Analysis and Comparison of Solar-Heat Driven Stirling, Brayton and Rankine Cycles for Space Power Generation
Total Page:16
File Type:pdf, Size:1020Kb
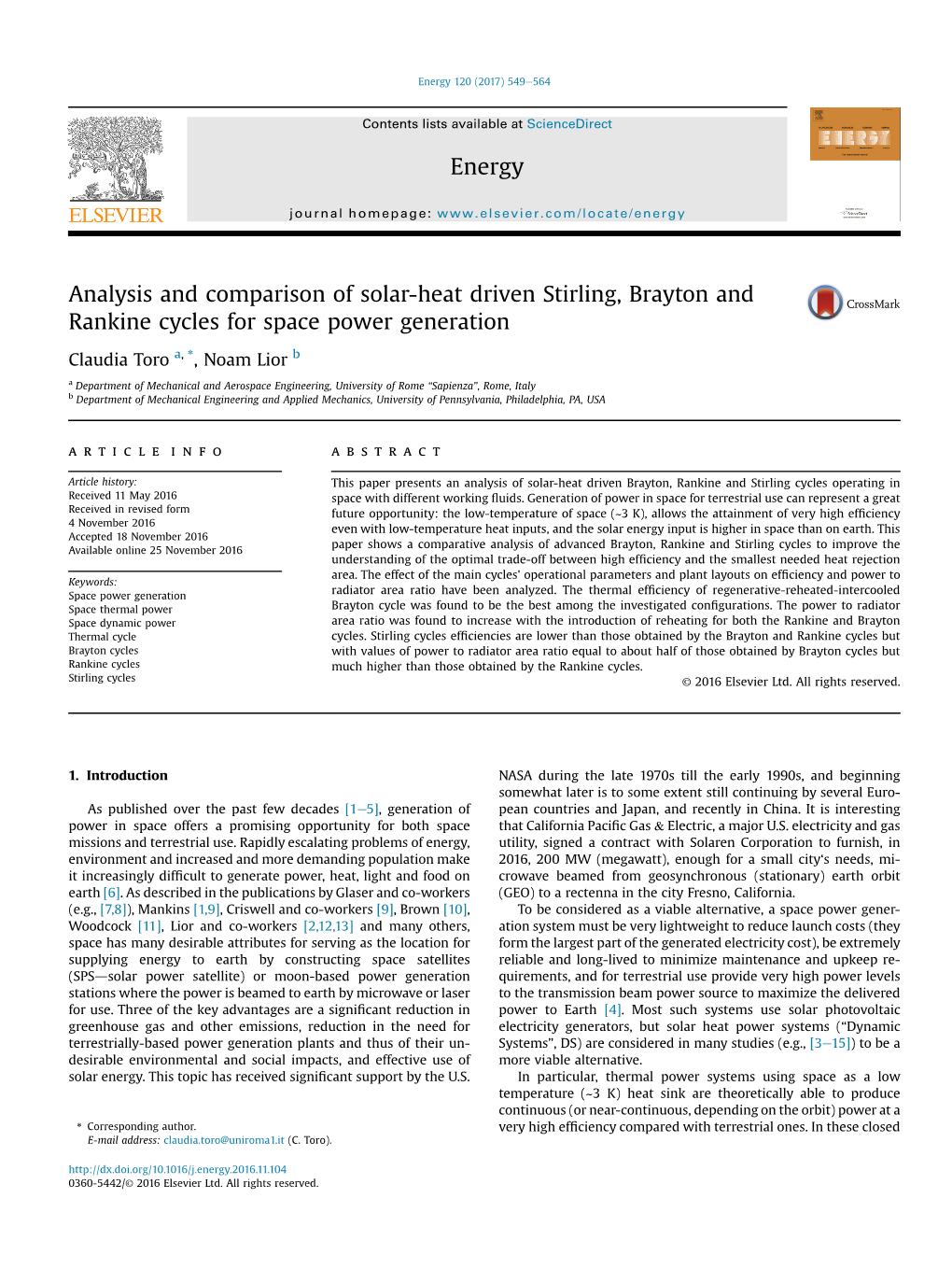
Load more
Recommended publications
-
Thermodynamic Optimization of an Organic Rankine Cycle for Power Generation from a Low Temperature Geothermal Heat Source
Thermodynamic Optimization of an Organic Rankine Cycle for Power Generation from a Low Temperature Geothermal Heat Source Inés Encabo Cáceres Roberto Agromayor Lars O. Nord Department of Energy and Process Engineering Norwegian University of Science and Technology (NTNU) Kolbjørn Hejes v.1B, NO-7491 Trondheim, Norway [email protected] Abstract fueled by natural gas or other fossil fuels (Macchi and Astolfi, 2017). However, during the last years, the The increasing concern on environment problems has increasing concern of the greenhouse effect and climate led to the development of renewable energy sources, change has led to an increase of renewable energy, such being the geothermal energy one of the most promising as wind and solar power. In addition to these listed ones in terms of power generation. Due to the low heat renewable energies, there is an energy source that shows source temperatures this energy provides, the use of a promising future due to the advantages it provides Organic Rankine Cycles is necessary to guarantee a when compared to other renewable energies. This good performance of the system. In this paper, the developing energy is geothermal energy, and its optimization of an Organic Rankine Cycle has been advantages are related to its availability (Macchi and carried out to determine the most suitable working fluid. Astolfi, 2017): it does not depend on the ambient Different cycle layouts and configurations for 39 conditions, it is stable, and it offers the possibility of different working fluids were simulated by means of a renewable energy base load operation. One of the Gradient Based Optimization Algorithm implemented challenges of geothermal energy is that it does not in MATLAB and linked to REFPROP property library. -
Transcritical Pressure Organic Rankine Cycle (ORC) Analysis Based on the Integrated-Average Temperature Difference in Evaporators
Applied Thermal Engineering 88 (2015) 2e13 Contents lists available at ScienceDirect Applied Thermal Engineering journal homepage: www.elsevier.com/locate/apthermeng Research paper Transcritical pressure Organic Rankine Cycle (ORC) analysis based on the integrated-average temperature difference in evaporators * Chao Yu, Jinliang Xu , Yasong Sun The Beijing Key Laboratory of Multiphase Flow and Heat Transfer for Low Grade Energy Utilizations, North China Electric Power University, Beijing 102206, PR China article info abstract Article history: Integrated-average temperature difference (DTave) was proposed to connect with exergy destruction (Ieva) Received 24 June 2014 in heat exchangers. Theoretical expressions were developed for DTave and Ieva. Based on transcritical Received in revised form pressure ORCs, evaporators were theoretically studied regarding DTave. An exact linear relationship be- 12 October 2014 tween DT and I was identified. The increased specific heats versus temperatures for organic fluid Accepted 11 November 2014 ave eva protruded its TeQ curve to decrease DT . Meanwhile, the decreased specific heats concaved its TeQ Available online 20 November 2014 ave curve to raise DTave. Organic fluid in the evaporator undergoes a protruded TeQ curve and a concaved T eQ curve, interfaced at the pseudo-critical temperature point. Elongating the specific heat increment Keywords: fi Organic Rankine Cycle section and shortening the speci c heat decrease section improved the cycle performance. Thus, the fi Integrated-average temperature difference system thermal and exergy ef ciencies were increased by increasing critical temperatures for 25 organic Exergy destruction fluids. Wet fluids had larger thermal and exergy efficiencies than dry fluids, due to the fact that wet fluids Thermal match shortened the superheated vapor flow section in condensers. -
Physics 170 - Thermodynamic Lecture 40
