The VISTA Infrared Camera [6269-34]
Total Page:16
File Type:pdf, Size:1020Kb
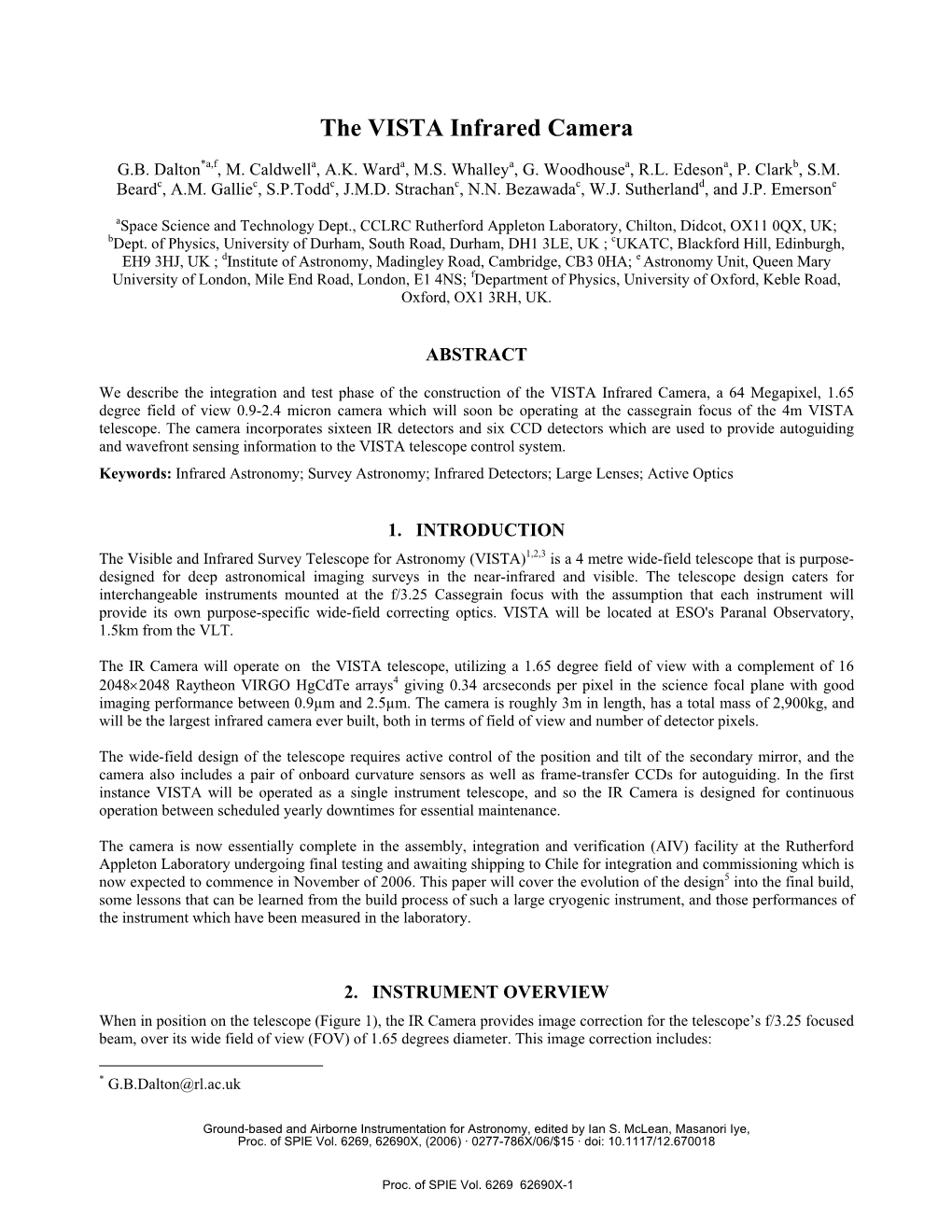
Load more
Recommended publications
-
The Case for Irish Membership of the European Southern Observatory Prepared by the Institute of Physics in Ireland June 2014
The Case for Irish Membership of the European Southern Observatory Prepared by the Institute of Physics in Ireland June 2014 The Case for Irish Membership of the European Southern Observatory Contents Summary 2 European Southern Observatory Overview 3 European Extremely Large Telescope 5 Summary of ESO Telescopes and Instrumentation 6 Technology Development at ESO 7 Big Data and Energy-Efficient Computing 8 Return to Industry 9 Ireland and Space Technologies 10 Astrophysics and Ireland 13 Undergraduate Teaching 15 Outreach and Astronomy 17 Education and Training 19 ESO Membership Fee 20 Conclusions 22 References 24 1 Summary The European Southern Observatory (ESO) is universally acknowledged as being the world leading facility for observational astronomy. The astrophysics community in Ireland is united in calling for Irish membership of ESO believing that this action would strongly support the Irish government’s commitment to its STEM (science, technology, engineering and maths) agenda. An essential element of the government’s plans for the Irish economy is to substantially grow its high-tech business sector. Physics is a core part of that base, with 86,000 jobs in Ireland in this sector1 while astrophysics, in particular, is a key driver both of science interest and especially of innovation. To support this agenda, Irish scientists and engineers need access to the best research facilities and with this access comes the benefits of spin-off technology, contracts and the jobs which this can bring. ESO is currently expanding its membership to include Brazil and is considering some eastern European countries. The cost of membership will increase as more states join and as Ireland’s GDP increases. -
ESO Calendar 2019
ESO Calendar 2019 European Southern Observatory Cover January February March April May June Rendering of the Extremely Large Telescope The Small Magellanic Cloud The Cat’s Paw and the Lobster Nebulae APEX and snowy Chajnantor VISTA’s cosmic view A sky full of galaxies ALMA’s dramatic surroundings This artist’s impression displays the Extremely One of our closest neighbours, the Small Magellanic This spectacular image from the VLT Survey The slumbering Atacama Pathfinder Experiment The Visible and Infrared Survey Telescope for This image contains a plethora of astronomical ALMA is a revolutionary astronomical telescope, Large Telescope (ELT) in all its grandeur. Sitting Cloud (SMC), is a dwarf irregular galaxy 200 000 Telescope (VST) shows the Cat’s Paw (upper right) (APEX) telescope sits beneath reddened skies in Astronomy (VISTA) is located at ESO’s Paranal treats. A subtle grouping of 1000 yellowish galaxies comprising an array of 66 giant antennas observing atop Cerro Armazones, 3046 m up in the Chilean light-years away. In the southern hemisphere, the and the Lobster (lower left) Nebulae. These vivid the snow covered Chajnantor landscape. Snow Observatory in Chile. The extreme altitude and arid cluster together near the centre of the frame. at millimetre and submillimetre wavelengths. It is Atacama Desert, the ELT’s mirror will be 39 metres SMC can be seen with the naked eye. The bright displays are sites of active star formation: photons blankets not only the ground, but also the many climate make for cloudless skies and excellent Combined with large quantities of hot gas and dark situated on the breathtaking Chajnantor Plateau, at in diameter: “the world’s biggest eye on the sky.” globular star cluster, 47 Tucanae, appears to the from hot young stars excite surrounding hydrogen peaks that encircle the Chilean plateau, which also viewing conditions. -
