View Annual Report
Total Page:16
File Type:pdf, Size:1020Kb
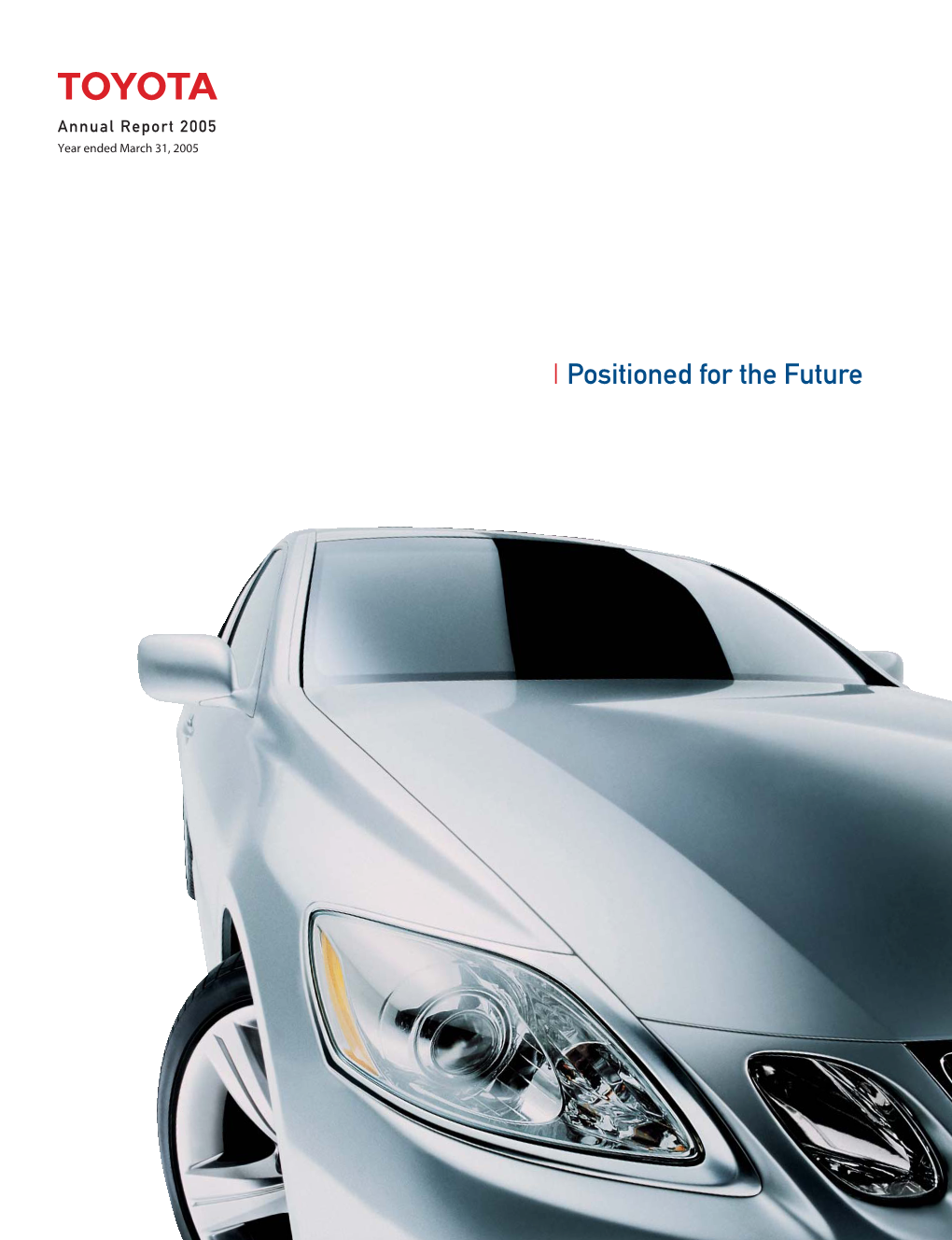
Load more
Recommended publications
-
Contacts in Japan Contacts in Asia
TheDirectoryof JapaneseAuto Manufacturers′ WbrldwidePurchaslng ● Contacts ● トOriginalEqulpment ● トOriginalEqulpment Service トAccessories トMaterials +RmR JA払NAuTOMOBILEMANUFACTURERSAssocIATION′INC. DAIHATSU CONTACTS IN JAPAN CONTACTS IN ASIA OE, Service, Accessories and Material OE Parts for Asian Plants: P.T. Astra Daihatsu Motor Daihatsu Motor Co., Ltd. JL. Gaya Motor 3/5, Sunter II, Jakarta 14350, urchasing Div. PO Box 1166 Jakarta 14011, Indonesia 1-1, Daihatsu-cho, Ikeda-shi, Phone: 62-21-651-0300 Osaka, 563-0044 Japan Fax: 62-21-651-0834 Phone: 072-754-3331 Fax: 072-751-7666 Perodua Manufacturing Sdn. Bhd. Lot 1896, Sungai Choh, Mukim Serendah, Locked Bag No.226, 48009 Rawang, Selangor Darul Ehsan, Malaysia Phone: 60-3-6092-8888 Fax: 60-3-6090-2167 1 HINO CONTACTS IN JAPAN CONTACTS IN ASIA OE, Service, Aceessories and Materials OE, Service Parts and Accessories Hino Motors, Ltd. For Indonesia Plant: Purchasing Planning Div. P.T. Hino Motors Manufacturing Indonesia 1-1, Hinodai 3-chome, Hino-shi, Kawasan Industri Kota Bukit Indah Blok D1 No.1 Tokyo 191-8660 Japan Purwakarta 41181, Phone: 042-586-5474/5481 Jawa Barat, Indonesia Fax: 042-586-5477 Phone: 0264-351-911 Fax: 0264-351-755 CONTACTS IN NORTH AMERICA For Malaysia Plant: Hino Motors (Malaysia) Sdn. Bhd. OE, Service Parts and Accessories Lot P.T. 24, Jalan 223, For America Plant: Section 51A 46100, Petaling Jaya, Hino Motors Manufacturing U.S.A., Inc. Selangor, Malaysia 290 S. Milliken Avenue Phone: 03-757-3517 Ontario, California 91761 Fax: 03-757-2235 Phone: 909-974-4850 Fax: 909-937-3480 For Thailand Plant: Hino Motors Manufacturing (Thailand)Ltd. -
Toyota Motor Corp
SECURITIES AND EXCHANGE COMMISSION FORM 20-F Annual and transition report of foreign private issuers pursuant to sections 13 or 15(d) Filing Date: 2021-06-24 | Period of Report: 2021-03-31 SEC Accession No. 0001193125-21-197902 (HTML Version on secdatabase.com) FILER TOYOTA MOTOR CORP/ Mailing Address Business Address TOYOTA MOTOR SALES 1 TOYOTA CHO TOYOTA CIK:1094517| IRS No.: 000000000 | State of Incorp.:M0 | Fiscal Year End: 0331 USA INC CITY Type: 20-F | Act: 34 | File No.: 001-14948 | Film No.: 211040557 6565 HEADQUARTERS AICHI PREFECTURE SIC: 3711 Motor vehicles & passenger car bodies DRIVE W1-3A 471-8571 PLANO TX 75024 JAPAN M0 00000 81-565-28-2121 Copyright © 2021 www.secdatabase.com. All Rights Reserved. Please Consider the Environment Before Printing This Document Table of Contents As filed with the U.S. Securities and Exchange Commission on June 24, 2021 UNITED STATES SECURITIES AND EXCHANGE COMMISSION Washington, D.C. 20549 FORM 20-F (Mark One) ☐ REGISTRATION STATEMENT PURSUANT TO SECTION 12(b) OR (g) OF THE SECURITIES EXCHANGE ACT OF 1934 OR ☒ ANNUAL REPORT PURSUANT TO SECTION 13 OR 15(d) OF THE SECURITIES EXCHANGE ACT OF 1934 For the fiscal year ended: March 31, 2021 OR ☐ TRANSITION REPORT PURSUANT TO SECTION 13 OR 15(d) OF THE SECURITIES EXCHANGE ACT OF 1934 OR ☐ SHELL COMPANY REPORT PURSUANT TO SECTION 13 OR 15(d) OF THE SECURITIES EXCHANGE ACT OF 1934 Commission file number: 001-14948 TOYOTA JIDOSHA KABUSHIKI KAISHA (Exact name of registrant as specified in its charter) TOYOTA MOTOR CORPORATION (Translation of registrants -