Physics 170 - Thermodynamic Lecture 40 ! The second law of thermodynamic 1 The Second Law of Thermodynamics and Entropy There are several diferent forms of the second law of thermodynamics: ! 1. In a thermal cycle, heat energy cannot be completely transformed into mechanical work. ! 2. It is impossible to construct an operational perpetual-motion machine. ! 3. It’s impossible for any process to have as its sole result the transfer of heat from a cooler to a hotter body ! 4. Heat flows naturally from a hot object to a cold object; heat will not flow spontaneously from a cold object to a hot object. ! ! Heat Engines and Thermal Pumps A heat engine converts heat energy into work. According to the second law of thermodynamics, however, it cannot convert *all* of the heat energy supplied to it into work. Basic heat engine: hot reservoir, cold reservoir, and a machine to convert heat energy into work. Heat Engines and Thermal Pumps 4 Heat Engines and Thermal Pumps This is a simplified diagram of a heat engine, along with its thermal cycle. Heat Engines and Thermal Pumps An important quantity characterizing a heat engine is the net work it does when going through an entire cycle. Heat Engines and Thermal Pumps Heat Engines and Thermal Pumps Thermal efciency of a heat engine: ! ! ! ! ! ! From the first law, it follows: Heat Engines and Thermal Pumps Yet another restatement of the second law of thermodynamics: No cyclic heat engine can convert its heat input completely to work. Heat Engines and Thermal Pumps A thermal pump is the opposite of a heat engine: it transfers heat energy from a cold reservoir to a hot one. -
Abstract 1. Introduction 2. Robert Stirling
Stirling Stuff Dr John S. Reid, Department of Physics, Meston Building, University of Aberdeen, Aberdeen AB12 3UE, Scotland Abstract Robert Stirling’s patent for what was essentially a new type of engine to create work from heat was submitted in 1816. Its reception was underwhelming and although the idea was sporadically developed, it was eclipsed by the steam engine and, later, the internal combustion engine. Today, though, the environmentally favourable credentials of the Stirling engine principles are driving a resurgence of interest, with modern designs using modern materials. These themes are woven through a historically based narrative that introduces Robert Stirling and his background, a description of his patent and the principles behind his engine, and discusses the now popular model Stirling engines readily available. These topical models, or alternatives made ‘in house’, form a good platform for investigating some of the thermodynamics governing the performance of engines in general. ---------------------------------------------------------------------------------------------------------------- 1. Introduction 2016 marks the bicentenary of the submission of Robert Stirling’s patent that described heat exchangers and the technology of the Stirling engine. James Watt was still alive in 1816 and his steam engine was gaining a foothold in mines, in mills, in a few goods railways and even in pioneering ‘steamers’. Who needed another new engine from another Scot? The Stirling engine is a markedly different machine from either the earlier steam engine or the later internal combustion engine. For reasons to be explained, after a comparatively obscure two centuries the Stirling engine is attracting new interest, for it has environmentally friendly credentials for an engine. This tribute introduces the man, his patent, the engine and how it is realised in example models readily available on the internet. -
Physics 100 Lecture 7
2 Physics 100 Lecture 7 Heat Engines and the 2nd Law of Thermodynamics February 12, 2018 3 Thermal Convection Warm fluid is less dense and rises while cool fluid sinks Resulting circulation efficiently transports thermal energy 4 COLD Convection HOT Turbulent motion of glycerol in a container heated from below and cooled from above. The bright lines show regions of rapid temperature variation. The fluid contains many "plumes," especially near the walls. The plumes can be identified as mushroom-shaped objects with heat flowing through the "stalk" and spreading in the "cap." The hot plumes tend to rise with their caps on top; falling, cold plumes are cap-down. All this plume activity is carried along in an overall counterclockwise "wind" caused by convection. Note the thermometer coming down from the top of the cell. Figure adapted from J. Zhang, S. Childress, A. Libchaber, Phys. Fluids 9, 1034 (1997). See detailed discussion in Kadanoff, L. P., Physics Today 54, 34 (August 2001). 