Flow Dependent Turbulent Schmidt Number in Containment Atmosphere Mixing
Total Page:16
File Type:pdf, Size:1020Kb
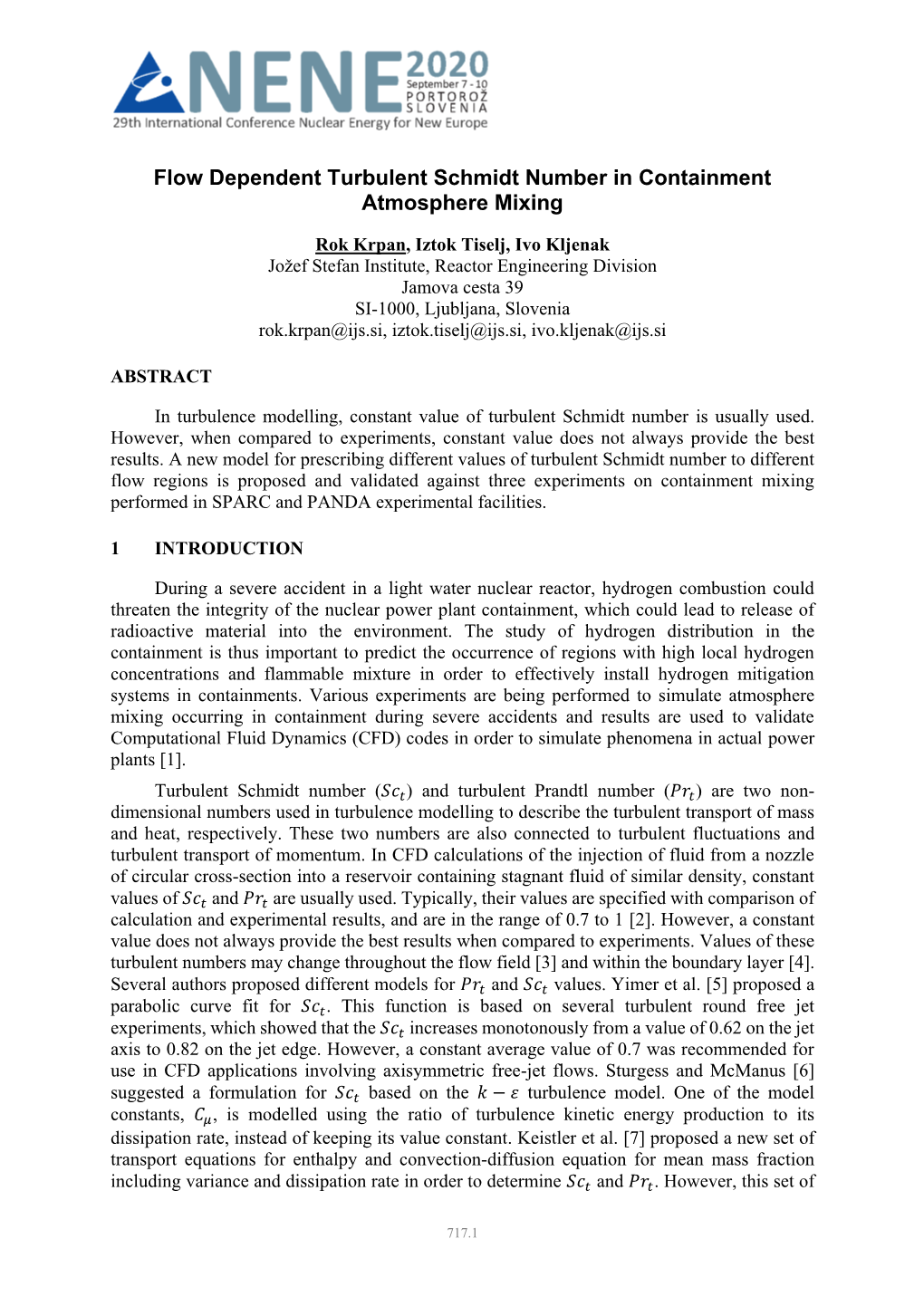
Load more
Recommended publications
-
Turbulent-Prandtl-Number.Pdf
Atmospheric Research 216 (2019) 86–105 Contents lists available at ScienceDirect Atmospheric Research journal homepage: www.elsevier.com/locate/atmosres Invited review article Turbulent Prandtl number in the atmospheric boundary layer - where are we T now? ⁎ Dan Li Department of Earth and Environment, Boston University, Boston, MA 02215, USA ARTICLE INFO ABSTRACT Keywords: First-order turbulence closure schemes continue to be work-horse models for weather and climate simulations. Atmospheric boundary layer The turbulent Prandtl number, which represents the dissimilarity between turbulent transport of momentum and Cospectral budget model heat, is a key parameter in such schemes. This paper reviews recent advances in our understanding and modeling Thermal stratification of the turbulent Prandtl number in high-Reynolds number and thermally stratified atmospheric boundary layer Turbulent Prandtl number (ABL) flows. Multiple lines of evidence suggest that there are strong linkages between the mean flowproperties such as the turbulent Prandtl number in the atmospheric surface layer (ASL) and the energy spectra in the inertial subrange governed by the Kolmogorov theory. Such linkages are formalized by a recently developed cospectral budget model, which provides a unifying framework for the turbulent Prandtl number in the ASL. The model demonstrates that the stability-dependence of the turbulent Prandtl number can be essentially captured with only two phenomenological constants. The model further explains the stability- and scale-dependences -
Analysis of Mass Transfer by Jet Impingement and Heat Transfer by Convection
Analysis of Mass Transfer by Jet Impingement and Study of Heat Transfer in a Trapezoidal Microchannel by Ejiro Stephen Ojada A thesis submitted in partial fulfillment of the requirements for the degree of Master of Science in Mechanical Engineering Department of Mechanical Engineering University of South Florida Major Professor: Muhammad M. Rahman, Ph.D. Frank Pyrtle, III, Ph.D. Rasim Guldiken, Ph.D. Date of Approval: November 5, 2009 Keywords: Fully-Confined Fluid, Sherwood number, Rotating Disk, Gadolinium, Heat Sink ©Copyright 2009, Ejiro Stephen Ojada i TABLE OF CONTENTS LIST OF FIGURES ii LIST OF SYMBOLS v ABSTRACT viii CHAPTER 1: INTRODUCTION AND LITERATURE REVIEW 1 1.1 Introduction (Mass Transfer by Jet Impingement ) 1 1.2 Literature Review (Mass Transfer by Jet Impingement) 2 1.3 Introduction (Heat Transfer in a Microchannel) 7 1.4 Literature Review (Heat Transfer in a Microchannel) 8 CHAPTER 2: ANALYSIS OF MASS TRANSFER BY JET IMPINGEMENT 15 2.1 Mathematical Model 15 2.2 Numerical Simulation 19 2.3 Results and Discussion 21 CHAPTER 3: ANALYSIS OF HEAT TRANSFER IN A TRAPEZOIDAL MICROCHANNEL 42 3.1 Modeling and Simulation 42 3.2 Results and Discussion 48 CHAPTER 4: CONCLUSION 65 REFERENCES 67 APPENDICES 79 Appendix A: FIDAP Code for Analysis of Mass Transfer by Jet Impingement 80 Appendix B: FIDAP Code for Fluid Flow and Heat Transfer in a Composite Trapezoidal Microchannel 86 i LIST OF FIGURES Figure 2.1a Confined liquid jet impingement between a rotating disk and an impingement plate, two-dimensional schematic. 18 Figure 2.1b Confined liquid jet impingement between a rotating disk and an impingement plate, three-dimensional schematic. -
Turbulence, Entropy and Dynamics
