Valve Lash Adjustment Elements
Total Page:16
File Type:pdf, Size:1020Kb
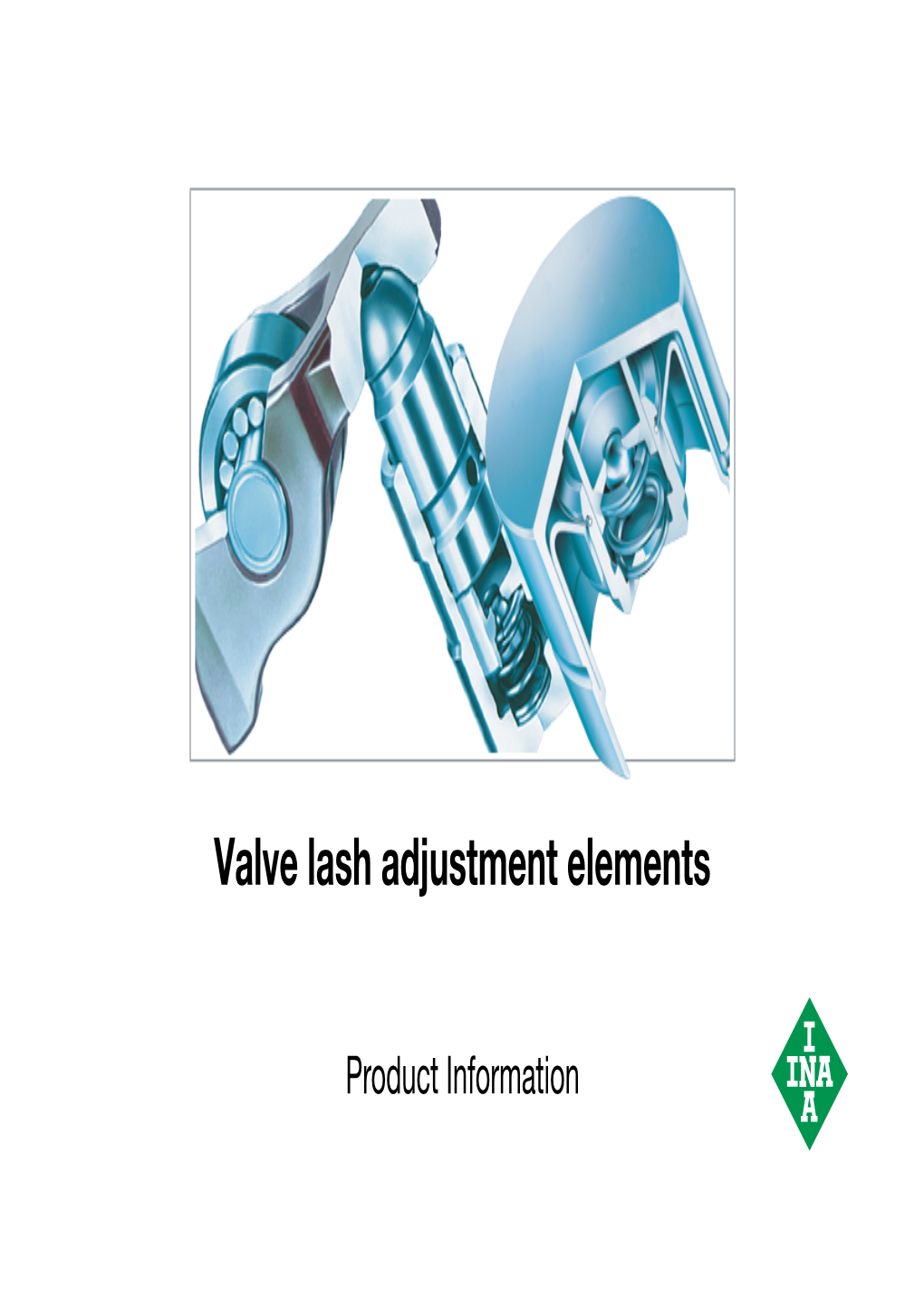
Load more
Recommended publications
-
Models Tio-540-Af1a
Lycoming Reciprocating Engine Division/ 652 Oliver Street Subsidiary of Textron Inc. Williamsport, PA 17701 U.S.A. 717/323-6181 TECHNICAL PUBLICATIONREVISION REVISION No. PUBLICATION PUBLICATION No. PUBLICATION DATE PC-315-8A TIO-540-AF1A PC-315-8 September, 1989 The page(s) furnished herewith are intended to replace the corresponding page(s) of the publication indicated above. Previous revisions to this publication This revision consists of: - None February, 1995 Pages 4-1, 4-2, 4-3 LYCOMING A Textron Company 652 Oliver Street Williamsport, PA 17701 U.S.A. 570/323-6181 TECHNICAL PUBLICATION SUPPLEMENT REVISION No. PUBLICATION PUBLICATION No. PUBLICATION DATE AF1 B Supplement TIO-540-AFIA PC-315-8 SEPTEMBER 1989 PC-315-8B Engines The attached pages have been revised to accommodate corrections and these page(s) need to replace the existing page(s) in your AF1 B Supplement . Page 6-5A, 6-7 - Revised Figure 25 Text Page 7-10 - Revised Figure 30 Illustration © 2002 by Lycoming, "All Rights Reserved" A Textron Company 652 Oliver Street Williamsport, PA 17701 U.S.A. 570/323-6181 TECHNICAL PUBLICATION SUPPLEMENT REVISION No. PUBLICATION PUBLICATION No. PUBLICATION DATE AFIB Supplement TIO-540-AF1 A PC-31 5-8 SEPTEMBER 1989 PC-31 5-8B Engines The page(s) furnished herewith are intended to be used In conjunction with the existing page(s) of the publication Indicated above. Previous revisions to this publication This supplement consists of: - FEBRUARY. 1995 NOVEMBER, 2002 PC-315-8A These Figures are to be used inconjunction with PC-315-8 Parts -
Special Service Tools for Lycoming Piston Engines March 2010 2
652 Oliver Street Williamsport, Pennsylvania 17701 SPECIAL SERVICE TOOLS FOR LYCOMING PISTON ENGINES MARCH 2010 2ND EDITION SSP384 LYCOMING SERVICE TOOLS INTRODUCTION This catalog replaces Tool Catalog SSP578 dated November, 1978. This catalog contains information relative to tools used for modification and maintenance of Lycoming opposed aircraft engines. It consists of four sections: The first is an alphabetical index and the second a numerical pictorial listing with brief descriptions. The third is a Service Publication Cross Reference Index and the fourth is a listing of obsolete tools. The illustrations used in this catalog show the general appearance of the tools but are not related according to size. In some cases, a single illustration has been used to cover a number of tools similar in appearance, with different tool numbers; therefore it is necessary, when ordering tools, to note carefully the descriptions and tool numbers in the text. Any tool described as being applicable to engines with “crosswise accessories” or ”crosswise accessory housings” do not include VO-435-B1A and TVO-435-F1A helicopter engines and TIO-541 and TIGO-541 integral accessory drive engines; tools applicable to these engines are specifically designated by engine model. PRICES This catalog does not list prices. A separate numerically arranged parts and tool price list is available and is supplied to distributors of Lycoming Engines. HOW TO ORDER Tools must be ordered by or through authorized Lycoming distributors. A tool must be designated by a tool number together with a name sufficiently descriptive to identify the tool. It is not necessary to write the full catalog description of the tool. -