TOYOTA MOTOR EUROPE NV/SA Information Pursuant to REACH
TOYOTA MOTOR EUROPE NV/SA Information pursuant to REACH Article 33 Article 33 of the REACH (Registration, Evaluation, Authorization and restriction of Chemicals) Regulation states that customers must be informed about the presence of Substances of Very High Concern (SVHCs) in our products, in order to guarantee their safe use. TOYOTA supports the goals of REACH, which are consistent with our own commitments to promote the responsible manufacturing, handling, use and disposal of our products. Based on the information we received from our suppliers, the SVHCs that may be present in component articles of your Toyota Avensis in concentrations above 0.1% by weight are shown in the table below. Please be aware that, where present in your vehicle, the SVHCs listed below are incorporated in such a way that the risk to humans or the environment can be excluded as long as the vehicle and its parts are used as intended. Every Toyota and Lexus vehicle is provided with an owner’s manual that describes the safe use of our products. Substance name CAS number Component article 1,2-Benzenedicarboxylic 68648-93-1 Seat acid, mixed decyl and hexyl and octyl diesters 2-Ethoxyethanol 110-80-5 Spoiler, Rr Lamp Acrylamide 79-06-1 Transmission Control, Lock Cylinder, Wire Harness, Body Switch, Chassis Switch, Lane Recognition, Driving Support, Cruise Control, Push Start, Engine Control, Security, Wireless Door Lock Aluminium oxide fibers 142844-00-6 Sliding Roof Benzyl butyl phthalate 85-68-7 Seat Bis(2-ethylhexyl) 117-81-7 Engine Unmoving No.1, Engine phthalate -
Sustainability Data Book 2017 Sustainability Data Book 2017
Sustainability Data Book 2017 Sustainability Data Book 2017 Editorial Policy Sustainability Data Book (Former Sustainability Report) focuses on reporting the yearly activities of Toyota such as Toyota CSR management and individual initiatives. Information on CSR initiatives is divided into chapters, including Society, Environment and Governance. We have also made available the “Environmental Report 2017 - Toward Toyota Environmental Challenge 2050” excerpted from the Sustainability Data Book 2017. In the Annual Report, Toyota shares with its stakeholders the ways in which Toyota’s business is contributing to the sustainable development of society and the Earth on a comprehensive basis from a medium- to long-term perspective. Annual Report http://www.toyota-global.com/investors/ir_library/annual/ Securities Reports