Key Words: Survey Telescopes, VISTA, VST, Survey Esocast Episode 74: Mapping the Southern Skies
Key words: Survey Telescopes, VISTA, VST, Survey ESOcast Episode 74: Mapping the Southern Skies 00:00 00:00 [Visuals start] [Visuals start] 1. Survey telescopes are designed to scan VST/VISTA footage/timelapses large areas of the sky quickly and deeply, looking for the rarest and most interesting astronomical objects. They use the latest technology on their scouting missions and produce huge amounts of data. ESO’s two dedicated survey telescopes are at work every clear night, carefully mapping the southern skies piece by piece. 00:32 00:00 ESOcast intro 2. This is the ESOcast! Cutting-edge science ESOcast introduction and life behind the scenes at ESO, the European Southern Observatory. 00:54 [Narrator] 3. VISTA and the VST — two powerful VST/VISTA footage survey telescopes: VISTA, the Visible and Infrared Survey Telescope for Astronomy, and the VST, the VLT Survey Telescope. 01:12 [Narrator] 4. Both telescopes are located at ESO’s Paranal Observatory Paranal Observatory in Chile and they are arguably the most powerful dedicated imaging survey telescopes in the world. 01:27 [Narrator] 5. Survey telescopes look for needles in VST/VISTA footage haystacks: rare astronomical objects, such as potentially dangerous near-Earth asteroids, hidden clusters, exploding stars and remote quasars. Unlike larger telescopes, which concentrate VISTA field, zoom in/zoom out on tiny parts of the sky in extreme detail, VISTA and the VST study broad areas of the sky. 02:00 [Narrator] 6. The resulting surveys produce huge Night sky with surveys archives of scientific data and pick up many interesting objects. These can then be studied in greater detail by much larger telescopes such as the neighbouring VLT. -
Astrophysics for the Next Decade
Astrophysics for the Next Decade Bruno Leibundgut (ESO) Astrophysics in a Golden Age • Full coverage of electro-magnetic spectrum – MAGIC/HESS ÆFermi/INTEGRAL Æ XMM/Chandra/Swift/Rossi XTE Æ Galex Æ HST/Gaia Æ ground-based optical/IR Æ Spitzer Æ Herschel Æ Planck Æ IRAM/JCMT/APEX/ALMA Æ radio telescopes – Large archive collections (e.g. ROSAT, ISO, ESO, HST, MAST) • Astro-particles joining in • cosmic rays, neutrinos, gravitational waves, dark matter searches Fantastic opportunities Astrophysics in a Golden Age • International Year of Astronomy – Fantastic boost in the public – Increased awareness – Strong public support – Continued interest • Connected to the ‘big’ questions • Where do we come from? • What is our future? Research themes • Similar for most observatories • Defined in several community for a – Astronet Science Vision and Roadmap – ESA Cosmic Vision initiative – National decadal reviews – Special publications • ESA-ESO working group reports • Specific fields (e.g. Connecting quarks with the Cosmos) Science themes • What matters in the universe? • Planets, planets, planets • How did stars and planets form? • The Milky Way our Home • Our own black hole • How galaxies form and evolve? • Fashions and other transients • When opportunity knocks What matters in the Universe? • Characterisation of dark matter and dark energy – Requires large samples – Multi-year and (often) multi-telescope projects • BAO (SDSS, 2dF, WiggleZ, BOSS, HETDEX) • Weak lensing (SNLS) • Supernovae (SNLS, ESSENCE, SDSS-II, SN Factory, LOSS, PanSTARRS, DES, -