Investigating the Effects of Oil Pressure on Valve Rotation for a Direct Acting Valve Train
INVESTIGATING THE EFFECTS OF OIL PRESSURE ON VALVE ROTATION FOR A DIRECT ACTING VALVE TRAIN Liviu JELENSCHI, Corneliu COFARU, Gabriel SANDU Transilvania University of Brasov, Romania Abstract. This paper investigates the influence of oil pressure on the engine exhaust valve rotation for a direct acting valve train. In introduction, a short presentation of the direct acting valve train is made and the necessity of the valve rotation is described. The test rig and the equipment used for measuring the influence of the oil pressure upon valve rotation are described in the main section of the paper. The results obtained revealed the fact that the oil pressure represents an important parameter which influences the valve rotation. Keywords: internal combustion engines, valve train, valve rotation, oil pressure 1. Introduction Internal combustion engines are complex systems, found in a continuous improvement. One of those improvements refers to increasing the service life up to 250,000 km with a minimal mechanical intervention during this period. This facts cause an increasing of impurities level from engine oil and also an increasing of components wear [1]. The valve train system represents one of the most important components of an internal combustion engine. The proper functioning of the valve train influences the gas exchange process and also the engine performances [2]. Today, five types of valve train systems exist, each of them having its advantages and Figure 1. The direct acting valve train components disadvantages, as shown in Table 1 [3, 4]. The valve motion is generated by the cam Table 1.Comparison between valve trains profile trough a hydraulic tappet. -
Hydraulic Roller Camshafts Chevrolet 90O V6 1987-1997 262 W/O Balance Shaft Cam Applications Basic Rpm Part NO
INTRODUCTION HISTORY OF ERSON CAMS In 1964, armed with a tremendous wealth of knowledge and a single cam-grinding machine, Sig Erson Racing Camshafts was born. The goal: To produce the best possible camshafts for all types of racing. The first Erson facility was a small 1600 square foot truck repair shop in Hawthorne, California. Meager beginnings for what Erson Cams was to become. With no budget for advertising or even state of the art machinery (lobe models and masters were often hand ground) Sig Erson Racing Camshafts quickly gained a huge following in both racing and the burgeoning hot rod scene of the 60's and 70's. It was simple, if you wanted a engine that made incredible power yet was easy on valve train parts, an Erson Cam was your only choice. Sig Erson Racing Camshafts quickly out grew the Hawthorne Facility and moved, in 1967 to a 4000 sq ft facility in Long Beach, California. In 1969, Mr. Erson and his crew of 10 full time cam grinders, moved yet again to a 10,000 sq ft building. At the time it was the largest facility in the country dedicated to state of the art camshaft development and grinding. In 1981 Super Shops Inc purchased Sig Erson Racing Camshafts. The name was changed to Erson Cams and the company was relocated to Carson City, Nevada. Erson Camshafts have powered motor sport racings greats to some impressive milestones: • Eddie Hill: The first Top Fuel Dragster to break the four-second barrier. • Chuck Etchells: The first Top Fuel Funny Car to break the four-second barrier. -
Lycoming and Sticking Valves by Steve Ells There Are Distinct