http://www.toyota.co.jp/jpn/investors/library/negotiable/ Sustainability Data Book 2017 http://www.toyota-global.com/sustainability/report/sr/ SEC Fillings http://www.toyota-global.com/investors/ir_library/sec/ Financial Results Environmental Report 2017 http://www.toyota-global.com/investors/financial_result/ —Toward Toyota Environmental Challenge 2050— http://www.toyota-global.com/sustainability/report/er/ Corporate Governance Reports http://www.toyota-global.com/investors/ir_library/cg/ • The Toyota website also provides information on corporate initiatives not included in the above reports. Sustainability http://www.toyota-global.com/sustainability/ Environment http://www.toyota-global.com/sustainability/environment/ Social Contribution Activities http://www.toyota-global.com/sustainability/social_contribution/ Period Covered Fiscal year 2016 (April 2016 to March 2017) Some of the initiatives in fiscal year 2017 are also included Toyota Motor Corporation (TMC)’s own initiatives and examples of those of its consolidated affiliates, etc., Scope of Report in Japan and overseas. -
2011 Annual Report (42Nd Term)
Annual Report For the year ended March 31, 2012 MESSAGE FROM THE PRESIDENT Please accept our gratitude for your continued support. Below are some remarks on the report for FUJITSU TEN's 42nd term (April 2011 to March 2012). Takashi Shigematsu, President (1) Business Environment Looking at the economy this term, although overseas business conditions in ASEAN and so on were good, the Chinese economy is showing signs of uncertainty. Moreover, advanced economies on the whole have been stagnant. In Japan, impacts of the Great East Japan Earthquake and flooding in Thailand led to a temporary downturn in business. Although the economy displayed some signs of recovery thanks to the restoration of supply chains and so on, the positive developments were delayed somewhat due to overseas economic trends and the impact of dramatic appreciation in the yen. In the domestic automotive market, restoration of the eco car subsidy program helped boost car sales, while the complete transition to terrestrial digital broadcasting encouraged repurchase demand for navigation products and so on, however, this was not enough to bring about full-scale recovery. Due to the effects of the Great East Japan Earthquake and flooding in Thailand, clients of automotive makers had to suspend operations and supply chains were severed, thus leading to reduced sales and production for FUJITSU TEN. Moreover, against a background of advancing price reduction for navigation products, intensifying competition with rival companies, dramatic and record-breaking appreciation of the yen and stagnation of the Japanese car market, which is our primary sales area, we were unfortunately unable to recover our sales figures. -
Annual Report 2009 Overseas Manufacturing Companies