TURBULENCE, ENTROPY AND DYNAMICS Lecture Notes, UPC 2014 Jose M. Redondo Contents 1 Turbulence 1 1.1 Features ................................................ 2 1.2 Examples of turbulence ........................................ 3 1.3 Heat and momentum transfer ..................................... 4 1.4 Kolmogorov’s theory of 1941 ..................................... 4 1.5 See also ................................................ 6 1.6 References and notes ......................................... 6 1.7 Further reading ............................................ 7 1.7.1 General ............................................ 7 1.7.2 Original scientific research papers and classic monographs .................. 7 1.8 External links ............................................. 7 2 Turbulence modeling 8 2.1 Closure problem ............................................ 8 2.2 Eddy viscosity ............................................. 8 2.3 Prandtl’s mixing-length concept .................................... 8 2.4 Smagorinsky model for the sub-grid scale eddy viscosity ....................... 8 2.5 Spalart–Allmaras, k–ε and k–ω models ................................ 9 2.6 Common models ........................................... 9 2.7 References ............................................... 9 2.7.1 Notes ............................................. 9 2.7.2 Other ............................................. 9 3 Reynolds stress equation model 10 3.1 Production term ............................................ 10 3.2 Pressure-strain interactions -
Huq, P. and E.J. Stewart, 2008. Measurements and Analysis of the Turbulent Schmidt Number in Density
GEOPHYSICAL RESEARCH LETTERS, VOL. 35, L23604, doi:10.1029/2008GL036056, 2008 Measurements and analysis of the turbulent Schmidt number in density stratified turbulence Pablo Huq1 and Edward J. Stewart2 Received 18 September 2008; revised 27 October 2008; accepted 3 November 2008; published 3 December 2008. [1] Results are reported of measurements of the turbulent where rw is the buoyancy flux, uw is the Reynolds shear Schmidt number Sct in a stably stratified water tunnel stress. The ratio Km/Kr is termed the turbulent Schmidt experiment. Sct values varied with two parameters: number Sct (rather than turbulent Prandtl number) as Richardson number, Ri, and ratio of time scales, T*, of salinity gradients in water are used for stratification in the eddy turnover and eddy advection from the source of experiments. Prescription of a functional dependence of Sct turbulence generation. For large values (T* 10) values on Ri = N2/S2 is a turbulence closure scheme [Kantha and of Sct approach those of neutral stratification (Sct 1). In Clayson, 2000]. Here the buoyancy frequency N is defined 2 contrast for small values (T* 1) values of Sct increase by the gradient of density r as N =(Àg/ro)(dr/dz), and g is with Ri. The variation of Sct with T* explains the large the gravitational acceleration. S =dU/dz is the velocity scatter of Sct values observed in atmospheric and oceanic shear. Analyses of field, lab and numerical (RANS, DNS data sets as a range of values of T* occur at any given Ri. and LES) data sets have led to the consensus that Sct The dependence of Sct values on advective processes increases with Ri [see Esau and Grachev, 2007, and upstream of the measurement location complicates the references therein]. -
The Analogy Between Heat and Mass Transfer in Low Temperature Crossflow Evaporation