First T Dwarfs in the VISTA Hemisphere Survey⋆⋆⋆
A&A 548, A53 (2012) Astronomy DOI: 10.1051/0004-6361/201220182 & c ESO 2012 Astrophysics First T dwarfs in the VISTA Hemisphere Survey, N. Lodieu1,2, B. Burningham3,A.Day-Jones4, R.-D. Scholz5, F. Marocco3, S. Koposov6,7, D. Barrado y Navascués8,9, P. W. Lucas3,P.Cruz9, J. Lillo9,H.Jones3, A. Perez-Garrido10,M.T.Ruiz4,D.Pinfield3,R.Rebolo1,2, V. J. S . B éjar 1,2, S. Boudreault1,2,J.P.Emerson11,M.Banerji9, E. González-Solares6, S. T. Hodgkin6, R. McMahon6,J.Canty3, and C. Contreras3 1 Instituto de Astrofísica de Canarias (IAC), Calle Vía Láctea s/n, 38200 La Laguna, Tenerife, Spain e-mail: [email protected] 2 Departamento de Astrofísica, Universidad de La Laguna (ULL), 38205 La Laguna, Tenerife, Spain 3 Centre for Astrophysics Research, Science and Technology Research Institute, University of Hertfordshire, HatfieldAL109AB,UK 4 Departamento de Astronomia, Universidad de Chile, Casilla 36-D, Santiago, Chile 5 Leibniz-Institut für Astrophysik Potsdam (AIP), An der Sternwarte 16, 14482 Potsdam, Germany 6 Institute of Astronomy, Madingley Road, Cambridge CB3 0HA, UK 7 Sternberg Astronomical Institute, Lomonosov Moscow State University, Universitetsky pr. 13, 119992 Moscow, Russia 8 Centro Astronómico Hispano Alemán, Calle Jesús Durbán Remón 2-2, 04004 Almería, Spain 9 Departamento de Astrofisica, Centro de Astrobiologia (INTA-CSIC), ESAC Campus, PO Box 78, 28691 Villanueva de la Cañada, Spain 10 Universidad Politécnica de Cartagena, Campus Muralla del Mar, Cartagena, 30202 Murcia, Spain 11 School of Physics & Astronomy, Queen Mary University of London, Mile End Road, London E1 4NS, UK Received 7 August 2012 / Accepted 8 October 2012 ABSTRACT Aims. -
Esoshop Catalogue
ESOshop Catalogue www.eso.org/esoshop Annual Report 2 Annual Report Annual Report Content 4 Annual Report 33 Mounted Images 6 Apparel 84 Postcards 11 Books 91 Posters 18 Brochures 96 Stickers 20 Calendar 99 Hubbleshop Catalogue 22 Media 27 Merchandise 31 Messenger Annual Report 3 Annual Report Annual Report 4 Annual Report Annual Report ESO Annual Report 2018 This report documents the many activities of the European Southern Observatory during 2018. Product ID ar_2018 Price 4 260576 727305 € 5.00 Annual Report 5 Apparel Apparel 6 Apparel Apparel Running Tank Women Running Tank Men ESO Cap If you love running outdoors or indoors, this run- If you love running outdoors or indoors, this run- The official ESO cap is available in navy blue and ning tank is a comfortable and affordable option. ning tank is a comfortable and affordable option. features an embroidered ESO logo on the front. On top, it is branded with a large, easy-to-see On top, it is branded with a large, easy-to-see It has an adjustable strap, measuring 46-60 cm ESO logo and website on the back and a smaller ESO logo and website on the back and a smaller (approx) in circumference, with a diameter of ESO 50th anniversary logo on the front, likely to ESO 50th anniversary logo on the front, likely to 20 cm (approx). raise the appreciation or the curiosity of fellow raise the appreciation or the curiosity of fellow runners. runners. Product ID apparel_0045 Product ID apparel_0015 (M) Product ID apparel_0020 (M) Price Price Price € 8.00 4 260576 720306 € 14.00 4 260576 720047 € 14.00 4 260576 720092 Product ID apparel_0014 (L) Product ID apparel_0019 (L) Price Price € 14.00 4 260576 720030 € 14.00 4 260576 720085 Product ID apparel_0013 (XL) Price € 14.00 4 260576 720023 Apparel 7 Apparel ESO Slim Fit Fleece Jacket ESO Slim Fit Fleece Jacket Men ESO Astronomical T-shirt Women This warm long-sleeve ESO fleece jacket is perfect This warm long-sleeve ESO fleece jacket is perfect This eye-catching nebular T-shirt features stunning for the winter. -