Management & Corporate Information Overseas Manufacturing Companies As of March 31, 2009 24 23 19 20 17 18 1 2 32 27-31,33 4 3 12 9 21 22 8 35 6 7 5 13 10 44 11 52 34,36 37 45 47-50 39 38 51 46 16 43 42 25 41 40 15 26 14 53 North America Country/Area Company name Main products Voting rights Start of ratio* (%) operations Canada 1 Canadian Autoparts Toyota Inc. (CAPTIN) Aluminum wheels 100.00 1985 2 Toyota Motor Manufacturing Canada Inc. (TMMC) Corolla, Matrix, RX350, RAV4 100.00 1988 U.S.A. 3 TABC, Inc. Catalytic converters, steering columns, 100.00 1971 stamped parts 4 New United Motor Manufacturing, Inc. (NUMMI)** Corolla, Tacoma 50.00 1984 5 Toyota Motor Manufacturing, Kentucky, Inc. (TMMK) Camry, Camry Hybrid, Camry Solara, 100.00 1988 Avalon, VENZA/engines 6 Catalytic Component Products, Inc. (CCP) Catalytic converters — 1991 7 Bodine Aluminum, Inc. Aluminum castings 100.00 1993 8 Toyota Motor Manufacturing, West Virginia, Inc. (TMMWV) Engines, transmissions 100.00 1998 9 Toyota Motor Manufacturing, Indiana, Inc. (TMMI) Tundra, Sequoia, Sienna 100.00 1999 10 Toyota Motor Manufacturing, Alabama, Inc. (TMMAL) Engines 100.00 2003 11 Toyota Motor Manufacturing, Texas, Inc. (TMMTX) Tundra 100.00 2006 12 Subaru of Indiana Automotive, Inc. (SIA)** Camry — 2007*** Mexico 13 Toyota Motor Manufacturing de Baja California Tacoma/Truck beds 100.00 2004 S.de R.L.de C.V. (TMMBC) Central and South America Country/Area Company name Main products Voting rights Start of ratio* (%) operations Argentina 14 Toyota Argentina S.A. -
UNITED STATES SECURITIES and EXCHANGE COMMISSION Washington, D.C
As filed with the Securities and Exchange Commission on June 24, 2016 UNITED STATES SECURITIES AND EXCHANGE COMMISSION Washington, D.C. 20549 FORM 20-F (Mark One) ‘ REGISTRATION STATEMENT PURSUANT TO SECTION 12(b) OR (g) OF THE SECURITIES EXCHANGE ACT OF 1934 OR È ANNUAL REPORT PURSUANT TO SECTION 13 OR 15(d) OF THE SECURITIES EXCHANGE ACT OF 1934 For the fiscal year ended: March 31, 2016 OR ‘ TRANSITION REPORT PURSUANT TO SECTION 13 OR 15(d) OF THE SECURITIES EXCHANGE ACT OF 1934 OR ‘ SHELL COMPANY REPORT PURSUANT TO SECTION 13 OR 15(d) OF THE SECURITIES EXCHANGE ACT OF 1934 Commission file number: 001-14948 TOYOTA JIDOSHA KABUSHIKI KAISHA (Exact Name of Registrant as Specified in its Charter) TOYOTA MOTOR CORPORATION (Translation of Registrant’s Name into English) Japan (Jurisdiction of Incorporation or Organization) 1 Toyota-cho, Toyota City Aichi Prefecture 471-8571 Japan +81 565 28-2121 (Address of Principal Executive Offices) Nobukazu Takano Telephone number: +81 565 28-2121 Facsimile number: +81 565 23-5800 Address: 1 Toyota-cho, Toyota City, Aichi Prefecture 471-8571, Japan (Name, telephone, e-mail and/or facsimile number and address of registrant’s contact person) Securities registered or to be registered pursuant to Section 12(b) of the Act: Title of Each Class: Name of Each Exchange on Which Registered: American Depositary Shares* The New York Stock Exchange Common Stock** * American Depositary Receipts evidence American Depositary Shares, each American Depositary Share representing two shares of the registrant’s Common Stock. ** No par value. Not for trading, but only in connection with the registration of American Depositary Shares, pursuant to the requirements of the U.S. -
