Influence of the CO2 Content in Shielding Gas on the Temperature
Total Page:16
File Type:pdf, Size:1020Kb
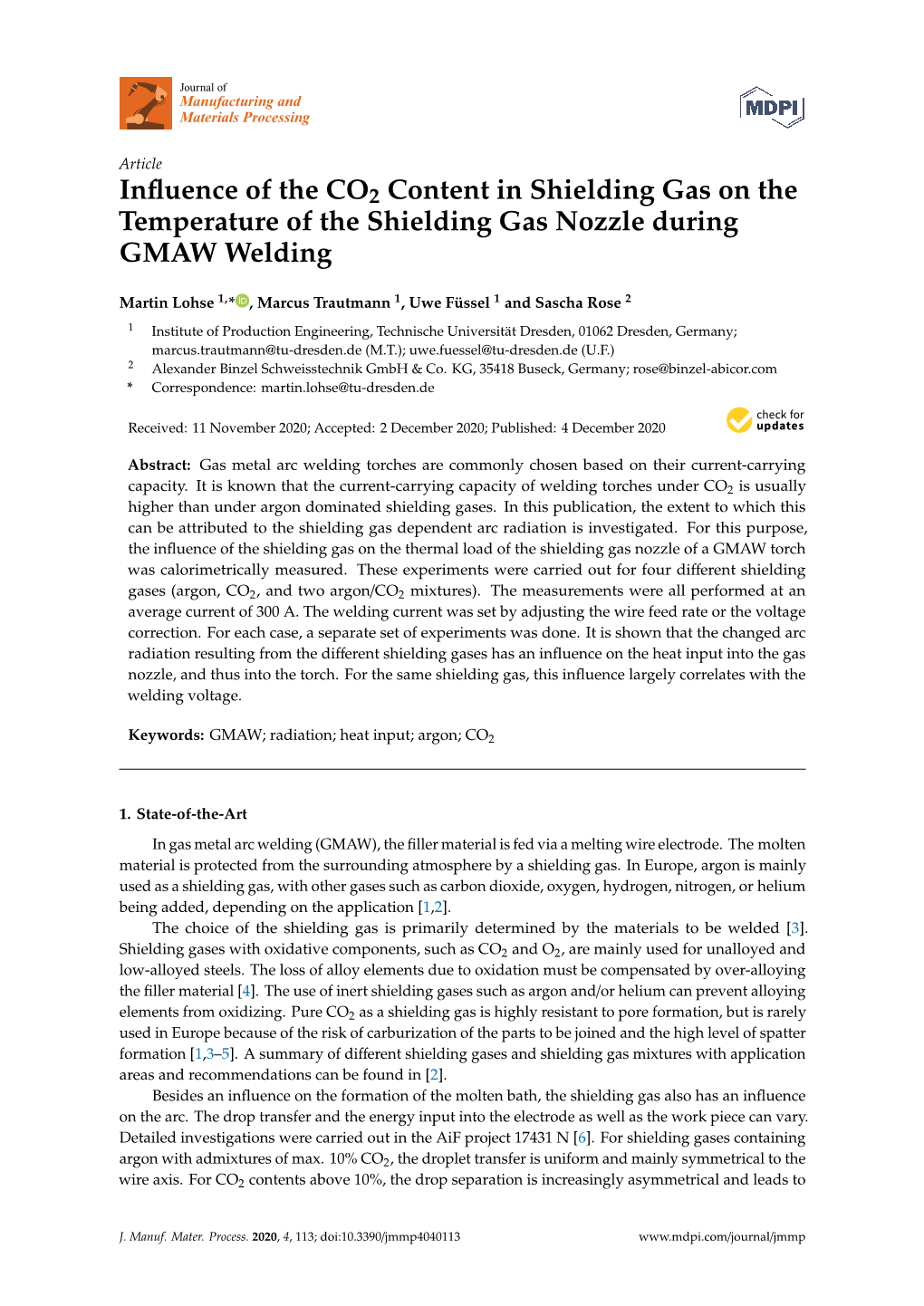
Load more
Recommended publications
-
Study and Characterization of EN AW 6181/6082-T6 and EN AC
metals Article Study and Characterization of EN AW 6181/6082-T6 and EN AC 42100-T6 Aluminum Alloy Welding of Structural Applications: Metal Inert Gas (MIG), Cold Metal Transfer (CMT), and Fiber Laser-MIG Hybrid Comparison Giovanna Cornacchia * and Silvia Cecchel DIMI, Department of Industrial and Mechanical Engineering, University of Brescia, via Branze 38, 25123 Brescia, Italy; [email protected] * Correspondence: [email protected]; Tel.: +39-030-371-5827; Fax: +39-030-370-2448 Received: 18 February 2020; Accepted: 26 March 2020; Published: 27 March 2020 Abstract: The present research investigates the effects of different welding techniques, namely traditional metal inert gas (MIG), cold metal transfer (CMT), and fiber laser-MIG hybrid, on the microstructural and mechanical properties of joints between extruded EN AW 6181/6082-T6 and cast EN AC 42100-T6 aluminum alloys. These types of weld are very interesting for junctions of Al-alloys parts in the transportation field to promote the lightweight of a large scale chassis. The weld joints were characterized through various metallurgical methods including optical microscopy and hardness measurements to assess their microstructure and to individuate the nature of the intermetallics, their morphology, and distribution. The results allowed for the evaluation of the discrepancies between the welding technologies (MIG, CMT, fiber laser) on different aluminum alloys that represent an exhaustive range of possible joints of a frame. For this reason, both simple bar samples and real junctions of a prototype frame of a sports car were studied and, compared where possible. The study demonstrated the higher quality of innovative CMT and fiber laser-MIG hybrid welding than traditional MIG and the comparison between casting and extrusion techniques provide some inputs for future developments in the automotive field. -
Formation and Distribution of Porosity in Al-Si Welds
Formation and Distribution of Porosity in Al-Si Welds by Pierre-Alexandre LEGAIT A Thesis Submitted to the Faculty Of the WORCESTER POLYTECHNIC INSTITUTE In partial fulfillment of the requirements for the Degree of Masters of Science In Material Science and Engineering By May 2005 APPROVED: Diran Apelian, Howmet Professor of Mechanical Engineering, Advisor Richard D. Sisson Jr., George F. Fuller Professor of Mechanical Engineering Material Science and Engineering, Program Head ABSTRACT Aluminum alloys are the subject of increasing interest (in the automotive industry, as well as aircraft industry), aiming to reduce the weight of components and also allowing a profit in term of energy saving. Concerning the assembly, riveting has been widely used in the aircraft industry, whereas welding seems to be promising in the car industry in the case of aluminum alloys. Nevertheless, welding can generate defects, such as porosity or hot cracking, which could limit its development. One of the major problems associated with the welding of aluminum alloys is the formation of gas porosity. Aluminum alloy cleanliness remaining one of the aluminum industry’s primary concerns, this project focuses on the formation and distribution of porosity in Al-Si welds. A literature review has been performed, to identify the mechanisms of porosity formation in welds and castings. Porosity distribution in welds has been investigated, based on three different welding techniques: hybrid Laser/MIG welding process, the electron beam welding process, and the MIG dual wire welding process. Porosity distribution results provide information on to the porosity formation mechanisms involved during welding. A complete microstructure, microhardness and EDX analysis have been carried out, to describe and quantify the solidification process within the welds. -