Lycoming and Sticking Valves By Steve Ells There are distinct differences between Lycoming and Continental engines. One of the most distinctive is the method each manufacturer uses to maintain acceptable exhaust valve temperatures. Exhaust valves undergo tremendous pressures and temperatures. Internal cylinder pressures can climb as high as 1,000 psi and temperatures as high as 2,000 degrees F. Yet they must still be metallurgic ally stable—they can't warp or stretch under these conditions. Continental chose to install a solid stemmed exhaust valve that is cooled by contact with the valve seat. This is the primary reason why Continental valve face-to-seat contact is critical. Whenever the valve face-to-seat contact is compromised—due to less than ideal machine work when fitting the valves, or when debris such as carbon or lead prevents a solid contact—valve cooling is compromised and valve overheating takes place. Over heating causes an easily identifiable metallic signature on the valve. This signature is the reason why a bore scope inspection of the valve is the number one engine health diagnostic tool for Continental engines. Lycoming took a different route. It chose to use valves with sodium-filled stems. This feature is very efficient at transferring heat away from the valve face and up the valve stem. The heat path is up the valve stem then by conduction out to the valve guides to the head cylinder cooling fins. Lycoming Valve Guide Reaming—Why and How Since Lycoming depends on heat transfer up the stem part of the valve the temperatures at the exhaust port and exhaust side of the aluminum cylinder head are hotter than the same areas in a Continental cylinder. -
Download Publication
652 Oliver Street SERVICE Williamsport, PA. 17701 U.S.A. Telephone +1 (800) 258-3279 U.S. and Canada (Toll Free) Telephone +1 (570) 323-6181 (Direct) Facsimile +1 (570) 327-7101 INSTRUCTION Email [email protected] www.lycoming.com DATE January 7, 2019 Service Instruction No. 1011N (Supersedes Service Instruction No. 1011M) Engineering Aspects are FAA Approved SUBJECT: Tappets and Lifters MODELS AFFECTED: All Lycoming engines TIME OF COMPLIANCE: At overhaul or at owner’s discretion REASON FOR REVISION: Added new engine model, TEO-540 Series to Table 3. NOTICE: Incomplete review of all the information in this document can cause errors. Read the entire Service Instruction to make sure you have a complete understanding of the requirements. This Service Instruction includes replacement part numbers, part supersedures, as well as inspection and replacement guidelines for tappets, hydraulic lifter assemblies, and hydraulic plungers on Lycoming Engines. Table 1 identifies the types of tappets and their respective part numbers. Table 2 shows the types of lifters and their respective part numbers. Table 3 identifies approved parts to be installed on Lycoming engines that use hydraulic lifters and tappets. Table 4 identifies the parts progression history for relevant superseded parts. Table 1 Tappet Types Straight Body Tappets Hyperbolic Tappet Roller Tappet Figure 1 Figure 2 Figure 4 Straight Body Hydraulic Figure 3 Hydraulic Solid Tappet* Spherical Tappet* Hyperbolic Tappet* Roller Tappet 15B28739 15B26588 15B26262 LRT23381 Supersedes: Supersedes: Supersedes: 15B26091 15B26064 15B21318 Before installation, apply undiluted lubricant to the face of the Before installation, apply tappet.** make-up engine oil to the tappets.** * Do not interchange with roller tappets.* (A different crankcase is necessary for roller tappets.) **Refer to the latest revision of Service Instruction No. -