New United Motor Manufacturing, Inc
THE ‘LEARNING BUREAUCRACY’: NEW UNITED MOTOR MANUFACTURING, INC. By Paul S. Adler Downloaded from http://www-bcf.usc.edu/~padler/ THE ‘LEARNING BUREAUCRACY’: NEW UNITED MOTOR MANUFACTURING, INC. by Paul S. Adler School of Business Administration University of Southern California Los Angeles 90089-1421 Tel: (213) 740-0748 DRAFT 3.1 April 1992 Forthcoming in Barry M. Staw and Larry L. Cummings (eds.) Research in Organizational Behavior, Greenwich, CT: JAI Press. Acknowledgements: The research on which this study is based would not have been possible without the generous cooperation of managers, workers and union officials at NUMMI. Gary Robinson helped transcribe taped interviews with them and discern the key points. This article has benefitted from the comments of several NUMMI people and from the responses of many friends and colleagues: Chris Argyris, Joel Beinin, Christian Berggren, Bob Brenner, Clair Brown, El Buffa, Bob Cole, John Ettlie, Steve Frenkel, Don Gerwin, Meg Graham, Jan Hopland, Sandy Jacoby, Ed Lawler, Ann Majchrzak, Ruth Milkman, Michael Reich, Dick Scott, Bill Simon, David Stern, Steve Wheelwright, Bob Sutton, Lowell Turner, and Stephen Wood. My thinking has also been stimulated by the reaction of colleagues to presentations at the USC, Harvard Business School, NYU, UCLA, and UC Berkeley. My thanks to all these people, many of whom still disagree. 2 TABLE OF CONTENTS INTRODUCTION .................................................................................................... 3 RESEARCH METHODS......................................................................................... -
Annual Report 2018|Corporate Data
Table of Contents Message from the President Toward the Mobility Society of the Future Initiatives for Sustainable Growth Corporate Data Corporate Data At a Glance History Financial Summary Non-Automotive Business Corporate/Stock Information At a Glance Number of Plants and Global Perspective/Data by Region Distributors* R&D Sites* Number of Employees Manufacturing Companies* (As of March 31, 2018) (As of March 31, 2018) (As of March 31, 2018) *Number of bases for Toyota and Lexus brands 369,124 (Consolidated, as of March 31, 2018) Other North Asia Europe America Europe Japan North Asia Japan 10 America 8 excluding Japan 29 24 17 5 3 Total Vehicle Production 3 21 — Other 8,964,133 (Consolidated, FY 2018) 4 6 8 114 0 Financial Highlights Total Vehicle Sales Net Revenues Operating Income Net Income Total Vehicle Sales for the Year Ended 8,964,394 8,964 thousand ¥29,379.5 billion ¥2,399.8 billion ¥2,493.9 billion March 31, 2018 (Consolidated, FY 2018) (Consolidated) -7 thousand +6.5% +20.3% +36.2% The