And Abiogenesis
Historical Development of the Distinction between Bio- and Abiogenesis. Robert B. Sheldon NASA/MSFC/NSSTC, 320 Sparkman Dr, Huntsville, AL, USA ABSTRACT Early greek philosophers laid the philosophical foundations of the distinction between bio and abiogenesis, when they debated organic and non-organic explanations for natural phenomena. Plato and Aristotle gave organic, or purpose-driven explanations for physical phenomena, whereas the materialist school of Democritus and Epicurus gave non-organic, or materialist explanations. These competing schools have alternated in popularity through history, with the present era dominated by epicurean schools of thought. Present controversies concerning evidence for exobiology and biogenesis have many aspects which reflect this millennial debate. Therefore this paper traces a selected history of this debate with some modern, 20th century developments due to quantum mechanics. It ¯nishes with an application of quantum information theory to several exobiology debates. Keywords: Biogenesis, Abiogenesis, Aristotle, Epicurus, Materialism, Information Theory 1. INTRODUCTION & ANCIENT HISTORY 1.1. Plato and Aristotle Both Plato and Aristotle believed that purpose was an essential ingredient in any scienti¯c explanation, or teleology in philosophical nomenclature. Therefore all explanations, said Aristotle, answer four basic questions: what is it made of, what does it represent, who made it, and why was it made, which have the nomenclature material, formal, e±cient and ¯nal causes.1 This aristotelean framework shaped the terms of the scienti¯c enquiry, invisibly directing greek science for over 500 years. For example, \organic" or \¯nal" causes were often deemed su±cient to explain natural phenomena, so that a rock fell when released from rest because it \desired" its own kind, the earth, over unlike elements such as air, water or ¯re. -
MTI Friction Welding Technology Brochure
Friction Welding Manufacturing Technology, Inc. All of us at MTI… would like to extend our thanks for your interest in our company. Manufacturing Technology, Inc. has been a leading manufacturer of inertia, direct drive and hybrid friction welders since 1976. We hope that the following pages will further spark your interest by detailing a number of our products, services and capabilities. We at MTI share a common goal…to help you solve your manufacturing problems in the most Table of Contents efficient way possible. Combining friction welding Introduction to Friction Welding 2 with custom designed automation, we have Advantages of MTI’s Process 3 demonstrated dramatic savings in labor and Inertia Friction Welding 4 material with no sacrifice to quality. Contact us Direct Drive & Hybrid Friction Welding 5 today to find out what we can do for you. Machine Monitors & Controllers 6 Safety Features 7 Flash Removal 7 MTI Welding Services 8 Weldable Combinations 9 Applications Aircraft/Aerospace 10 Oil Field Pieces 14 Military 16 Bimetallic & Special 20 Agricultural & Trucking 22 Automotive 28 General 38 Special Welders & Automated Machines 46 Machine Models & Capabilities 48 Friction Welding 4 What It Is Friction welding is a solid-state joining process that produces coalescence in materials, using the heat developed between surfaces through a combination of mechanically induced rubbing motion and Information applied load. The resulting joint is of forged quality. Under normal conditions, the faying surfaces do not melt. Filler metal, flux and shielding gas are not required with this process. Dissimilar Materials Even metal combinations not normally considered compatible can be joined by friction welding, such as aluminum to steel, copper to aluminum, titanium to copper and nickel alloys to steel. -
