues they were raising. Now I am not so sure that is the best approach.The issues are too disparate, and some of them, if I may be excused for expressing myself so directly,seem to me beside the point. Instead,I thinkit would be more fruitfulif I tried to restatemy general thesis, in words, taking into accountas best I can the criticisms that seem to me most relevant. My immediatepoint of departureis the "Keynesian message." By that term I have in mind not anotherrendition of what Keynes meant in The General Theory. (I am not particularlyqualified, in any event, to give such a rendition.) I have in mind more the spirit of that which constitutes what might be called the Keynesian outlook or economic philosophy. Now this "spirit" is hardlyan objective entity, and need- less to say it is my interpretationof it which is here recorded.Neverthe- less, and allowing for normalhuman differences in perception,I would hope there might be rough agreementon those features I am about to highlight.