Operator's Manual
Total Page:16
File Type:pdf, Size:1020Kb
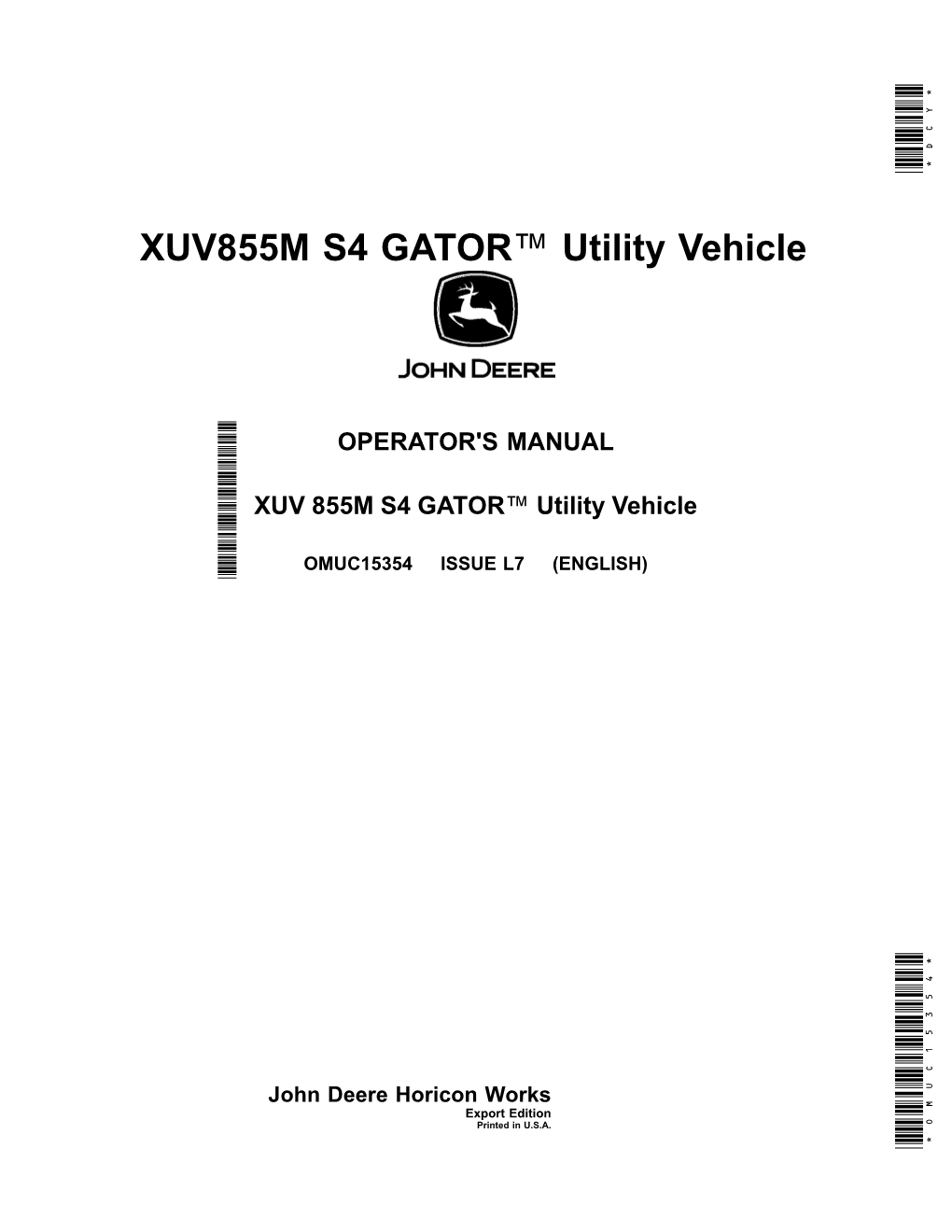
Load more
Recommended publications
-
Dispersal Sale of TRACTORS, GATOR, GRASSLAND MACHINERY, CATTLE EQUIPMENT, STANDING MAIZE and MAIZE SILAGE
Dispersal Sale of TRACTORS, GATOR, GRASSLAND MACHINERY, CATTLE EQUIPMENT, STANDING MAIZE AND MAIZE SILAGE For Mr Colin Watson (t/a Quality Milk Ltd) AT BUTLERS ROAD FARM, LONG COMPTON, SHIPSTON ON STOUR, WARWICKSHIRE, CV36 5LQ (1 mile off the A3400, 5 miles Chipping Norton, 6 miles Shipston on Stour) ON THURSDAY 21st AUGUST 2014 at 11am Terms: Strictly Payment on the Day; No Buyers Premium 01600 860 300 grichards.co.uk Gwilym Richards & Co Ltd, The Estate Office, Pant Glas, Llanishen, Chepstow, Monmouthshire NP16 6QQ Also at Wotton-under-Edge, Glos. Regulated by RICS. GENERAL CONDITIONS OF SALE 1.1 Every Vendor, Bidder and Purchaser shall be deemed to have full knowledge of the Composite Conditions and to agree to be bound by them. 1.1.1 All livestock is sold subject to these conditions, ("the Conditions"), the Livestock Auctioneers Association Conditions of Sale (2009 edition, as amended) ("the LAA Conditions") and, in the case of any pedigree livestock, any special conditions expressly applicable ("the Special Conditions") (all together "the Composite Conditions"). 1.1.2 If there is any conflict or inconsistency between the elements comprising the Composite Conditions the order of precedence shall be first, the Special Conditions, secondly the Conditions and thirdly, the LAA Conditions. 1.1.3 A copy of the LAA Conditions and any Special Conditions is available for inspection upon request. 1.2.1 All other lots are sold subject to these conditions, ("the Conditions"), and any special conditions expressly applicable ("the Special Conditions") (all together "the Composite Conditions"). 1.2.2 If there is any conflict or inconsistency between the elements comprising the Composite Conditions the order of precedence shall be first, the Special Conditions and secondly, the Conditions. -
Legeros Fire Blog Archives 2006-2015
Post Your Rosters! - Legeros Fire Blog Archives 2006-2015 Legeros Fire Blog Archives 2006-2015 - Post Your « Which Department to W… » Parasailing Accident … Rosters! Post Your Rosters! 08/29/09 594 W - + 20 - 11 Discussing Fayetteville's new rescue caused me to think, I wonder what their entire fleet looks like? Is anyone willing to post a full Fayetteville Fire Department apparatus roster? Ditto for the other larger departments around North Carolina? I'd love to see and compare apparatus and units from the state's top twenty municipalities (for starters): Asheville, Burlington, Cary, Chapel Hill, Charlotte, Concord, Durham, Fayetteville, Gastonia, Goldsboro, Greensboro, Greenville, Hickory, High Point, Jacksonville, Raleigh, Rocky Mount, Wilmington, Wilson, and Winston-Salem. Not sure how to post a list? Just mail it to Mike, and I'll post. Here's Raleigh's full