Parameter Optimization of Gas Metal Arc Welding Process on Duplex 2205 Stainless Steel Using Irb1410 Arc Welding Robot
International Research Journal of Engineering and Technology (IRJET) e-ISSN: 2395-0056 Volume: 08 Issue: 03 | Mar 2021 www.irjet.net p-ISSN: 2395-0072 PARAMETER OPTIMIZATION OF GAS METAL ARC WELDING PROCESS ON DUPLEX 2205 STAINLESS STEEL USING IRB1410 ARC WELDING ROBOT Anand Jayakumar A1, Yash Nigam2, Vighneswaran C3, Surender S4 1Asst. Professor, Dept. of Mechanical Engineering, Sri Ramakrishna Institute of Technology, India 2,3,4Student, Dept. of Mechanical Engineering, Sri Ramakrishna Institute of Technology, India ---------------------------------------------------------------------***---------------------------------------------------------------------- Abstract - This review paper outline the recent research consumable MIG wire electrode and the workpiece metal(s), works on parameter optimization of duplex 2205 stainless which will heats the workpiece metal(s), causing them to steel using IRB1410 arc welding robot. Gas metal arc welding melt and join. Gas metal arc welding, also known as metal (GMAW) process has widely been employed due to the wide inert gas (MIG) welding, uses a continuous solid wire range of applications, cheap consumables and easy handling. A electrode that travels through the welding gun, which is suitable model is needed to investigate the characteristics of accompanied by a shielding gas to protect it from the effects of process parameters on the bead geometry in the contaminants. Gas metal arc welding (GMAW) is a welding GMA welding process in order to achieve a high level of processby an arc in which the source of heat is an arc is welding performance and quality. This paper is intended to formed between the consumable metal electrode and the represent new algorithms in the robotic GMA welding process work piece with an externally supplied gaseous shield of to predict process parameters on top-bead distance. -
Blending Hydrogen Into Natural Gas Pipeline Networks: a Review of Key Issues
Blending Hydrogen into Natural Gas Pipeline Networks: A Review of Key Issues M. W. Melaina, O. Antonia, and M. Penev NREL is a national laboratory of the U.S. Department of Energy, Office of Energy Efficiency & Renewable Energy, operated by the Alliance for Sustainable Energy, LLC. Technical Report NREL/TP-5600-51995 March 2013 Contract No. DE-AC36-08GO28308 Blending Hydrogen into Natural Gas Pipeline Networks: A Review of Key Issues M. W. Melaina, O. Antonia, and M. Penev Prepared under Task No. HT12.2010 NREL is a national laboratory of the U.S. Department of Energy, Office of Energy Efficiency & Renewable Energy, operated by the Alliance for Sustainable Energy, LLC. National Renewable Energy Laboratory Technical Report 15013 Denver West Parkway NREL/TP-5600-51995 Golden, Colorado 80401 March 2013 303-275-3000 • www.nrel.gov Contract No. DE-AC36-08GO28308 NOTICE This report was prepared as an account of work sponsored by an agency of the United States government. Neither the United States government nor any agency thereof, nor any of their employees, makes any warranty, express or implied, or assumes any legal liability or responsibility for the accuracy, completeness, or usefulness of any information, apparatus, product, or process disclosed, or represents that its use would not infringe privately owned rights. Reference herein to any specific commercial product, process, or service by trade name, trademark, manufacturer, or otherwise does not necessarily constitute or imply its endorsement, recommendation, or favoring by the United States government or any agency thereof. The views and opinions of authors expressed herein do not necessarily state or reflect those of the United States government or any agency thereof. -