second of each pair of Total Liquid Assets (net) Total Shareholder Return (max) R&D Expenses Capital Expenditures fi gures is the year-on-year change. ¥8,025.9 billion ¥1,200.1 billion ¥1,064.2 billion ¥1,302.7 billion +¥262.9 billion +¥117.7 billion +¥26.7 billion +¥90.9 billion 46 TOYOTA Annual Report 2018 Table of Contents Message from the President Toward the Mobility Society of the Future Initiatives for Sustainable Growth Corporate Data Corporate Data At a Glance History Financial Summary Non-Automotive Business Corporate/Stock Information -
Pdf: 660 Kb / 236
As filed with the Securities and Exchange Commission on June 23, 2017 UNITED STATES SECURITIES AND EXCHANGE COMMISSION Washington, D.C. 20549 FORM 20-F (Mark One) ‘ REGISTRATION STATEMENT PURSUANT TO SECTION 12(b) OR (g) OF THE SECURITIES EXCHANGE ACT OF 1934 OR È ANNUAL REPORT PURSUANT TO SECTION 13 OR 15(d) OF THE SECURITIES EXCHANGE ACT OF 1934 For the fiscal year ended: March 31, 2017 OR ‘ TRANSITION REPORT PURSUANT TO SECTION 13 OR 15(d) OF THE SECURITIES EXCHANGE ACT OF 1934 OR ‘ SHELL COMPANY REPORT PURSUANT TO SECTION 13 OR 15(d) OF THE SECURITIES EXCHANGE ACT OF 1934 Commission file number: 001-14948 TOYOTA JIDOSHA KABUSHIKI KAISHA (Exact Name of Registrant as Specified in its Charter) TOYOTA MOTOR CORPORATION (Translation of Registrant’s Name into English) Japan (Jurisdiction of Incorporation or Organization) 1 Toyota-cho, Toyota City Aichi Prefecture 471-8571 Japan +81 565 28-2121 (Address of Principal Executive Offices) Nobukazu Takano Telephone number: +81 565 28-2121 Facsimile number: +81 565 23-5800 Address: 1 Toyota-cho, Toyota City, Aichi Prefecture 471-8571, Japan (Name, telephone, e-mail and/or facsimile number and address of registrant’s contact person) Securities registered or to be registered pursuant to Section 12(b) of the Act: Title of Each Class: Name of Each Exchange on Which Registered: American Depositary Shares* The New York Stock Exchange Common Stock** * American Depositary Receipts evidence American Depositary Shares, each American Depositary Share representing two shares of the registrant’s Common Stock. ** No par value. Not for trading, but only in connection with the registration of American Depositary Shares, pursuant to the requirements of the U.S. -
UNITED STATES SECURITIES and EXCHANGE COMMISSION Washington, D.C
As filed with the Securities and Exchange Commission on June 25, 2012 UNITED STATES SECURITIES AND EXCHANGE COMMISSION Washington, D.C. 20549 FORM 20-F (Mark One) ‘ REGISTRATION STATEMENT PURSUANT TO SECTION 12(b) OR (g) OF THE SECURITIES EXCHANGE ACT OF 1934 OR È ANNUAL REPORT PURSUANT TO SECTION 13 OR 15(d) OF THE SECURITIES EXCHANGE ACT OF 1934 For the fiscal year ended: March 31, 2012 OR ‘ TRANSITION REPORT PURSUANT TO SECTION 13 OR 15(d) OF THE SECURITIES EXCHANGE ACT OF 1934 OR ‘ SHELL COMPANY REPORT PURSUANT TO SECTION 13 OR 15(d) OF THE SECURITIES EXCHANGE ACT OF 1934 Commission file