View metadata, citation and similar papers at core.ac.uk brought to you by CORE provided by AUT Scholarly Commons The analogy between heat and mass transfer in low temperature crossflow evaporation Reza Enayatollahi*, Roy Jonathan Nates, Timothy Anderson Department of Mechanical Engineering, Auckland University of Technology, Auckland, New Zealand. Corresponding Author: Reza Enayatollahi Email Address: [email protected] Postal Address: WD308, 19 St Paul Street, Auckland CBD, Auckland, New Zealand Phone Number: +64 9 921 9999 x8109 Abstract This study experimentally determines the relationship between the heat and mass transfer, in a crossflow configuration in which a ducted airflow passes through a planar water jet. An initial exploration using the Chilton-Colburn analogy resulted in a coefficient of determination of 0.72. On this basis, a re-examination of the heat and mass transfer processes by Buckingham’s-π theorem and a least square analysis led to the proposal of a new dimensionless number referred to as the Lewis Number of Evaporation. A modified version of the Chilton-Colburn analogy incorporating the Lewis Number of Evaporation was developed leading to a coefficient of determination of 0.96. 1. Introduction Heat and mass transfer devices involving a liquid interacting with a gas flow have a wide range of applications including distillation plants, cooling towers and aeration processes and desiccant drying [1-5]. Many studies have gone through characterising the heat and mass transfer in such configurations [6-9]. The mechanisms of heat and mass transfer are similar and analogical. Therefore, in some special cases where, either the heat or mass transfer data are not reliable or may not be available, the heat and mass transfer analogy can be used to determine the missing or unreliable set of data. -
1 Pe = Re× Sc Peclet Number
Passive Scalar Diffusion in the Near Field Region of Turbulent Rectangular Submerged Free Jets Andrea Boghia, Ivan Di Venutab, Fabio Gorib,* a School of Water, Energy and Agrifood, Cranfield University, Cranfield, Bedfordshire MK43 0AL, United Kingdom, b Department of Industrial Engineering, University of Rome “Tor Vergata”, Via del Politecnico 1, 00133 Rome, Italy. * Corresponding Author, [email protected] Abstract Jets are a common way to transfer mass among fluids, or from a fluid to a surface. At moderate Reynolds numbers and low turbulent intensities the jet exhibits a Near Field Region (NFR) several diameters long. Numerical results and a theoretical model are presented for the passive scalar diffusion in the NFR of a submerged free jet. Large Eddy Simulations (LES), in the Reynolds number 5000-40,000 and the Schmidt number range 1-100, are performed obtaining the passive scalar fields. Three mathematical models for the passive scalar diffusion are presented; the first one is valid in the NFR, specifically in the Undisturbed Region of Flow (URF), and the other two, obtained under the hypotheses of Tollmien and Görtler momentum spreadings, are valid in the Potential Core Region (PCR). The last two models employ a turbulent Schmidt number inversely proportional to the mean velocity gradient, conclusion obtained by the LES numerical results. The self-similar solutions of the passive scalar show good agreement with the LES results. The wide range of Reynolds and Schmidt numbers investigated gives generality to the results. Keywords: Submerged Rectangular Free Jet; Turbulent Flow; Near Field Region; Undisturbed Region of Flow; Passive Scalar; Large Eddy Simulation; Self-Similarity. -
Compressible Effects Modelling in Turbulent Cavitating Flows Jean Decaix, Eric Goncalvès Da Silva