Very Large Telescope Paranal Science Operations VIRCAM/VISTA User Manual
EUROPEAN SOUTHERN OBSERVATORY Organization Europeene´ pour des Recherches Astronomiques dans l’Hemisph´ ere` Austral Europaische¨ Organization f¨ur astronomische Forschung in der s¨udlichen Hemisphare¨ ESO - European Southern Observatory Karl-Schwarzschild Str. 2, D-85748 Garching bei M¨unchen Very Large Telescope Paranal Science Operations VIRCAM/VISTA User Manual Doc. No. VIS-MAN-ESO-06000-0002 Issue 85.0, Date 18/12/2009 V. D. Ivanov, T. Szeifert Prepared ................................................ Date Signature A. Kaufer Approved ................................................ Date Signature C. Dumas Released ................................................ Date Signature ii VIRCAM/VISTAUserManual VIS-MAN-ESO-06000-0002 This page was intentionally left blank VIRCAM/VISTAUserManual VIS-MAN-ESO-06000-0002 iii Change Record Issue Date Section affected Reason/Initiation/Documents/Remarks 0.10 09/09/2008 All Creation 1.00 18/12/2009 All First public release for P85. 1.01 01/07/2010 All Update for P86 Phase II and P87 Phase I. 1.02 01/12/2010 Twilight, overheads. Update P87 Phase II. 1.03 11/03/2011 Minor updates. Update P88 Phase I. 1.04 04/08/2011 Web links updated. 1.05 13/06/2013 Template tile6sky info. Update P92 Phase I. iv VIRCAM/VISTAUserManual VIS-MAN-ESO-06000-0002 This page was intentionally left blank VIRCAM/VISTAUserManual VIS-MAN-ESO-06000-0002 v Contents 1 Introduction 1 2 Applicabledocumentsandothersourcesofinformation 3 3 Abbreviations and Acronyms 5 4 VISTA and VIRCAM in a nut-shell 6 5 The VISTA Telescope – Technical Description 7 6 The VIRCAM - VISTA Infra-Red Camera 9 6.1 Generalfeatures ................................. ...... 9 6.2 Detectors ....................................... .... 11 6.3 Filters ......................................... .... 15 6.4 Sensitivity.................................... -
The ESO Survey Telescopes — Mapping the Sky in the Finest Detail
The ESO Survey Telescopes — Mapping the Sky in the Finest Detail European Southern Observatory The Milky Way arches over the VISTA telescope. Credit: ESO/Y. Beletsky The ESO Survey Telescopes — Mapping the Sky in the Finest Detail Two powerful survey telescopes — the sky at near-infrared wavelengths. VISTA National Institute for Astrophysics (INAF). Visible and Infrared Survey Telescope was conceived and developed by a The VST became operational at Paranal for Astronomy (VISTA) and the VLT Survey consortium of 18 UK universities led by early in 2011. Telescope (VST) — are sited at ESO’s Queen Mary, University of London, and its Paranal Observatory in northern Chile. construction was managed by the UK The scientific goals of the surveys include They are arguably the most powerful Science and Technology Facilities Coun- many of the most exciting problems in dedicated imaging survey telescopes in cil’s UK Astronomy Technology Centre in astrophysics today, ranging from the nature the world and greatly increase the scien- Edinburgh. VISTA was given to ESO as of dark energy to the threat of near-Earth tific discovery potential of the Paranal an in-kind contribution as part of the UK’s asteroids. Large teams of astronomers Observatory. accession agreement. throughout Europe are conducting the surveys. Some cover most of the southern Many of the most interesting astronomical VISTA’s main mirror is the most highly sky while others focus on smaller areas. objects — from tiny, but potentially dan- curved mirror of its size ever made and its gerous, near-Earth asteroids to the most construction is a formidable accomplish- Both VISTA and the VST are producing remote quasars — are rare. -