fleet... E01 - 2009 Pierce Arrow XT pumper, 1500/500/20 E02 - 2005 Pierce Enforcer pumper, 1500/500/20 E03 - 2006 Pierce Enforce pumper, 1500/500/20 E04 - 1997 Pierce Saber pumper, 1250/500 E05 - 2002 Spartan/Quality Metro Star pumper, 1250/500 E06 - 2004 American LaFrance Eagle, 1500/500 E07 - 2002 Spartan/Quality Metro Star pumper, 1250/500 E08 - 2006 Pierce Enforcer pumper, 1500/500/20 E09 - 2008 Pierce Enforcer pumper, 1500/500/20 E10 - 1998 Pierce Saber pumper, 1250/500 E11 - 2005 Pierce Enforcer pumper, 1500/500/20 E12 - 2006 Pierce Enforcer pumper, 1500/500/20 E13 - 2004 American LaFrance Eagle pumper, 1500/500 E14 - 2004 American LaFrance Eagle pumper, 1500/500 E15 - 2006 -
Washington Co GL Loss Run As of April 30 2017.Xlsx
Washington County General Liability Loss Run as of 4/30/2017 2014 2015 2016 2017 GL ‐ Advances $15,241.80 $15,295.95 $0.00 $0.00 GL ‐ Judgment $0.00 $0.00 $0.00 $0.00 GL ‐ Legal Expense $7,518.36 $9,813.18 $21,035.47 $489.20 GL ‐ Legal Fees $224,344.25 $191,150.88 $127,478.97 $11,305.75 GL ‐ Settlement $195,700.00 $13,378.98 $250.00 $0.00 Total $442,804.41 $229,638.99 $148,764.44 $11,794.95 Open Claims 1 8 37 19 Closed Claims 44 40 5 0 Total Claims 45 48 42 19 Association of Arkansas Counties Risk Management Fund Washington County Vehicle Schedule Dept. Year/Make/Model Serial# Inv.# Value Deductible ROAD BOMAG K300 ROLLER 9157 10-6-4 PROP ROAD BOMAG ROLLER BW205 1561 10-6-5 PROP ROAD BROCE MK-1 TRANSFER BROOM 0061 10-20-3 PROP ROAD BROS ROLLER SP300 9409 10-6-010 PROP ROAD CAT 966C LOADER 5589 10-16-012 PROP ROAD CAT ASPHALT PAVER 0118 10-190-8 PROP ROAD CAT BACKHOE W/TRACMAC 0510/1034 10-8-9 PROP ROAD CAT CRAWLER DOZER 5930 10-004-002 PROP ROAD CAT D-6 DOZER 1356 10-004-004 PROP ROAD CAT D-6 DOZER 3975 10-004-005 PROP ROAD CAT D-6 DOZER W/RIPPER 0595 10-004-003 PROP ROAD CAT 06H OS DOZER 1538 10-004-006 PROP ROAD CAT ELEVATING SCRAPER 613C 1803 10-19-02 PROP ROAD CAT RUBBER TIRE LOADER 966F 1779 10-16-007 PROP ROAD CAT SCRAPER 621 B TX-7 0495 10-19-10 PROP ROAD CEDAR RAPIDS PAVER 5446 10-190-5 PROP ROAD DENISON GRADELL ROAD GRADER 9251 10-13-004 PROP ROAD DYNAPAC DOUBLE DRUM ROLLER 0625 10-6-8 PROP ROAD DYNAPAC PADDLE FOOT ROLLER 1803 10-6-9 PROP ROAD DYNAPAC VIBRATORY CA251D ROLLER 2993 10-6-17 PROP ROAD ENTNYRE CHIP SPREADER 0079 10-5-9517 -
Catalog August 2020
1stStrike Oilfield Surplus Auction Catalog August 2020 August 2020 1stStrike Oilfield Surplus Auction Saturday August 1st, 2020 Open @ 7:00am Auction Starts @ 8:30am 1096 Van Horn Road, Fairbanks, Alaska Inspection: Saturday July 25th through Friday July 31st 9:00am to 5:00pm Load-out: 10:00am to 5:00pm on Sunday August 2nd and 9:00am to 5:00pm Monday August 3rd through Saturday August 8th Welcome to the Oilfield Surplus Auction including inventory from the primary North Slope companies and other major industrial companies. This auction includes Heavy Equipment, Vehicles, Trucks, Industrial Products, Construction Equipment, Pipeline