GSS-124 Welding Fabrication for Gunsmiths 1.0 Unit
Lassen Community College Course Outline GSS-124 Welding Fabrication for Gunsmiths 1.0 Unit I. Catalog Description Students will select and fabricate gunsmith related projects using appropriate welding processes and techniques. Students will also have an opportunity to learn or improve welding skills related to the gunsmith vocation. Does Not Transfer to UC/CSU 50 Hours Lab Scheduled: II. Coding Information Repeatability: Take 1 Time Grading Option: Pass/No Pass Only Credit Type: Credit - Not Degree Applicable TOP Code: 095650 III. Course Objectives A. Course Student Learning Outcomes Upon completion of this course the student will be able to: Safely handle equipment to gas tungsten weld selected joint designs to critical industry standards. B. Course Objectives Upon completion of this course the student will be able to: 1. Explain the setup of both oxygen/acetylene welding and cutting. 2. Demonstrate correct project layout. 3. Demonstrate oxy/ace cutting. 4. Employ oxygen/acetylene welding to construct project. 5. Demonstrate setup of SMAW machine. 6. Identify and select correct electrodes. 7. Fabricate project using SMAW. 8. Demonstrate cleanup procedures. IV. Course Content A. Safety precautions 1. Electrical shock 2. Radiation hazards 3. Compressed gases 4. Air contamination 5. Emergency shop procedures B. Oxyacetylene welding 1. T-joints 2. Open butt joint - flat C. Shielded metal arc welding 1. T-joint - flat 2. T-joint - vertical GSS-124 Welding Fabrication for Gunsmiths Page 1 D. Gas metal arc welding 1. T-joint - flat 2. T-joint - vertical E. Gas tungsten arc welding 1. T-joint - flat 2. T-joint - vertical F. Cutting 1. -
Viscosity of Gases References
VISCOSITY OF GASES Marcia L. Huber and Allan H. Harvey The following table gives the viscosity of some common gases generally less than 2% . Uncertainties for the viscosities of gases in as a function of temperature . Unless otherwise noted, the viscosity this table are generally less than 3%; uncertainty information on values refer to a pressure of 100 kPa (1 bar) . The notation P = 0 specific fluids can be found in the references . Viscosity is given in indicates that the low-pressure limiting value is given . The dif- units of μPa s; note that 1 μPa s = 10–5 poise . Substances are listed ference between the viscosity at 100 kPa and the limiting value is in the modified Hill order (see Introduction) . Viscosity in μPa s 100 K 200 K 300 K 400 K 500 K 600 K Ref. Air 7 .1 13 .3 18 .5 23 .1 27 .1 30 .8 1 Ar Argon (P = 0) 8 .1 15 .9 22 .7 28 .6 33 .9 38 .8 2, 3*, 4* BF3 Boron trifluoride 12 .3 17 .1 21 .7 26 .1 30 .2 5 ClH Hydrogen chloride 14 .6 19 .7 24 .3 5 F6S Sulfur hexafluoride (P = 0) 15 .3 19 .7 23 .8 27 .6 6 H2 Normal hydrogen (P = 0) 4 .1 6 .8 8 .9 10 .9 12 .8 14 .5 3*, 7 D2 Deuterium (P = 0) 5 .9 9 .6 12 .6 15 .4 17 .9 20 .3 8 H2O Water (P = 0) 9 .8 13 .4 17 .3 21 .4 9 D2O Deuterium oxide (P = 0) 10 .2 13 .7 17 .8 22 .0 10 H2S Hydrogen sulfide 12 .5 16 .9 21 .2 25 .4 11 H3N Ammonia 10 .2 14 .0 17 .9 21 .7 12 He Helium (P = 0) 9 .6 15 .1 19 .9 24 .3 28 .3 32 .2 13 Kr Krypton (P = 0) 17 .4 25 .5 32 .9 39 .6 45 .8 14 NO Nitric oxide 13 .8 19 .2 23 .8 28 .0 31 .9 5 N2 Nitrogen 7 .0 12 .9 17 .9 22 .2 26 .1 29 .6 1, 15* N2O Nitrous -