Official Mopar Performance Engines Catalog
PERFORMANCE ENGINES CATALOG WHEN PASSION BECOMES POWER. WHEN LONGEVITY BECOMES LEGACY. WHEN THE RUMBLE BECOMES A ROAR. THAT’S WHEN YOU’VE UNLEASHED YOUR VEHICLE’S ULTIMATE PERFORMANCE. TABLE OF CONTENTS GEN III HEMI® ENGINES BIG BLOCK ENGINES 345 / 6.1L / 6.2L / 392 / 426 361 / 383 / 400 06 09 Crate HEMI® Engines 32 413 / 426 / 440 12 Crate HEMI® Engine Kits 34 Engine Hardware 14 Crate HEMI® Engine Accessories 34 Crankshafts & Hardware 16 Blocks 35 Timing Chains & Sprockets 17 Crankshafts & Hardware 36 Vibration Dampers 18 Pistons & Connecting Rods 36 Camshafts, Lifters & Hardware 18 Camshafts 38 Cylinder Heads, Gaskets & Hardware 19 Cylinder Heads, Gaskets & Hardware 38 Intake Manifolds, Hardware & Gaskets 19 Valvetrain 40 Valves & Valvetrain Hardware 42 Valve Covers & Hardware ® 44 Oiling Components GEN II HEMI ENGINES 45 Cooling Systems 426 / 572 20 22 Engine Hardware 22 Blocks SMALL BLOCK ENGINES 22 Crankshafts & Hardware 273 / 318 / 340 23 Timing Chains & Sprockets 46 360 / 5.2L / 5.9L 23 Vibration Dampers 48 Engine Hardware 23 Forged Aluminum Pistons 48 Timing Chains & Sprockets 24 Camshafts, Lifters & Hardware 48 Crankshafts & Hardware 25 Cylinder Heads, Gaskets & Hardware 50 Vibration Dampers 26 Valvetrain Hardware 51 Camshafts, Lifters & Hardware 26 Rocker Arms, Shafts, Stands & Hardware 52 Cylinder Heads, Gaskets & Hardware 27 Valve Covers & Hardware 54 Valvetrain Hardware 28 Oiling Components 55 Rocker Arms, Shafts, Stands & Hardware 29 Engine Cooling 56 Valve Covers & Hardware 29 Engine Installation Components 58 Intake Manifolds, Hardware & Gaskets 30 Intake Manifolds, Hardware & Gaskets 60 Oiling Components 60 Cooling Systems PERFORMANCE GAUGES 64 Gauges 62 67 Gauge Pods *Many images shown throughout the catalog are representative of the product. -
09A-Engine-Ewj-3.1L TD.Pdf
WJ ENGINE 9 - 1 ENGINE TABLE OF CONTENTS page page DESCRIPTION AND OPERATION OILPAN...............................45 ENGINE IDENTIFICATION ...................1 OIL PUMP..............................45 HYDRAULIC TAPPETS .....................2 OIL PUMP PRESSURE RELIEF VALVE ........46 DIAGNOSIS AND TESTING PISTONS AND CONNECTING ROD SERVICE DIAGNOSIS—DIESEL— ASSEMBLY............................48 MECHANICAL. ..........................9 ROCKER ARMS AND PUSH RODS ..........31 SERVICE DIAGNOSIS—DIESEL— TIMING GEAR COVER ....................41 PERFORMANCE .........................3 TIMING GEAR COVER OIL SEAL............40 TAPPET NOISE ..........................11 TRANSMISSION PILOT BUSHING ...........53 SERVICE PROCEDURES VALVE SPRINGS.........................31 VALVE SERVICE .........................11 VIBRATION DAMPER .....................40 REMOVAL AND INSTALLATION DISASSEMBLY AND ASSEMBLY 3.1L TURBO DIESEL ENGINE...............13 HYDRAULIC TAPPETS ....................58 CAMSHAFT .............................42 CLEANING AND INSPECTION CAMSHAFT BEARINGS....................44 CYLINDER HEAD ........................59 CRANKSHAFT AND MAIN BEARINGS ........55 CYLINDER WALL LINER ASSEMBLY .........61 CYLINDER HEAD COVER ..................28 OIL PUMP..............................61 CYLINDER WALL LINER ASSEMBLY .........51 PISTONS AND CONNECTING ROD ENGINE CYLINDER HEAD .................33 ASSEMBLY............................60 ENGINE OIL FILTER ......................48 ROCKER ARMS AND PUSH RODS ..........59 EXHAUST AND INTAKE MANIFOLD ..........24 -