5 The temperature of land changes more quickly than the nearby ocean. Thus convective “sea breezes” blow ____ during the day and ____ during the night. A. onshore … onshore B. onshore … offshore C. offshore … onshore D. offshore … offshore 6 The temperature of land changes more quickly than the nearby ocean. Thus convective “sea breezes” blow ____ during the day and ____ during the night. A. onshore … onshore B.onshore … offshore C.offshore … onshore D.offshore … offshore 7 Thermal radiation Any object whose temperature is above zero Kelvin emits energy in the form of electromagnetic radiation Objects both absorb and emit EM radiation continuously, and this phenomenon helps determine the object’s equilibrium temperature 8 The electromagnetic spectrum 9 Thermal radiation We’ll examine this concept some more in chapter 6 10 Why does the Earth cool more quickly on clear nights than it does on cloudy nights? A. -
Feasibility Study Into Stirling Engines Application in Ship's Energy Systems
Transactions on the Built Environment vol 42, © 1999 WIT Press, www.witpress.com, ISSN 1743-3509 Feasibility study into Stirling engines application in ship's energy systems S. Zmudzki, Faculty of Maritime Technology, Technical University of Szczecin, 71- 065 Szczecin, al Piastow 41, Poland E-mail: szmudzkia@shiptech. tuniv.szczecin.pl Abstract The possibility of utilization of solar energy as well as exhaust gas energy from main and auxiliary marine diesel engines for driving Stirling engines has been analysed. The Stirling engines are used for driving current generators. The solar dish Stirling units of 100 kW total effective power may be installed on a board of different type of ships. The system utilizing the exhaust gas energy has been provided with three-way catalyst which may lead to the reduction of emissions below limits established by appropriate regulations. 1 Introduction The Stirling engine belongs to a group of piston engines with so called external supply of heat energy, flowing then through metal walls of engine heater into working gas circulating in the working space. The heat energy supply may be realized or by means of direct effect of the high temperature energy source or by an intermediate heating system i.e. heat pipe or pool-boiler receiver. Thus, the design provides for the possibility of application of different types of heat energy of sufficiently large power. In particular, the advantages of Stirling engines are set off when using the alternative energy sources, especially waste heat energy, the operating costs for which are relatively lower in comparison with capital costs. In case of ship s energy installations, the solar energy available at appropriate geographical latitudes for ships having very large open deck surface / i.e. -
Fuel Cells Versus Heat Engines: a Perspective of Thermodynamic and Production
Fuel Cells Versus Heat Engines: A Perspective of Thermodynamic and Production Efficiencies Introduction: Fuel Cells are being developed as a powering method which may be able to provide clean and efficient energy conversion from chemicals to work. An analysis of their real efficiencies and productivity vis. a vis. combustion engines is made in this report. The most common mode of transportation currently used is gasoline or diesel engine powered automobiles. These engines are broadly described as internal combustion engines, in that they develop mechanical work by the burning of fossil fuel derivatives and harnessing the resultant energy by allowing the hot combustion product gases to expand against a cylinder. This arrangement allows for the fuel heat release and the expansion work to be performed in the same location. This is in contrast to external combustion engines, in which the fuel heat release is performed separately from the gas expansion that allows for mechanical work generation (an example of such an engine is steam power, where fuel is used to heat a boiler, and the steam then drives a piston). The internal combustion engine has proven to be an affordable and effective means of generating mechanical work from a fuel. However, because the majority of these engines are powered by a hydrocarbon fossil fuel, there has been recent concern both about the continued availability of fossil fuels and the environmental effects caused by the combustion of these fuels. There has been much recent publicity regarding an alternate means of generating work; the hydrogen fuel cell. These fuel cells produce electric potential work through the electrochemical reaction of hydrogen and oxygen, with the reaction product being water. -