Surplus, and more. All terms and conditions applicable to material consigned shall likewise be applicable to any and all additional Consignors, as appropriate. Immediately upon bid award, buyer is responsible for securing lot(s) to the maximum extent possible to protect from weather, theft, or any other loss. Recommendation or approval of cargo carriers or handlers by any employee or any affiliated entity of 1stStrike, shall be done only as an accommodation to the Buyer. The Buyer acknowledges and agrees that they shall have no rights or remedies based upon any act or omission by a cargo carrier or handler. Loading assistance is provided as a courtesy, however, purchaser assumes all risk and responsibility for loading and removal of purchases. 1stStrike reserves the right to require proof of adequate insurance coverage from any purchaser for items requiring dismantling, rigging or hot cutting. Documents of transfer, including motor vehicle ownership documents will be provided to the purchaser within seven days following the auction or as soon thereafter as such documents are available. -
App D1 Ivanpah AQ EITP Rev2.Xls Em Summary 1 of 9 Ivanpah Substation Workforce Estimate
Appendix D Air Quality and Greenhouse Gases This page intentionally left blank Ivanpah Substation Emission Summary Total Activity Emissions(lbs) Activity ROG CO NOX SOX PM10 PM2.5 CO2 CH4 Phase 1 Grading On-Site 818 2798 7385 8 512 274 740794 52 On-Road 9 83 9 0.1 2329 471 10957 0.8 Phase 2 Civil On-Site 682 2232 6113 7 340 214 667830 47 On-Road 19 174 19 0.2 1992 412 23009 1.7 Phase 3 Electrical On-Site 676 2093 6017 7 278 192 634213 44 On-Road 22 198 22 0.3 2522 516 26296 2.0 Total All Activities (lbs) 2226 7577 19566 22 7972 2079 2103100 147 Total All Activities (tons) 1.1 3.8 10 0.011 4.0 1.0 1052 0.074 Total Construction Days 160 160 160 160 160 160 160 160 Average Daily Emissions (lbs) 13.9 47.4 122 0.14 49.8 13.0 13144 0.92 Assumed that on site combustion PM2.5 is 75% of PM10 Assumed that on site combustion CH4 is 0.00007 of CO2 App D1 Ivanpah AQ EITP Rev2.xls Em Summary 1 of 9 Ivanpah Substation Workforce Estimate Work Activity Activity Production Estimated Average Primary Estimated Duration of Primary Equipment Estimated Horse- Probable Equipment Estimated Schedule Use Description Power Fuel Type Quantity Workforce (Days) (Hrs/Day) Estimated Production Per Day Survey Crew 2 15 10 3/4 ton pick-up truck, 4X4 300 Diesel 2 2 15 4 Vehicle for transportation to and from work John Deere Gator 20 Gas 2 2 40 6 Transport personnel around site Grading Crew 5 40 10 3/4 ton pick-up truck, 4X4 300 Diesel 5 5 40 4 Bulldozer 350 Diesel 1 40 4 Dump truck 350 Diesel 1 40 6 Paddle graders 350 Diesel 3 40 8 Water truck 300 Diesel 1 40 4 Front end -
11-19-0907 Intended Specification