Compressible effects modelling in turbulent cavitating flows Jean Decaix, Eric Goncalvès da Silva To cite this version: Jean Decaix, Eric Goncalvès da Silva. Compressible effects modelling in turbulent cav- itating flows. European Journal of Mechanics - B/Fluids, Elsevier, 2013, 39, pp.11-31. 10.1016/j.euromechflu.2012.12.001. hal-00768757 HAL Id: hal-00768757 https://hal.archives-ouvertes.fr/hal-00768757 Submitted on 12 Feb 2013 HAL is a multi-disciplinary open access L’archive ouverte pluridisciplinaire HAL, est archive for the deposit and dissemination of sci- destinée au dépôt et à la diffusion de documents entific research documents, whether they are pub- scientifiques de niveau recherche, publiés ou non, lished or not. The documents may come from émanant des établissements d’enseignement et de teaching and research institutions in France or recherche français ou étrangers, des laboratoires abroad, or from public or private research centers. publics ou privés. Compressible Effects Modelling in Turbulent Cavitating Flows Jean Decaix∗, Eric Goncalv`es∗ LEGI-Grenoble INP, 1025 rue de la Piscine, 38400 St Martin d’Heres, France Abstract A compressible, multiphase, one-fluid RANS solver has been developed to study turbulent cavitating flows. The interplay between turbulence and cav- itation regarding the unsteadiness and structure of the flow is complex and not well understood. This constitutes a determinant point to accurately sim- ulate the dynamic behaviour of sheet cavities. In the present study, different formulations including compressibility effects on turbulence are investigated. Numerical results are given for two partial cavities on Venturi geometries and comparisons are made with experimental data. -
Stability and Instability of Hydromagnetic Taylor-Couette Flows
Physics reports Physics reports (2018) 1–110 DRAFT Stability and instability of hydromagnetic Taylor-Couette flows Gunther¨ Rudiger¨ a;∗, Marcus Gellerta, Rainer Hollerbachb, Manfred Schultza, Frank Stefanic aLeibniz-Institut f¨urAstrophysik Potsdam (AIP), An der Sternwarte 16, D-14482 Potsdam, Germany bDepartment of Applied Mathematics, University of Leeds, Leeds, LS2 9JT, United Kingdom cHelmholtz-Zentrum Dresden-Rossendorf, Bautzner Landstr. 400, D-01328 Dresden, Germany Abstract Decades ago S. Lundquist, S. Chandrasekhar, P. H. Roberts and R. J. Tayler first posed questions about the stability of Taylor- Couette flows of conducting material under the influence of large-scale magnetic fields. These and many new questions can now be answered numerically where the nonlinear simulations even provide the instability-induced values of several transport coefficients. The cylindrical containers are axially unbounded and penetrated by magnetic background fields with axial and/or azimuthal components. The influence of the magnetic Prandtl number Pm on the onset of the instabilities is shown to be substantial. The potential flow subject to axial fieldspbecomes unstable against axisymmetric perturbations for a certain supercritical value of the averaged Reynolds number Rm = Re · Rm (with Re the Reynolds number of rotation, Rm its magnetic Reynolds number). Rotation profiles as flat as the quasi-Keplerian rotation law scale similarly but only for Pm 1 while for Pm 1 the instability instead sets in for supercritical Rm at an optimal value of the magnetic field. Among the considered instabilities of azimuthal fields, those of the Chandrasekhar-type, where the background field and the background flow have identical radial profiles, are particularly interesting. -
On the Values for the Turbulent Schmidt Number in Environmental Flows