IGO-540, IGSO-540 Series
Operators Manual Lycoming IGO-540, IGSO-540 Series Approved by FAA 3rd Edition Part No. 60297-15 January 2008 652 Oliver Street Williamsport, PA. 17701 U.S.A. 570/323-6181 IGO-540, IGSO-540 Series Operators Manual Lycoming Part Number: 60297-15 ©2008 by Lycoming. All rights reserved. Lycoming and Powered by Lycoming are trademarks or registered trademarks of Lycoming. All brand and product names referenced in this publication are trademarks or registered trademarks of their respective companies. For additional information: Mailing address: Lycoming Engines 652 Oliver Street Williamsport, PA 17701 U.S.A. Phone: Factory: 570-323-6181 Sales Department: 570-327-7268 Fax: 570-327-7101 Lycomings regular business hours are Monday through Friday from 8:00 AM through 5:00 PM Eastern Time (-5 GMT) Visit us on the World Wide Web at: http://www.lycoming.com LYCOMING OPERATORS MANUAL ATTENTION OWNERS, OPERATORS, AND MAINTENANCE PERSONNEL This operators manual contains a description of the engine, its specifications, and detailed information on how to operate and maintain it. Such maintenance procedures that may be required in conjunction with periodic inspections are also included. This manual is intended for use by owners, pilots and maintenance personnel responsible for care of Lycoming powered aircraft. Modifications and repair procedures are contained in Lycoming overhaul manuals; maintenance personnel should refer to these for such procedures. SAFETY WARNING Neglecting to follow the operating instructions and to carry out periodic maintenance procedures can result in poor engine performance and power loss. Also, if power and speed limitations specified in this manual are exceeded, for any reason; damage to the engine and personal injury can happen. -
June 21, 1955 A
June 21, 1955 A. W. RCKENEBACH 2,711,161 HYDRAULIC TAPPET Filed Sept. 16, 1952 Sheets-Sheet l ÆTTF|- | ?%zzzzzzzzzzzzzz INVENTOR AUGUST W. RICKENBACH ATTORAVEYS June 21, 1955 A. W. RICKENEBACH 2,711,161 HYDRAULIC TAPPET 2 Sheets-Sheet 2 S ??? È INVENTOR. AUGUST W. RICKENBACH. AT TORNEYs. 2,711,16 United States Patent Office Faterated Jurae 25, 1955 2 way, slight spurious movements delivered to the tappet are not transferred to the valves. - 2,711,161 In view of the foregoing, it will be appreciated that it is an object of the present invention to provide an im HYDRAULIC TAPPET 3 proved hydraulic tappet. August W. Rickenbach, Williamsport, Pa., assignor to Another object of the invention is to provide means Avco Manufacturing Corporation, Cincinnati, Ohio, a for improving hydraulic tappet operation which can be corporation of Delaware readily added to existing tappets at very little cost. It is also an object of the invention to provide a hy Application September 16, 1952, Serial No. 309,787 draulic tappet which will prevent the transmission of very 1 Ciaim. (Cl. 123-90) small movements to the valve linkage. Stated otherwise, it is an object of the invention to provide a hydraulic tappet, the components of which must undergo a slight The present invention relates to a component of an relative movement before the tappet will be effective to internal combustion engine, and, more specifically, to an transfer motion from a camshaft to an associated valve. improved hydraulic tappet for use in an internal combus A still further object of the invention is the provision tion engine having valves for controlling the intake or of an improvement for a hydraulic tappet which will exhaust of gases from a cylinder of the engine. -