INTENDED SPECIFICATIONS BID 11-19-0907 NOTICE: FSA will not be adding any new specifications or models for Bid 11-19-0907. We will only be correcting the model numbers that are listed below. July 13th: Specification #01 – Full Size Pursuit Vehicles – RWD (Police Package) Ford Crown Victoria (P7B/720A) Chevrolet Caprice (1EW19/9C1) Dodge Charger (LDDE48/29A) Specification #02 – Full Size Pursuit Vehicles – FWD (Police Package) Chevrolet Impala (1WS19/9C1) Specification #03 – Full Size Utility Vehicles – RWD (Police Package) Ford Explorer Chevrolet Tahoe 1500 (CC10706/PPV) Specification #04 – Full Size 4-Door Administrative Vehicles Ford Crown Victoria (P7C) Ford Taurus (P2D) Chevrolet Impala (1WF19) Dodge Charger (LDDM48) Specification #05 – Mid Size 4-Door Administrative Vehicles Ford Fusion (P0H) Chevrolet Malibu (1ZJ69) Dodge Avenger (JSDH41) Toyota Camry (2552) Specification #06 – Compact 4-Door Administrative Vehicles Ford Focus (P3E) Chevrolet Cruze (1PL69) Dodge Caliber (PMDP49) Toyota Corolla (1832) Specification #07 – Hybrid 4-Door Administrative Vehicles Ford Fusion (P0L) Honda Civic (FA3629EW) Toyota Camry (2560) Toyota Prius (1223) Specification #08 – Small 2 Passenger Electric Vehicle Electro Bubble Buddy (2P) Global Electric Motors (e2) Specification #09 – Three Wheeled Personal Transporter, Electric T3 Personal Mobility Vehicle Specification #10 – Off-Road Utility Vehicle - 4 Wheel Drive American Sportsworks CW650 Bobcat 3400 Case IH Scout XL Club Car XRT 1550 2011 Intended Specifications Page 1 Specification #10 – Off-Road -
Fiscal Year 2019-2020 Adopted Budget
Fiscal Year 2019-2020 Adopted Budget PO Box 101, Wentworth, NC 27320 | 371 NC 65, Reidsville, NC 27320 Rockingham County, North Carolina ANNUAL OPERATING BUDGET FISCAL YEAR 2020 (July 1, 2019 through June 30, 2020) County Commissioners A. Reece Pyrtle, Jr., Chairman Mark F. Richardson, Vice-Chairman Kevin Berger Mark F. Richardson T. Craig Travis County Officials Lance L. Metzler, County Manager John M. Morris, County Attorney Keli G. Watkins, Clerk to the Board Pat Galloway, Financial Services Director Paul Murray, Strategic Management Director Samuel S. Page, Sheriff Benjamin J. Curtis, Register of Deeds 371 NC Hwy 65 Reidsville, NC 27320 336-342-8100 www.co.rockingham.nc.us The Government Finance Officers Association of the United States and Canada (GFOA) presented a Distinguished Budget Presentation Award to Rockingham County, North Carolina for its annual budget for the fiscal year beginning July 1, 2018. In order to receive this award, a governmental unit must publish a budget document that meets program criteria as a policy document, as an operations guide, as a financial plan, and as a communications device. This award is valid for a period of one year only. We believe our current budget continues to conform to program requirements, and we are submitting it to GFOA to determine its eligibility for another award. TABLE OF CONTENTS (Blue text is hyperlink) Vision, Mission, and Strategic Focus Areas ................................................................................................................................. 1 -