The ESO Survey Telescopes — Mapping the Sky in the Finest Detail
The ESO Survey Telescopes — Mapping the Sky in the Finest Detail European Southern Observatory The ESO Survey Telescopes — Mapping the Sky in the Finest Detail Two new and powerful telescopes — the VISTA has a main mirror 4.1 metres full Moon. It complements VISTA and will Visible and Infrared Survey Telescope for across and is by far the largest telescope survey the visible-light sky. Astronomy (VISTA) and the VLT Survey in the world dedicated to surveying the Telescope (VST) — are starting their work sky at near-infrared wavelengths. VISTA The VST is the result of a joint venture at ESO’s Paranal Observatory in northern was conceived and developed by a between ESO and the Capodimonte As- Chile. They are arguably the most power- consortium of 18 UK universities led by tronomical Observatory (OAC) of Naples, ful dedicated imaging survey telescopes Queen Mary, University of London, and a research centre of the Italian National in the world and will hugely increase the its construction was managed by the UK Institute for Astrophysics (INAF). The VST scientific discovery potential of the Paranal Science and Technology Facilities Coun- is expected to become operational at Observatory. cil’s UK Astronomy Technology Centre in Paranal early in 2011. Edinburgh. VISTA was given to ESO as an Many of the most interesting astronomi- in-kind contribution as part of the UK’s The scientific goals of the surveys include cal objects — from tiny, but potentially accession agreement. many of the most exciting problems in as- dangerous, near-Earth asteroids to the trophysics today, ranging from the nature most remote quasars — are rare. -
ESO Public Surveys with VST and VISTA
ESO PS with the VST and VISTA The ESO Survey team: Magda Arnaboldi, Mark J Neeser, Laura C Parker, Piero Rosati, Marco Lombardi, Jörg P Dietrich, Wolfgang Hummel. A new chapter for European astronomy will soon begin with dedicated survey telescopes in the optical and near-infrared. The intent of this article is to illustrate the ESO policies for managing PS and validating their advanced data products, to introduce the VST and VISTA telescopes along with their wide-field instruments, and to provide a brief summary of the planned public surveys (PS). ESO policies for PS and their implementation These large collaborative surveys within Europe target many of the fundamental questions in astrophysics today, ranging from the nature of dark energy to the universality of the stellar initial mass function. In the following, we illustrate briefly the mechanisms that ESO has set in place to manage the survey projects, to ensure their legacy value and their usefulness for the astronomical community at large. Survey Management Plan: The PIs whose public survey (PS) proposals have been reviewed by the Public Survey Panel (PSP) and recommended by the Observing Programme Committee (OPC) are then asked to submit their Survey Management Plan (SMP). The ESO Guidelines for the preparation of the SMP are available at http://www.eso.org/observing/observing.html. The SMP represents an additional form requested from the PIs and it is an integral part of ESO’s appraisal of the proposal. The SMP aims at collecting the necessary information to carry out PS in Service Mode (SM), and allows for an efficient and timely planning of Phase 2 and telescope operations. -