Atmospheric Gases Student Handout Atmospheric Gases
Atmospheric Gases Student Handout Atmospheric Gases Driving Question: What is our atmosphere made of? In this activity you will: 1. Explore the variety and ratio of compounds and elements that make up the Earth’s atmosphere. 2. Understand volumetric measurements of gases in the atmosphere. 3. Visually depict the composition of the atmosphere. Background Information: Understanding Concentration Measurements In this activity, we will investigate the gas composition of our planet’s atmosphere. We use percentages to represent units of gas composition. A percent (%) is equivalent to 1 part out of 100 equal units. 1% = 1 part out of 100 For smaller concentrations scientists use parts per million (ppm) to represent concentrations of gases (or pollutants) in the atmosphere). One ppm is equivalent to 1 part out of 1,000,000 if the volume being measured is separated into 1,000,000 equal units. 1 ppm = 1 part out of 1,000,000 In this activity, you will use graph paper to represent the concentration of different gases in the atmosphere. Copyright © 2011 Environmental Literacy and Inquiry Working Group at Lehigh University Atmospheric Gases Student Handout 2 Here are some examples to help visualize parts per million: The common unit mg/liter is equal to ppm concentration Four drops of ink in a 55-gallon barrel of water would produce an "ink concentration" of 1 ppm. 1 12-oz can of soda pop in a 30-meter swimming pool 1 3-oz chocolate bar on a football field Atmospheric Composition Activity You will be creating a graphic model of the atmosphere composition using the Atmospheric Composition of Clean Dry Air activity sheet. -
Infrared Spectroscopy of Matrix-Isolated Polycyclic Aromatic Hydrocarbon Ions
J. Phys. Chem. A 2000, 104, 3655-3669 3655 Infrared Spectroscopy of Matrix-Isolated Polycyclic Aromatic Hydrocarbon Ions. 5. PAHs Incorporating a Cyclopentadienyl Ring† D. M. Hudgins,* C. W. Bauschlicher, Jr., and L. J. Allamandola NASA Ames Research Center, MS 245-6, Moffett Field, California 94035 J. C. Fetzer CheVron Research Company, Richmond, California 94802 ReceiVed: NoVember 5, 1999; In Final Form: February 9, 2000 The matrix-isolation technique has been employed to measure the mid-infrared spectra of the ions of several polycyclic aromatic hydrocarbons whose structures incorporate a cyclopentadienyl ring. These include the cations of fluoranthene (C16H10), benzo[a]fluoranthene, benzo[b]fluoranthene, benzo[j]fluoranthene, and benzo- [k]fluoranthene (all C20H12 isomers), as well as the anions of benzo[a]fluoranthene and benzo[j]fluoranthene. With the exception of fluoranthene, which presented significant theoretical difficulties, the experimental data are compared to theoretically calculated values obtained using density functional theory (DFT) at the B3LYP/ 4-31G level. In general, there is good overall agreement between the two data sets, with the positional agreement between the experimentally measured and theoretically predicted bands somewhat better than that associated with their intensities. The results are also consistent with previous experimental studies of polycyclic aromatic hydrocarbon ions. Specifically, in both the cationic and anionic species the strongest ion bands typically cluster in the 1450 to 1300 cm-1 range, reflecting an order-of-magnitude enhancement in the CC stretching and CH in-plane bending modes between 1600 and 1100 cm-1 in these species. The aromatic CH out-of- plane bending modes, on the other hand, are usually modestly suppressed (e 2x - 5x) in the cations relative to those of the neutral species, with the nonadjacent CH modes most strongly affected. -