Utility Vehicle OPERATOR's MANUAL HPX815E Gator
*DCY* HPX815E Gator™ Utility Vehicle OPERATOR'S MANUAL HPX815E Gator™ Utility Vehicle OMUC12667 ISSUE H7 (ENGLISH) *OMUC12667* John Deere Horicon Works Export Edition Printed in U.S.A. *omuc12667* Introduction Thank You for Purchasing a John Deere adequate protection to the occupants in that Product environment unless equipped with a FOPS and/or OPS. We appreciate having you as a customer and wish you The cab available from the manufacturer is not designed many years of safe and satisfied use of your machine. to provide adequate protection from hazardous substances. The operator must wear appropriate MX00654,000020B-19-10MAY17 personal protection equipment. The manufacturer accepts no liability for damage or Using Your Operator’s Manual injury resulting from this misuse, and these risks must be borne solely by the user. Compliance with, and strict This manual is an important part of your machine and adherence to, the conditions of operation, service, and should remain with the machine when you sell it. repair as specified by the manufacturer also constitute Reading your operator’s manual will help you and others essential elements for the intended use. avoid personal injury or damage to the machine. This machine should be operated, serviced, and Information given in this manual will provide the operator repaired only by persons familiar with all its particular with the safest and most effective use of the machine. characteristics and acquainted with the relevant safety Knowing how to operate this machine safely and rules (accident prevention). The accident prevention correctly will allow you to train others who may operate regulations, all other generally recognized regulations this machine. -
Public Auction Saturday, October 22, 2011 James G
Public Auction Saturday, October 22, 2011 James G. Murphy Inc. PUBLIC AUCTION Commercial & Industrial Auctioneers 9AM - SATURDAY - OCTOBER 22 1994 CHEV KODIAK P.O. Box 82160, Kenmore, WA 98028 Preview 8-5, Friday, October 21 1978 MERCEDES UNIMOG 18226 68th Ave NE, KENMORE, WA NO MINIMUMS - NO RESERVES SCAFFOLDING 1997, 1996 FORD FLATBEDS 1998 KENWORTH T800 JACOBSEN 628D (32) BUSES 1992 CAT D6H Series II 1996 FORD LTS9000 1999 FORD F450 PAINT STRIPER James G. Murphy Inc. James G. Murphy Inc. Commercial & Industrial Auctioneers Commercial & Industrial Auctioneers 1999 TYMCO 2004 FREIGHTLINER FL70 2005 ELGIN CROSSWIND www.murphyauction.com 425.486.1246 or 800.426.3008 PUBLIC AUCTION TERMS & CONDITIONS Due to insurance & safety reasons, children under 12 cannot be admitted NO BUYERS PREMIUM ON HEAVY EQUIPMENT & VEHICLES Heavy Equipment, Heavy Trucks, 10% BUYERS PREMIUM ON ALL SMALL TOOLS AND SMALL EQUIPMENT In addition, a 3% buyers premium will be charged on all internet purchases PAYMENT: Full payment must be made by no later than 4 p.m., Tuesday, Trailers, Buses, Vehicles, RV’s following the auction. A 25% deposit is required by