number: 001-14948 TOYOTA JIDOSHA KABUSHIKI KAISHA (Exact Name of Registrant as Specified in its Charter) TOYOTA MOTOR CORPORATION (Translation of Registrant’s Name into English) Japan (Jurisdiction of Incorporation or Organization) 1 Toyota-cho, Toyota City Aichi Prefecture 471-8571 Japan +81 565 28-2121 (Address of Principal Executive Offices) Kenichiro Makino Telephone number: +81 565 28-2121 Facsimile number: +81 565 23-5800 Address: 1 Toyota-cho, Toyota City, Aichi Prefecture 471-8571, Japan (Name, telephone, e-mail and/or facsimile number and address of registrant’s contact person) Securities registered or to be registered pursuant to Section 12(b) of the Act: Title of Each Class: Name of Each Exchange on Which Registered: American Depositary Shares* The New York Stock Exchange Common Stock** * American Depositary Receipts evidence American Depositary Shares, each American Depositary Share representing two shares of the registrant’s Common Stock. ** No par value. Not for trading, but only in connection with the registration of American Depositary Shares, pursuant to the requirements of the U.S. -
ANNUAL REPORT 2007 Asia Start of Voting Rights Company Name Operations Ratio* (%) Main Products China a Tianjin Jinfeng Auto Parts Co., Ltd
Overseas Manufacturing Companies (Plants that manufacture or assemble Toyota- or Lexus-brand vehicles and component manufacturers established by Toyota) As of March 31, 2007 North America Start of Voting rights Company name operations ratio* (%) Main products Canada 1 Canadian Autoparts Toyota Inc. (CAPTIN) Feb. 1985 100.00 Aluminum wheels 2 Toyota Motor Manufacturing Canada Inc. (TMMC) Nov. 1988 100.00 Corolla, Matrix, RX, engines U.S.A. 3 TABC, Inc. Nov. 1971 100.00 Catalytic converters, stamping parts, steering columns, truck beds 4 New United Motor Manufacturing, Inc. (NUMMI)** Dec. 1984 50.00 Corolla, Tacoma 5 Toyota Motor Manufacturing, Kentucky, Inc. (TMMK) May 1988 100.00 Avalon, Camry, Camry Hybrid, Solara, engines 6 Bodine Aluminum, Inc. Jan. 1993 100.00 Aluminum castings 7 Toyota Motor Manufacturing, West Virginia, Inc. (TMMWV) Nov. 1998 100.00 Engines, transmissions 8 Toyota Motor Manufacturing, Indiana, Inc. (TMMI) Feb. 1999 100.00 Tundra, Sequoia, Sienna 9 Toyota Motor Manufacturing, Alabama, Inc. (TMMAL) Apr. 2003 100.00 Engines 0 Toyota Motor Manufacturing, Texas, Inc. (TMMTX) Nov. 2006 100.00 Tundra - Subaru of Indiana Automotive, Inc. (SIA)** Apr. 2007 *** — Camry Mexico = Toyota Motor Manufacturing de Baja California Sept. 2004 100.00 Truck beds, Tacoma S.de R.L.de C.V, (TMMBC) Central and South America Start of Voting rights Company name operations ratio* (%) Main products Argentina q Toyota Argentina S.A. (TASA) Mar. 1997 100.00 Hilux, Fortuner Brazil w Toyota do Brasil Ltda. May 1959 100.00 Corolla, Fielder Colombia e Sociedad de Fabricacion de Automotores S.A. Mar. 1992 28.00 Land Cruiser Prado Venezuela r Toyota de Venezuela Compania Anonima (TDV)** Nov.