Recording and Evaluating the Pv Diagram with CASSY
LD Heat Physics Thermodynamic cycle Leaflets P2.6.2.4 Hot-air engine: quantitative experiments The hot-air engine as a heat engine: Recording and evaluating the pV diagram with CASSY Objects of the experiment Recording the pV diagram for different heating voltages. Determining the mechanical work per revolution from the enclosed area. Principles The cycle of a heat engine is frequently represented as a closed curve in a pV diagram (p: pressure, V: volume). Here the mechanical work taken from the system is given by the en- closed area: W = − ͛ p ⋅ dV (I) The cycle of the hot-air engine is often described in an idealised form as a Stirling cycle (see Fig. 1), i.e., a succession of isochoric heating (a), isothermal expansion (b), isochoric cooling (c) and isothermal compression (d). This description, however, is a rough approximation because the working piston moves sinusoidally and therefore an isochoric change of state cannot be expected. In this experiment, the pV diagram is recorded with the computer-assisted data acquisition system CASSY for comparison with the real behaviour of the hot-air engine. A pressure sensor measures the pressure p in the cylinder and a displacement sensor measures the position s of the working piston, from which the volume V is calculated. The measured values are immediately displayed on the monitor in a pV diagram. Fig. 1 pV diagram of the Stirling cycle 0210-Wei 1 P2.6.2.4 LD Physics Leaflets Setup Apparatus The experimental setup is illustrated in Fig. 2. 1 hot-air engine . 388 182 1 U-core with yoke . -
Novel Hot Air Engine and Its Mathematical Model – Experimental Measurements and Numerical Analysis
POLLACK PERIODICA An International Journal for Engineering and Information Sciences DOI: 10.1556/606.2019.14.1.5 Vol. 14, No. 1, pp. 47–58 (2019) www.akademiai.com NOVEL HOT AIR ENGINE AND ITS MATHEMATICAL MODEL – EXPERIMENTAL MEASUREMENTS AND NUMERICAL ANALYSIS 1 Gyula KRAMER, 2 Gabor SZEPESI *, 3 Zoltán SIMÉNFALVI 1,2,3 Department of Chemical Machinery, Institute of Energy and Chemical Machinery University of Miskolc, Miskolc-Egyetemváros 3515, Hungary e-mail: [email protected], [email protected], [email protected] Received 11 December 2017; accepted 25 June 2018 Abstract: In the relevant literature there are many types of heat engines. One of those is the group of the so called hot air engines. This paper introduces their world, also introduces the new kind of machine that was developed and built at Department of Chemical Machinery, Institute of Energy and Chemical Machinery, University of Miskolc. Emphasizing the novelty of construction and the working principle are explained. Also the mathematical model of this new engine was prepared and compared to the real model of engine. Keywords: Hot, Air, Engine, Mathematical model 1. Introduction There are three types of volumetric heat engines: the internal combustion engines; steam engines; and hot air engines. The first one is well known, because it is on zenith nowadays. The steam machines are also well known, because their time has just passed, even the elder ones could see those in use. But the hot air engines are forgotten. Our aim is to consider that one. The history of hot air engines is 200 years old. -
Sustainable Energy Conversion Through the Use of Organic Rankine Cycles for Waste Heat Recovery and Solar Applications
ENERGY SYSTEMS RESEARCH UNIT AEROSPACE AND MECHANICAL ENGINEERING DEPARTMENT UNIVERSITY OF LIÈGE Sustainable Energy Conversion Through the Use of Organic Rankine Cycles for Waste Heat Recovery and Solar Applications. in Partial Fulfillment of the Requirements for the Degree of Doctor of Applied Sciences Presented to the Faculty of Applied Science of the University of Liège (Belgium) by Sylvain Quoilin Liège, October 2011 Introductory remarks Version 1.1, published in October 2011 © 2011 Sylvain Quoilin 〈►[email protected]〉 Licence. This work is licensed under the Creative Commons Attribution - No Derivative Works 2.5 License. To view a copy of this license, visit ►http://creativecommons.org/licenses/by-nd/2.5/ or send a letter to Creative Commons, 543 Howard Street, 5th Floor, San Francisco, California, 