Università di Napoli Federico II, 1224 On the Values for the Turbulent Schmidt Number in Environmental Flows Carlo Gualtieri University of Napoli Federico II, Napoli, Italy Acknowledgements Athanasios Angeloudis1, Fabian Bombardelli2, Sanjeev Jha3, Thorsten Stoesser 4 1 Imperial College, London, UK 2 University of California at Davis, Davis, USA Lyon, April 27, 2018 3 University of Manitoba, Winnipeg, Canada 4 Cardiff University, Cardiff, UK Outline of seminar Introduction Some remarks on turbulence and turbulence modeling The Turbulent Schmidt Number within the RANS Approach Review of the Literature on the Parameterization of the Turbulent Schmidt Number Water Systems Atmosphere Systems Case Studies Contaminant Dispersion Due to Transverse Turbulent Mixing in a Shallow Water Flow Tracer Transport in a Contact Tank Sediment Transport in Suspension Discussion Concluding remarks On the Values for the Turbulent Schmidt Number in Environmental Flows Università di Napoli Federico II, 1224 Importance of fluids in the environment – 1 Think about it. All living creatures are immersed in a moving fluid or another, in the air of the atmosphere or water of rivers, lakes and sea. http://quagroup.com/hydrologic-cycle/ On the Values for the Turbulent Schmidt Number in Environmental Flows Università di Napoli Federico II, 1224 Importance of fluids in the environment – 2 Flow transport has a number of benefits: It takes things away, and usually to a larger place (rivers to lake and sea, local airshed to broader atmosphere, troposphere to stratosphere, etc.) It creates time delay to allow modifications to take place along the way (ex: biodegradation of organic wastes down a river) Fluid motion at human and larger scales is almost always unstable, and the ensuing turbulence generates mixing , which • reduces concentrations, and • promotes encounters (fluid-fluid, interfaces with other fluid or soil), which in turn promote chemical reactions and transformation. -
Effect of Schmidt Number on the Structure and Propagation of Density Currents
OATAO is an open access repository that collects the work of Toulouse researchers and makes it freely available over the web where possible This is an author’s version published in: http://oatao.univ-toulouse.fr/9409 Official URL: http://doi.org/10.1007/s00162-008-0085-2 To cite this version: Bonometti, Thomas and Balachandar, Sivaramakrishnan Effect of schmidt number on the structure and propagation of density currents. (2008) Theoretical and Computational Fluid Dynamics, 22 (5). 341-361. ISSN 0935-4964 Any correspondence concerning this service should be sent to the repository administrator: [email protected] DOI 10.1007/s00162-008-0085-2 Thomas Bonometti · S. Balachandar Effect of Schmidt number on the structure and propagation of density currents Abstract The results of a numerical study of two- and three-dimensional Boussinesq density currents are described. They are aimed at exploring the role of the Schmidt number on the structure and dynamics of den- sity driven currents. Two complementary approaches are used, namely a spectral method and a finite-volume interface capturing method. They allow for the first time to describe density currents in the whole range of 2 4 Schmidt number 1 ≤ Sc ≤∞and Reynolds number 10 ≤ Re ≤ 10 . The present results confirm that the Schmidt number only weakly influences the structure and dynamics of density currents provided the 4 Reynolds number of the flow is large, say of O(10 ) or more. On the contrary low- to moderate-Re density currents are dependant on Sc as the structure of the mixing region and the front velocities are modified by diffusion effects. -
Mixing in High Schmidt Number Turbulent Jets Differs from Gas-Phase