the close of business, auction day. Cash, cashier’s check, Master & Visa cards only. Personal or company checks accepted ONLY with bank letter of guarantee From Contractors, City & County Agencies, Phone & Utility Companies, AUCTIONEERS NOTE: U.S. Marshal, & Others An $100 vehicle documentation fee will be charged on the purchase of every 2003 FREIGHTLINER FC80 2004 VOLVO VLN670 1999 MACK CL713 motor vehicle including cars, trucks, vans, & trailers REMOVAL: There will be no removal during the auction unless otherwise announced by the auctioneer. -
Wwn200829sm.Pdf
11 August 29, 2020 www.TheBargainHunter.com Vol. 18 No. 29 Dan Starcher The Wayne County Transportation Improvement District secured nearly $150,000 from the Ohio Department of Transportation for two area roadway projects. Construction equipment sits at the future site of a BellStore at 1046 N. Apple Creek Road. Money awarded to the project from ODOT will save taxpayer money by covering 25% of the cost. See page 4. RESIDENTIAL CUSTOMER RESIDENTIAL PERMIT NO. 148 NO. PERMIT Canton, OH Canton, LOCAL See additional news 6 Better numbers 12 Great catch PAID POSTAGE U.S. STANDARD PRESORTED and more online at County’s unemployment Triway wide receiver hopes to *****************ECRWSS**** www.thebargainhunter.com figures slowly improve. generate college interest. 2 2 • Wooster Weekly News August 29, 2020 Wayne commissioners reduce requirements, 7368 CR 623 • PO Box 358 extend deadline for small business grants Millersburg OH 44654 330-674-2300 • 888-674-1010 By Dan Starcher closures are eligible. Fax 888-769-3960 To reach additional small —Personal protective OFFICE HOURS businesses negatively impacted equipment or other COVID- Mon. - Thurs. 8:00 AM - 5:00 PM financially by the coronavirus Fri. 8:00 AM - Noon related costs such as expenses pandemic, the Wayne County related to compliance with DISPLAY AD DEADLINE commissioners have reduced the Responsible Restart Ohio are Call 330-763-2938 restrictions involved in applying eligible. for a Wayne County Small Busi- TUESDAYS AT NOON —Sole proprietors can Stark • Tusc • S. Tusc ness Relief Program grant. use grant funding as income “We are pleased to have replacement by providing docu- WEDNESDAYS AT 11:00 AM awarded $126,550 to 27 area Wooster mentation on lost revenue from small businesses,” commis- March 1 to May 31, 2020, due WEDNESDAYS AT NOON sioner Sue Smail said. -
Request for Information (Rfi)
REQUEST FOR INFORMATION (RFI) CINCINNATI FLEET UPGRADES DUE DATE: Friday, January 20, 2017 @ 4:00 p.m. RFI NUMBER: RFI513OESFLEET ACCEPTANCE: Patrick Duhaney, Chief Procurement Officer City of Cincinnati, Division of Purchasing 805 Central Avenue, Suite 234 Cincinnati Ohio 45202 Submittal: One (1) electronic copy emailed in PDF format to [email protected]. All submitted responses must have RFI Reference Number, Time, and Date Due. Requests for information related to this Proposal should be directed to: Lyndsay Harvey, Buyer