Army Tm 9-2815-253-24 Air Force to 38G1-93-2 Marine Corps Tm 2815-24/3 C3 Change Headquarters, Departments of the Army, the Air Force and Headquarters, U.S
ARMY TM 9-2815-253-24 This copy is a reprint which includes current AIR FORCE TO 38G1-93-2 pages from Change 1. MARINE CORPS TM 2815-24/3 TECHNICAL MANUAL UNIT, DIRECT SUPPORT AND GENERAL SUPPORT MAINTENANCE INSTRUCTIONS DIESEL ENGINE MODEL DN4M 4 CYLINDER 1.2 LITER NSN: 2815-01-350-2206 DISTRIBUTION STATEMENT A: Approved for public release; distribution is unlimited. HEADQUARTERS, DEPARTMENTS OF THE ARMY, AND THE AIR FORCE, AND HEADQUARTERS, U.S. MARINE CORPS 15 SEPTEMBER 1993 ARMY TM 9-2815-253-24 AIR FORCE TO 38G1-93-2 MARINE CORPS TM 2815-24/3 C3 CHANGE HEADQUARTERS, DEPARTMENTS OF THE ARMY, THE AIR FORCE AND HEADQUARTERS, U.S. MARINE CORPS NO. 3 WASHINGTON, D.C., 30 OCTOBER 1996 UNIT, DIRECT SUPPORT AND GENERAL SUPPORT MAINTENANCE INSTRUCTIONS DIESEL ENGINE MODEL DN4M 4 CYLINDER 1.2 LITER NSN: 2815-01-350-2206 DISTRIBUTION STATEMENT A: Approved for public release; distribution is unlimited TM 9-2815-253-24/TO 38G1-93-2fTM 2815-24/3, 15 September 1993, is changed as follows: 1. Remove and insert pages as indicated below. New or changed text material is indicated by a vertical bar in the margin. An illustration change is indicated by a miniature pointing hand. Remove pages Insert pages i and ii i and ii 3-1 and 3-2 3-1 and 3-2, 3-13 and 3-14 3-13 and 3-14 3-27 and 3-28 3-27 and 3-28 2. Retain this sheet in front of manual for reference purposes. ARMY TM 9-2815-253-24 AIR FORCE TO 38G1-93-2 MARINE CORPS TM 2815-24/3 C2 CHANGE HEADQUARTERS, DEPARTMENTS OF THE ARMY, THE AIR FORCE AND HEADQUARTERS, U.S. -
Investigating the Hydraulic Tappet Rotation for a Direct Acting Valve Train
Bulletin of the Transilvania University of Bra şov Series I: Engineering Sciences • Vol. 5 (54) No. 1 - 2012 INVESTIGATING THE HYDRAULIC TAPPET ROTATION FOR A DIRECT ACTING VALVE TRAIN L. JELENSCHI 1 C. COFARU 1 G. SANDU 1 Abstract: The paper presents the research regarding the rotational movement of a hydraulic tappet from a direct acting valve train system. Firstly the advantages and disadvantages of the tappet rotation during engine functioning are described. Then, a description of the virtual model of the direct acting valve train modeling process is made and the parameters that influence the rotational movement are presented. The results obtained with the virtual model are presented in comparison with the experimental results obtained by other authors. The conclusions revealed that the position of the camshaft, the engine speed and the friction coefficient have a significant influence on the hydraulic tappet rotation. Key words: direct acting valve train, tappet rotation, dynamic analysis, wear. 1. Introduction entails a massive wear [5], [8], [12], [14]. An analysis of the tappet rotation is The analysis of the valve train system is important because it is known the fact that very important because it influences the friction loses because of the valve train gas exchange process and the engine represent almost 21% from entire engine performance. The main role of this system friction loses. So if the tappet rotates the is to ensure a suitable filling of engine value of the friction loses decrease cylinders with gasoline-air mixture for significant [6], [8-10]. spark ignition engines or with air for Also the tappet rotation ensures a compression ignition engine.