94105, USA. Contact the author to request other uses if necessary. Trademarks and service marks. All trademarks, service marks, logos and company names mentioned in this work are property of their respective owner. They are protected under trademark law and unfair competition law. The importance of the glossary. It is strongly recommended to read the glossary in full before starting with the first chapter. Hints for screen use. This work is optimized for both screen and paper use. It is recommended to use the digital version where applicable. It is a file in Portable Document Format (PDF) with hyperlinks for convenient navigation. All hyperlinks are marked with link flags (►). Hyperlinks in diagrams might be marked with colored borders instead. Navigation aid for bibliographic references. Bibliographic references to works which are publicly available as PDF files mention the logical page number and an offset (if non-zero) to calculate the physical page number. -
Rankine Cycle Definitions
Rankine Cycle Reading Problems 11.1 ! 11.7 11.29, 11.36, 11.43, 11.47, 11.52, 11.55, 11.58, 11.74 Definitions • working fluid is alternately vaporized and condensed as it recirculates in a closed cycle • the standard vapour cycle that excludes internal irreversibilities is called the Ideal Rankine Cycle Analyze the Process Device 1st Law Balance Boiler h2 + qH = h3 ) qH = h3 − h2 (in) Turbine h3 = h4 + wT ) wT = h3 − h4 (out) Condenser h4 = h1 + qL ) qL = h4 − h1 (out) Pump h1 + wP = h2 ) wP = h2 − h1 (in) 1 The Rankine efficiency is net work output ηR = heat supplied to the boiler (h − h ) + (h − h ) = 3 4 1 2 (h3 − h2) Effects of Boiler and Condenser Pressure We know the efficiency is proportional to T η / 1 − L TH The question is ! how do we increase efficiency ) TL # and/or TH ". 1. INCREASED BOILER PRESSURE: • an increase in boiler pressure results in a higher TH for the same TL, therefore η ". • but 40 has a lower quality than 4 – wetter steam at the turbine exhaust – results in cavitation of the turbine blades – η # plus " maintenance • quality should be > 80 − 90% at the turbine exhaust 2 2. LOWER TL: • we are generally limited by the T ER (lake, river, etc.) eg. lake @ 15 ◦C + ∆T = 10 ◦C = 25 ◦C | {z } resistance to HT ) Psat = 3:169 kP a. • this is why we have a condenser – the pressure at the exit of the turbine can be less than atmospheric pressure 3. INCREASED TH BY ADDING SUPERHEAT: • the average temperature at which heat is supplied in the boiler can be increased by superheating the steam – dry saturated steam from the boiler is passed through a second bank of smaller bore tubes within the boiler until the steam reaches the required temperature – The value of T H , the mean temperature at which heat is added, increases, while TL remains constant. -
Thermodynamics of Power Generation
THERMAL MACHINES AND HEAT ENGINES Thermal machines ......................................................................................................................................... 1 The heat engine ......................................................................................................................................... 2 What it is ............................................................................................................................................... 2 What it is for ......................................................................................................................................... 2 Thermal aspects of heat engines ........................................................................................................... 3 Carnot cycle .............................................................................................................................................. 3 Gas power cycles ...................................................................................................................................... 4 Otto cycle .............................................................................................................................................. 5 Diesel cycle ........................................................................................................................................... 8 Brayton cycle .....................................................................................................................................