Email: [email protected] Issue Date: December 23, 2016 NOTE: The City publishes information on the City of Cincinnati Internet web site at www.cincinnati-oh.gov, which includes the Cincinnati Municipal Code and the information concerning the rules and registration information about the Small Business Enterprise Program. Offerors may register as a City vendor online at www.cincinnati-oh.gov/vss . I. REQUEST PURPOSE OF RFI The City of Cincinnati’s (“the City”) Division of Purchasing on behalf of the City’s Office of Environment and Sustainability (OES), cordially requests information from qualified companies to provide innovative and financially sustainable proposals to improve the environmental footprint of the City of Cincinnati’s Fleet. Specifically, The City desires to investigate potential vehicles and fuel technologies that can reduce the Oxides of Nitrogen (NOx) emissions of its fleet in order to utilize a new potential funding source from Ohio Environmental Protection Agency (OEPA) available in the fall of 2017. Information on this funding can be found here: http://www.epa.ohio.gov/oeef/EnvironmentalEducation.aspx#131365122-vw-mitigation- grants The responding company shall be qualified and experienced in the industry and have a demonstrated track record of work with federal, state, or local governments. -
20 Product Catalog
www.femcomfg.com 2015 PRODUCT CATALOG Enclosures, Weather Brakes, Sunshades & Umbrellas ROPS & Canopies GENERAL OFFICES 1132 WEST 1ST STREET McPherson, KS 67460 Toll Free: 1-800-677-0898 Fax: (620) 241-3532 Specializing in Weather & Web: www.femcomfg.com Email: [email protected] Safety Protection FEMCO, INC. GENERAL POLICIES PRICING: Prices are as stated on current price sheets and are subject to change without no- tice. SHIPPING & HANDLING: When possible, we will ship via UPS to reduce freight costs. How- ever, due to extra labor involved in weighing and stamping, a shipping and handling charge of $4.00 will be added to all UPS Shipments. For UPS 100wt, an additional charge of $10.00 will be added (200lb. minimum).Items shipping via a truckline will ship freight collect only. TERMS: Terms are Net 30 days with approved credit. Please pay by invoice – no statement will be sent. A charge of 1.5% per month (annual percentage rate of 18%) will be charged on unpaid balances. Those customers requesting an open account may do so and ship current shipments COD until your account has been approved. Government Purchase Orders: Femco, Inc. must receive payment before product will be sent on all government orders. Payment can be paid by Visa or Master Card. FEMCO, INC.: Warranty on products is 90 days from the date of purchase. This warranty is on workmanship and materials only. This warranty is limited to replacement of “defective” parts only and does not cover any labor charges to remove or reinstall part(s). To prevent shortages, all packages are sealed with pilfer-proof tape and electronically weighed.