Tracer Applications of Noble Gas Radionuclides in the Geosciences
To be published in Earth-Science Reviews Tracer Applications of Noble Gas Radionuclides in the Geosciences (August 20, 2013) Z.-T. Lua,b, P. Schlosserc,d, W.M. Smethie Jr.c, N.C. Sturchioe, T.P. Fischerf, B.M. Kennedyg, R. Purtscherth, J.P. Severinghausi, D.K. Solomonj, T. Tanhuak, R. Yokochie,l a Physics Division, Argonne National Laboratory, Argonne, Illinois, USA b Department of Physics and Enrico Fermi Institute, University of Chicago, Chicago, USA c Lamont-Doherty Earth Observatory, Columbia University, Palisades, New York, USA d Department of Earth and Environmental Sciences and Department of Earth and Environmental Engineering, Columbia University, New York, USA e Department of Earth and Environmental Sciences, University of Illinois at Chicago, Chicago, IL, USA f Department of Earth and Planetary Sciences, University of New Mexico, Albuquerque, USA g Center for Isotope Geochemistry, Lawrence Berkeley National Laboratory, Berkeley, USA h Climate and Environmental Physics, Physics Institute, University of Bern, Bern, Switzerland i Scripps Institution of Oceanography, University of California, San Diego, USA j Department of Geology and Geophysics, University of Utah, Salt Lake City, USA k GEOMAR Helmholtz Center for Ocean Research Kiel, Marine Biogeochemistry, Kiel, Germany l Department of Geophysical Sciences, University of Chicago, Chicago, USA Abstract 81 85 39 Noble gas radionuclides, including Kr (t1/2 = 229,000 yr), Kr (t1/2 = 10.8 yr), and Ar (t1/2 = 269 yr), possess nearly ideal chemical and physical properties for studies of earth and environmental processes. Recent advances in Atom Trap Trace Analysis (ATTA), a laser-based atom counting method, have enabled routine measurements of the radiokrypton isotopes, as well as the demonstration of the ability to measure 39Ar in environmental samples. -
Guidelines for the Welded Fabrication of Nickel-Containing Stainless Steels for Corrosion Resistant Services
NiDl Nickel Development Institute Guidelines for the welded fabrication of nickel-containing stainless steels for corrosion resistant services A Nickel Development Institute Reference Book, Series No 11 007 Table of Contents Introduction ........................................................................................................ i PART I – For the welder ...................................................................................... 1 Physical properties of austenitic steels .......................................................... 2 Factors affecting corrosion resistance of stainless steel welds ....................... 2 Full penetration welds .............................................................................. 2 Seal welding crevices .............................................................................. 2 Embedded iron ........................................................................................ 2 Avoid surface oxides from welding ........................................................... 3 Other welding related defects ................................................................... 3 Welding qualifications ................................................................................... 3 Welder training ............................................................................................. 4 Preparation for welding ................................................................................. 4 Cutting and joint preparation ...................................................................