Top-100-Images-From-ESO.Pdf
To his Majesty Albert II of Belgium. Sharing our admiration of the wonders of the Universe. Top 100 Images from ESO VISTA’s infrared view of the Orion Nebula This wide-ield view of the Orion Nebula (Messier 42), lying about 1350 light-years from Earth, was taken with the VISTA infrared survey telescope at ESO’s Paranal Observatory in Chile. The new telescope’s huge ield of view allows the whole nebula and its surroundings to be imaged in a single picture and its infrared vision also means that it can peer deep into the normally hidden dusty regions and reveal the curious antics of the very active young stars buried there. This image was created from images taken through Z, J and Ks ilters in the near-infrared part of the spectrum. The exposure times were ten minutes per ilter. The image covers a region of sky about one degree by 1.5 degrees. Credit: ESO/J. Emerson/VISTA. Acknowledgment: Cambridge Astronomical Survey Unit 6 | Top 100 Images from ESO Top 100 Images from ESO | 7 The Helix Nebula This colour-composite image of the Helix Nebula (NGC 7293) was created from images obtained using the the Wide Field Imager (WFI), an astronomical camera attached to the 2.2-metre Max-Planck Society/ESO telescope at the La Silla observatory in Chile. The blue-green glow in the centre of the Helix comes from oxygen atoms shining under effects of the intense ultraviolet radiation of the 120 000 degree Celsius central star and the hot gas. Further out from the star and beyond the ring of knots, the red colour from hydrogen and nitrogen is more prominent. -
Project Status [6267-7]
VISTA: Project Status Alistair M McPherson*1, Andrew Born1, Will Sutherland2, Jim Emerson3, Bryan Little1, Paul Jeffers1, Malcolm Stewart1, John Murray1, Kim Ward4. 1United Kingdom Astronomy Technology Centre, Royal Observatory Edinburgh, Blackford Hill, Edinburgh, EH9 3HJ, UK 2Institute for Astronomy Madingley Road Cambridge, CB3 0HA, UK 3Astronomy Unit. School of Mathematical Sciences, Queen Mary University of London, Mile End Road London E1 4NS, UK 4 Rutherford Appleton Laboratory, Chilton, Didcot, Oxfordshire, OX11 0QX, UK ABSTRACT VISTA is a 4-m wide field survey telescope with a near infra-red camera and a demanding f/1 primary design now well into its manufacturing phase. We contracted out major items, and generated a coordinated approach to the management of engineering budgets through systems engineering, risks through risk management, and safety through the generation of safety cases. Control of the interfaces and science requirements has been maintained and developed through the current phase. The project is developing the commissioning plan to deliver an effective and safe facility. The current status of VISTA is presented as we move towards the on site integration phase. Keywords: VISTA, Infrared, Survey, Telescope, Wide Field Astronomy 1 INTRODUCTION The Visible and Infrared Survey Telescope for Astronomy (VISTA) is a 4 metre class wide field telescope designed to conduct large-scale, surveys of the sky at near infrared wavelengths (0.9 to 2.5 µm). It could also operate at visible wavelengths (0.35 to 1.0 µm) if a second camera became available. VISTA will become a part of ESO’s Cerro Paranal Observatory in Chile, and can in effect be considered as a single integrated IR camera with a field of view of 1.65 degrees, in which the “telescope” is really the fore-optics.