Mixing in High Schmidt Number Turbulent Jets Thesis by Paul Lewis Miller In Partial Fulfillment of the Requirements for the Degree of Doctor of Philosophy California Institute of Technology Pasadena., California 1991 (submitted April 25, 1991) 01991 Paul Lewis Miller All rights reserved Acknowledgements I wish to acknowledge the following people for their assistance and/or sup- port during the time I have been at Caltech and GALCIT. First and foremost, I thank my advisor, Paul Dimotakis, for his encouragement throughout my graduate studies, and for many suggestions and contributions to this work. His scientific understanding and his personal character have made an indelible impression upon me. In collaboration with Paul, Dan Lang is responsible for a large number of accomplishments while at GALCIT that have greatly facilitated and improved this thesis. These include, among others, development of the HYDRA computer system and libraries, data acquisition support, and electronic design. His efforts have been a tremendous help. I give special thanks to Gene Broadwell, whose ideas concerning turbulent mixing have had a strong influence on this thesis. His friendship over the past several years is especially appreciated. Several of my fellow students have contributed help. In particular I'd like to thank Cliff Frieler, who is always interested in a problem, usually has a solution, and never refuses a request for assistance, and Dave Dowling, for assistance at the onset of the experiments and the indirect influence of his impressive thesis. Many staff members at GALCIT provided important contributions in the course of this work. Herb Gaebler offered assistance with a number of mechani- cal matters, Harry Hamaguchi produced the photographs of the facility and con- ducted the difficult printing of the jet growth-rate pictures, Pave1 Svitek aided in construction of the Phase I1 improvements and with the jet calibration, and Phil Wood created a piece of art with his machining of the new nozzle. -
Characterising the Heat and Mass Transfer Coefficients for a Crossflow
View metadata, citation and similar papers at core.ac.uk brought to you by CORE provided by AUT Scholarly Commons Characterising the heat and mass transfer coefficients for a crossflow interaction of air and water Reza Enayatollahi*, Roy Jonathan Nates, Timothy Anderson Department of Mechanical Engineering, Auckland University of Technology, Auckland, New Zealand. Corresponding Author: Reza Enayatollahi Email Address: [email protected] Postal Address: WD308, 19 St Paul Street, Auckland CBD, Auckland, New Zealand Phone Number: +64 9 921 9999 x8109 Abstract An experimental study was performed in order to characterise the heat and mass transfer processes, where an air stream passes through a sheet of falling water in a crossflow configuration. To achieve this, the hydrodynamics of a vertical liquid sheet in a ducted gaseous crossflow were studied. Four distinct flow regimes were identified (a stable sheet, a broken sheet, a flapping sheet and a lifted sheet) and mapped using Reynolds and Weber numbers. Subsequently, the Buckingham π theorem and a least squares analyses were employed leading to the proposal of two new dimensionless numbers referred to as the Prandtl Number of Evaporation and the Schmidt Number of Evaporation. These describe the heat and mass transfer in low temperature evaporation processes with crossflow interaction. Using these dimensionless numbers, empirical correlations for Sherwood and Nusselt numbers for the identified flow regimes were experimentally determined. These correlations were in a good agreement with their corresponding experimental values. It was found that flapping sheets have the strongest heat and mass transfer intensities whereas the weakest intensities were seen for the “stable” sheets.